Text and images: Jurgen Laudus, Vice President and General Manager of Materialise Manufacturing, 4 November 2024
In the current landscape of the 3D printing industry, it's crucial to differentiate between the prototyping market and serial manufacturing.
The prototyping sector is experiencing a decline, driven by three key factors.
- Firstly, the challenging economic climate has led to reduced investments, particularly impacting industries like automotive, which plays a vital role in European manufacturing.
- Secondly, there is a growing trend of companies insourcing their prototyping services, acquiring 3D printing systems, and managing these operations internally.
- Finally, China's technological advancements and ability to maintain cost efficiency have resulted in a significant shift, with more prototyping business being outsourced to China.
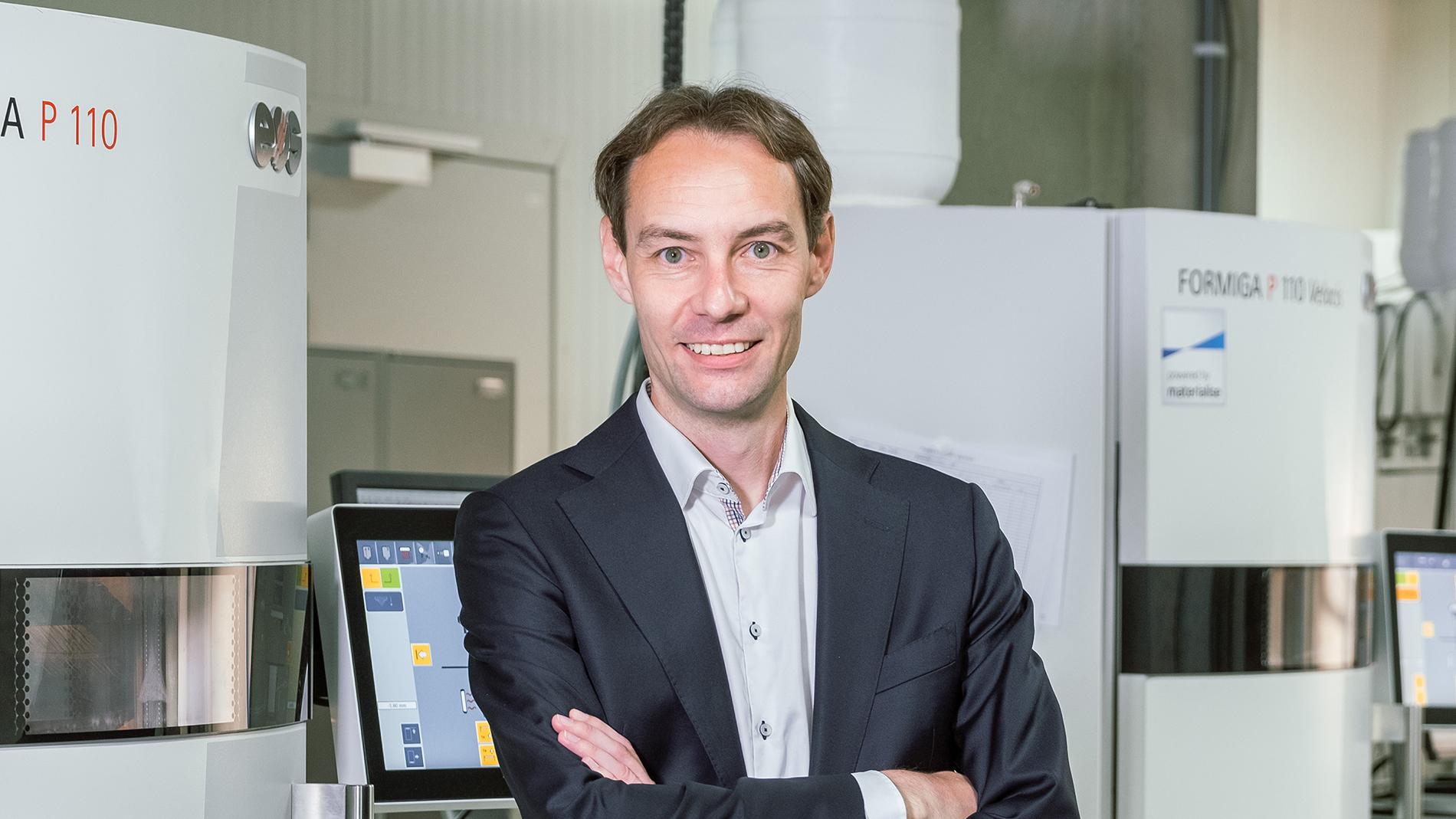
When we turn to serial manufacturing, there is continued growth, with double-digit increases. This expansion is driven by the medtech sector, which focuses on the development of medical devices for healthcare, as well as the aerospace industry.
We are observing a clear divide between the prototyping and serial manufacturing sectors. Many companies remain focused on prototyping, but there’s a growing necessity for them to shift towards serial manufacturing in an ‘adapt or die’ scenario. At Materialise, we began investing in serial manufacturing back in 2011, and while the current economic climate has heightened the urgency for this transformation, significant barriers remain.
Need for redesign
One major hurdle is the need for redesign. Components that have traditionally been produced using conventional manufacturing methods must be redesigned for additive manufacturing, which is both costly and complex. Although this redesign is a non-recurring cost, it often limits the adoption of 3D printing, especially for upgrade-designs in industries like aerospace. However, when entirely new airplane designs emerge, we believe 3D printing will play a more significant role.
The second barrier is the need for process optimization. Achieving the required quality standards involves fine-tuning and optimizing the 3D printing production processes, which takes time but is essential for success.
There is also a clear call to action for the additive manufacturing industry. The AM sector must collaborate closely with the broader manufacturing industry to identify, nurture, and expand new applications. Currently, many manufacturing companies face challenges when trying to adopt and scale 3D printing operations. A significant number of them still grapple with the perceived complexity of AM technology. It is up to the 3D printing industry to dismantle these barriers and support manufacturers in successfully integrating and scaling their 3D printing operations.
FURTHER INFORMATION:
We have also discussed the current market situation with four other AM experts:
- Arno Held, AM Ventures: „It is positive that dubious participants have left the table“
- Rainer Lotz, Renishaw: “The good long-term prospects are not at risk”
- Jurgen Laudus, Materialise Manufacturing: Big difference between prototyping and series production
- Rainer Gebhardt, VDMA: „More confident than the average“
Materialise at Formnext 2024: Hall 12.1, Booth C139
Tags
- Market reports and studies