Formnext gives outstanding ideas for modern production the stage they deserve with the Formnext Awards!
What are the Formnext Awards?
The AM world shines thanks to talented, motivated people who continue to advance the technology and thus drive the entire industry. It’s therefore only fitting that their ideas should receive the time in the spotlight they deserve – for the good of the industry and the forward-thinking development of modern production as a whole.
At the last Formnext, the new awards format and the winners of the six categories attracted considerable international attention.
In 2025, we will write the next chapter in this success story by once again presenting the Formnext Awards in six different categories.
Spotlight on your ideas
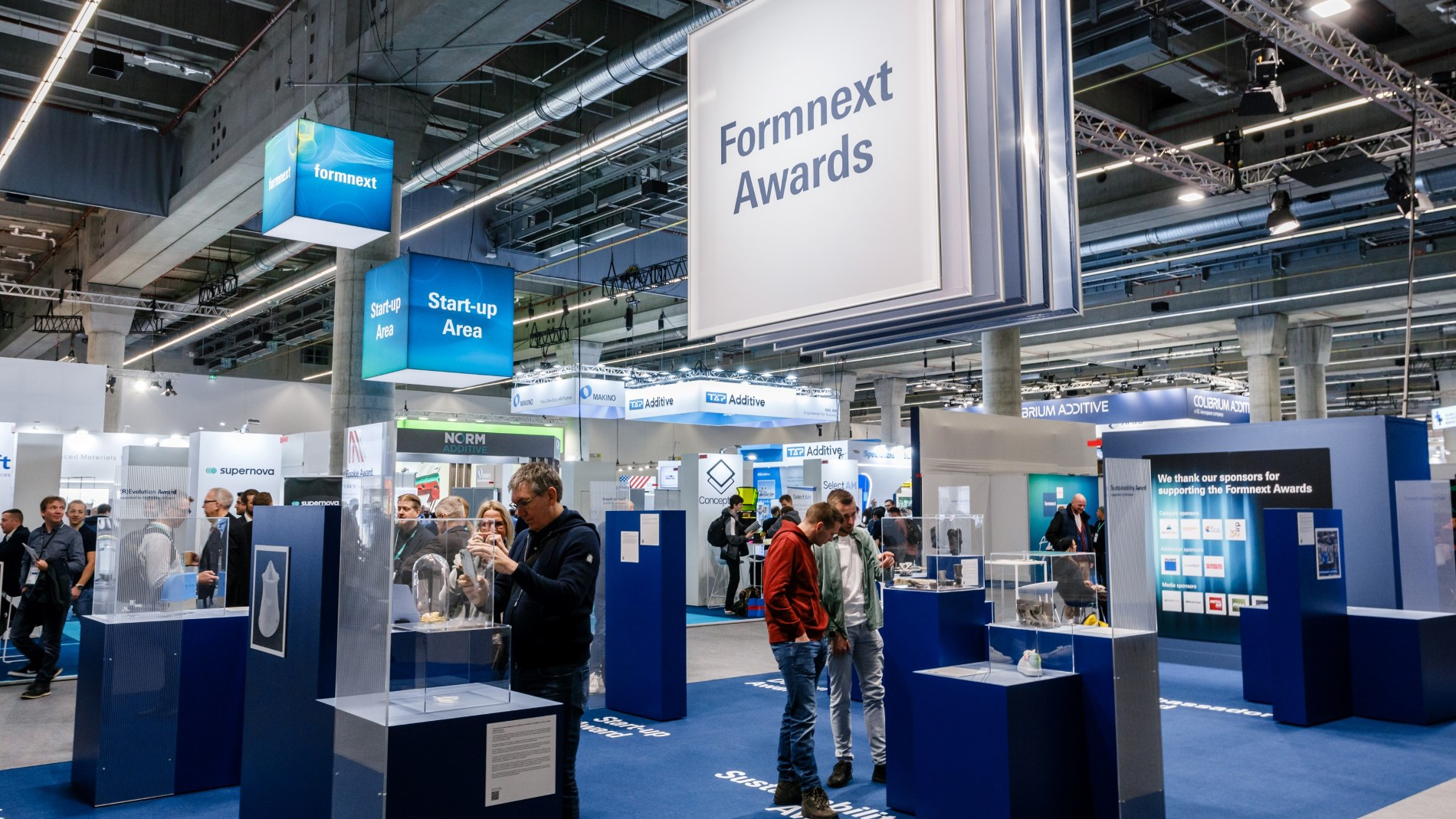
The finalists will be selected by the panel of judges, and the overall winners will be chosen at Formnext, with the help of a public vote. The winners will be presented at the award ceremony on the evening of Thursday 20 November 2025.
Formnext’s on-site and online visitors (online voting will start in september) will have the opportunity to vote for one of the finalists in each of the six categories and thus help determine the final result. In addition to the unique Formnext Award trophy designed by SUTOSUTO, the winners will also receive attractive prize packages.
Start your submission in the category you want to submit to.
Categories & submission criteria
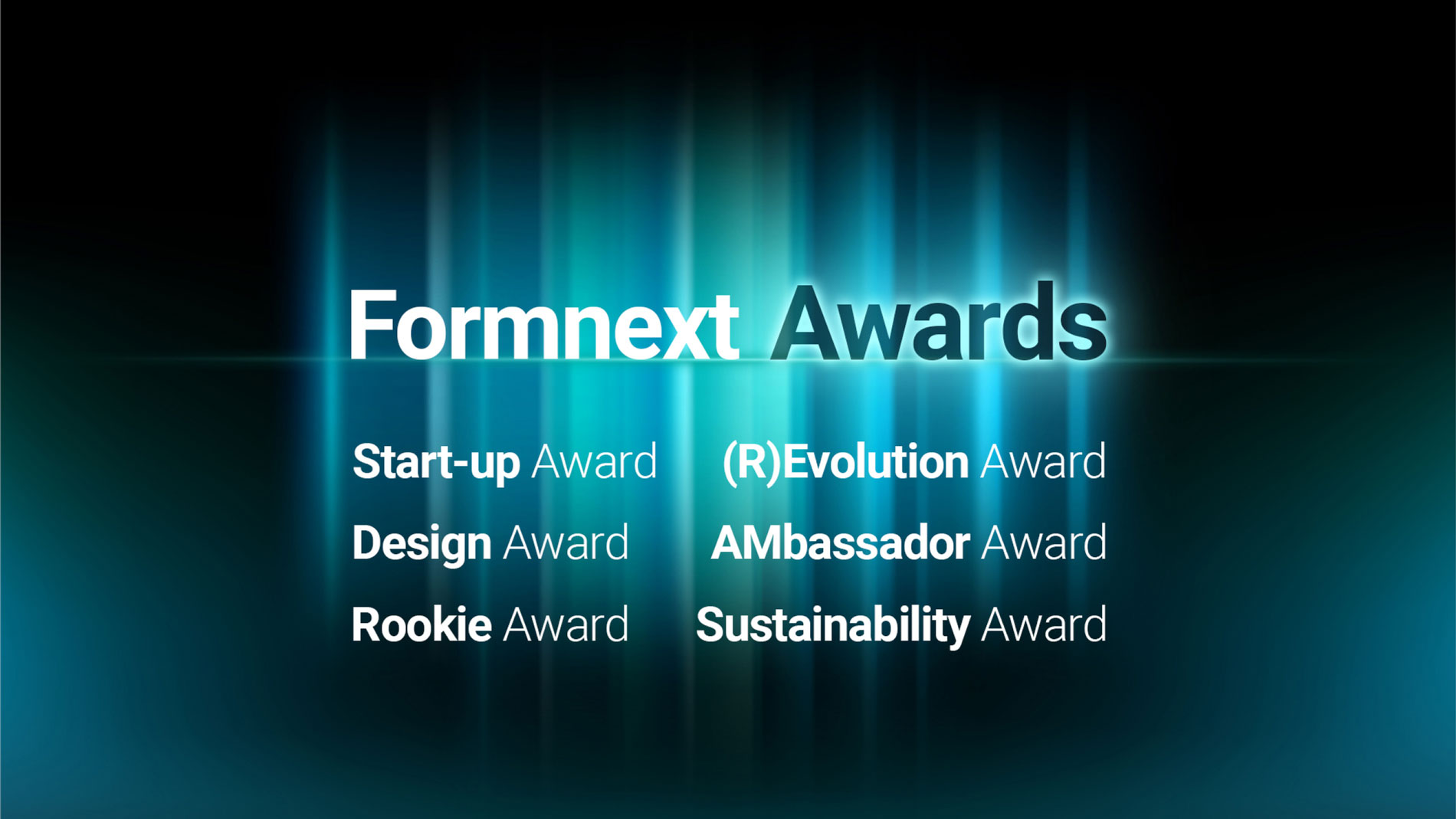
Enter the Formnext Awards, which will be conferred on aspiring young companies, future-oriented sustainable business models, and cutting-edge technologies, and much more. The Formnext Awards are looking for rookies, revolutionaries, and more – there is sure to be a category in which you can shine.
We look forward to your submissions and wish you the greatest success! If you have any questions, please contact Caroline Meier.
AMbassador Award
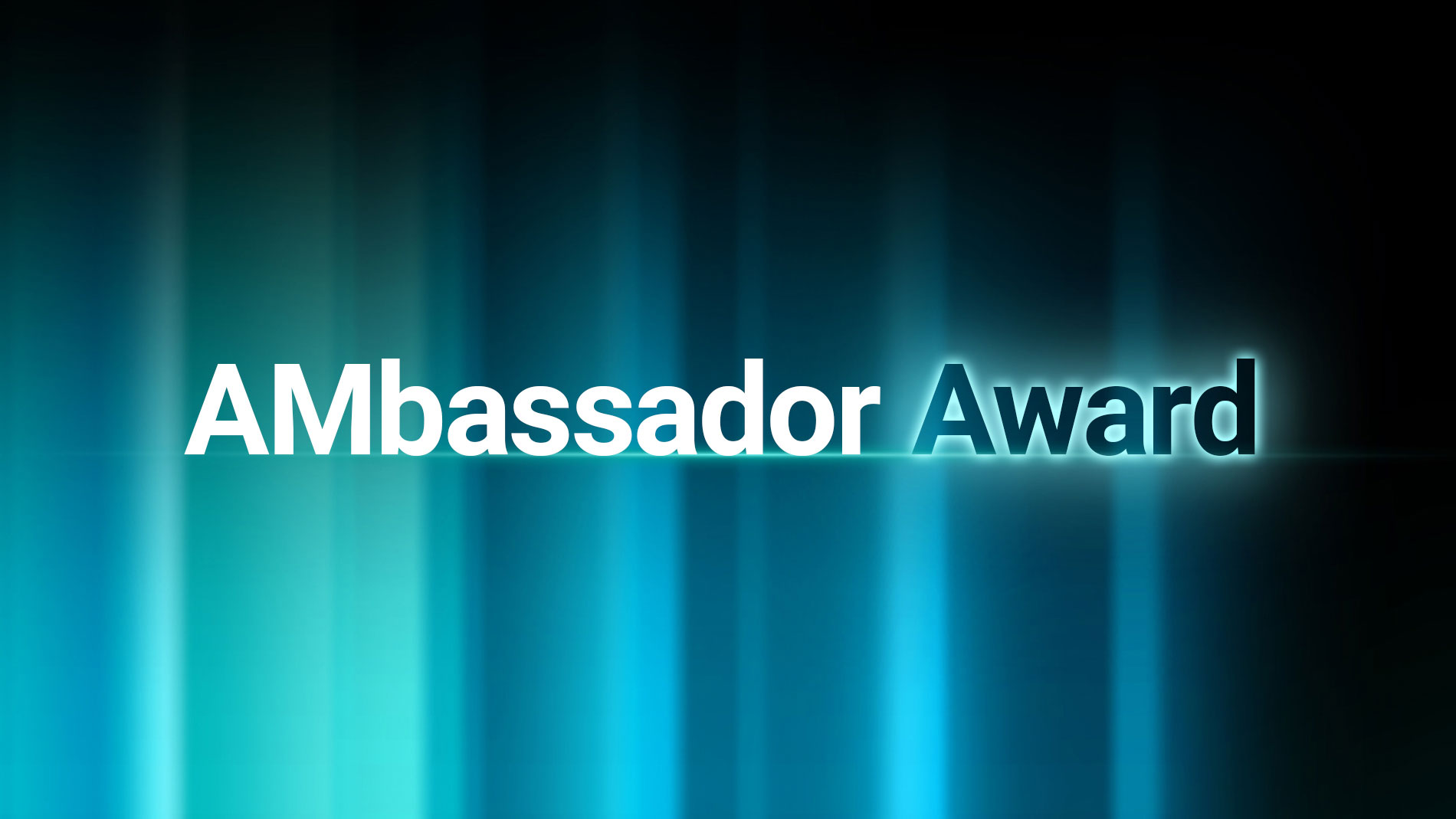
For a relatively new technology like Additive Manufacturing it is important to have individuals or initiatives that pave the way and speed up the adoption of the technology. The AMbassador Award honors individuals or organizations who provide real impact on the industry through training and educational programs or their personal advocacy.
Submission criteria
The following questions are submitted and evaluated by the jury:
- What is your connection to AM?
- Describe your project and which challenge does it tackle?
- Describe your projects technical excellence & level of novelty according to the following criteria: Practical applicability, technical focus, innovation of the concept, change process, actuality, novelty factor and relevance
- How do you personally or your project impact society or industry? (impact, range, focus on industry, impact on society, durability and effectiveness of your impact, educational excellence and impact on people)
What you can win
- Integration in all relevant Formnext marketing and communication activities worldwide
- Presentation of the project at the Formnext Awards special showcase and at the awards ceremony
- A 3D-printed award, designed by SUTOSUTO
- Cash and, if applicable, non-cash prizes
Submit your application with a short video (max. 1 minute) and convince the jury from your submission. Further details can be found in the online application form.
Deadline for submission: 31 August 2025
Design Award
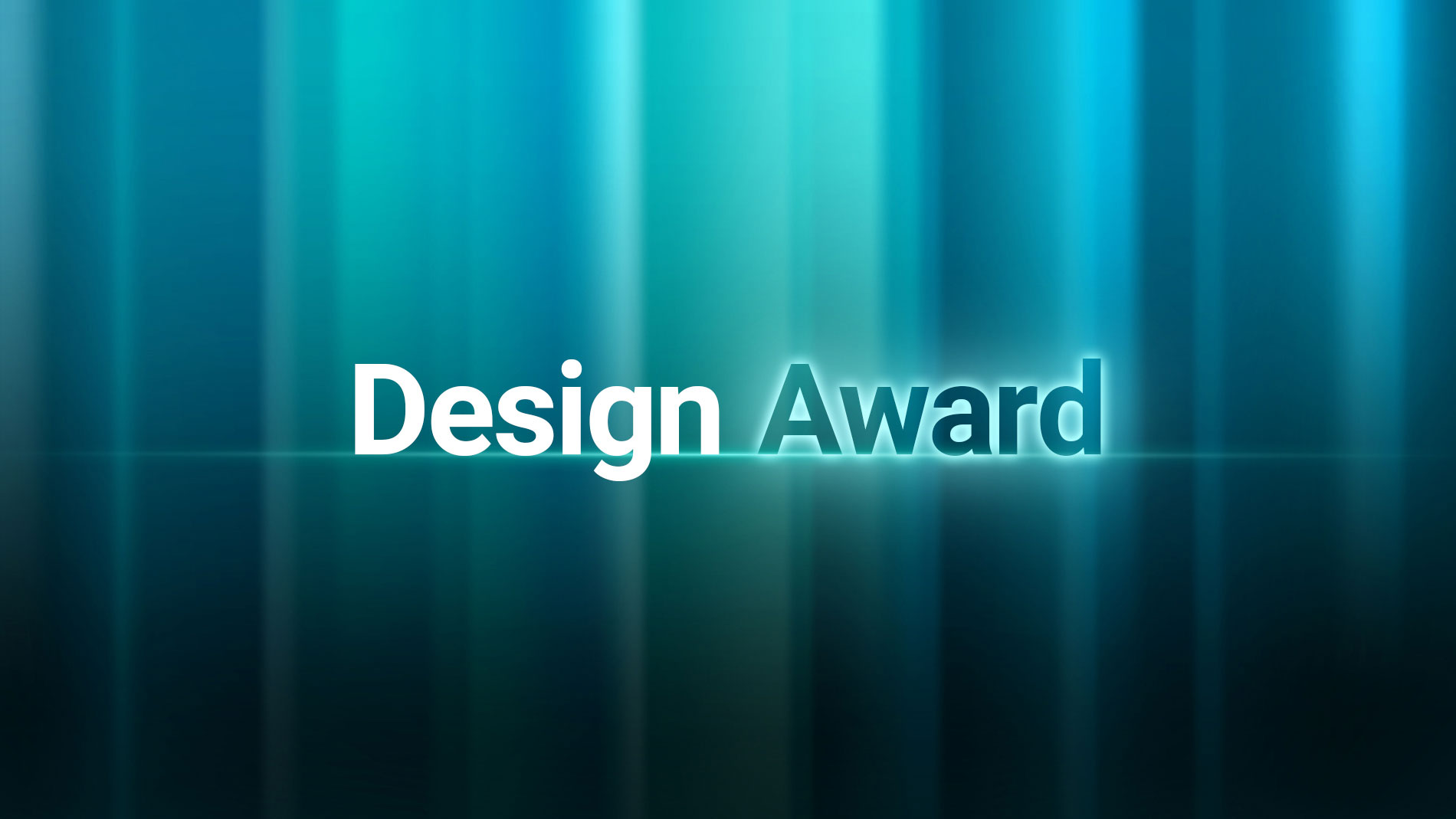
Additive Manufacturing provides an unrivaled degree of design freedom. To merely apply AM for aesthetical purposes, however, is short sighted. By identifying concepts that take into account aesthetical and functional aspects, the Design Award is bound to highlight the importance of smart and ingenious design for AM.
Submission criteria
The following questions are submitted and evaluated by the jury:
- Describe the design aesthetic and how it relates to the specific manufacturing process, style definition and performance of the design.
- How does Additive Manufacturing enable an innovative solution that would not be possible with other manufacturing methods?
- Explain how the design was engineered to optimize for the capabilities and limitations of the chosen Additive manufacturing process and materials.
- What are the economic advantages of using Additive Manufacturing to produce the design, compared to other fabrication methods?
- What is the social relevance of the design? How does it improve the lives of the users or benefit society at large?
What you can win
- Integration in all relevant Formnext marketing and communication activities worldwide
- Presentation of the project at the Formnext Awards special showcase and at the awards ceremony
- A 3D-printed award, designed by SUTOSUTO
- Cash and, if applicable, non-cash prizes
Submit your application with a short video (max. 1 minute) and convince the jury from your submission. Further details can be found in the online application form.
Deadline for submission: 31 August 2025
(R)Evolution Award
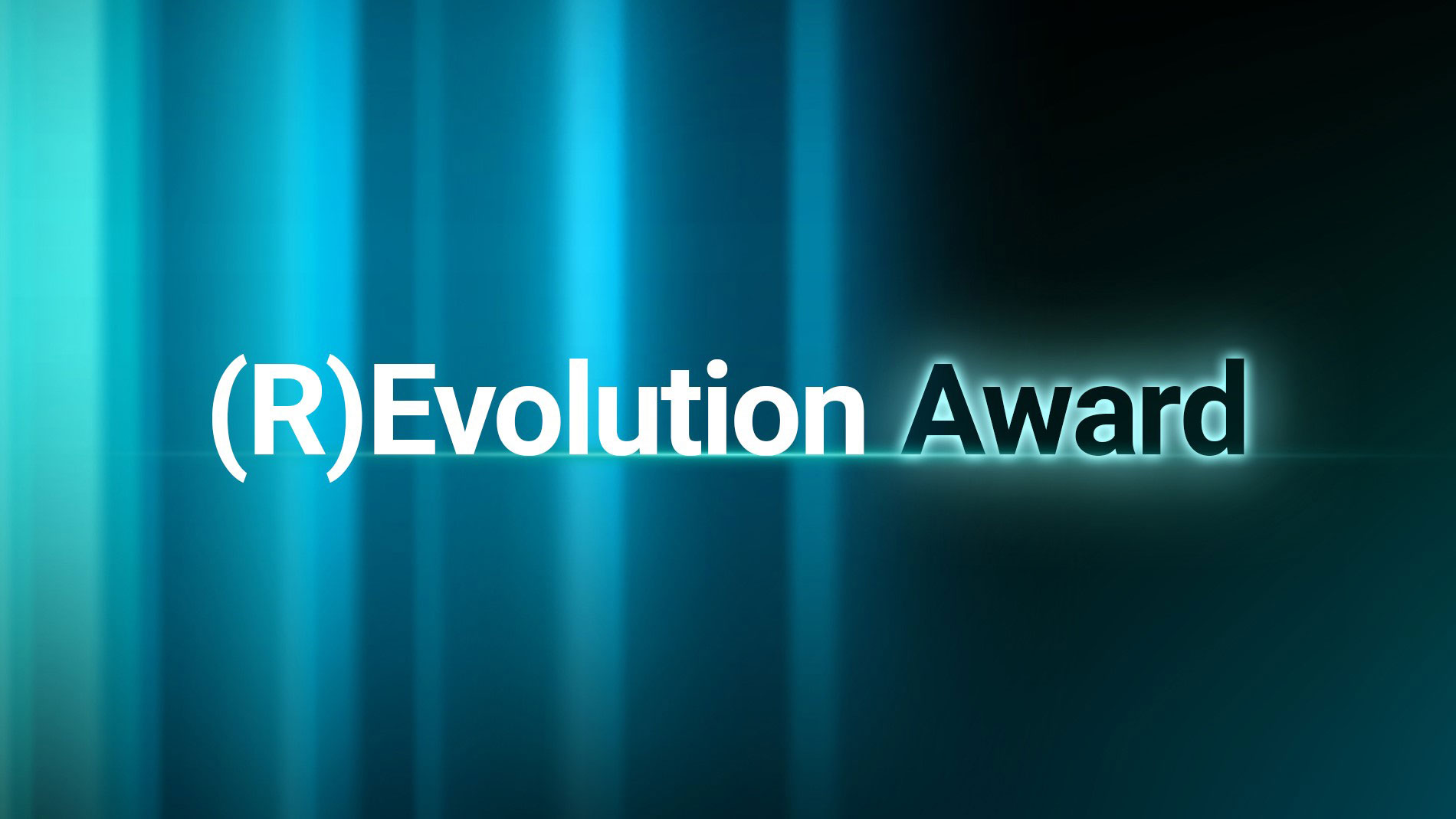
Additive technologies are developing fast and it is hard to keep track. Even exceptional products that are groundbreaking and advance the adoption of AM considerably may be missed by AM end users. In order to change that, we invite Formnext exhibitors to pitch their products and services to our jury. Stand out from the crowd and enter your submission today.
Submission criteria
The following questions are submitted and evaluated by the jury:
- What is the TRL of your product on a scale of 1-9? Please comment the given figure.
- Which impact will your new product/solution/tool have on:
- The general market and on your competitors?
- Your customers` way of working?
- Your customers` process chain?
- Your customers` lead time? (please prove with quantitative data)
- Your customers` product performance/quality?
- Where is your product revolutionary vs. an evolution? and why you think your product/solution/tool is revolutionary?
- How does it compare to:
- Similar solutions in the market?
- Conventional (subtractive) manufacturing solution?
- Do you have a use case demonstrating the business model for your product/solution/tool?
- Were you able to validate your product with a customer? (If so, please describe the customer feedback)
- What are the product`s shortcomings?
- What’s the environmental impact of this product/solution/tool?
- Which type of background should your ideal user have?
- How much time you think the user would need to dedicate to learn how to use your product/solution/tool to the fullest?
+++ Submissions are reserved for Formnext exhibitors. +++
What you can win
- Integration in all relevant Formnext marketing and communication activities worldwide
- Presentation of the project at the Formnext Awards special showcase and at the awards ceremony
- A 3D-printed award, designed by SUTOSUTO
- Non-cash prize
Submit your application with a short video (max. 1 minute) and convince the jury from your submission. Further details can be found in the online application form.
Deadline for submission: 31 August 2025
Rookie Award
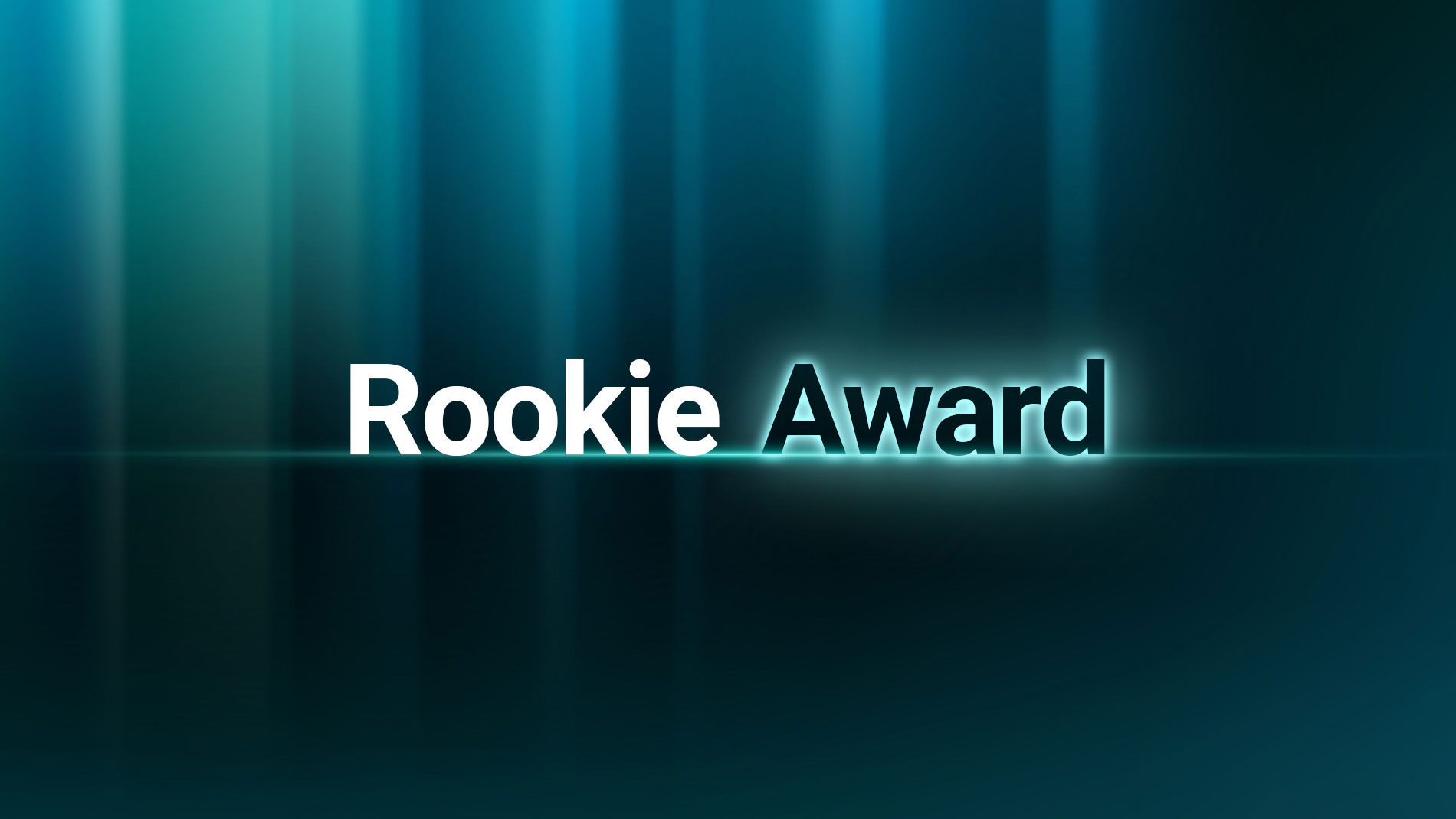
Do you have a convincing idea in the AM sector, but have not been able to get it off the ground? Are you looking for support and first contacts into the AM industry? Then the Rookie Award at Formnext is the right award to promote and develop your idea.
The Rookie Award is for bright minds,
- whose company has not been yet founded or was founded less than a year ago
- with a convincing business idea in the AM sector
- for whom no significant investment (with the exception of pre-seed funding, angel funding or government funding) has been made yet
Submission criteria
The following questions are submitted and evaluated by the jury:
- For whom are you creating value?
- For what value are your customers really willing to pay?
- Who are your key partners?
- What are the most important costs inherent in your business model?
- Which problem do you solve and how does your product solve it?
- Why is your team the right one to tackle the market?
- What kind of progress do you already have?
- What are your ambitions after winning the Rookie Award?
What you can win
- Integration in all relevant Formnext marketing and communication activities worldwide
- Presentation of the project at the Formnext Awards special showcase and at the awards ceremony
- Possibility to pitch your product at Formnext (for the 3 finalists)
- Company coaching via one of our jury members
- A 3D-printed award, designed by SUTOSUTO
Submit your application with a short video (max. 1 minute) and convince the jury from your submission. Further details can be found in the online application form.
Deadline for submission: 31 August 2025
Start-up Award
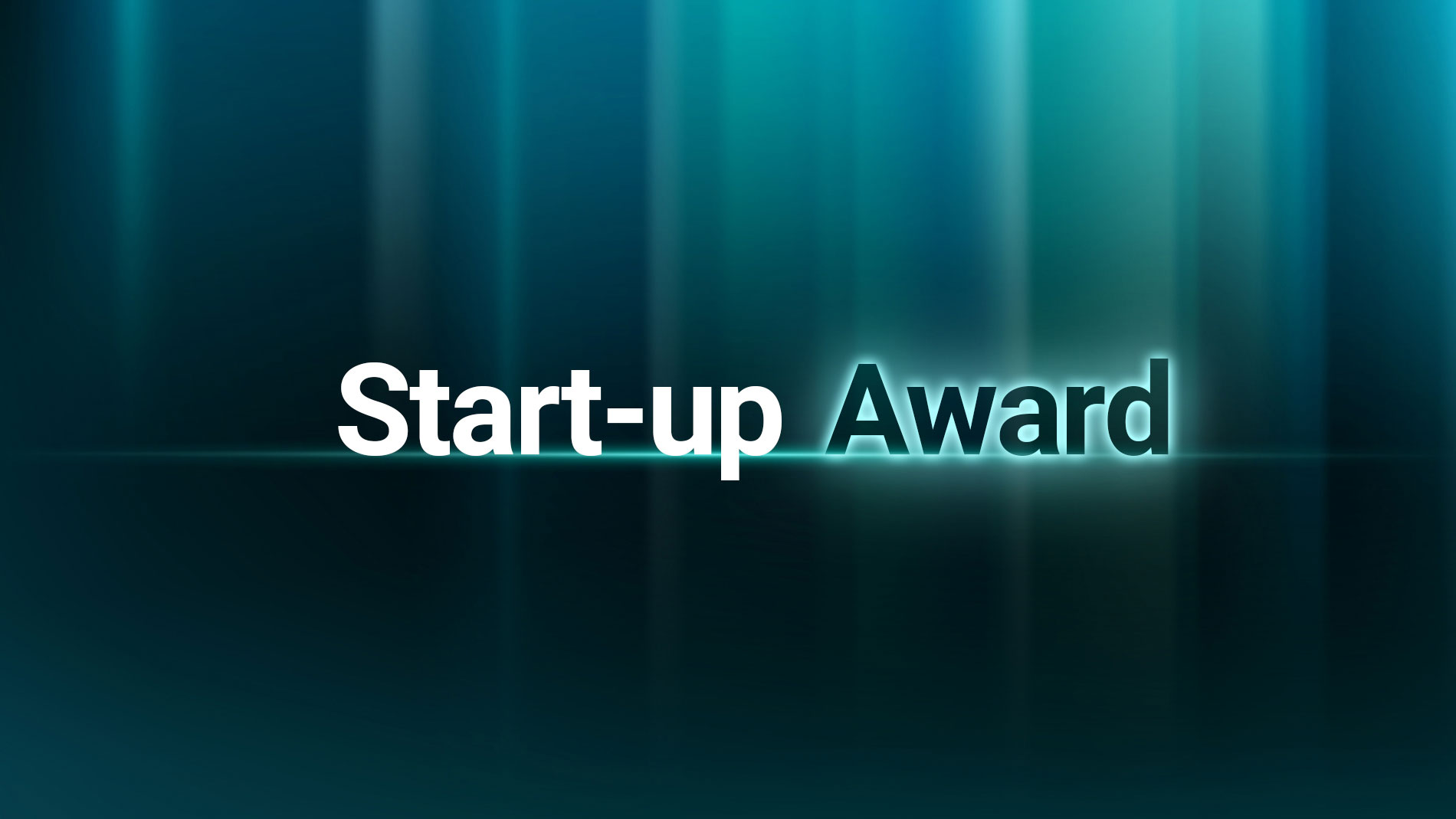
Set the course for the future of your start-up in the AM world, expand your network and convince potential investors. Winning the Start-up Award will give you a substantial boost and provide a big entry in the world of AM.
For inspiring young companies with viable business models, that…
- were founded within the last five years
- annual turnover must not exceed 10 million euros
- have developed at least one marketable product (sample, prototype or beta version) that corresponds to the list of approved product groups in order to exhibit at Formnext
Submission criteria
The following questions are submitted and evaluated by the jury:
- Which problem do you solve and how does your product solve it?
- On which customer segment do you focus and how do you approach them?
- Who are your competitors and what can you do better than them?
- What's your business model? How do you earn money? Which partners are involved?
- Why is your team the right one to tackle the market?
What you can win
- 5 finalists will receive a stand in the Start-up Area during Formnext
- 1 winner will receive a cash prize
- Inclusion of your start-up company in all relevant and global marketing and communication activities at Formnext
- Pitch opportunity with a short product presentation at Formnext
- Company coaching by one of our jury members
- A 3D-printed award, designed by SUTOSUTO
Submission Start-up Award: Deadline for submission was 31 July 2025
Sustainability Award
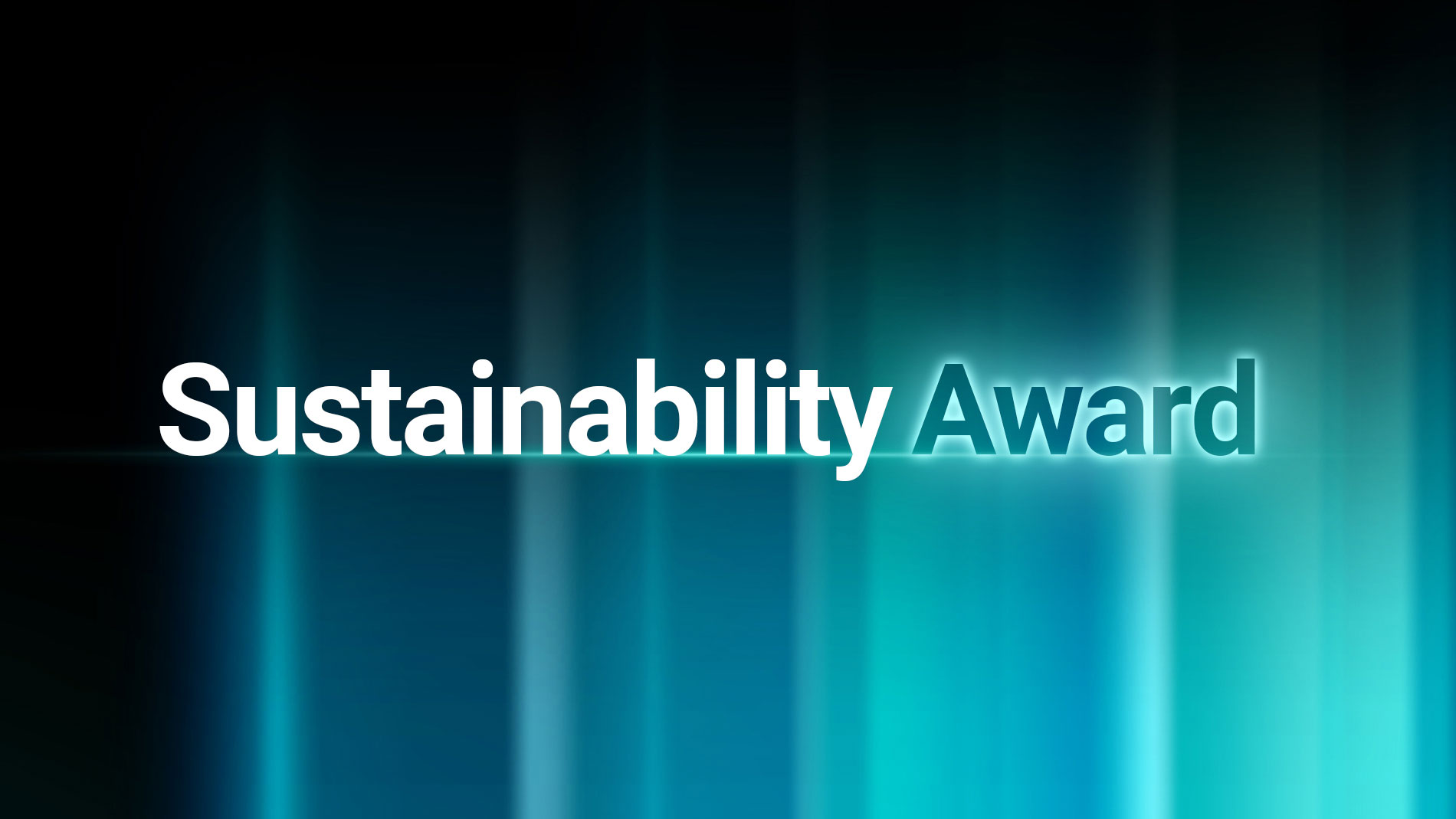
The AM technology is often referred to as a sustainable technology. This may be true in some cases. The real value may, however, only be found during the product’s life cycle. The Sustainability Award will assess exactly that. Not only the production phase, but the full life cycle of AM use cases and products.
The special value of this award:
- Direct combination of AM and sustainability using an LCA (Life Cycle Assessment),
- not limited to individual materials and manufacturing processes
- Evaluation of overall use case
Submission criteria
The following questions are submitted and evaluated by the jury:
- Describe your use case in general (material/industry sector and field of use/market size and potential growth rate/scalability/transferability to other market segments).
- What is the challenge that your project is tackling?
- What is the USP of your project?
- Describe the life cycle assessment of your use case along the process chain using an LCA matrix.
- Please provide an analysis that illustrates the full business case and analyzes the impact of the AM implementation strategy beyond the part-by-part comparison.
- Which of the 17 UN sustainable development goals (SDGs) does your use case address?
What you can win
- Integration in all relevant Formnext marketing and communication activities worldwide
- Presentation of the project at the Formnext Awards special showcase and at the awards ceremony
- A 3D-printed award, designed by SUTOSUTO
- Cash and, if appicable, non-cash prizes
The basis of your application is a questionnaire, which is based on the questions of an LCA matrix and a business case analysis. Details on the requirements and questions that the analysis should answer, as well as an example, can be found in the online application form.
Submit your application with a short video (max. 1 minute) and convince the jury from your submission. Further details can be found in the online application form.
Deadline for submission: 31 August 2025
Contact & sponsorship
Do you want to pave the way for young innovative ideas in the AM world? Then become a sponsor of the Formnext Awards 2025 – we still have space on the sponsor wall! You can find all the details here:
If you have any questions about taking part in the Formnext Awards or the sponsorship options, feel free to reach out: