Die Formnext gibt Ihren Ideen mit den Formnext Awards die Bühne, die sie verdienen!
Zum Hintergrund
Die AM-Welt ist geprägt von talentierten, motivierten und begabten Menschen, die die Technologie und somit die ganze Branche vorantreiben. Sie haben es verdient, dass ihre Ideen die entsprechende Aufmerksamkeit erhalten und ins Rampenlicht gerückt werden – für die Branche und für die zukunftsfähige Weiterentwicklung moderner Fertigung.
Auf der letzten Formnext hatten das neue Awardkonzept sowie die Gewinner der sechs Kategorien international starke Beachtung gefunden.
2025 wird die Formnext diese Erfolgsgeschichte weiterschreiben und mit den Formnext Awards wieder in sechs verschiedenen Kategorien auszeichnen.
Ihre Bühne auf der Formnext
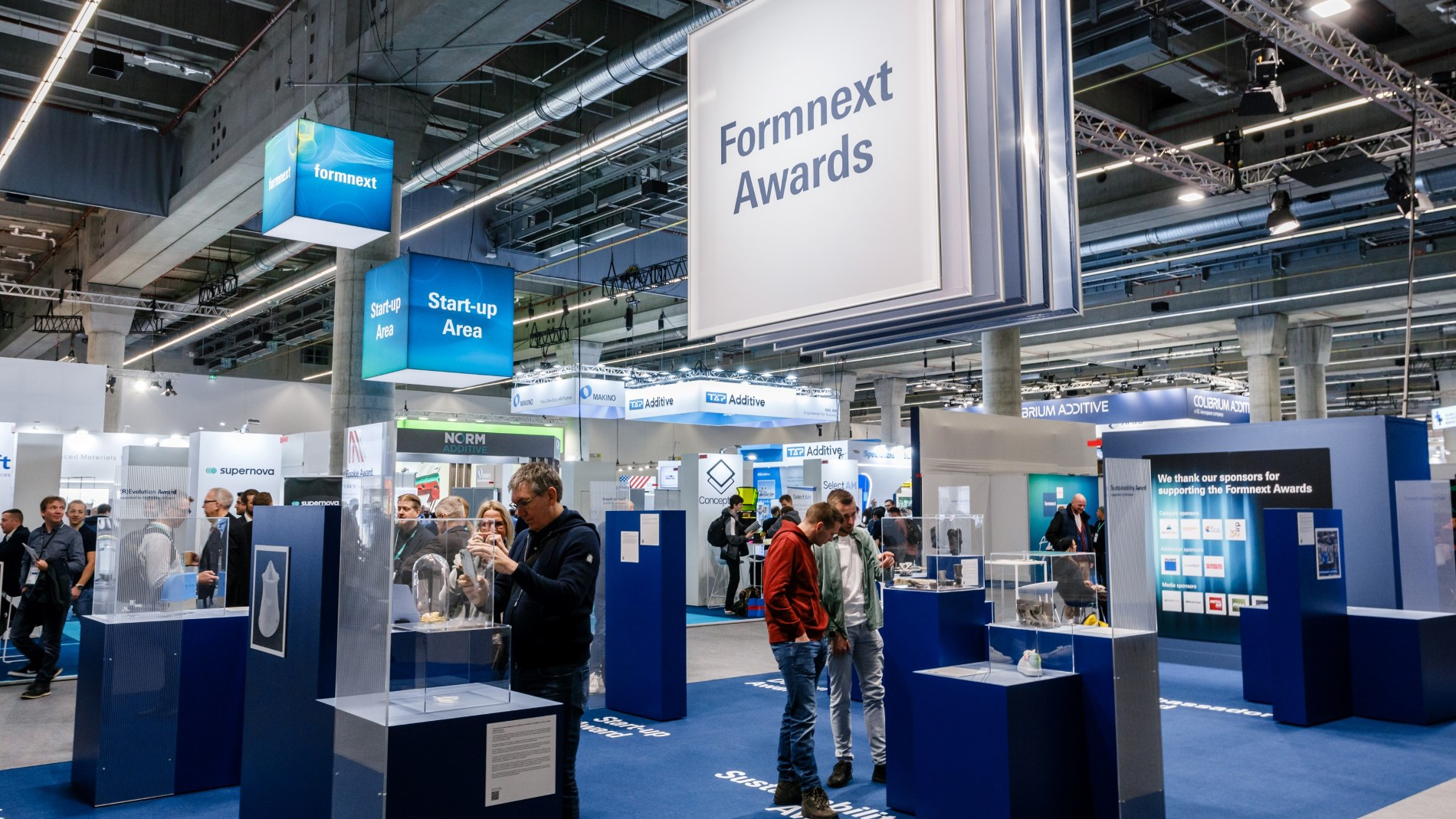
Aus den durch die Jury ausgewählten Finalisten werden auf der Formnext, mit der Unterstützung des Public Voting, schließlich die Gewinner gekürt. Die Sieger werden im Rahmen der Award-Verleihung am Donnerstagabend, 20.11.2025 präsentiert.
Beim Public Voting haben sowohl die Besucher der Formnext vor Ort sowie online ab Oktober die Möglichkeit, in jeder der sechs Kategorien einem der Finalisten ihre Stimme zu geben und so das Endergebnis mitzubestimmen. Neben der anspruchsvoll gestalteten Formnext-Award-Trophäe erhalten die Sieger Geld- und/oder Sachpreise (z.B. ein Unternehmenscoaching).
Kategorien & Teilnahmeoptionen
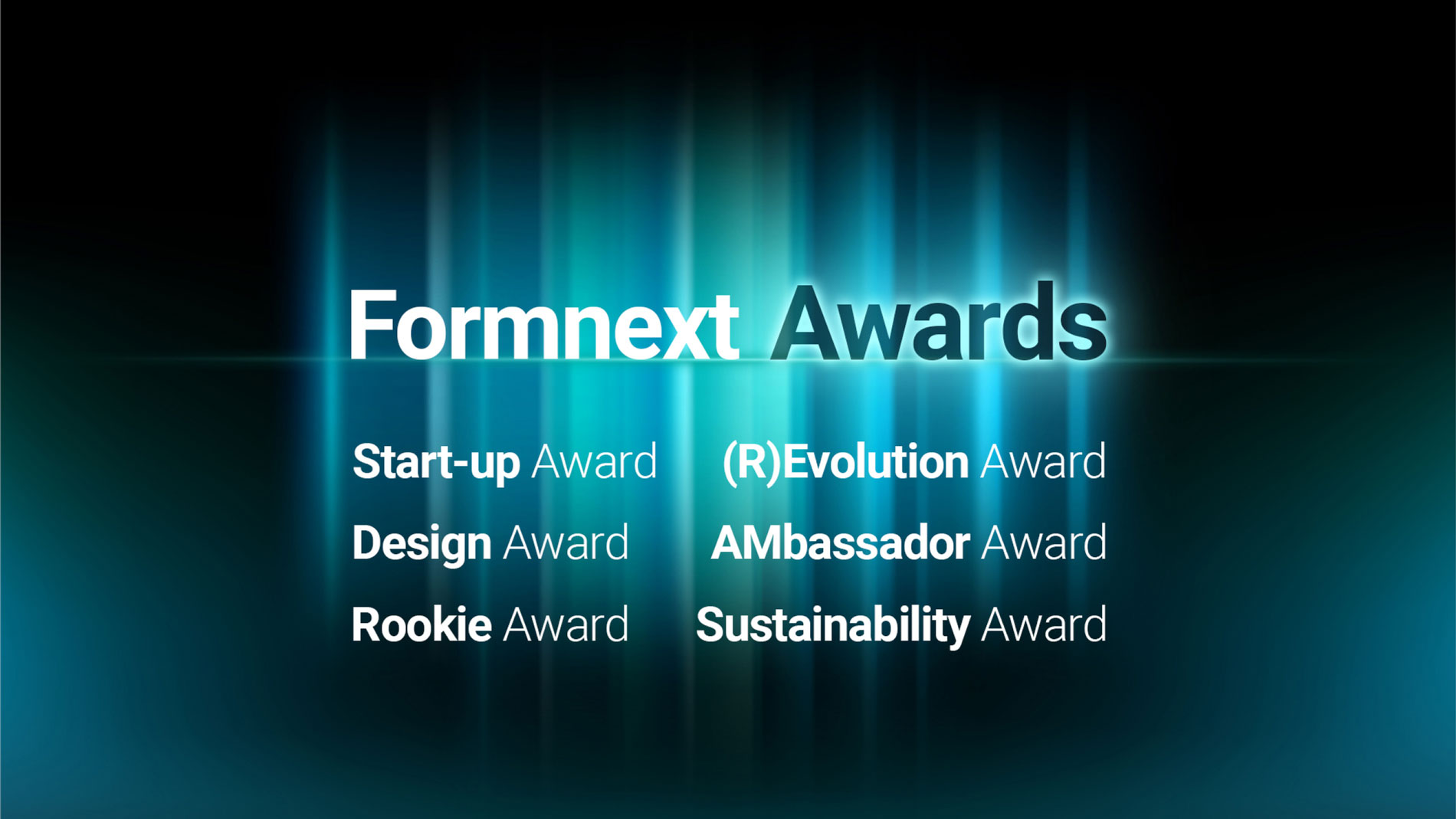
Die Formnext Awards prämieren auch 2025 in sechs Kategorien u.a. aufstrebende junge Unternehmen, zukunftsweisende nachhaltige Geschäftsmodelle und progressive Technologien.
AMbassador Award
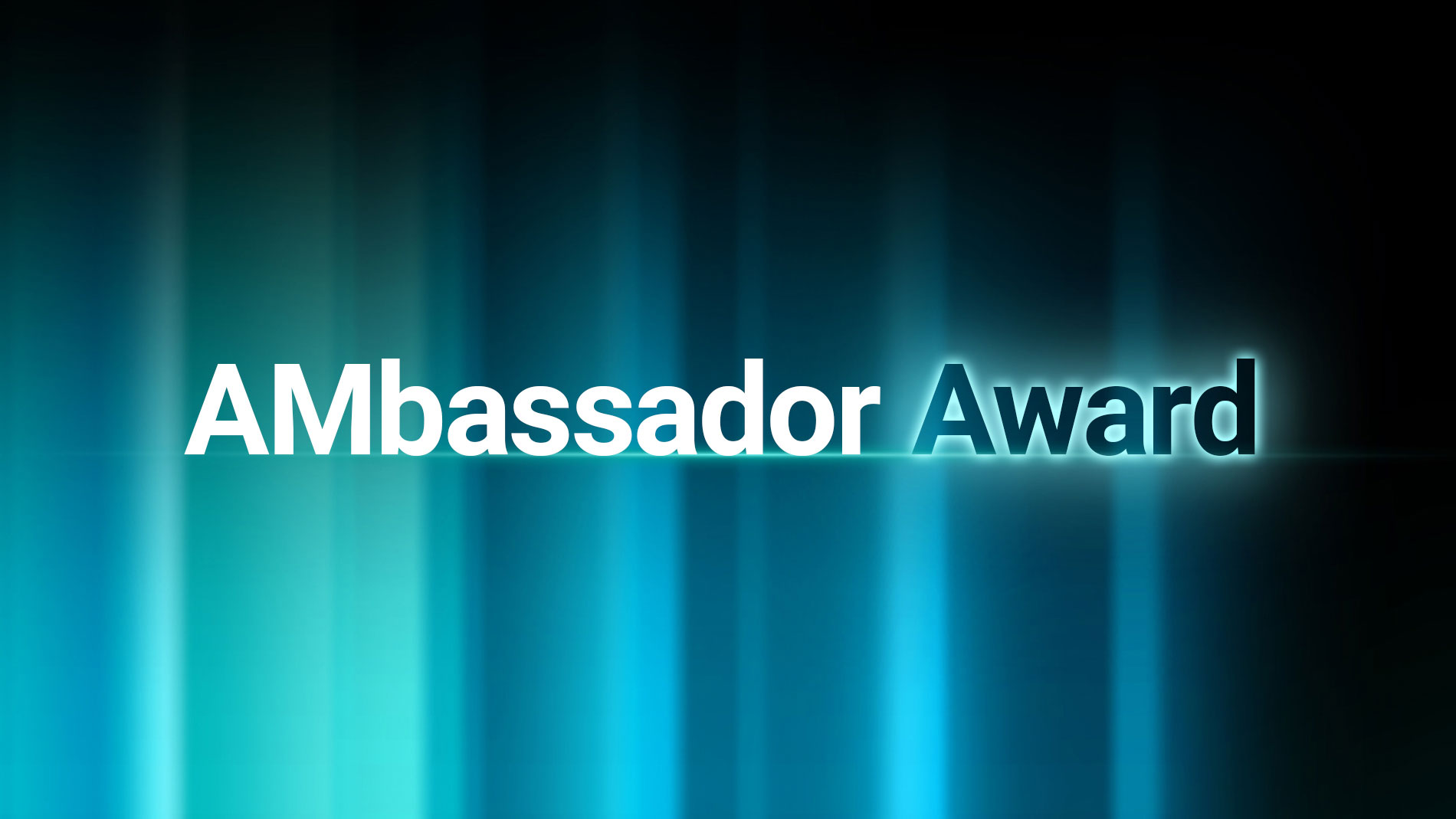
Für eine vergleichsweise neue Technologie wie Additive Manufacturing ist es wichtig, dass es Personen oder Initiativen gibt, die den Weg bereiten und die Einführung von Technologien beschleunigen. Der AMbassador Award ehrt herausragende Einzelpersonen oder Organisationen, die durch innovative Trainings- und Ausbildungsansätze, Projekte oder ihre persönliche Fürsprache einen einzigartigen Einfluss auf die Branche und die Anwender nehmen.
Die Kriterien
Folgende Fragestellungen werden bei der Einreichung abgefragt und von der Jury bewertet:
- Wie ist Ihre Verbindung zu AM?
- Beschreiben Sie Ihr Projekt und welche Herausforderung stellt es dar?
- Beschreiben Sie die technische Exzellenz und den Grad der Neuheit Ihres Projekts nach folgenden Kriterien: Praktische Anwendbarkeit, technischer Schwerpunkt, Innovation des Konzepts, Veränderungsprozess, Aktualität, Neuheitsfaktor und Relevanz
- Wie wirken Sie persönlich oder Ihr Projekt auf die Gesellschaft oder die Industrie (Auswirkung, Reichweite, Fokus auf die Industrie, Auswirkung auf die Gesellschaft, Dauerhaftigkeit und Wirksamkeit Ihres Einflusses, Pädagogische Exzellenz und Auswirkungen auf die Menschen)?
Das Preispaket
- Einbindung in alle relevanten und weltweiten Marketing- und Kommunikationsaktivitäten der Formnext
- Präsentation des Projektes auf der Formnext Awards Sonderschau und bei der Preisverleihung
- Ein 3D-gedruckter Award, gestaltet von SUTOSUTO
- Vorstellung des Projekts in unserem Rahmenprogramm am Karrieretag
- Geld- und Sachpreise
Leider ist die Einreichungsphase bereits vorüber. Details zu den Finalisten, ihren Ideen und wie Sie für Ihre Favoriten voten können, erfahren Sie hier Anfang Oktober.
Design Award
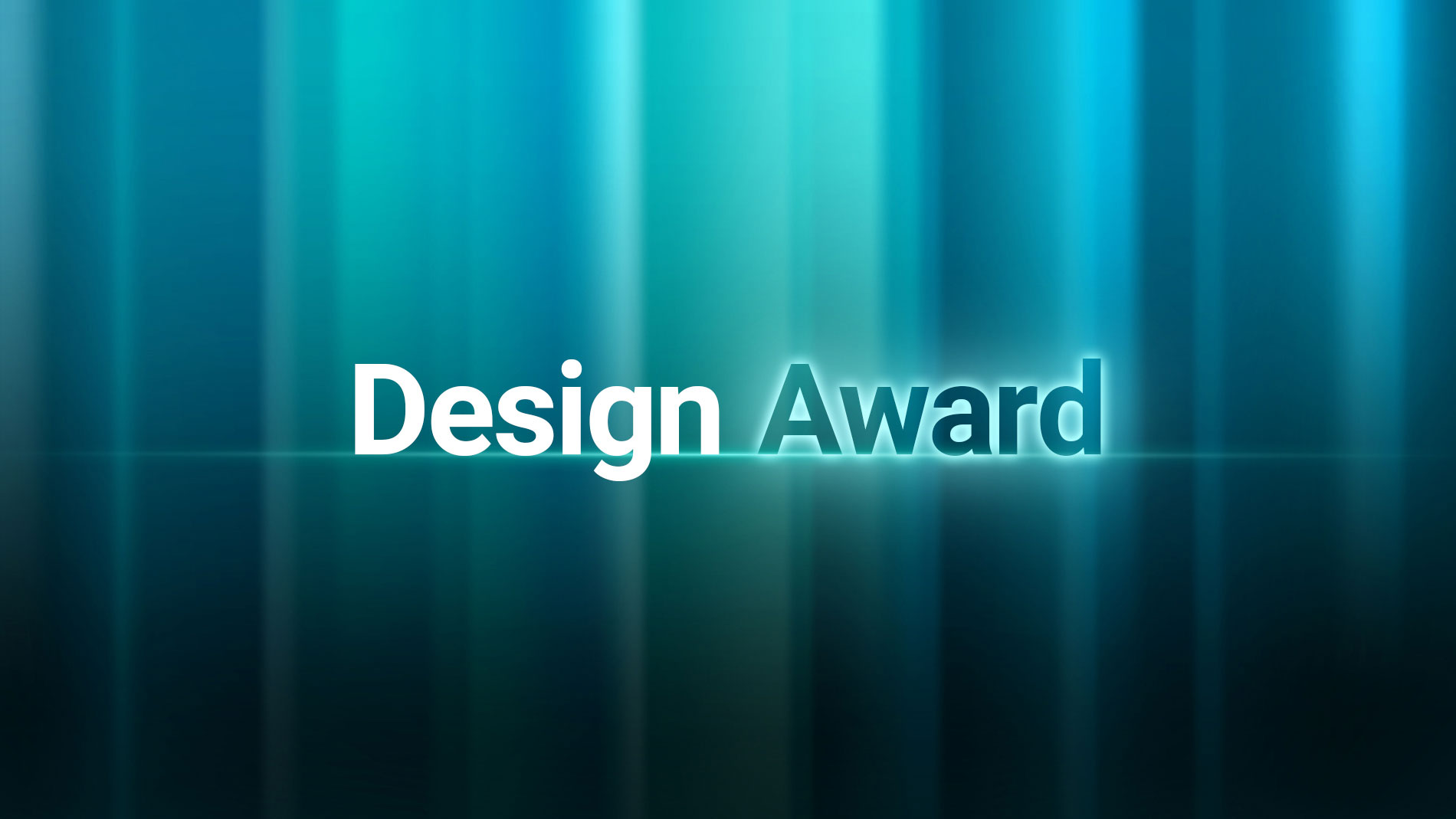
Additive Manufacturing bietet einen unvergleichlichen Grad an Gestaltungsfreiheit. AM nur für ästhetische Zwecke zu nutzen, schöpft nicht das volle Potential der Technologie aus. Durch die Identifizierung von Konzepten, die sowohl ästhetische als auch funktionale Aspekte berücksichtigen, hebt der Design Award die Bedeutung von intelligentem und einfallsreichem Design für AM hervor.
Die Kriterien
Folgende Fragestellungen werden bei der Einreichung abgefragt und von der Jury bewertet:
- Beschreiben Sie die Ästhetik des Designs und wie sie sich auf den spezifischen Herstellungsprozess, die Stildefinition und die Leistung des Entwurfs bezieht.
- Wie ermöglicht die Additive Fertigung eine innovative Lösung, die mit anderen Fertigungsverfahren nicht möglich wäre?
- Erläutern Sie, inwiefern das Design so gestaltet wurde, dass es die Möglichkeiten und Grenzen des gewählten additiven Fertigungsverfahrens und der Materialien optimal ausnutzt.
- Welche wirtschaftlichen Vorteile bietet die Verwendung der Additiven Fertigung im Vergleich zu anderen Fertigungsverfahren?
- Welche gesellschaftliche Bedeutung hat Ihr Design? Wie verbessert es das Leben der Nutzer oder kommt der Gesellschaft insgesamt zugute?
Das Preispaket
- Einbindung in alle relevanten und weltweiten Marketing- und Kommunikationsaktivitäten der Formnext
- Präsentation des Projektes auf der Formnext Awards Sonderschau und bei der Preisverleihung
- Ein 3D-gedruckter Award, gestaltet von SUTOSUTO
- Geld- und Sachpreise
Leider ist die Einreichungsphase bereits vorüber. Details zu den Finalisten, ihren Ideen und wie Sie für Ihre Favoriten voten können, erfahren Sie hier Anfang Oktober.
(R)Evolution Award
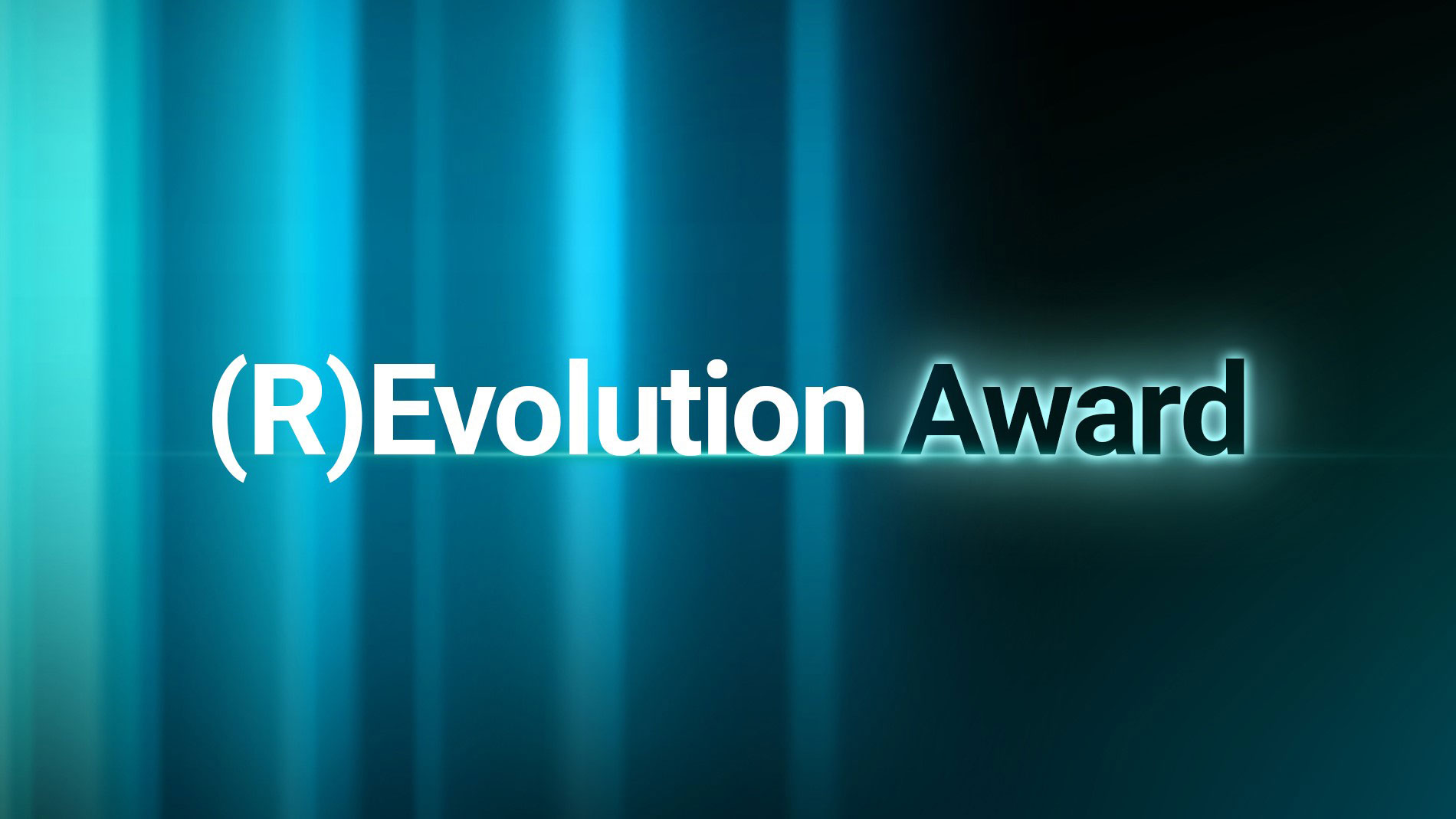
Additive Technologien entwickeln sich schnell und es ist schwer, den Überblick zu behalten. Selbst außergewöhnliche Produkte, die bahnbrechend sind und die Industrialisierung von AM erheblich vorantreiben, können von AM-Endnutzern übersehen werden. Um das zu ändern, laden wir Formnext Aussteller ein, ihre Produkte und Dienstleistungen unserer Jury vorzustellen. Heben Sie sich von der Masse ab und reichen Sie Ihre Bewerbung noch heute ein.
Die Kriterien
Folgende Fragestellungen werden bei der Einreichung abgefragt und von der Jury bewertet:
- Wie hoch ist der TRL (Technologiereifegrad) Ihres Produkts auf einer Skala von 1-9? Bitte kommentieren Sie die angegebene Zahl.
- Welche Auswirkungen wird Ihr neues Produkt/Lösung/Werkzeug haben, auf…
- den allgemeinen Markt und bei Ihren Konkurrenten?
- die Arbeitsweise Ihrer Kunden?
- die Prozesskette Ihrer Kunden?
- die Vorlaufzeit Ihrer Kunden? (bitte mit quantitativen Daten belegen)
- die Leistung/Qualität der Produkte Ihrer Kunden?
- Wo ist Ihr Produkt revolutionär im Vergleich zu einer Evolution? Warum denken Sie, dass Ihr Produkt/Lösung/Werkzeug revolutionär ist?
- Wie sieht es im Vergleich aus zu…
- ähnlichen Lösungen auf dem Markt?
- einer konventionellen (subtraktiven) Fertigungslösung?
- Haben Sie einen Anwendungsfall, der das Geschäftsmodell für Ihr Produkt/Ihre Lösung/Ihr Werkzeug demonstriert?
- Konnten Sie Ihr Produkt bei einem Kunden validieren? (Wenn ja, beschreiben Sie bitte das Kundenfeedback)
- Was sind die Schwachstellen des Produkts?
- Welche Umweltauswirkungen hat dieses Produkt/diese Lösung/dieses Werkzeug?
- Welche Art von Hintergrund sollte Ihr idealer Anwender haben?
- Wie viel Zeit wird der Nutzer Ihrer Meinung nach aufwenden müssen, um zu lernen, wie er Ihr Produkt/Ihre Lösung/Ihr Werkzeug optimal nutzen kann?
+++ Einreichungen sind Formnext Ausstellern vorbehalten. +++
Das Preispaket
- Einbindung in alle relevanten und weltweiten Marketing- und Kommunikationsaktivitäten der Formnext
- Präsentation des Projektes auf der Formnext Awards Sonderschau und bei der Preisverleihung
- Ein 3D-gedruckter Award, gestaltet von SUTOSUTO
- Sachpreis
Leider ist die Einreichungsphase bereits vorüber. Details zu den Finalisten, ihren Ideen und wie Sie für Ihre Favoriten voten können, erfahren Sie hier Anfang Oktober.
Rookie Award
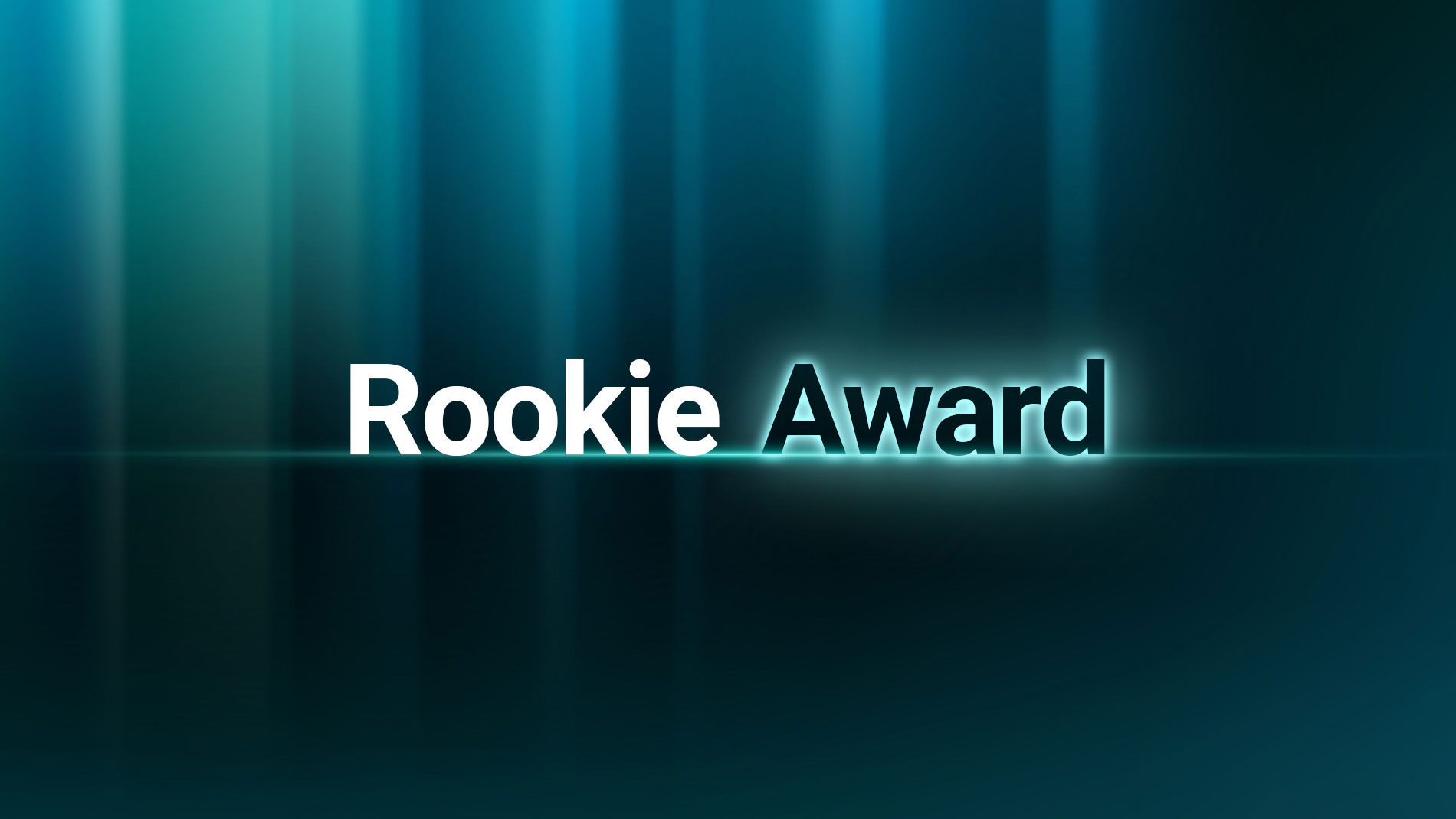
Haben Sie eine überzeugende Idee im AM-Sektor, konnten sie aber bisher nicht umsetzen? Suchen Sie Unterstützung und erste Kontakte in die AM-Branche? Dann ist der Rookie Award auf der Formnext genau das Richtige, um Ihre Idee voranzubringen und weiterzuentwickeln.
Für kluge Köpfe,
- deren Firma noch nicht gegründet oder vor weniger als einem Jahr gegründet wurde
- mit einer überzeugenden Geschäftsidee im AM-Sektor
- für die noch keine nennenswerten Investitionen (außer: Pre-Seed Funding , Angel-Finanzierung oder Staatliche Finanzierung) getätigt worden sind
- Minimales existenzfähiges Produkt ist erforderlich (Foto)
Die Kriterien
Folgende Fragestellungen werden bei der Einreichung abgefragt und von der Jury bewertet:
- Für wen schaffen Sie Mehrwert?
- Für welchen Wert sind Ihre Kunden wirklich bereit zu zahlen?
- Wer sind Ihre wichtigsten Partner?
- Was sind die wichtigsten Kosten, die mit Ihrem Geschäftsmodell verbunden sind?
- Welches Problem lösen Sie und wie löst Ihr Produkt dieses Problem?
- Warum ist Ihr Team das richtige, um den Markt anzugehen?
- Welche Art von Fortschritt haben Sie bereits erzielt?
- Welche Ambitionen haben Sie nach dem Gewinn des Rookie Award?
Das Preispaket
- Einbindung in alle relevanten und weltweiten Marketing- und Kommunikationsaktivitäten der Formnext
- Präsentation des Projektes auf der Formnext Awards Sonderschau und bei der Preisverleihung
- Pitch-Möglichkeit mit kurzer Produktvorstellung auf der Formnext (für die 3 Finalisten)
- Unternehmenscoaching über eines unserer Jurymitglieder
- Ein 3D-gedruckter Award, gestaltet von SUTOSUTO
Leider ist die Einreichungsphase bereits vorüber. Details zu den Finalisten, ihren Ideen und wie Sie für Ihre Favoriten voten können, erfahren Sie hier Anfang Oktober.
Start-up Award
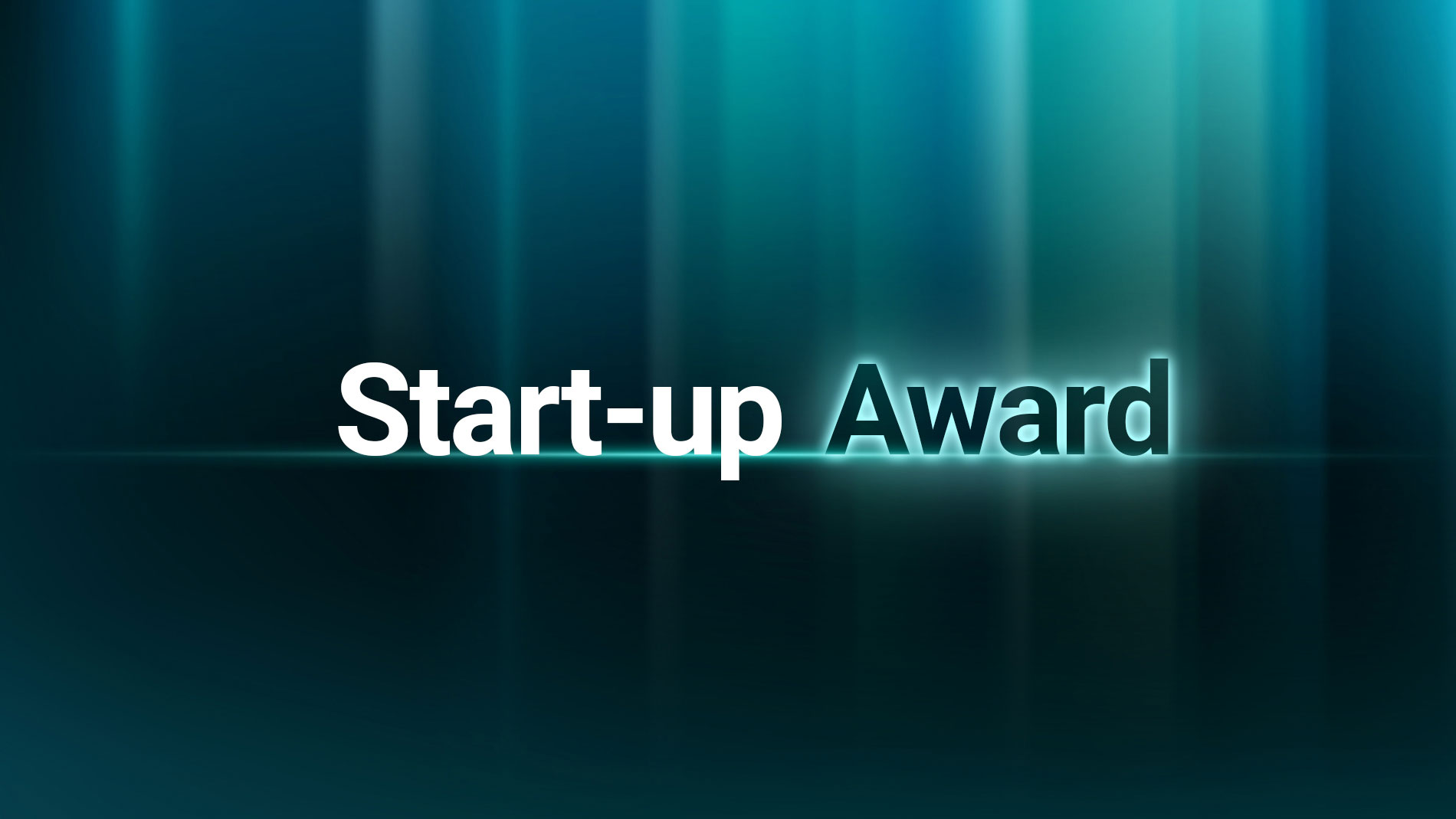
Gestalten Sie die Zukunft Ihres Start-ups in der AM-Welt, erweitern Sie Ihr Netzwerk und begeistern Sie potenzielle Investoren. Der Gewinn des Start-up Awards gibt Ihnen einen kräftigen Schub und öffnet Ihnen die Tür zur AM-Welt.
Für junge, inspirierende Unternehmen mit umsetzbaren Geschäftsmodellen…
- die innerhalb der letzten fünf Jahre gegründet wurden
- deren Jahresumsatz 10 Millionen Euro nicht überschreitet
- die mindestens ein marktfähiges Produkt (Muster, Prototyp oder Beta-Version) entwickelt haben, das der Liste der zugelassenen Formnext-Produktgruppen entspricht
Die Kriterien
Folgende Fragestellungen werden bei der Einreichung abgefragt und von der Jury bewertet:
- Welches Problem lösen Sie und wie lösen Sie es mit Ihrem Produkt?
- Auf welches Kundensegment konzentrieren Sie sich und wie sprechen Sie es an?
- Wer sind Ihre Konkurrenten und was können Sie besser machen als sie?
- Was ist Ihr Geschäftsmodell? Wie verdienen Sie Geld? Welche Partner sind involviert?
- Warum ist Ihr Team das richtige, um den Markt anzugehen?
Das Preispaket
- 5 Finalisten erhalten einen Stand auf der Start-up Area
- 1 Gewinner erhält einen Geldpreis
- Einbindung Ihres Start-up Unternehmens in alle relevanten und weltweiten Marketing- und Kommunikationsaktivitäten der Formnext
- Pitch-Möglichkeit mit kurzer Produktvorstellung auf der Formnext
- Unternehmenscoaching über eines unserer Jurymitglieder
- Ein 3D-gedruckter Award, gestaltet von SUTOSUTO
Leider ist die Einreichungsphase bereits vorüber. Details zu den Finalisten, ihren Ideen und wie Sie für Ihre Favoriten voten können, erfahren Sie hier Anfang Oktober.
Sustainability Award
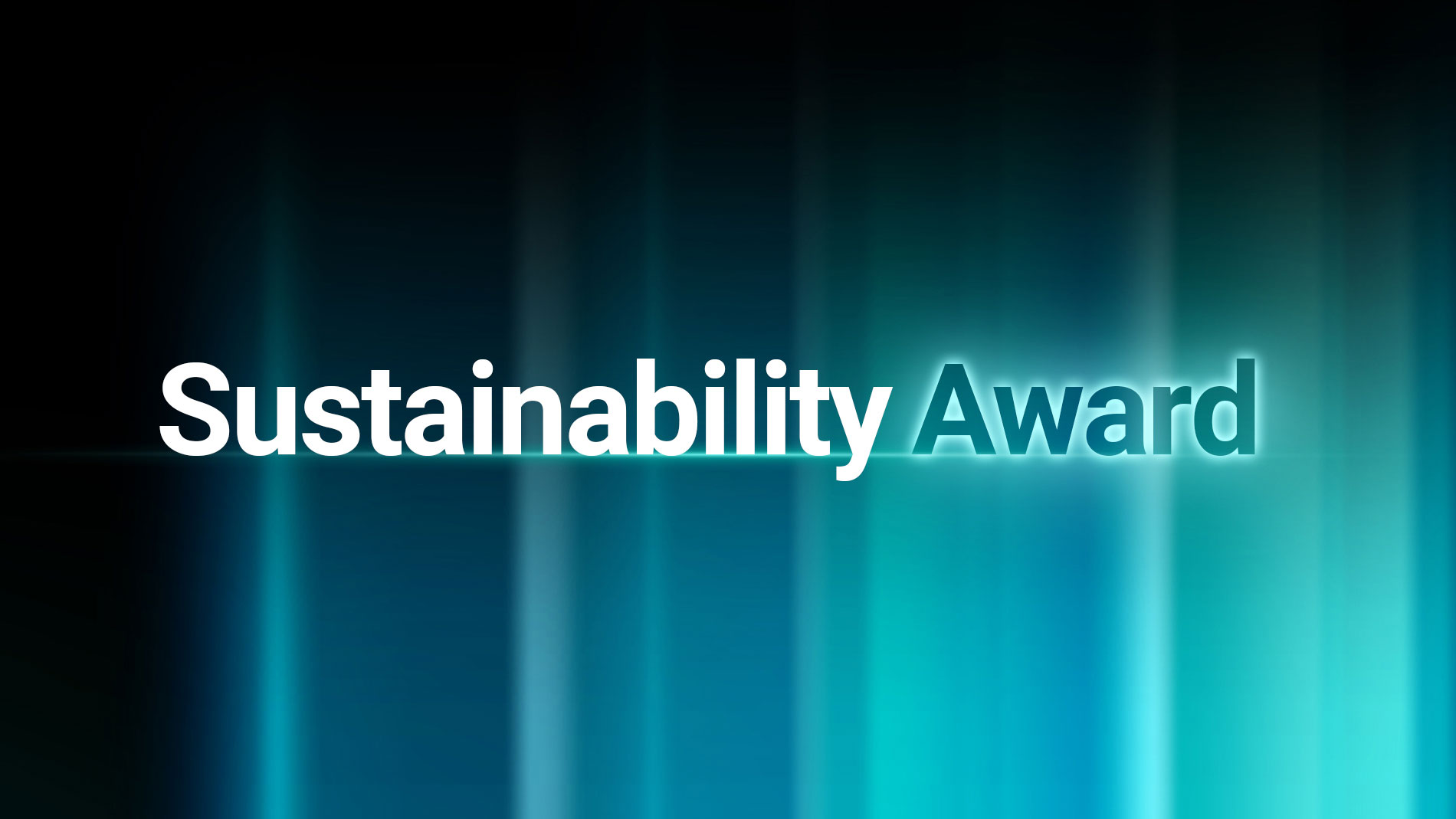
Die AM-Technologie wird oft als nachhaltige Technologie bezeichnet. Das mag in einigen Fällen zutreffen. Der wahre Wert zeigt sich jedoch oft erst im Lebenszyklus des Produkts. Genau diesen bewertet der Sustainability Award. Nicht nur die Produktionsphase, sondern den gesamten Produktlebenszyklus von AM-Anwendungen und Produkten.
Der besondere Wert dieses Awards liegt in der:
- direkten Verbindung von AM und Nachhaltigkeit durch eine Lebenszyklusanalyse (LCA),
- die sich nicht auf einzelne Materialien und Fertigungsprozesse beschränkt
- Bewertung des gesamten Anwendungsfalls
Die Kriterien
Folgende Fragestellungen werden bei der Einreichung abgefragt und von der Jury bewertet:
- Beschreiben Sie Ihren Anwendungsfall im Allgemeinen (Material/Industriezweig und Einsatzgebiet/Marktgröße und potenzielle Wachstumsrate/Skalierbarkeit/Übertragbarkeit auf andere Marktsegmente).
- Welches ist die Herausforderung, die Ihr Projekt in Angriff nimmt?
- Was ist der USP Ihres Projekts?
- Beschreiben Sie die Ökobilanz Ihres Anwendungsfalls entlang der Prozesskette anhand einer LCA-Matrix.
- Bitte stellen Sie eine Analyse zur Verfügung, die den gesamten Business Case veranschaulicht und die Auswirkungen der Strategie zur Umsetzung von AM über den Teil-für-Teil-Vergleich hinaus analysiert.
- Welches der 17 UN-Ziele für nachhaltige Entwicklung (SDGs) wird von Ihrem Anwendungsfall angesprochen?
Das Preispaket
- Einbindung in alle relevanten und weltweiten Marketing- und Kommunikationsaktivitäten der Formnext
- Präsentation des Projektes auf der Formnext Awards Sonderschau und bei der Preisverleihung
- Ein 3D-gedruckter Award, gestaltet von SUTOSUTO
- Geld- und ggf. Sachpreise
Leider ist die Einreichungsphase bereits vorüber. Details zu den Finalisten, ihren Ideen und wie Sie für Ihre Favoriten voten können, erfahren Sie hier Anfang Oktober.
Kontakt & Sponsorship
Sie wollen neuen Ideen den Weg in die AM-Welt ebnen? Dann werden Sie Sponsor der Formnext Awards – wir haben noch Platz auf der Sponsorenwand! Hier finden Sie alle Details:
Für alle Fragen rund um Ihre Teilnahme an den Formnext Awards und die Sponsoringoptionen wenden Sie sich auch gerne persönlich an: