by Thomas Masuch
Research project examining the potential of Additive Manufacturing for combustion engines
Even though electric and hydrogen drives are on everyone’s lips in the mobility world, conventional combustion engines are also being developed further. “For one thing, the diesel engine definitely has its uses, such as in ships or trains,” explains Nils Büchau, research associate at the Chair of Internal Combustion Engines (VKA) at RWTH Aachen University. “You can’t just offer everyone a Tesla in developing countries, either.”
With the VKA, Büchau is involved in a research project investigating the use of Additive Manufacturing for combustion engines. Under the consortium leadership of engineering service provider FEV Europe GmbH, the BMWi-funded LeiMot project is working on a conventional diesel engine from VW (Volkswagen 2.0 TDI, EA 288 evo), mainly with an eye toward exploring the potential of additive lightweight components.
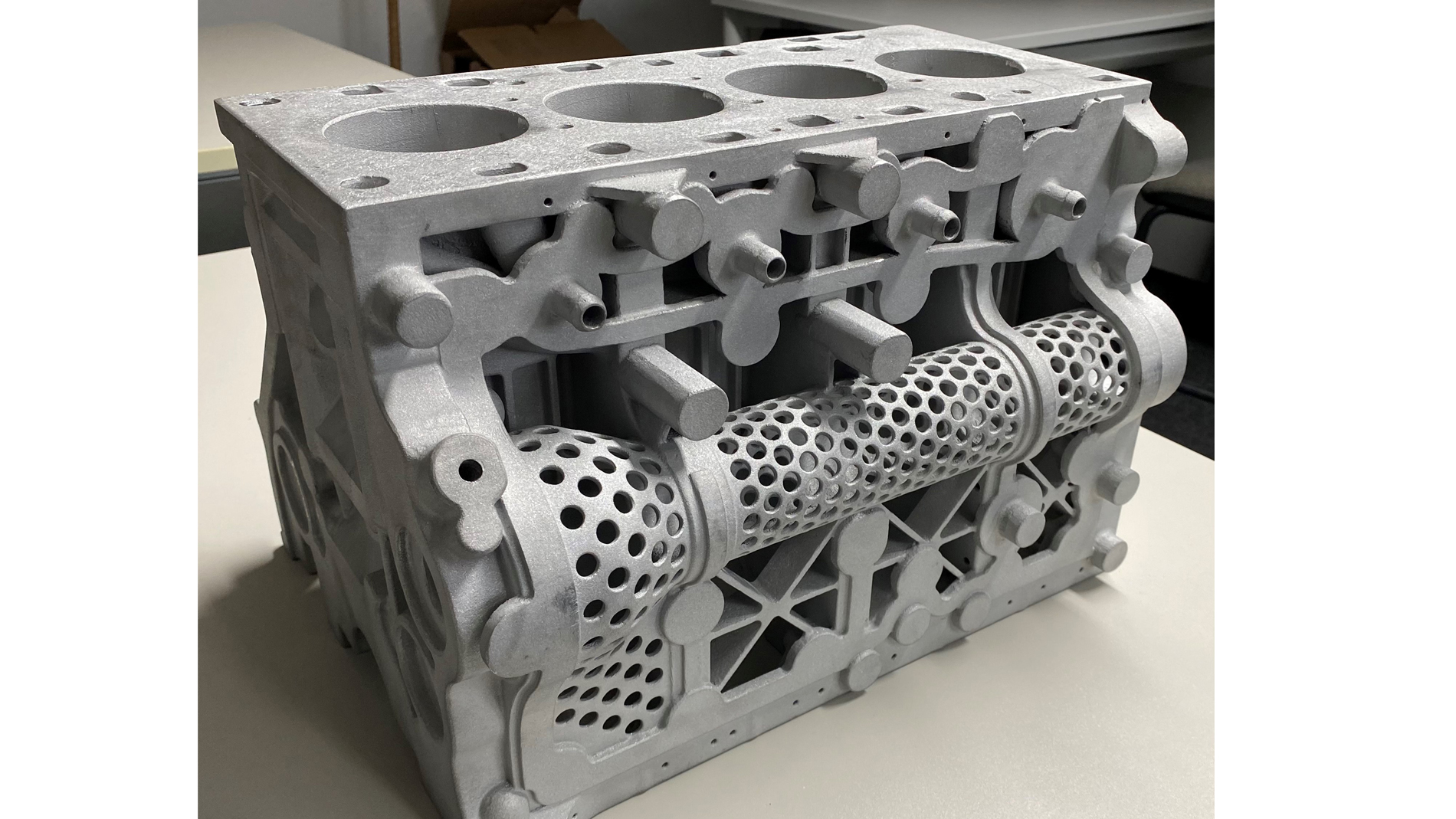
The focus thus far has been on the cylinder head and aluminum crankcase of the four-cylinder engine. Here, the use of AM indicated the highest potential for optimization. “The components have been redesigned to support subsequent Additive Manufacturing. New features that improve cooling and lubrication have also come into play,” Büchau says.
The LeiMot project has achieved improved cooling performance by reducing the diameters of the cooling lines to as little as three millimeters and positioning them to more efficiently dissipate heat directly at critical points. The resulting higher flow velocities have contributed to the improvements, as well.
In addition, the thinner cooling lines have reduced the volume of coolant in the cylinder head by over 60%, which gives the diesel engine a significant advantage. “Here, emissions occur almost exclusively in the cold-running phase,” Büchau reports. “Thanks to the smaller cooling circuit, the engine reaches its operating temperature more quickly and thus runs cleaner.”
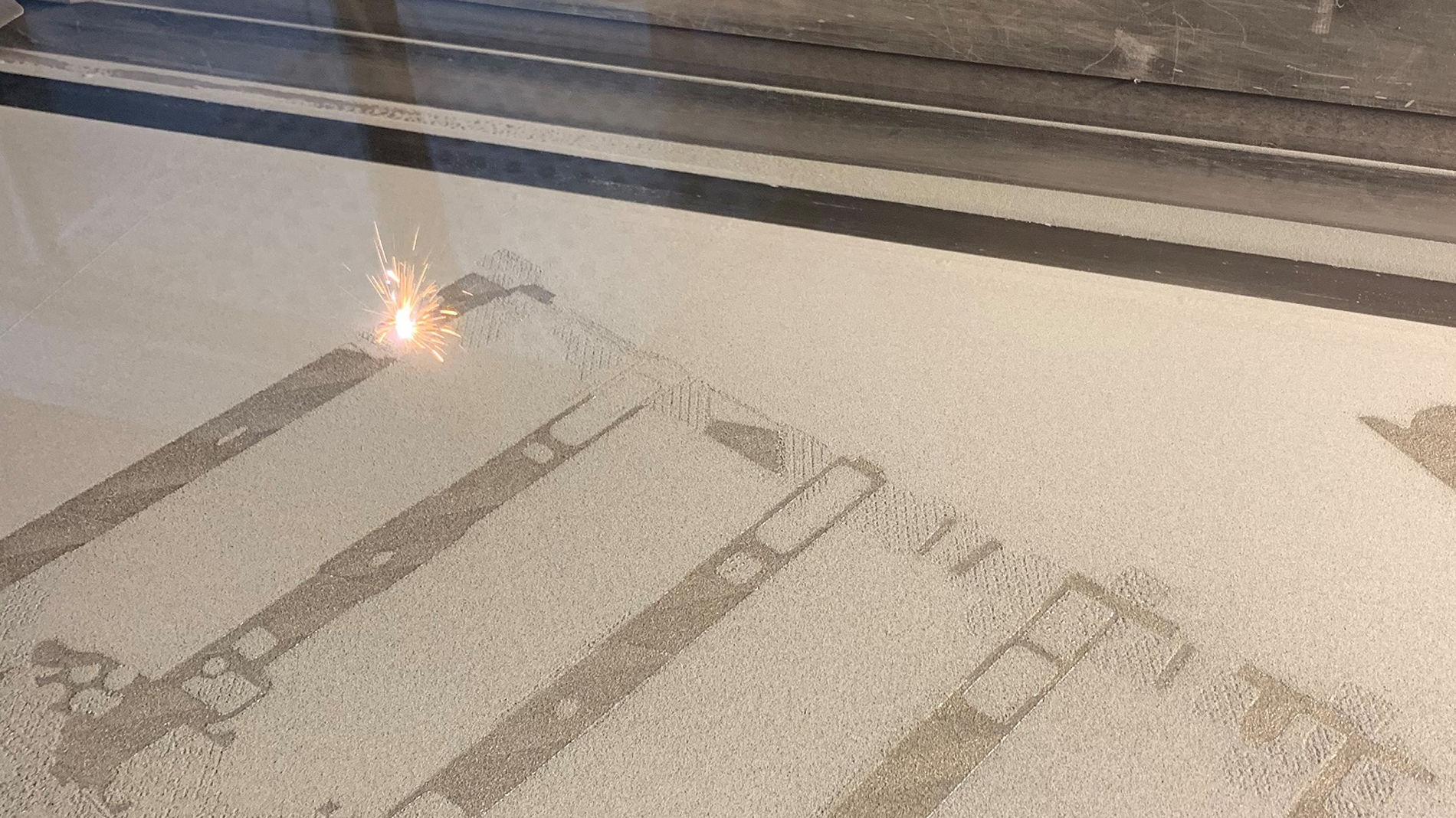
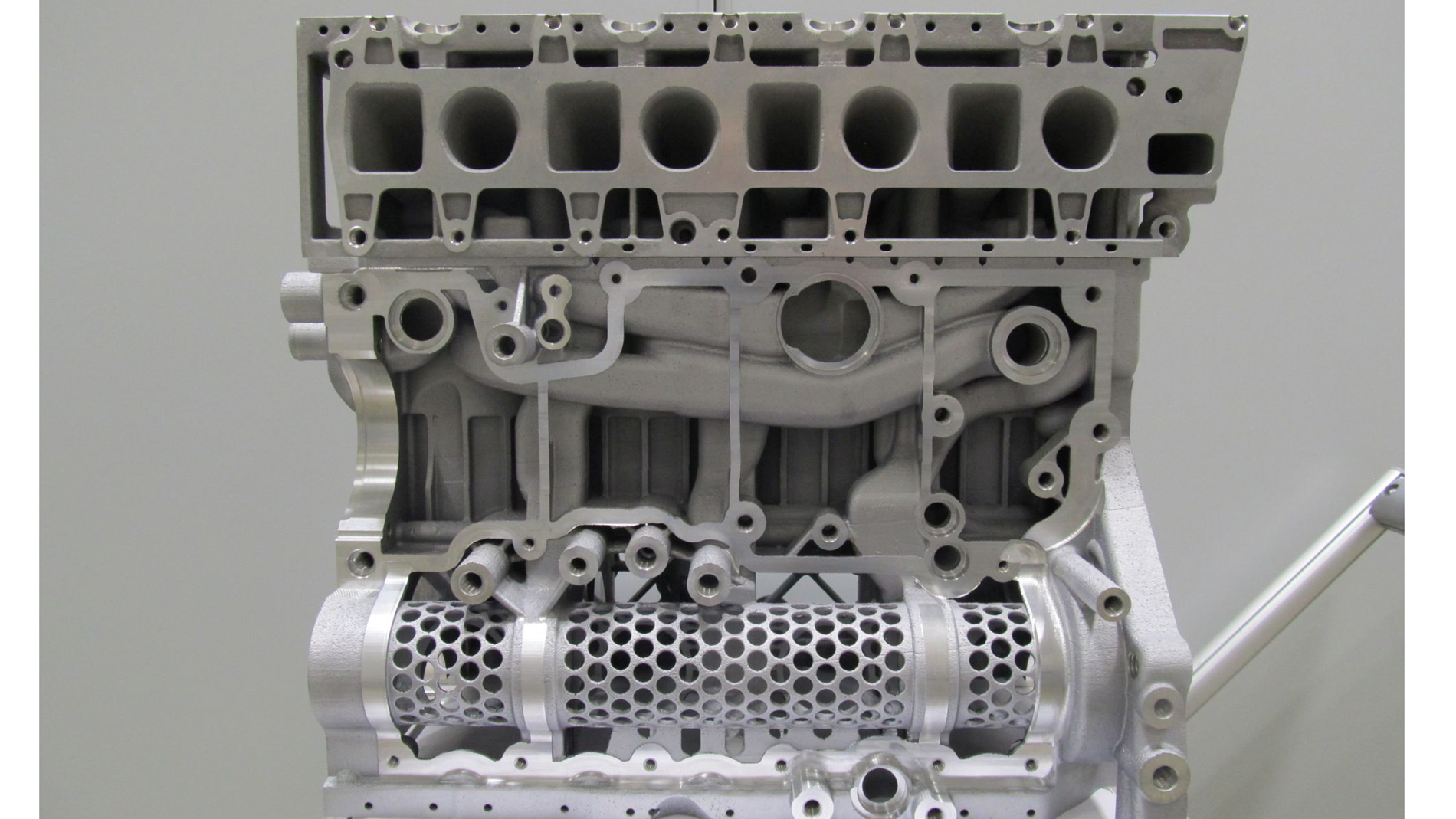
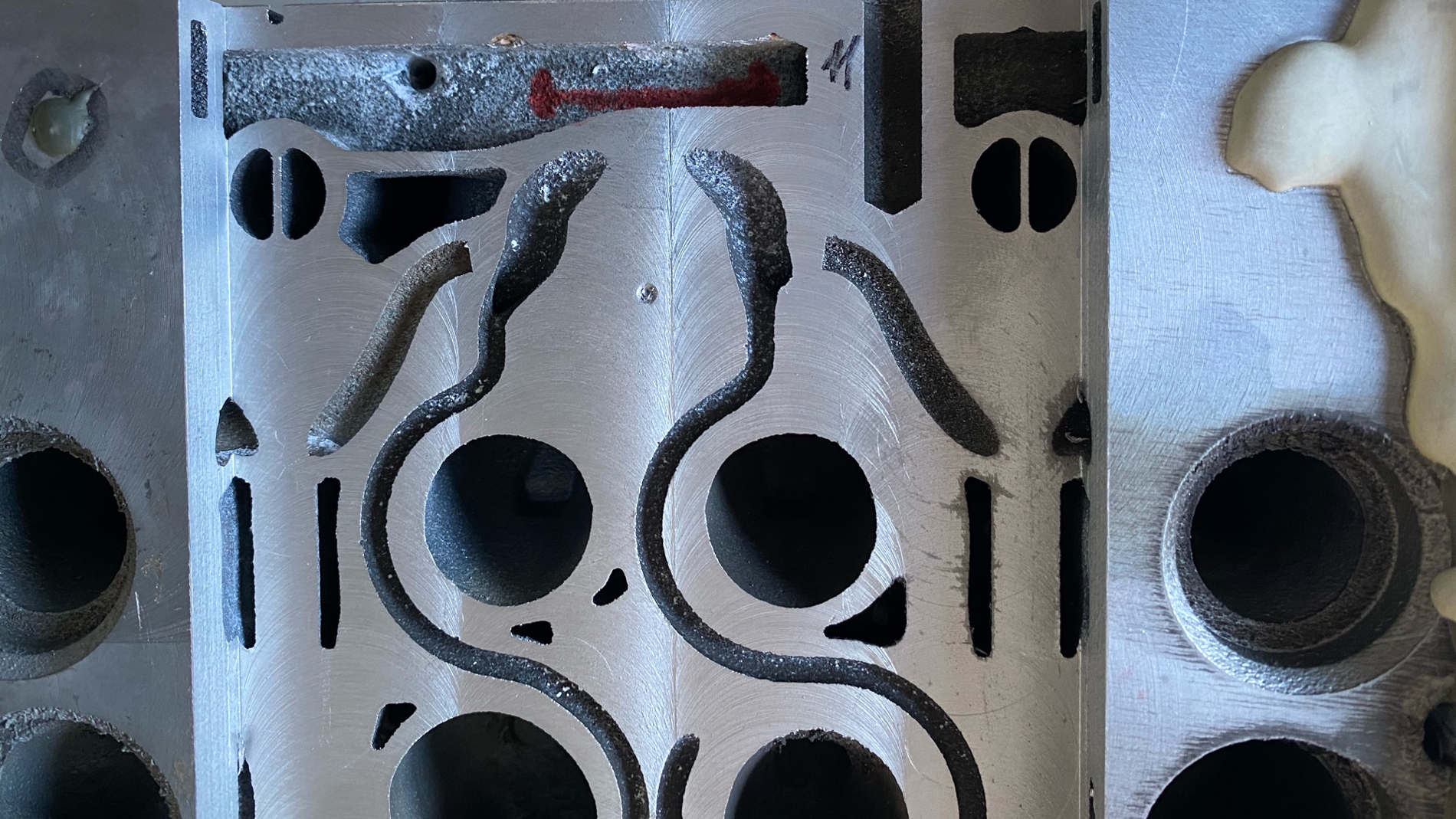
“Not one-size-fits-all”
Büchau and his research colleagues also gained important insights during the Additive Manufacturing of the 8.6-kilogram cylinder head, which was 3D-printed from the aluminum alloy AlSi10Mg over about four days using selective laser melting (SLM) on an X Line system from Concept Laser. “When you print faster, it results in rougher surfaces. Printing slower takes longer, but you get a better surface finish, which has a clear impact with thinner cross sections,” says Büchau. “There’s no one-size-fits-all approach here; the advantages you gain in one area a have an impact in another.” This has also been demonstrated in the post-processing of 3D-printed components. “The surface finish in the small channels requires electrochemical treatment (Hirtisation). However, this process has to take place after heat treatment due to the chemical reactions in the aluminum alloy,” Buchau continues. “A different orientation of the components to be printed in the powder bed can also lead to improved surfaces without electrochemical post-treatment.”
Luxury segment or casting
Even if the high cost of Additive Manufacturing still makes the use of the cylinder head or crankcase in automotive series production rather unlikely, Büchau draws a very positive interim conclusion: The concept of 3D Printing these two parts – which are about 22 percent lighter than the reference components – is quite realistic in the near future in small series, motor sports, or low volumes in the 10,000–20,000 range. “That’s where the patented cooling system and Additive Manufacturing in particular can help push diesel technology even further, even with new fuels.” Büchau explains. Meanwhile, he has high hopes for another novel approach: The features developed in the LeiMot project can also be used for cast cylinder heads and crankcases using things like 3D-printed cores.
AM TECHNOLOGY:
Additive Manufacturing for metal - powder_bed_fusion
A structured overview of the complex and multi-layered world of Additive Manufacturing processes, process steps and fields of application can be found in our AM Field Guide.
FURTHER INFORMATION:
Tags
- Automotive
- Additive Manufacturing