von Thomas Masuch
Ein Forschungsprojekt untersucht Potenziale von Additiver Fertigung für Verbrennungsmotoren
Auch wenn in der Mobilitätswelt Elektro- und Wasserstoffantriebe in aller Munde sind, werden auch herkömmliche Verbrennungsmotoren weiterentwickelt. „Zum einen hat der Dieselmotor zum Beispiel bei Schiffen oder Zügen durchaus seine Berechtigung“, erklärt Nils Büchau, Wissenschaftlicher Mitarbeiter am Lehrstuhl für Verbrennungskraftmaschinen (VKA) der RWTH Aachen University. „Zum anderen kann man in vielen Entwicklungsländern den Menschen kaum einen Tesla anbieten.“
Mit dem VKA ist Büchau an einem Forschungsprojekt beteiligt, bei dem der Einsatz der Additiven Fertigung für Verbrennungsmotoren untersucht wird. Unter Konsortialführung des Ingenieurdienstleisters FEV Europe GmbH beschäftigt sich das vom BMWi geförderte LeiMot-Projekt (Leichtbau-Motor) mit einem herkömmlichen Dieselmotor von VW (Volkswagen 2.0 TDI, EA 288 evo) und wollte vor allem die Potenziale additiver Leichtbaukomponenten ergründen.
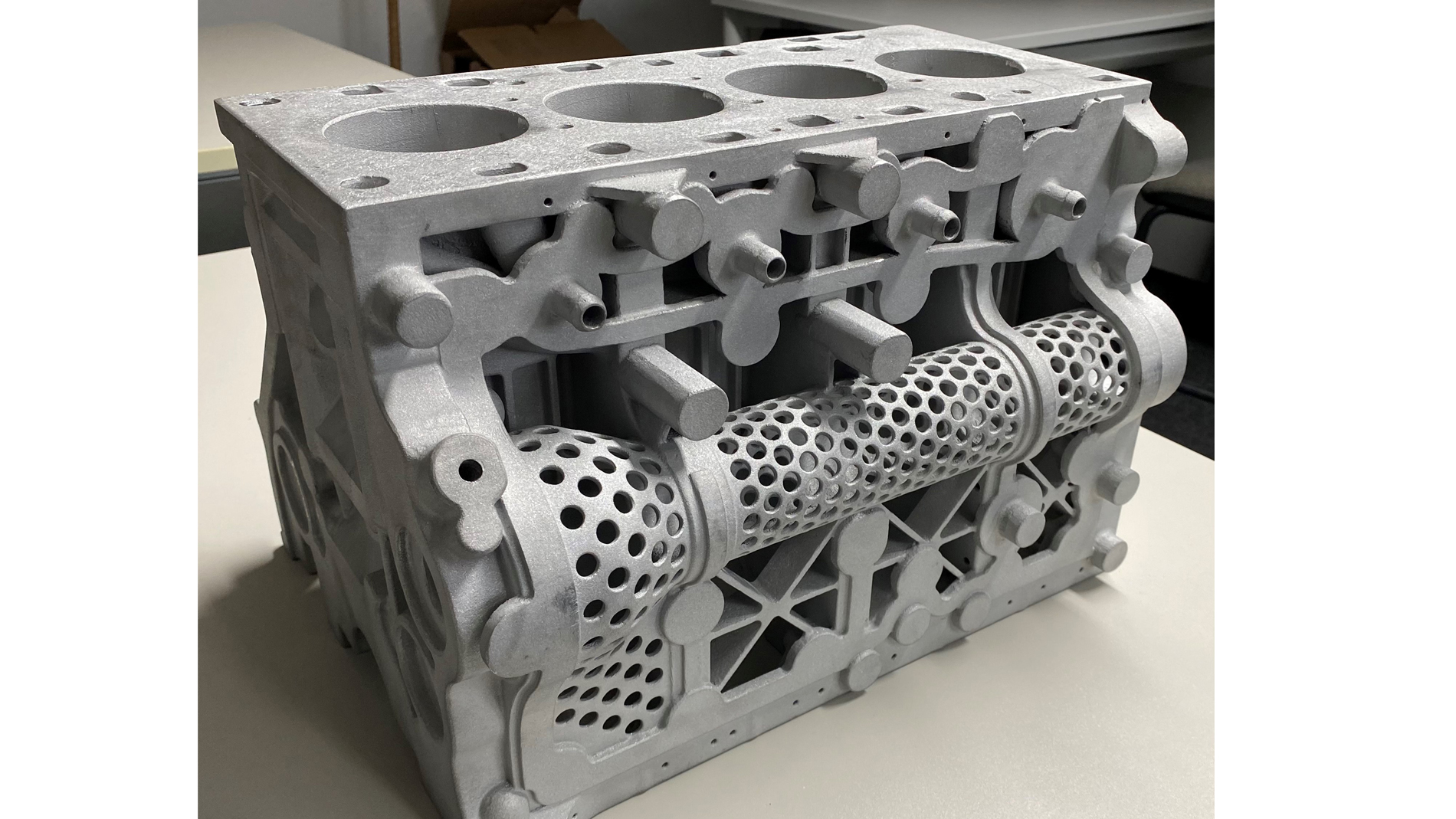
Im Fokus standen dabei der Zylinderkopf und das Aluminium-Kurbelgehäuse des 4-Zylinder Motors. Hier wurden beim Einsatz Additiver Fertigung die höchsten Optimierungspotenziale identifiziert. „Die Bauteile wurden im Hinblick auf die spätere Additive Fertigung neu konstruiert. Dabei kamen auch neue Features zum Zuge, die die Kühlung und die Schmierung verbessern“, so Büchau.
Die bessere Kühlleistung ließ sich dadurch erreichen, dass die Durchmesser der Kühlleitungen auf bis zu 3 Millimeter reduziert und die Leitungen so positioniert wurden, dass sie direkt an neuralgischen Punkten die Wärme effizienter abtransportieren können. Dies wurde auch durch die resultierenden höheren Fließgeschwindigkeiten erreicht.
Die dünneren Kühlleitungen führten auch dazu, dass sich das Volumen der Kühlflüssigkeit im Zylinderkopf um über 60 Prozent verringerte. Damit konnte für den Dieselmotor ein signifikanter Vorteil erzielt werden: „Hier entstehen die Emissionen fast ausschließlich in der Kaltlaufphase“, erklärt Büchau. „Durch den kleineren Kühlkreislauf erreicht der Motor schneller seine Betriebstemperatur und läuft dadurch sauberer."
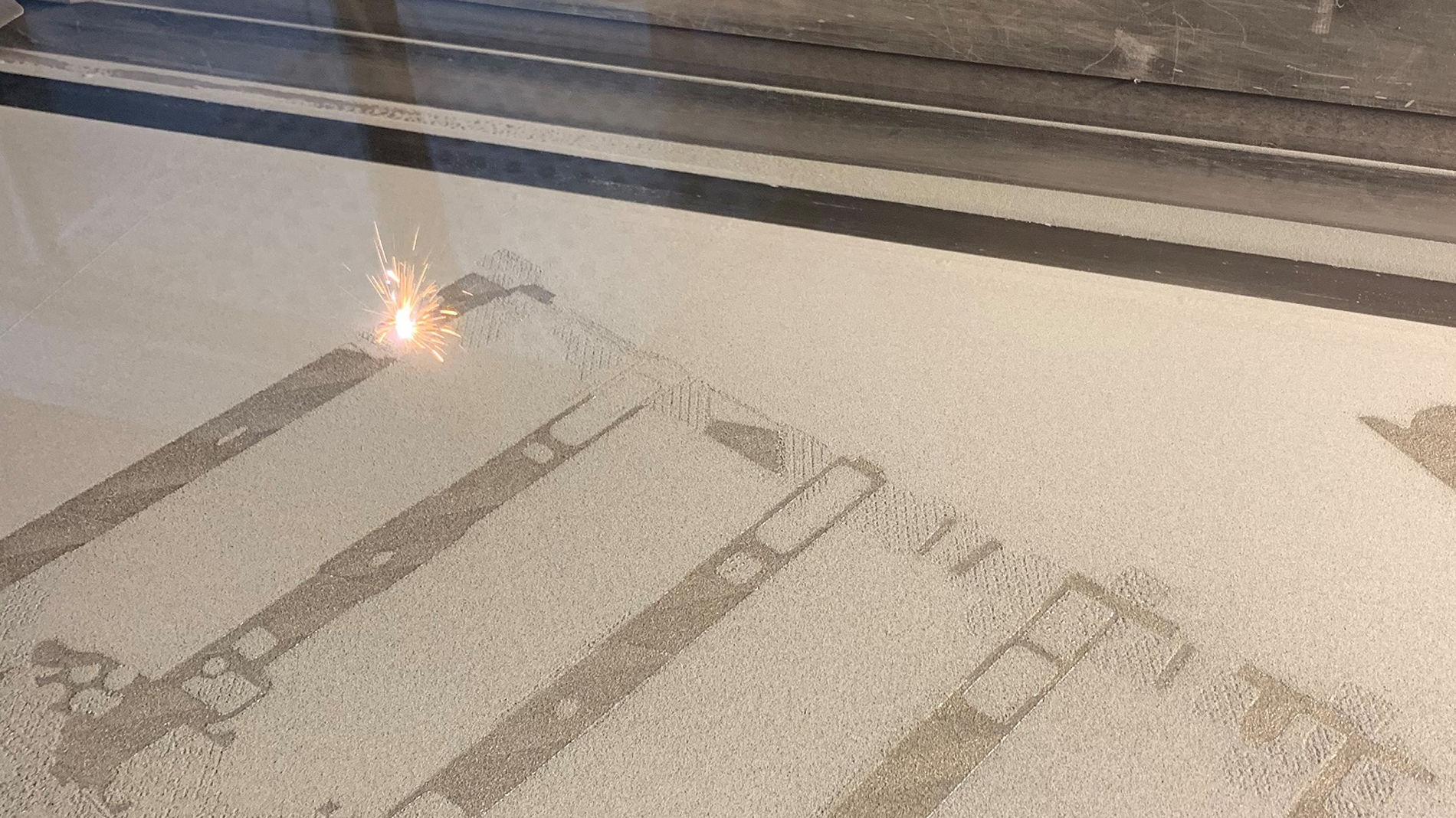
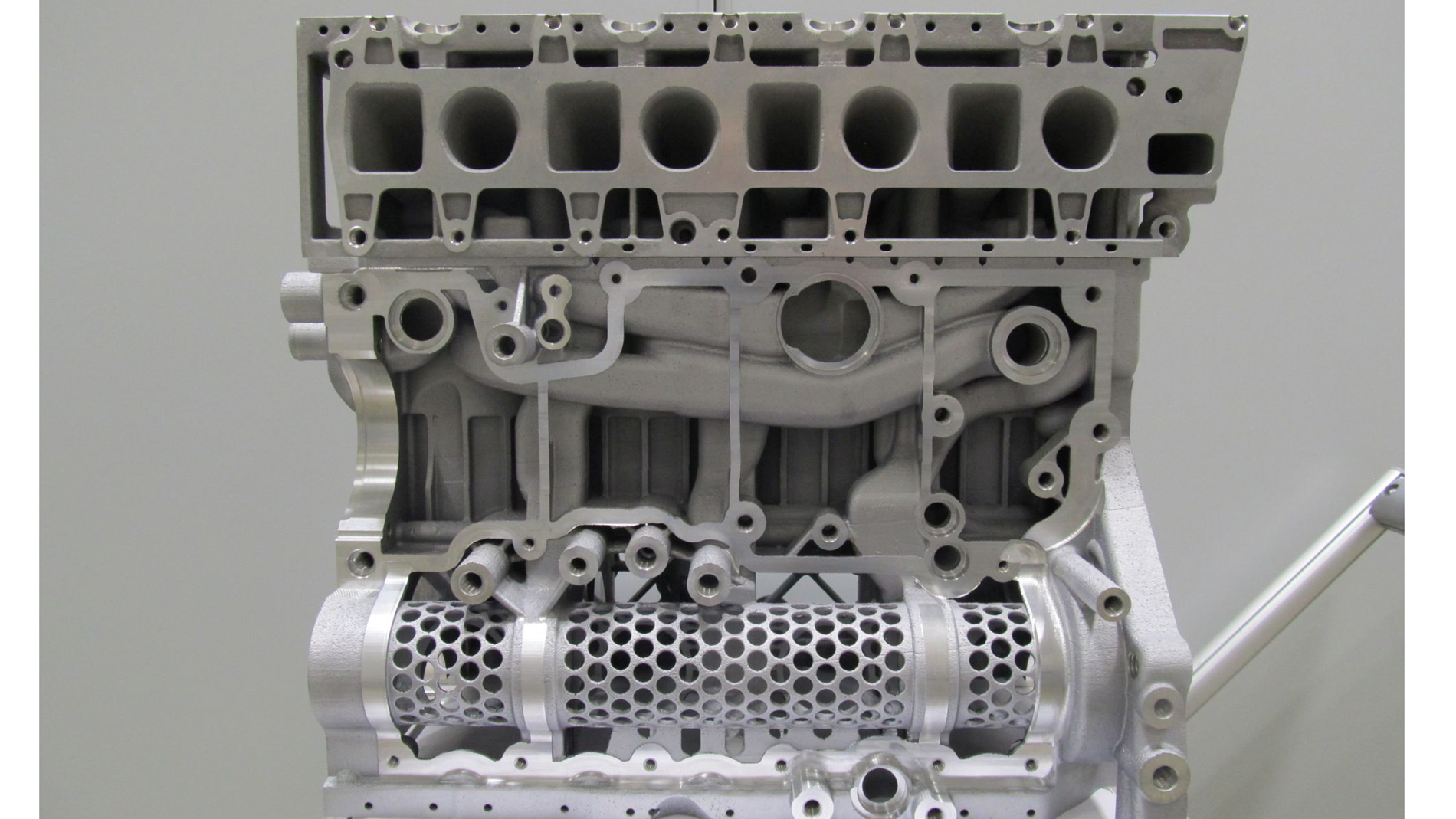
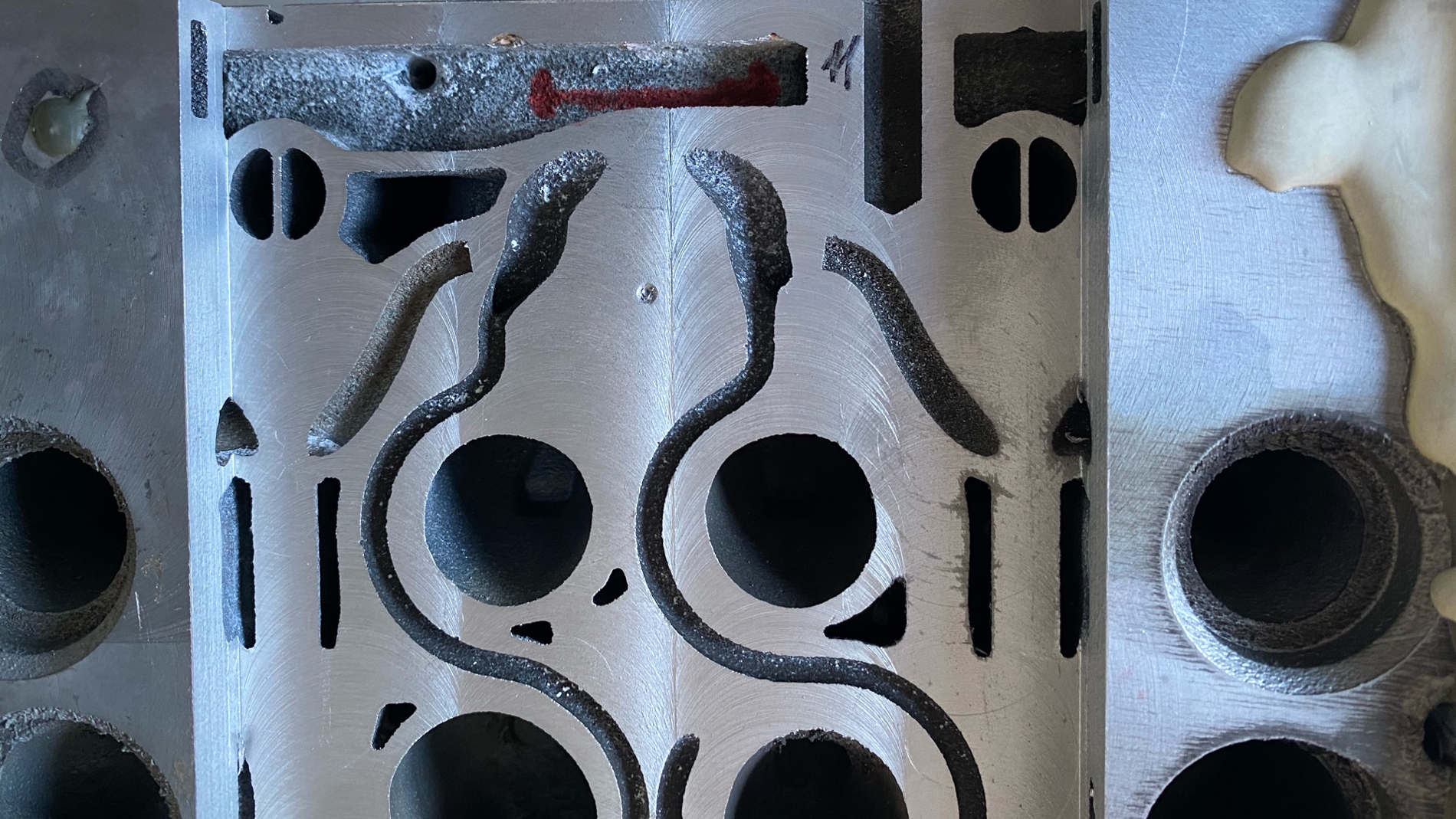
„Keine Eier legende Wollmilchsau“
Wichtige Erkenntnisse gewannen Büchau und seine Forscherkollegen auch bei der Additiven Fertigung des 8,6 Kilogramm schweren Zylinderkopfes, der aus der Aluminiumlegierung AlSi10Mg im Selective Laser Melting (SLM) auf einer XLine-Anlage von Concept Laser 3D-gedruckt wurde. Der Druck dauerte rund vier Tage. „Wenn man schneller druckt, führt dies zu raueren Oberflächen. Ein eher langsamerer Druck dauert länger, verbessert aber die Güte der Oberfläche. Und diese hat bei den dünneren Querschnitten einen deutlichen Einfluss“, so Büchau, der damit auch zu dem Fazit kommt, dass „es keine Eier legende Wollmilchsau gibt. Oft haben Vorteile an der einen Stelle Auswirkungen an einer anderen.“ Das hat sich auch bei der Nachbearbeitung der 3D-gedruckten Bauteile gezeigt: „Die Oberflächengüte in den kleinen Kanälen erfordert eine elektrochemische Behandlung (Hirtisieren). Dieser Prozess muss aber aufgrund der chemischen Reaktionen der Aluminiumlegierung nach der Wärmebehandlung stattfinden. Auch kann eine andere Ausrichtung der zu druckenden Komponenten im Pulverbett auch ohne elektrochemische Nachbehandlung zu verbesserten Oberflächen führen.“
Luxussegment oder Guss
Auch wenn der hohe Aufwand bei der Additiven Fertigung den Einsatz des Zylinderkopfes oder des Kurbelgehäuses in der Automobil-Serienfertigung eher noch unwahrscheinlich macht, zieht Büchau ein sehr positives Zwischenfazit: Zum einen sei das Konzept des 3D-gedruckten Zylinderkopfes und des Kurbelgehäuses, die ca. 22 Prozent leichter sind als die Referenzkomponenten, im Motorsport oder in Serien mit geringen Stückzahlen im Bereich von 10.000–20.000 in der nächsten Zeit durchaus denkbar. „Da können vor allem das patentierte Kühlsystem und die Additive Fertigung helfen, die Dieseltechnologie auch mit neuen Kraftstoffen noch weiter zu treiben.“ Und als zweite Option verspricht sich Büchau einiges von einem neuartigen Ansatz: Die entwickelten Features können z. B. mittels 3D-gedruckter Kerne für gegossene Zylinderköpfe und Kurbelgehäuse verwendet werden.
AM-VERFAHREN:
Additive Manufacturing für Metalle - powder_bed_fusion
Einen strukturierten Überblick in die komplexe und vielschichtige Welt der additiven Fertigungsverfahren, Prozessschritte und Anwendungsfelder liefert Ihnen unser AM Field Guide.
MEHR INFOS UNTER:
Tags
- Additive Fertigung