17 May 2023, by Thomas Masuch
With a bionic mindset, inexpensive desktop printers, a wealth of expertise, and an extraordinary concept for additive manufacturing, Paolo Matassoni has built up an AM department at Andritz Kaiser GmbH that now supplies a portion of the Andritz group with 3D-printed parts. The department’s additive approach has also played a formative role in the development of Andritz Kaiser’s latest 300-ton mechanical press.
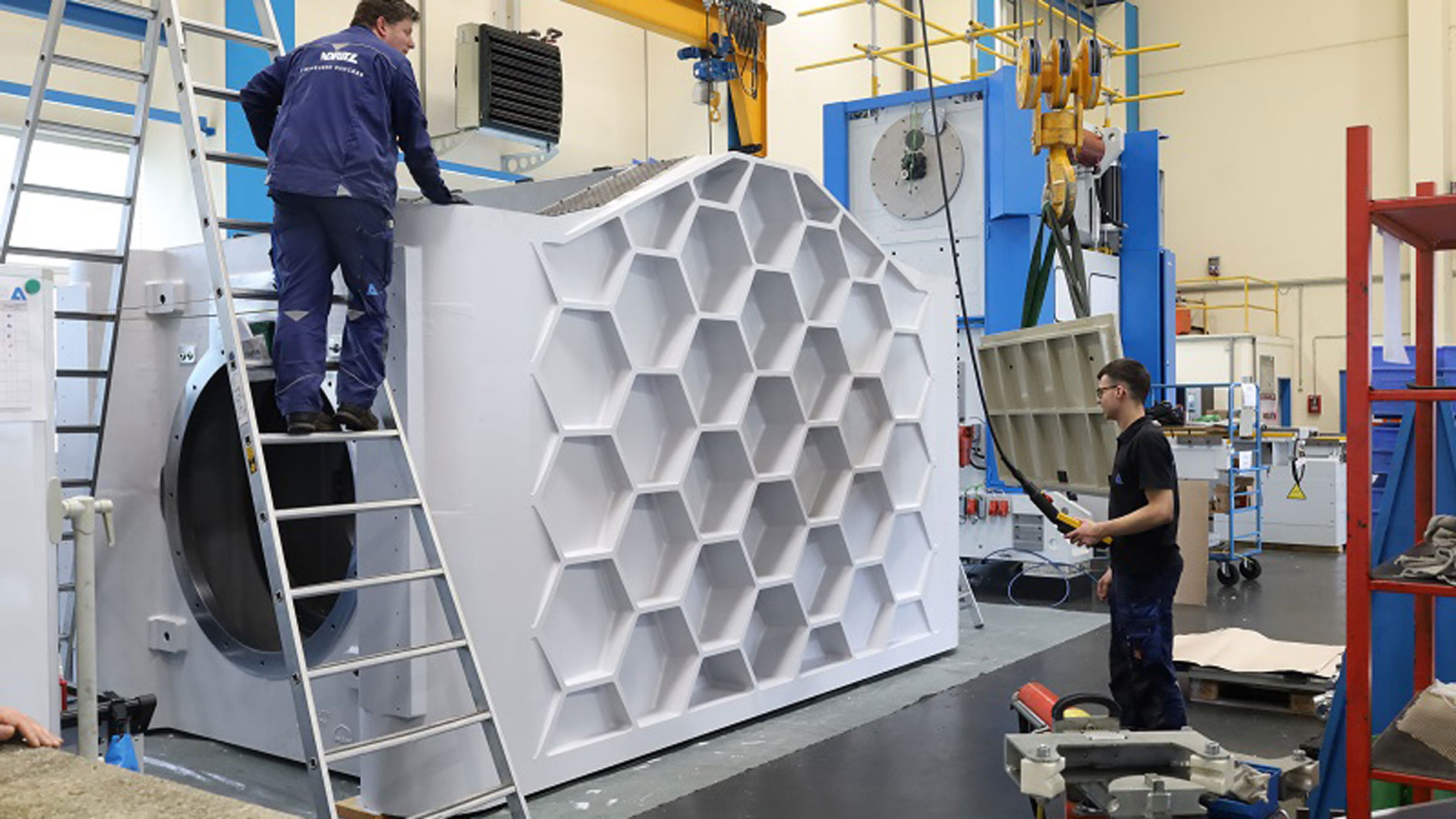
We stand before a cast-iron giant wearing a honeycomb crown. Paolo Matassoni runs a hand over the elegantly designed top section of the new mechanical press, which is three meters tall and weighs in at 60 tons on its own. The smile of an artist gazing in silent satisfaction upon a work that has taken countless hours of effort spreads across his face.
A short walk away on the gray-and-black floor of Andritz Kaiser’s assembly hall in Bretten (southwest Germany), a heavy-looking press bed painted in white waits, ready to anchor the press securely to the floor once it is installed inside the machine’s base. Like the roots of a mangrove, its supports branch into individual struts that form hollow spaces and combine with the 100-ton bed to create a single sinuous unit. The bionic balance of this cast-iron creation – which is roughly the size of a single-family house – is seamless but for a few locations that have been machined to a steely shine with millimeter-level precision to allow for the installation of further components.
While the press bed was cast using conventional methods, the head of development at Andritz Kaiser GmbH reveals that he “never would have dared to design something like this without borrowing from the world of 3D printing”. Matassoni had already integrated numerous 3D-printed components into this machine’s much smaller predecessor (which we reported on in our 02/2020 issue). The ToP-Line KSH2 in front of us – officially described as an “automatic stamping and forming press” – represents the next milestone in Andritz Kaiser’s efforts to incorporate additive manufacturing into its machines.
Paolo Matassoni in front of the 100-ton press bed. Image: Thomas Masuch
A total of 120 3D-printed parts have been built into this 300-ton unit, which was specifically developed to meet the requirements of hydrogen technology. It will be used to produce the kind of bipolar plates that constitute the core of hydrogen fuel cells. The AM components in the ToP-Line KSH2 press range from smaller joints and enclosures to oil return components and collection trays, lamp mounts, and gear wheels. Like the press bed, the honeycombed top section and the ram were conventionally cast, but still maintain the bionic aesthetic that was inspired by 3D printing, as Matassoni explains.
Another special feature will eventually be attached to the side of the top section: a safety brake and angle encoder for the press’s 800-kilowatt servo motor. “That’s an important safety component; we printed and cast the mount for it,” reports Manuel Mozer, one of Matassoni’s coworkers. “As a result, the brake helps reduce vibration, and machining it is also possible.”
The various 3D-printed, bionically designed parts that have gone into the ToP-Line KSH2 make it lighter (and thus more efficient) without sacrificing stability. This improved performance is key in the production of bipolar plates, which requires a high degree of both precision and output. In addition, Andritz Kaiser can now handle special requests and repairs in a more cost-effective manner. The company’s additive strategy has also impacted the time needed for related developments. “We’ve gotten much faster in that respect, thanks in particular to all the things we’ve learned,” says Matassoni. “It feels like it takes half the time it used to!”
A lifeline for colleagues on a deadline
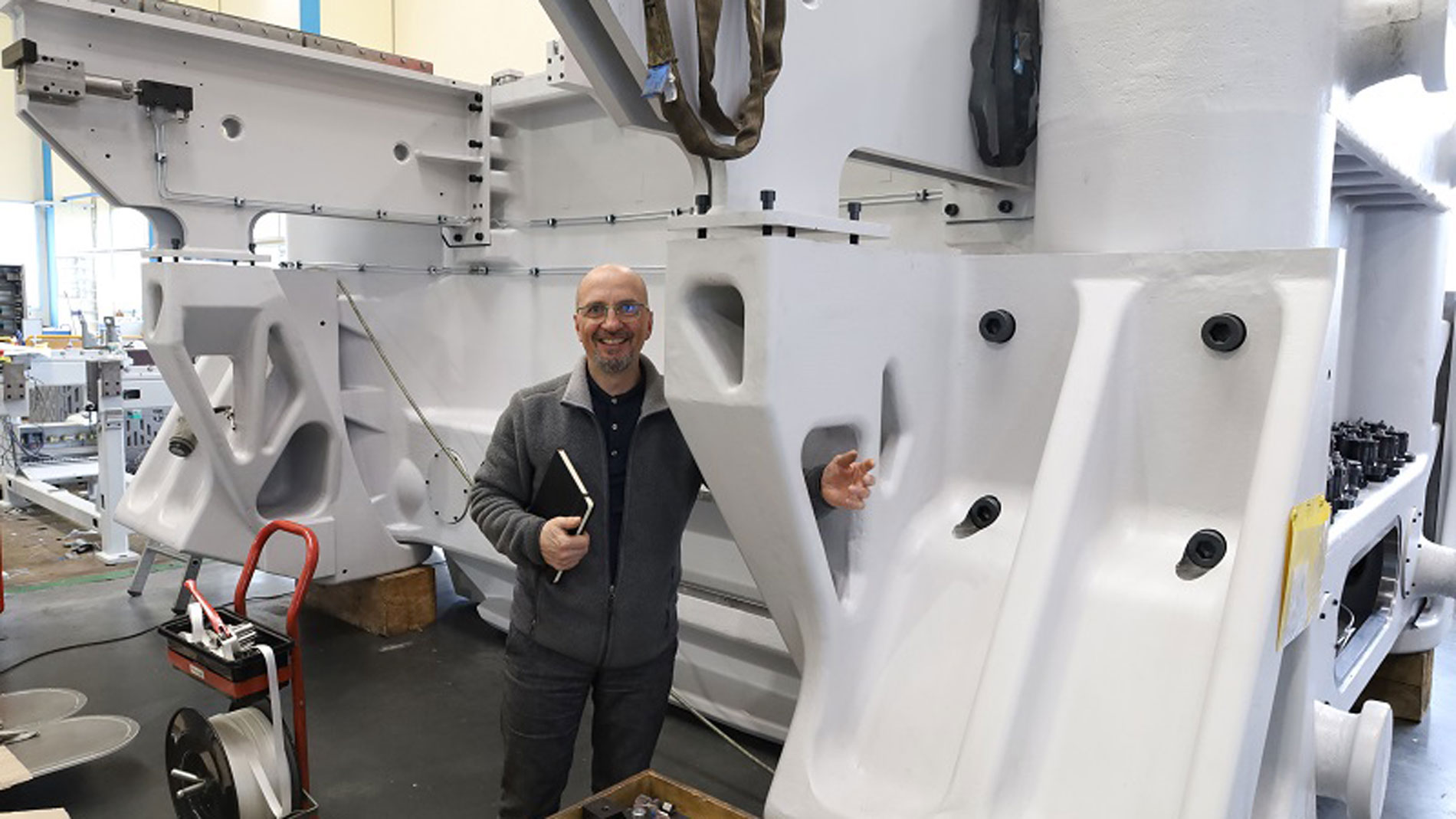
If you’re wondering how a soft, elegant engineering aesthetic could have come to guide the development of powerful new machines in a conservative industry where elemental forces drive heavy press rams at seemingly impossible speeds, look no further than Paolo Matassoni himself and the management board at Andritz Kaiser. The 53-year-old has been immersed in 3D printing and bionic designs inspired by nature since 2002. His comfortable knit jacket and gray slacks are a fair reflection of his mindset: Matassoni is a free spirit, but a practical one who expresses himself with style and intent through his knowledge of the importance of nuance.
The fact that he develops house-sized presses intead of Italian sports cars may be related to the freedom he has had at Andritz Kaiser to gradually take advantage of the benefits of AM in mechanical engineering. Describing himself as a “free thinker who has managed to capture the imaginations of the higher-ups on occasion”, he has indeed won over more and more colleagues at this traditional company, which has belonged to the international Andritz group since 2004.
Its AM department, Tec-Farm, has since added three young, disruption-minded members with a passion for 3D printing. It now operates as a service provider within the Andritz group, which has more than 250 production locations and some 28,000 employees around the world. Tec-Farm’s additive services are offset through an internal cost center based on the time required, materials purchased, printer depreciation, and other costs. “We can then invest the profits in more technology – meaning printers,” says a pleased Matassoni.
Handling internal projects for its international corporate group is now “how we earn our keep”, says Lena Glöckler, another design engineer at Andritz Kaiser. Sometimes colleagues come to Tec-Farm when they discover that a certain part is missing and their project’s deadline is looming. “We’re usually able to throw them a lifeline and help out in a hurry,” Glöckler says. While conventionally manufactured parts normally take four to six weeks, the department’s 3D-printed components are typically ready in just two days. Meanwhile, additive manufacturing has continued to establish a stronger presence in Andritz Kaiser’s assembly hall, as well. “We didn’t expect that area to be an ongoing source of inspiration for so many innovations,” Manuel Mozer reveals. “You can tell that our colleagues there are thinking about AM.” That wasn’t always the case, as Mozer goes on to explain. “In the beginning, plenty of people at the company weren’t big believers in the direction we were taking, and some of them even had a certain amount of antipathy toward 3D printing,” he recalls. “It’s completely different now; there aren’t nearly as many skeptics.”
The amount of appreciation people now have for AM at Andritz Kaiser is evident in a promotional video that highlights the company’s use of 3D printing. Matassoni has also received a design award from the entire Andritz group.
An eccentric shaft with oil drainage rings. The shape of the segments ensures that they can be assembled with a tight fit. Images: Thomas Masuch
“Customers and purchasers understand the forms”
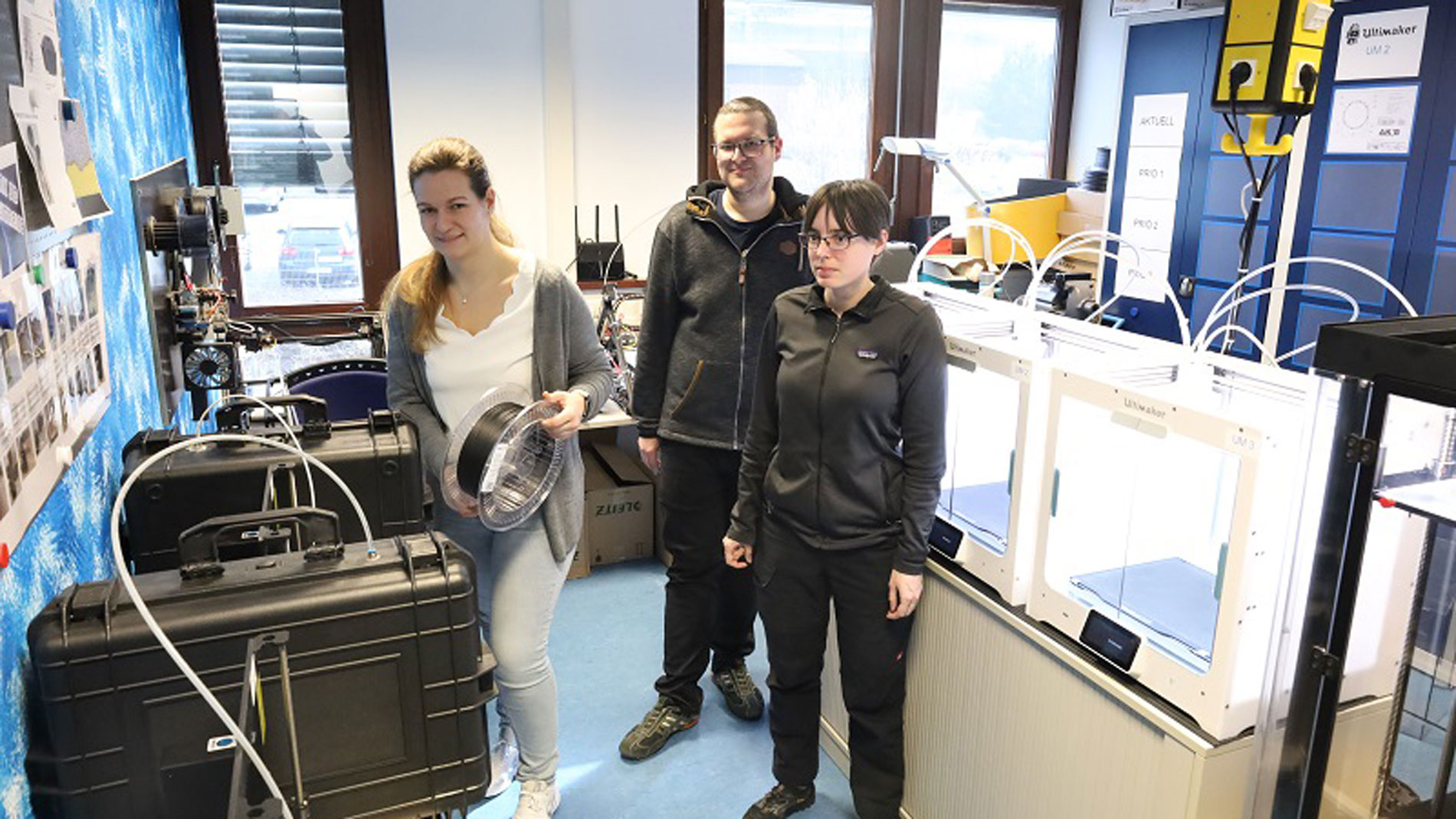
Along with the 16,000 kilonewtons of pressing force it can generate, the unique bionic design of the ToP-Line KSH2 has played a central role in winning over not only the people at Andritz Kaiser, but potential customers, as well. “They see what we’re capable of in terms of innovation,” Matassoni affirms. “Even if they don’t grasp every technical detail, customers and purchasers understand the forms because they come from nature and seem familiar right away. That makes the machine more logical.”
These innovations can be traced all the way back to the development phase. According to Matassoni, this is another area where the benefits of the company’s additive strategy are readily apparent. His AM team is also forging into more and more new territory that would have been unthinkable in the past. “Thanks to 3D printing, we’ve gotten bolder and honed our innovative capability,” Matassoni says, adding that the technology gives his team a type of safety net in the event of failure. “We can reverse course quickly if something doesn’t work out.”
“Think big, print small”
Tec-Farm’s plastic components are 3D-printed in a room located at the end of an office hallway in Andritz Kaiser’s administrative building. Here, one finds a row of around a dozen desktop printers, most of them from Ultimaker and Prusa. “We started with FDM six years ago, and we’ve stuck with it,” Manuel Mozer says. The printers are affordable – the basic versions of some of the printers in use at the company cost around €1,000 – but “you can produce quality results in industrial settings as well,” Mozer continues. “It does take a good bit of expertise, though.”
That’s exactly what hobbyists like Mozer, Lena Glöckler, and their colleague Alena Dehm have. As we pass by, they point out a belt printer from iFactory that seems to have sprouted a tangled mass of colorful cables, all of which lead to a control box. It’s difficult to imagine how the printer looked in its original form. “For our purposes, FDM printing is actually better because the technical systems available are more open and less complex, which gives us the freedom to make our modifications. That wouldn’t be possible with SLS printing, for example,” Mozer explains. This kind of improvised, yet technically flawless creativity is what Paolo Matassoni likes to see. “I’m happy to have young people contributing their knowledge and taking our AM production to the next level,” he declares.
This expertise is also enabling Andritz Kaiser to use its desktop printers to produce large parts like oil drainage rings or the enclosure for the ToP-Line KSH2’s angle encoder. Such components are split into segments, bonded together, partially filled with plastic, and then machined into their final form. “To make sure the parts fit right, we include the tongues and grooves when printing them,” reveals Alena Dehm. This was how Andritz Kaiser printed its biggest component yet: an air deflector ring for a generator turbine measuring 1.2 meters in diameter. “Think big, print small” is how Matassoni describes his philosophy, which sometimes means using small FDM printers to manufacture parts for systems that cost millions of euros. “That probably makes us something of a black sheep in the world of AM,” he admits. Applying this DIY method on an industrial scale has nevertheless resulted in a single-digit machine hour rate, as Lena Glöckler points out. “That means we can more than compete with CNC,” she adds.
Filled components offer greater stability
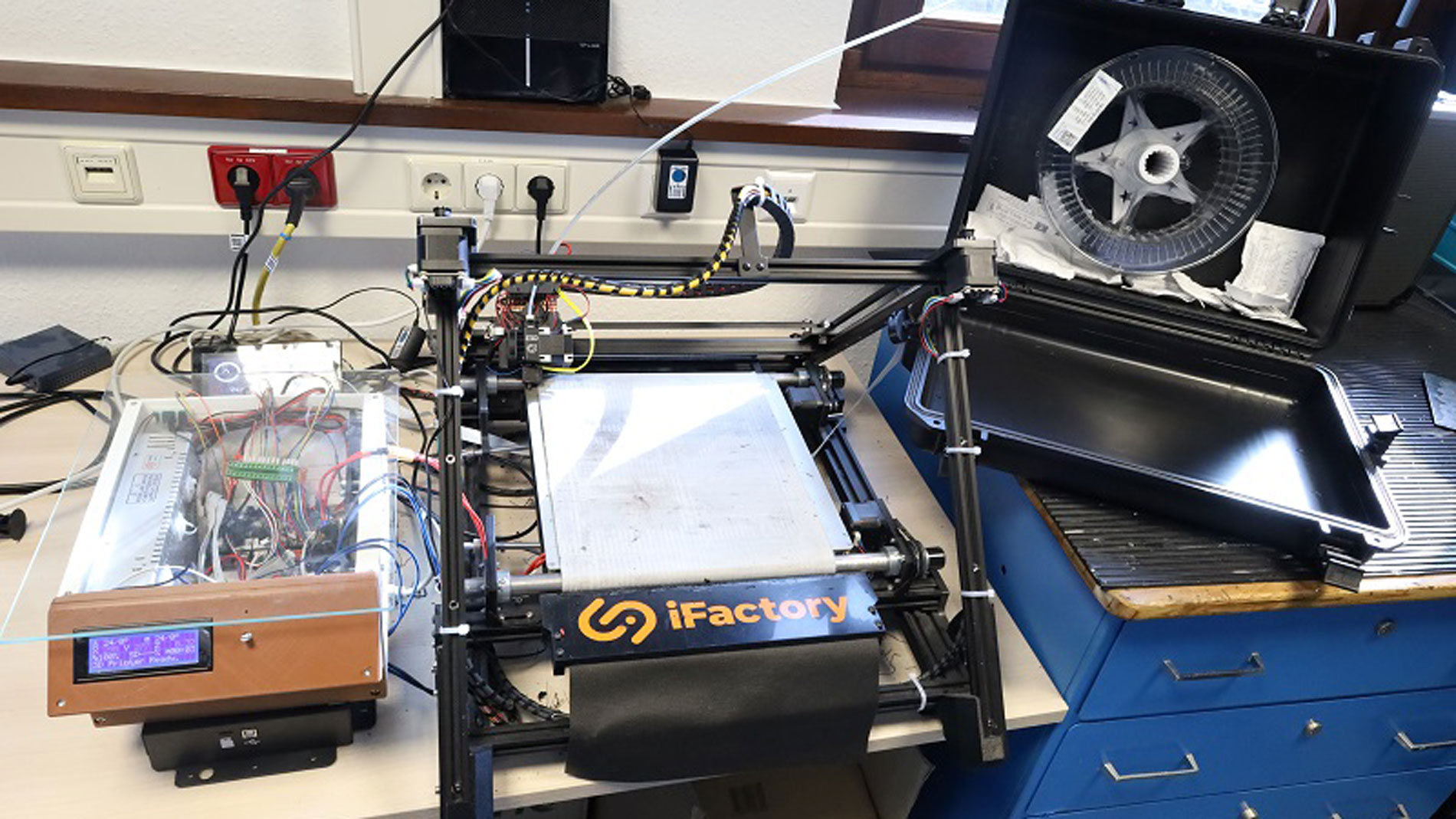
Virtually all of Andritz Kaiser’s AM components are 3D-printed using fiber-reinforced plastic (PA6). In cases involving larger parts, this is how the external enclosure is made before being filled with a type of duroplast that contains metal particles. Since this filling material doesn’t come cheap, Manuel Mozer has come up with another DIY solution: Like reinforced concrete, duroplast can simply be filled with metal wool.
“The method works in the same way as a human leg, where the bone provides stability inside a covering of muscle and skin,” explains Matassoni, who once served as an EMT alongside his job as a design engineer. He says this technique also presents a great deal of further potential, as well. It’s also easy to add bits of brass to the composite, for example, or electronic components like sensors. This opens the door to solutions on many new levels.
During tensile testing, the team also discovered that their filled components were able to withstand much more strain than those made entirely of fiber-reinforced plastic. Matassoni attributes this to the way the filling significantly increases a part’s stability along the z-axis and improves the bonds between its individual layers.
Asking the materials different questions
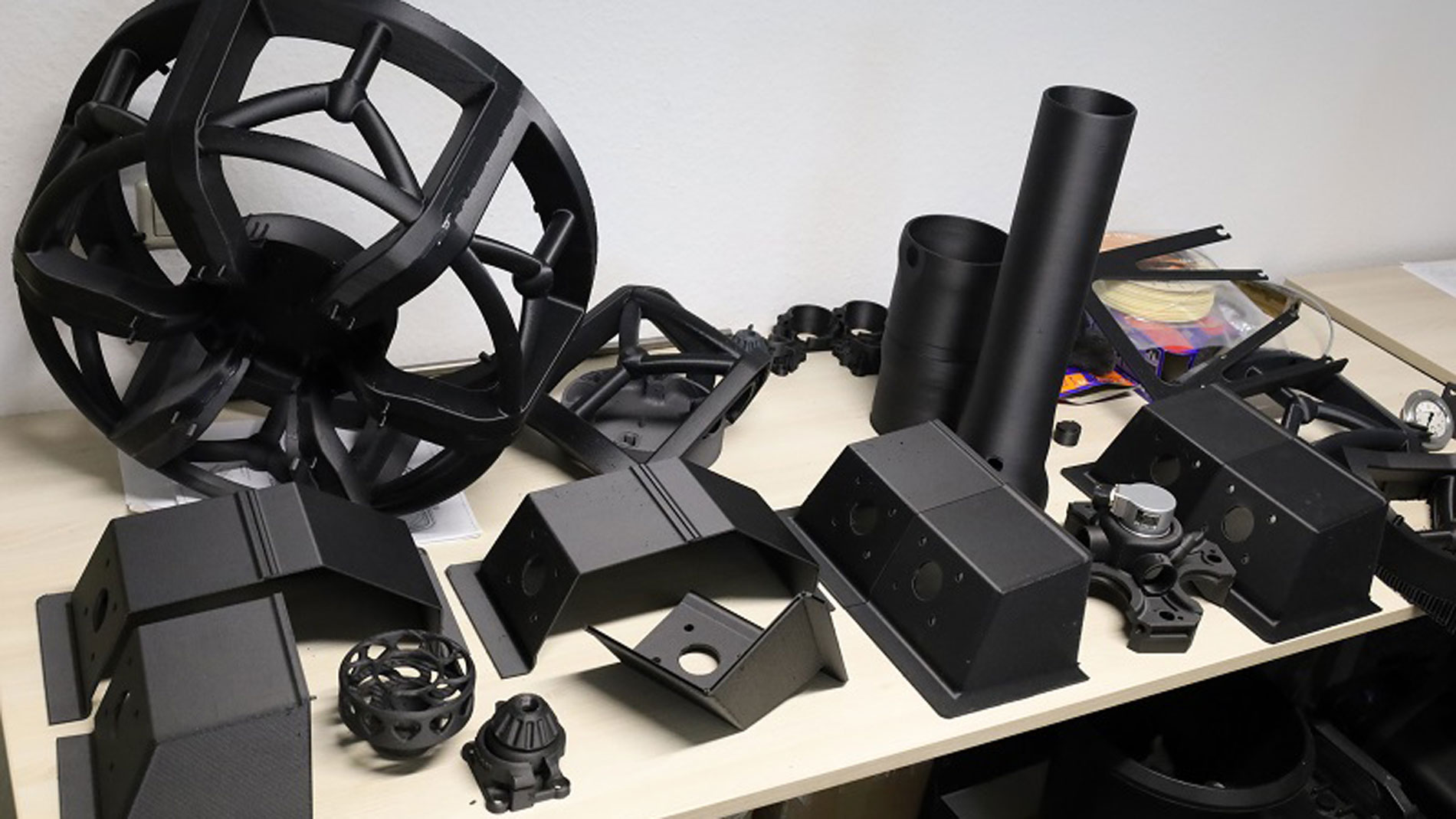
Next to each of the desktop printers in Tec-Farm’s room is a black case of nearly the same size that supplies the unit with filament. These cases preserve spools of the material in an air-tight environment. “We’ve conducted numerous material tests, and one of the things we’ve figured out is that the raw material we use has to be as dry as possible,” says Mozer.
One morning, he found fairly definitive proof of the need for such tests waiting for him on his desk. Mozer had printed a series of test components the day before. “They still looked good that evening, but just a day later, one had sort of exploded all by itself,” he recalls. It wasn’t long before the AM had figured out the reason why. “With some materials, a component of a certain size can basically tear itself apart due to its internal tension,” Mozer explains.
Meanwhile, parts made of other materials had deformed because they were too sensitive to humidity. “We tested materials and came up with different results even though the specification sheets said the same thing,” reports Matassoni, who then developed a test series of his own that was different from the standard procedures. “The manufacturers had obtained their data using tensile testing; we simply came up with different questions for the materials to answer.”
A thread cube becomes the norm
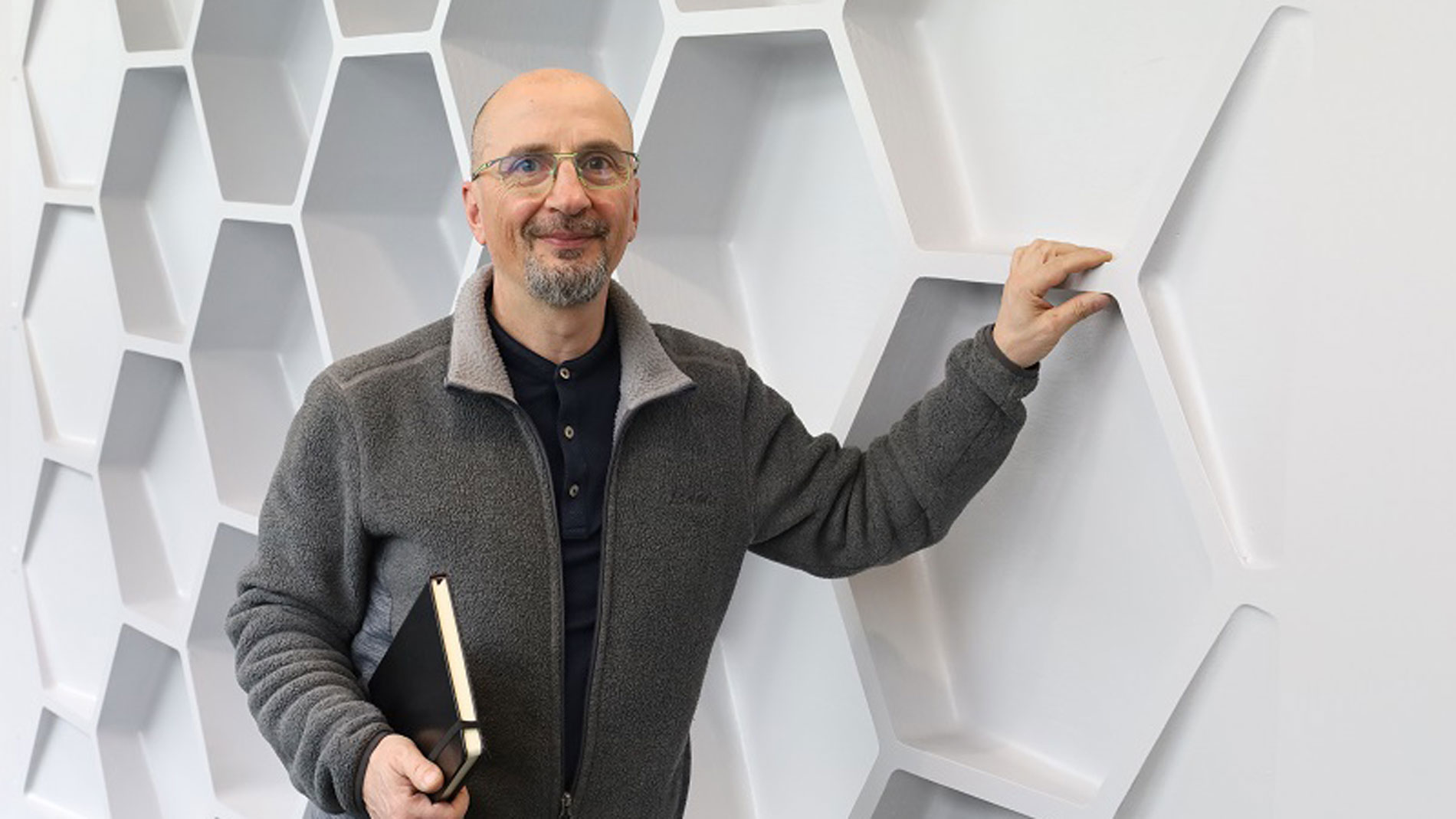
Known as the “AK norm”, the test procedure developed in Bretten involves 3D-printing a cube with a screw thread in the middle. A torque wrench is then used to turn a screw into the cube until it bursts. “One of the things we discovered is that some materials are really hard, but don’t offer much bonding between their layers,” Matassoni says. Throughout this process, Andritz Kaiser’s material partner was FiberThree from nearby Darmstadt, which Matassoni met at Formnext 2019. “They follow a philosophy similar to ours and have grown along with us,” he continues.
At this point, the team turned its attention to finding the right material for its internal applications. “Ideally, you’d have a special material for every printing job,” says Mozer. To operate efficiently, however, Tec-Farm chose a material that offered the best possible balance of stability, resistance to oil and temperature, and machinability. “Going with a compromise like this does involve making some concessions, though,” points out Matassoni. “There’s just no universal solution that works well for every intended use.” Matassoni and his colleagues compensate for any shortcomings that arise by adapting their designs accordingly.
He goes on to describe how a number of the company’s suppliers have been amazed to find out how much time a mechanical engineering company is spending on research. However, pouring all that effort into material development enables Andritz Kaiser to save a great deal in other areas. “That’s the path we’ve chosen, and it’s not the beaten one,” Matassoni says.
“As standard as a power drill”
Meanwhile, the Tec-Farm team is far from finished: For one thing, its members plan to keep spreading the AM gospel at Andritz Kaiser, including by implementing decentralized manufacturing at specific locations and installing 3D printers in the vehicles of mechanics in the field. This would enable them to print the spare parts they need on-site. “We want 3D printers to be as standard as a power drill,” declares Matassoni, who adds that settling the issue of fire safety at customer locations is the last thing standing in the way.
At the same time, he wants to continue establishing the additive mindset not only at Andritz Kaiser, but throughout the entire Andritz group. Matassoni believes that the core concern here is “figuring out what the components themselves need and forgetting all about the requirements of manufacturing”. In this way, the company’s design engineers could leave their complex two-dimensional plans behind and immerse themselves more and more in bionic systems. “We’re talking about a paradigm shift, and that requires a certain amount of mental anarchy,” Matassoni states. He says that the solutions are just waiting to be found in nature, albeit in different places. “You just have to know how to put the answers together.”
MORE INFORMATION:
To learn more about the about the FDM process (Fused Deposition Modeling) check out the AM-Field-Guide.
Tags
- Mechanical and plant engineering