Text and Photos: Thomas Masuch — 08 June 2020
In developing its latest mechanical press, Andritz Kaiser GmbH took advantage of the innovative potential of Additive Manufacturing and bionic design. The unique combination of its corporate strategy, a passion for industrial 3D Printing, and sources of inspiration in the natural world has proved valuable in a number of ways.
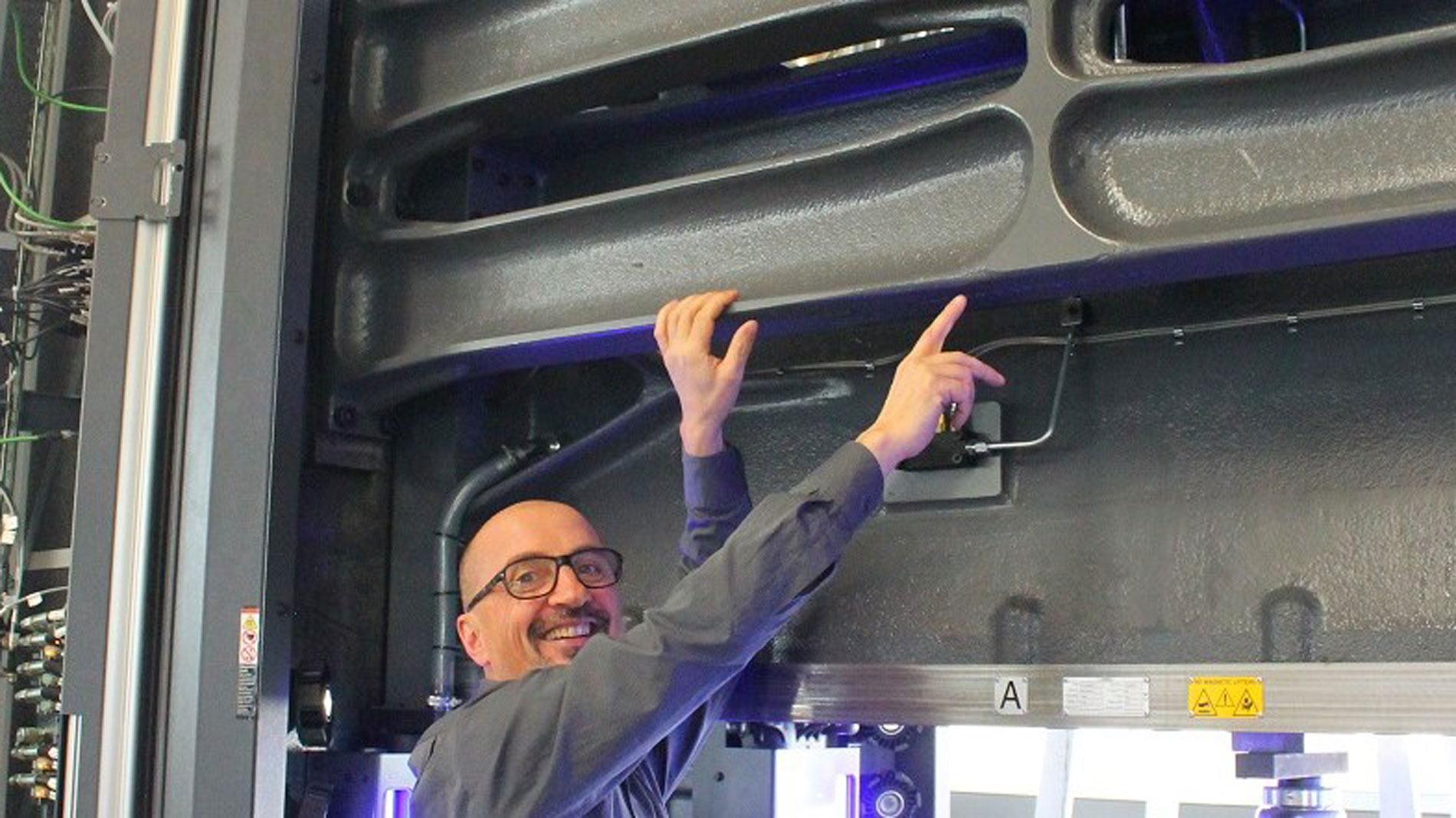
Standing amidst other steel colossi as tall as buildings at the front of the production facility, the 30-ton ToP-Line 2000 has the look of a stylish design installation. Here, in an exhibition area set up specifically for this cutting-edge mechanical press, its progenitor points up at the machine’s 3,5-ton plunger with a cryptic question. »Do you see the river pebble?« Paolo Matassoni asks.
With the smell of oil and industry permeating the air and the scene dominated by huge units that will spend the next 20-plus years forming sheets of metal with thousands of kilonewtons of pressing force, the image of a river pebble seems a little out of place. That type of smooth, round stone – along with various flora and fauna – was nevertheless the inspiration that informed Matassoni’s efforts in designing the machine before us. Indeed, many of the components of the latest generation of presses made in Bretten, Germany, were created this way. »Plenty of designs are already found in nature – we’re just copying them!« Matassoni, the head of development at Andritz Kaiser GmbH, explains. The 52-year-old engineer has been able to implement the components’ flowing transitions and bionic forms in the industrial realm thanks to his own excitement about the possibilities of 3D Printing and the additive mindset his team has adopted.
"Once you adopt an additive mindset and corresponding working methods, new improvements and ideas start coming to you almost automatically."
A full 150 of the parts that go into the ToP-Line 2000 were created with the help of 3D Printing. They range from a casting weighing several tons (whose form was printed) to the oil drip pan, an array of mounts and gears, and a titanium belt wheel that, in addition to its actual purpose, decorates the imposing- yet-elegant machine behind a covering of clear plastic.
"A Connection to what surrounds us"
When I first met Paolo Matassoni at Formnext 2019, he told me about the tremendous possibilities 3D Printing held in store for engineers like him. He also spoke of his own unique approach, which takes inspiration from nature and »the sense of connection to what surrounds us«. He described how this was enabling him to design parts optimized for additive purposes using relatively simple means thanks to the »tension it creates between the engineer and the component«. Matassoni was happy to reveal his heartfelt passion for the subject – an amiable combination of technical sophistication and philosophical techniques.
I came away from our first meeting admiring a person who was clearly and completely fulfilled by his profession, yet also maintained a hint of skepticism. Can industrial 3D Printing be that simple when you have Matassoni’s »chakra« for additive design? And if so, do you really need software solutions for component optimization – no matter how many awards and accolades they might have won?
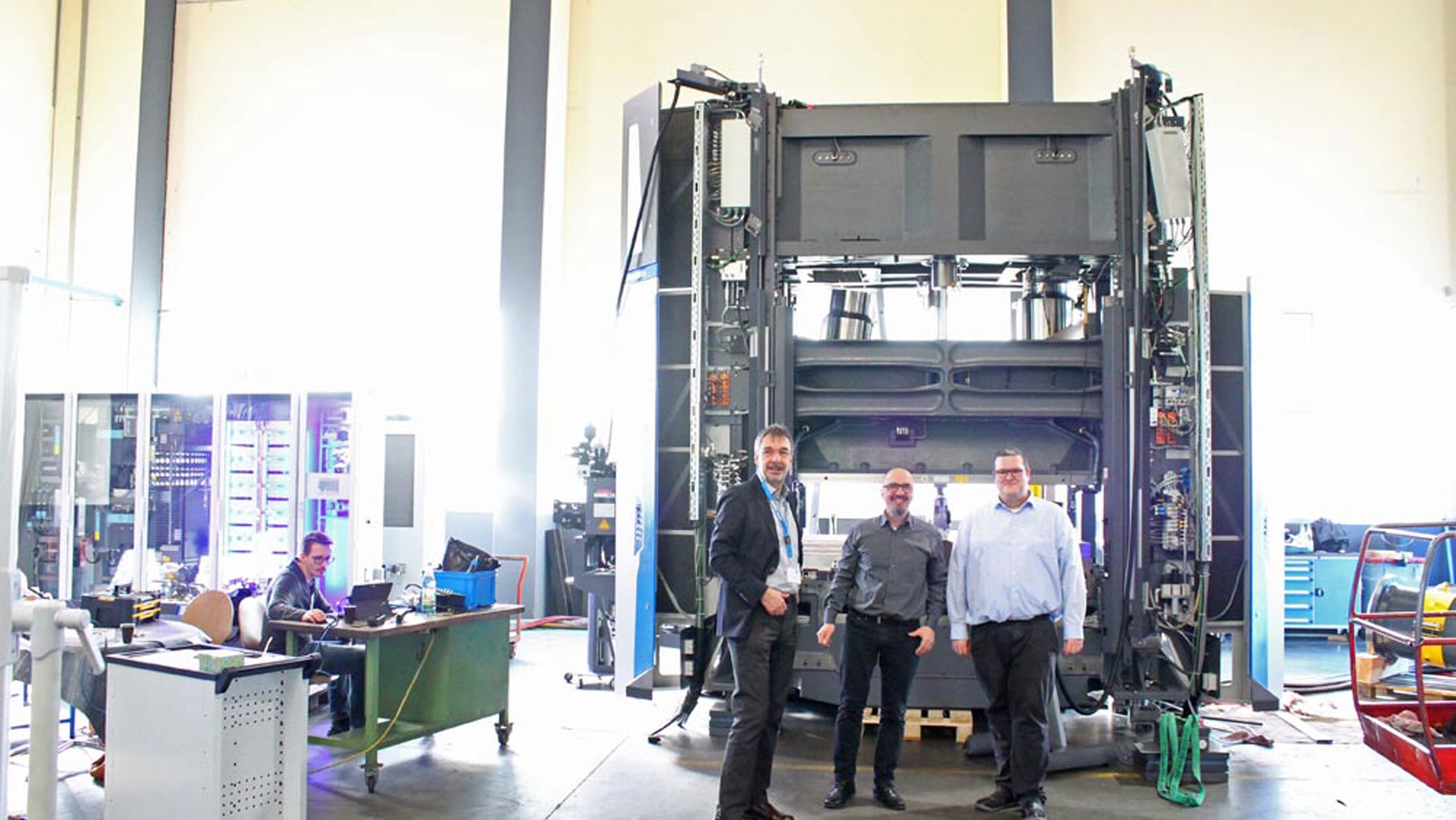
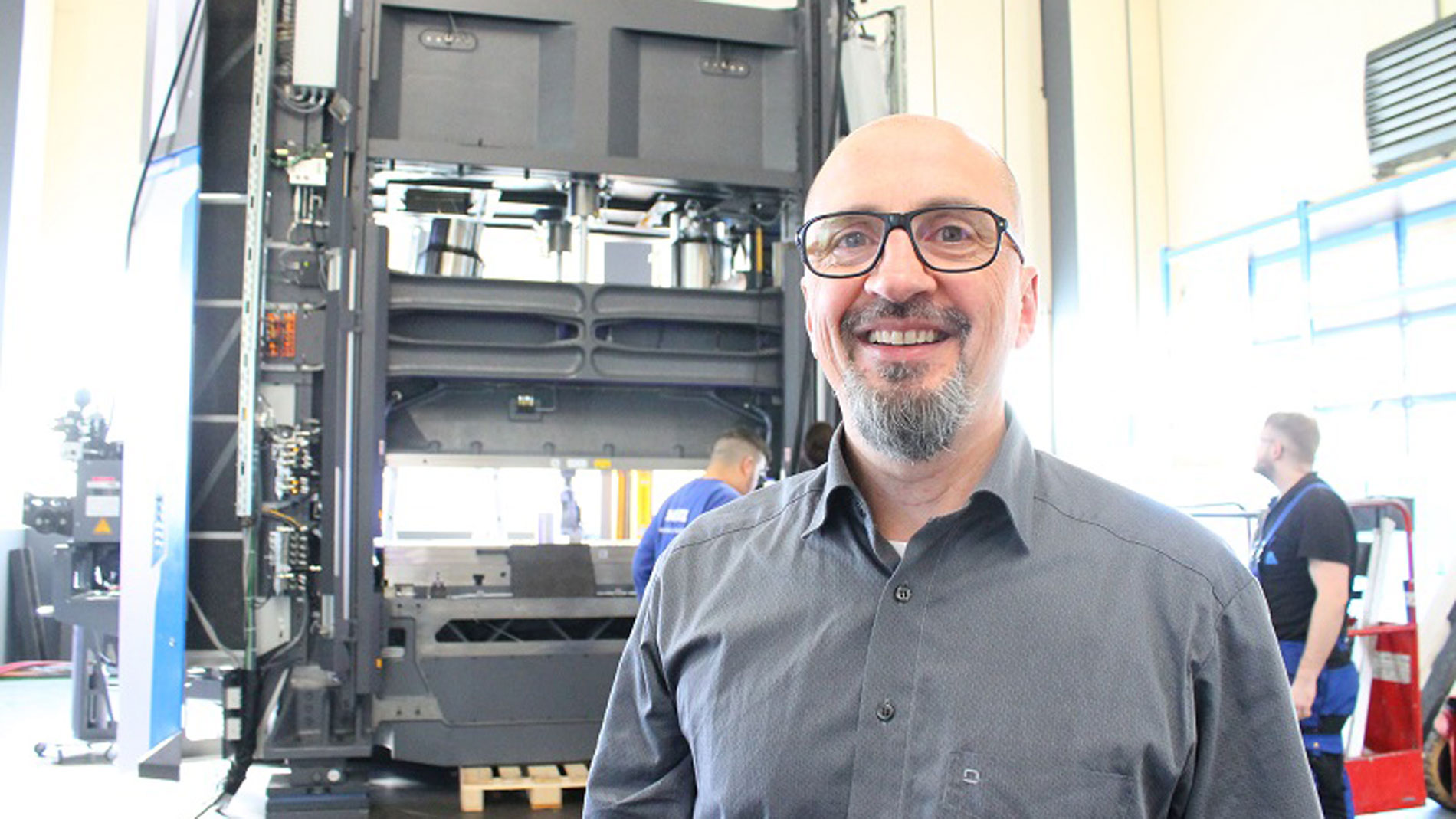
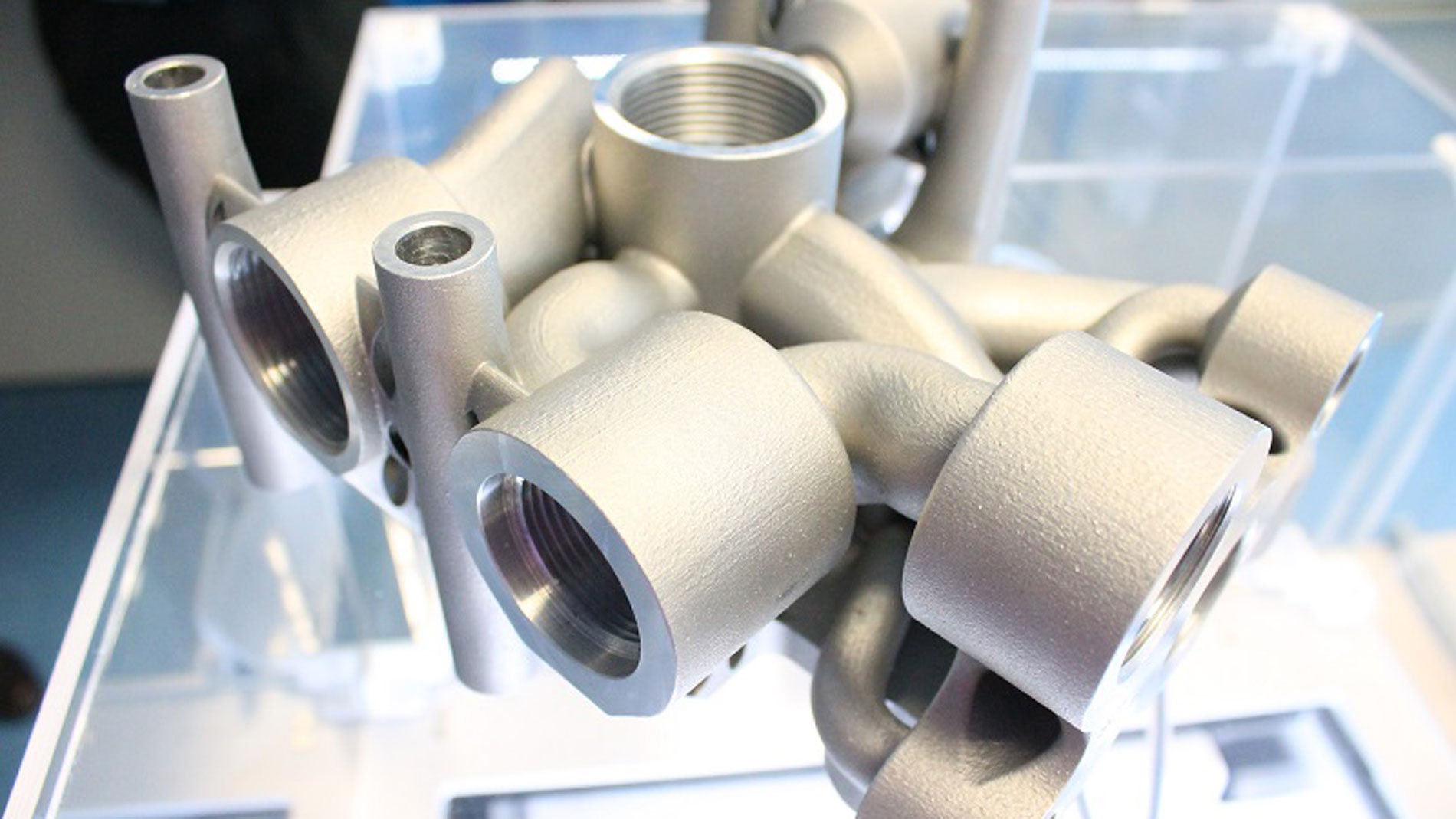
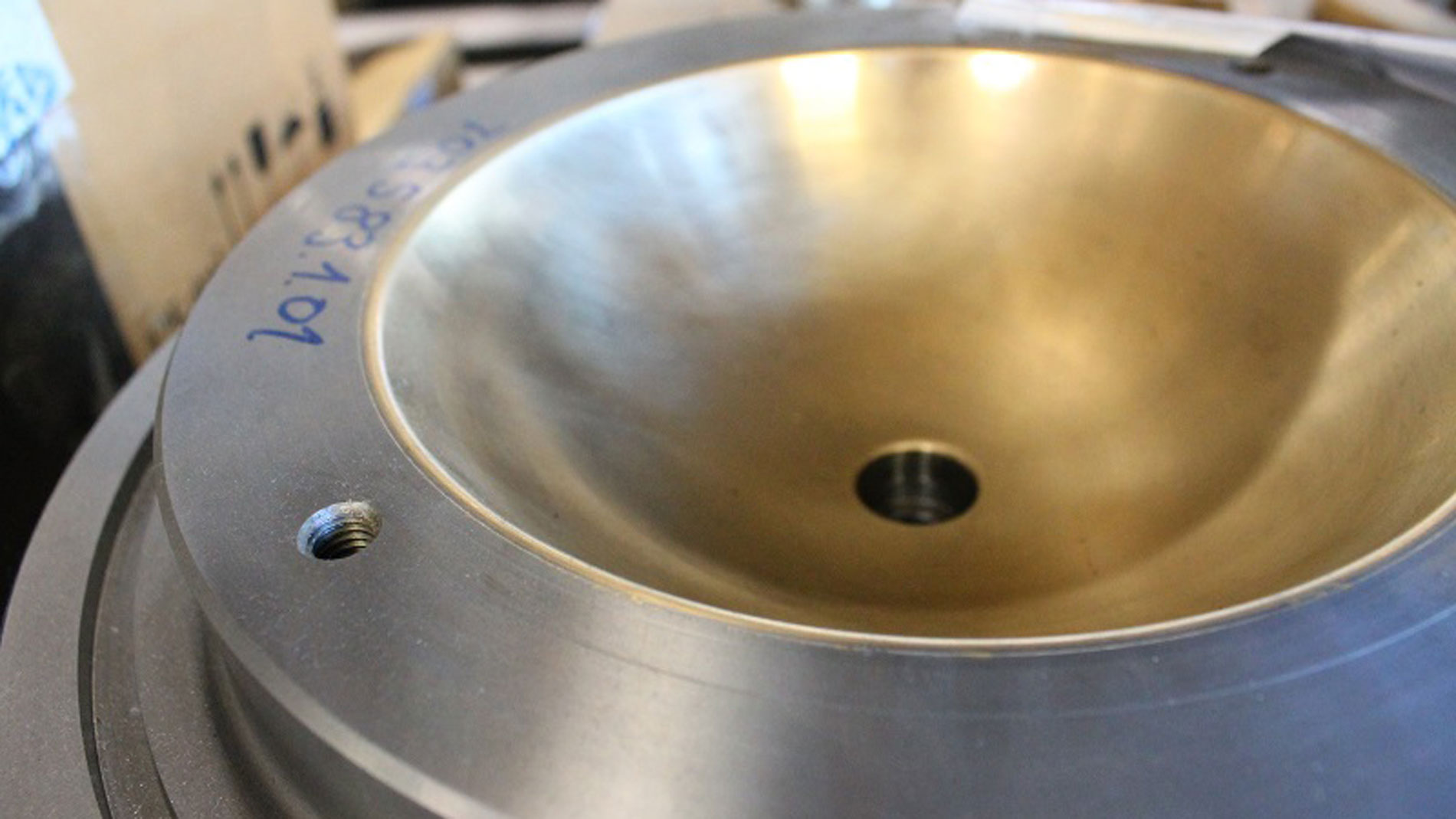
It all started with Ball Sockets
These are the questions I’m looking to have answered during my visit to the Andritz Kaiser headquarters in Bretten, which lies just a few kilometers northwest of a well-known Cistercian abbey that dates back to the Middle Ages. Along with the assembly area for large machine presses, we pass by thousands of spare parts and components as make our way through two much bigger halls. One of the countless shelves contains ball sockets around 40 centimeters wide – Matassoni’s first venture into the world of 3D Printing 10 years ago. Using a laser cladding technique, he applied an additive layer of bronze that bonded to the socket’s internal surface. An array of tests then put this coated ball socket on its path to becoming the current standard in Andritz Kaiser presses.
In addition to Matassoni’s unflagging enthusiasm for the technology, his chosen workplace is a key reason why a company whose history stretches back more than 70 years then began manufacturing more and more parts using additive methods. 3D Printing is also integral to its latest generation of products. »Back then, I wasn’t in the position I am today,« explains Matassoni, who nevertheless managed to win over the development and controlling departments, along with the executive board. »It wouldn’t have been possible at any other company; the project would have gone dormant.« Having made a name for himself as a free thinker, Matassoni »was given the freedom I needed,« as he puts it. »Then I started shocking the executives with parts that actually worked,« he adds with a grin.
It didn’t take long for managing directors Stefan Kaiser and Joachim Bolz to be intrigued by the possibilities of Additive Manufacturing. »After attending Formnext, we bought a 3D printer without knowing exactly what components we wanted to make with it,« Kaiser recalls. Besides giving their engineers the chance to get acquainted with 3D Printing, they wanted to make the jobs at the company more attractive to the technically minded. Andritz Kaiser is based in the Stuttgart region, after all, where it has to compete with industry giants like Porsche, Daimler, and Bosch for skilled personnel.
A competitive Edge in additive Innovations
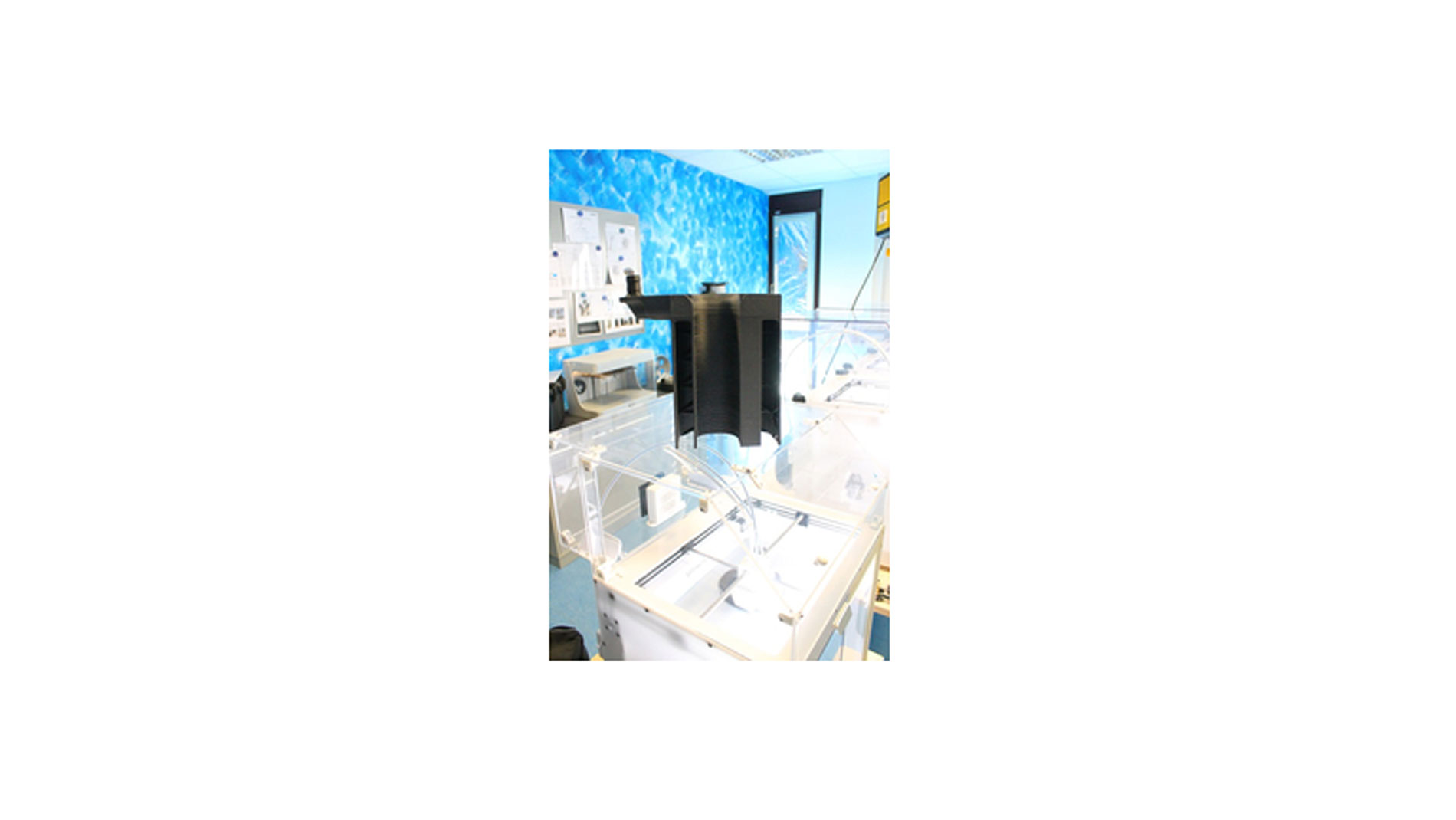
The company’s applications of additive technology are also driven by business concerns, of course. A large share of its customers operate in the automotive industry, where the rise of electric vehicles in particular had put many firms in a challenging economic situation even before the onset of the COVID-19 pandemic. For optimists like Paolo Matassoni, however, difficult circumstances like these provide »strong impetus for innovation«. In that sense, Andritz Kaiser’s business interests dovetail perfectly with its passion for Additive Manufacturing.
Innovative thinking is a high priority for Stefan Kaiser, as well. That’s why he’s sure to include the company’s 3D printing room when giving customers the tour of its facilities. »Customers obviously aren’t going to buy machine presses just because we’ve built them with 3D-printed parts, but these components do enable us to demonstrate how innovative we are,« the managing director points out. At the end of the day, he believes that can indeed encourage a customer to make a purchase.
This is how Andritz Kaiser, which manufactures around 35 presses each year, wants to use technical advancements to set itself apart from the low-cost production its competitors favor. That said, the ToP-Line 2000 represents more than just a technological improvement on the previous model. »It’s the first time we’ve ever redesigned a machine from the ground up,« Matassoni affirms, adding that past advancements had mostly been driven by customer requests.
Design Improvements in 150 additive Components
In evaluating potential innovations, Andritz Kaiser takes a clear, mathematical approach: Ideas are assessed based on individual weighted criteria that allow for a maximum score of 110 points. »We’ve gone on to implement everything that scored over 100 points,« Kaiser reports. »In the past several years, most of these ideas have involved 3D-printed parts.« Using a diagnostic matrix, the company has selected around 150 parts, improved their design, and produced them using AM methods.
»This has lowered our production costs in some cases, but above all, it’s led to a lot of technological improvements in our presses,« Matassoni reveals. The company has employed bionic design to achieve more rigidity, for example, which in turn has reduced the amount of vibration in its machines. In units that perform dozens of strokes per minute, Matassoni says this translates into a great deal of added value in terms of maintenance and useful life. Meanwhile, the ToP-Line 2000’s oil drip pan now has interior ridges that recall the pattern of human veins; these are designed to reduce consumption. »They keep lubricant from flowing upward, which can happen at high stroke rates,« explains Matassoni, who has been an active paramedic for 25 years in addition to his day job. Finally, the eye-catching titanium belt wheel has been trimmed down to 700 grams, which facilitates feed rates that are up to 30 percent faster. »Depending on the application, this can also increase the performance of the entire press by up to 30 percent,« Matassoni continues. These enhancements can be applied to presses that have already been delivered, as well.
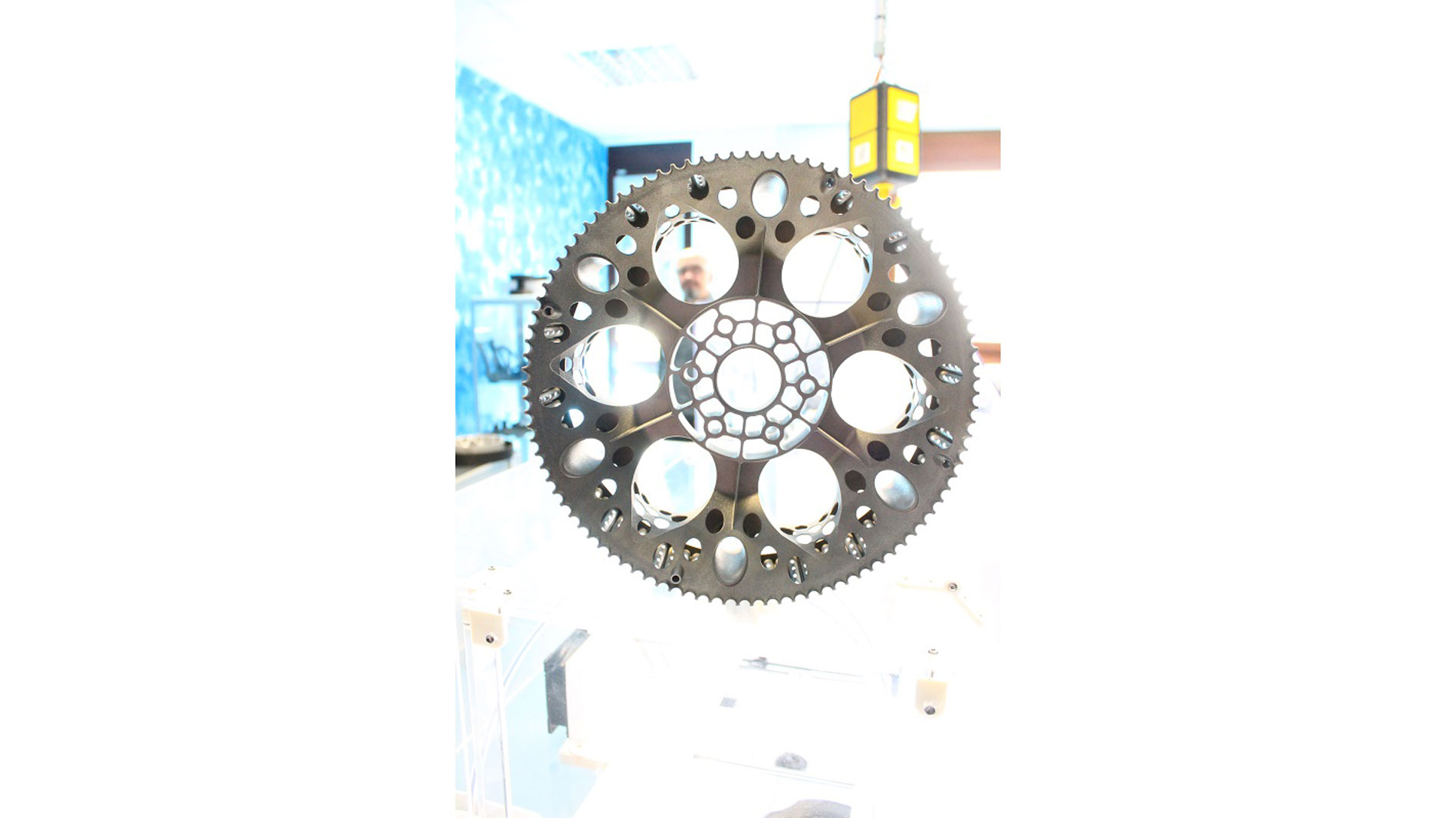
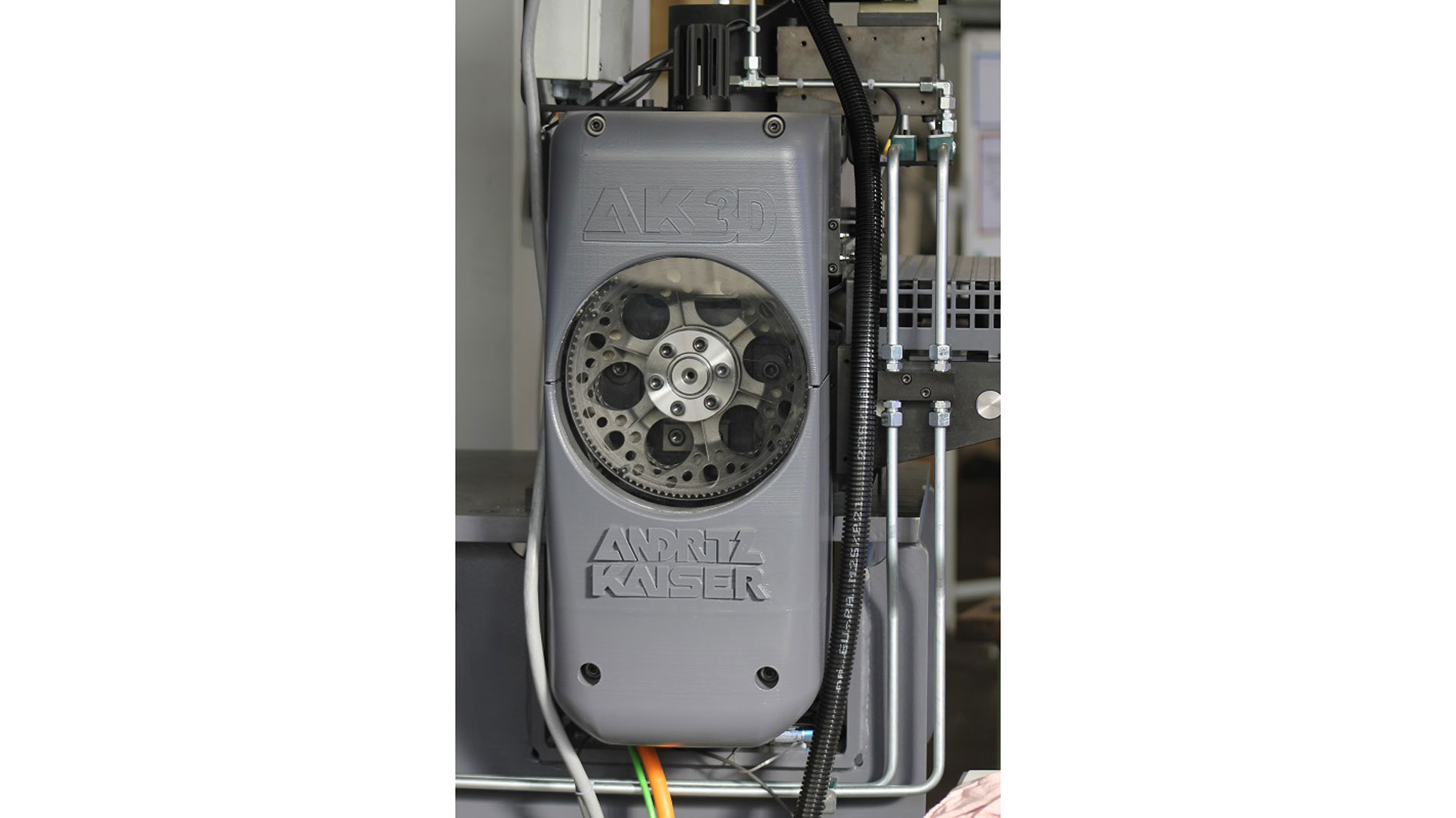
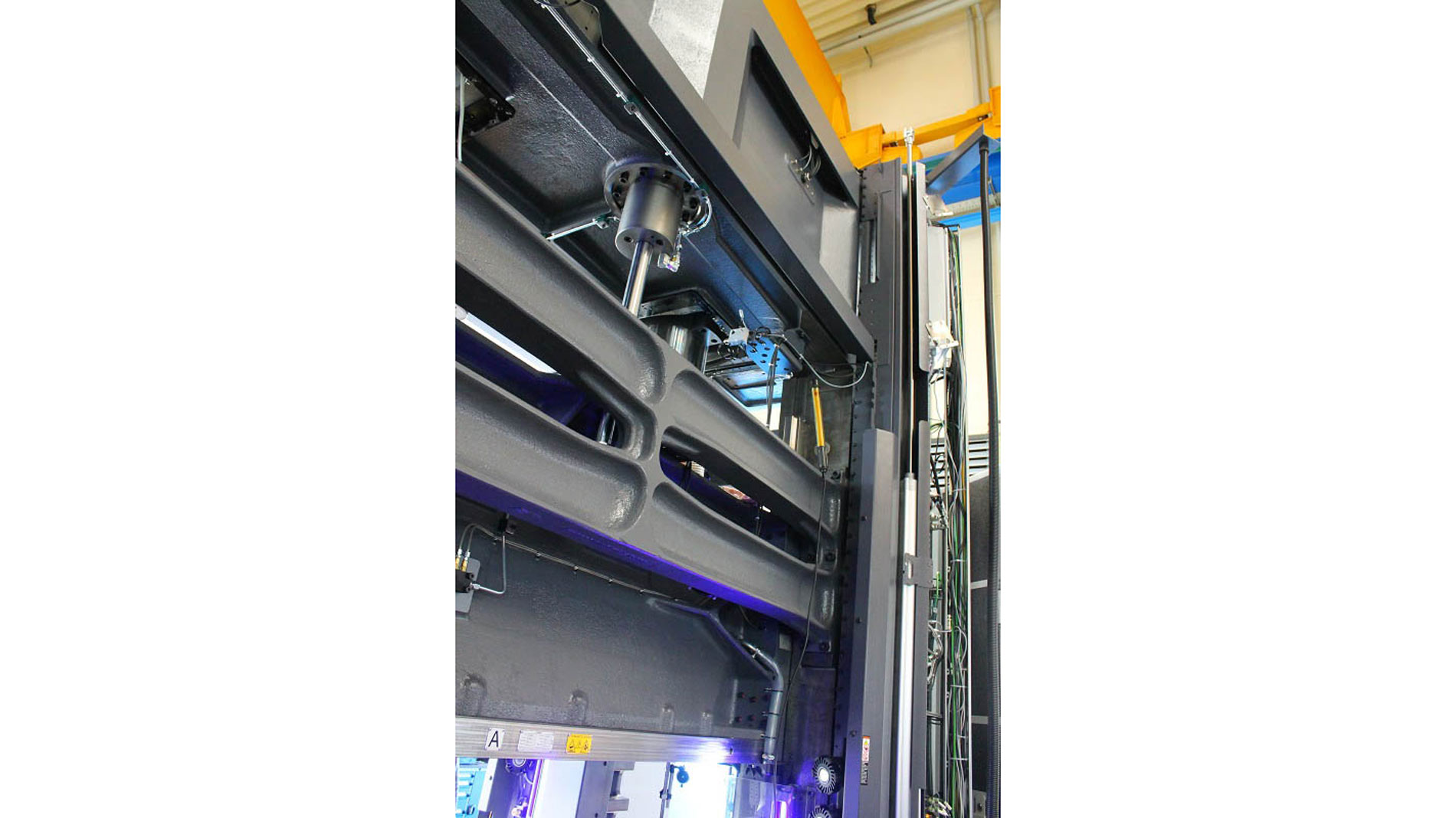
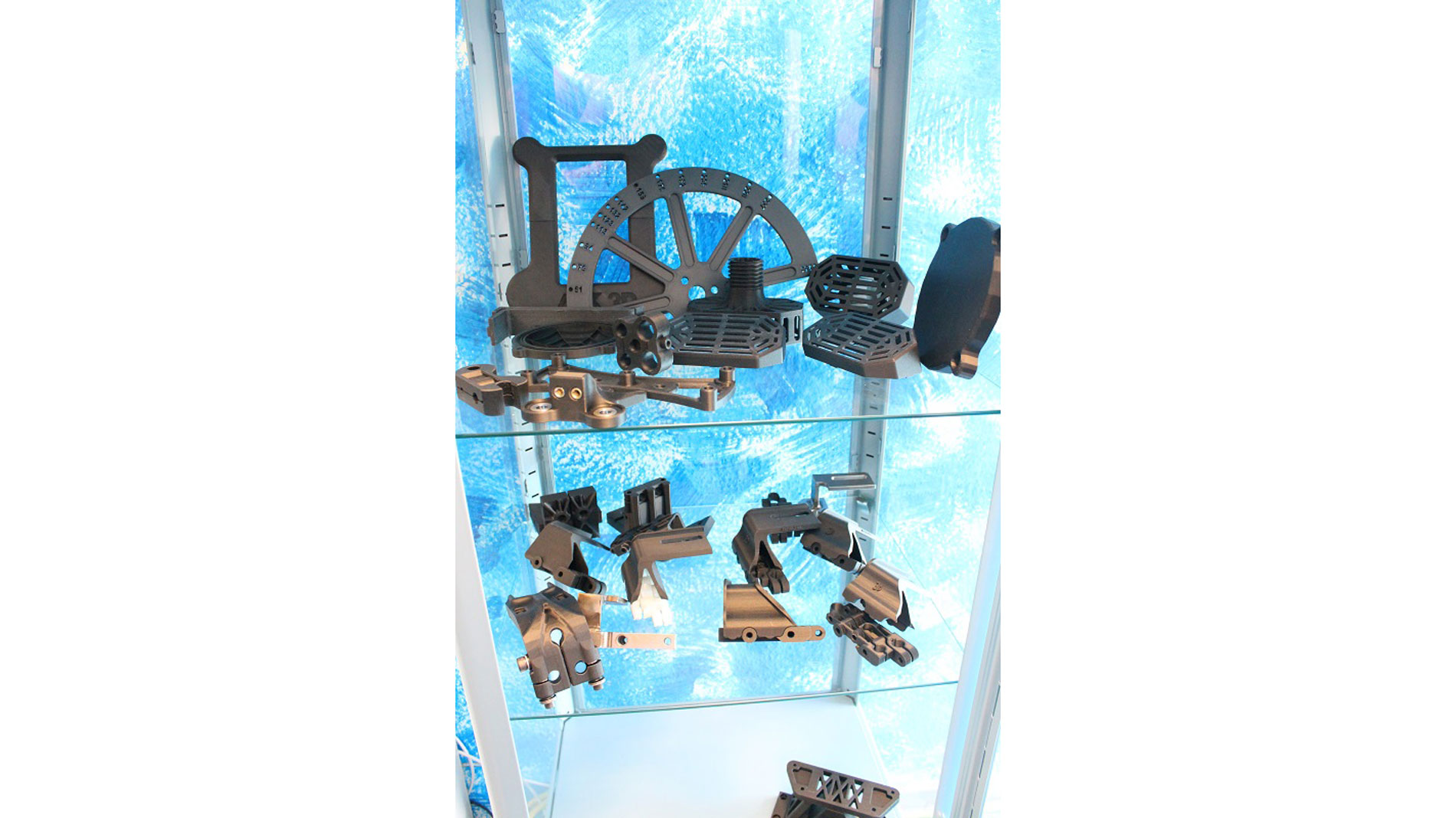
Added Value from unexpected Sources
Andritz Kaiser’s forays into Additive Manufacturing have tapped into further sources of value that Matassoni hadn’t even been counting on. The bionic shape of the ToP-Line 2000’s plunger has also proved easier to cast, for instance, which he says has resulted in higher casting quality.
»Once you adopt an additive mindset and corresponding working methods, new improvements and ideas start coming to you almost automatically,« the impassioned engineer reveals. »It’s like opening a door to a hallway full of more doors!« Matassoni describes this as an invaluable advantage in business terms, as well – one that might never be clearly quantifiable, but has become so compelling at Andritz Kaiser that the company continues to advance its efforts in AM. These are soon to include further training in 3D printing for employees in production and assembly. Serving as the guiding concept will be Professor Claus Mattheck’s book Körpersprache der Bauteile (»The Body Language of Components«), which imparts a unique understanding of mechanics, lightweight design, and deformation with the help of river pebbles, mountains, bones, and a bear named Pauli.
Less than five Euros per Hours
The operational center of AM production at Andritz Kaiser is located in a 20-square-meter space at the end of an office hallway. Here, we find a row of five FDM desktop printers that Matassoni and his young colleague Manuel Motzer use to produce test components, along with all the plastic parts they need. »These machines operate at a rate of less than five euros per hour,« Motzer says. »Other technologies just can’t compete.«
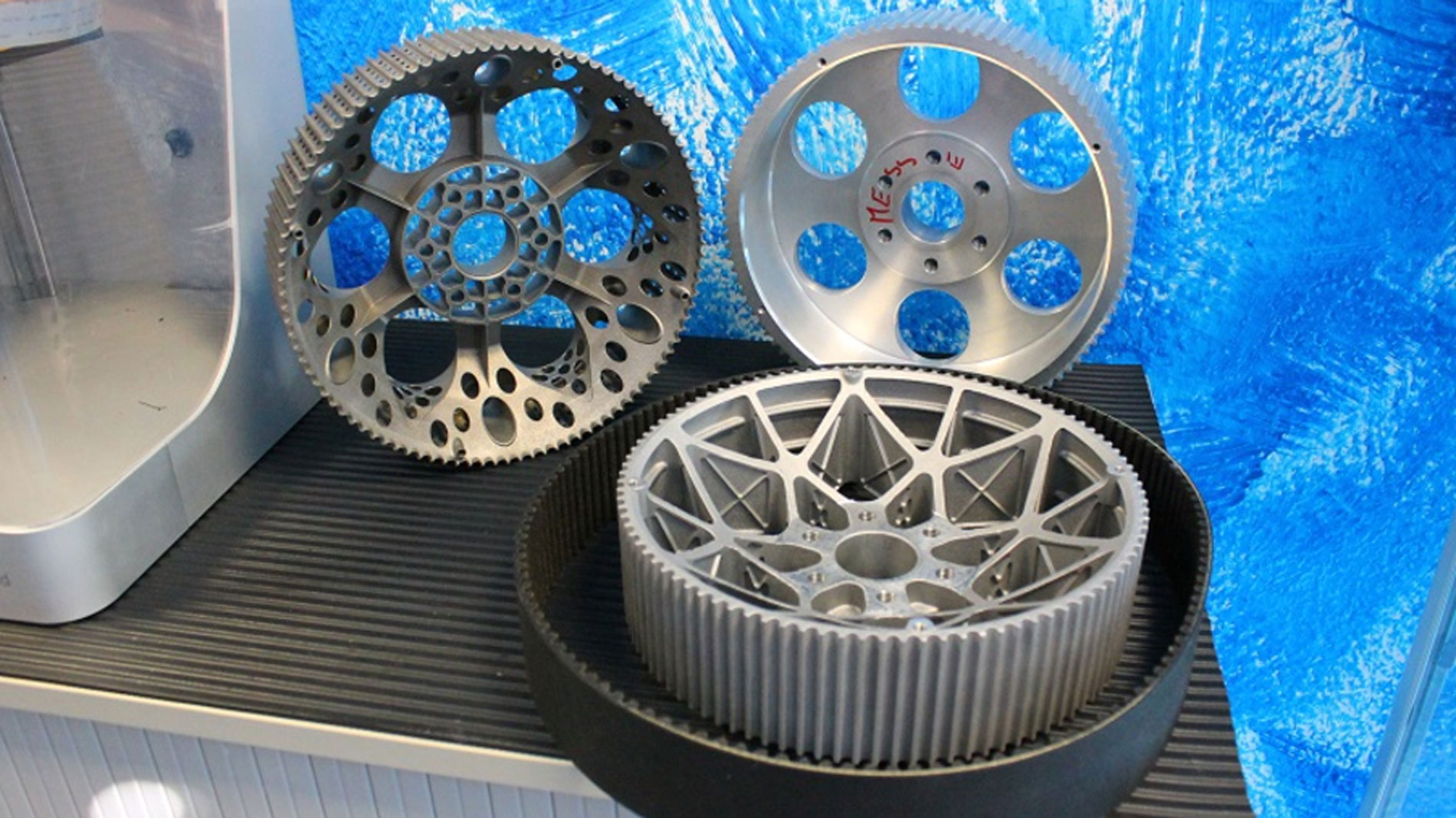
Corresponding CAD models are created on screen two doors away in the development and design engineering department. While the AM departments of other companies use specialized software to calculate bionic optimizations, Matassoni and Motzer are entirely old-school: They do things »by hand and gut instinct« with the conventional (and parameter-free) CAD program One Space Designer and figure out the rigidity of their creations using the finite element method. For Matassoni, this saves both time and money, which can be decisive factors for a traditional midsize company when it comes to adopting new technology.
»I wouldn’t have thought so in the beginning either, but we don’t need those additive optimization programs,« he says. »After all, all the problems we run into in mechanical engineering are exactly the same in nature.« This is what inspired the creation of the oil drip pan, the titanium belt wheel, and the curves of the press’s plunger. Matassoni crossed paths with the belt wheel’s design, which resembles a tortoise’s shell, while on a hiking vacation in Spain.
Many more components are sure to follow at the company’s headquarters in Bretten. »Additive manufacturing is a passion of mine; it fits the way I think,« explains Matassoni, who continues to take inspiration from the technical possibilities and creative freedom AM offers in new projects. All his ideas have led to a bit of a problem, however: »I’ve had to accept the fact that I’ll never be able to realize them all in my lifetime!«
Andritz Kaiser GmbH
Based in Bretten (Baden-Württemberg), Germany, Andritz Kaiser GmbH has belonged to the international Andritz group since 2004. It currently employs around 140 people. The company, which has been building on a tradition of excellence for 75 years, manufactures products that include stamping and metal-forming presses capable of generating up to 25,000 kilonewtons of force and eight megawatts of drive power. In the automotive industry (for example), a single press can produce as many as 2.5 million body components per year.
andritz.com
Tags
- Additive Manufacturing