Text und Fotos: Thomas Masuch — 08.06.2020
Bei der Neugestaltung ihrer neuesten mechanischen Presse hat Andritz Kaiser GmbH die Innovationskraft von additiver Fertigung und bionischem Design genutzt. Zahlreiche Mehrwerte entstanden aus einem einmaligen Zusammenspiel von Unternehmensstrategie, der Begeisterung für industriellen 3D-Druck und der Inspiration durch die Natur.
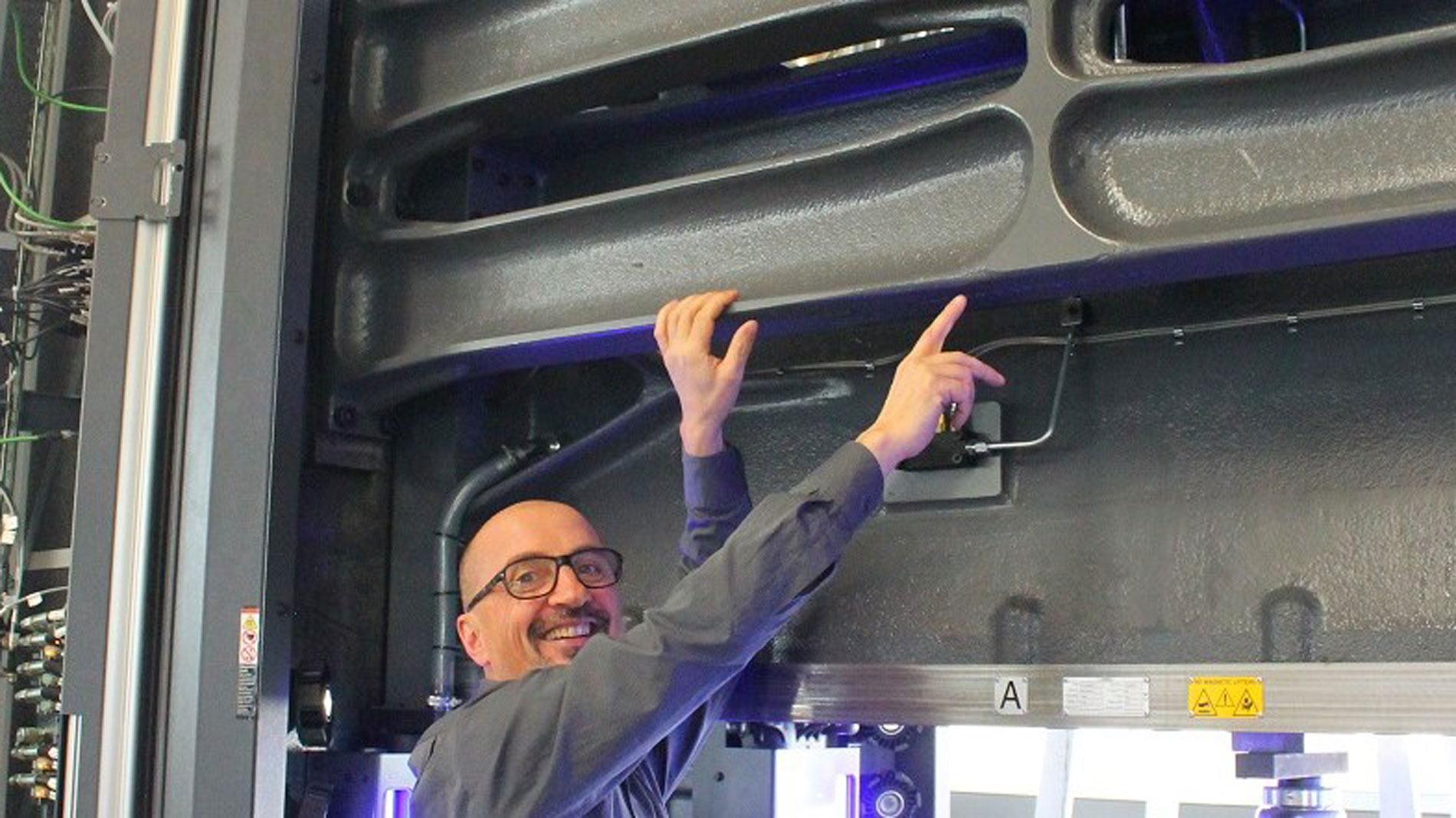
An der Stirnseite der Produktionshalle, in Nachbarschaft zu den anderen haushohen stählernen Kolossen, wirkt die 30 Tonnen schwere »ToP-Line 2000« wie ein stylisches Designerstück. Hier, im eigens für die moderne mechanische Presse hergerichteten Vorführbereich, zeigt Design-Vater Paolo Matassoni in die Höhe auf den 3,5 Tonnen schweren Stößel und fragt: »Erkennen Sie den Bachkiesel wieder?«
An einem Ort, wo der Geruch nach Öl und Stahl die Luft durchsetzt und das Auge auf stählerne Kolosse trifft, die in den nächsten zwanzig und mehr Jahren immer wieder mit tonnenschweren Kräften Metallbleche verformen, erscheint der Gedanke an einen Bachkiesel weit hergeholt. Doch trotzdem waren solch runde Steinchen und andere Objekte aus Flora und Fauna für Matassoni gestalterisches Leitbild und Ideengeber. Zahlreiche Bauteile der neuen Pressengeneration aus Bretten sind danach entstanden. »Viele Designs sind ja durch die Natur schon vorgegeben, wir kopieren nur«, erklärt der Entwicklungsleiter der Andritz Kaiser GmbH. Die runden und fließenden Übergänge sowie die bionischen Formen konnte der 52-jährige Techniker umsetzen, weil er schon seit Jahren von den Möglichkeiten des 3D-Drucks begeistert ist und weil er und sein Team die additive Denkweise verinnerlicht haben.
"Wenn man einmal anfängt, additiv zu denken und zu arbeiten, folgen fast automatisch weitere neue Verbesserungen und Ideen."
Insgesamt 150 Bauteile der »ToP-Line 2000« sind mithilfe des 3D-Drucks entstanden; das reicht vom tonnenschweren Gussteil, dessen Form 3D-gedruckt wurde, über zahlreiche Halterungen, Zahnräder und der Ölfangschale bis hin zum Riemenrad aus Titan, das als funktionales Schmuckstück hinter einer transparenten Kunststoffplatte die wuchtig-elegante Maschine schmückt.
"Verbundenheit zu dem, was um uns ist"
Als ich Paolo Matassoni das erste Mal auf der Formnext 2019 traf, berichtete er von den großartigen Möglichkeiten, die der 3D-Druck einem Ingenieur wie ihm gebe, und auch von seiner besonderen Herangehensweise, die einerseits von der Inspiration durch die Natur geprägt ist und »von der Verbundenheit zu dem, was um uns ist.« Das ermögliche ihm, mit vergleichsweise einfachen Mitteln additiv optimierte Bauteile zu konstruieren, wenn »ein Spanungsfeld zwischen Konstrukteur und Bauteilen entsteht«. Matassoni offenbart gern seine innige Begeisterung, die technische Raffinessen und philosophische Ansätze wohlwollend umschließt.
Dieses erste Treffen hinterließ bei mir eine Bewunderung für jemanden, der offenbar die kompromisslose Erfüllung in seinem Beruf empfindet, gemischt mit einer Prise Skepsis. Kann industrieller 3D-Druck so einfach sein, wenn man wie Matassoni das »Chakra für additive Konstruktion« hat? Und sind dann die teilweise gepriesenen und mit Awards ausgezeichneten Softwarelösungen zur Bauteiloptimierung überflüssig?
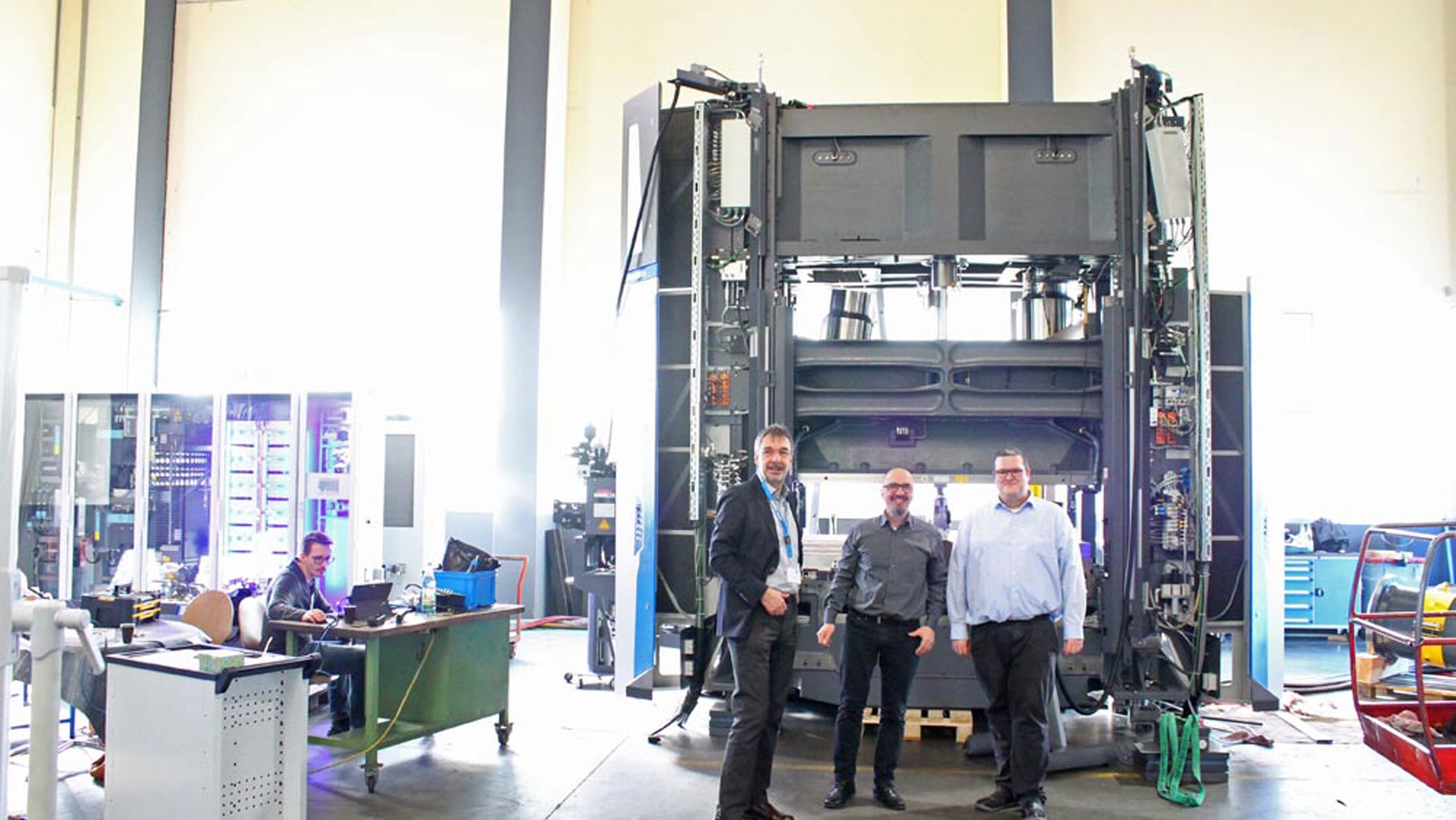
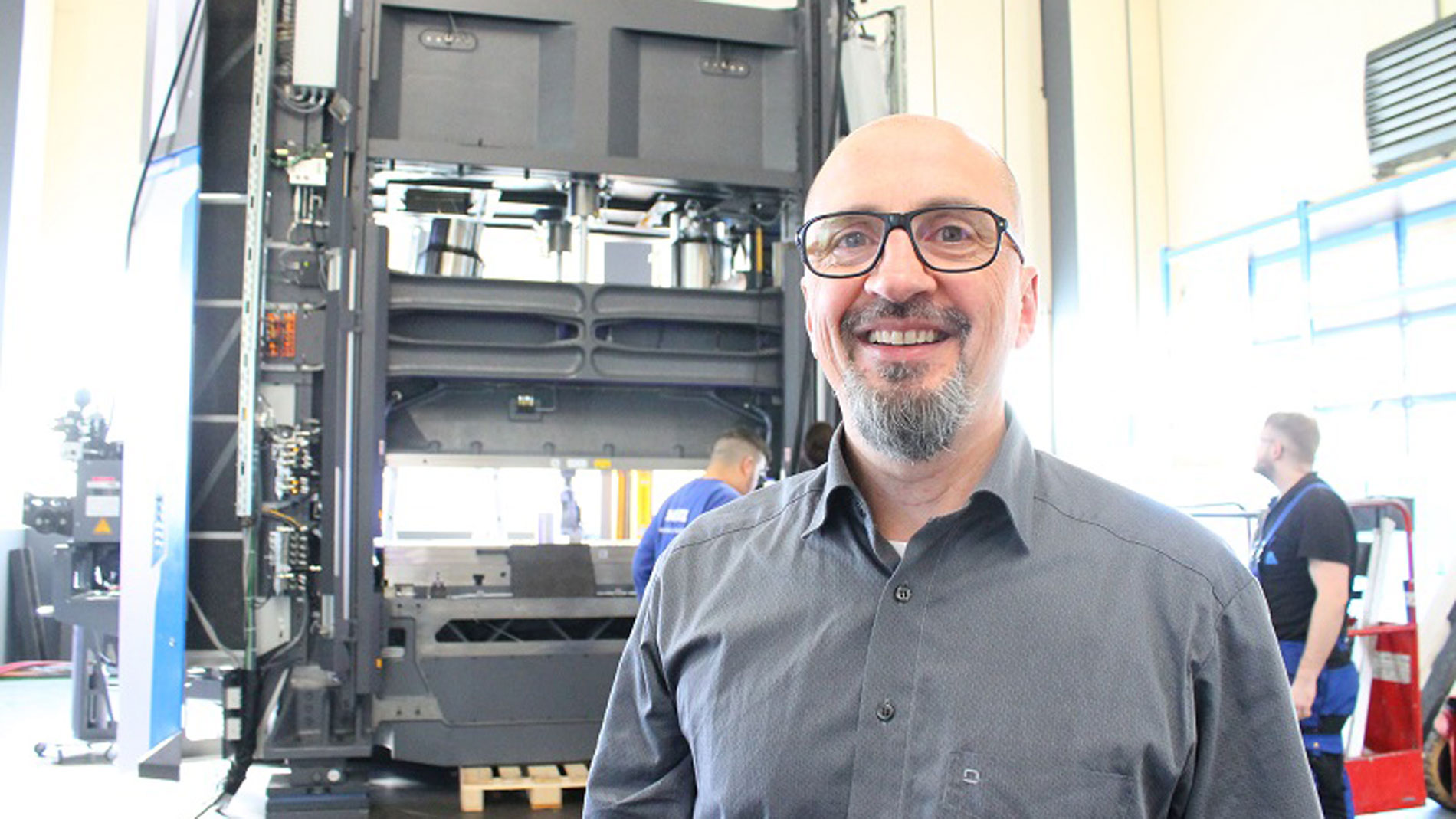
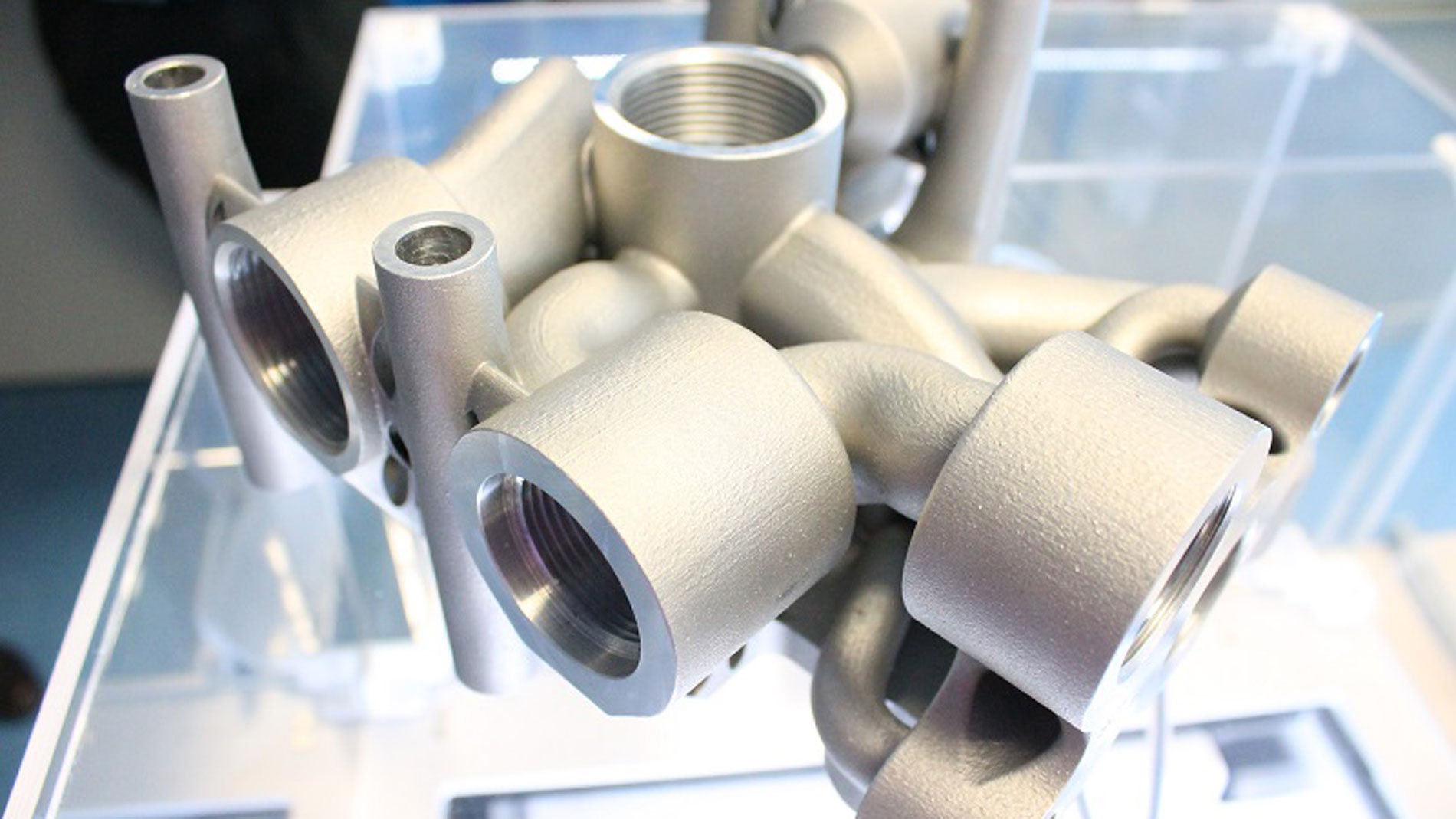
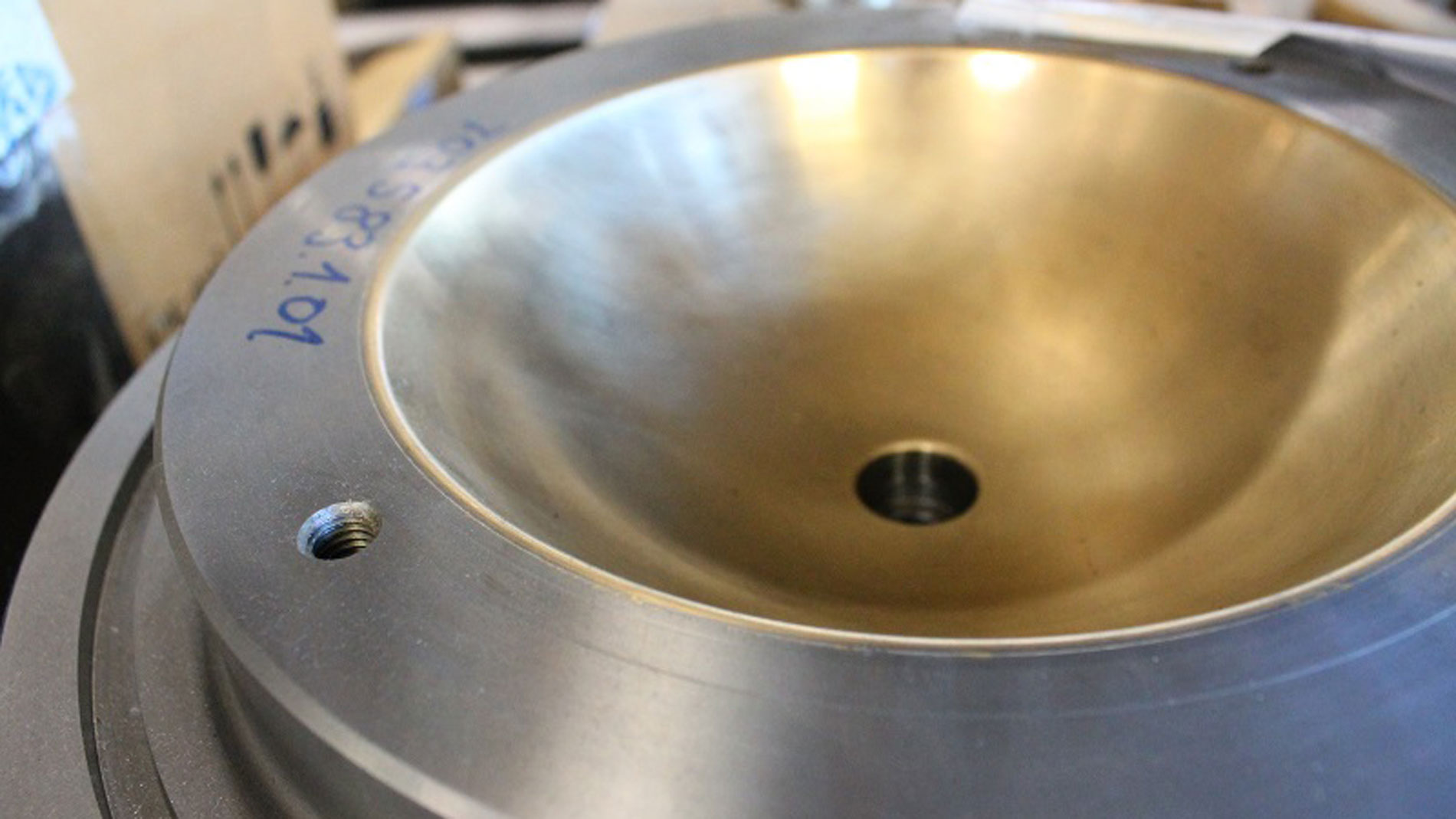
Mit der Kugelpfanne fing es an
Beantwortet werden die Fragen bei einem Besuch am Firmensitz von Andritz Kaiser in Bretten, nur wenige Kilometer entfernt von der berühmten mittelalterlichen Klosteranlage der Zisterzienser in Maulbronn. Neben der Montagehalle für die großen mechanischen Pressen durchschreiten wir zwei deutlich größere Hallen entlang Tausender Einzel- und Ersatzteile sowie Komponenten. In einem der zahllosen Regale liegt eine rund 40 Zentimeter breite Kugelpfanne, mit der sich Matassoni bereits vor 10 Jahren auf den Weg des 3D-Drucks begab. Die Innenfläche ließ er per Laserauftragsschweißen additiv beschichten. Die Bronzeschicht verband sich fest mit der Unterlage, und nach zahlreichen Prüfungen ist die beschichtete Kugelpfanne heute Standard in den Pressen von Andritz Kaiser.
Dass ein Traditionsbetrieb mit über 70-jähriger Geschichte danach immer mehr Teile additiv fertigte und nun seine neueste Produktgeneration durchgehend vom 3D-Druck geprägt ist, liegt neben Matassonis ausdauernder Begeisterung für diese Technologie auch an dem Umfeld, in dem er bei Andritz Kaiser beruflich aufgehoben ist. »Ich war damals noch nicht in der Position wie heute«, erinnert er sich, doch er schaffte es, die Entwicklungsabteilung, das Controlling und die Geschäftsführung zu überzeugen. »Das ging nur in diesem Unternehmen, woanders wäre das Projekt eingeschlafen. « Matassoni hatte sich als Freigeist einen Namen gemacht, »und so bekam ich die nötigen Freiheiten. Und dann schockte ich die Geschäftsführung mit Teilen, die funktionierten «, schmunzelt er.
Auch die Geschäftsführer Stefan Kaiser und Joachim Bolz waren früh von den Möglichkeiten der additiven Fertigung angetan. »Nach einem Besuch auf der Formnext haben wir einen 3D-Drucker gekauft, ohne genau zu wissen, welche Teile wir damit fertigen wollten«, erinnert sich Kaiser. Die Ingenieure im Unternehmen sollten sich mit dem 3D-Druck einfach beschäftigen, zudem sollten die Arbeitsplätze für Techniker attraktiver werden. Schließlich muss sich Andritz Kaiser beim Kampf um Fachkräfte in der Stuttgarter Region gegen Branchenriesen wie Porsche, Daimler oder Bosch behaupten.
Additive Innovationskraft als Wettbewerbsfaktor
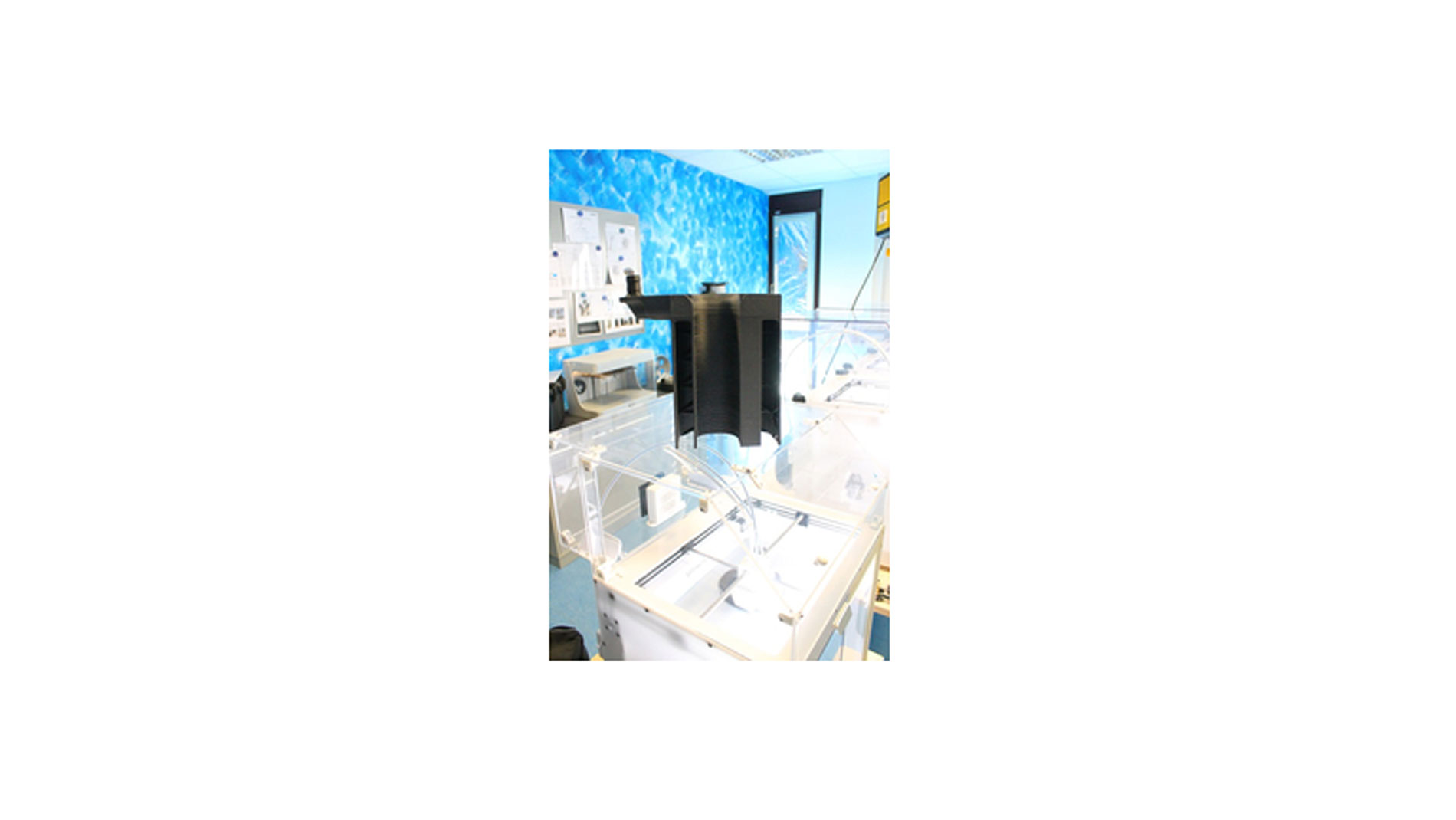
Bei Andritz Kaiser in Bretten hat der Einsatz der additiven Technik natürlich auch einen geschäftlichen Hintergrund. Ein Großteil der Kunden stammt aus der Automobilindustrie, und hier war die wirtschaftliche Situation für viele Unternehmen vor allem durch die Elektrifizierung auch vor der Corona-Krise schon herausfordernd. Doch wer positiv denkt, wie Paolo Matassoni, sieht in der »besonderen wirtschaftlichen Situation einen starken Antrieb für Innovationen«. So gehen additive Leidenschaft und geschäftliche Interessen des Unternehmens eine stimmige Symbiose ein.
Auch für Geschäftsführer Stefan Kaiser hat innovatives Denken einen hohen Stellenwert. Deshalb führt er Kunden bei einem Firmenrundgang auch in den 3D-Druck-Raum. »Sicherlich kaufen die Kunden keine Presse, nur weil da jetzt 3D-gedruckte Teile verbaut sind, aber wir können anhand dieser vielen additiv gefertigten Bausteine unsere Innovationskraft unter Beweis stellen.« Und letztendlich könne das dann auch das Kaufverhalten eines Kunden positiv beeinflussen.
Und so will sich das Unternehmen mit einer Jahresproduktion von rund 35 Pressen durch technische Entwicklungen von der relativ günstig produzierenden Konkurrenz abheben. Die »ToP-Line 2000« ist dabei nicht nur eine technologische Weiterentwicklung des Vorgängermodells. »Zum ersten Mal haben wir eine Maschine von Grund auf neu konzipiert«, erklärt Matassoni. In der Vergangenheit seien Weiterentwicklungen meist von Kundenwünschen ausgegangen.
150 additive Bauteile konstrutiv verbessert
Bei der Bewertung von möglicher Innovationen verfolgt man bei Andritz Kaiser einen klaren, mathematischen Ansatz: Ideen werden nach einzelnen, gewichteten Kriterien benotet und können so eine Maximalpunktzahl von 110 erreichen. »Alles, was über 100 Punkte war, haben wir umgesetzt«, erklärt Kaiser. Und diese Auswahl bestand in den letzten Jahren überwiegend aus 3D-gedruckten Teilen. « Mithilfe eines diagnostischen Gitters wurden rund 150 Bauteile ausgewählt, konstruktiv verbessert und letztlich additiv gefertigt.
»Das hat teilweise Produktionskosten gespart, aber vor allem zu zahlreichen technologischen Verbesserungen der Presse geführt«, schwärmt Matassoni. Durch das bionische Design konnte die Steifigkeit erhöht und damit die Schwingungen reduziert werden. Das erzeuge bei Dutzenden Hüben pro Minute einen großen Mehrwert in Bezug auf Lebensdauer und Wartung. Bei der Ölfangschale haben innenliegende Rippen, die an die Struktur menschlicher Venen erinnern, den Verbrauch reduziert. »Damit wird verhindert, dass aufgrund der schnellen Hubbewegungen Schmieröl nach oben fließt«, erklärt der Techniker, der neben seinem Beruf seit 25 Jahren als Rettungssanitäter aktiv ist. Und das optisch ansprechende Riemenrad aus Titan ermöglicht durch sein auf 700 Gramm reduziertes Gewicht einen bis zu 30 Prozent schnelleren Vorschub. »Das kann je nach Anwendung die Leistung der gesamten Presse um bis zu 30 Prozent erhöhen.« Auch bereits ausgelieferte Pressen können damit nachgerüstet werden.
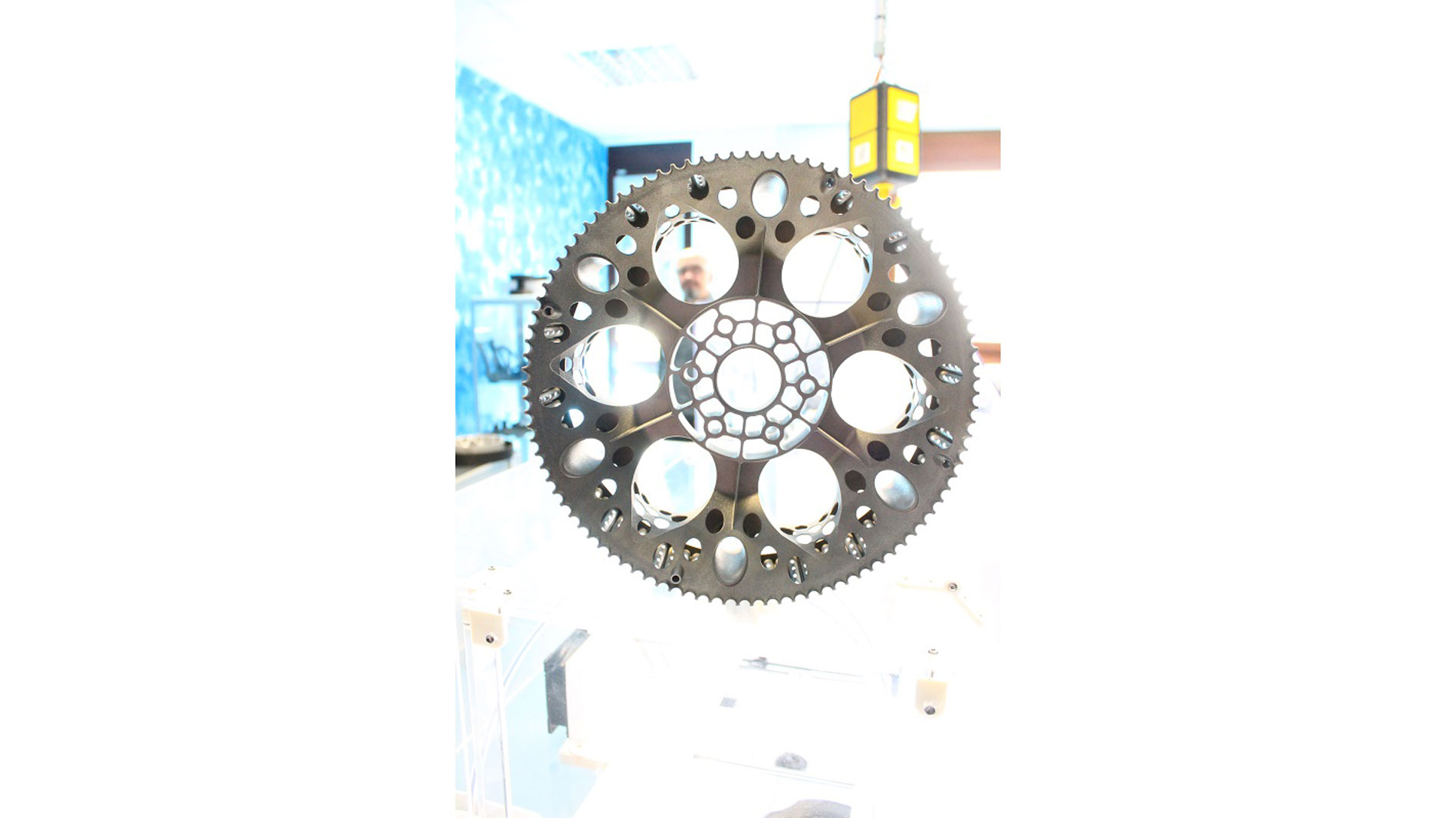
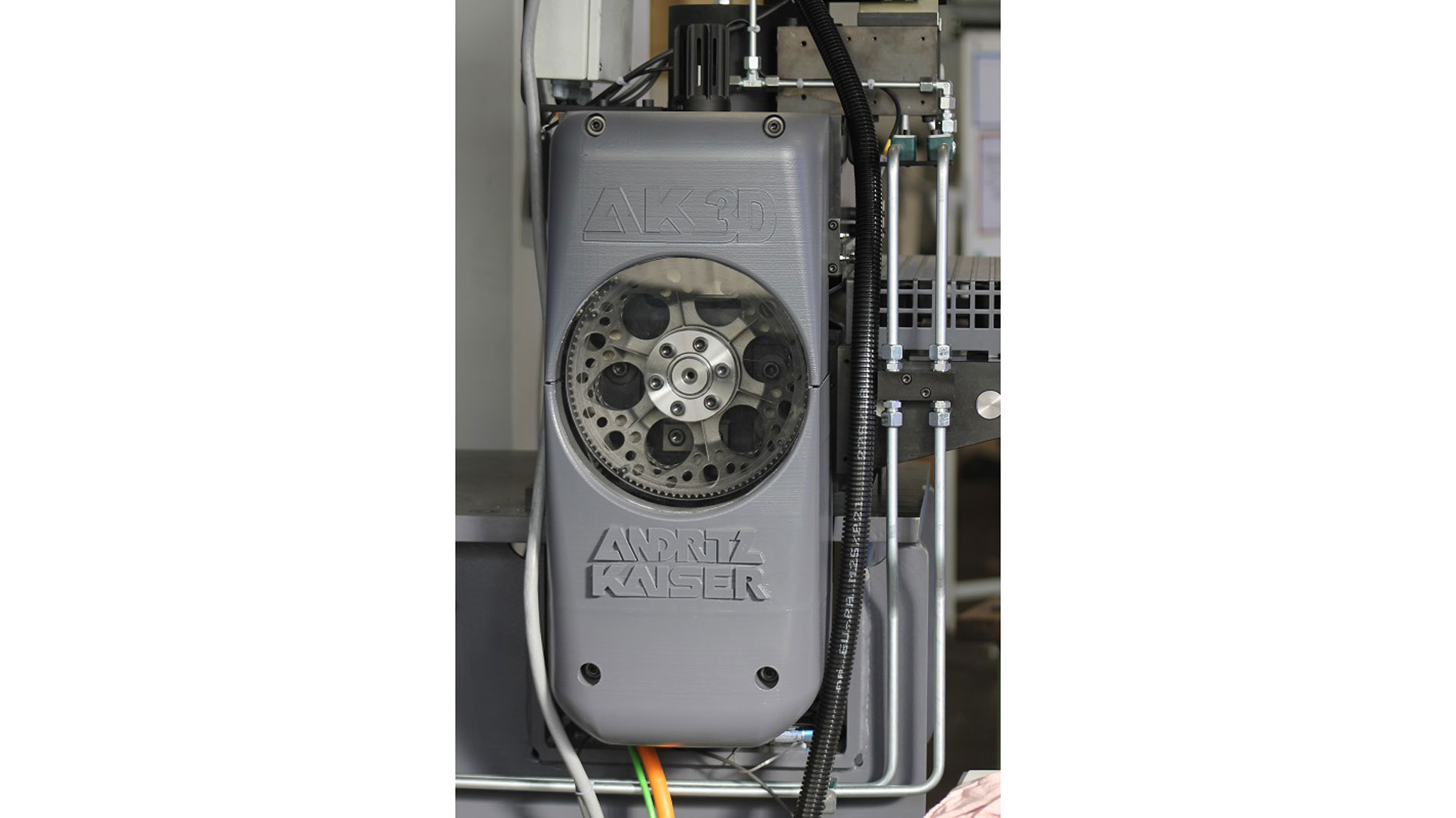
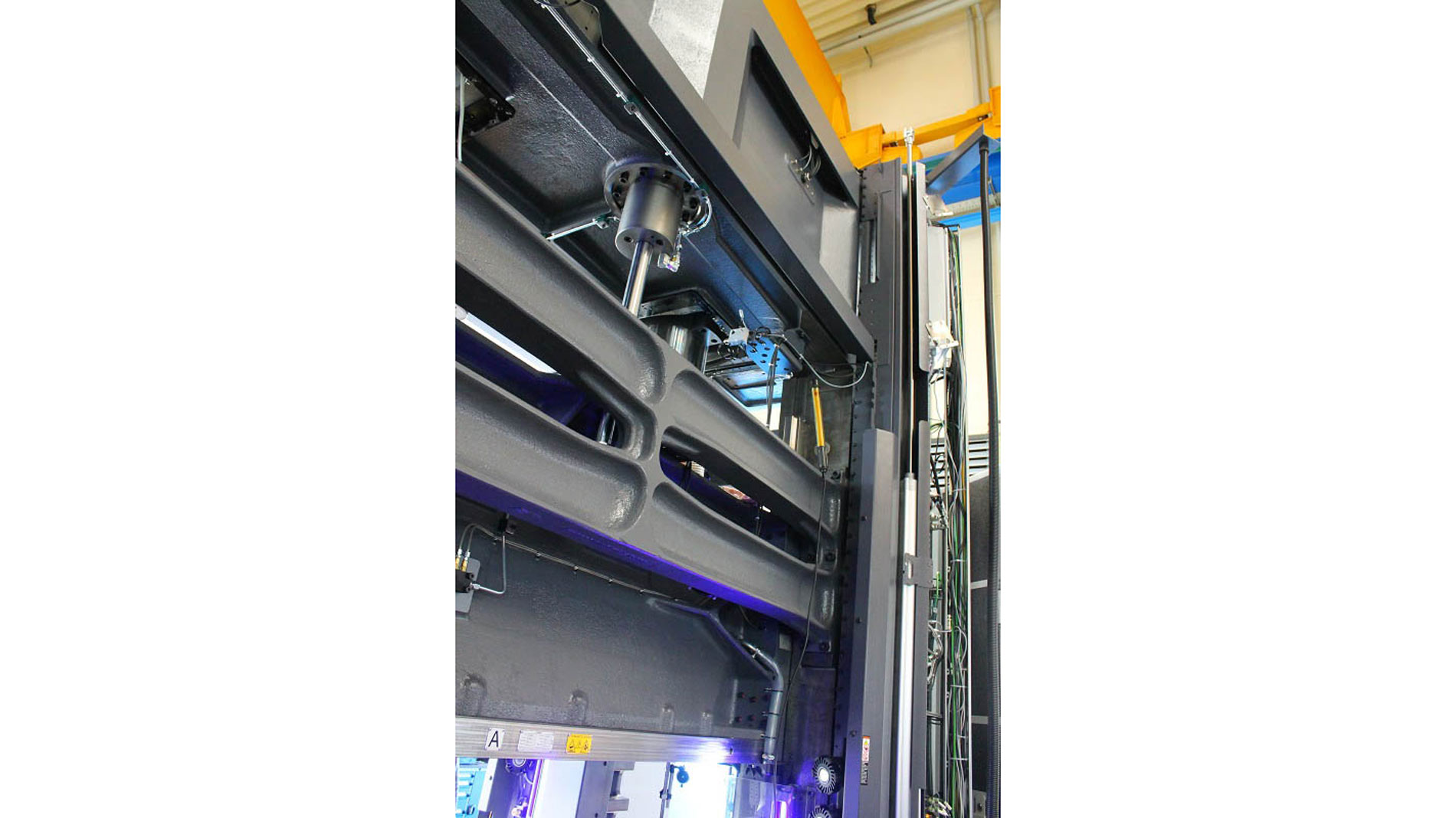
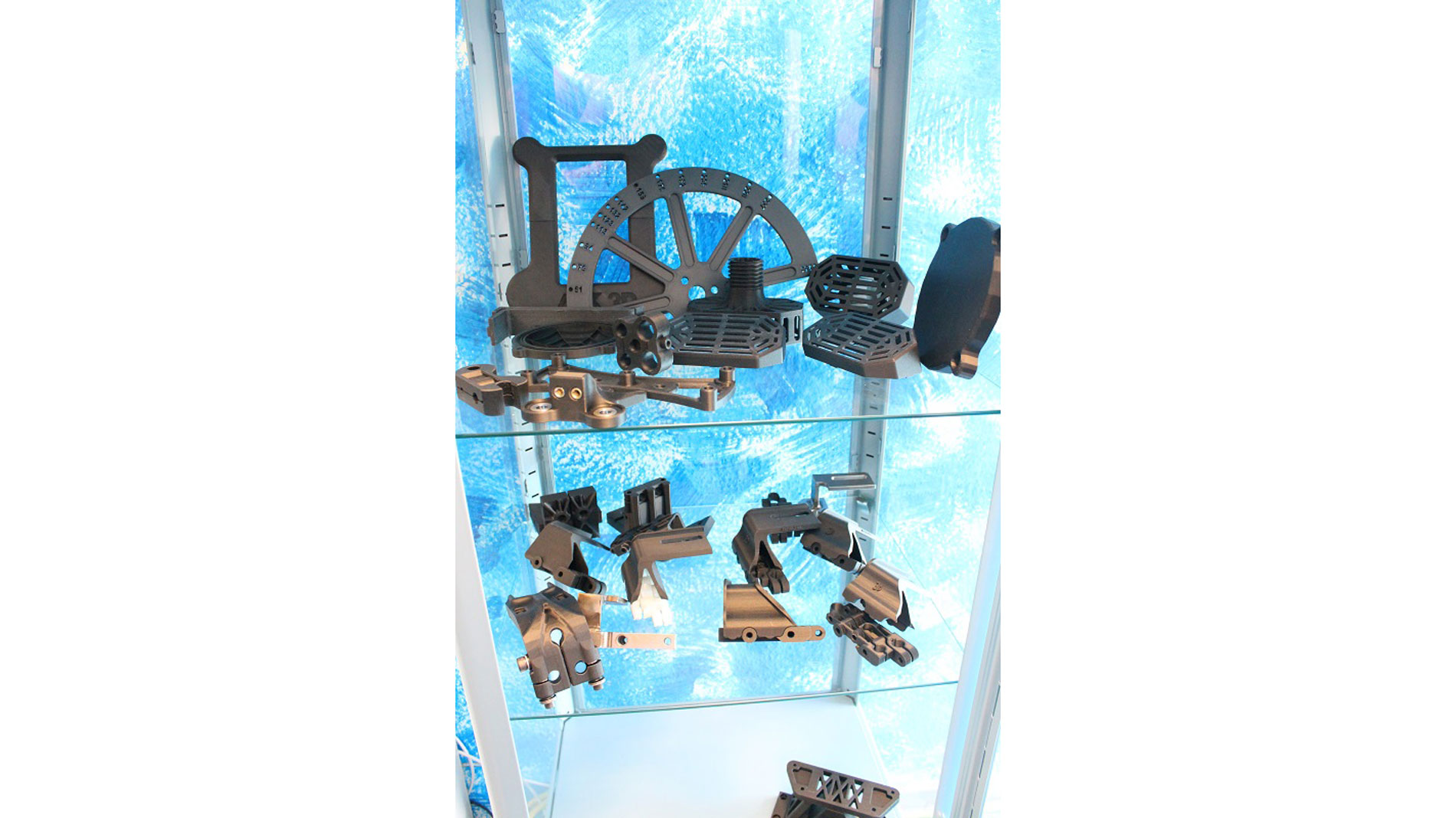
Vorher nicht geplante Mehrwerte
Durch die Beschäftigung mit additiver Fertigung haben sich in Bretten weitere Mehrwerte ergeben, mit denen Matassoni vorher gar nicht gerechnet hatte: Der bionisch geformte Stößel lasse sich zum Beispiel besser gießen, was die Gussqualität erhöht habe.
»Wenn man einmal anfängt, additiv zu denken und zu arbeiten, folgen fast automatisch weitere neue Verbesserungen und Ideen«, erklärt der begeisterte Techniker. »Man öffnet eine Tür und kommt auf einen Flur, von dem noch viele weitere Türen abzweigen.« Das sei auch wirtschaftlich ein unschätzbarer Faktor, der sich zwar nie eindeutig darstellen lasse, aber bei Andritz Kaiser inzwischen so überzeugend sei, dass die additive Fertigung im Unternehmen immer weiter vorangetrieben werde. So sollen in Kürze auch die Mitarbeiter in der Fertigung und der Montage Fortbildung im 3D-Druck erhalten. Als Leitbild dient hier Prof. Claus Matthecks Buch »Körpersprache der Bauteile«, das mithilfe von Bachkiesel, Bergen, Knochen, Zugdreieck und Pauli, dem Bär, ein besonderes Verständnis von Mechanik, Leichtbau und Verformung vermittelt.
Stundensatz von unter 5 Euro
Am Ende eines Büroflurs befindet sich das operative, rund 20 Quadratmeter große Zentrum der AM-Fertigung. Hier reihen sich 5-FDM-Desktopdrucker, auf denen Matassoni und sein junger Kollege Manuel Motzer die Test- und alle benötigten Kunststoffbauteile drucken. »Der Stundensatz der Maschinen liegt bei unter 5 Euro, da kann keine andere Technologie mithalten«, erklärt Motzer.
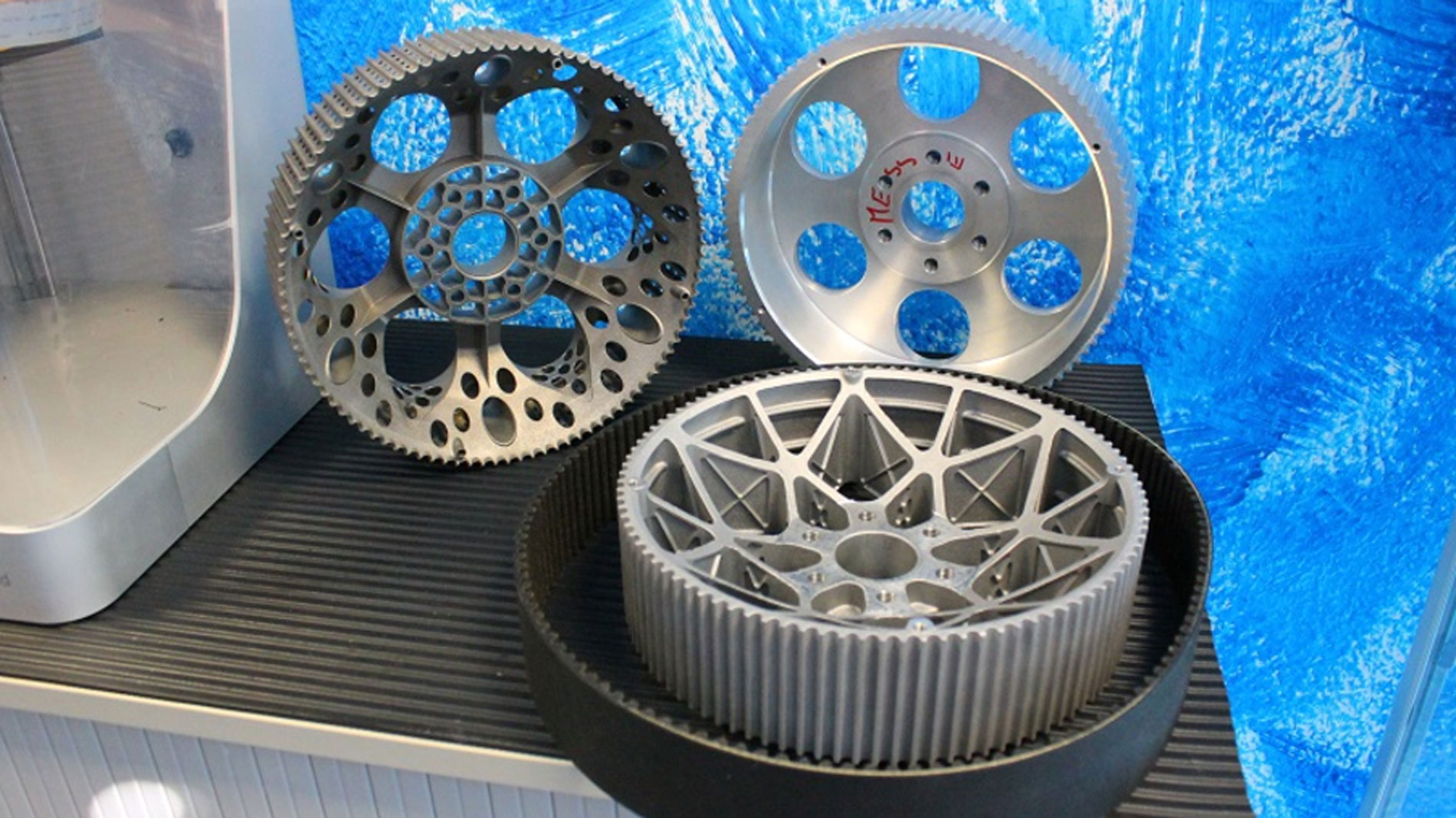
Zwei Türen weiter, in der Abteilung Entwicklung und Konstruktion, entstehen die CAD-Modelle am Bildschirm. Während in den AM-Abteilungen anderer Unternehmen spezialisierte Software bionische Optimierungen errechnet, konstruieren Matassoni und Motzer ganz klassisch »mit der Hand und aus dem Bauch heraus« mit ihrem traditionellen, parameterfreien CAD-Programm OneSpace Designer. Anschließend berechnen sie die Festigkeit mittels der Finite-Elemente-Methode. Für Matassoni spart das nicht nur Zeit, sondern auch finanzielle Ressourcen, was bei einem traditionellen Mittelständler den Ausschlag über den Einsatz einer neuen Technologie geben kann.
»Ich hätte das am Anfang auch nicht gedacht, aber wir brauchen die Optimierungsprogramme für additives Design nicht«, erklärt der Techniker. »Alle Problemstellungen sind schließlich in der Natur genauso vorhanden wie im Maschinenbau.« So ist die gerippte Ölfangschale entstanden, der geschwungene Stößel und auch das Riemenrad aus Titan. Die Idee zu dessen Design, das sich am Panzer einer Landschildkröte orientiert, lief dem Ingenieur bei einem Wanderurlaub in Spanien über den Weg.
Sicherlich werden noch viele weitere Bauteile in Bretten folgen. »Additive Fertigung ist eine Herzensangelegenheit und passt zu meinem Denken«, erklärt Matassoni, den die technischen Möglichkeiten und gestalterischen Freiheiten zu immer neuen Projekten inspirieren. Allerdings hat er jetzt so viele Ideen, »dass ich erkennen musste, dass meine Lebenszeit dafür nicht mehr ausreicht«.
Andritz Kaiser GmbH
Die Andritz Kaiser GmbH aus Bretten in Baden-Württemberg beschäftigt rund 140 Mitarbeiter und gehört seit 2004 zur internationalen Andritz-Gruppe. Zu den Produkten des Traditionsunternehmens mit 75-jähriger Geschichte gehören Stand- und Umformautomaten sowie verschiedene mechanische Pressen mit einer Presskraft bis 25.000 Kilonewton und einer Antriebsleistung bis 8 Megawatt. Auf einer Presse können zum Beispiel in der Automobilindustrie bis zu 2,5 Mio. Karosserieteile pro Jahr produziert werden.
andritz.com
Tags
- Additive Fertigung