Text: Thomas Masuch
Ronny Bernstein has been fully integrating 3D printing into the growth strategy of Bernstein Mechanische Fertigung (BMF) – a medium-sized system supplier for post-processing – for many years. The innovative Saxon is one of Germany’s pioneers, particularly in the highly conventional mechanical and plant engineering sector. His company produces around 50,000 parts per year on its 14 3D printers, some of which are also used for the production of the Twister, a surface treatment system. This means BMF also makes use of AM itself.
Closely interlinked
The close intertwining of mechanical and plant engineering with Additive Manufacturing is also emphasized by Rainer Gebhardt, project manager of the AM working group within the German mechanical engineering association VDMA. “AM is first and foremost mechanical engineering, and at the same time, there’s great potential for the use of AM in mechanical engineering,” he affirms.
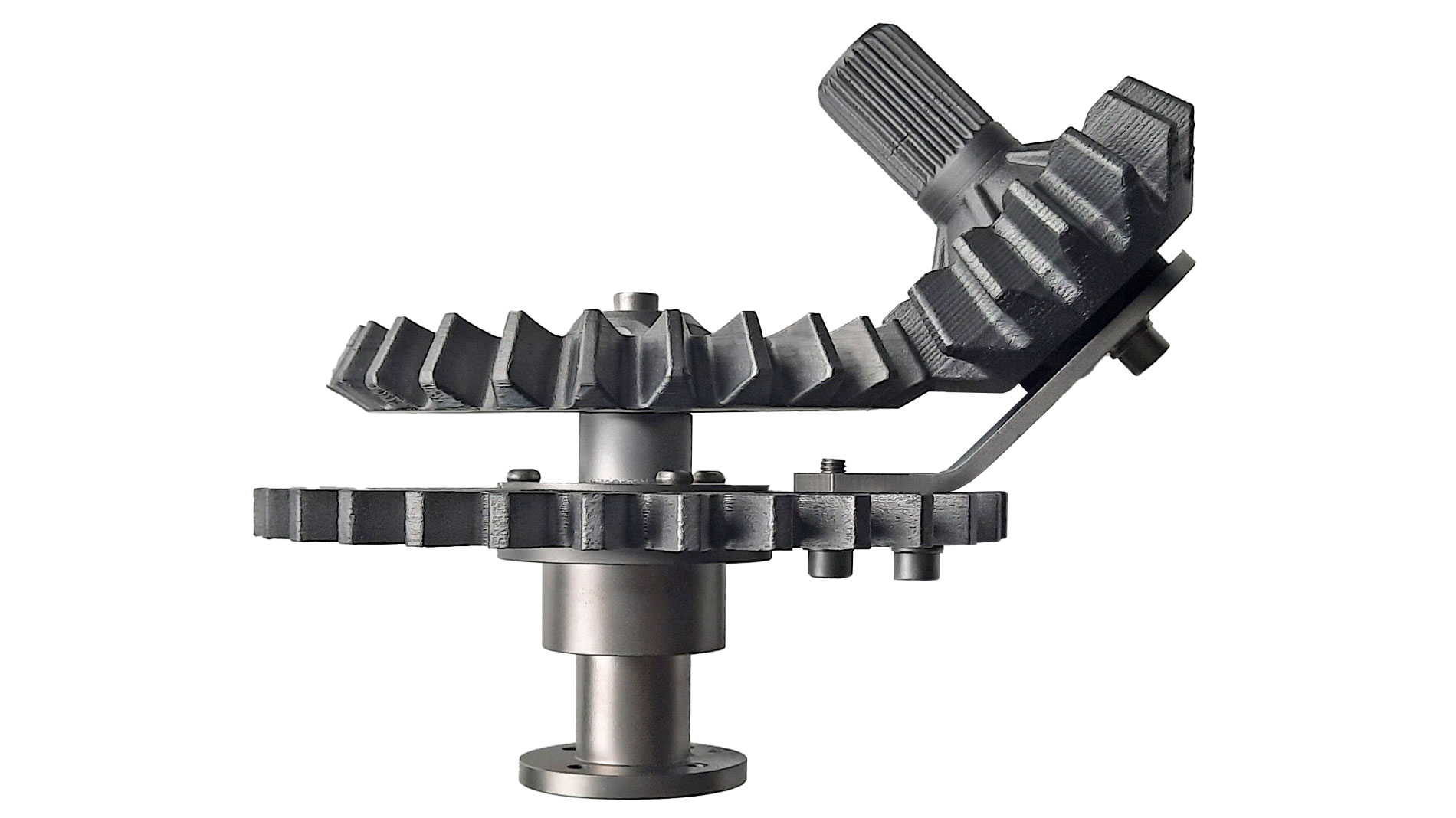
Generally speaking, however, turnover from AM currently only plays a minor role compared to mechanical engineering: While mechanical and plant engineering companies in the EU alone generated turnover of €910 billion in 2024, turnover from the sale and servicing of AM systems amounted to just around €5 billion according to the latest Wohlers Report – and that’s all around the world. When listing the most important AM user industries, mechanical and plant engineering is not at the top of the list; in market studies on Additive Manufacturing, the industry is sometimes not included at all, or only marginally. In the current Ampower report, the sector is included in the “Industrial” user segment, which accounted for 11.6 percent of AM system sales in 2024.
A more concrete indication of the importance of Additive Manufacturing in mechanical and plant engineering is provided by the VDMA’s AM working group, which has over 200 members (around half of which are manufacturers of machines and systems, with suppliers of AM systems, materials, software, or services making up the rest). This puts the group, which was established in 2014, on a par with some of the VDMA's 32 trade associations and their 3,500 member companies. This is a clear signal that the young technology is being taken seriously by traditional mechanical engineering companies.
Modest turnover, but considerable impact
The often widespread “dilemma” of Additive Manufacturing is particularly evident in mechanical and plant engineering: In terms of turnover, 3D printing plays a very small role, but it ensures that innovations are possible and machines are becoming more advanced, which results in a fairly large (and not always measurable) added economic value overall. AM is also increasingly becoming a decisive factor in improving the performance of production systems. “In relation to overall systems, a comparatively modest number of small 3D-printed components often ensure that the performance of a large system, sometimes costing many millions of euros, is significantly improved,” Rainer Gebhardt explains. Examples of this include special grippers, heat exchangers, or tools with conformal cooling.
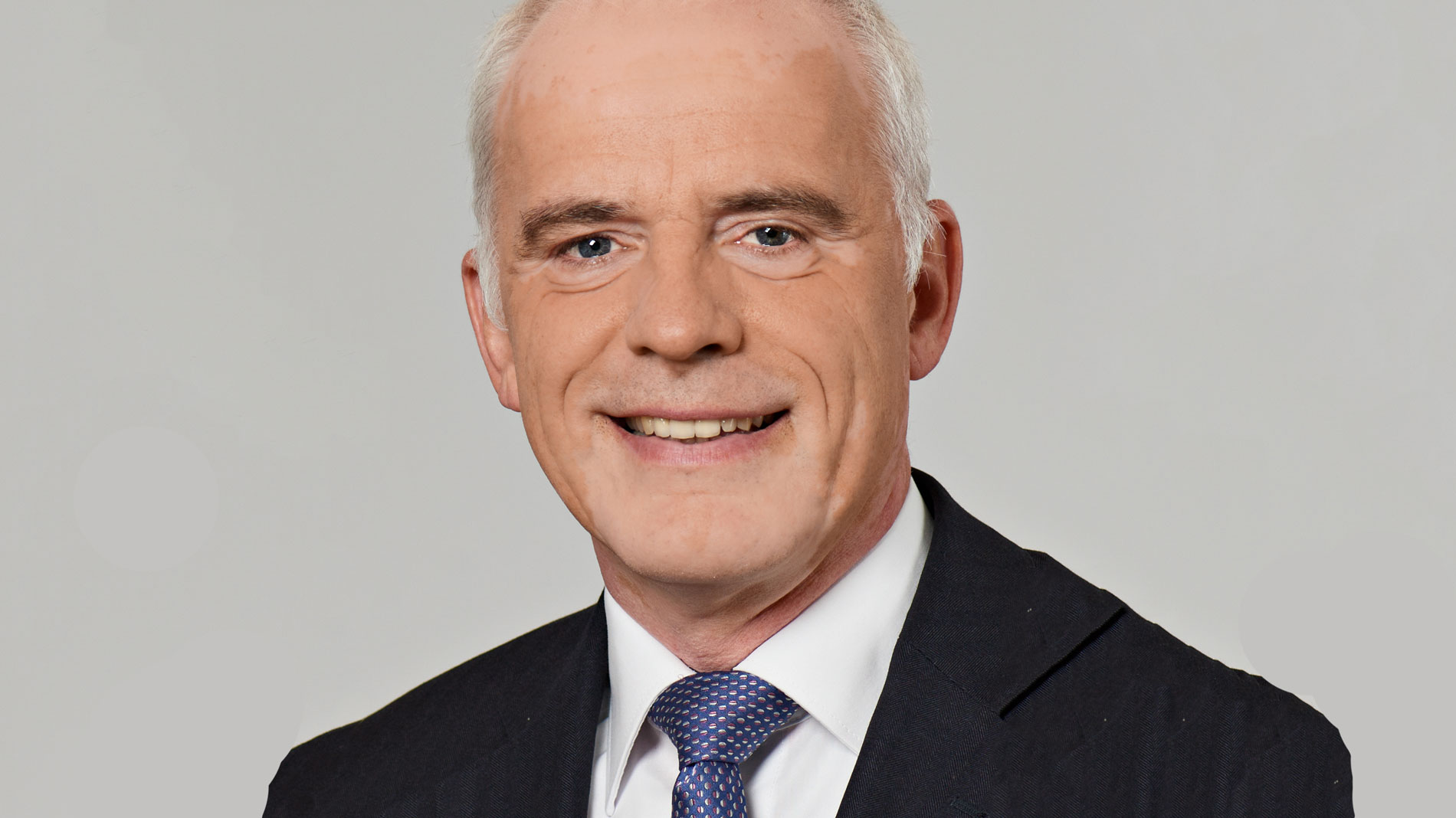
The 3D printing service provider Protiq also manufactures a wide range of different components for mechanical and plant engineering. These include functionally integrated metal components, assembly-friendly special solutions, and highly specialized plastic parts for technical devices. “In mechanical and plant engineering, every gram and every second of assembly time often counts. We’re therefore increasingly realizing components that would consist of several individual components in conventional processes and would first have to be laboriously adapted to the individual machine in question,” explains Stefan de Groot, sales manager at Protiq. 3D printing also demonstrates its advantages when it comes to robust guides, complex devices, or individually designed components for test benches, for example, which can be designed more efficiently and flexibly using AM.
It is therefore hardly surprising that Rainer Gebhardt also ascribes an extremely important role to Additive Manufacturing in mechanical and plant engineering. "Especially with regard to industrial production and the factory of the future, Additive Manufacturing is very important in combination with traditional mechanical and plant engineering. After all, simply putting an AM machine on a greenfield site hardly makes sense in the vast majority of cases," he points out. Major machine manufacturers such as DMG Mori, Trumpf, and Arburg build AM systems that meet all the standards of industrial production in terms of interfaces, sensors, quality, and reliability.
Confident market forecast
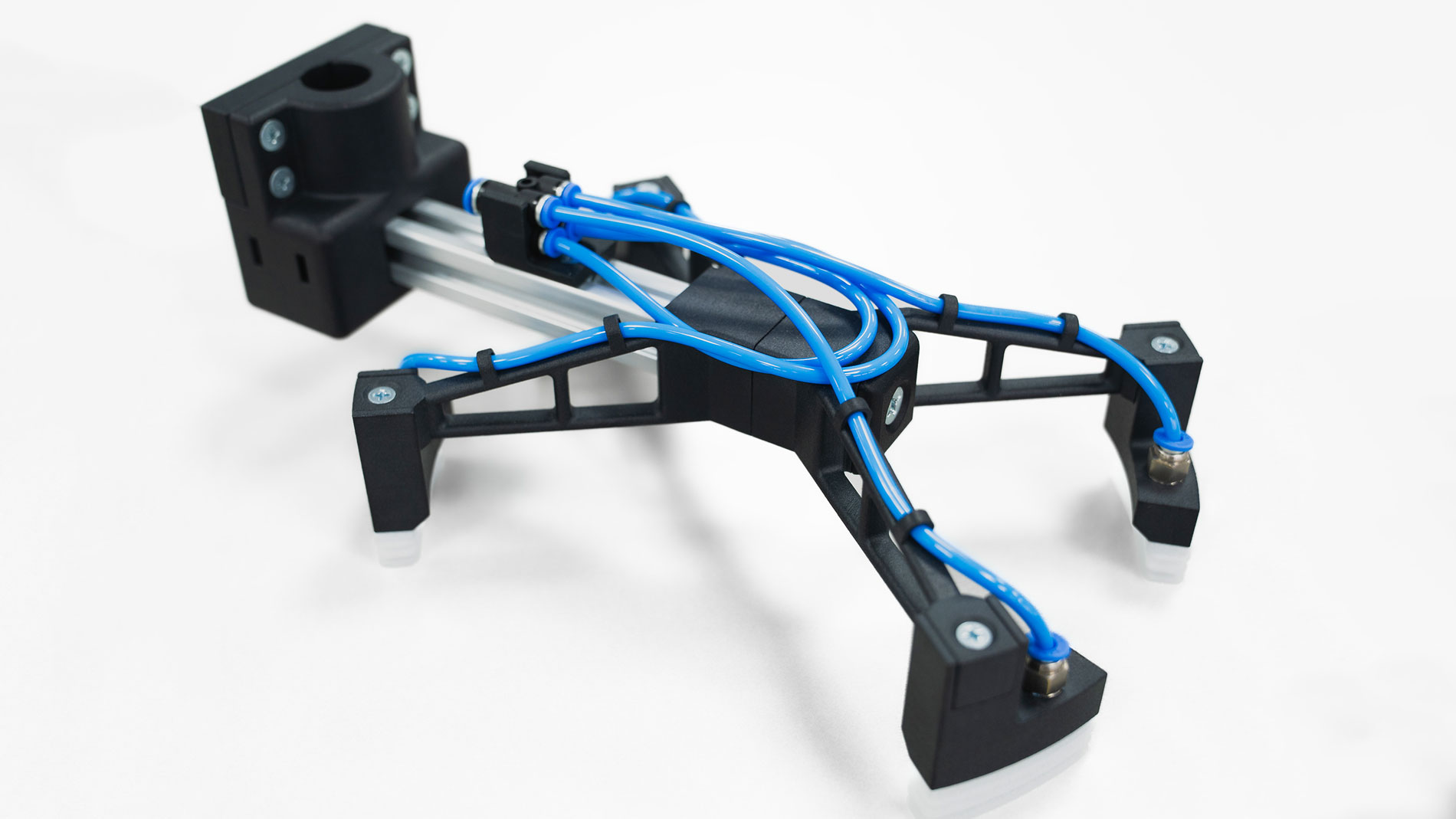
At the same time, Gebhardt is convinced that the mechanical and plant engineering sector has sufficient volume and potential for companies specializing in AM to grow in the long term. This is also backed up by Ampower’s figures: While the sector’s sales volume has hardly changed in the past three years, the Hamburg-based market analysts expect average annual growth of 13% over the next five years, which is slightly higher than the forecast for the AM market as a whole. Ampower managing director Matthias Schmidt-Lehr attributes this positive development to increasingly affordable AM systems, among other things: "This is a strong trend. PBF systems in metal and polymer are now available for less than €50,000, not to mention from manufacturers such as Bambulabs. This makes it easier for medium-sized companies for whom large investments in AM systems were often not an option in the past to get started with Additive Manufacturing. In addition, the 3D printing of production equipment is becoming more and more widespread, partly due to the tireless work of many resellers."
Ronny Bernstein is also seeing significant growth in 3D printing in mechanical and plant engineering, “and significantly more than in the rest of the market”. Among other reasons, he cites the way that designs are changing with a new generation of employees, resulting in more applications. In addition, the number of users is continuously increasing. Although 3D printing remains a niche in the industry, “the companies that have identified a sensible application are using 3D printing and earning money with it,” Bernstein reveals.
Some challenges remain
Nevertheless, mechanical and plant engineering still has some challenges to contend with. The industry is rather conservative, and according to Rainer Gebhardt, “the margins are not particularly high – it's not comparable to medicine or aircraft construction.”. This is why manufacturers of conventional machines are also approaching Additive Manufacturing rather cautiously. “In difficult economic times, the willingness to try out something new is also often limited,” Gebhardt adds.
The particular challenge for companies in the mechanical and plant engineering sector is that although Additive Manufacturing can significantly improve their own products, “you don't automatically get paid for it,” Gebhardt says. “Customers are happy about faster machine set-up times, for example, but also say that they don't necessarily want to spend more money because of it.” However, as more and more manufacturers in the industry turn their attention to AM and advance their machines’ technology, there is hardly any way around Additive Manufacturing for those who want to remain competitive in the future.
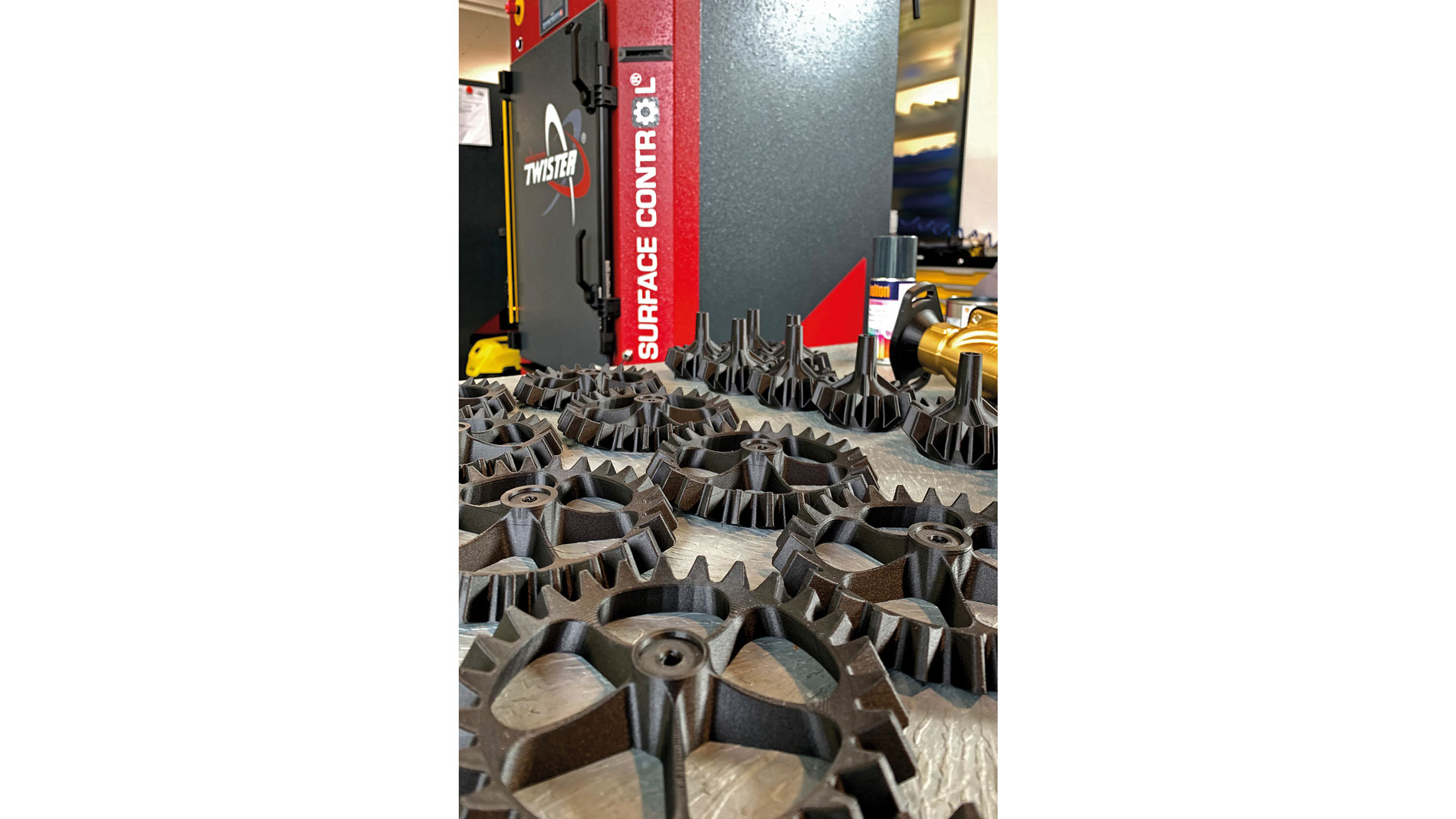
Focus on efficiency
As a solution to this challenge, an approach seems to have established itself in mechanical engineering that makes the most efficient use of relatively manageable investments and develops practicable manufacturing solutions in order to achieve results that lead to a noticeable difference.
Additive Manufacturing has also led to many innovations in the field of tools. Tools (or tool inserts) with conformal cooling are a typical example here. These are generally somewhat more expensive than “normal” tools, but can significantly increase the performance of an expensive injection molding machine, as Gebhardt explains. There can be improvements in the quality of manufactured products, as well. The French company Addup, which has been operating its Tooling Competence Center on the campus of RWTH Aachen University since 2023, has shown that this area is also attractive for manufacturers of AM systems.
Progress in standardization
The development of the AM sector in mechanical and plant engineering is also reflected by the fact that standardization in the field of AM is slowly picking up speed. According to Gebhardt, this topic has been one of the most important challenges for many years. “Some companies have developed really good components with AM, but were unable to use them because no AM standard existed.” Although this has not yet changed completely, efforts are being made to develop industry-specific standards. Examples of this are the EU’s Pressure Equipment Directive and the VDMA’s product category rule 34178:2025-04, which is for determining the carbon footprint of machine tools and machines for Additive Manufacturing.
Further information:
You can find out how companies like BMF and Protiq are succeeding using 3D printing in versatile ways in exclusive background reports: