Text: Thomas Masuch
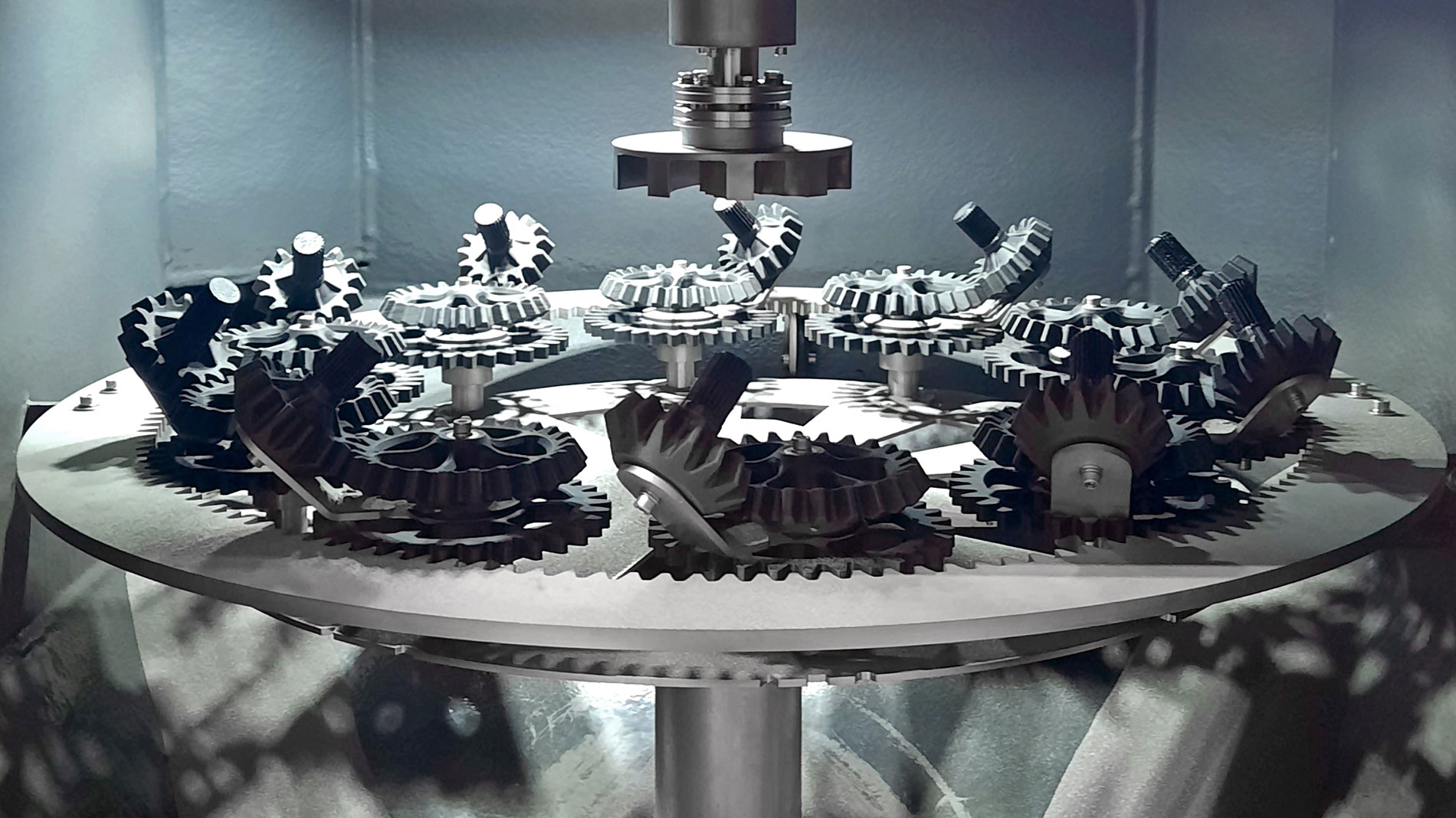
At Bernstein Mechanical Fabrication (BMF) in Chemnitz, Germany, 3D printing is used in a variety of ways. Firstly, in production: At BMF, many parts have been “brought back” from conventional manufacturing, as managing director Ronny Bernstein explains. This means that components that are often made of metal are now printed from plastic. In a Twister machine (BMF's main product), this equates to around 50 larger components and hundreds of smaller ones measuring less than two centimeters.
Bernstein is seeing significant cost savings for his company, which manufactures the Twister system for surface treatment and also produces both individual and series parts by means of 3D printing. “We don't have to keep hundreds of milled parts in stock, but we always have the parts available when we need them,” he points out. However, this advantage is not yet recognized by many mechanical and plant engineers. “Many only compare production costs and say, 'I can mill this for the same price. I can mill that for the same price.'” What they don't consider is that milling often requires significantly higher quantities to be ordered. Bernstein says that the indirect cost benefits of 3D printing are then not considered at all.
50,000 parts per year
In addition to producing components for the Twister, BMF manufactures parts for its own production and provides services to other customers. Every year, a total of 50,000 components are produced on its 14 3D printers, which operate around the clock.
BMF also generates revenue from its customers' spare parts by uploading numerous components for its machines to the cloud. Customers can then order and print these parts as required. “This saves customers a lot of time and money,” explains Bernstein. Compared to conventionally manufactured spare parts, 3D-printed variants cost significantly less. The customer just needs to have a market-ready printer. Bernstein adds that the investment is “manageable” compared to the cost of a Twister, which is around €65,000. BMF also provides a guarantee for its 3D-printed components, as long as the corresponding material is ordered from BMF. Furthermore, customers only have to pay if the component is of good quality when it comes out of the printer.
Injection of ideas
Sometimes, orders for spare parts can lead to more intensive collaboration in the field of 3D printing. "Some customers order additional designs and components, which we create and upload to the cloud individually," Bernstein continues. Other customers then design and print their own items, which BMF can see based on the larger material orders they place. Bernstein believes that the key to the success of Additive Manufacturing lies in users' own experiences: “When people see what works, they also come up with new ideas. This injection of ideas is very important.”
Bernstein is also generally seeing significant growth in 3D printing in mechanical and plant engineering – “significantly more than the rest of the market”, he says. This is partly due to a new generation of employees who are changing the way design is approached, resulting in more applications. On the other hand, the number of users is constantly growing. Although 3D printing is still a niche industry, Bernstein says that companies that have found sensible applications are using 3D printing and generating revenue. “It's true that not every innovation generates revenue, but in the long term, 3D printing ensures you're part of a growing market.”