Text: Thomas Masuch
Some of its important applications include functional prototypes, spare parts, and customized components that would be difficult to realize conventionally, or only with long delivery times. “In mechanical and plant engineering, every gram and every second of assembly time often counts. That’s why we’re increasingly producing components that would traditionally consist of several individual parts and require laborious adaptation of each machine,” explains Stefan de Groot, Protiq's sales manager. Robust guides, complex devices, and individually designed components for test benches are just a few examples at the company.
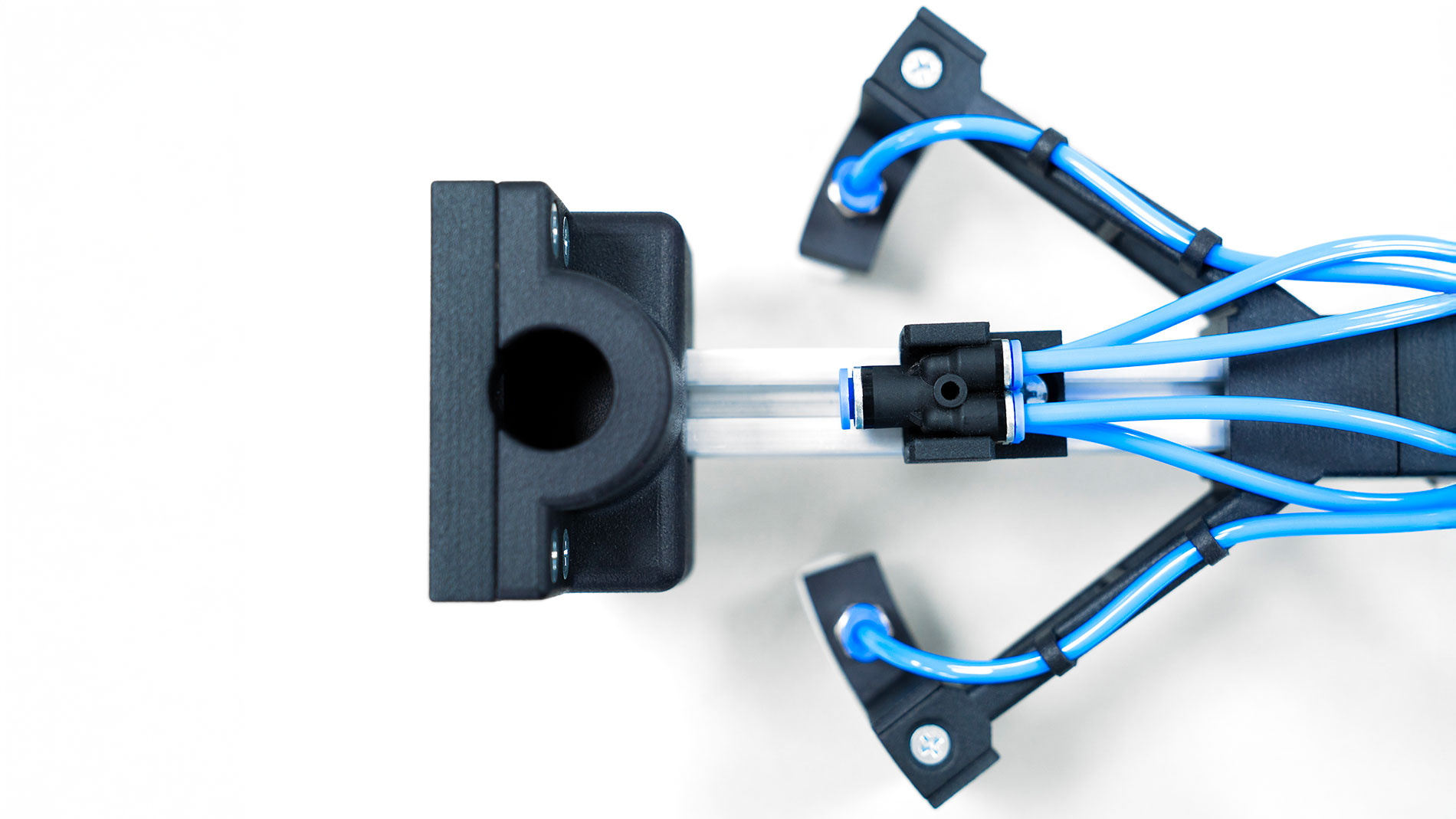
A lighter, faster robot gripper
De Groot cites a custom-developed robot gripper as another example of how Additive Manufacturing can bring all its strengths to bear in mechanical and plant engineering. The gripper is used for handling injection-molded plastic components and packaging materials, among other things — in other words, in typical pick-and-place processes or for the automated loading of machines and devices.
A Scara 4-axis robot wields the gripper to move payloads of up to 1.2 kg vertically or up to 1.0 kg horizontally, achieving handling speeds as fast as 1.6 meters per second in the process. “This speed is only possible because we were able to reduce the weight of the 3D-printed gripper to 460 grams,” explains de Groot. “That’s a significant difference compared to the conventionally manufactured competing product, which weighs around 2 kg.” Overall, this enables higher cycle rates and greater efficiency in the production process.
The gripper's design is based on a hybrid approach: The vacuum segments and structural parts are made of PA12, and the flexible suction bellows are made of TPU with a Shore hardness of 80A. The system is supplemented by an item profile for targeted stiffening and removal of the tool’s center point (the gripper's center of action).
“The gripper is designed in such a way that it can be repaired within a few minutes in the event of a defect and, if necessary, adapted to new requirements within a few hours – for example, by modifying the gripper’s geometry,” de Groot continues. A predetermined breaking point was also deliberately integrated into the design. It gives way in a controlled manner in the event of a machine crash, preventing further damage to the entire system. This functionality can be precisely tailored to the requirements at hand thanks to the geometric design freedom afforded by Additive Manufacturing.
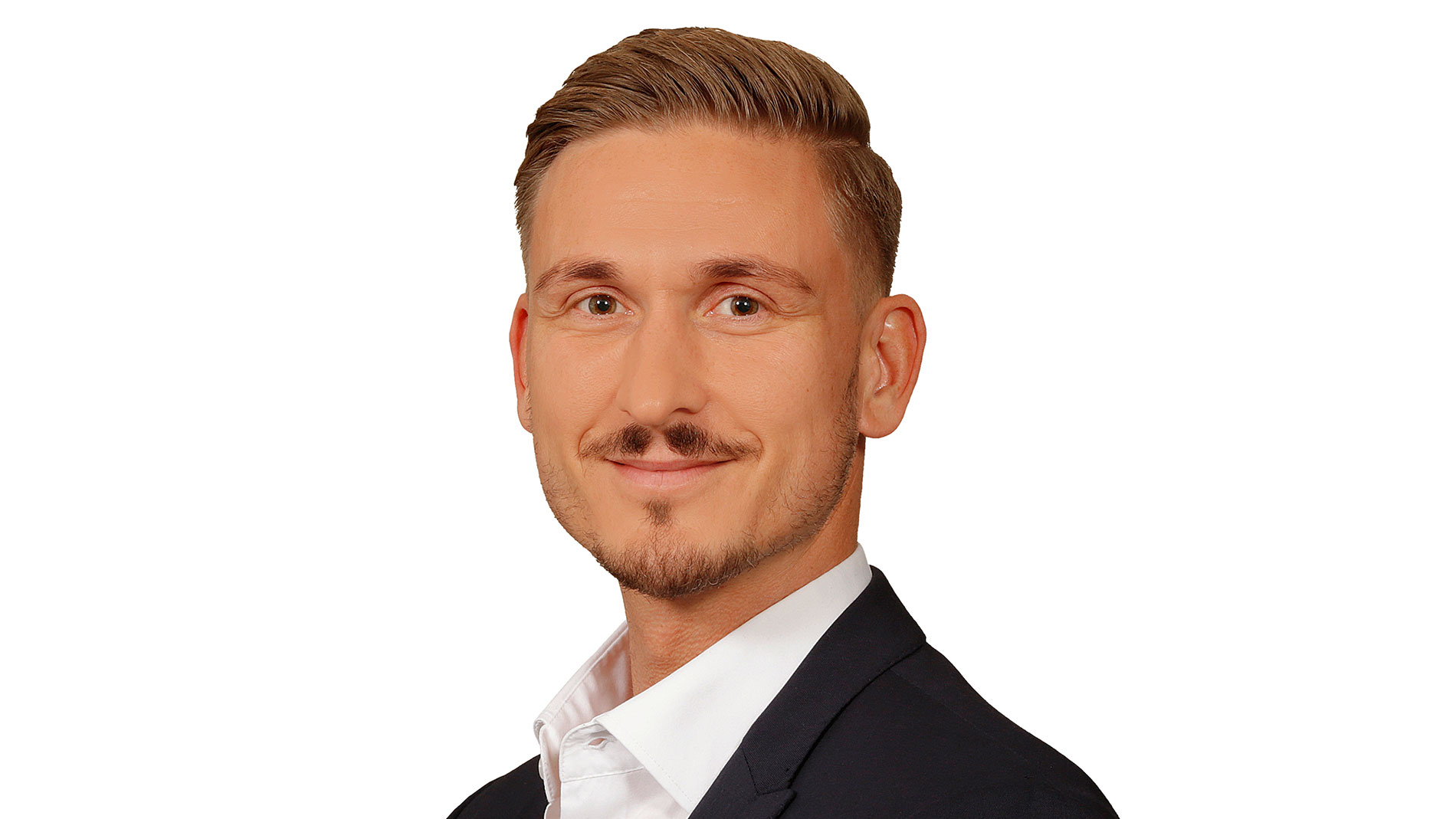
Origin in toolmaking
Protiq’s very industry-oriented AM strategy is also due to the company’s origins: Based in Blomberg (North Rhine-Westphalia), Germany, it was spun off in 2016 and is now a subsidiary of the Phoenix Contact Group. Prior to this, Phoenix Contact had already been operating an internal competence center for Additive Manufacturing since 2010 in order to meet its own requirements. “We benefit from our close cooperation with the in-house mechanical engineering and development departments. Our origins in toolmaking at Phoenix Contact give us a deep understanding of manufacturing processes, not to mention precision- and series-production requirements,” says de Groot. This enables Protiq to meet the particular challenges of mechanical and plant engineering, where components are often subjected to high mechanical or thermal loads. “Material-compatible design, topology optimization, and targeted functional integration are crucial here,” de Groot points out.
Variety in materials and processes
“Our aim is not only to supply companies from the mechanical and plant engineering sector with parts, but also to support them with in-depth expertise and practical advice – from design optimization to the selection of the right process,” says de Groot. Protiq has more than 20 Additive Manufacturing systems in total and employs 25 people at its site in Blomberg.
While being spun off nine years ago, the company also launched a digital manufacturing platform: the Protiq Marketplace. More than 50 other manufacturing service providers have since joined the platform to provide a very wide range of materials and processes. “Thanks to this diversity, we can always offer the right material for a planned application: from high-strength stainless steel alloys to temperature-resistant plastics,” Stefan de Groot is happy to report..