24 April 2023
Every day, firefighters around the world are deployed on sometimes life-threatening missions. To make these missions safer and more efficient, the Laboratory of Sustainability Robotics at the Swiss Federal Laboratories for Materials Testing and Research (Empa) has developed a special drone for firefighting operations. A decisive contribution was made by temperature-resistant components produced using SLS 3D printing.
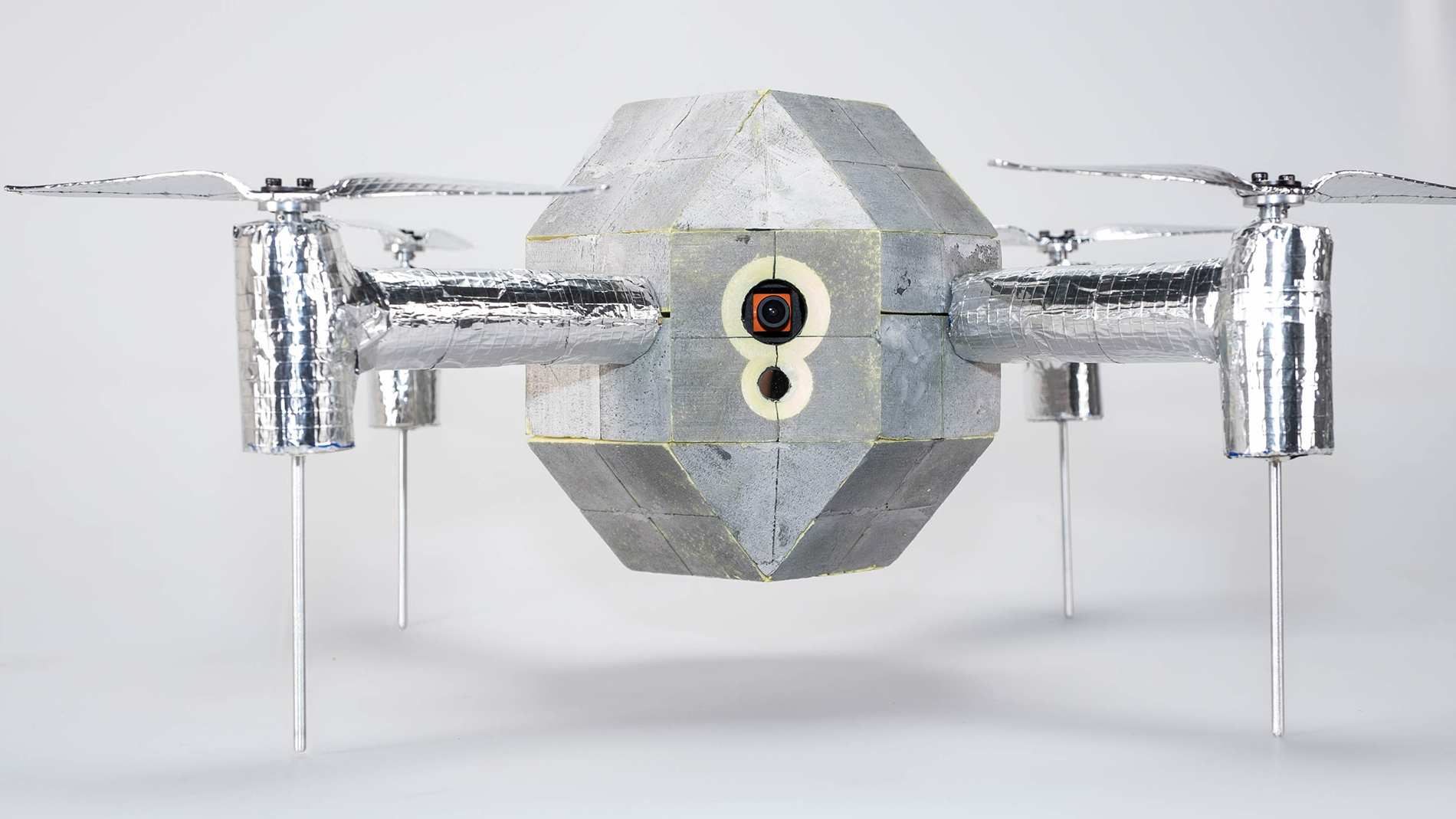
The drone is designed to provide important information from a safe distance during firefighting missions. It uses an infrared sensor as well as a conventional RGB camera, making missions safer and more efficient.
"Usually, drones are not designed to function in extreme temperatures. The materials used tend to melt or even burn," explains Empa development engineer David Häusermann. "For the prototype of the fire drone we had to search for materials that could withstand high temperatures up to 200°C." Thus, in cooperation with materials scientists at Empa, a polyimide aerogel heat shield was developed to effectively protect the drone's internal electronics.
Additive manufacturing technologies such as FDM (fused deposition modeling) were used during the development phase as they offer great design freedom. Later in the project, the FDM components were replaced by laser-sintered PA12 elements due to their improved accuracy, material quality and temperature resistance.
Images: Empa
The 3D printed parts sponsored by Sintratec were used for the mounting frames of the aerogel shell, fixing points for electronic components, clamps for the rotor arms, and the gearbox housings. "These parts fulfilled all of our project requirements and performed as expected when tested in real-life conditions," reports Häusermann, who now plans to use SLS technology again in future projects.
FURTHER INFORMATION:
Tags
- Additive Manufacturing
- Design and product development