29 March 2023
3D printing is also becoming increasingly common in the bicycle industry, where it is apparently making the transition from prototype production to industrial use. Mythos, a manufacturer of bicycle components from Great Britain, has launched a 3D-printed stem for mountain bikes.
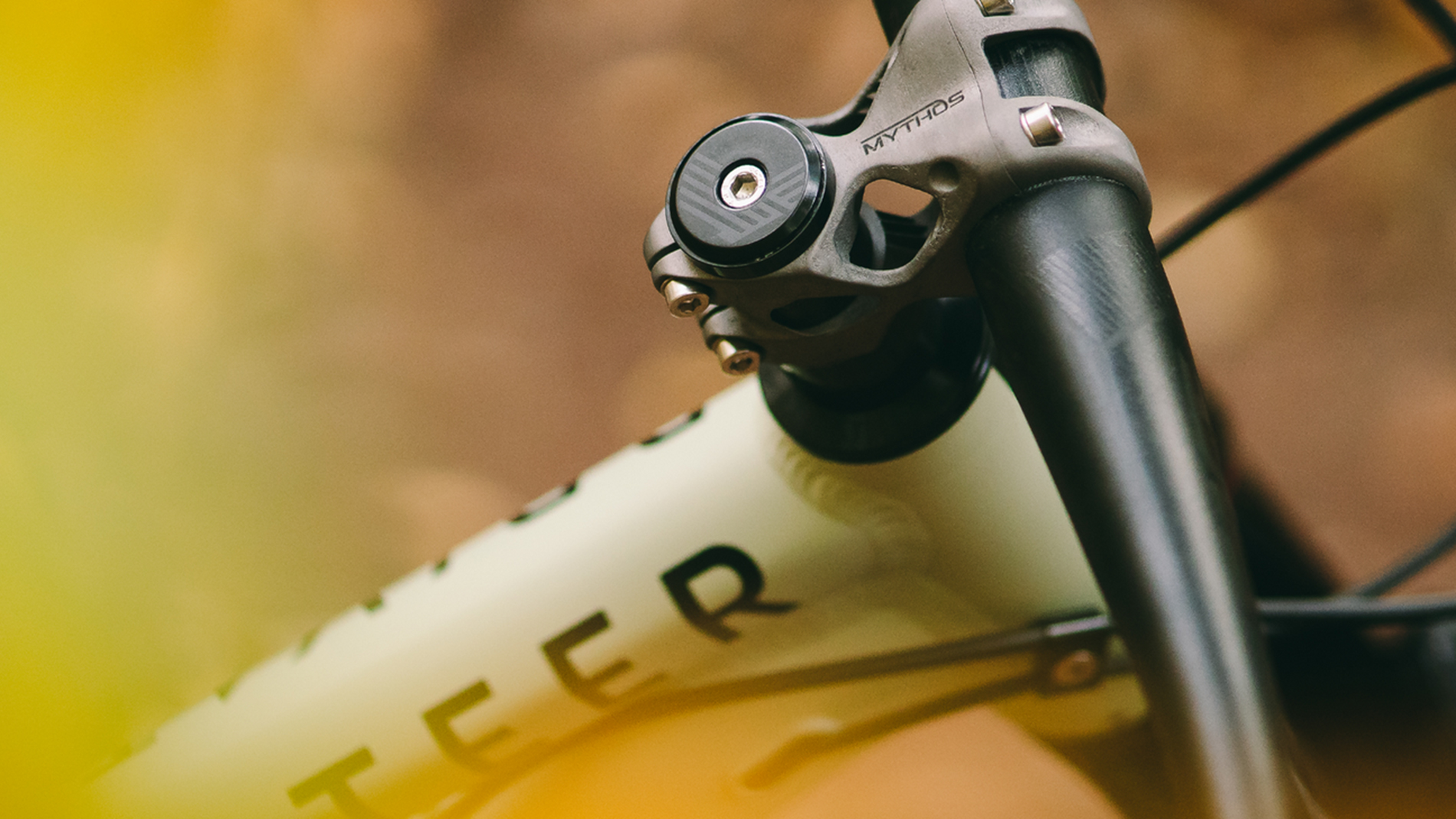
Made of titanium, the Mythos IXO stem is not exactly cheap at a price of around €330, but the company says the material is of "aerospace quality (Ti6Al4V)" and printed using an EBM process. In addition, Mythos promises a higher resistance to torsion and bending. The stem was developed and manufactured by Metron Advanced Equipment.
3D printing is also playing an increasingly important role in the development of new bicycle models; from individual components through to complete bicycle frames.
Kalkhoff, a German bicycle manufacturer with over 100 years of experience in the cycle industry, has significantly accelerated the development of its new models with the help of additive manufacturing. In cooperation with Materialise, the company has created an entire aluminum frame for e-bikes, using 3D printing to make the individual components. The result was a fully functional prototype that is also able to withstand loads of up to 170 kg. In addition to functional testing, Kalkhoff also uses the prototype for trade shows, where customers can test ride and familiarize themselves with the bike before the official market launch.
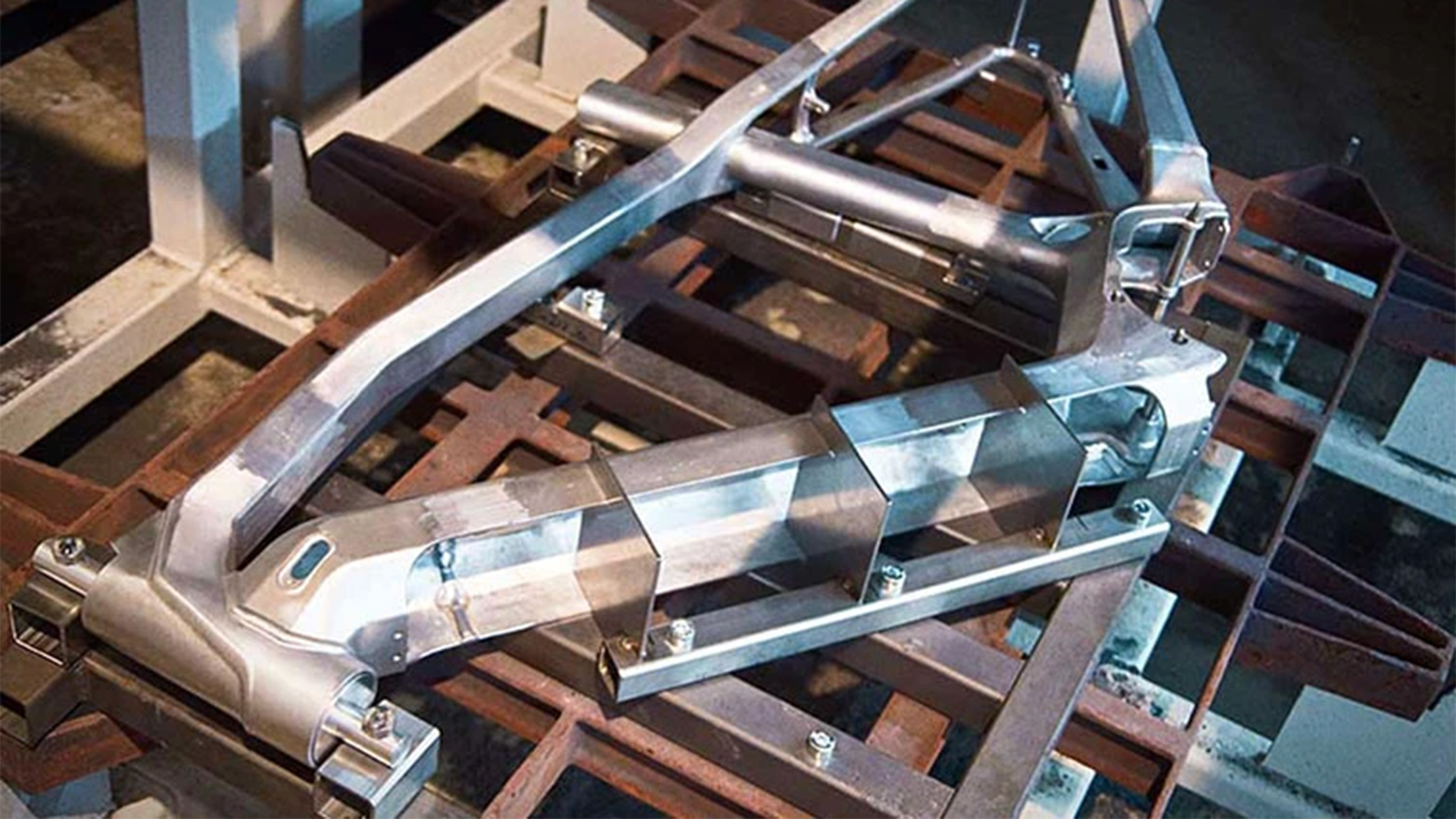
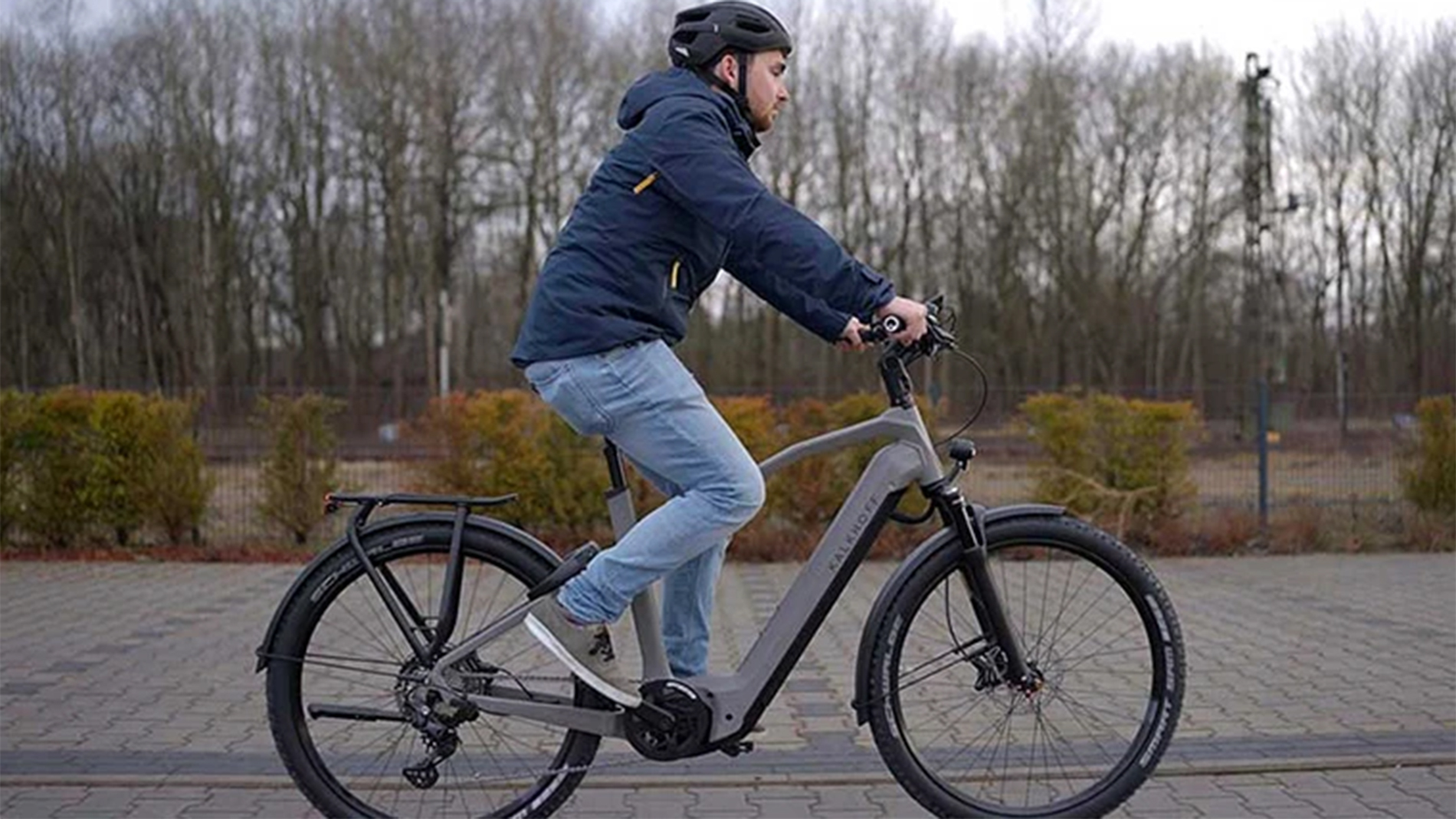
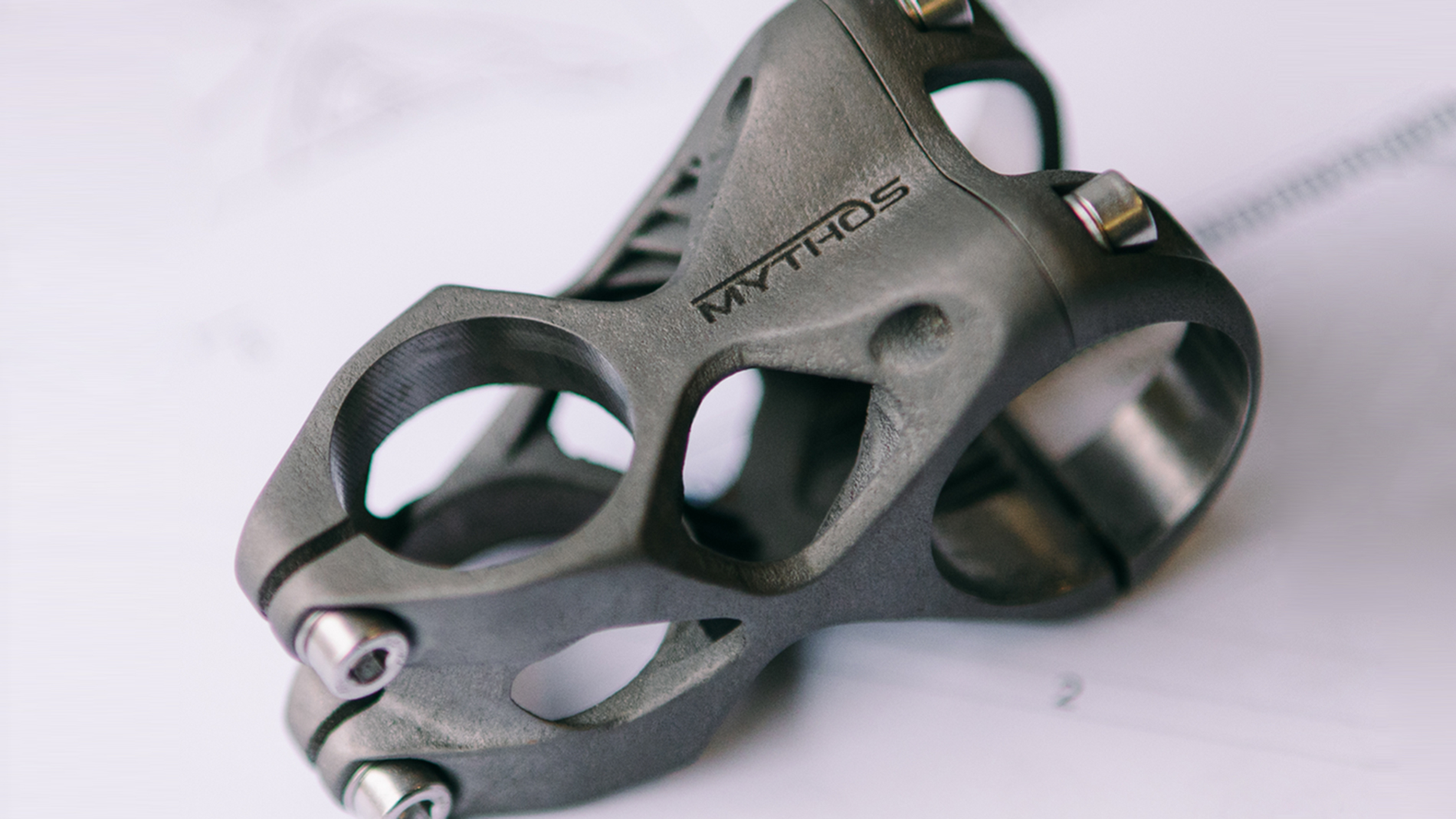
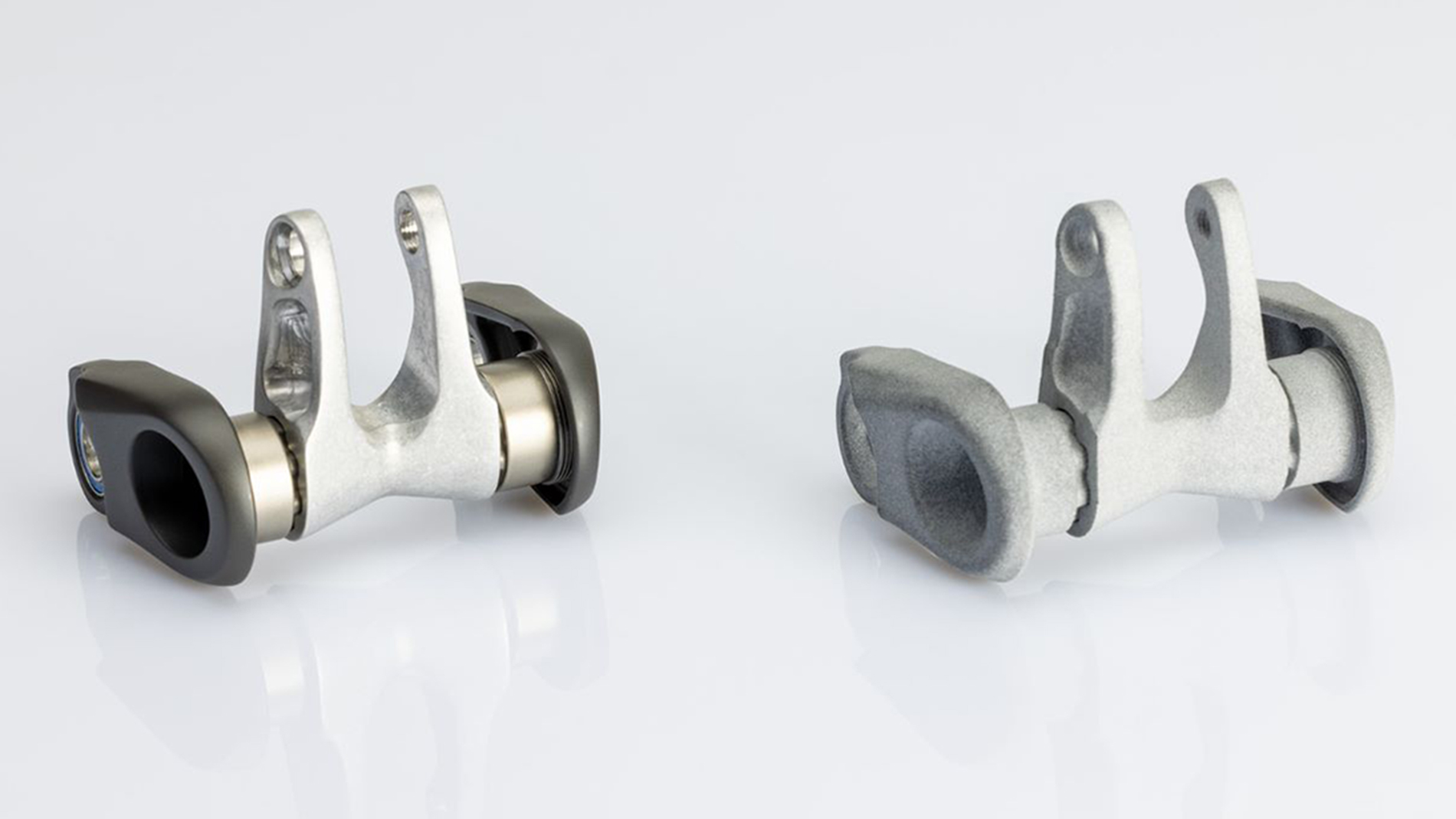
Develop faster; protect intellectual property
International sports brand Scott Sports, which employs more than 1,500 people worldwide, is also increasingly adopting 3D printing to develop new bike components. Scott Sports has increasingly invested in additive manufacturing in recent years to simplify development process of its sporting goods.
"With the help of 3D printing, we have been able to significantly simplify the development process and efficiently develop and produce directly at our headquarters in Givisiez, Switzerland. This not only allows us to benefit from shorter lead times, but also protects our intellectual property," explains Benjamin Schmitt, Head of Digital Manufacturing, Scott Sports S.A. The HP Multi Jet Fusion is also used in the production of custom-made shoe soles for the Tailored-Fits brand.
Tags
- Additive Manufacturing
- Research and development