Text: Thomas Masuch, 20 March 2024
Product designer Klaus Liese has become a 3D printing expert in his XMoove project. Back in 2016, he developed a flexible light that can adapt to the size of a table and the number of people sitting at it. The lamp, which is 3D-printed in a single piece (including the body, hinges and cable ducts), can be extended from 30 to 140 centimeters and provides the perfect lighting conditions for two to eight guests.
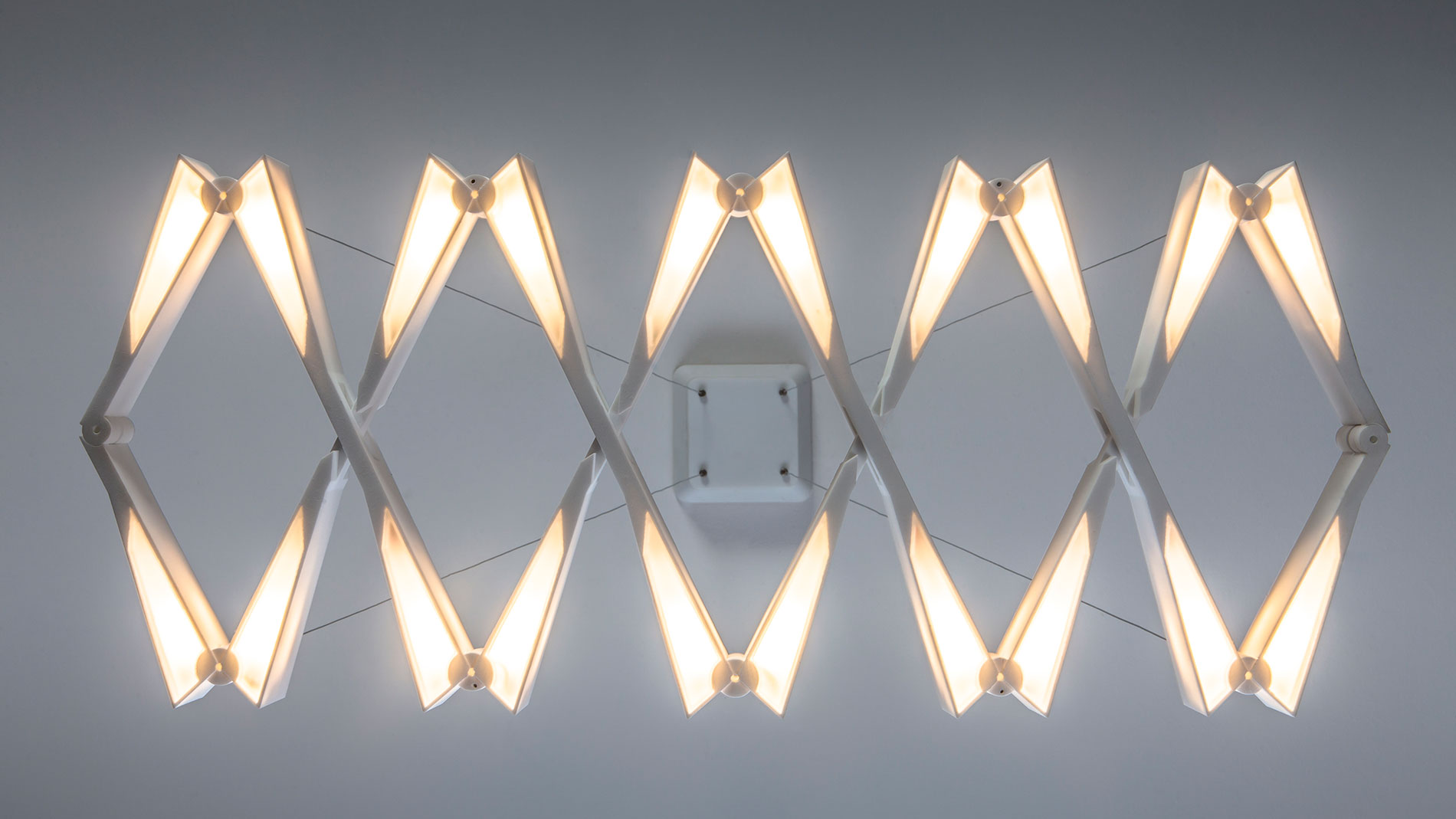
Liese presented the XMoove luminaire at the Light+Building trade fair in Frankfurt in 2016 and went on to win the German Design Award a year later. Besides finding buyers in quite a few private individuals, the luminaire has given him “an immense reputation as a product designer, which has enabled me to work on very good projects even years later.”
However, this exclusive product required not only an unusual design concept, but high-quality production, as well. After initially working with a start-up, Liese has had XMoove manufactured by the 3D printing service provider Formrise in Töging am Inn, Bavaria, since 2019. The lights are produced there using a selective laser sintering (SLS) process in which high energy input melts plastic powder and forms layers up to .06 millimeters thick.
New design possibilities
3D printing offers product designers enormous creative possibilities. Shapes are now conceivable that were previously impossible to implement in everything from interior products to furniture and jewelry (made of plastic or gold, for example). In addition, exhibitors at Formnext – the world's most important trade fair in additive manufacturing and modern production processes – have already presented extravagant chairs made from plastic or concrete and vases made from sustainably produced filaments. Other applications range from watch cases to exhibition booth construction. The extraordinary 3D-printed wall designs at the Tiffany & Co. store at Singapore Airport or the Dior Gallery in Paris, for example, show how much these and other applications enrich business and everyday life.
At the same time, additive manufacturing is sustainable: only the material that is needed is used. Production takes place on demand, and only the required amount of chairs, lights, glasses or earrings are 3D-printed. Unlike with injection molding, no molds are required. This makes warehousing superfluous and avoids additional costs.
Extraordinary 3D-printed interior solutions: Tiffany & Co store at Singapore airport and Dior Gallery in Paris. Images: Tiffany, Dior / Kristen Pelou
The jewelry sector, for instance, has become an interesting niche for Formrise alongside traditional sectors such as the automotive industry. Co-founder and -director Robert Razavi sees great growth potential here: His company has already sintered and refined numerous earrings for Maria Boltenstern since 2019, and the Austrian jewelry designer's collection has since expanded significantly. Several thousand pieces of jewelry are created every year in Formrise’s industrial 3D printers.
Razavi also sees “a lot of room for improvement” in the interior sector in connection with SLS production. Whether it’s chairs, tables, vases or other furnishings, the combination of design freedom and sustainability opens up unique perspectives. “Filament and granulate printing from recycled materials can already be found in applications such as vases. In contrast, the potential of interior and fashion products manufactured using SLS and renewable raw materials – PA11 made from castor oil, for example – with almost complete freedom of design is still largely untapped.”
Robert Razavi still sees great growth potential in the jewelry sector in particular. Pictures: Formrise
Significant production expertise required
For product designer Klaus Liese, who designs lights for well-known manufacturers in his day-to-day business, 3D printing has paved the way for his own products. “We’ve broken completely new technical ground and also applied for several patents,” he reports. Even though this involved a lot of additional work, it was worth it for the man from Bonn: “I'm very happy that I took this step.”
As exclusive products also require high-quality 3D printing, working with a service provider like Formrise was the right step for Liese. “Additively manufacturing such complex components requires an enormous amount of expertise,” he affirms. In order to improve the production process even further, he has worked with Formrise over the years to optimize the design of his luminaire for the requirements of 3D printing. For example, the need to easily remove the unused powder inside the luminaire and to open and close the luminaire with the desired amount of force has to be taken into account at the design stage.
The XMoove light can be extended from 30 to 140 centimeters. Images: Klaus Liese
Printing, smoothing and coloring
Formrise also prints prototypes and spare parts for Daimler Trucks and Buses and various caravan manufacturers. It even manufactures several thousand pairs of glasses every year. The service provider can also transfer the expertise gained here to projects such as the XMoove. Nevertheless, even for an experienced AM expert like Robert Razavi, the luminaire was not just another everyday production order. “Since the single-piece design includes hinges and small gap dimensions, the challenge was to deliver a product with perfect haptics and color within the scope of the technical possibilities the customer can expect in this price segment.” The entire production process has to be geared towards the end product in order to meet the requirements in terms of mechanics, function and surface finish. “At the same time, the filigree components also have to be treated very carefully during the manufacturing process to ensure that they survive the post-processing and dyeing,” Razavi explains. As with jewelry, the filigree structures of the luminaire make vibratory grinding impossible. Formrise therefore uses a mechanical post-processing method to compact the surfaces. “The roughness is significantly reduced and we achieve repeatable, rich and bright RAL colors in line with the customer’s requirements.”
Due to the complex manufacturing process, finding a service provider with the right expertise is all the more important for product designers who want to use additive manufacturing, as Razavi points out. “The key questions here are: How good is the manufacturing and consulting quality? What expertise is available in terms of post-processing and coloring? And how quickly, precisely and repeatably can product-relevant settings be integrated into the production process?”
Jewelry designer Maria Boltenstern uses 3D printing for her collections. Images: Boltenstern
FURTHER INFORMATION:
Tags
- Services
- Design and product development