Text: Thomas Masuch, 5 November 2024
Innovations in systems and materials are constantly making new applications possible, and this is precisely where Additive Manufacturing shows what it can do and how it creates added value in various industries. Numerous exhibitors will be presenting new components and applications of this kind at Formnext 2024. Meanwhile, it is also becoming apparent that the medical and aerospace sectors are particularly important drivers of AM’s development. The innovative applications in these fields range from better aortic models for training surgeons and bone replacements for cats to components for satellite communication or rocket propulsion. However, traditional industries are also constantly improving their products thanks to AM, as pump manufacturer KSB is proving.
Precisely replicating the mechanical properties of tissue
French company 3Deus Dynamics is poised to present 3D-printed aortic models specifically designed to improve surgical training and pre-operative planning. According to the company, the innovation in these models is that they accurately replicate the mechanical properties of human tissue, providing surgeons with a realistic hands-on training experience. The models are made of silicone, which offers better flexibility and tactile feedback compared to traditional hard plastic or resin models. 3Deus Dynamics offers its own patented silicone 3D-printing process for the production of complex and realistic anatomical models. For surgical training, complex procedures such as endovascular aortic repair (EVAR) can be simulated in an environment that mimics real operating room conditions. According to recent studies, the use of simulations with 3D-printed models significantly reduces procedure time and radiation exposure and improves surgeon performance by up to 40 percent.
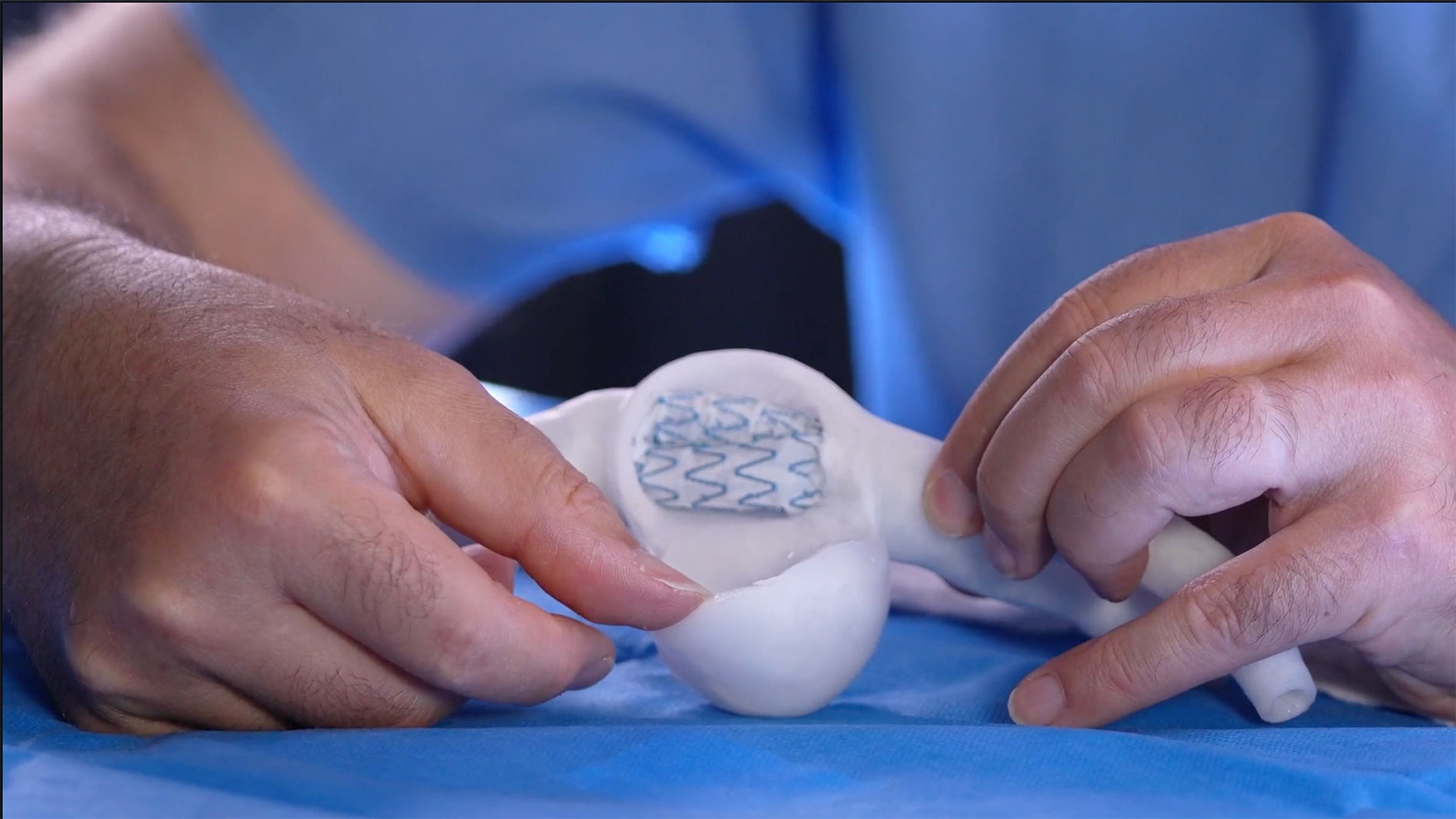
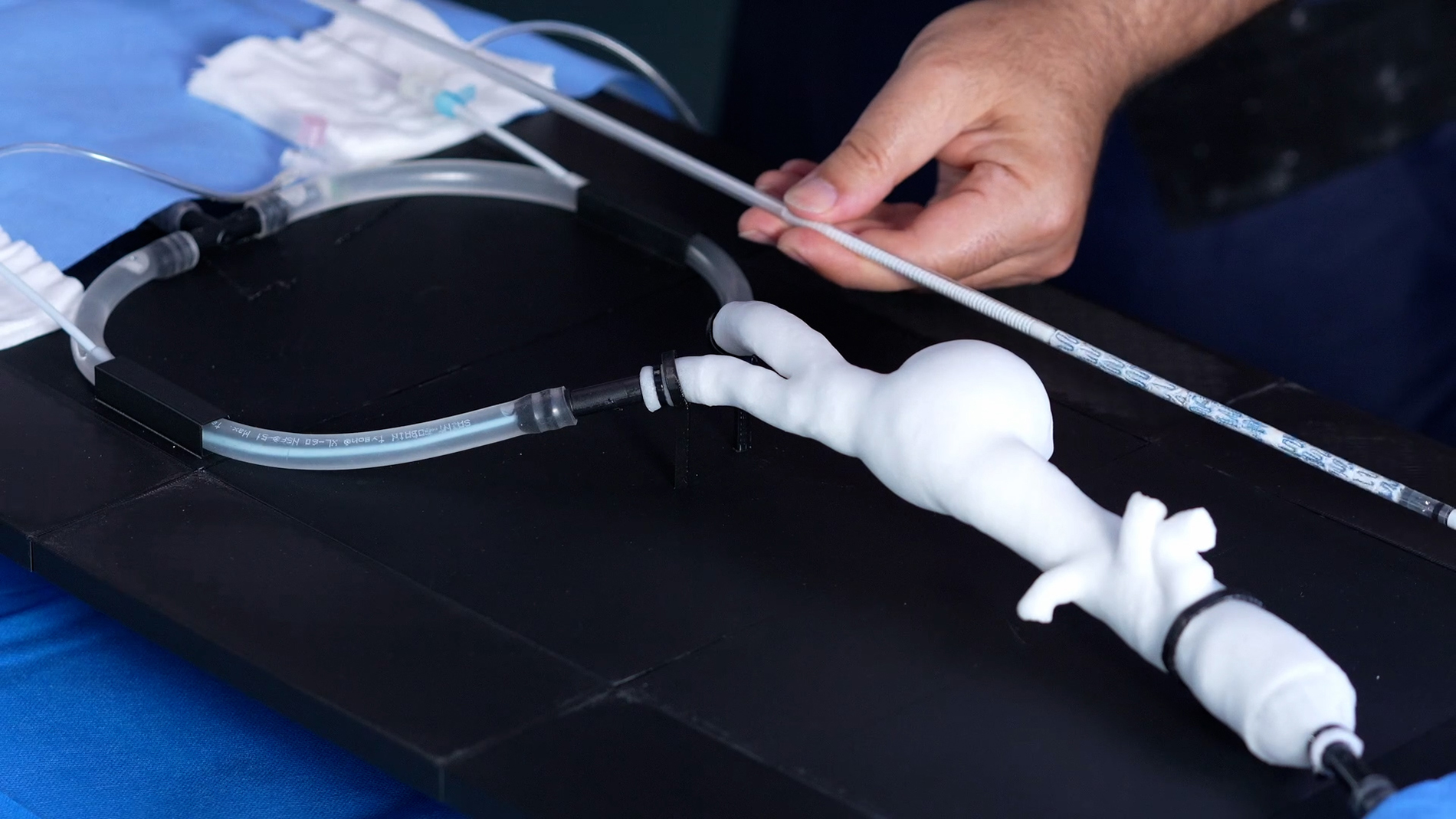
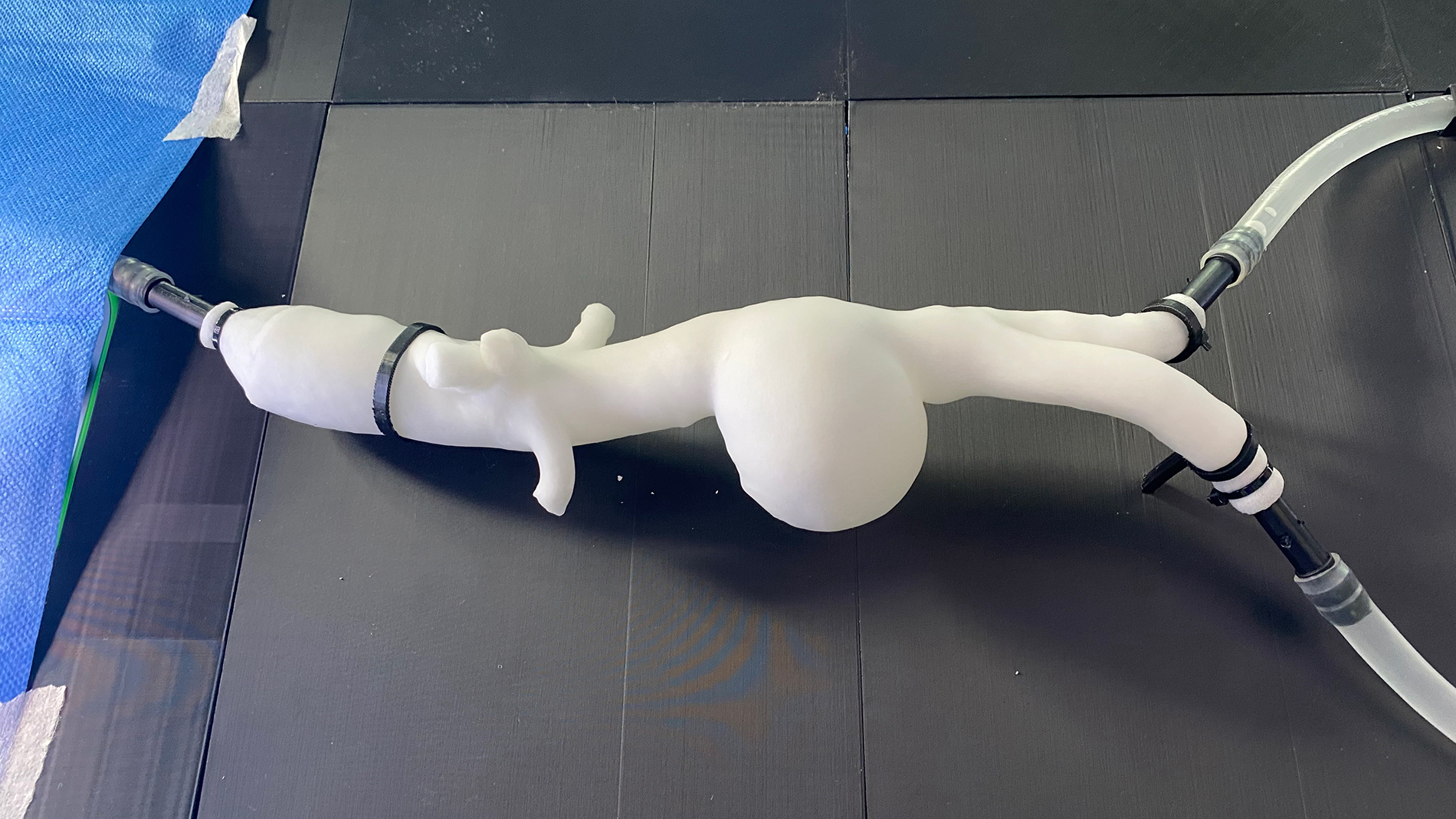
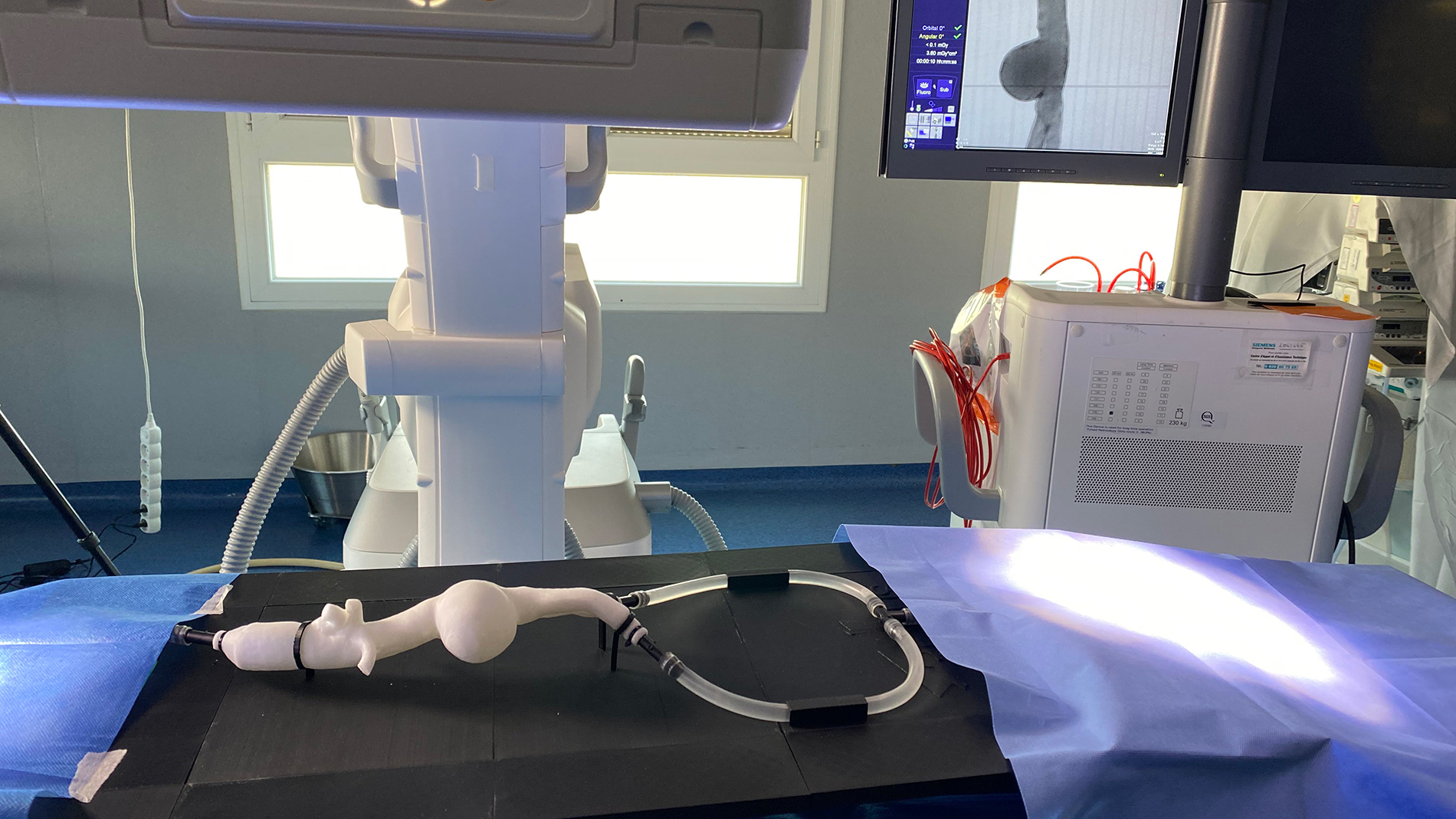
Bone replacement for a cat
Veterinary medicine is another area that really benefits from the quick implementation and adaptability of AM. Unlike in human medicine, materials that have just appeared on the market or have been optimized for a particular area of application can be introduced and tested more quickly. This enables veterinarians to offer the most modern and effective treatment methods without compromising on safety or quality. For an impressive example of this, consider the recent case of a cat that was suffering from a severe bone defect on its left lower leg after being bitten by a dog. Thanks to modern imaging techniques such as CT scanning, the Austrian veterinarian Danilo Borak was able to identify and measure the defect, which enabled CADdent to construct a bone replacement structure. This was then manufactured from hydroxyapatite using lithography-based ceramic manufacturing (LCM). The cat was then able to put its full weight on the leg just three days after the operation.
GGW filters via 3D screen printing
Modern communication systems such as satellites or mobile networks require higher data rates and capacities. As a result, higher frequency bands in the millimeter-wave range are increasingly being used. However, as frequency increases, wavelength decreases, which means that the components of such systems must become smaller. This ongoing trend of miniaturization demands technologies capable of realizing components like filters, antennas, or diplexers. According to the Fraunhofer Institute for Manufacturing Technology and Advanced Materials (IFAM), 3D screen printing has proven to be an ideal method for manufacturing these components. In a joint project with the European Space Agency (ESA) and the University of Kiel, excellent results were achieved using groove-gap-waveguide (GGW) technology. This technology has proven to be highly suitable for creating components in the millimeter-wave range. The quality of the components produced in this project is comparable to conventionally milled parts. However, 3D screen printing offers greater flexibility and cost-effectiveness, especially for high-volume production.
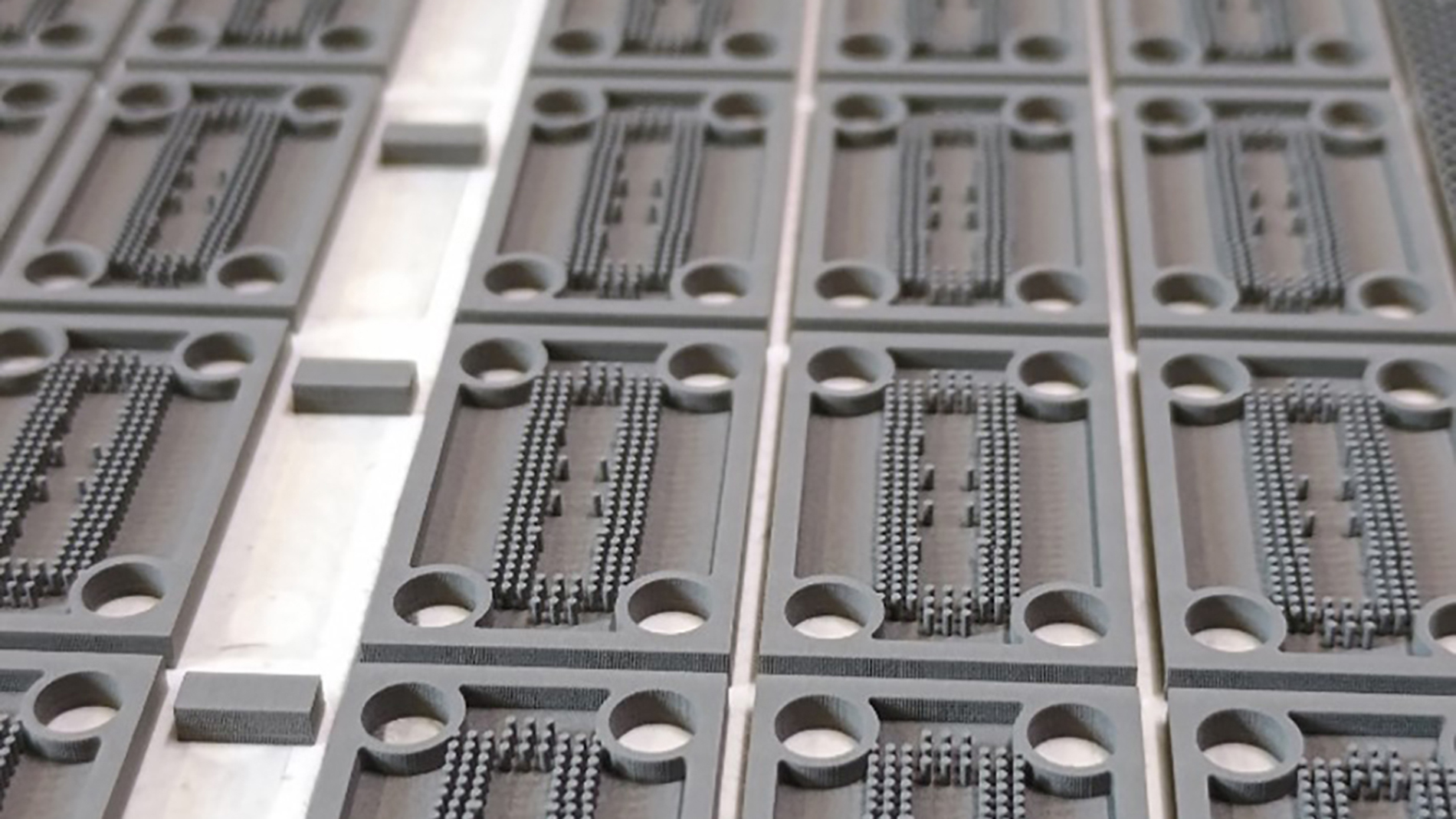
New impetus for European space travel
To enhance the competitiveness of European space transportation systems, the Fraunhofer Institute for Laser Technology (ILT) is developing groundbreaking manufacturing technologies for rocket components as part of the Enlighten project. One major boost for European space travel comes from a rocket engine nozzle manufactured using laser material deposition (LMD). “The wide range of possibilities offered by LMD technology drastically improve our speed and cost-effectiveness in manufacturing new generations of rocket nozzles,” explains sub-project coordinator Min-Uh Ko. The nozzle being developed at Fraunhofer ILT is designed for use as a component in the next generation of rockets to emerge from the Ariane program. ArianeGroup is the overall coordinator in charge of the Enlighten project. While the rocket nozzle can already be produced using conventional methods, the process currently involves many individual sequential steps, which presents challenges in terms of time and costs.
Image: Fraunhofer ILT
Channel-infused design
KSB SE & Co. KGaA will be showcasing a new, 3D-printed split housing for magnetically coupled pumps at Formnext 2024. The component, named MagnoProtect, offers the safety of a double-walled split housing without the drawbacks of significant heating and high eddy current losses. Compared to conventional split-tube motor pumps, the new magnetically coupled versions demonstrate significantly better overall efficiency while maintaining comparable safety levels. With its completely channel-infused design, KSB’s the new split housing provides a second redundant static safety feature against leakage of the conveyed medium.
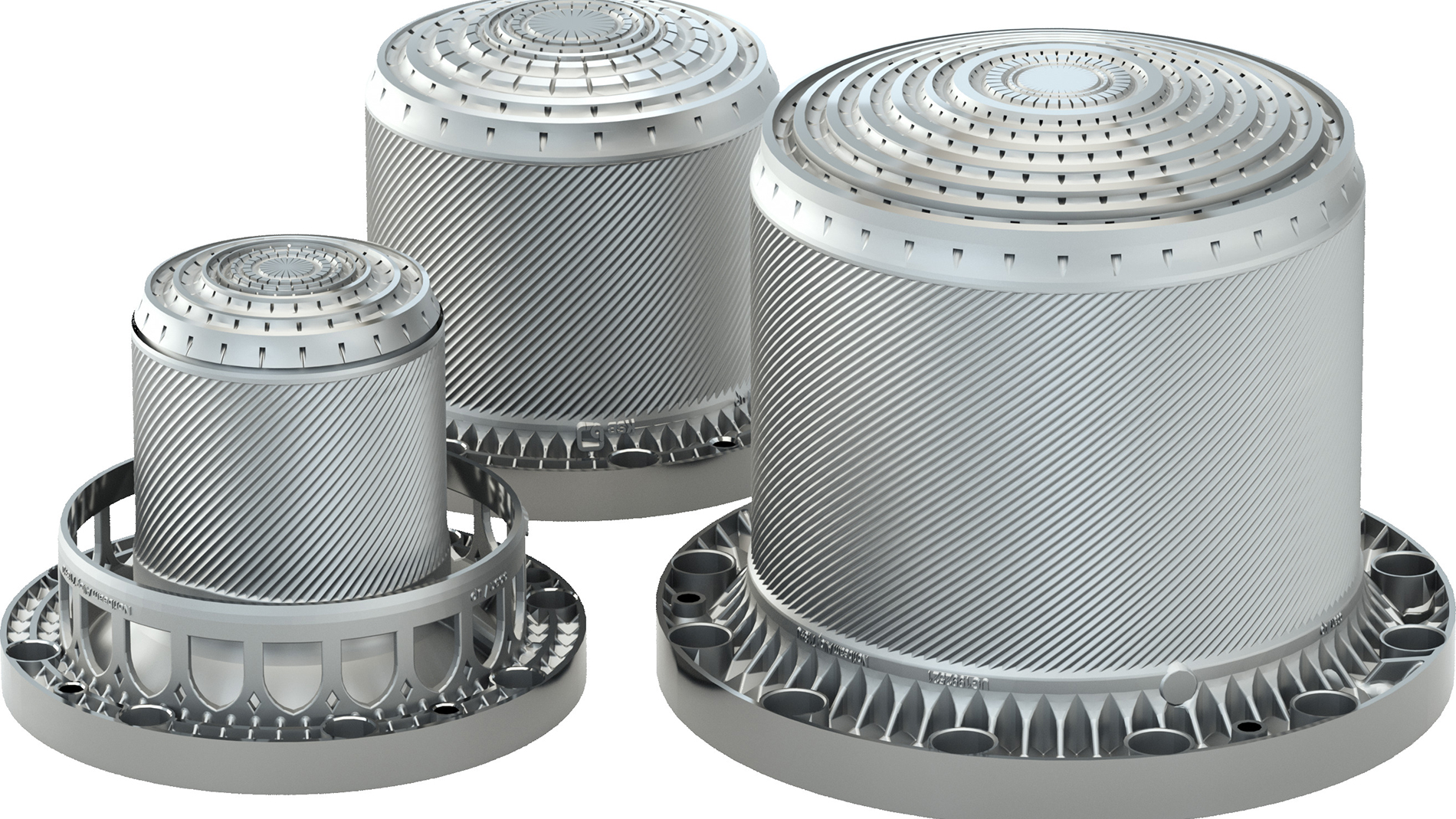
FURTHER INFORMATION:
You will find all the companies mentioned at Formnext 2024:
3Deus Dynamics: Hall 11.1, Booth B03
CADdent: Hall 12.1, Booth E79
Fraunhofer ILT: Hall 11.0, Booth D31
Fraunhofer IFAM: Hall 11.0, Booth D31
KSB: Hall 12.0, Booth B01M
Tags
- Additive Manufacturing