by Matthias Schmidt-Lehr
After suffering quite a shock due to COVID-19, broad sections of the AM market are now getting back on track. Things can be quite different depending on the region, industry, or technology you look at, however.
This year, the AM industry seems to be shaking off the effects of the pandemic for the most part, heralding a return to its usual annual growth rate of around 20 percent. That said, it’s important to be aware of how the recent developments vary by region, industry segment, and technology.
In geographical terms, the trends are the same as in years past: The United States, which remains the world’s largest AM market by far, also boasts the highest growth rates. China and Germany rank second and third, respectively, with somewhat lower rates of growth. Although the US industry entered the metal AM market quite a bit later and many companies still have a lot of catching up to do, an impressive number of new firms are emerging across the pond. A large portion of these start-ups and the vast majority of corresponding global investments are currently connected to US-based suppliers and users of Additive Manufacturing.
Recovery in automotive, meteoric growth in aerospace
Medical technology, aviation, and vehicle manufacturing have historically been the biggest target markets for AM systems, materials, and production services (see graphic). The development of the latter two sectors played a particularly prominent role in the AM industry’s plunging revenues in 2020, and the negative effects will be felt in aviation for some time to come. This field is expected to need several years to recover, along with the support of investments from the military sector in particular (in aircraft engines, for example).
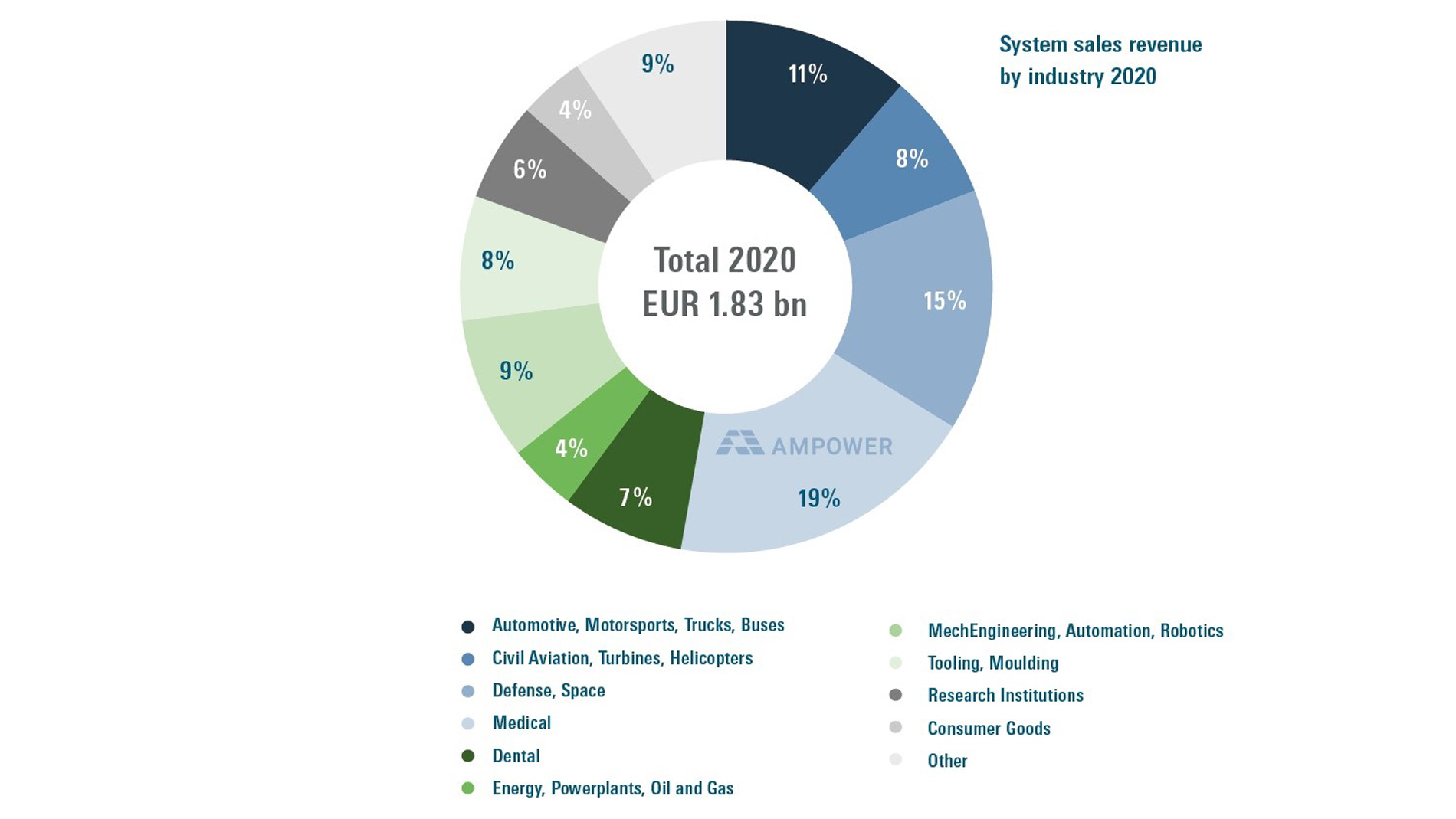
While the vehicle production industry has rebounded much more quickly, it is becoming increasingly clear that direct AM applications are still the exclusive domain of the sportscar and luxury segment. At the same time, additive techniques have well and truly arrived in the areas of tools, means of production, and pilot runs – and plenty of potential still remains untapped. Aerospace is another area that has returned to the high rate of growth it had been enjoying in recent years in metal 3D Printing. Increased demand is projected going forward, as well, especially in connection with large installations capable of building things like more powerful rocket engines of a single piece from high-performance materials.
Supplier saturation in established processes
When one takes a closer look at the various technology segments in AM, two seemingly contradictory trends – growth and consolidation – become increasingly apparent. An oversaturation of technology suppliers can also be observed in established AM processes, which will lead to various mergers and acquisitions in the years ahead. In stereolithography, laser powder bed fusion, and FDM, companies’ strategies are shifting more and more toward profit-oriented structures. Their investments are thus being tied much more closely to specific market and profitability prospects. Some companies that have been active in AM for many years have even been making significant cuts and reorganizing their operations of late to reflect the market corrections that have taken place.
Meanwhile, the situation in new, forward-thinking technologies could hardly be more different: Expansive investments in start-ups like Seurat or Nexa3D have shown that AM is far from reaching its full potential and more major growth can be expected in the coming years.
Matthias Schmidt-Lehr is the co-founder and CEO of AMPOWER. Every year in March, the company publishes a marketing report that takes a look at the development of Additive Manufacturing around the world.
Ampower at Formnext 2021:
Hall 12.0, Booth E98
FURTHER INFORMATION:
Tags
- Additive Manufacturing