Chairs have been used to increase comfort for thousands of years. Whereas a simple wooden structure generally did the job in the early years, the concept has since evolved into a vast product field for a variety of purposes, including comfort, functionality, and design. Even though the perception of these three aspects has quite changed over time, the materials have remained mostly the same: wood, metal, foam, and fabric. Lately, however, demand has been growing for new solutions.
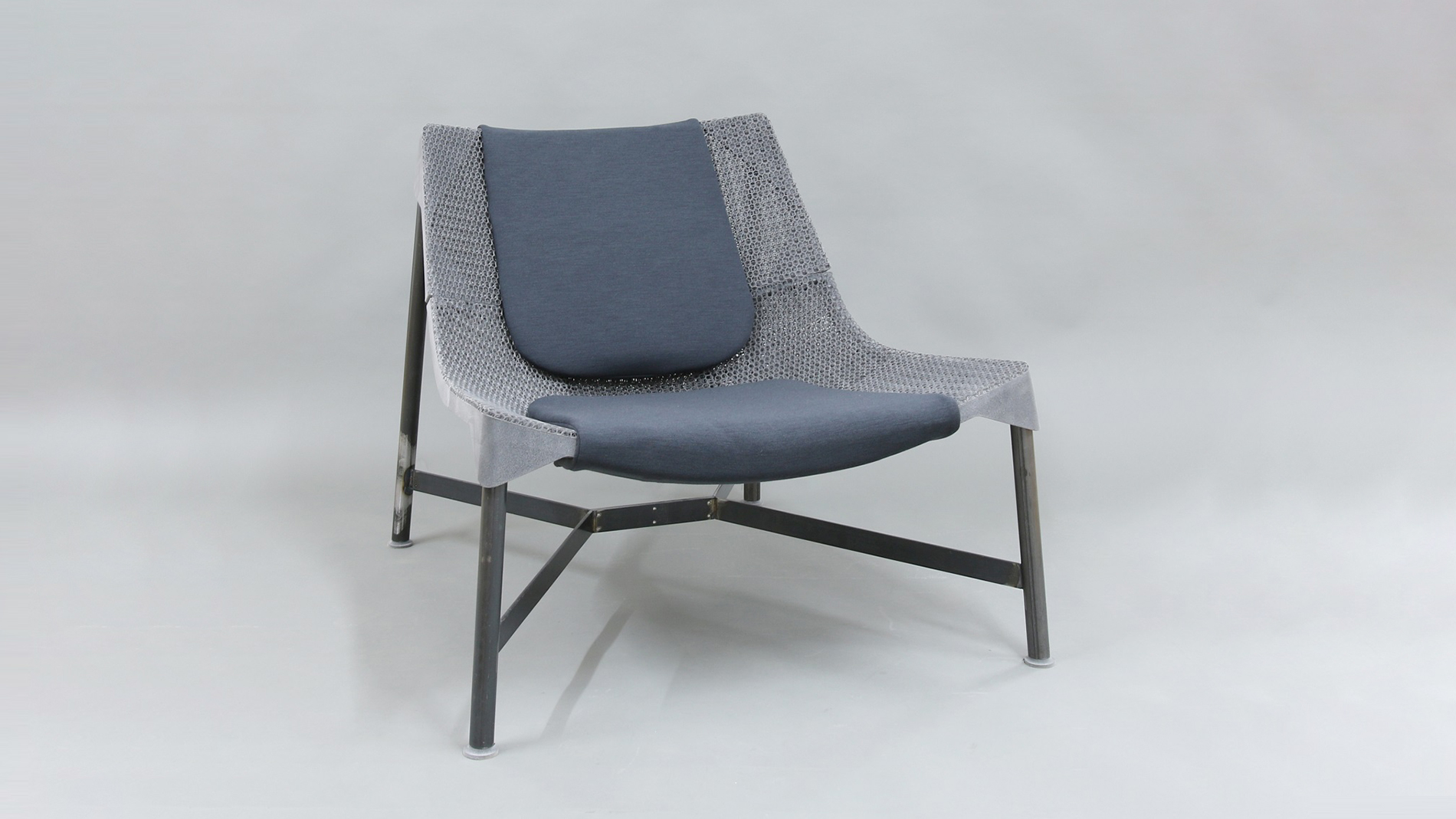
After setting out with the goal to build a perfect seat, the team at Oechsler AG realized that the furniture market had been sticking to similar materials for years. An additional analysis of usual production processes led to deep insights into how seating applications are constructed and manufactured. Armed with this knowledge, the team aimed to create a product that would not be a single futuristic copy, but a real alternative to previous seating.
Oechsler assigned the design portion of the project to a partner with corresponding expertise, namely Steinbauer Design. The main goal was to use as few materials as possible and achieve the highest flexibility in terms of design and functionality. The design approach aimed to reduce the parts used in conventional lounge chairs as much as possible by combining soft and hard parts into one component. Using lattice technology, Oechsler achieved these special properties and also printed the connection elements between the seat and chair feet using BASF’s Ultrasint TPU01 on a HP Jet Fusion 5210 3D printing solution.
Printed parts as a substitution for racks
The comfort of any sitting furniture depends on two main factors: the design and the cushioning. Endless combinations of different lattice sizes, thicknesses, and forms allow any degree of the latter variable.
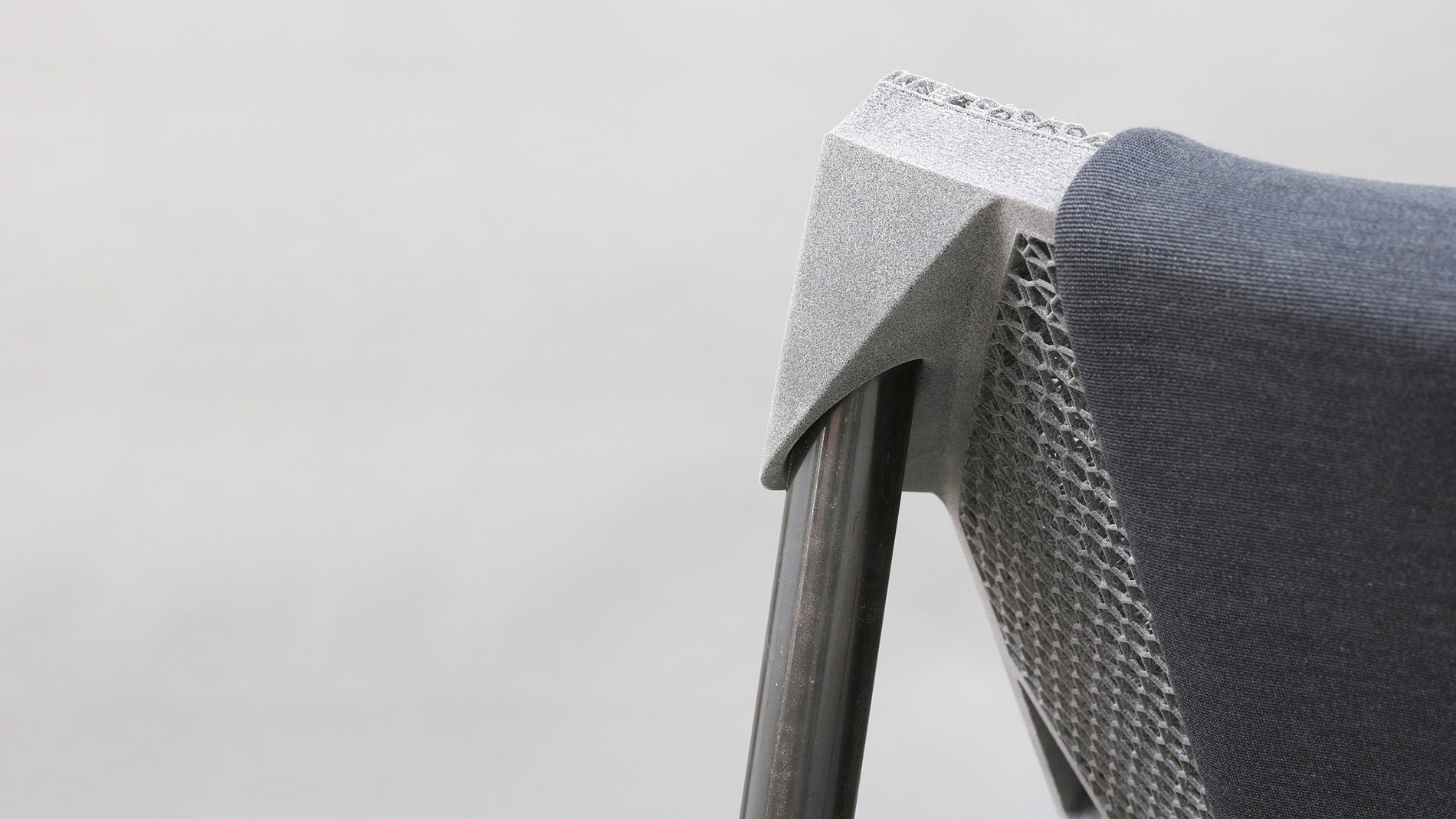
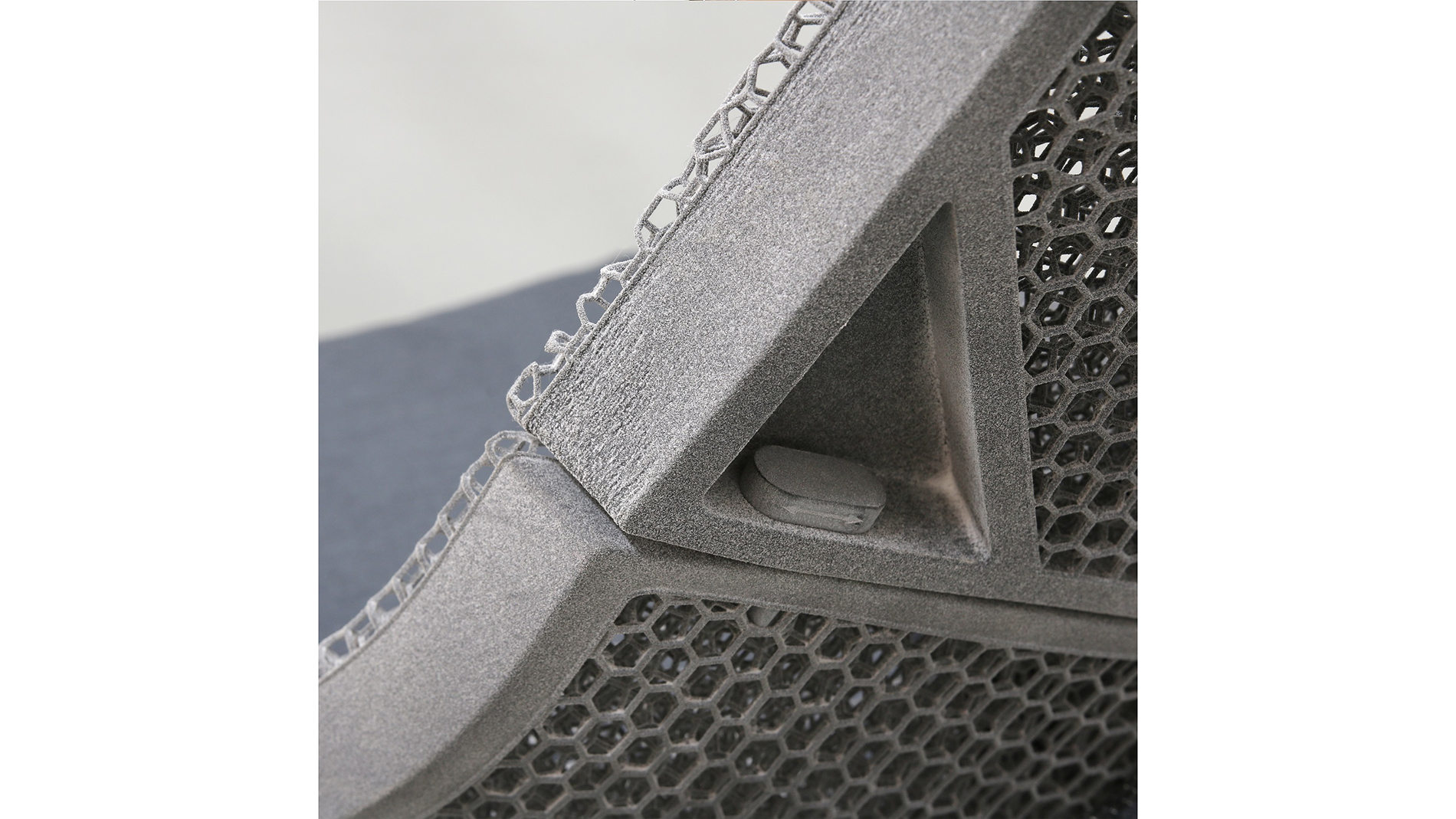
With the help of Additive Manufacturing, fabrics, springs, and foam layers can be eliminated without losing comfort. To stabilize parts of the seating, rigid printed parts serve as a substitution for racks. The 3D-printed product can also act as a base for further processing. By adding other printed components, racks, or textiles, for example, its appearance can easily be changed, offering a whole new variety of design perspectives.
By printing rigid and soft parts as one structure, Oechsler created the hybrid chair “Slope” with ergonomic and comfortable cushioning. An optional textile cover can simply be attached to the top. Moreover, the chair is very easy to disassemble and transport due to its light weight.
FURTHER INFORMATION:
Oechsler AG at Formnext 2021:
Hall 12.0, booth B62
Tags
- Additive Manufacturing