Text: Thomas Masuch, 7 November 2024
In the field of post-processing and ancillary process systems, Formnext 2024 exhibitors will be showcasing innovations for numerous AM technologies and for a wide range of requirements and applications. In one respect, the innovations are a response to the increasing number of ever larger and heavier additively manufactured components; here, Formnext will be showcasing new solutions for depowdering and post-processing. Exhibitors will also be presenting other exciting innovations, such as for heat treatment, debinding and coloring additively manufactured plastic components. Other innovations will focus on the removal of support structures – for example, with the help of dry ice or by using a dissolving station and soluble material.
De-powdering two-ton components
Solukon's new de-powdering system for beam-melted metal parts can handle components weighing more than two tons. The SFM-AT1500-S, which will be on display live for the first time at Formnext, is Solukon's largest metal de-powdering system to date. It can accommodate components measuring 600 x 600 x 1500 mm or 820 x 820 x 1300 mm with a maximum weight of 2,100 kg (including the build plate). To allow powder to flow, the solid component at hand must be subjected to strong vibrations. Solukon has developed a new decoupling concept to ensure that these vibrations are not transmitted to the rest of the system.
The new SFM-AT1500-S system will be on display live for the first time at Formnext. Image: Solukon
Post-processing components weighing up to 250 kg
Joke Technology will be showcasing its enhanced Eneskapostprocess 5.0 workstation for the safe post-processing of 3D-printed products at Formnext. This new generation offers a larger workspace, as well as optimized, efficient, and ergonomic handling. With the new Eneskapostprocess 5.0, Joke is responding to the trend toward larger and more complex 3D-printed components by offering a 50-percent-larger workspace (a 560-liter volume for components weighing up to 250 kilograms). Just 10 centimeters longer and wider than the original model, the workstation can be loaded manually or by forklift truck or crane.
The enhanced Eneskapostprocess 5.0 workstation. Images: Joke
Up to 1,400 °C
Nabertherm will be presenting the new LH..DB product series for the thermal treatment of ceramic parts and additively manufactured components at Formnext 2024. These compact furnaces are designed for debinding and sintering conventionally manufactured ceramic parts on a laboratory scale while also meeting the requirements of thermal post-processing in connection with additively manufactured components. Nabertherm’s new furnaces will be available in two sizes with volumes of 120 or 216 liters and maximum furnace temperatures of 1,300 or 1,400 °C. When using the optional gas box, processes can be performed at up to 1,100 °C.
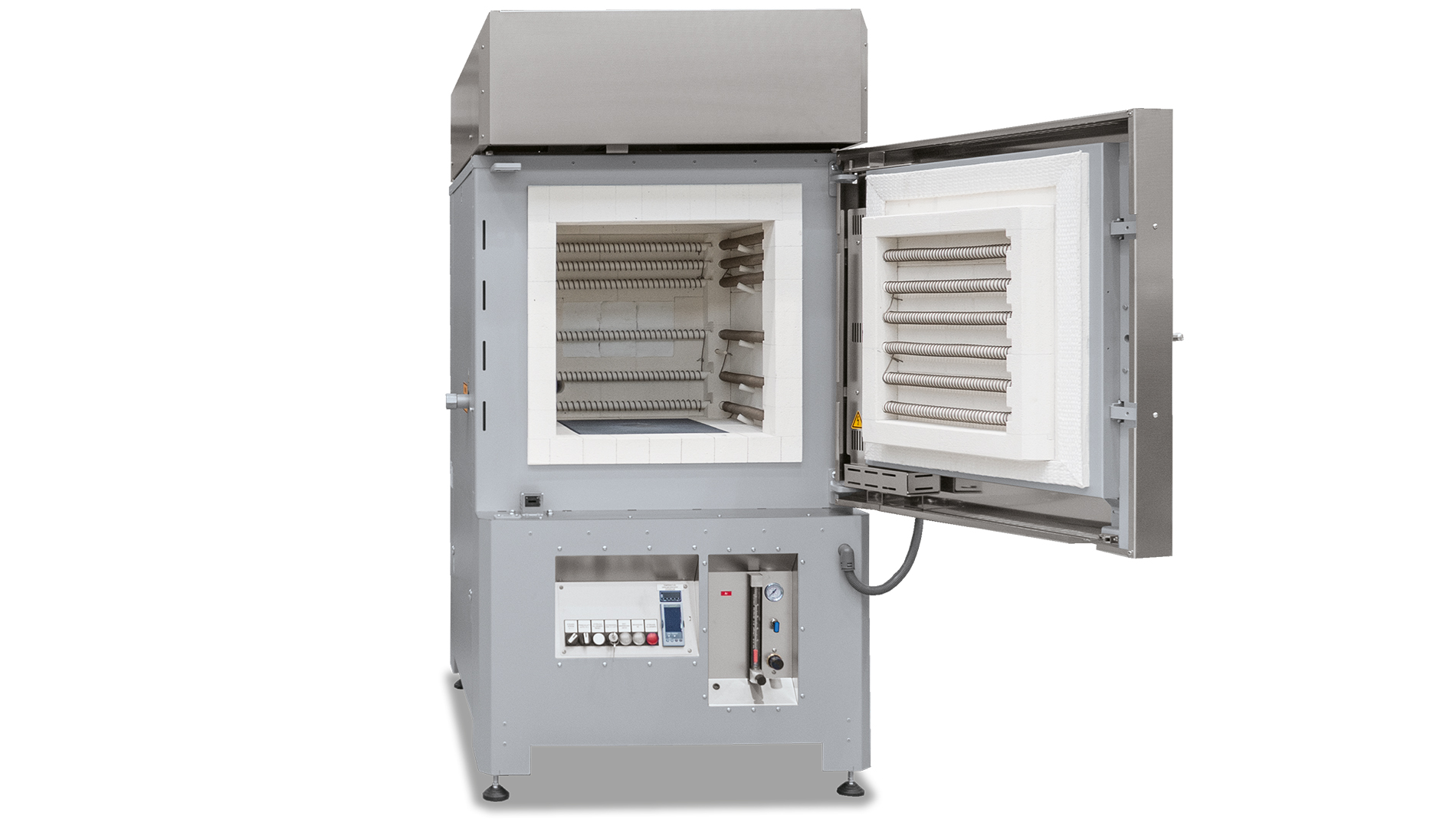
Coloring series parts and prototypes
The MiniColor, a dyeing system Thies has specifically designed for additively manufactured polymer parts, will be showcased at Formnext. According to the company, the system is suitable for coloring series components, spare parts, and functional prototypes efficiently and consistently. The new T390 control system monitors every process step to ensure reliability, while the new Smart Color Inject function eliminates the need for manual dye preparation by the machine operator. The system also enables automated liquid dye handling and precise dye feeding, which guarantees color reproducibility.
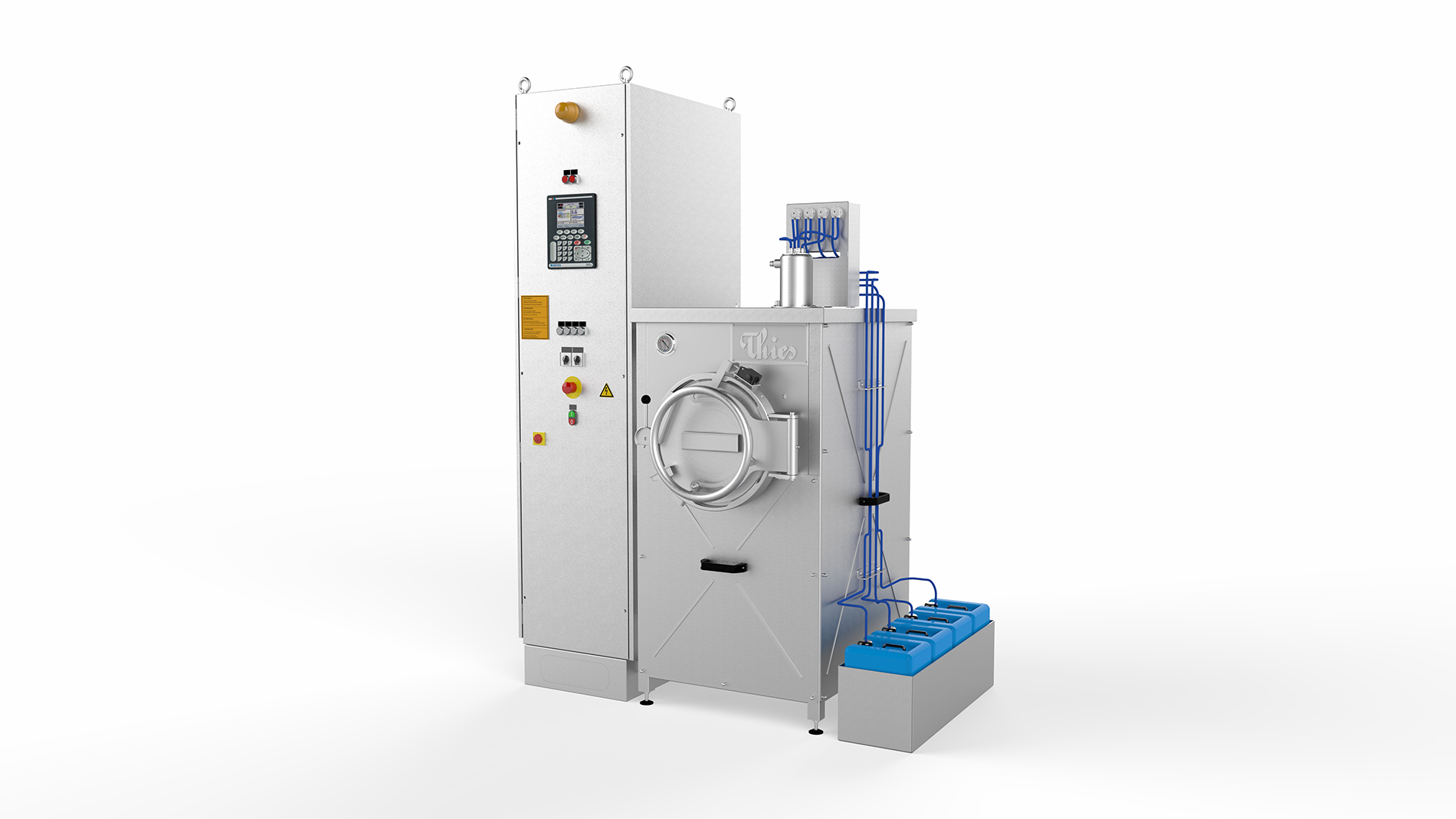
Removing support structures with dry ice
AMbitious powered by Toolcraft will be presenting the use of dry ice blasting to remove support structures at Formnext. Until now, this process was often time-consuming and manually burdensome for metal 3D-printed components. The dry ice blasting system offers an efficient solution by semi-automating the process and improving ergonomic working conditions. The throughput time per component can be reduced by up to 15 minutes, as AMbitious reports. In addition, working conditions are improved through the minimization of physically strenuous activities. This technology is already being used successfully in production at Toolcraft AG.
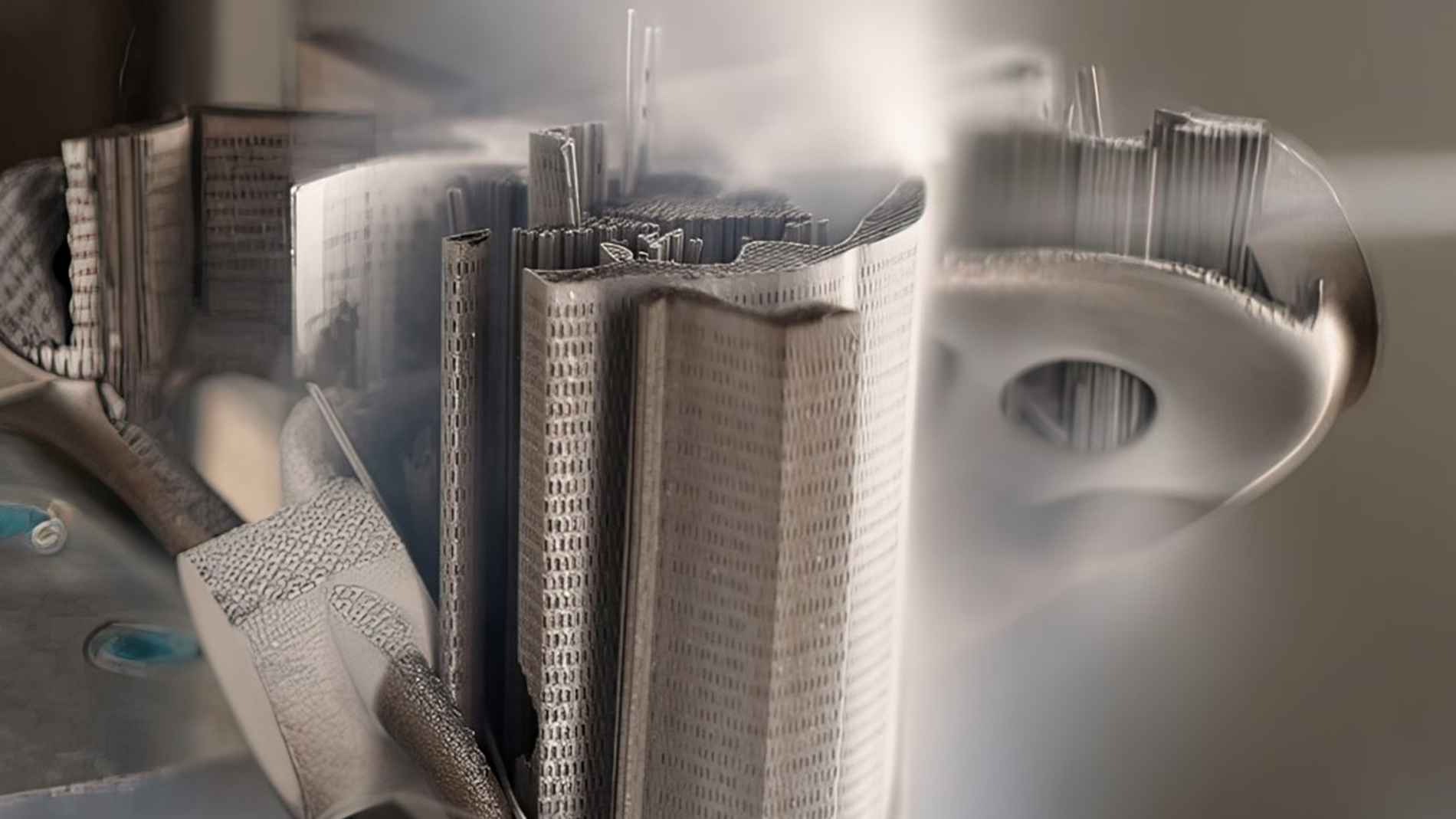
Soluble solutions
Xioneer focuses on soluble support materials and post-processing solutions for granulate and filament 3D printing. At Formnext, the company is presenting its new VXL 150 support material, which has been specially developed for high-temperature printing, as well as the new Vortex XL tank. This tank is available in three different versions, each with a nearly doubled capacity of 60 liters. Xioneer will also be presenting the new Vortex EZ Dental dissolving station, a heatable desktop device for quick and easy removal of support materials in a water bath.
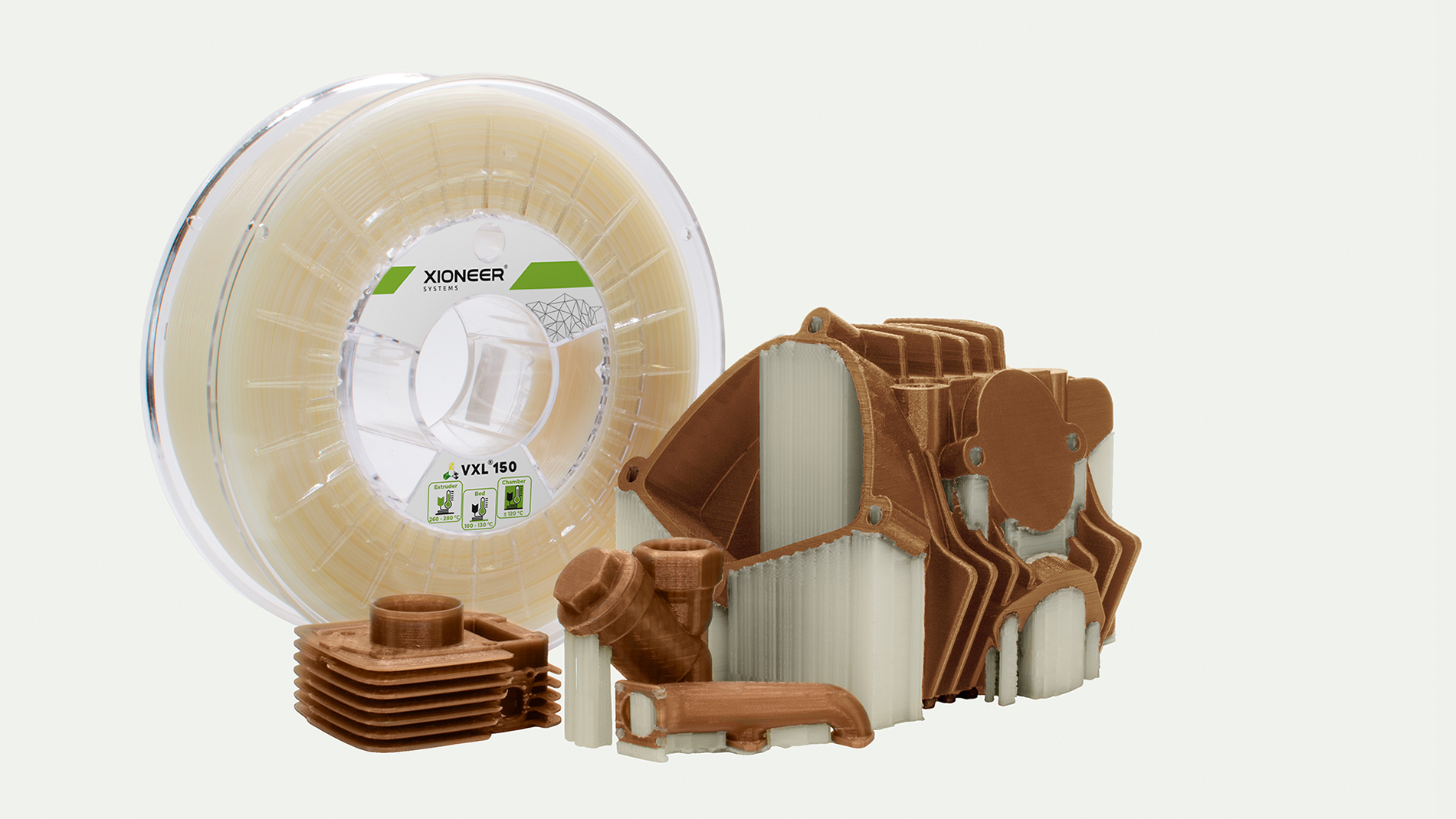
FURTHER INFORMATION:
You will find all the companies mentioned at Formnext 2024:
AMbitious powered by Toolcraft: Hall 12.1, Booth D101
Joke Technology: Hall 12.0, Booth D 121
Nabertherm: Hall 11.0, Booth A31
Solukon: Hall 12.0, Booth D71
Thies: Hall 12.1, Booth B02
Xioneer: Hall 12.1, Booth E121
Tags
- Additive Manufacturing