Text: Thomas Masuch, 17 February 2024
Materials are the key to new applications that will lead to more widespread use of additive manufacturing. The number of different powders available is rather limited, however – especially in metal 3D printing. While the demand for new materials is definitely there, the process of developing them is complex and expensive.
Those who work in metal 3D printing have a few dozen standard materials at their disposal, ranging from various types of steel to copper, titanium, and aluminum alloys and even cobalt and tungsten. “Plenty of OEMs and tier-one companies are looking for alternative materials in small volumes,” reports Dr. Haneen Daoud, deputy head of the metals division at Neue Materialien Bayreuth (NMB). “Powder manufacturers, however, are only willing to produce large quantities.” At the moment, she is seeing the most demand for special materials (see definition below) in the aviation industry, renewable energy, hydrogen and thermal energy, and electromobility. Institutes like NMB specialize in developing and manufacturing powders in the smaller quantities companies need. “This enables them to carry out feasibility studies and bring new products to market,” Dr. Daoud explains.
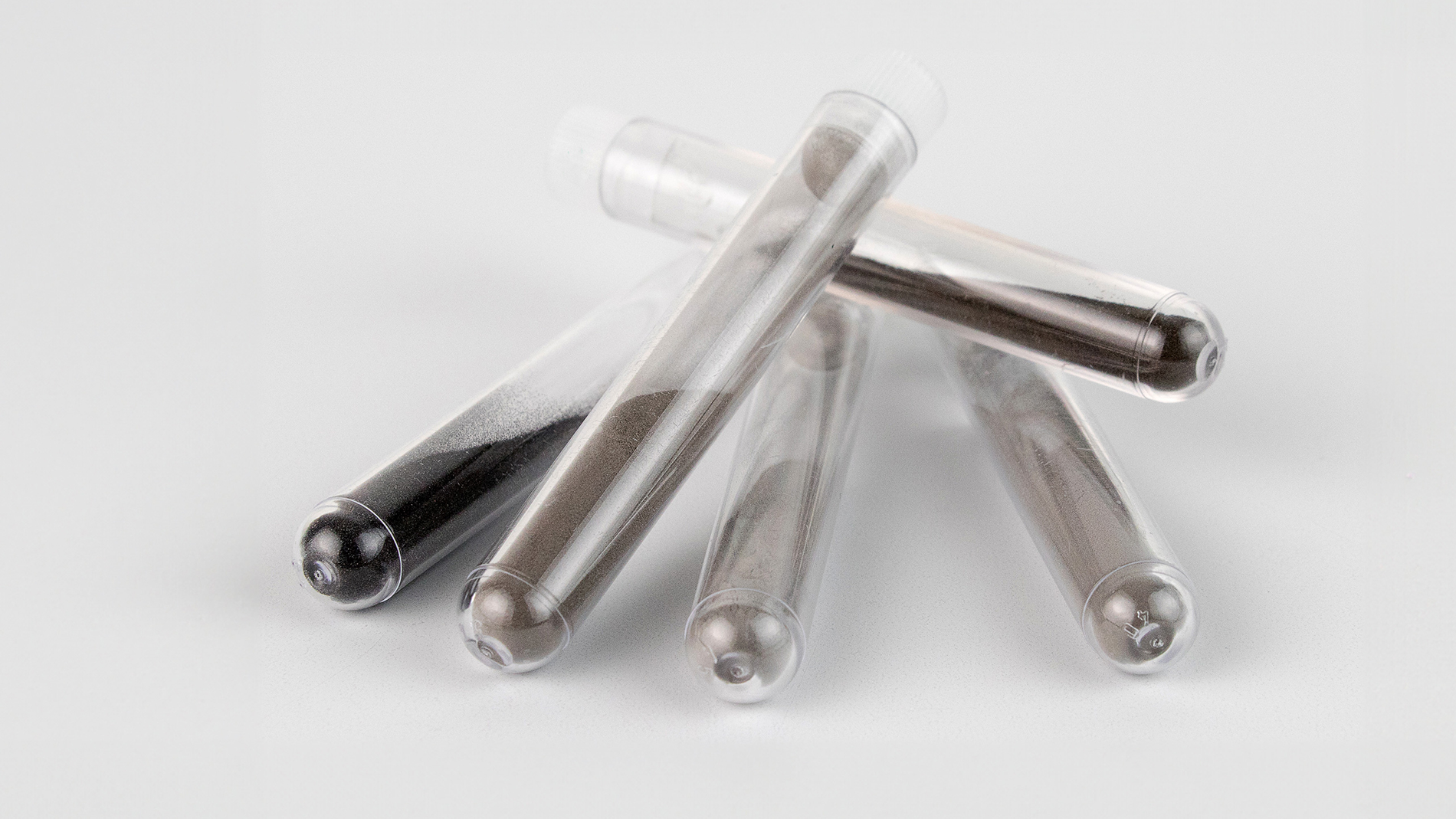
Image: Mimete
Creating a special material for use in AM isn’t exactly easy, though. Nico Geis, a technology transfer expert at NMB, estimates that it takes around three to four years to develop a new metal alloy for additive manufacturing. “At the same time, the current market for special materials in AM is small in terms of volume,” Geis reports, which is why not many investments are being made in this sector.
The customers that commission NMB to come up with new materials are often midsized companies that leverage the resulting research to expand their production expertise (which they then keep in-house). In other words, there may be any number of new AM solutions and materials out there already; they’re just not on the open market. For many companies, research of this kind is tremendously important when it comes to gaining a competitive edge. “It’s often what gives rise to the DNA at the heart of the next generation,” Geis reveals.
Using less energy and raw material
Dr. Daoud reckons there are around 10 to 20 special materials on the market. It’s also hardly unheard of for different companies to be developing the same powders at the same time. “Users are often working toward the same goals to improve the characteristics of things they’re already selling,” she says. In developing new materials, firms are often looking to overcome similar challenges, such as the need to save energy and raw materials or increase the useful life of their products.
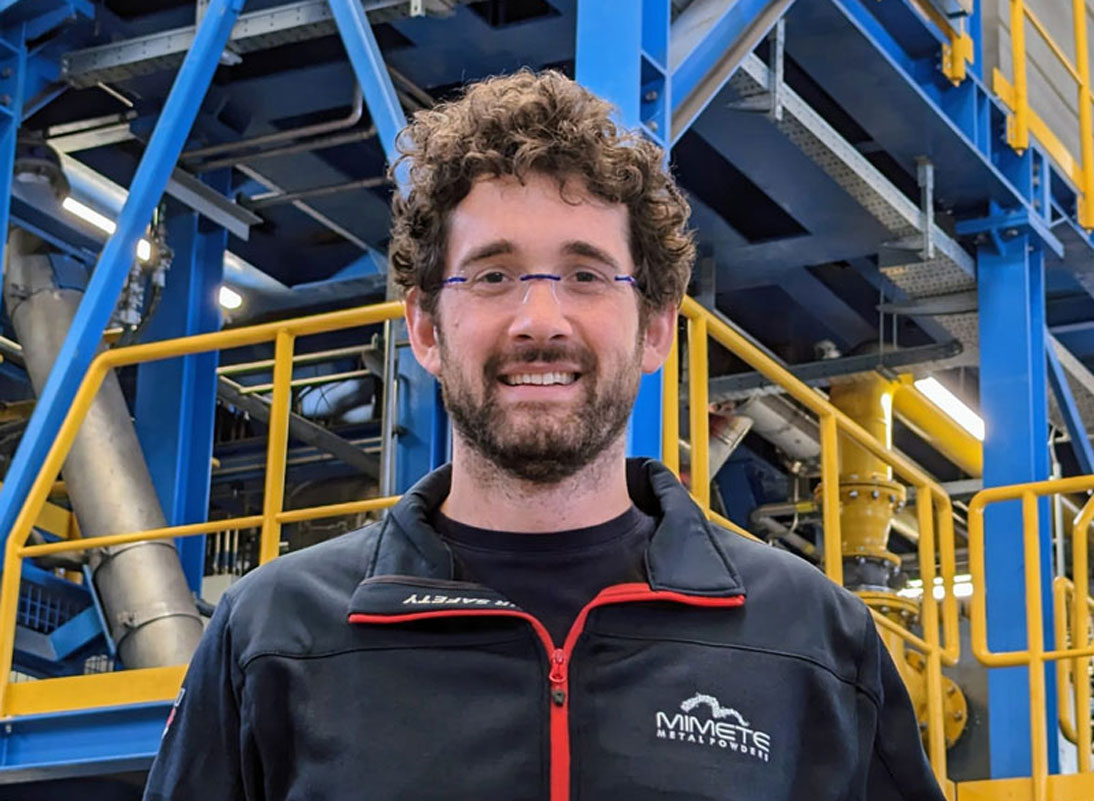
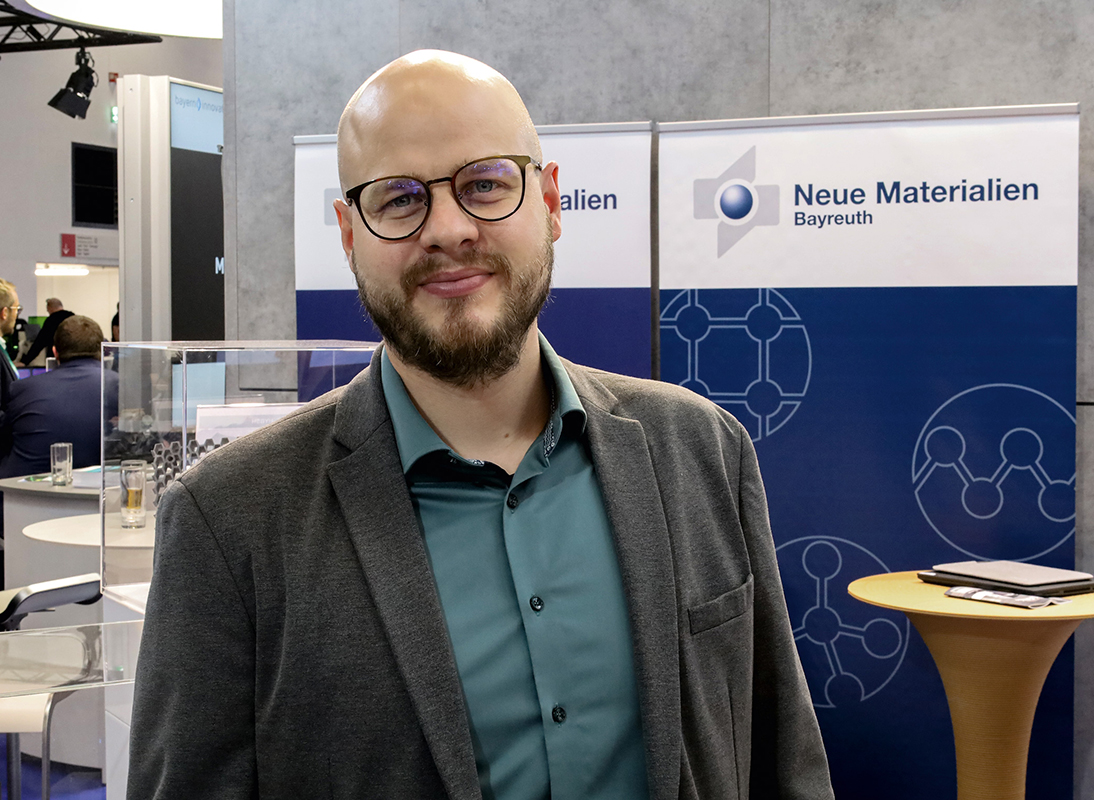
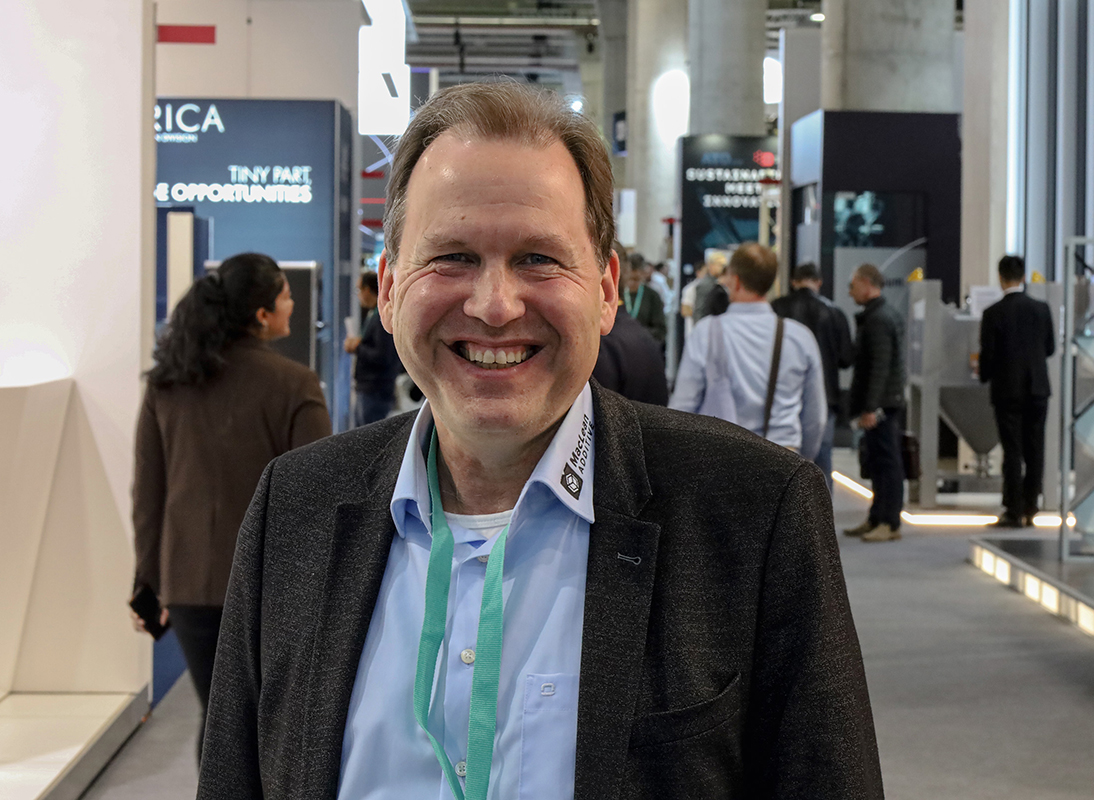
Andrea Tarabiono, Nico Geis, and Harald Lemke (from the left) were among those showcasing their companies' material expertise at Formnext 2023. Images: Thomas Masuch, Mimete
The successful applications NMB has realized with special materials in AM include pump components, seals, and turbine parts that need to withstand extremely high temperatures (around 700° C). In these cases, the institute has made use of titanium-, nickel-, and cobalt-based materials that are either difficult or impossible to weld, but offer high creep resistance, the desired thermomechanical properties, and very good resistance to oxidation. “Without these materials, we wouldn’t have been able to achieve those characteristics,” Dr. Daoud says.
Five variants of one superalloy
Another way to find the right material for a particular use case is to conduct a series of targeted experiments, explains Andrea Tarabiono, production manager at Mimete. After identifying five variants of a nickel superalloy that suited its purposes, an OEM ordered small batches of the variants from this Italian producer of AM powders. Some initial tests of the materials’ compatibility with laser powder bed fusion (LPBF) were conducted, and one variant was then selected for further testing. Following additional analysis (including with larger batches), the metal powder in question made a successful transition into production.
Careful consideration required
When you talk with Harald Lemke, you quickly realize why the development of new materials is anything but a straightforward endeavor. As director of product management at MacLean-Fogg Component Solutions, Lemke develops and brings to market types of steel that are specifically designed for AM-based toolmaking. He says he hears calls for “advanced materials” all the time at industry conferences. “To succeed in developing and commercializing materials like these, however, you have to make some very detailed considerations,” he points out.
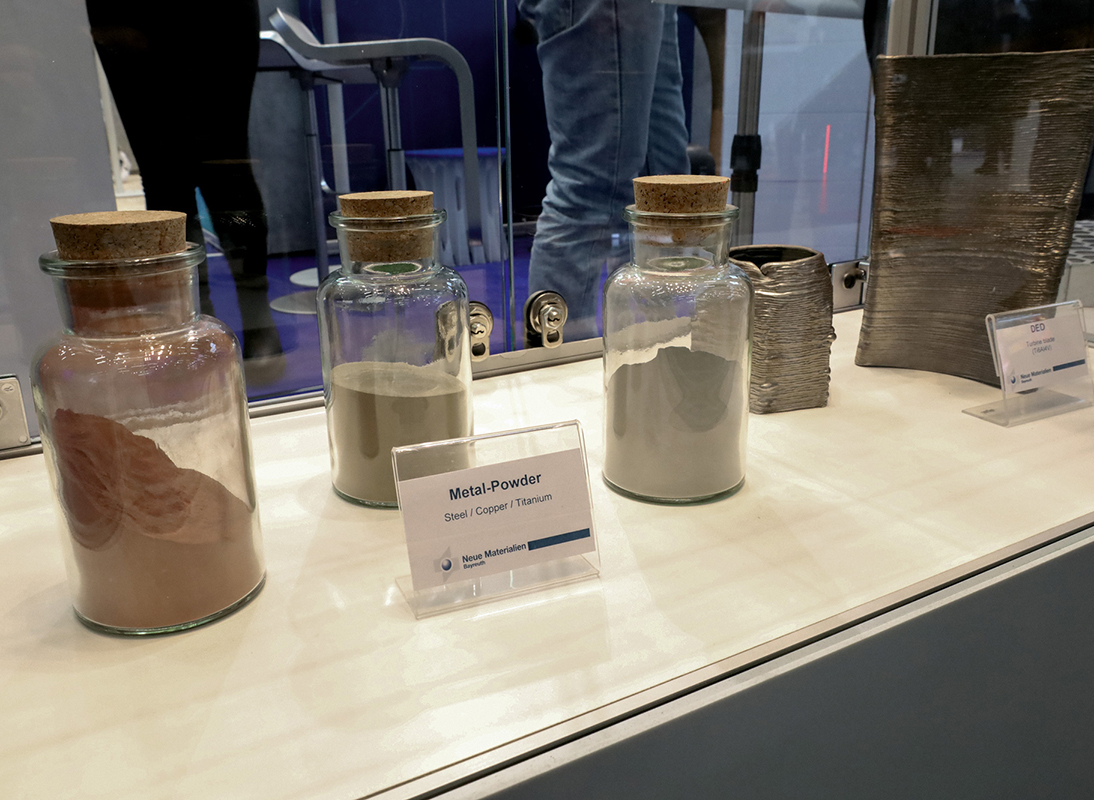
At Formnext, NMB not only presented various powders ...
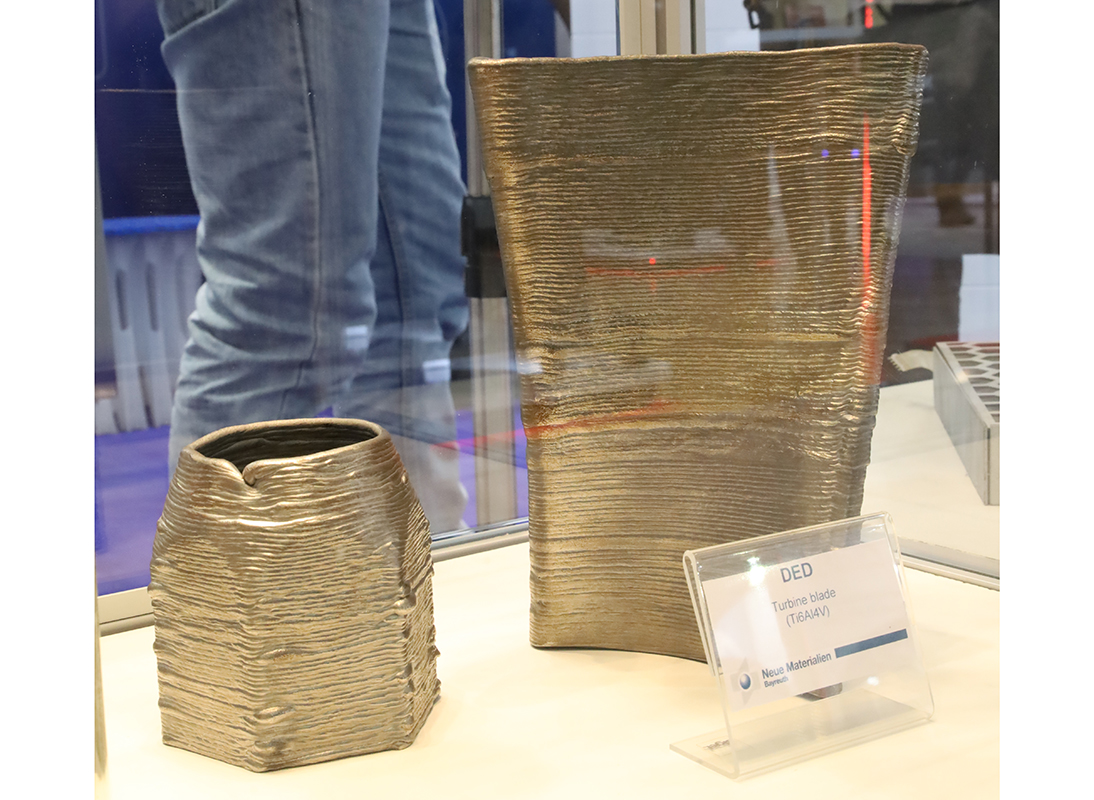
....but also applications such as a turbine blade printed in the DED process....
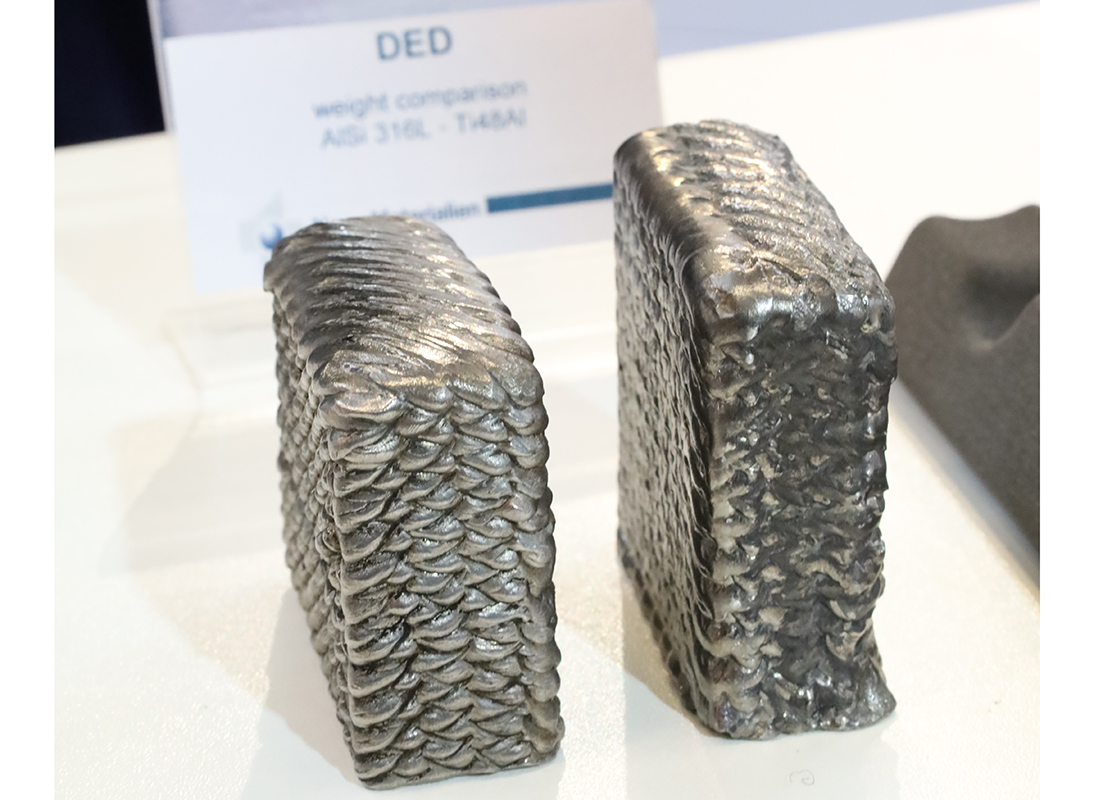
....or a weight comparison of AlSi316L and Ti48Al. Photos: Thomas Masuch
Lemke is aware of a number of advanced LPBF materials that are “in the pipeline” in spite of the significant challenges involved. The number is quite small, though, and materials like these are typically only used in small quantities, which he attributes to the long lead times and test cycles in material development. “The development costs are often too high, and the commercialization process takes too long,” Lemke affirms. Considering how niche most of the current markets are for which such materials can be optimized, he says it’s virtually impossible to turn a profit.
“That’s why it’s no wonder end users still mainly use conventional materials for most LPBF applications,” he continues. “Until such applications seem scalable, we won’t see evolutionary improvements that optimize the alloys for LPBF.” According to Lemke, modifications like these can be found in nickel and titanium alloys in particular, as well as in alloys of aluminum and steel.
A high degree of effort
For Dr. Daoud, meanwhile, the significant amount of work involved in developing special materials stems from the unique aspects of 3D printing with metal. For one thing, the corresponding material systems are usually not available in the form of wire or powder. The parts produced also tend to cool quickly, which leads to cracks and severely limits the feasible size of additively manufactured components. And as if the whole undertaking wasn’t already complicated enough, the properties of atomized powders vary a great deal from producer to producer. “That sometimes means having to spend a lot of time adjusting your process parameters,” Dr. Daoud says.
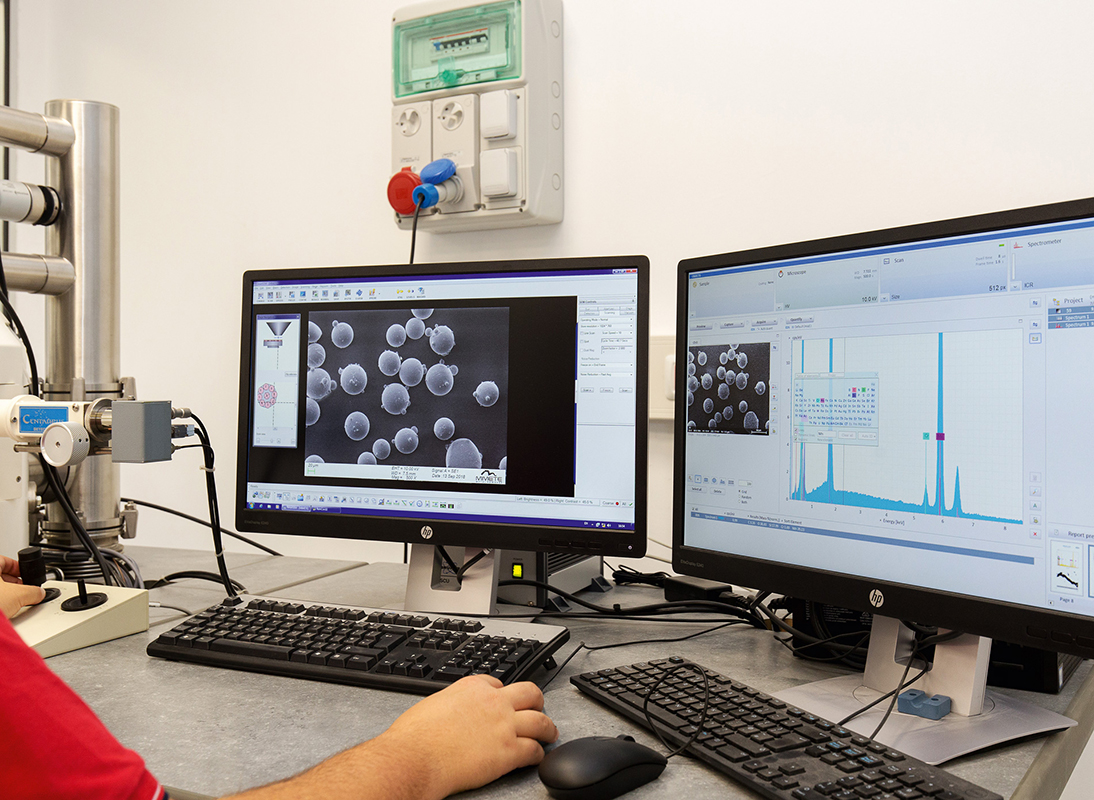
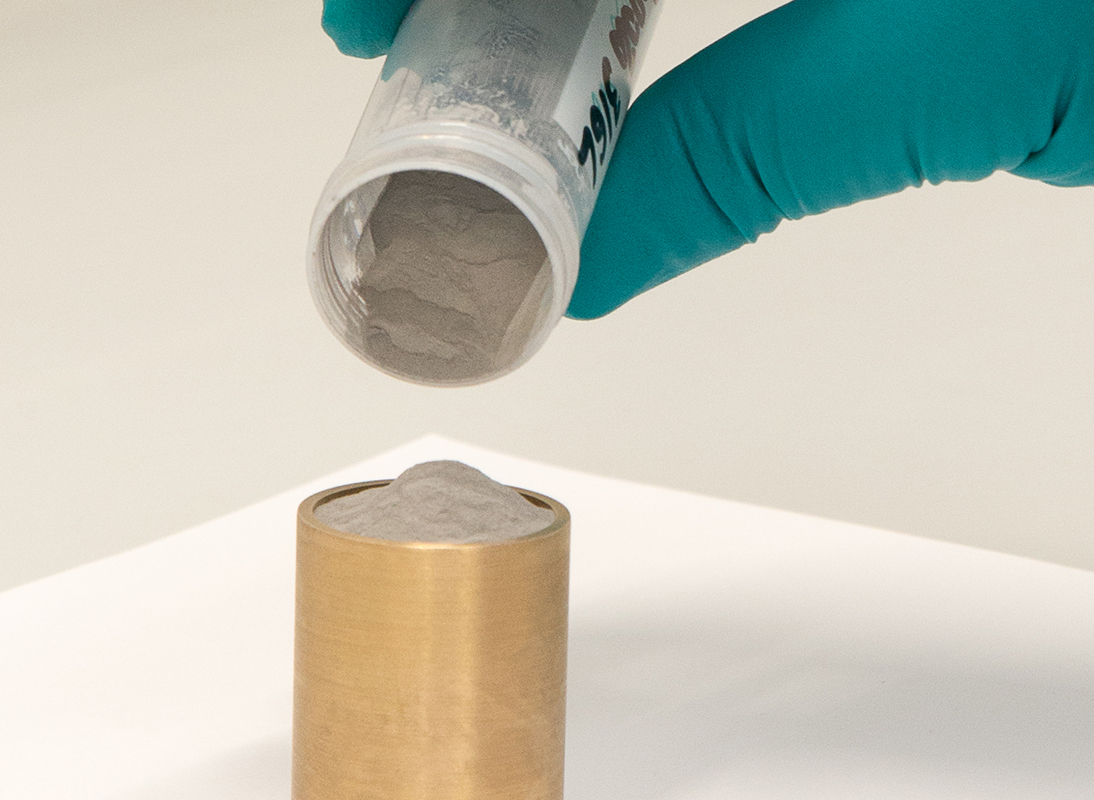
Material development in the laboratory at Mimete. Image: Mimete
Different approaches to research
NMB’s research on new materials takes place either as part of doctoral theses or in bilateral research projects that are financed by one or more companies. Efforts to solve “larger issues” of a fundamental nature can also be eligible for public funding. Here, NMB handles the actual material development up to the point of small series production, which includes relevant methods of characterization. The requests it receives come from both companies interested in using the resulting materials and firms that produce or supply materials themselves.
“Before you start developing a new material, you have to ask yourself a number of different questions,” explains Nico Geis. “How much effort will the project take? Is there a market that’s willing to pay for the material? And along with the economic aspects, the question of how a new material performs in a lifecycle assessment is one that’s coming up more and more in market research.” For example, it’s an advantage in terms of both economics and energy if the gases used in a given process can be recovered and refined by means of corresponding system technology.
The research projects at NMB – which cover plastics, as well – also try to find ways to come up with solutions faster by means of more intelligent processes. “In some cases, we don’t even need a new material,” Geis says. “We can reach our objectives with coatings, surface finishing, multimaterial printing, or hybrid materials.” Sometimes, a new production process also leads to new results. Take the time NMB combined two unalloyed materials in wire form in a DED process, for instance, in a targeted effort to achieve better material characteristics for specific use cases – all without using adapted raw materials. “Nothing is impossible in chemistry, but you do have to think things all the way through, including with regard to processing and the eventual application at hand,” Geis says.
Definitions
Special materials combine various properties (such as hardness, ductility, or resistance to rust) to offer the best possible solution for a particular set of requirements. (Harald Lemke)
Special materials are designed for requirements or applications where the standard materials available don’t offer an adequate solution. (Nico Geis)
FURTHER INFORMATION:
Tags
- Materials
- Additive Manufacturing
- Research and development