Text: Thomas Masuch, 17.02.2024
Materialien sind der Schlüssel zu neuen Anwendungen und damit zur stärkeren Verbreitung der Additiven Fertigung. Doch die Zahl der Pulver, insbesondere für den Metall-3D-Druck, ist recht überschaubar. Der Bedarf nach neuen Materialien ist da – doch die Entwicklung ist aufwendig und teuer.
Im Metallbereich sind einige Dutzend Standardmaterialien verfügbar – das reicht von verschiedenen Stählen über Kupfer-, Titan- und Aluminiumlegierungen bis hin zu Kobalt und Wolfram. „Viele OEMs und Tier-1-Unternehmen sind auf der Suche nach alternativen Materialien in kleinen Mengen, aber die Pulverhersteller sind nur bereit, in großen Mengen zu produzieren“, berichtet Dr.-Ing. Haneen Daoud, stellvertretende Leiterin Geschäftsbereich Metalle bei Neue Materialien Bayreuth (NMB). Den größten Bedarf an Sondermaterialien (siehe Definition unten) sieht Daoud derzeit in der Luftfahrtindustrie, den erneuerbaren Energien, der Wasserstoff- und Wärmeenergie und der Elektromobilität. Institute wie NMB haben sich darauf spezialisiert, Pulver in kleinen Mengen zu entwickeln und herzustellen. „Damit können dann Machbarkeitsstudien erstellt und neue Produkte auf den Markt gebracht werden.“
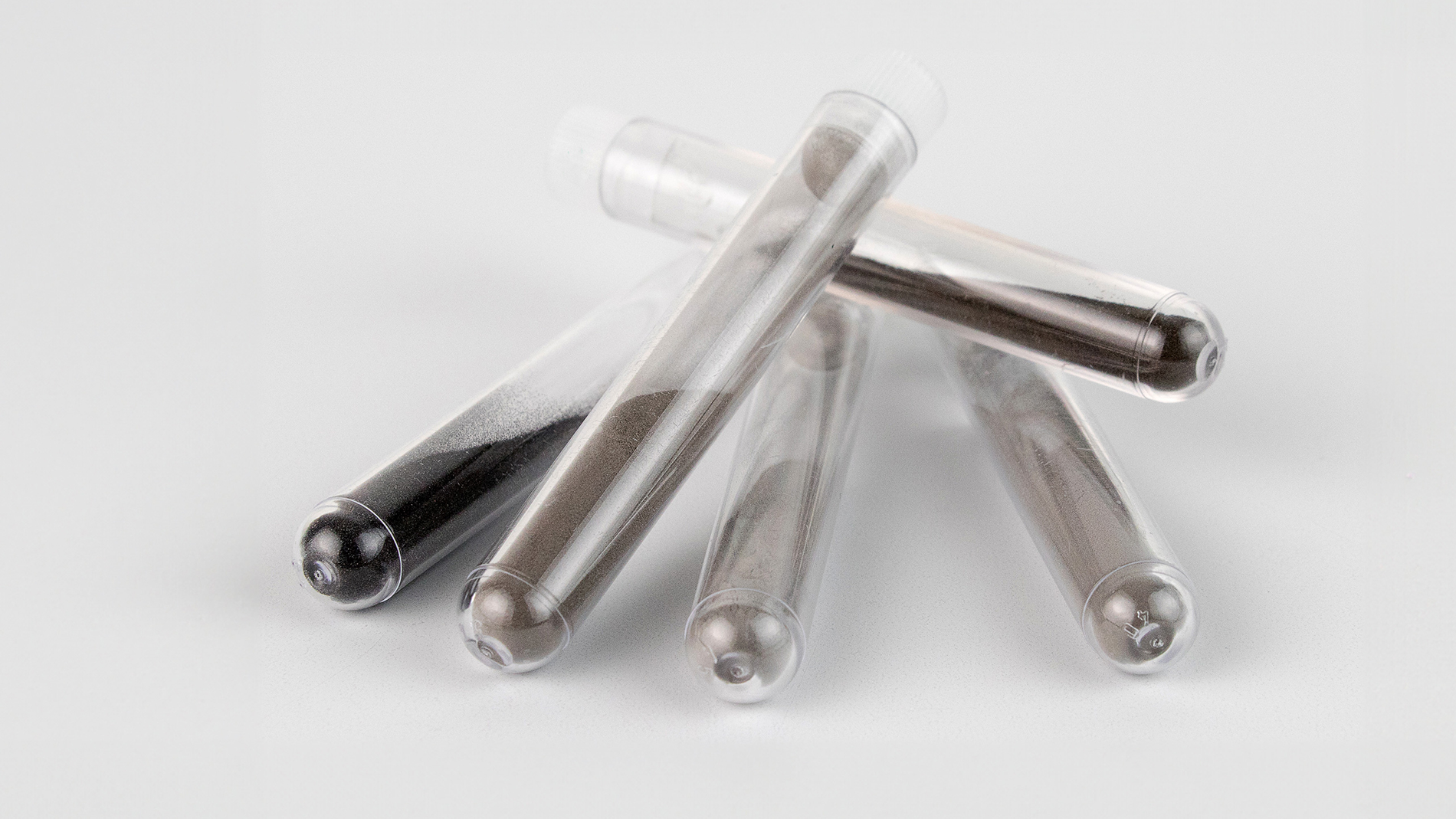
Bild: Mimete
Doch der Aufwand, um solch ein Sondermaterial für den Einsatz in der Additiven Fertigung zu entwickeln, ist nicht gerade gering: Auf rund drei bis vier Jahre schätzt Nico Geis, Experte für Technologietransfer bei NMB, die Entwicklungszeit für eine neue Metall-Legierung für die Additive Fertigung. „Allerdings ist der Markt für Sondermaterialien in der Additiven Fertigung derzeit vom Volumen her gering“, sodass die Investitionen in diesem Sektor recht überschaubar bleiben.
Die Kunden, die bei NMB neue Materialien entwickeln lassen, sind oftmals mittelständische Betriebe, die mithilfe der Forschungsarbeiten ihr Produktions-Know-how erweitern (und es auch intern behalten). Das bedeutet: So manche neue AM-Lösung und neue Werkstoffe gibt es vielleicht schon, sie sind allerdings nicht auf dem Markt verfügbar. Für viele Unternehmen sind solche Forschungen allerdings enorm wichtig, um sich einen Wettbewerbsvorteil zu verschaffen. „Daraus leitet sich oft die DNA für die nächste Generation ab“, erklärt Geis.
Rohstoffe und Energie einsparen
Rund 10 bis 20 Sondermaterialien gibt es auf dem Markt, schätzt Haneen Daoud. Dabei kann es durchaus vorkommen, dass verschiedene Unternehmen parallel an der Entwicklung gleicher Pulver arbeiten. „Oft haben die Anwender die gleichen Ziele, um die Eigenschaften ihrer derzeit verkauften Produkte zu verbessern.“ So wollen verschiedene Unternehmen mit der Entwicklung neuer Materialien ähnliche Herausforderungen lösen, zum Beispiel Rohstoffe und Energie zu sparen oder die Lebensdauer der Produkte zu verlängern.
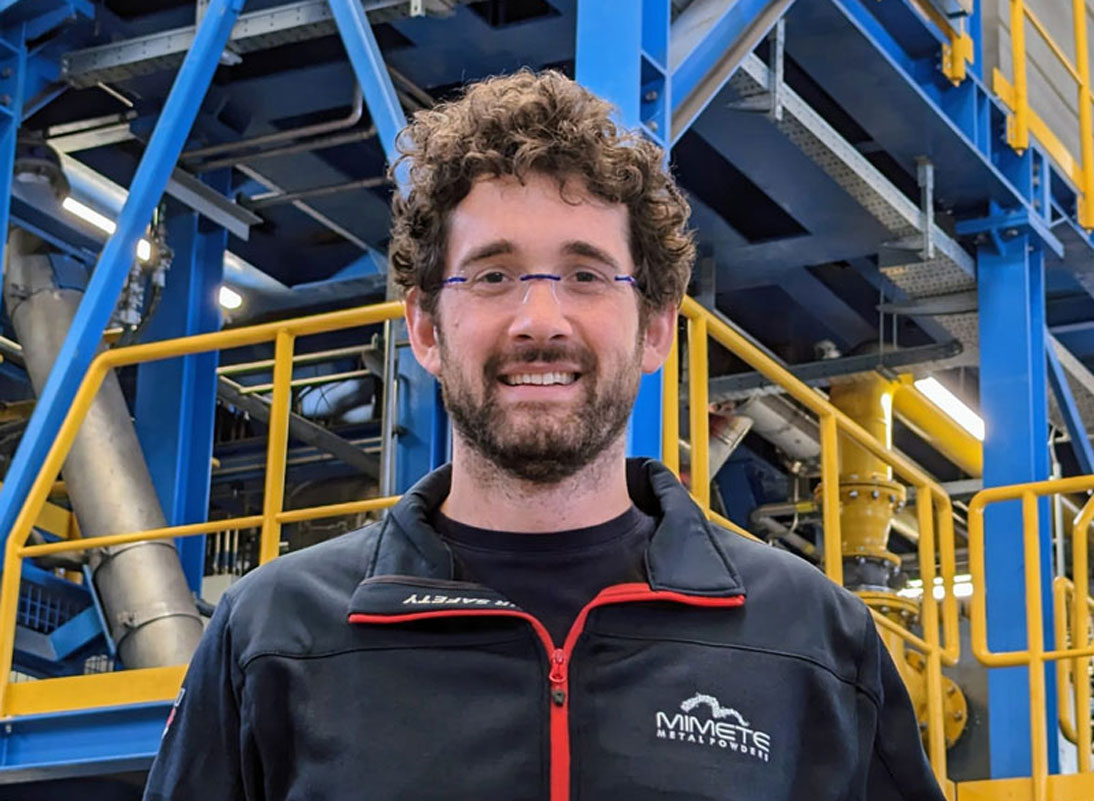
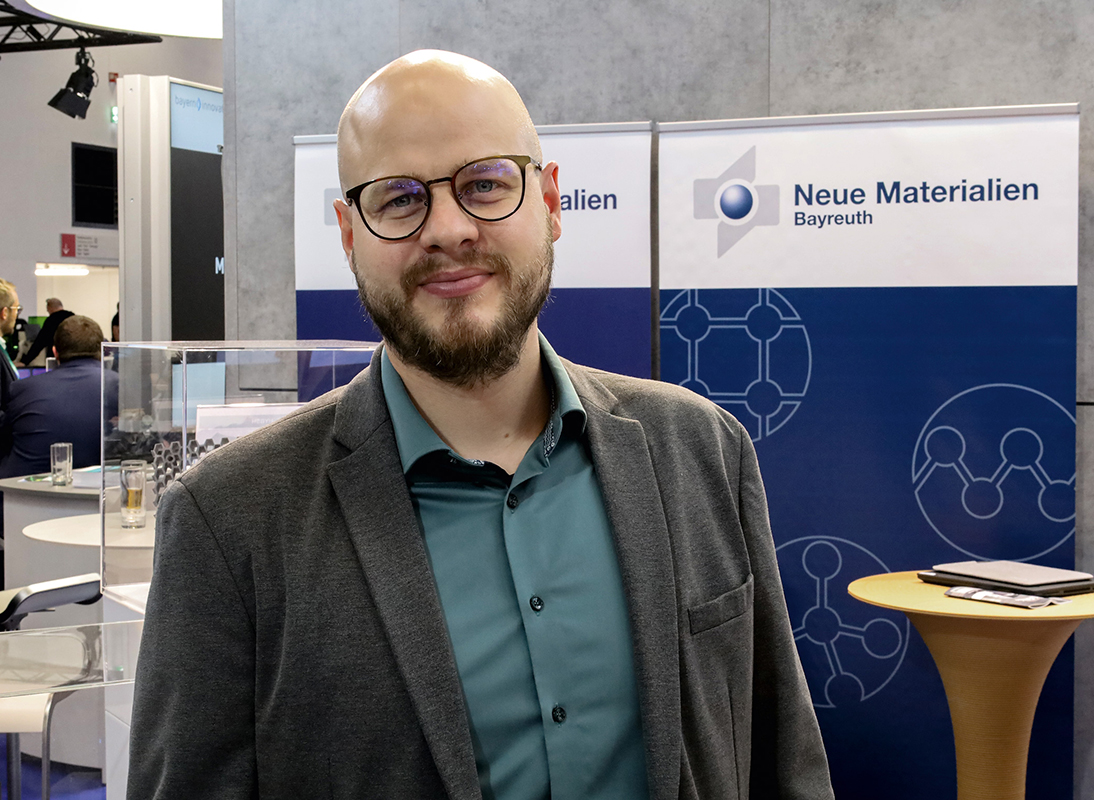
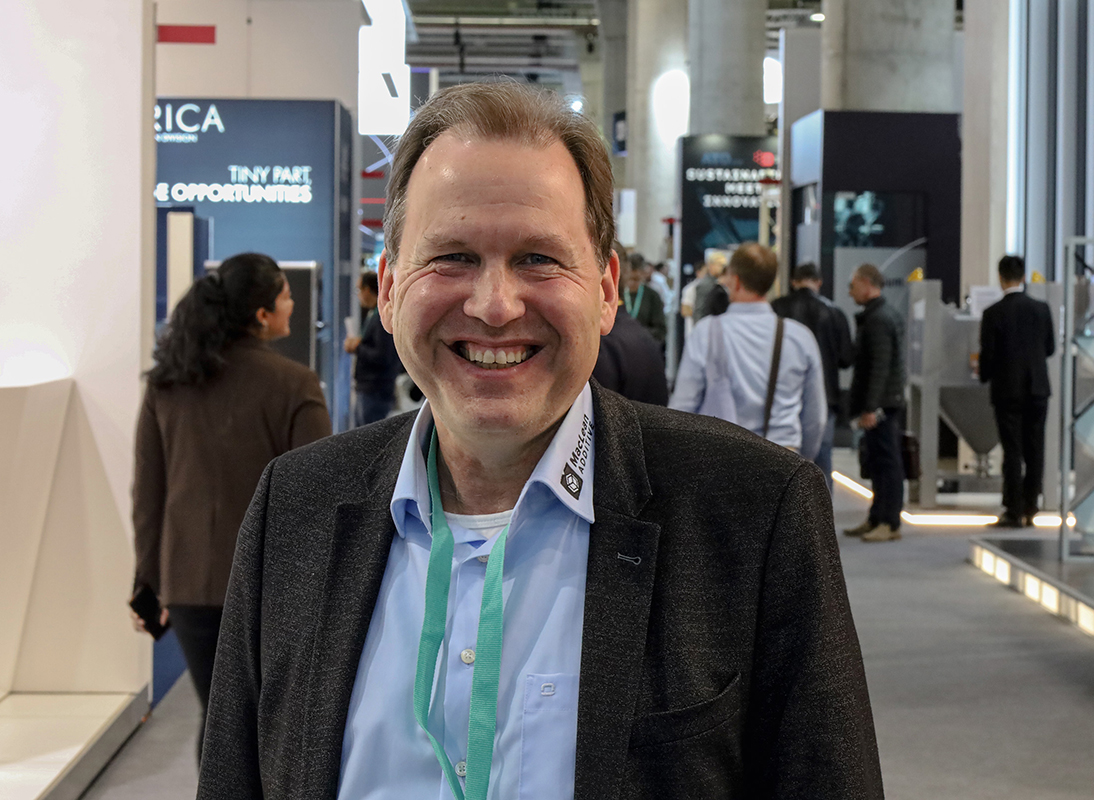
Zeigten mit ihren Unternehmen auch auf der Formnext 2023 ihre Kompetenz im Bereich Materialien: Andrea Tarabiono , Nico Geis und Harald Lemke (von links). Fotos: Thomas Masuch, Mimete
Beispiele für erfolgreiche Anwendungen, die NMB mit Sondermaterialien in der Additiven Fertigung erzielen konnte, sind zum Beispiel Pumpenteile, Dichtungen oder Turbinenteile, die sehr hohen Temperaturen bis zu 700 °C ausgesetzt sind. Dabei kamen schlecht und nicht schweißbare Werkstoffe auf Titan-, Nickel- und Kobaltbasis, die eine hohe Kriechbeständigkeit, die gewünschten thermomechanischen Eigenschaften und eine sehr gute Oxidationsbeständigkeit bieten, zum Einsatz. „Diese Merkmale konnten nur durch die Verwendung dieser Materialien erreicht werden“, erklärt Haneen Daoud.
Fünf Varianten
Gleichzeitig kann die Suche nach dem passenden Material auch über eine gezielte Versuchsreihe laufen, erklärt Andrea Tarabiono, Production Manager bei Mimete. Ein OEM hatte fünf Varianten einer Nickelsuperlegierung identifiziert und kleine Chargen bei dem italienischen AM-Pulverhersteller bestellt. Nach ersten Tests zur LPBF-Verarbeitbarkeit wurde eine Variante für weitere Tests ausgewählt. Später folgten weitere Tests, auch mit größeren Chargen, und das Metallpulver wurde danach erfolgreich in die Produktion überführt.
Entwicklung erfordert detaillierte Überlegungen
Wenn man sich mit Harald Lemke unterhält, wird recht schnell klar, warum die Entwicklung neuer Materialien nicht gerade ein einfaches Geschäft ist. Lemke, der als Director of Product Management bei MacLean-Fogg Component Solutions spezialisierte AM-Sonderstähle für den Werkzeugbau entwickelt und auf den Markt bringt, hört auf Konferenzen immer wieder den Ruf nach sogenannten fortschrittlichen Materialien. „Doch deren erfolgreiche Entwicklung und ihre Kommerzialisierung erfordern sehr detaillierte Überlegungen.“
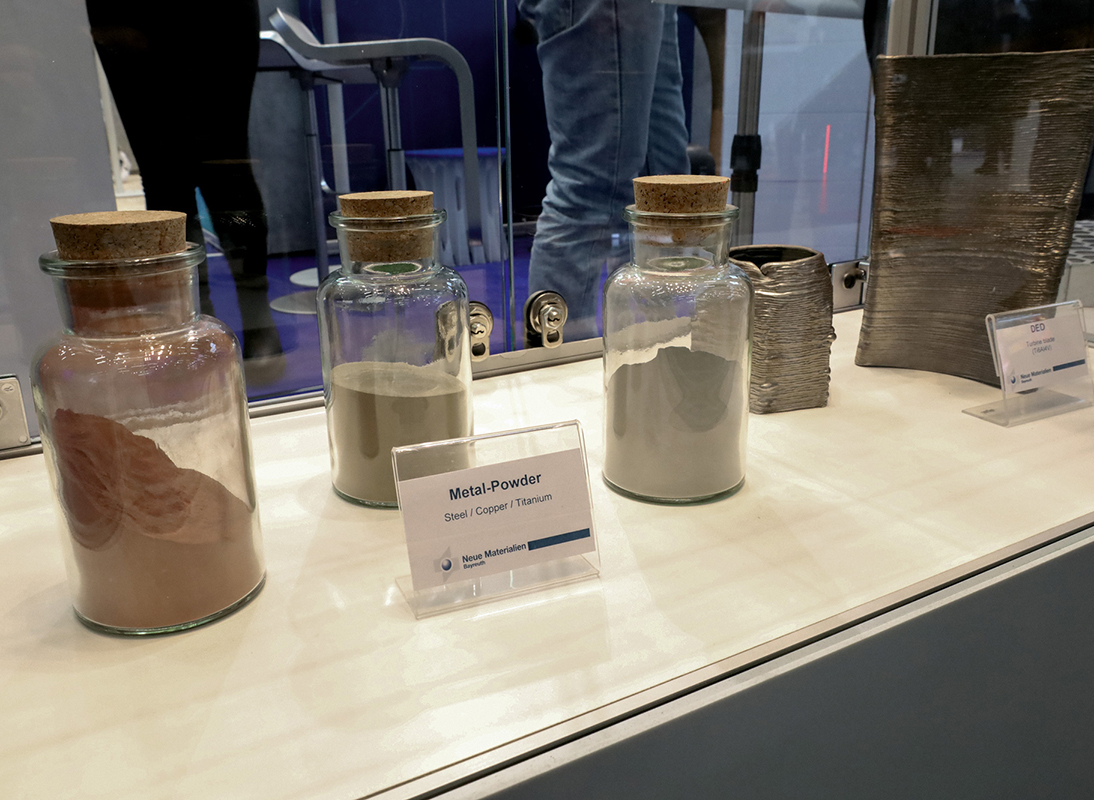
Auf der Formnext präsentierte NMB nicht nur verschiedene Pulver …
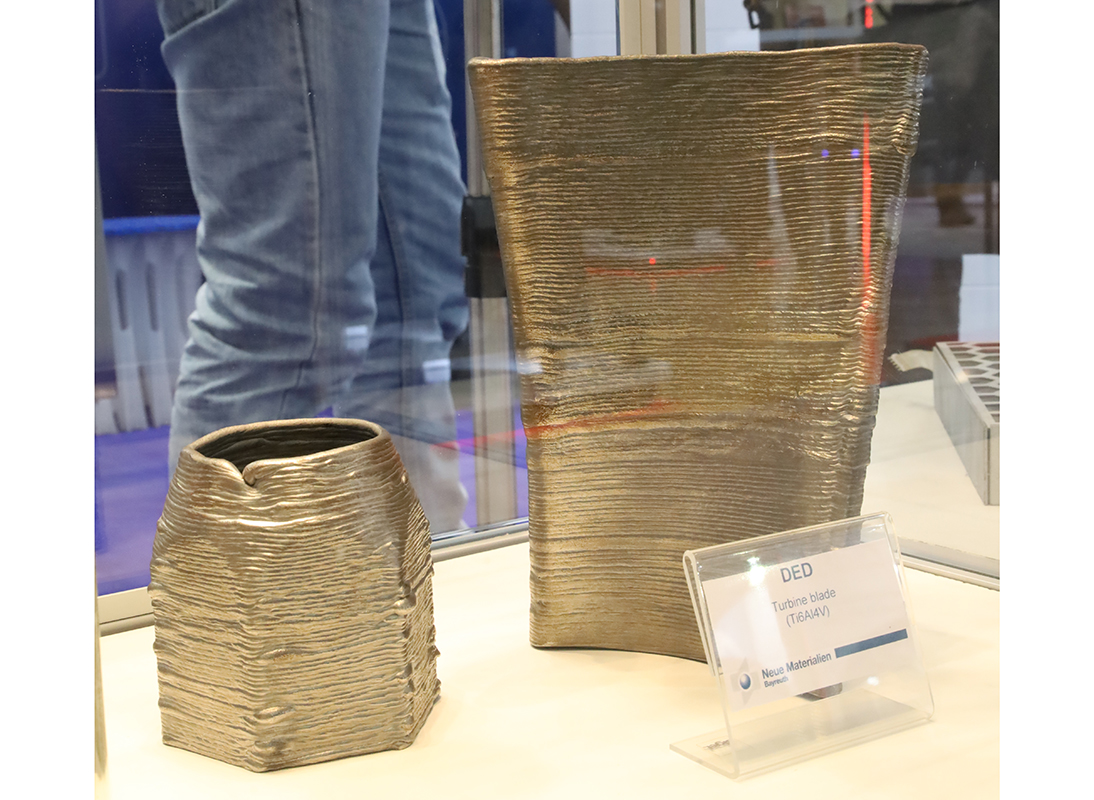
….sondern auch Anwendungen, wie ein im DED-Verfahren gedrucktes Turbinenblatt….
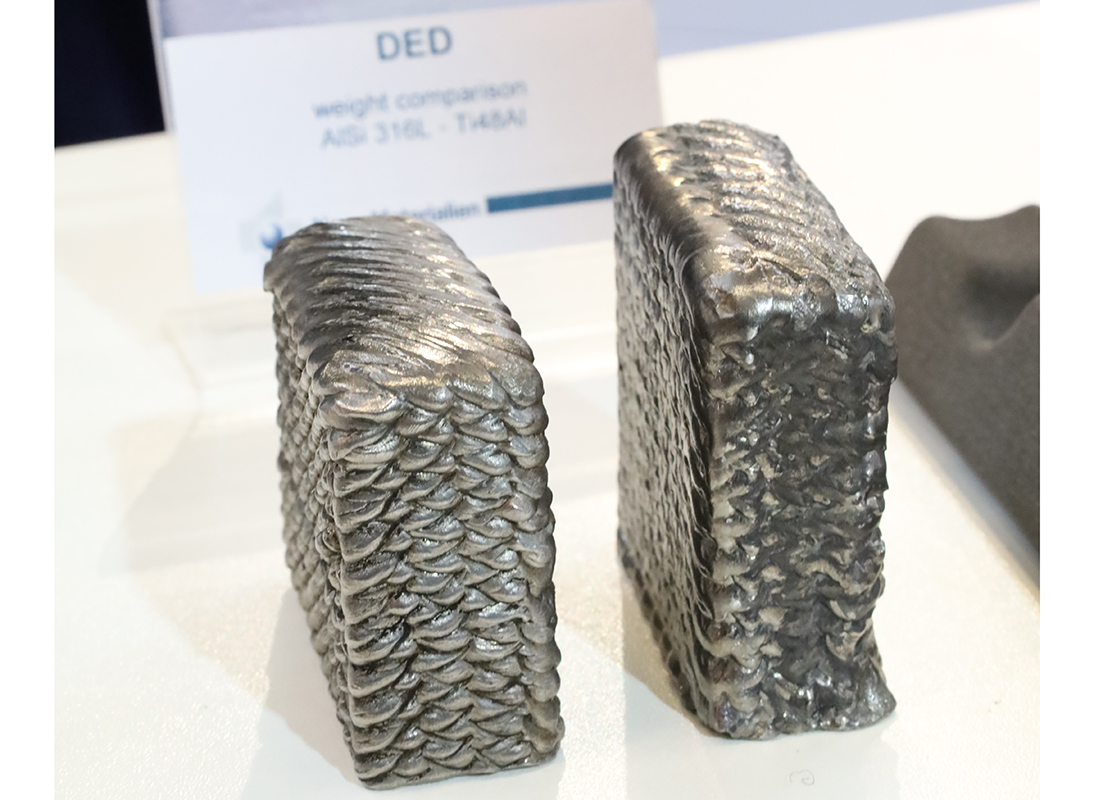
….oder einen Gewichtsvergleich von AlSi316L und Ti48Al. Fotos: Thomas Masuch
Zwar weiß Lemke, dass derzeit trotz großer Herausforderungen einige fortschrittliche LPBF-Materialien „in der Pipeline“ sind. Dass deren Zahl aber eher überschaubar ist und die Verwendung eher in kleineren Mengen stattfindet, liegt für Lemke an den langen Vorlaufzeiten und Testzyklen in der Materialentwicklung. „Die Entwicklungskosten sind oft zu hoch und die Kommerzialisierungszeiten zu lang.“ Mit Blick auf die meisten der derzeitigen Nischenmärkte, für die solche Materialien optimiert werden können, sei es kaum möglich, dabei rentabel zu sein.
„Da verwundert es nicht, dass Endanwender immer noch für die meisten LPBF-Anwendungen hauptsächlich herkömmliche Materialien verwenden. Erst wenn solche Anwendungen skalierbar erscheinen, werden die Legierungen evolutionär verbessert, um sie für LPBF zu optimieren.“ Laut Lemke findet man solche modifizierten Legierungen insbesondere bei Nickel- und Titan- sowie bei Aluminium- und Stahllegierungen.
Hoher Entwicklungsaufwand
Den hohen Aufwand für die Entwicklung von Sondermaterialien sieht Haneen Daoud in der Besonderheit der Additiven Fertigung metallischer Bauteile begründet: Zum einen liegen derartige Materialsysteme in der Regel nicht als Draht bzw. Pulver vor. Darüber hinaus führen schnelle Abkühlraten zur Rissbildung und somit zur Schädigung der Bauteile, was die realisierbare Baugröße additiv gefertigter Teile stark limitiert. Und um das Ganze noch komplexer zu machen, variieren die Eigenschaften von verdüsten Pulvern von Hersteller zu Hersteller stark. „Das macht mitunter eine aufwendige Anpassung der Prozessparameter nötig“, erklärt Daoud.
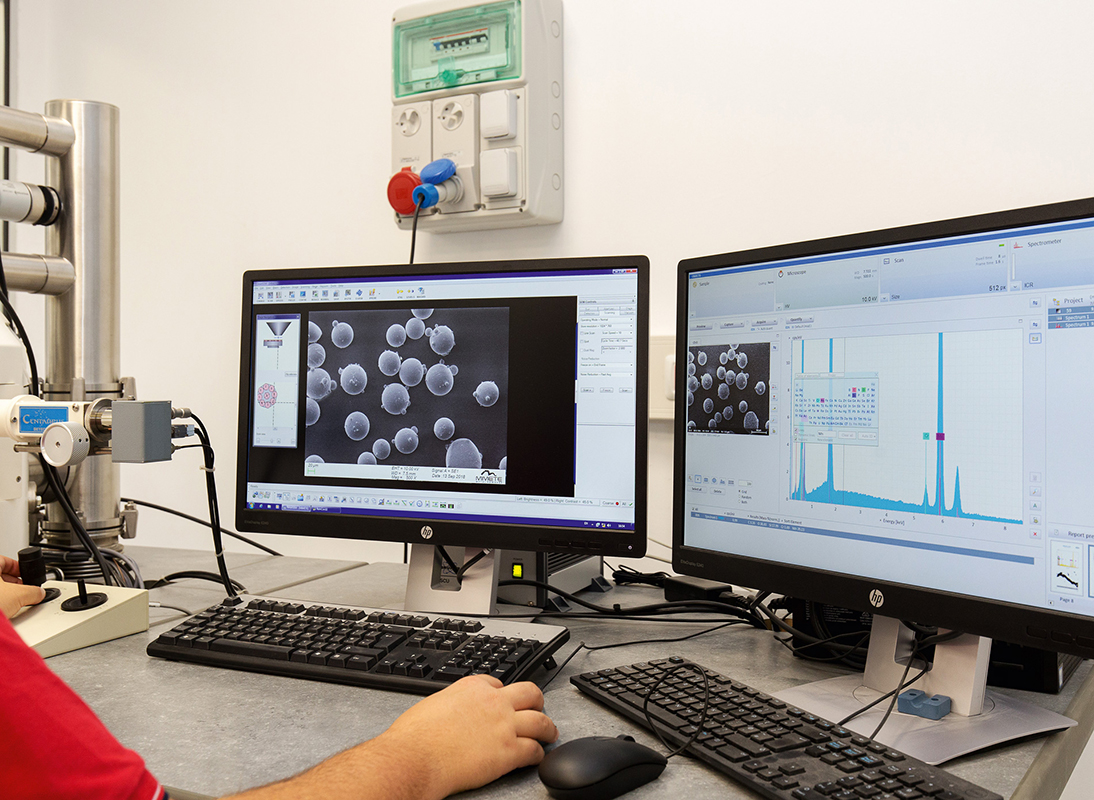
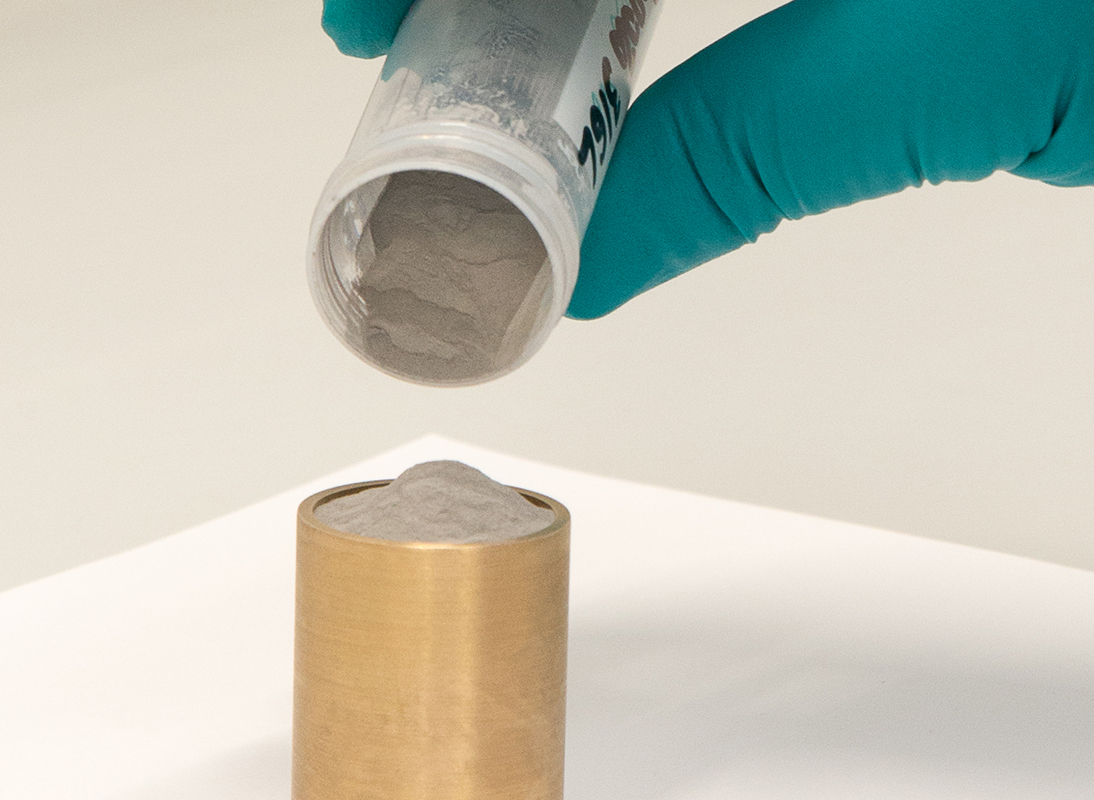
Materialentwicklung im Labor bei Mimete. Bild: Mimete
Verschiedene Forschungsansätze
Wenn bei NMB neue Materialien erforscht werden, geschieht das entweder im Rahmen von Doktorarbeiten oder von bilateralen Forschungsprojekten, die von einem oder mehreren Unternehmen finanziert werden. Grundsätzliche „größere Problemstellungen“ können auch öffentlich gefördert werden. Dabei übernimmt NMB die Materialentwicklung bis zur Kleinserienproduktion einschließlich einschlägiger Charakterisierungsmethoden. Die Aufträge der Unternehmen kommen sowohl von Anwendern als auch von Materialherstellern und Zulieferern.
„Bevor man ein neues Material entwickelt, muss man sich erst einmal verschiedene Fragen stellen“, so Geis. „Wie aufwendig ist das Projekt? Gibt es dafür eine Zahlungsbereitschaft im Markt? Und neben der Betrachtung der Wirtschaftlichkeit stellt sich in der Marktforschung auch immer mehr die Frage, wie ein neues Material im Life-Cycle-Assessment abschneidet.“ So ist es zum Beispiel energetisch und wirtschaftlich vorteilhaft, wenn die innerhalb eines Prozesses verwendeten Prozessgase durch entsprechende Anlagentechnologie zurückgewonnen und aufbereitet werden können.
In den Forschungsprojekten am NMB, die auch den Kunststoffbereich umfassen, wird auch versucht, mit intelligenteren Prozessen zu einer schnelleren Lösung zu kommen. „Manchmal benötigen wir gar kein neues Material, sondern können auch durch Beschichtungen, Oberflächenveredelung oder Multimaterialdruck und Hybridmaterialien zum Ziel kommen.“ Und manchmal führt auch ein neuer Herstellungsprozess zu neuen Ergebnissen: So hat NMB zwei Reinmaterialien aus Draht im DED-Prozess zusammengeführt und so gezielt verbesserte Materialeigenschaften für spezifische Anwendungsfälle erzielt – ohne den Einsatz angepasster Rohmaterialien. „In der Chemie ist nichts unmöglich – man muss allerdings den ganzen Weg mitdenken, über die Verarbeitung bis zur Anwendung.
Definitionen
Sondermaterialien kombinieren verschiedene Eigenschaften wie zum Beispiel hart, duktil, nicht rostend und andere, um für ein bestimmtes Anforderungsprofil die optimale Lösung zu bieten. (Harald Lemke)
Sondermaterialien sind geeignet für Anforderungen oder Anwendungen, für die mit den verfügbaren Standardmaterialien keine Lösung vorhanden ist. (Nico Geis)
MEHR INFOS UNTER:
Tags
- Werkstoffe und Halbzeuge
- Additive Fertigung
- Forschung und Entwicklung