Text: Thomas Masuch, 18.02.2024
Eigentlich sollte die Marine-Industrie mit ihren geringen Stückzahlen eine gute Adresse für den 3D-Druck sein – doch die Entwicklung der Additiven Fertigung in diesem Bereich ging in den vergangenen Jahren nicht wirklich rasant voran. Inzwischen scheint AM auch auf dem Wasser angekommen zu sein: Es werden ganze Boote gedruckt, und die führenden Nationen haben für ihre Marine Projekte ins Leben gerufen, wie AM auf Schiffen installiert werden kann.
Bei der Deutschen Marine ist Kapitänleutnant Dr. Sascha Hartig als Koordinator 3D-Druck Marine für die Implementierung des 3D-Drucks zuständig. In gerade einmal sieben Monaten hat Hartig mit seinem Team 153 Use Cases gefunden, in der Regel kleine Kunststoffteile, deren 3D-Druck „hilft, die Einsatzbereitschaft eines Schiffes zu verbessern“. In der Regel werden dabei defekte Bauteile 3D-gedruckt und bleiben so lange im Einsatz, bis das Schiff den nächsten Versorgungshafen anläuft und hier die ursprünglichen Ersatzteile zur Verfügung stehen. Lob für die neue Technologie gab es bei der Deutschen Marine auch schon von höchster Stelle: „Mit der Einführung des 3D-Drucks beginnt für die Marine ein neues Zeitalter für die Verbesserung der Ersatzteillage und die spontane Reaktion bei Notinstandsetzungen“, urteilte der Inspekteur der Marine, Vizeadmiral Christian Kaack.
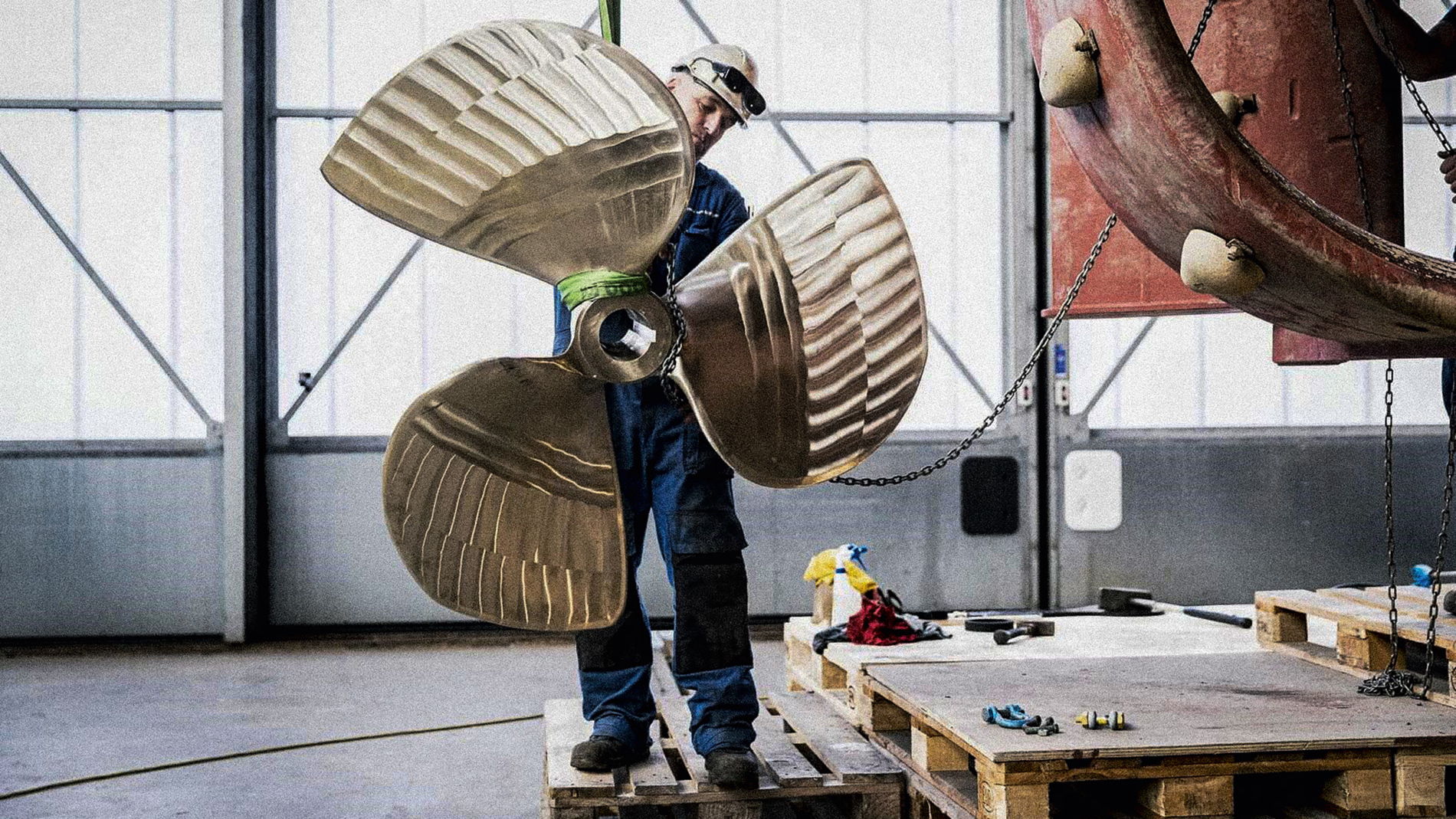
Montage des 3D-gedruckten WAAMpeller von Ramlab. Bild: Ramlab
Dabei hat die Deutsche Marine schon seit einigen Jahren vereinzelt Drucker an Bord, anfangs zu Forschungszwecken, inzwischen immer mehr für den realen Einsatz. Beispiele für reale Anwendungen sind Ventile für die Abwasseraufbereitung oder Halterungen für Elektronikkomponenten, die nach zehn Jahren nicht mehr beim Hersteller verfügbar sind, Seewasserfilter aus Nylon, die im Gegensatz zu den Stahlkomponenten nicht korrodieren, oder Interimsbauteile für das Feuerlöschsystem.
In einem weiteren Fall konnte ein Blindflansch für einen ausgebauten Wärmetauscher des Seewasserkühlsystems auf See gedruckt werden. Aufgrund eines defekten Ventils liefen jeden Tag 180 Liter Wasser ins Schiff, diese Leckage konnte durch die Nutzung der Technologie gestoppt werden.
Neben den Reparaturmöglichkeiten nutzt Hartig den 3D-Druck auch, um zum Beispiel Prototypen zu drucken und so die Additive Fertigung als Innovation Driver für das Militär zu nutzen. „Das bringt dann mitunter auch das Strahlen in die Augen der Soldaten.“ In Zukunft will Hartig die Nutzung von AM in der Marine noch deutlich weiter ausbauen. Ein Schlüssel dazu sind auch die Vernetzung und die internationale Entwicklung von Standards, sodass sich zum Beispiel bei internationalen Manövern Schiffe gegenseitig mit Interimsbauteilen aus dem 3D-Drucker versorgen können und nicht jedes Schiff das gesamte AM-Portfolio an Bord haben muss.
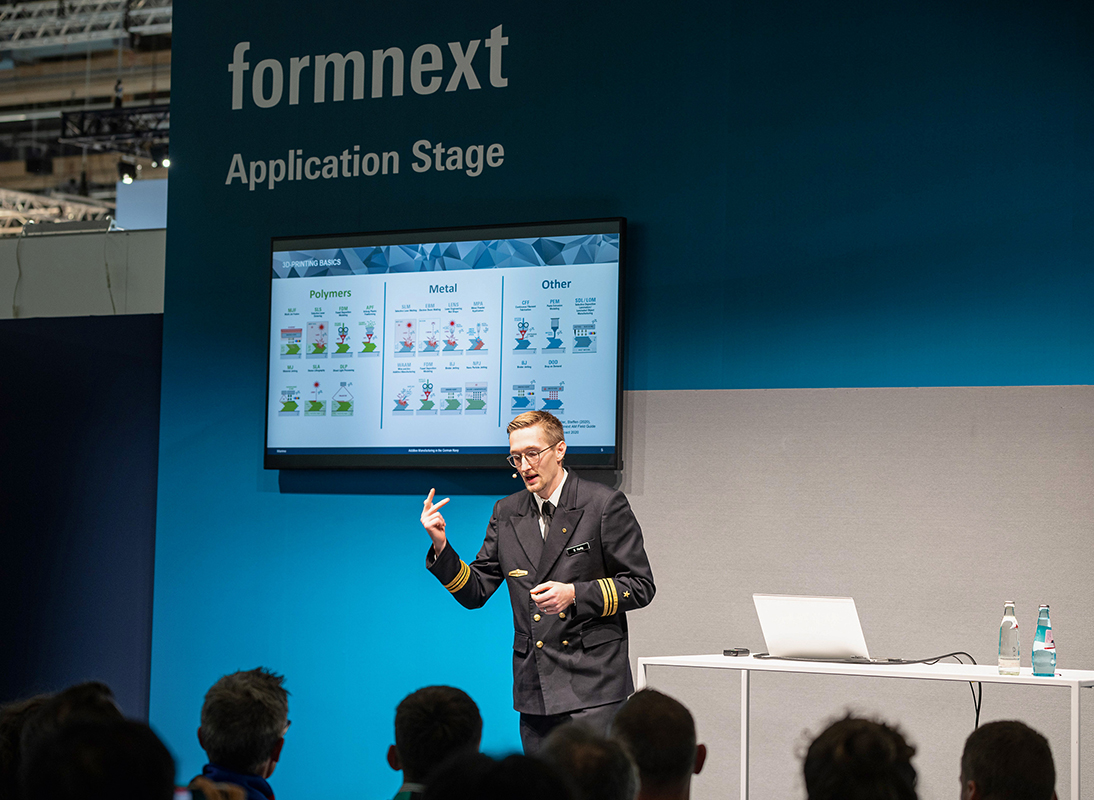
Kapitänleutnant Sascha Hartig stellte auch im Konferenzprogramm der Formnext 2023 die additive Entwicklung bei der Deutschen Marine vor. Bild: Mathias Kutt
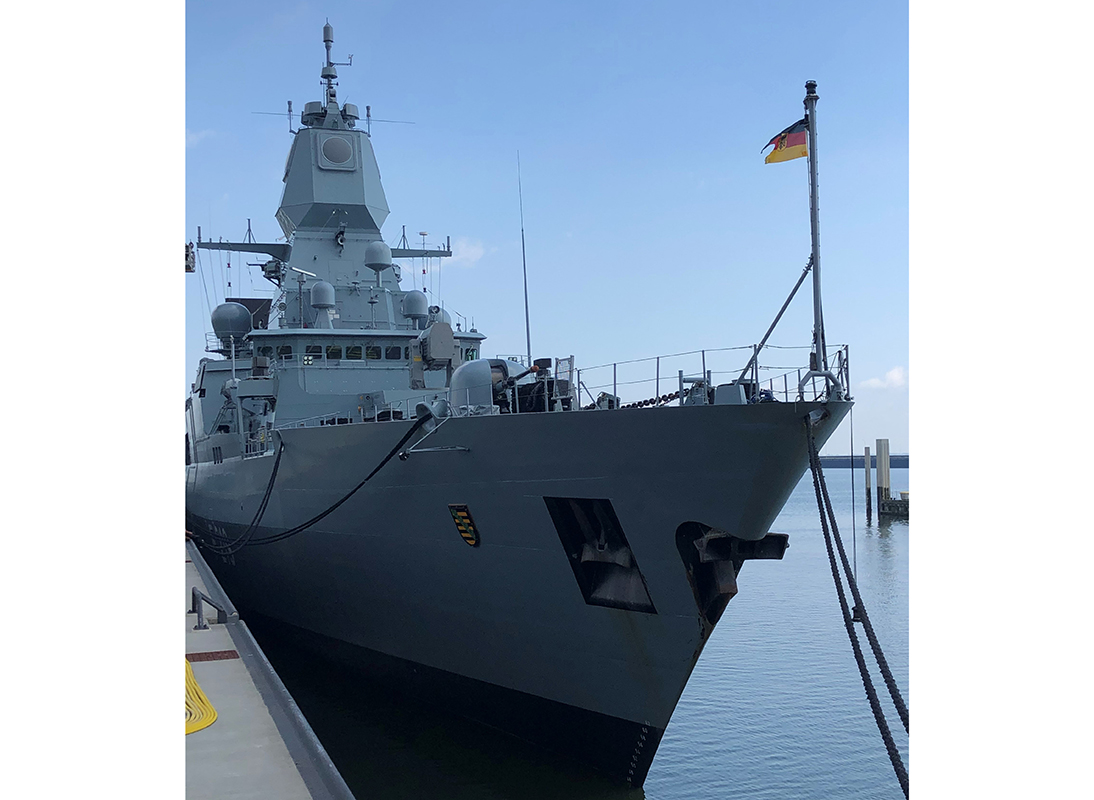
Auf der Fregatte Sachsen wurde der 3D-Druck getestet. Bild. Deutsche Marine
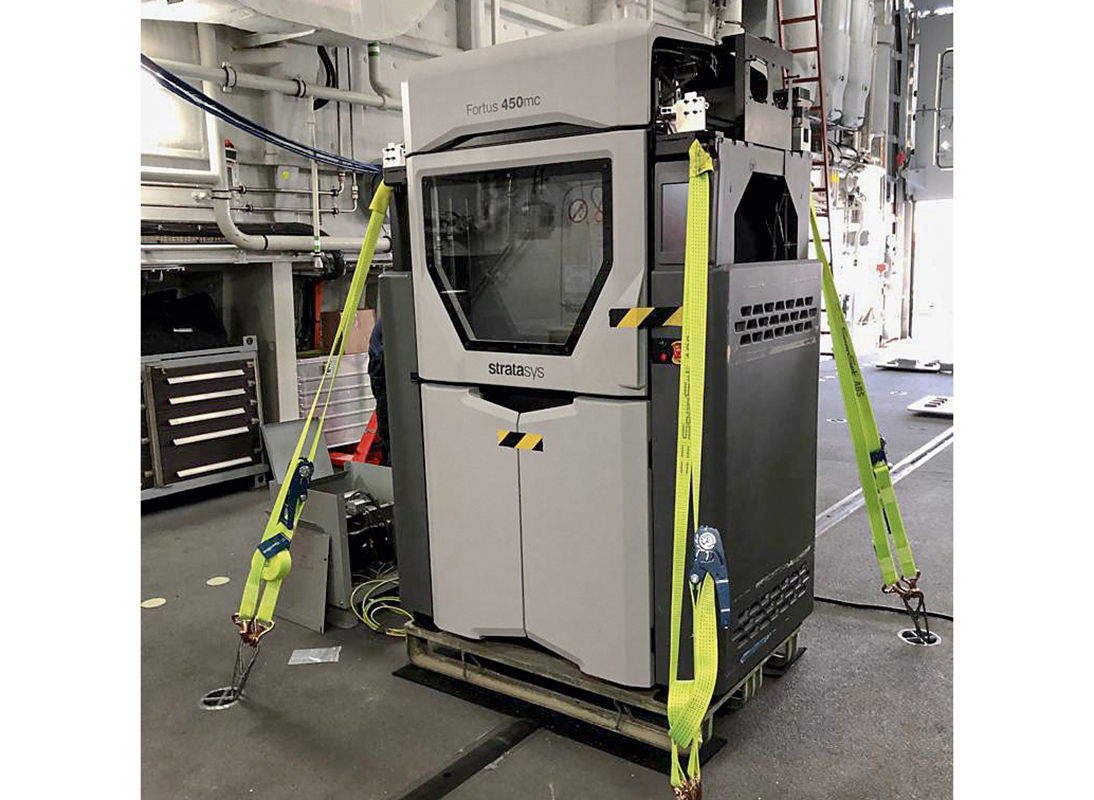
Installiert wurde unter anderem ein 3D-Drucker von Stratasys. Bild: Deutsche Marine
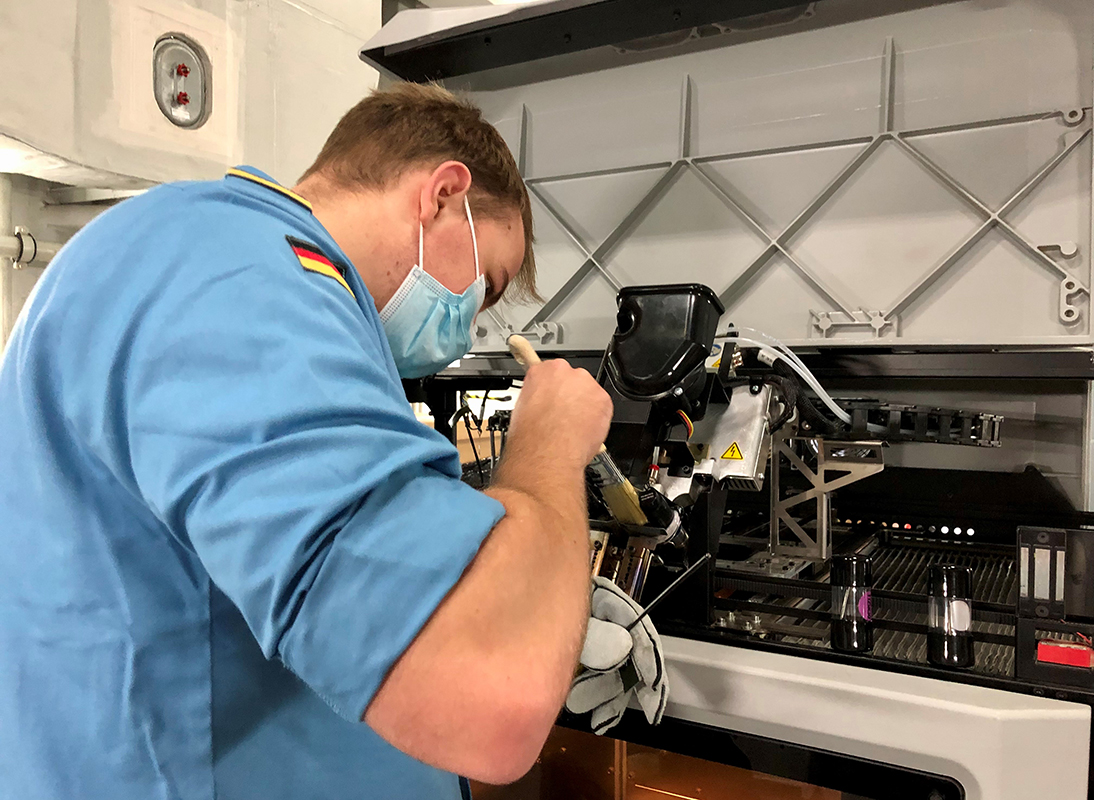
Aufgrund eines defekten Ventils liefen jeden Tag 180 Liter Wasser ins Schiff. Bild: Deutsche Marine
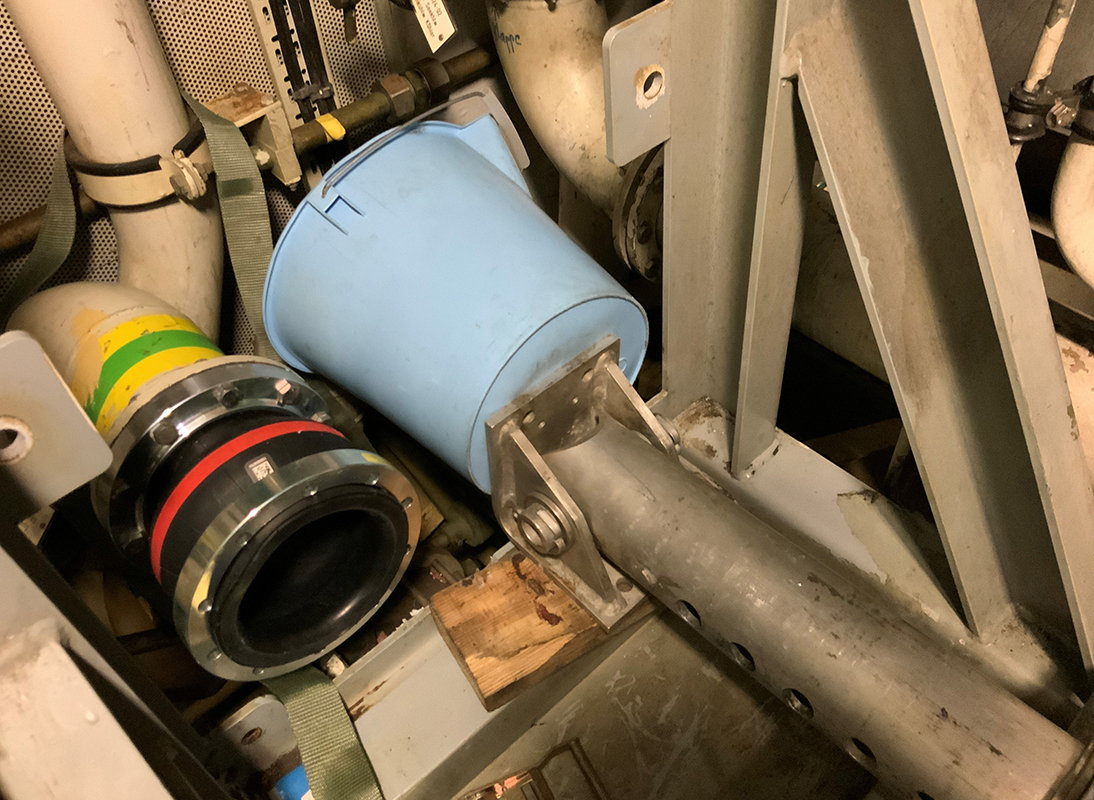
Die Leckage konnte durch die Nutzung des 3D-Drucks gestoppt werden. Bild: Deutsche Marine
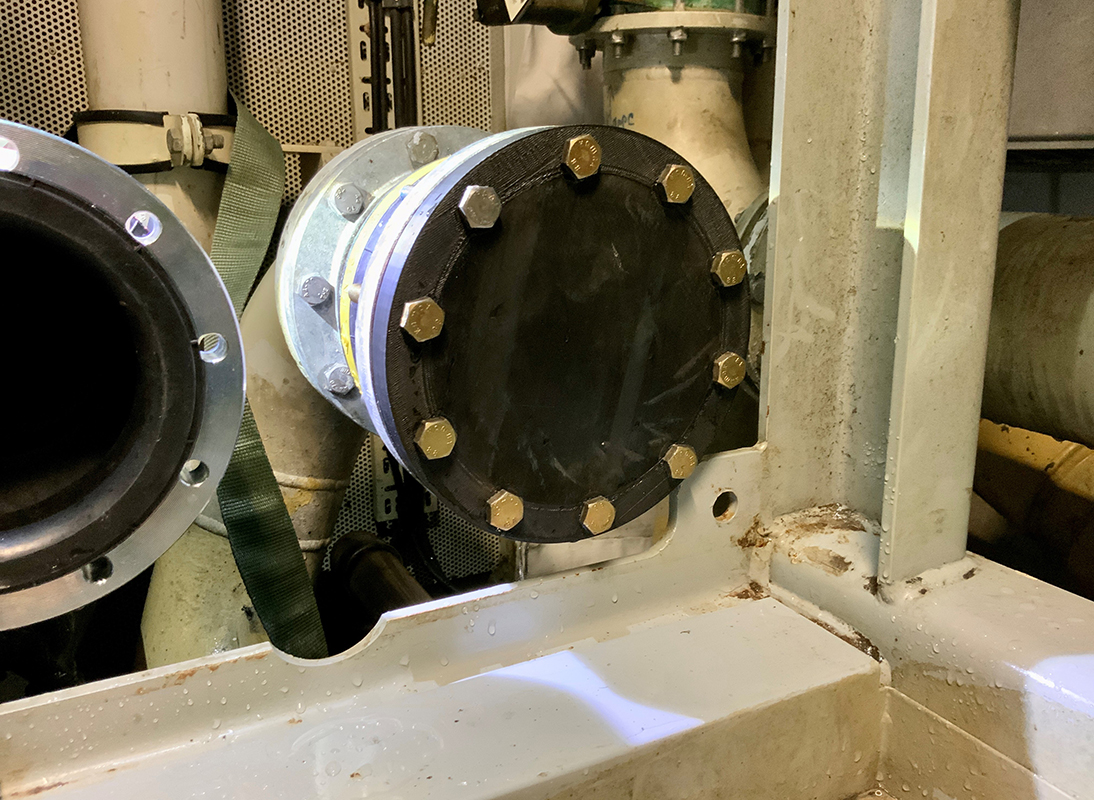
Die Leckage konnte durch die Nutzung des 3D-Drucks gestoppt werden. Bild: Deutsche Marine
Propeller und Unterwasser-Lebensräume
Das im Hafen von Rotterdam beheimatete Ramlab ist eines der Unternehmen mit der längsten AM-Erfahrung im Marine-Bereich. Das Unternehmen konzentriert sich auf das Wire Arc Additive Manufacturing (WAAM) und hat bereits 2017 den WAAMpeller 3D-gedruckt – „unser bekanntestes Schiffbauteil“, wie CEO Vincent Wegener erklärt. Der erste 3D-gedruckte und zertifizierte Propeller der Welt mit einem Gewicht von 220 Kilogramm und einem Durchmesser von 150 Zentimetern entstand in Zusammenarbeit mit Damen Shipyards, Promarin, Autodesk und Bureau Veritas. Seitdem hat Ramlab zusammen mit der Königlichen Niederländischen Marine und DNV am Druck eines Edelstahl-Impellers gearbeitet und war am 3D-Druck der ersten Hochdruckkomponenten für Vallourec in der Öl- und Gasindustrie beteiligt. Bei dem aktuellen Projekt geht es unter Wasser: Mit sechs MaxQ-Robotersystemen, die in einer sechseckigen Konfiguration angeordnet sind, entstehen die weltweit ersten 3D-gedruckten Unterwasser-Lebensräume für Menschen. Die Roboter fertigen dabei synchron die Rumpfsegmente, die mehr als 30 Tonnen wiegen und anschließend von DNV zertifiziert werden.
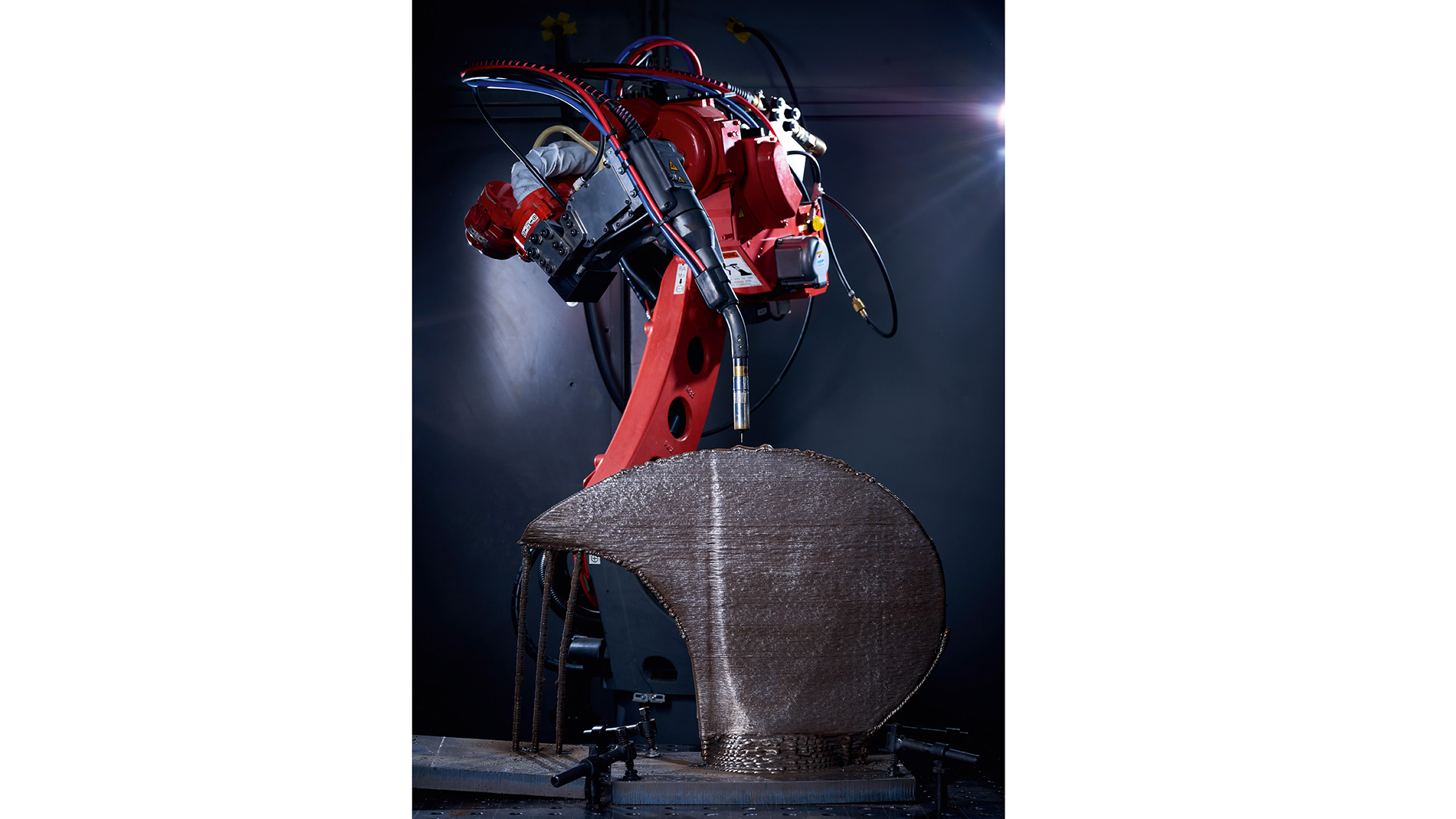
Auch international immer mehr Anwendungen
Inzwischen ist auch international die Additive Fertigung auf immer mehr Marine-Schiffen zu finden. So hat die indische Marine zusammen mit dem 3D-Druck-Dienstleister think3D ein Kreiselpumpen-Laufrad gedruckt. Die australische Marine hat sich einen WarpSpeed3D-3D-Metalldrucker angeschafft, um die Wartung von Patrouillenschiffen zu verbessern. Und auch auf Schiffen der U.S. Navy sind 3D-Drucker im Einsatz – so zum Beispiel seit Juli 2022 ein Markforged X7 Field Edition auf dem U-Boot USS New Hampshire. Gedruckt wurden unter anderem Ersatz für undichte Rohrleitungen und Elektronik-Gehäuse. Ein Metalldrucker kam zudem erfolgreich auf der 257 Meter langen USS Bataan zum Einsatz. Auf einem Phillips Additive Hybrid wurde eine Düse eines Salzwasser-Auslassventils 3D-gedruckt und nachbearbeitet.
Daneben spielt die Additive Fertigung auch beim eigentlichen Schiffbau eine immer größere Rolle, auch wenn sich viele Projekte noch im Entwicklungsstadium befinden. So arbeitet die U.S. Navy beim Bau von U-Booten u. a. mit dem australischen AM-Unternehmen AML3D zusammen, was unter anderem auch die Fertigung des Prototyps einer tonnenschweren Komponente im WAAM-Verfahren einschließt.
In der Kombination von qualitativ hochwertigen Teilen und einer deutlichen Verkürzung der Durchlaufzeit sieht Ramlab-CEO Wegener das größte Potenzial für WAAM im Marine-Bereich. „Das ist zum Beispiel der Grund, warum die U.S. Navy diese Technologie für ihre U-Boote aktiv verfolgt.“
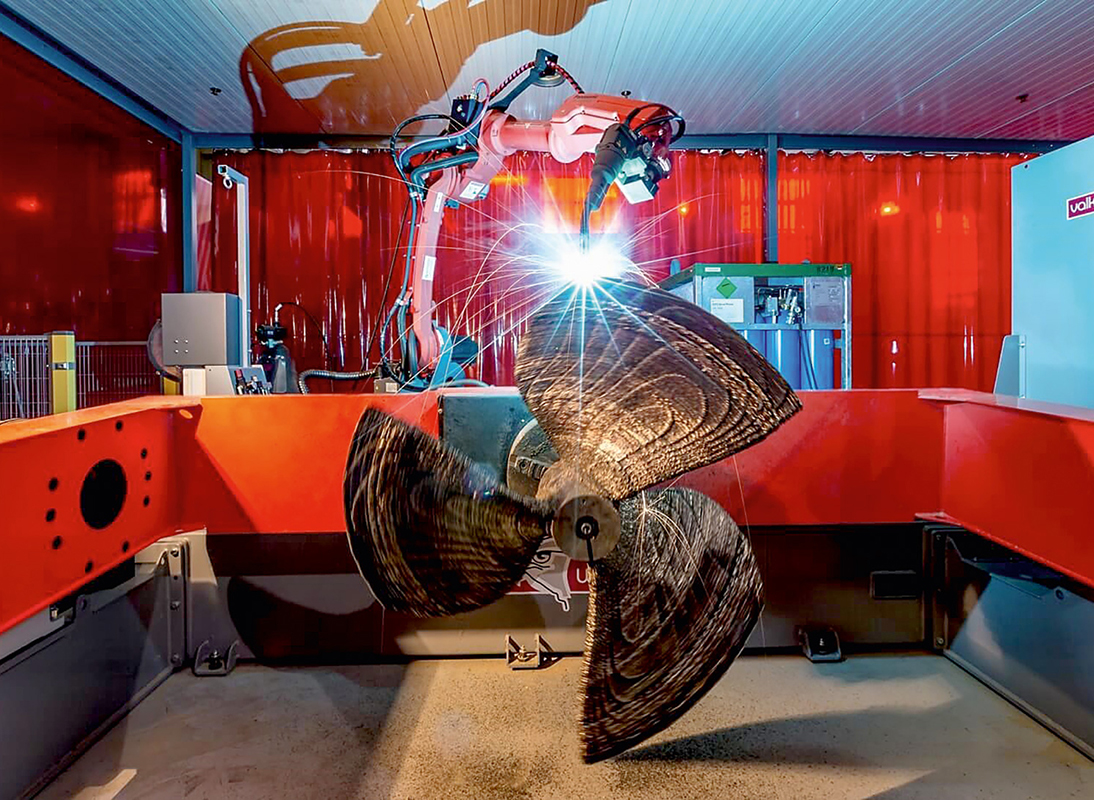
Produktion des WAAMpeller…
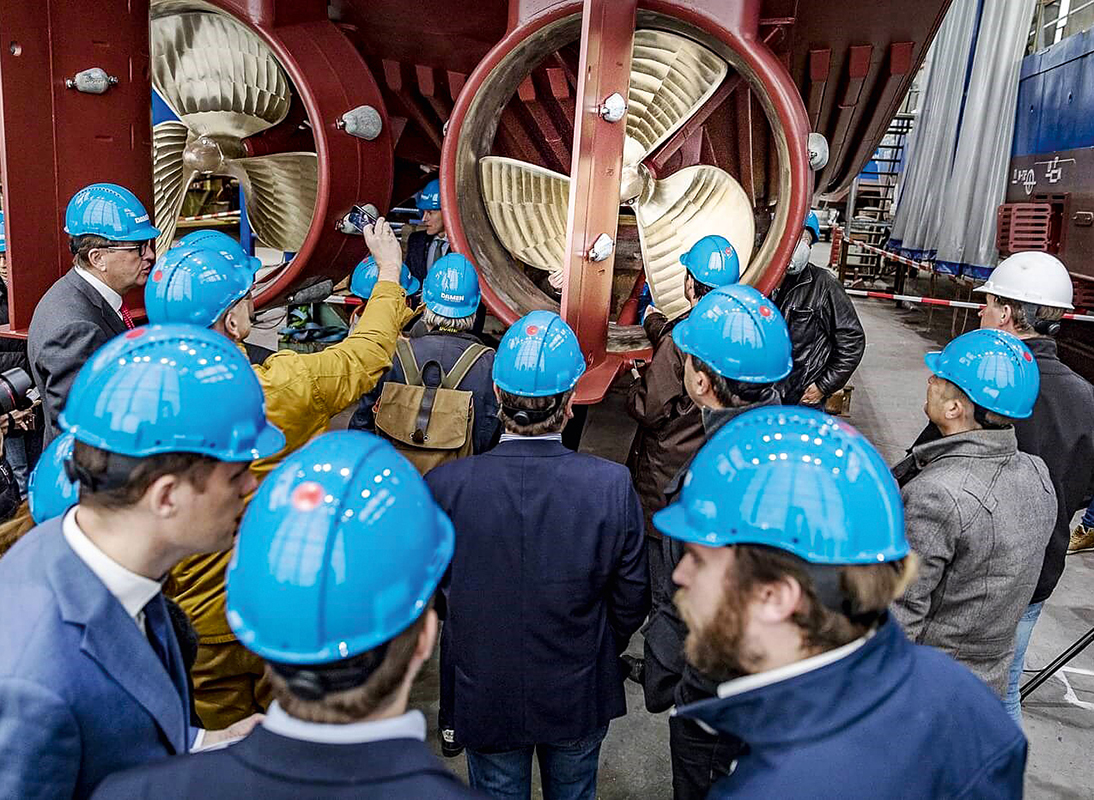
….und Event nach dem Einbau im Schiff. Fotos: Ramlab
Zertifizierung als Herausforderung
Dass die Aditive Fertigung in der Marine nicht noch weiter verbreitet ist, führt Kapitänleutnant Hartig darauf zurück, dass der Sektor ein eher konservativer Bereich des Maschinenbaus ist. „Auch sind die Bauteile im Bereich Metall meist sehr groß, und die Entwicklung der erforderlichen Maschinen hat erst in den letzten Jahren stattgefunden. Die Legierungen, die im Schiffbau verwendet werden, standen bzw. stehen nicht im Fokus der AM-Industrie.“ Darüber hinaus ist es oftmals ein großes Problem in der Marine, dass die Design-Daten Eigentum der Werften und damit nicht verfügbar sind. Als weitere Hürde nennt Hartig das nötige personelle Know-how einschließlich Design, Bedienung der Drucker und Nachbearbeitung. „Dies ist bei den vorhandenen Ressourcen sehr schwer zu ermöglichen.“ Dennoch waren Hartigs Experimente bei der Deutschen Marine erfolgreich, „weil wir zusätzliche Ressourcen in Form von Personal und Material an Bord gebracht und so die Besatzung nicht eingeschränkt haben“.
Auch Vincent Wegener sieht die größte Herausforderung für die weitere Entwicklung des 3D-Drucks im Marine-Bereich im Prozess der Zertifizierung von gedruckten Teilen. „Nicht nur die Unternehmen, die mit WAAM beginnen, müssen einen Lernprozess durchlaufen, um Teile zu drucken und zu zertifizieren, sondern auch die Zertifizierungsstellen mussten und müssen diesen Prozess durchlaufen.“ Laut Wegener nimmt das Wissen über den Prozess und die Akzeptanz von WAAM als alternativer Fertigungstechnologie stetig zu. „Angetrieben von der Notwendigkeit geht die Entwicklung in die gewünschte Richtung.“
MEHR INFOS UNTER:
Tags
- Offshore und Marine