“For sure, the parts that we use in our underwater vehicles have to be strong and robust, and absolutely conform to design intent”, explains Jeremy Sitbon, Chief Robotics Engineer - Marine Robotics Systems at Ecosub Robotics. “3D Printing is preferred over injection moulding as we find the technology more versatile, and the design freedom allows us to innovate great parts. Also, our volumes are low with maybe 10 parts per month, so injection moulding would not be economical.”
The company sees enormous potential for its underwater vehicles, which can be used in the defense, oil and gas sectors, as well as in science for climate change research. That's why Ecosub Robotics also has a clear eye on the cost factor. “Price is key to making this advanced technology available to a wide user group”, says Nick Allen, Managing Director at 3DPrintuk, a 3D printing service provider that supplies Ecosub Robotics with additively manufactured components on a regular basis.
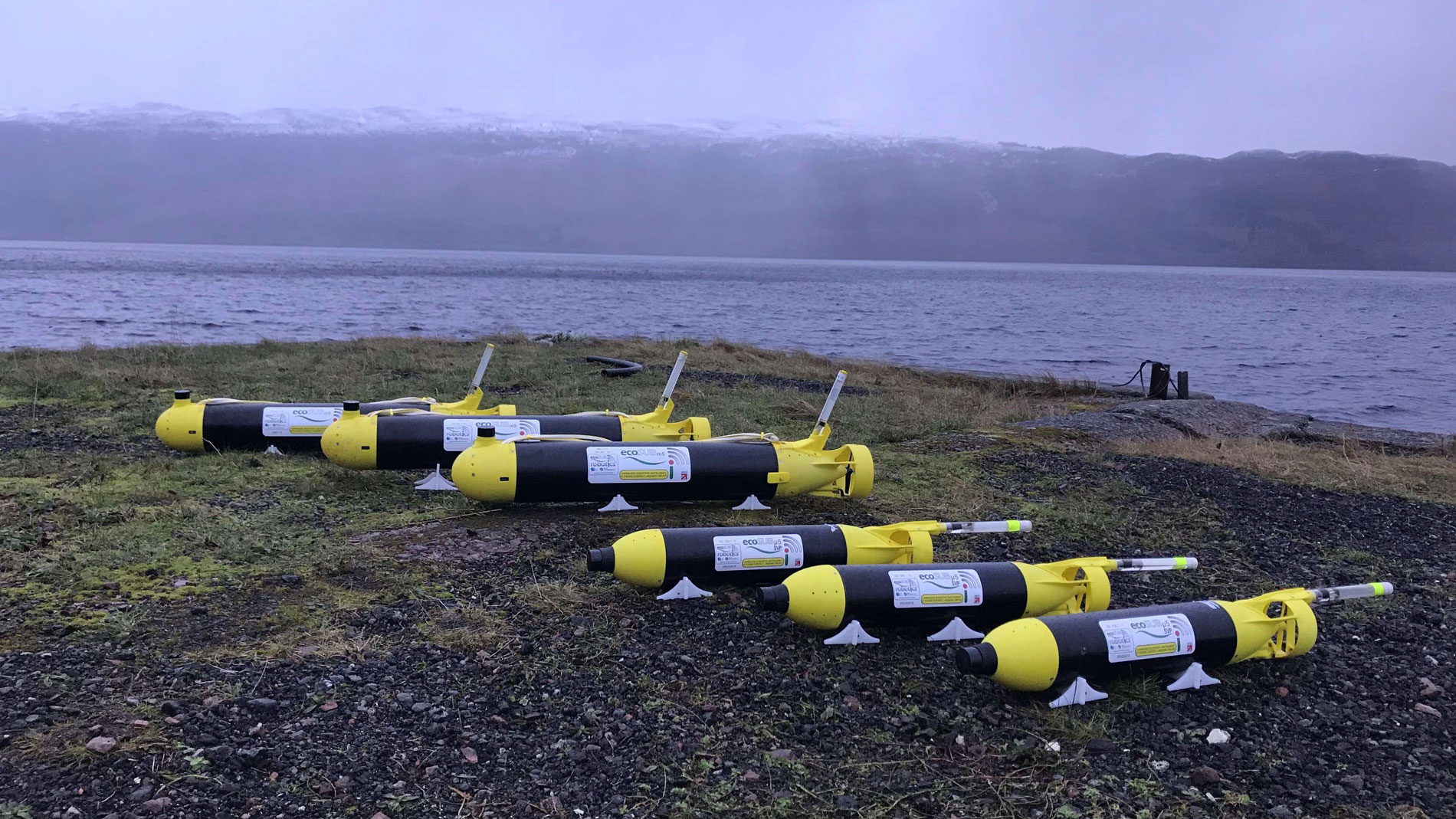
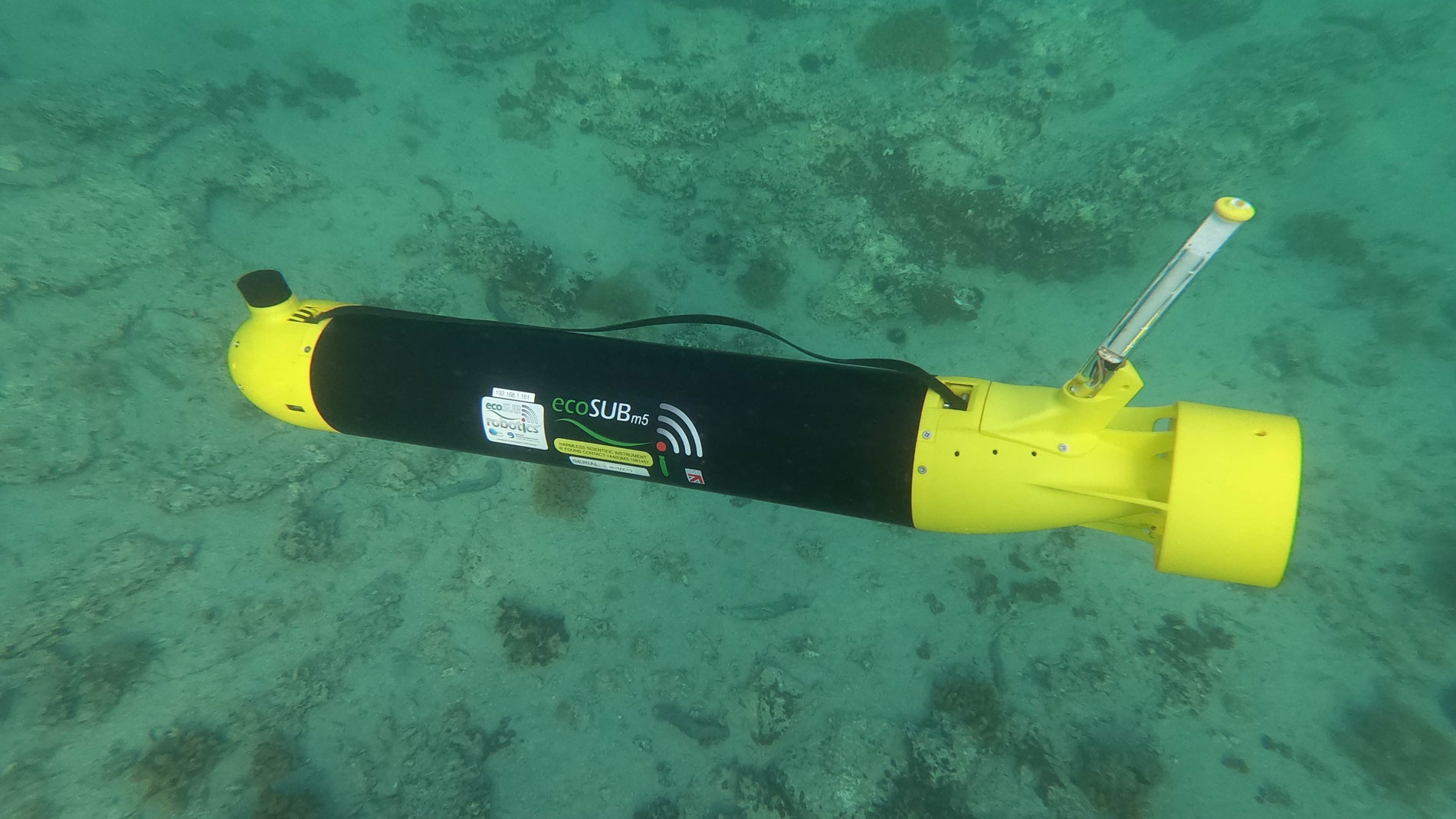
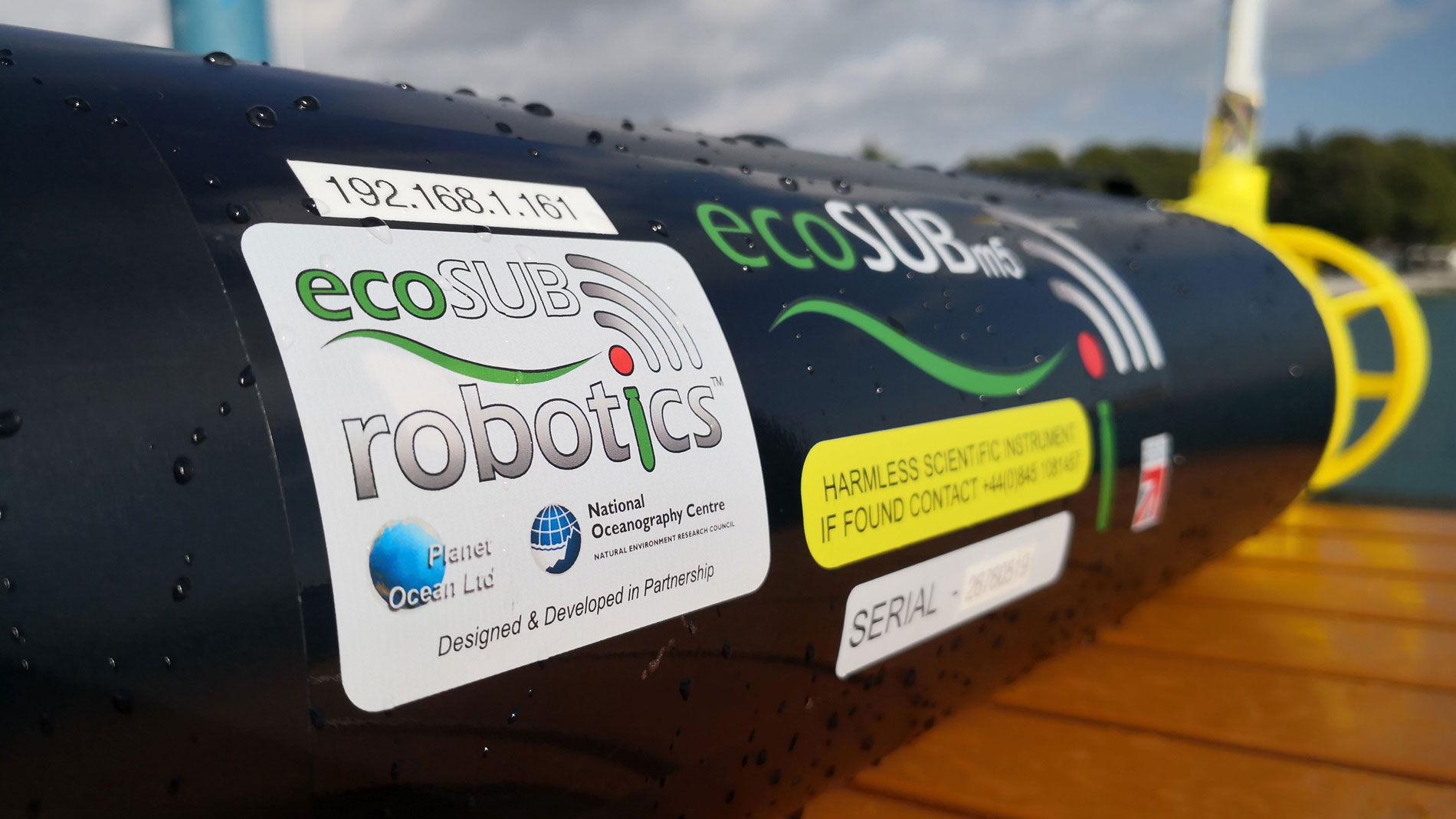
Both technologies offer advantages
Ecosub Robotics uses two different technologies for manufacturing: SLS and MJF. This also has to do with the different areas of application of the 3D-printed components. “There are two different kinds of parts and components in the vehicles, external parts that can be seen, and internal parts that cannot”, Sitbon explains.
The external parts need to be yellow for the sake of visibility, “and we use SLS for these as the technology produces whiter parts than MJF, and in our opinion this makes the addition of a colour that much more definite and striking.” MJF parts are somewhat greyer. For parts used internally, and which do not need to be coloured, Ecosub Robotics uses MJF parts as they are typically less expensive.
In general, Sitbon has identified advantages and disadvantages for both technologies and intends to continue assessing them. However, the company is more than satisfied with the results of both processes so far. “Because of the harsh environments that some of our vehicles are used in, integrity of material chosen is everything, and we are amazed by both processes which can withstand intense cold, high pressure, and the corrosive nature of salt water, and still pass rigorous water-tightness tests.”
FURTHER INFORMATION:
AM TECHNOLOGY:
Additive Manufacturing for Polymers
A structured overview of the complex and multi-layered world of Additive Manufacturing, process steps and fields of application can be found in our AM Field Guide.
Tags
- Additive Manufacturing
- Offshore and marine