Text: Thomas Masuch; Photos: GKN — 08 February 2020
The upheaval in the automotive industry is also posing serious challenges to suppliers. After all, vehicles with electric drive systems require significantly fewer components. This is why one of the world’s largest automotive suppliers, GKN Powder Metallurgy, is relying on Additive Manufacturing in an effort to expand its presence in other areas of industry, as well. In recently acquiring Forecast 3D, the group has even brought technology for plastics into the fold.
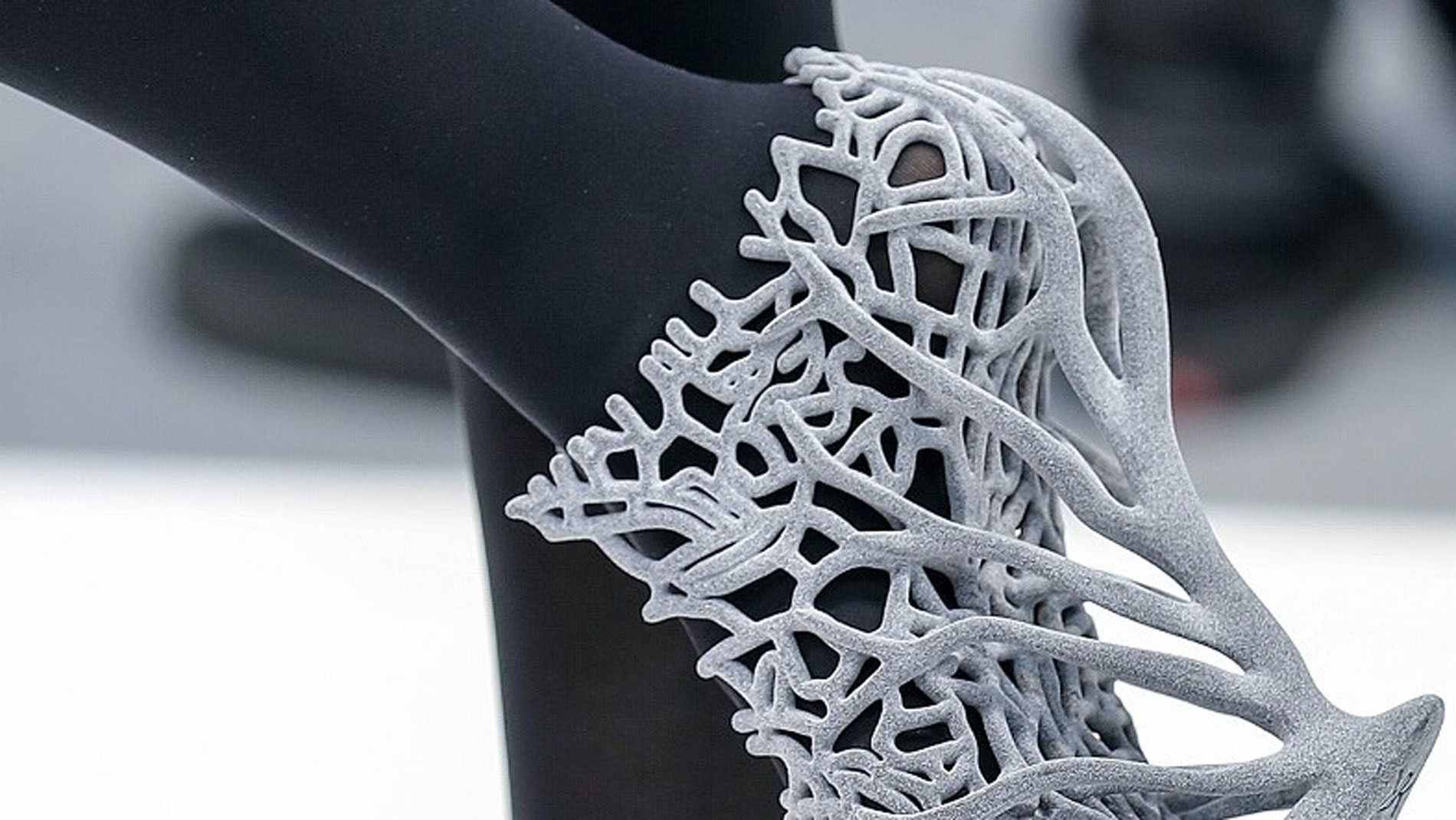
To respond to the changes taking place in the automotive industry, GKN already established a new division (GKN Additive) six years ago. According to Guido Degen, who leads the division as president of Additive Manufacturing, GKN has since made an »intensive investment in technology and development « in this field. This is expected to pay dividends quite soon, with Degen planning to have his division in the black starting in 2020.
Just how important Additive Manufacturing is to this international corporation is also evident in the fact that the GKN Additive division – whose current staff of 200 employees is relatively small – has the same formal status as divisions like GKN Hoeganaes (which produces around 300,000 tons of metal powder each year) and GKN Sinter (which manufactures 10 million metal components per day). Guido Degen is also a member of the executive team at GKN Powder Metallurgy.
For the AM president, the electrification of vehicles presents a tremendous challenge for a global automotive supplier like GKN. »Around 85% of the parts we make are for the automotive industry, and half of them go into the engine or transmission«, he reveals. »For Together with VW and HP, GKN has already presented the first serial 3D Printing. (right). Applications from other industries, such as fashion (left), were showcased by the company at Formnext 2019 vehicles with purely electric drive systems, there’s a huge drop in the number of components required.«
"Instead of having to take a greenfield approach and build new factories, we can establish AM plants at existing facilities."
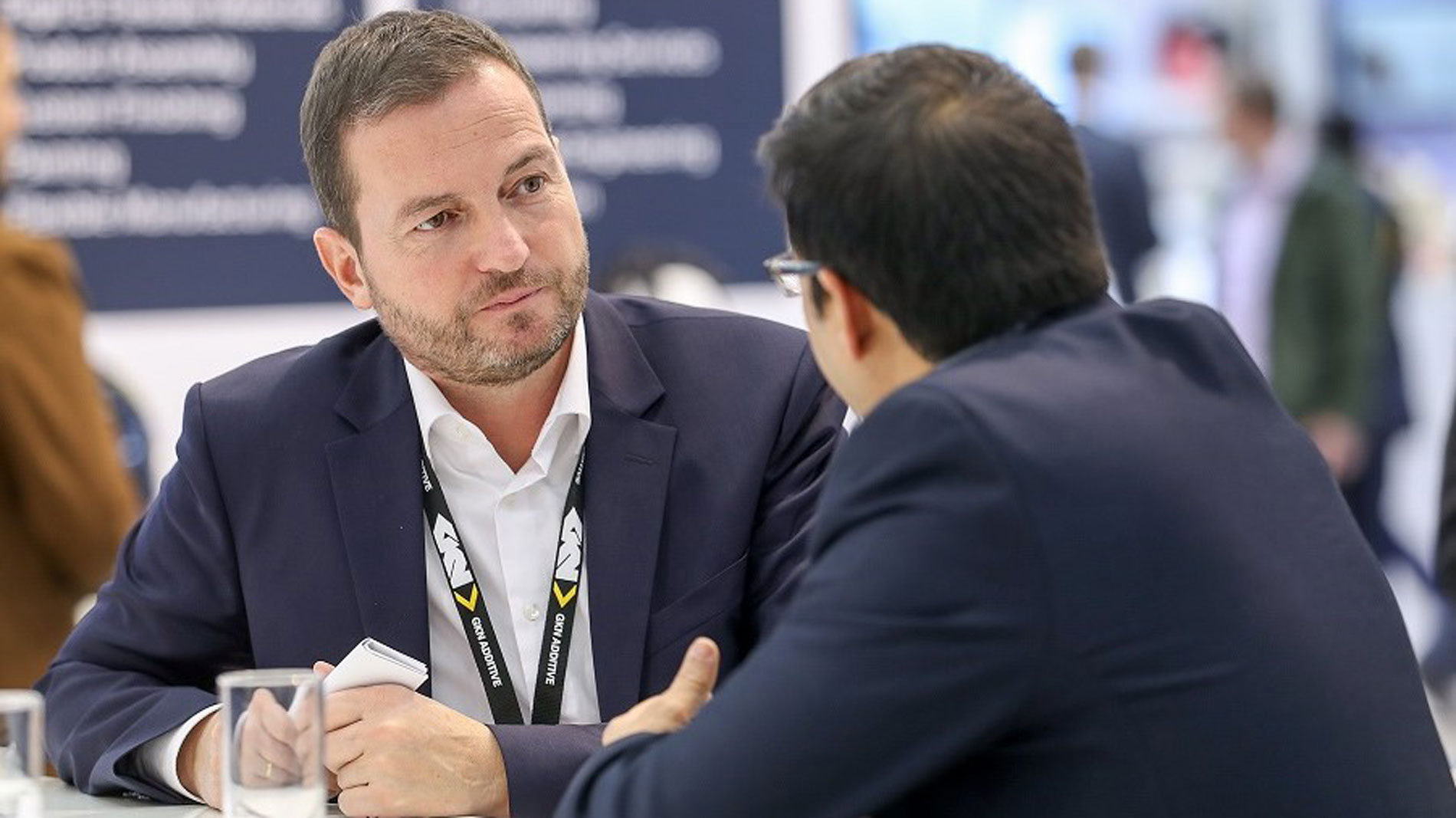
GKN took the plunge into the world of AM back in 2013. At its location in Radevormwald, Germany, the group spent the first four years developing qualified and secure processes for laser sintering. These processes are now used in production at GKN’s plant in nearby Bonn. There, GKN Additive produces prototypes and series comprising as many as a thousand components for numerous areas of industry. While some of them are for motorsport, the short-term demand for AM is »coming more and more from areas outside of automotive«, as Degen explains.
Diversifying across various user industries is a cornerstone of GKN’s strategy for the ongoing development of its AM division. »We’re not fixated on just the automobile industry«, Degen affirms. Indeed, GKN Additive has been tasked with applying the group’s knowledge to other sectors, especially when it comes to powder and sintering.
GKN’s established and certified production line in Bonn serves as a prototype for other AM production operations around the world. This is an area where GKN Additive benefits from its parent company’s global network. »Instead of having to take a greenfield approach and build new factories, we can establish AM plants at existing facilities«, Degen says. He goes on to describe how GKN’s production site in Bonn has already provided the template for three AM plants – in Detroit, Philadelphia, and Danyang (near Shanghai).
As the next step in its development, GKN Additive is planning to assemble an innovative additive production line in cooperation with BMW and other project partners. It will be based on laser sintering technology and offer outstanding cost efficiency thanks to digitalization and the way it largely automates production and post-processing. The first pilot lines are expected to commence operations at GKN (Bonn) and BMW (Munich) in 2021.
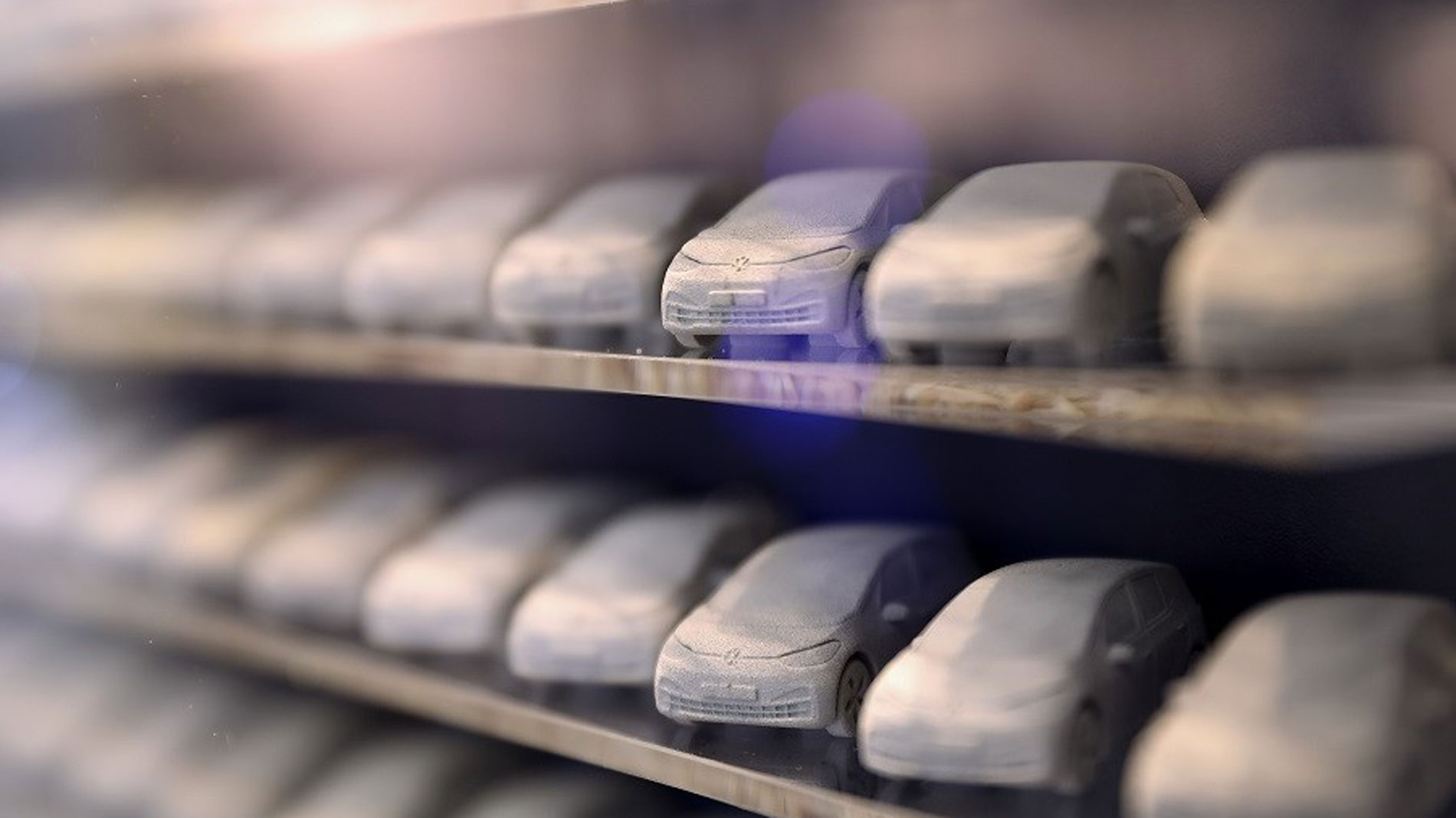
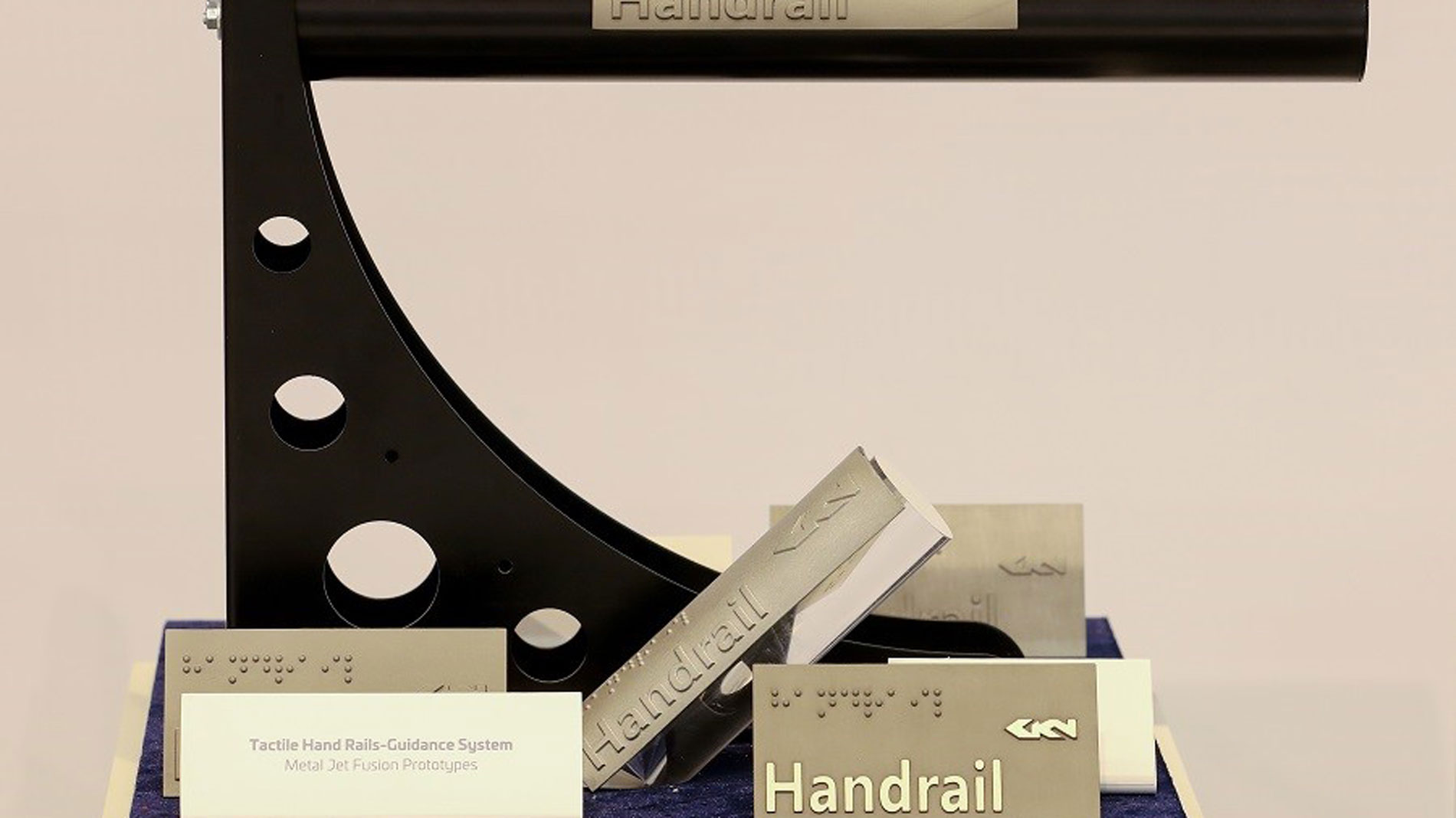
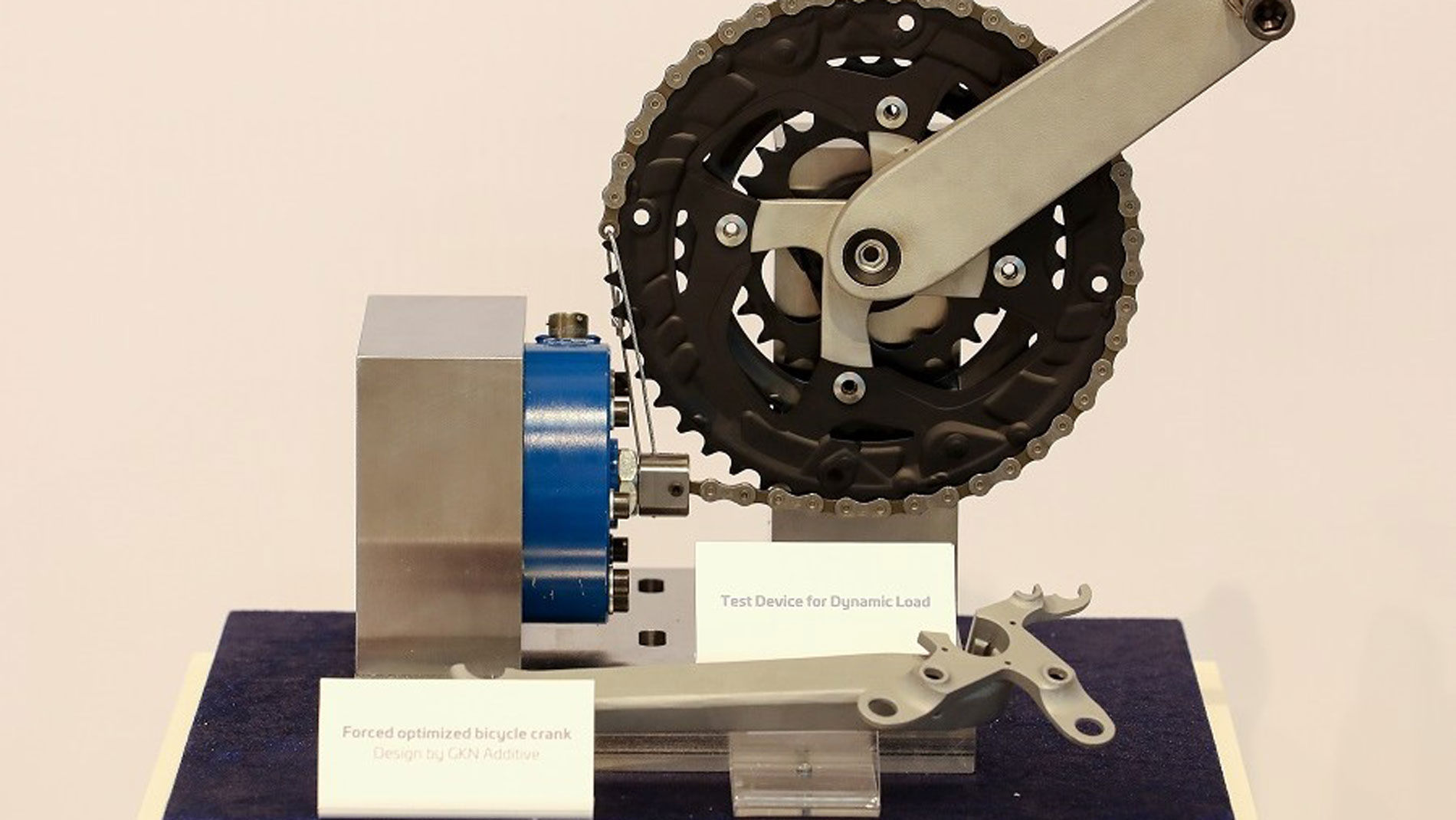
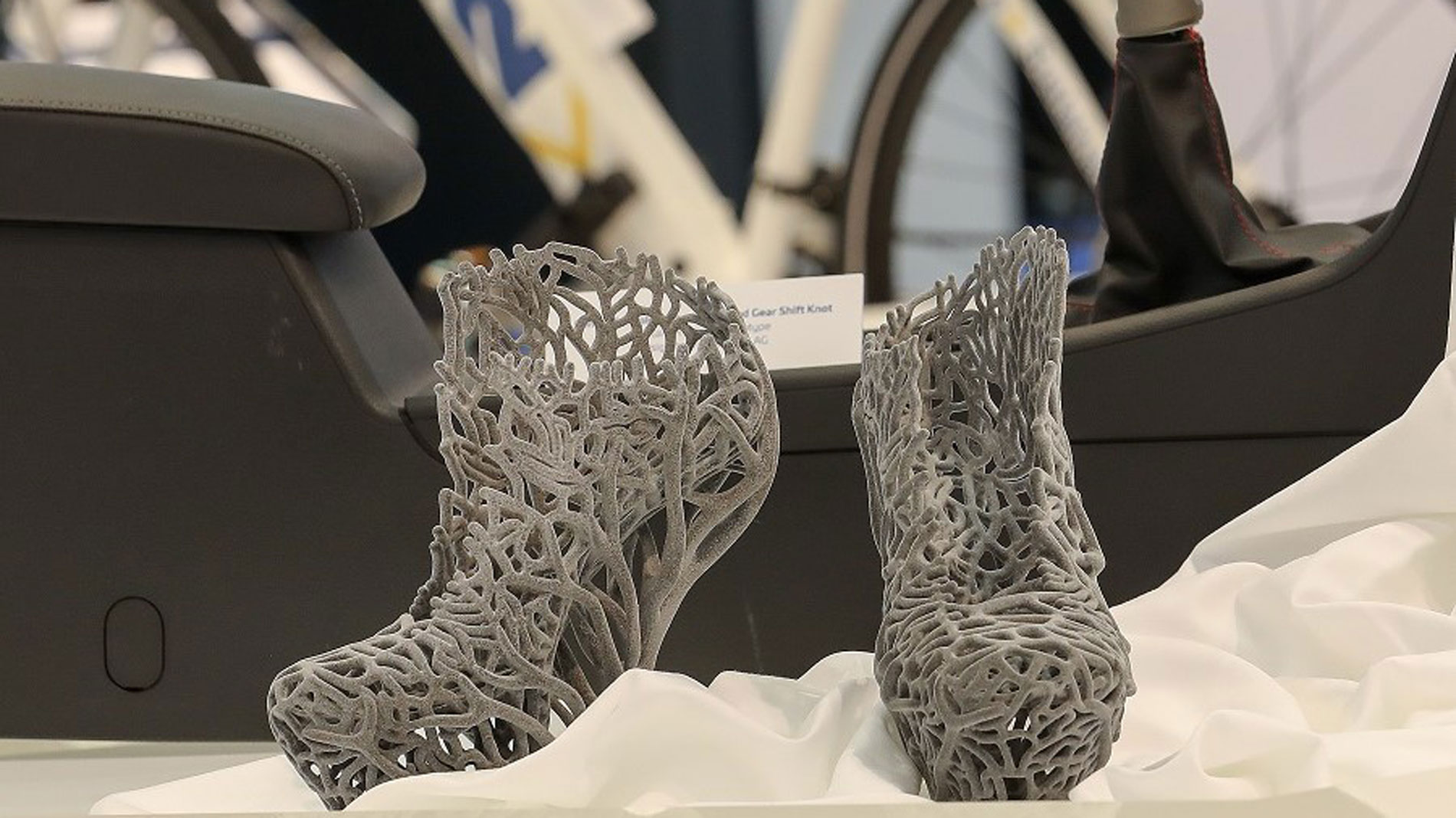
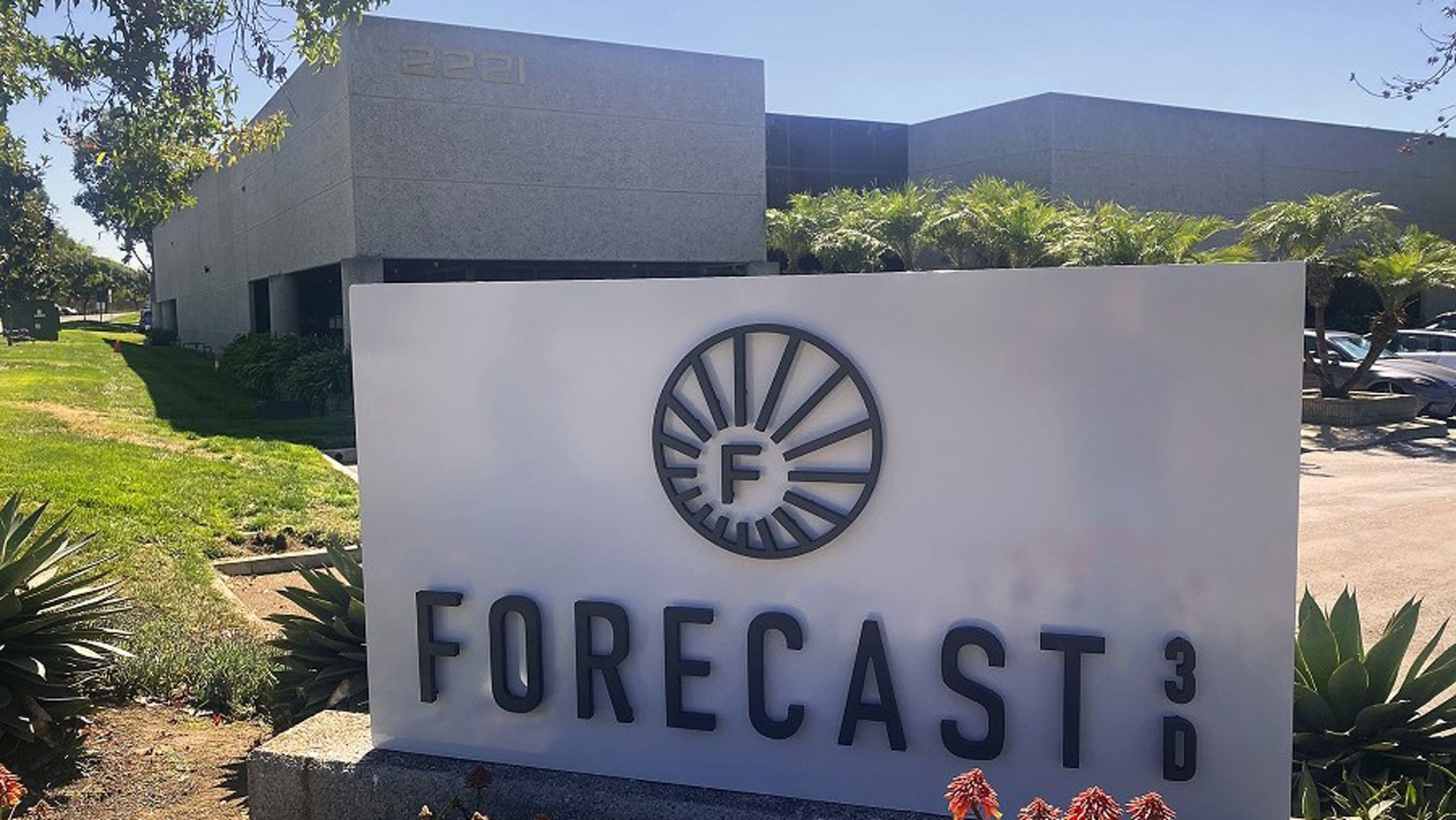
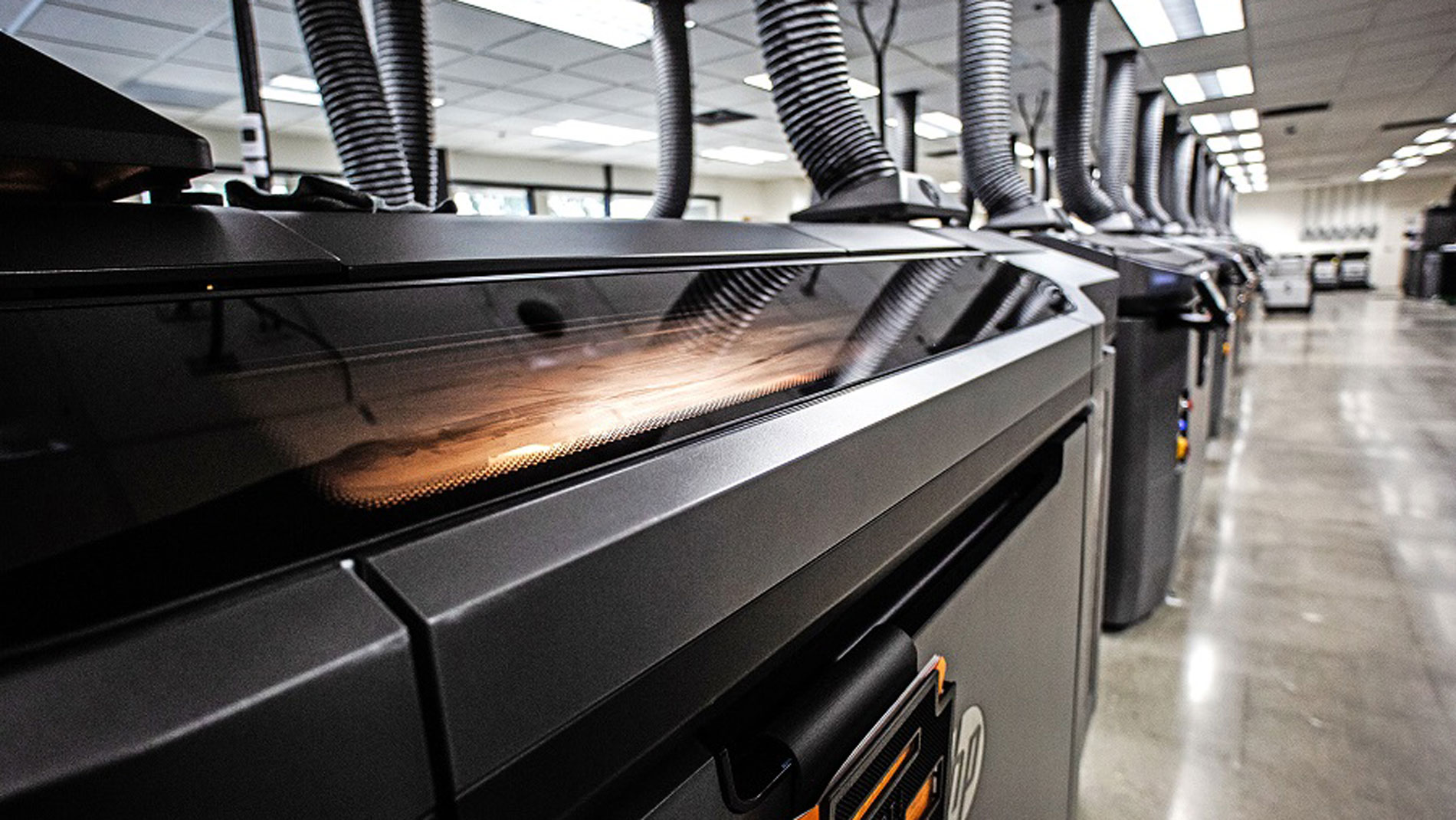
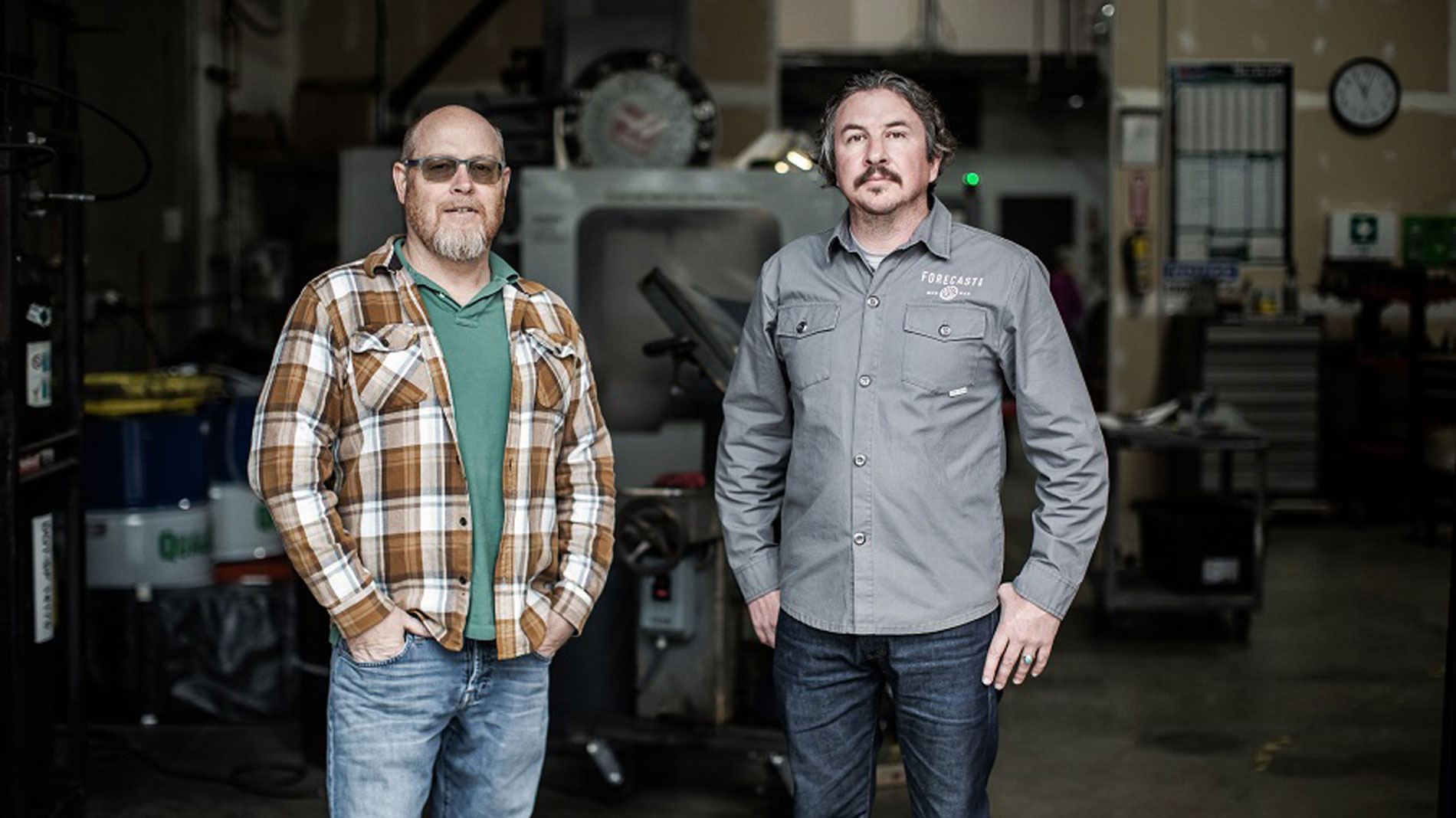
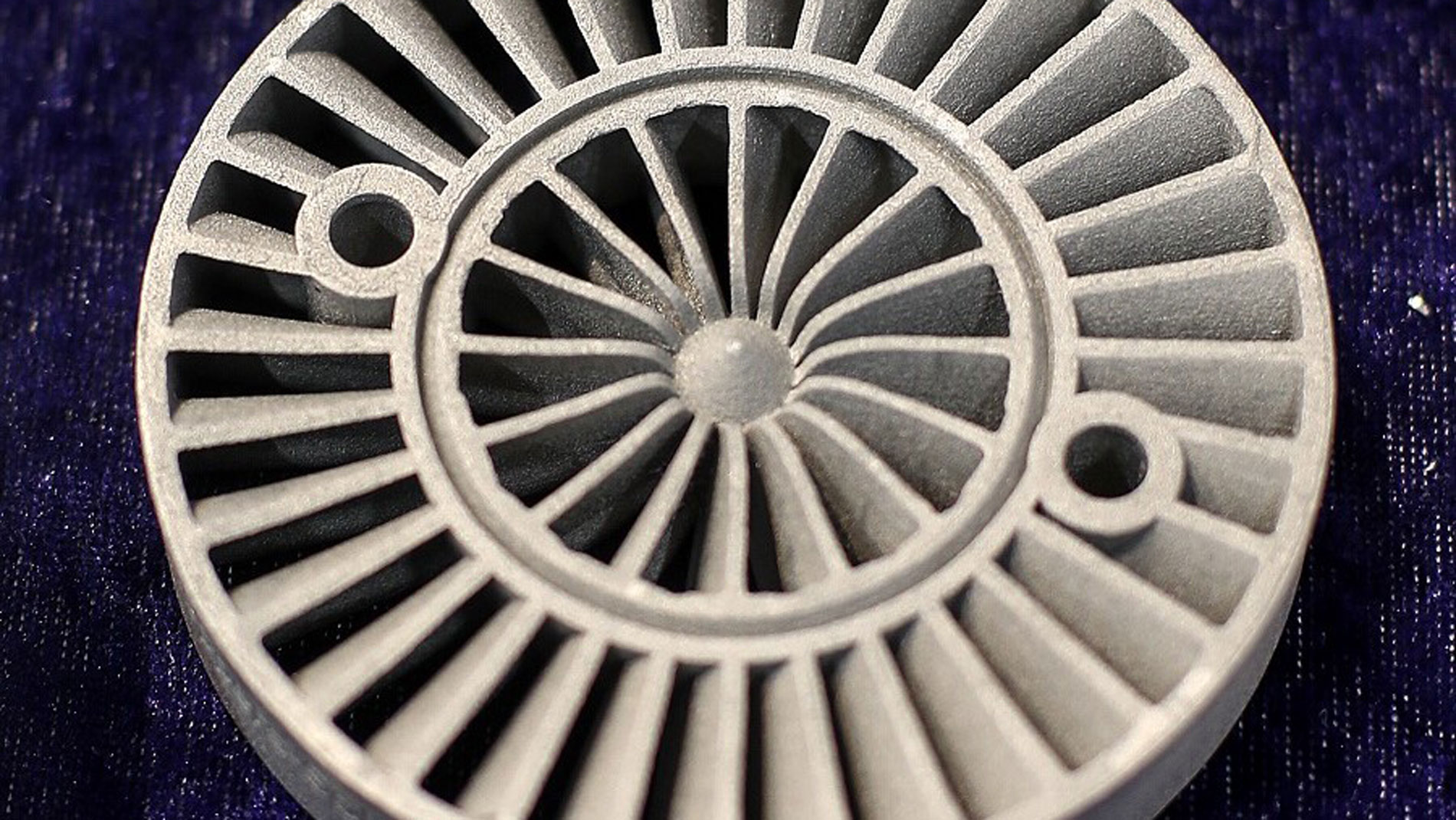
"Still not enough Applications"
For two years, Degen and a team of around 50 employees who work on metals within GKN Additive have been striving to find new applications for AM technology or develop them along with customers. »We’re well situated here, but unfortunately, there still aren’t enough specific applications«, Degen reports. He believes one of the most important reasons why has to do with the additive mindset, which has yet to reach a sufficient number of designers and engineers. Even though GKN has been shaped by AM as much as it has, Degen says only around 20% of its engineers take the technology into account as a solution process – and that figure is even quite a bit lower at other companies. »There’s still a lot that needs to be done. After all, Additive Manufacturing only makes sense when it offers added value«, he continues. »If we don’t optimize our components, all the efficiency gains in the world won’t make AM affordable enough when it comes to laser sintering.«
Degen nevertheless sees a large amount of potential in laser sintering, thanks in part to the automotive industry’s focus on electric drive systems. VW alone wants to bring 80 new electric models to market by 2025. Since the initial stages of this trend are requiring rather small quantities of designs that are often complex, Degen is predicting strong growth in the share of 3D-printed components. Furthermore, running on batteries generates a massive amount of heat that needs to be dissipated by intelligent heat management systems. »This will lead to a lot more copper and aluminum being built into vehicles«, Degen points out. These materials are highly compatible with powder bed production processes. Meanwhile, Degen thinks that many new applications of AM technology are on the way with respect to vehicle interiors and chassis.
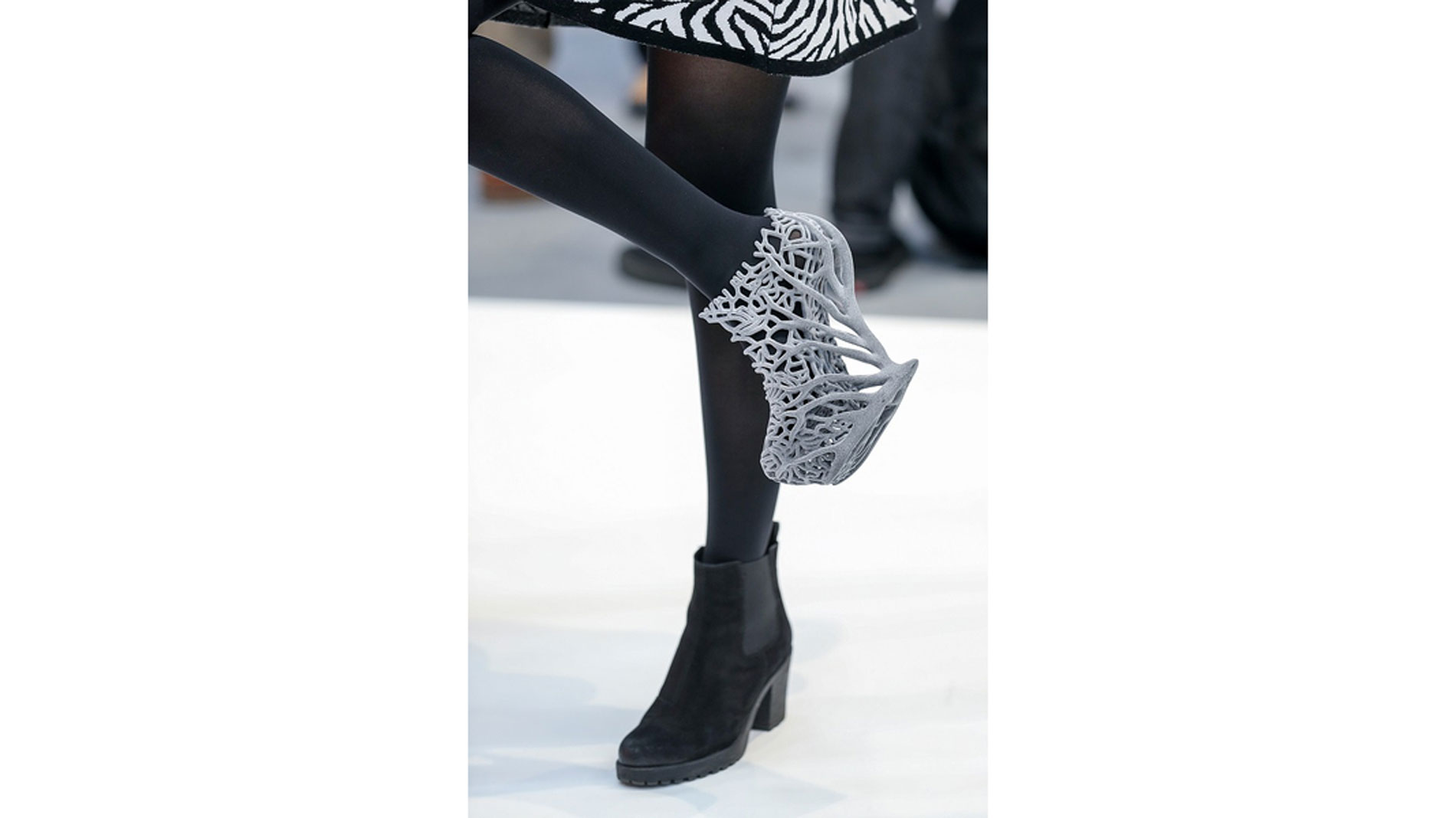
To tap into further additive potential, GKN has been developing binder jetting technology along with HP since 2018. Here, GKN is mainly contributing its expertise in powders and sintering. When HP begins marketing 3D printers equipped with this technology, its partner will not only gain access to an intriguing area of business for its specialized powders; it will already know a great deal about a technology capable of additive mass production, as well.
Acquiring Forecast 3D
In October 2019, GKN Additive took another significant step in expanding its business activities in AM in acquiring the service provider Forecast 3D. The Californian company has been 3D-printing plastics for 25 years, and the addition of its 150 employees quadrupled the division’s workforce in one fell swoop.
»The idea of an organization with our metal DNA buying up a company focused on plastics probably seems unusual at first glance, but it definitely makes strategic sense«, Degen says. For one thing, he points out, the move has enabled GKN Additive to tap into an extensive portfolio of customers that are mainly based on the west coast of the United States, which is presenting cross-selling opportunities in metals. »On top of that, we’ve secured new expertise in plastics that we’ll be gradually transferring to our other production sites around the world«, Degen adds.
FURTHER INFORMATION:
Tags
- Additive Manufacturing