By Thomas Masuch, 15 February 2024
With printers and special materials from the Fabrica Group, Nano Dimension wants to make all-new applications at the micro level possible – even beyond printed electronics. The Israeli company presented numerous components at Formnext, including tiny screws that can replace metal parts in the manufacture of smartphones, for example. »Until now, it was impossible to make such components from plastic,« explains Nir Sade, GM AM, SVP Product Champion.
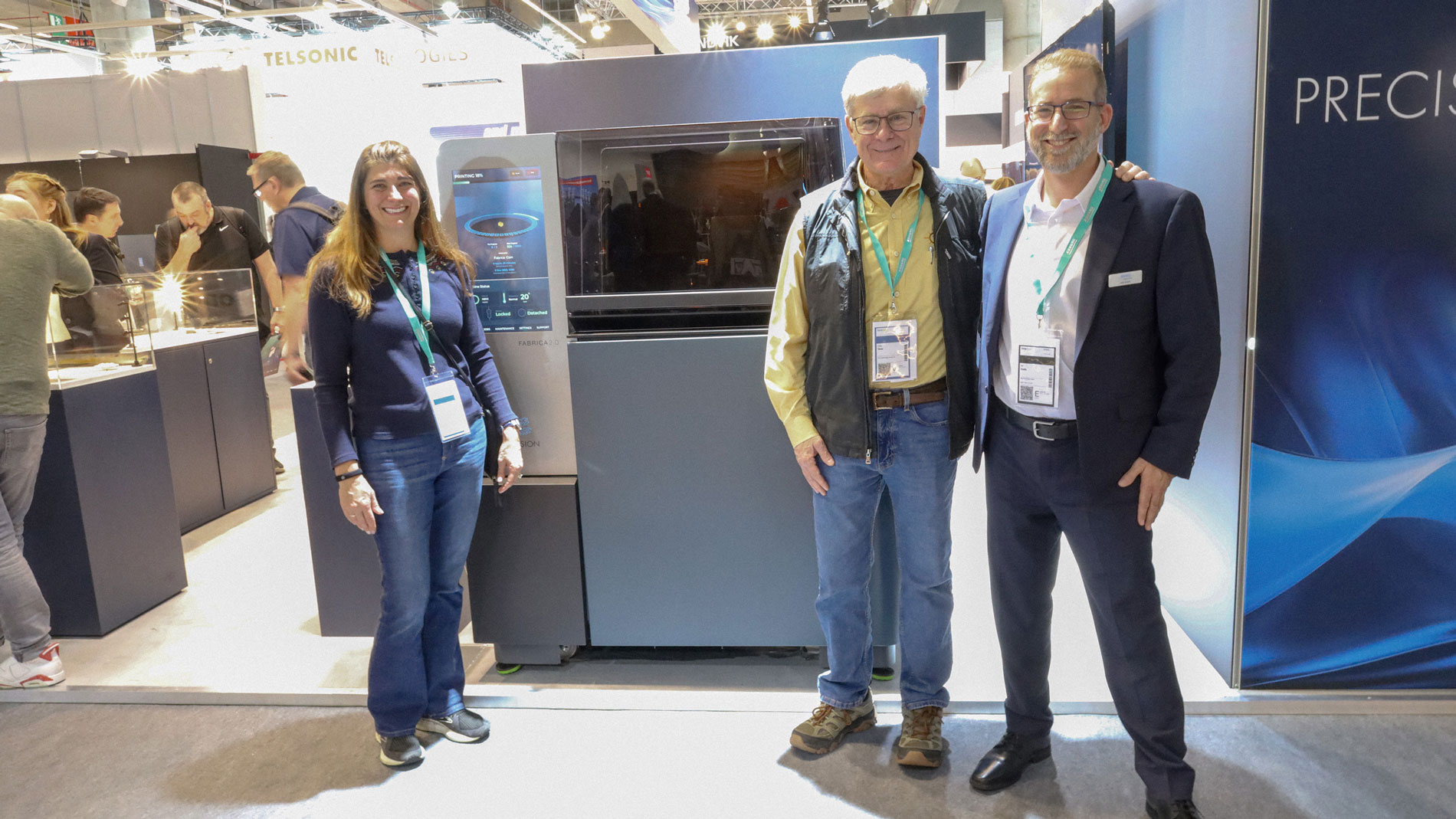
The Technology House, a contract manufacturer from the US state of Ohio, has become a believer in the technology after beta-testing the company’s Tera machines and now using it for two years. »Micro 3D Printing is giving a new boost to product development, « explains CEO Chip Gear. »Components are getting smaller and smaller, and ultimately, so are the overall products. There’s a lot of potential for the aerospace industry, for example, but also for other sectors.«
Gear and his daughter, Tracy Brent (president of The Technology House), spent three days taking in the innovations at Formnext in Frankfurt. »This is the right place to see the developments and advances within the AM market. At Formnext, we were able to experience a wide variety of systems and materials bundled together and efficiently in one place,« Gear continues. »This gave us the opportunity to find and select the most suitable solutions for our production.«
Founded in 1987 and now employing 85 people, his company has built up an impressive AM machine park that includes numerous printers from the likes of HP, Carbon, and 3D Systems. On a production floor spanning around 500 square meters, components are also conventionally milled or manufactured using injection molding or EDM processes.
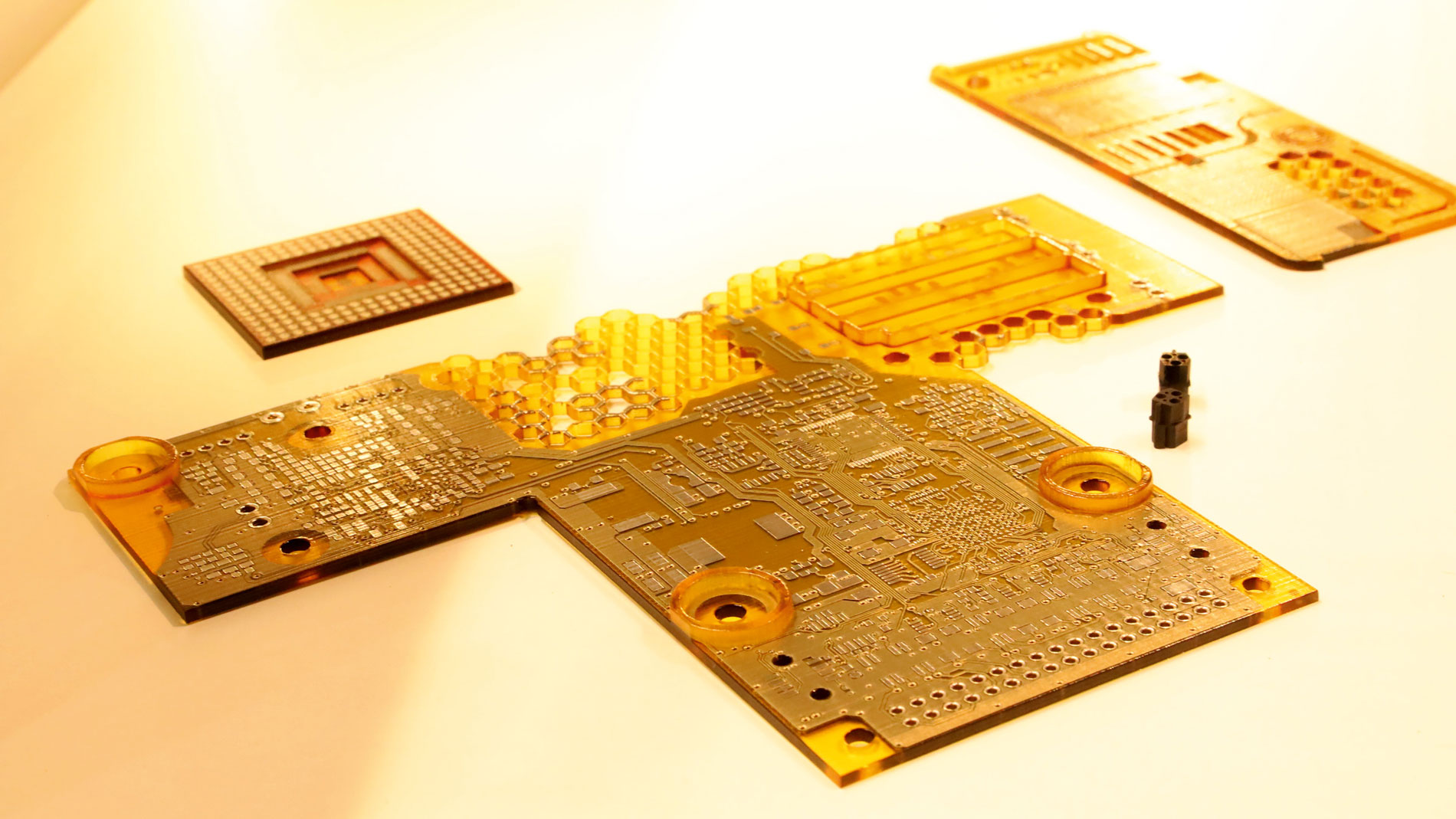
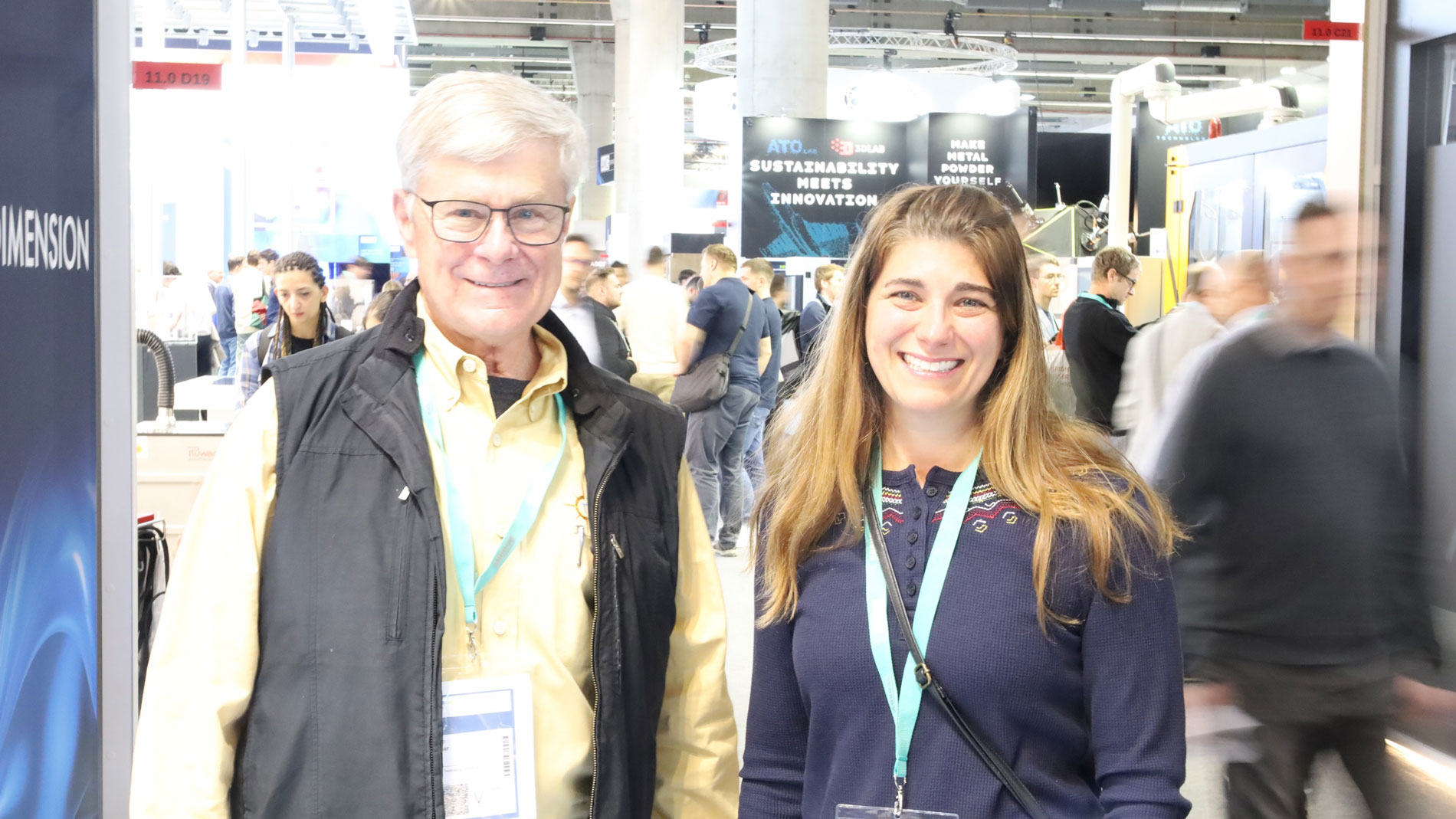
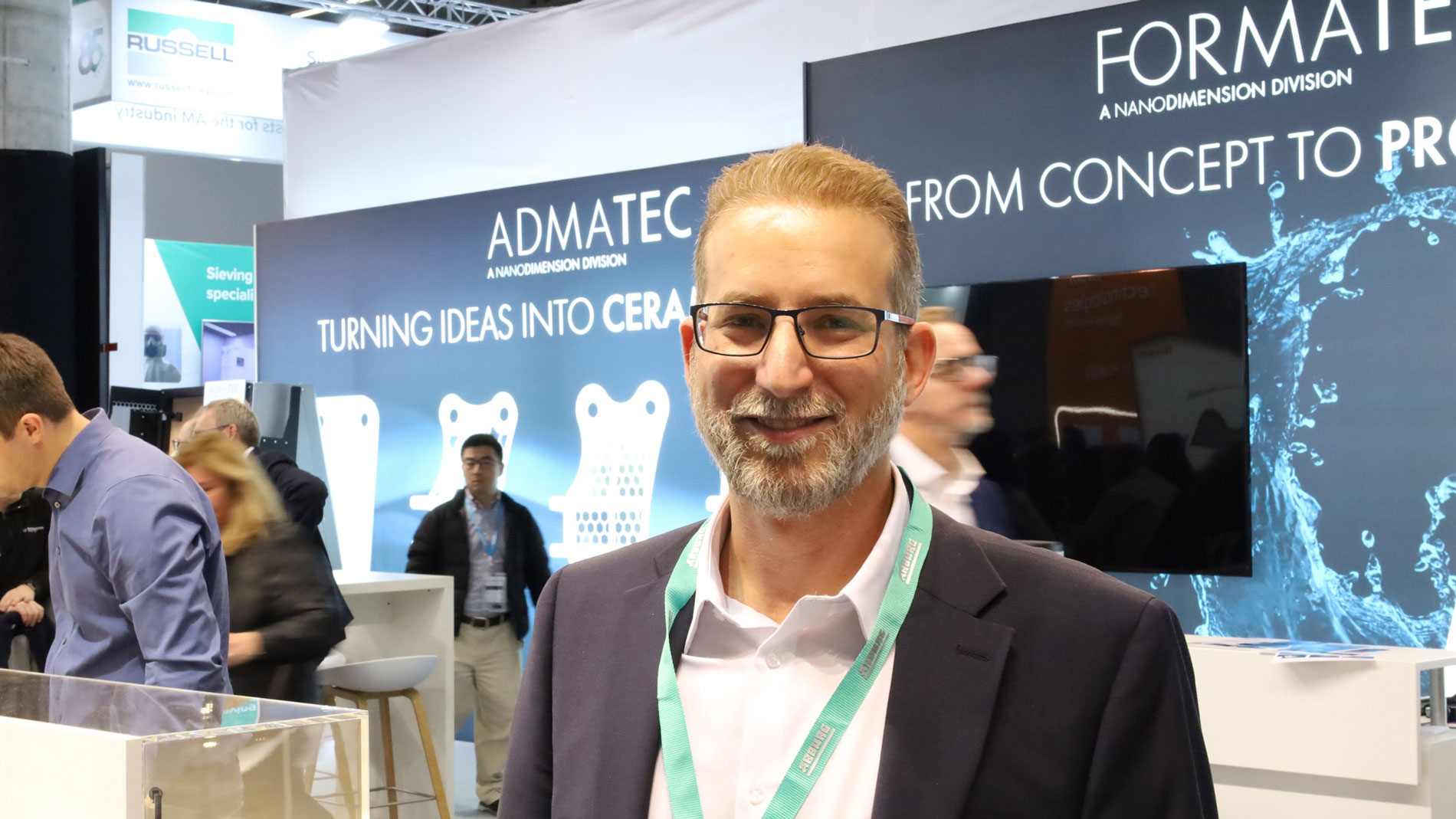
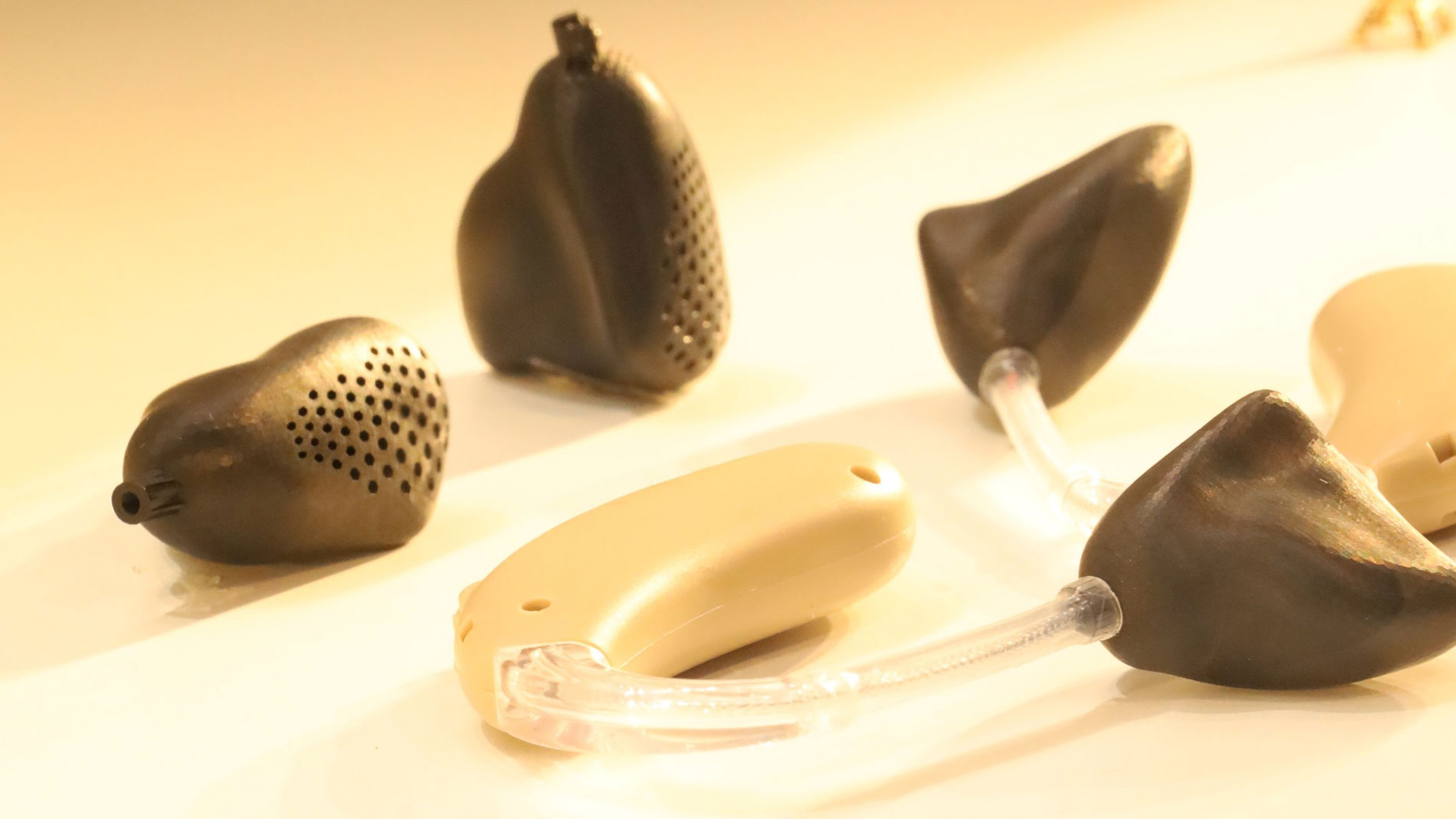
AM components now account for 30 percent of The Technology House’s turnover, and Brent and Gear want to increase this further. However, there are still challenges to be overcome in nano technology, especially in post-processing. »How do you clean the components, and how do you measure them?« Brent points out. »That said, we’re already seeing important improvements on the market.«
Nano Dimension finished beta testing its Tera machines more than a year ago and has already installed 10 systems, as Nir Sade reports.
FURTHER INFORMATION:
Tags
- Additive Manufacturing
- Formnext News
- Consumer Health Care
- Aviation and aerospace
- Electronic engineering and electronics