Text: Thomas Masuch; Photos: Farsoon — 15 June 2020
International groups cooperate with Chinese companies and research institutions to drive their technological development and gain access to markets. Dr. Dirk Simon, managing director of Farsoon Europe GmbH, has supported numerous collaborations between German and Chinese firms and is now using his experience to advance applications in Additive Manufacturing.
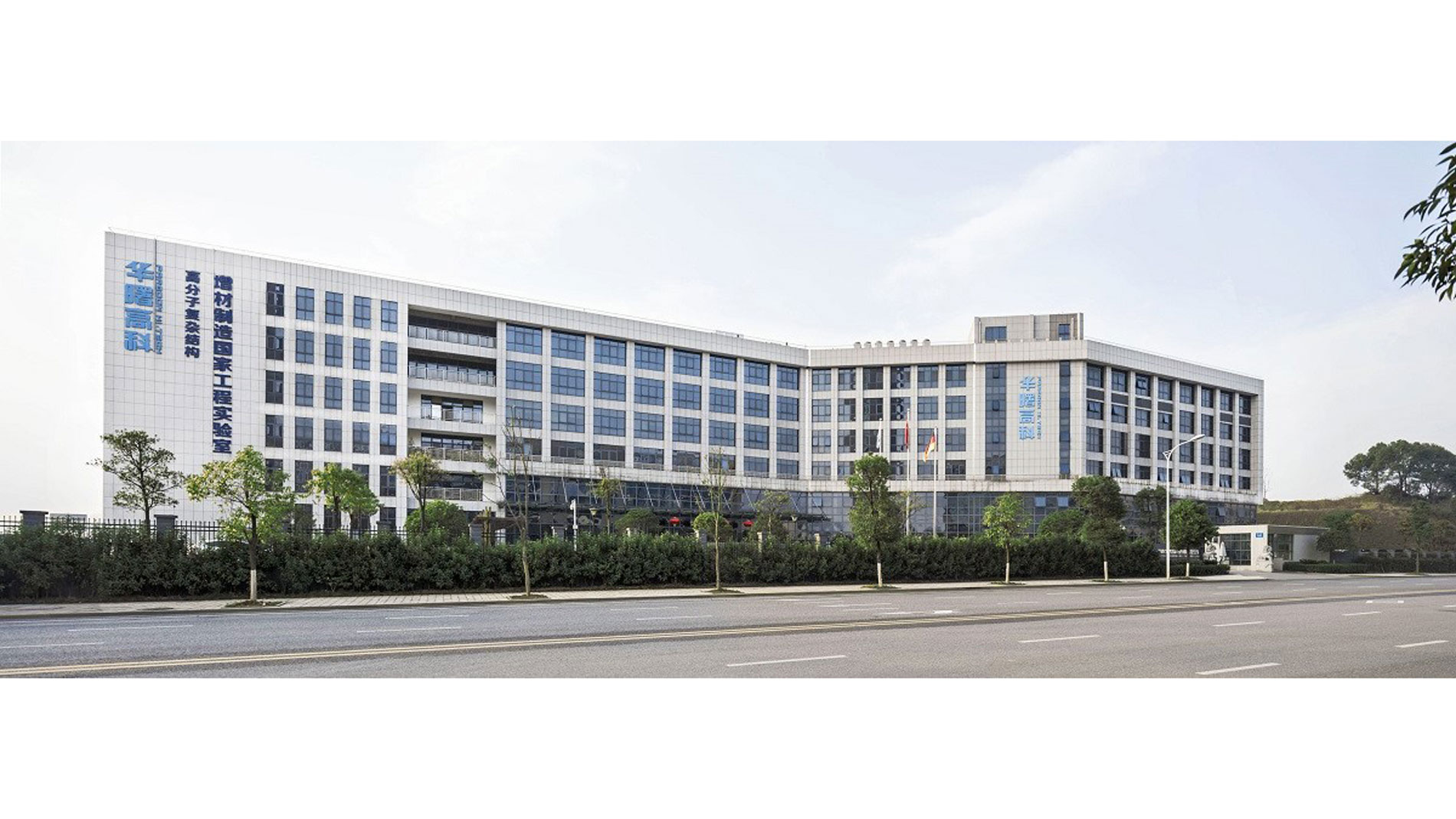
When Dr. Dirk Simon signed a cooperation agreement in China for the first time in 1999, he says the type of cooperation was »not comparable to how things work today.« That arrangement involved the development of flame-resistant plastics along with the Chinese Academy of Sciences in Beijing. Dr. Simon also describes the manner of communication – along with the feeling-out process and agreements on the eventual monetization of research results – as very different. »It’s gotten much easier these days; it’s a completely different world,« he says. Dr. Simon goes on to cite the legal regulations that now apply to such cooperations, and the fact that they’ve taken on a much more open format. He reports that China is another country where the concept of open innovation has clearly been having an even greater impact on the mindsets of those who work in R&D departments.
As part of his work at BASF and Farsoon Europe GmbH – the European service and sales subsidiary he has headed for the past two years – Dr. Simon has also assisted other collaborations. In 2013, for example, BASF launched its development initiative in China and began working closely with Farsoon. »It wasn’t about just application technology; the focus was on real research, as well,« he explains. The undertaking resulted in a new high-performance material and a machine optimized to work with it – the Farsoon HT251P. »That machine and the Polyamide 6 powder were designed to be a perfect match,« recalls Dr. Simon, who oversaw 3D printing activities as an authorized representative of BASF 3D Printing Solutions GmbH until March 2018.
Up to 360 degrees (C)
Among other things, the material required a processing temperature of more 200 degrees (Celsius), which in turn entailed technical adjustments in machine design, seals, remaining oxygen levels, and more. This machine- material tandem has since gone international; its adherents include PATAC, the Chinese development partner of General Motors, which uses the HT251P and PA6 to produce functional prototypes for motor compartments. In Germany, FKM Sintertechnik also uses the pairing for things like manufacturing its own automotive prototypes.
Elsewhere in the field of high-temperature applications, Farsoon has also been cooperating with aviation giant Airbus since 2019. Due to the strict requirements placed on interior aircraft components, the processing temperatures involved are even higher – up to 360 degrees (C), in fact. This collaboration has brought forth a new machine that Farsoon will be presenting at Formnext 2020.
The Farsoon Flight HT403P serves as proof that China can now contend with the world’s best when it comes to the ability to innovate. While the Flight™ technology came together without international cooperation, Farsoon has since begun working with Western firms again to beta-test its latest creation. Switzerland’s Rapid Manufacturing AG is currently analyzing the HT403P’s suitability for European environments. The machine has a build cylinder measuring 400 x 400 x 540 cubic millimeters and a 500-watt laser that (according to the manufacturer) is especially fast at shaping the black polyamide powder into plastic components.
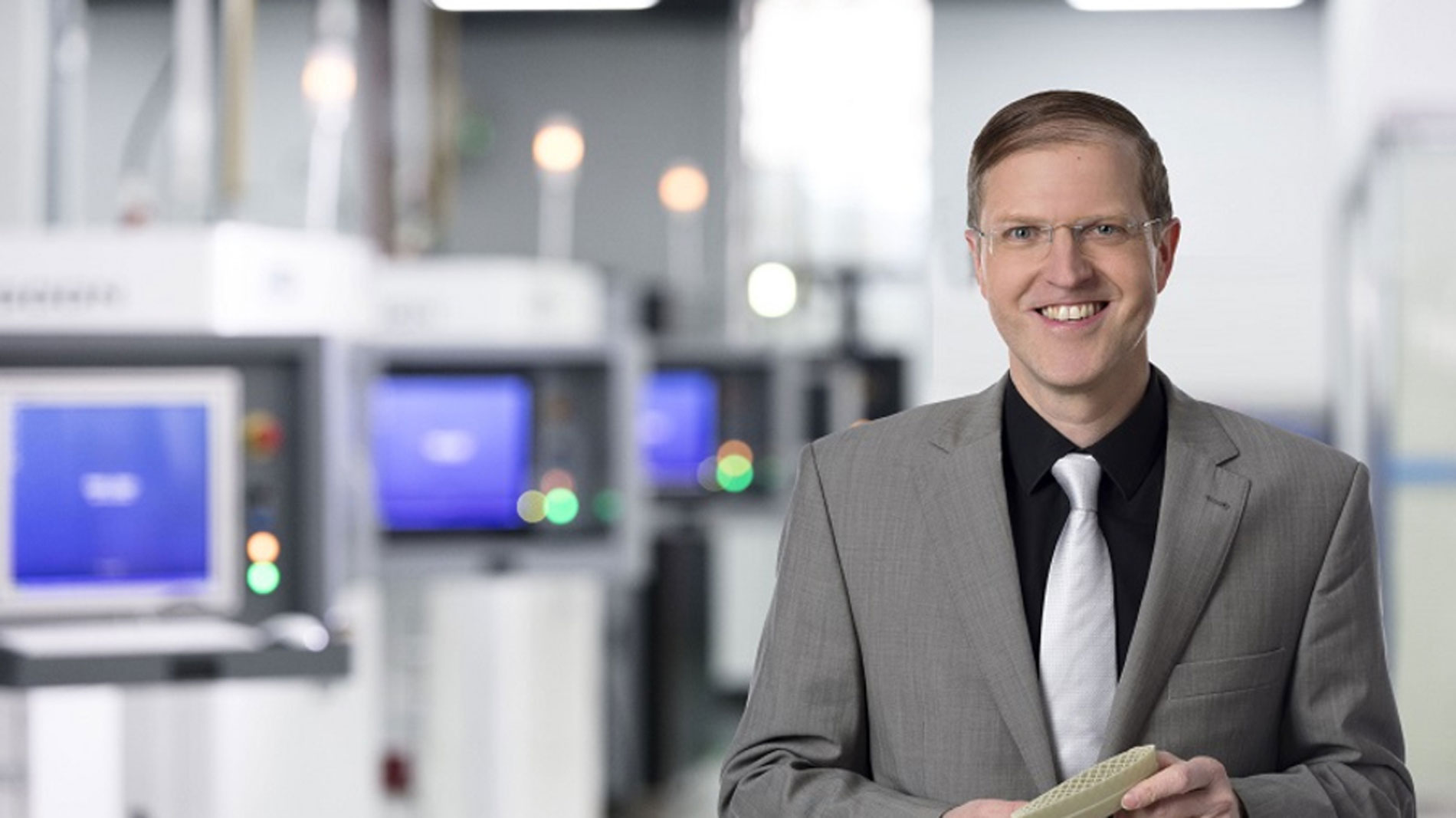
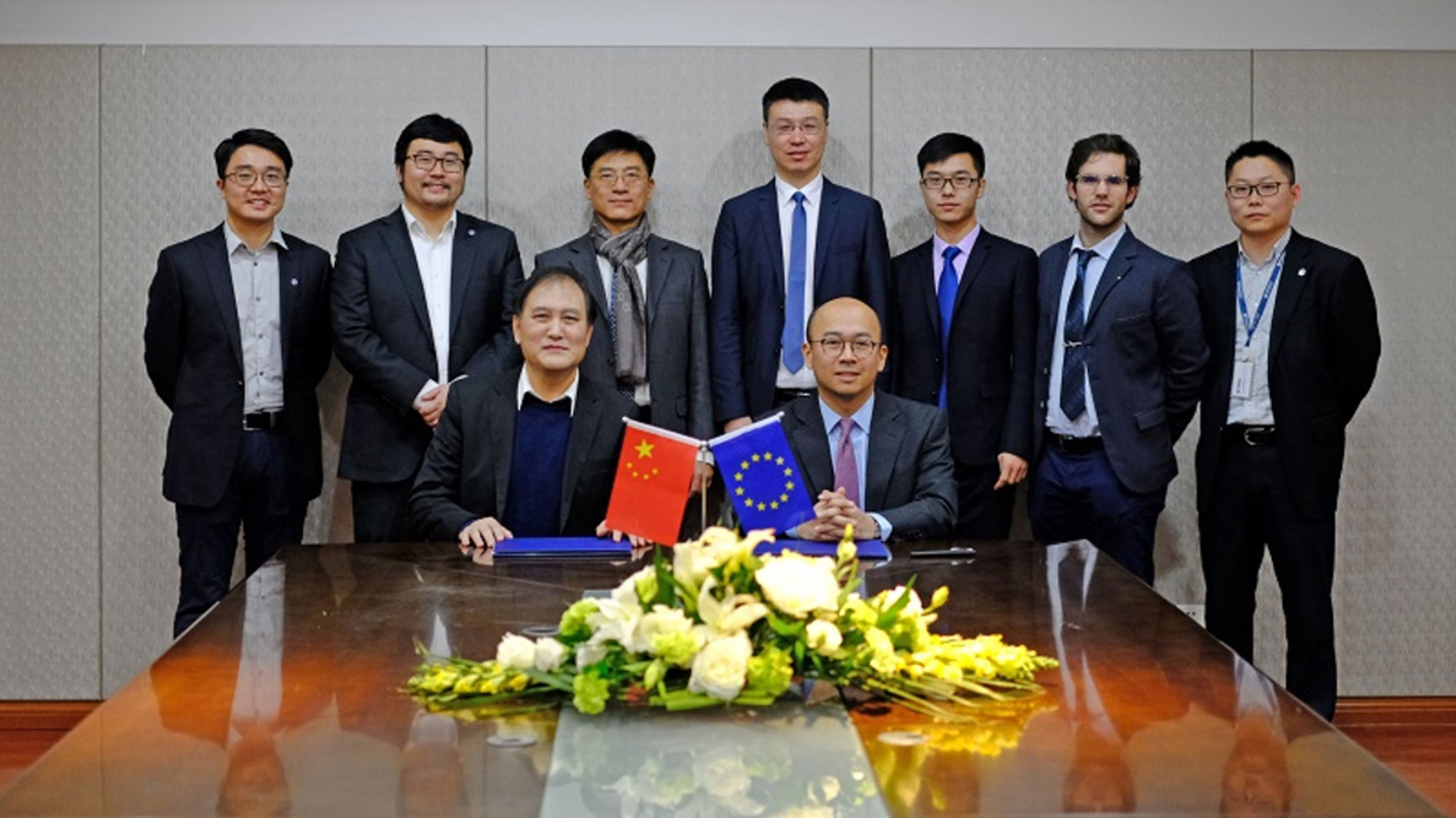
It’s through international cooperations like these that Farsoon is not only developing its technological expertise, but continuing to burnish its reputation around the world, as well. According to Dr. Simon, this makes it easier for his company to enter Western markets. He points out that it remains difficult for Chinese firms to get a foothold in Europe. Although he believes that their general image has improved of late, Dr. Simon still encounters people in Europe who assume that a Chinese company must surely be selling its machines at a much lower price point than its competition on the continent. »That’s not what we do,« he says before explaining that Farsoon is working to win customers over by »offering more for the same price, like Toyota started doing 30 years ago in the automobile industry.«
To expand its presence further in Europe’s crucial marketplace, the company founded the Stuttgart-based Farsoon Europe GmbH in April 2018. Dr. Simon has led the subsidiary from the very beginning, offering Farsoon’s entire line of machines and local service and maintenance with the help of 12 employees.
Farsoon Technologies
Founded in 2009 by Dr. Xiaoshu Xu, Farsoon Technologies is a full-service provider in the field of plastic laser sintering and metal laser melting technology. Dr. Xu remains the chairman of the company, which employs around 300 people around the world. In the early 1990s, he was the technical director of the laser sintering pioneer DTM (now 3D Systems). These days, Farsoon is making its machines compatible with materials from any manufacturer based on its »Open for Industry« philosophy.
farsoon.com
Tags
- Additive Manufacturing