26 March 2024
Even in times that have not gotten any easier for start-ups, the additive world is showing that it’s always coming up with new innovations. After several years of development, the US start-up Fluent Metal and its new AM technology are now ready for their market debut. Founded in 2020 by Peter Schmitt, former chief designer at Desktop Metal, the company's drop-on-demand approach promises to be an efficient production method that can be used to process most metals.
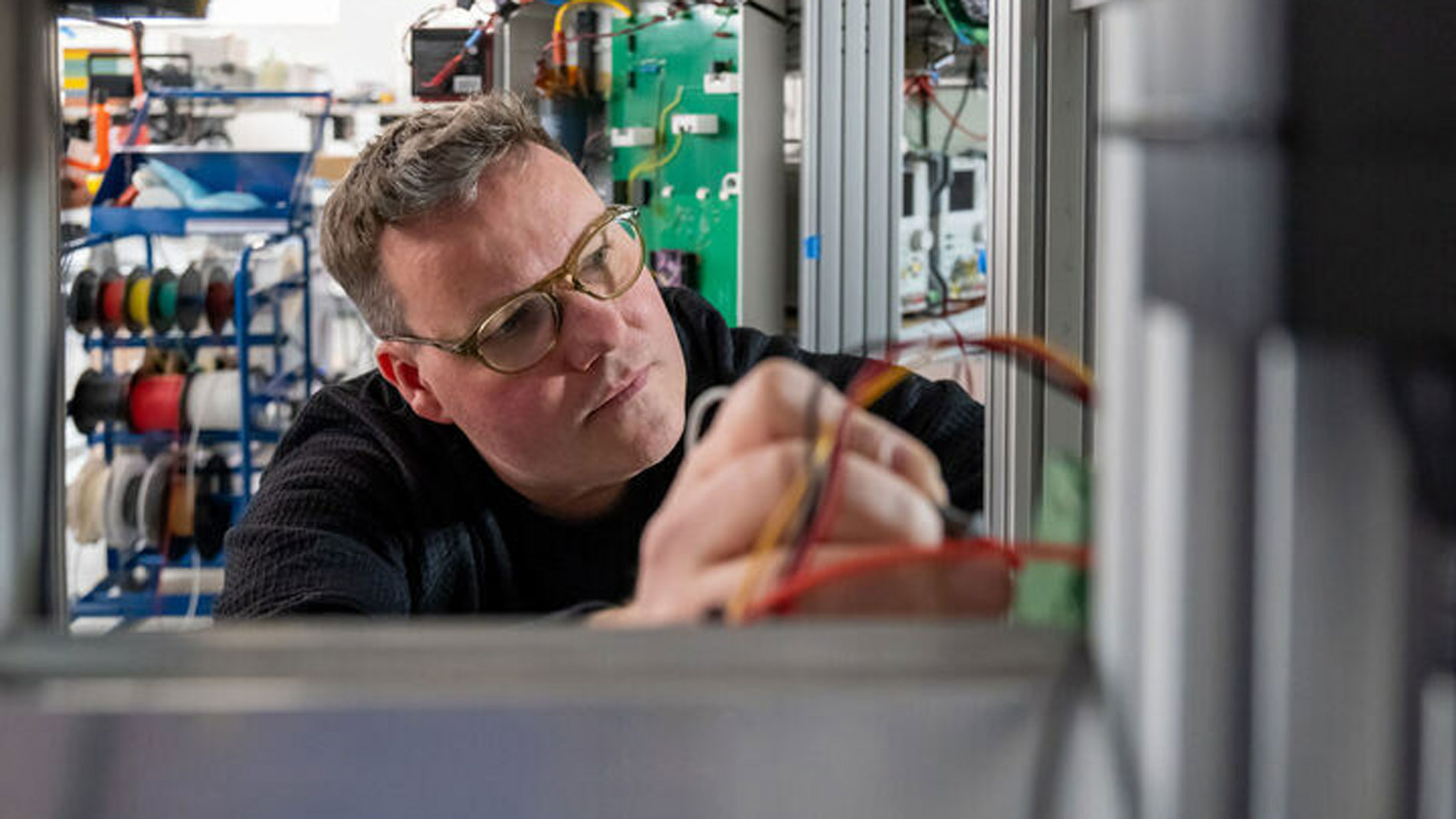
To fuel its further development, the young company has already received USD 5.5 million in funding (the bulk of it from E15 with participation from Pillar VC and industry angels). With its drop-shaped 3D printing, which is reminiscent of inkjet printing, Fluent Metal promises a lean overhead process that produces functional parts more sustainably and efficiently.
“Drop-on-demand technology is an elegant approach to creating complex metal components,” says Schmitt, who is also the CEO of Fluent Metal. “Whether it's prototype iterations of an idea or production runs of a single part, Fluent Metal will provide customers with great operational and material flexibility. This freedom will unlock new creativity and problem-solving abilities across industries.”
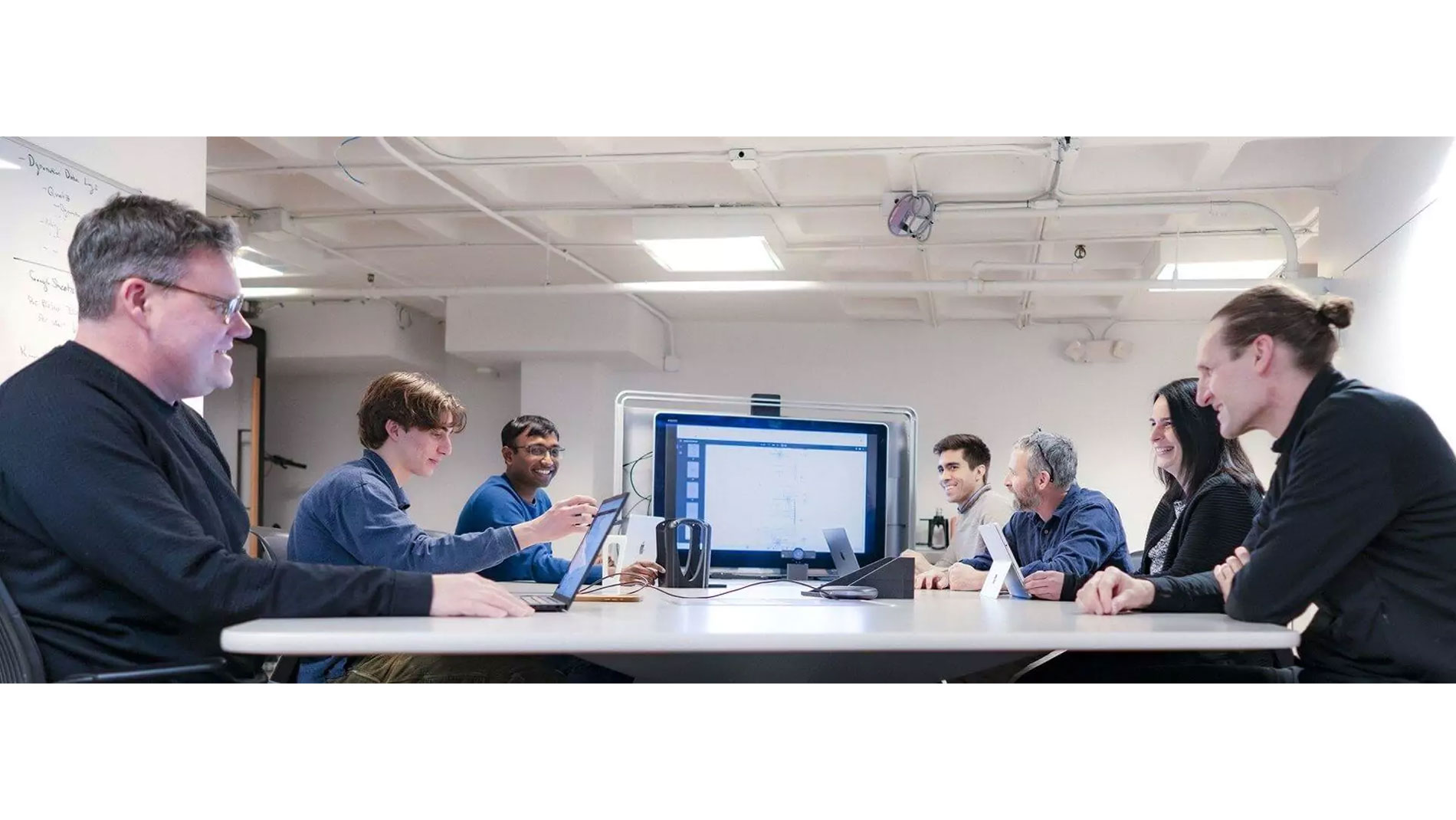
The Fluent Metal team. Image: Fluent Metal
Using wire as the starting material, Fluent Metal enables multi-metal printing that produces no waste. The company claims that it's even possible to combine high-value metals in intricate ways. Complex shapes such as fully enclosed voids and internal channels can be realized thanks to the inkjet-like printhead and parallel throughput.
Fluent Metal says that its approach is designed for safe operations on a typical manufacturing floor or even in a prototyping shop, without the need for clean rooms or expensive safety measures. Material changeover is also designed to be as easy as plug-and-play, which reduces setup effort and allows for higher machine uptime.
Industry veterans from Vulcan Forms and the MIT Media Lab are leading the young company along with Peter Schmitt.
MORE INFORMATION:
Tags
- Additive Manufacturing
- Aviation and aerospace