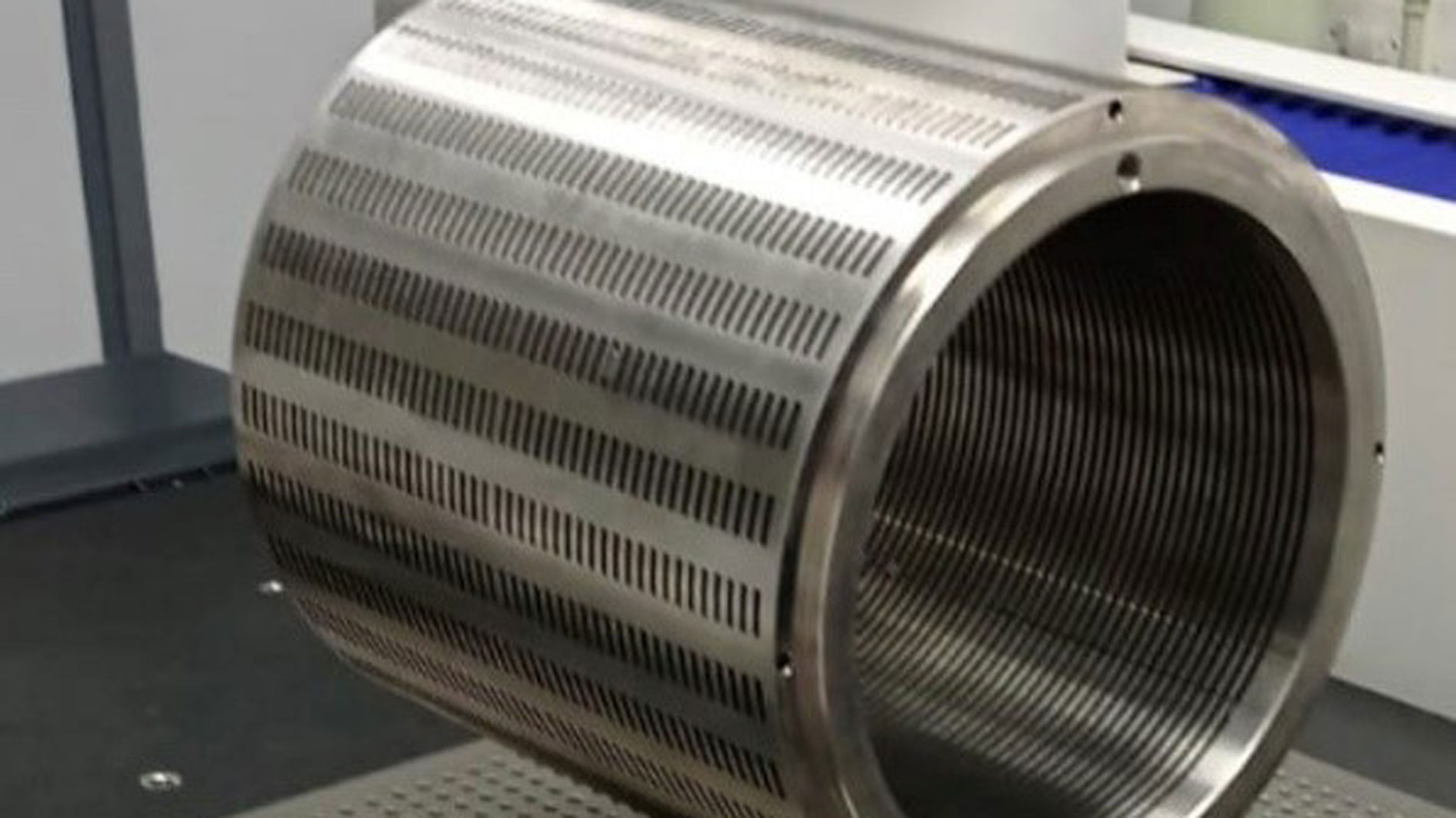
The project partners came up with the solution based on Additive Manufacturing to overcome some of the previous challenges at the power plant, which included long delivery times, high costs, and limited technical support from the original equipment manufacturer (OEM). These factors jeopardized the availability of critical spare parts the plant requires for continuous operation.
One key objective was to reduce delivery times in order to meet a scheduled maintenance date in 12 weeks. The project used a specific metal powder made of Inconel 718, which is produced by Fomas Group: Mimete V 718, a nickel-based alloy that, according to Fomas, has very good properties in high-temperature environments.
Production was closely monitored throughout the development chain, from initial design to printing and quality testing. In the end, the labyrinth cage was produced in just eight weeks, including the design, prototyping, and testing phases. Fomas reports that the costs were also reduced by 16 percent compared to the conventional part.
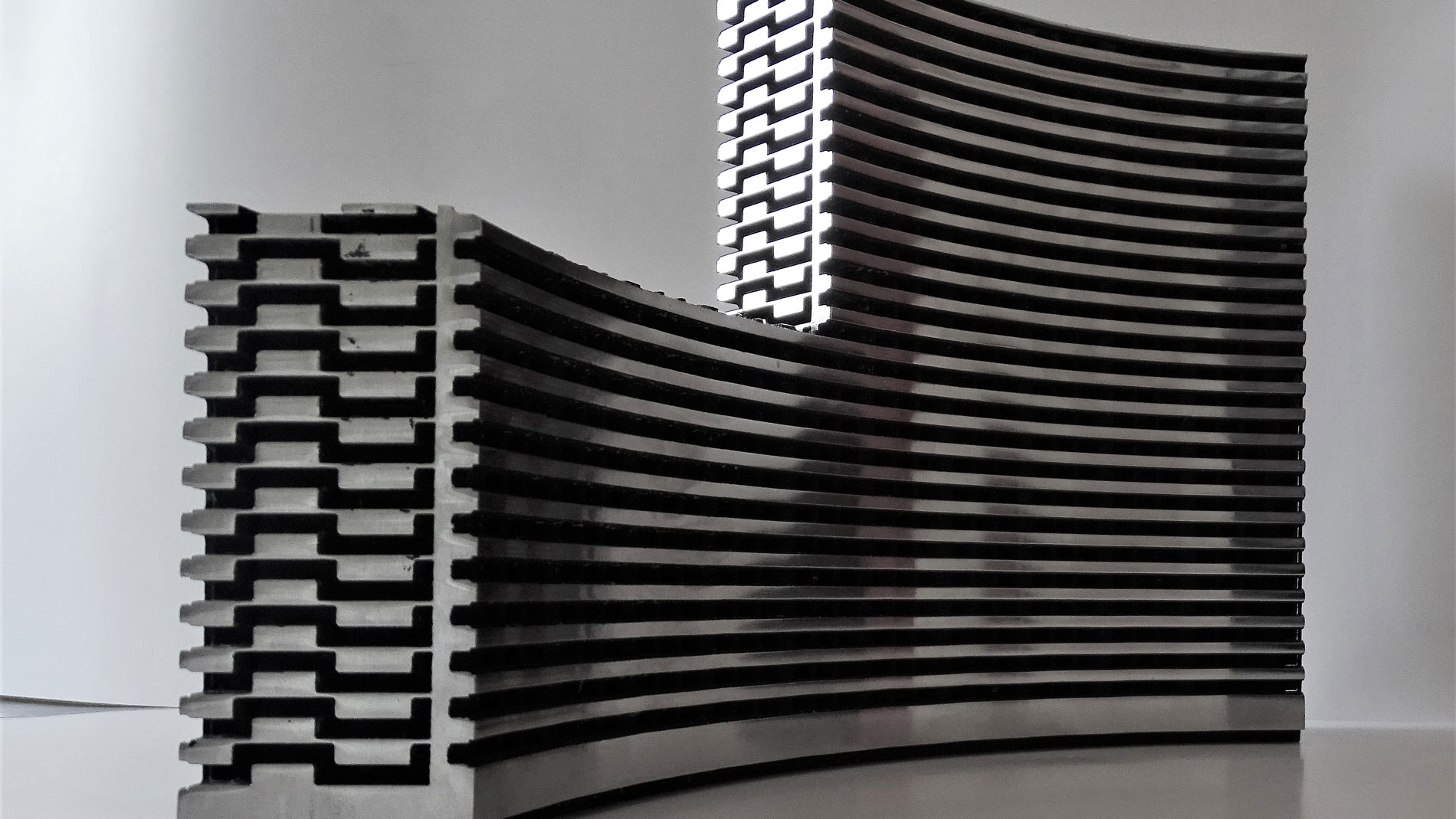