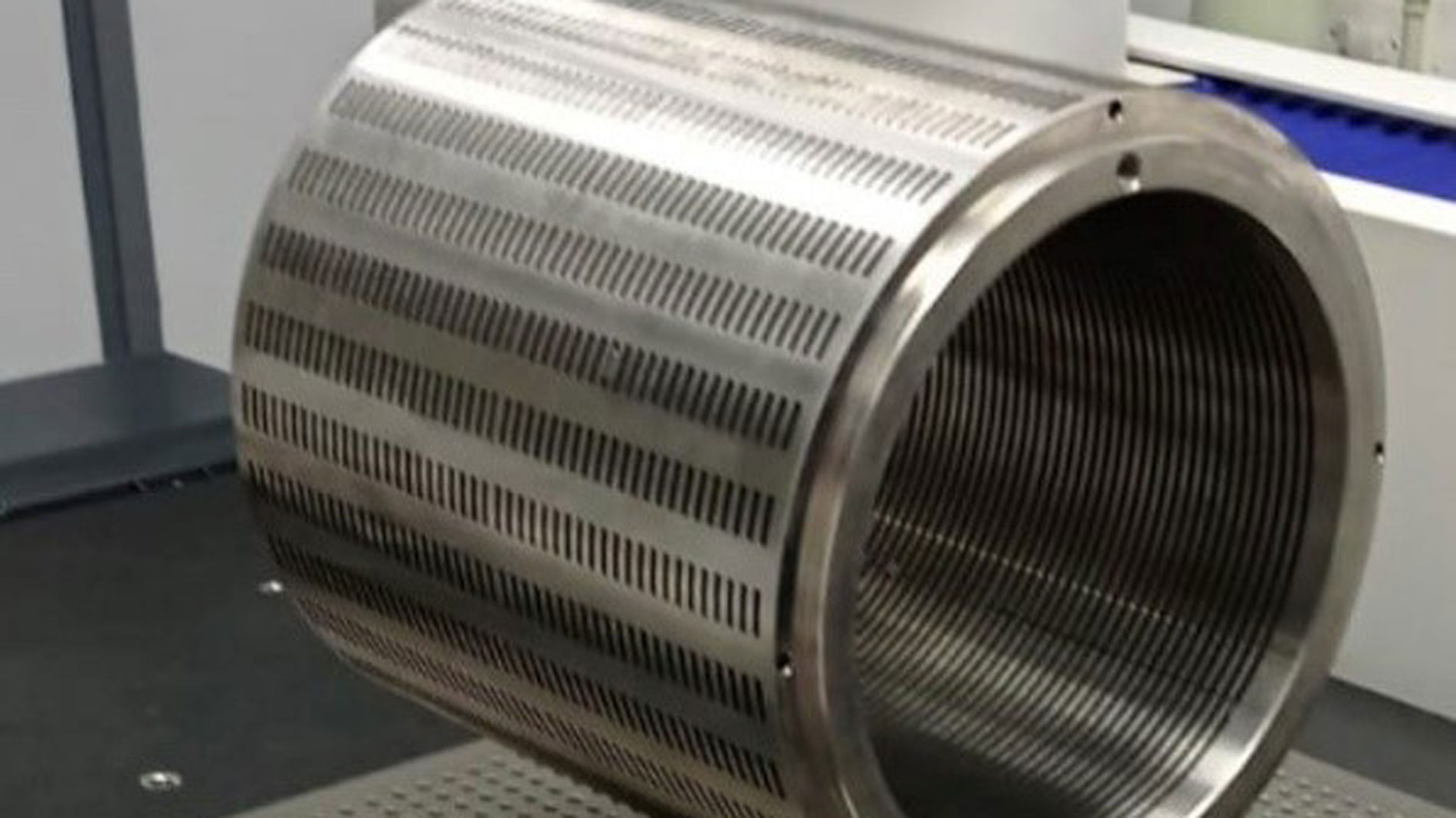
Die Projektpartner entwickelten eine auf der Additiven Fertigung basierende Lösung, mit der einige der bisherigen Herausforderungen im Kraftwerk beseitigt werden sollten: lange Lieferzeiten, hohe Kosten und eine begrenzte technische Unterstützung durch den Erstausrüster (OEM). Diese Faktoren gefährdeten die Verfügbarkeit wichtiger Ersatzteile, die für einen kontinuierlichen Betrieb erforderlich waren.
Ein wichtiges Ziel war die Verkürzung der Lieferzeiten, um einen geplanten Wartungstermin innerhalb von zwölf Wochen einhalten zu können. Bei dem Projekt kam ein spezifisches Metallpulver aus Inconel 718, einer Nickelbasislegierung der Fomas Group, zum Einsatz: Mimete V718. Das Material besitzt laut Fomas sehr gute Eigenschaften in Hochtemperaturumgebungen.
Die Produktion wurde während der gesamten Entwicklungskette genau überwacht, vom ersten Entwurf bis zum Druck und den Qualitätstests. Letztendlich wurde der Labyrinthkäfig in nur acht Wochen hergestellt, einschließlich Entwurfs-, Prototyping- und Testphase. Laut Fomas konnten auch die Kosten im Vergleich zum herkömmlichen Teil um 16 Prozent reduziert werden.
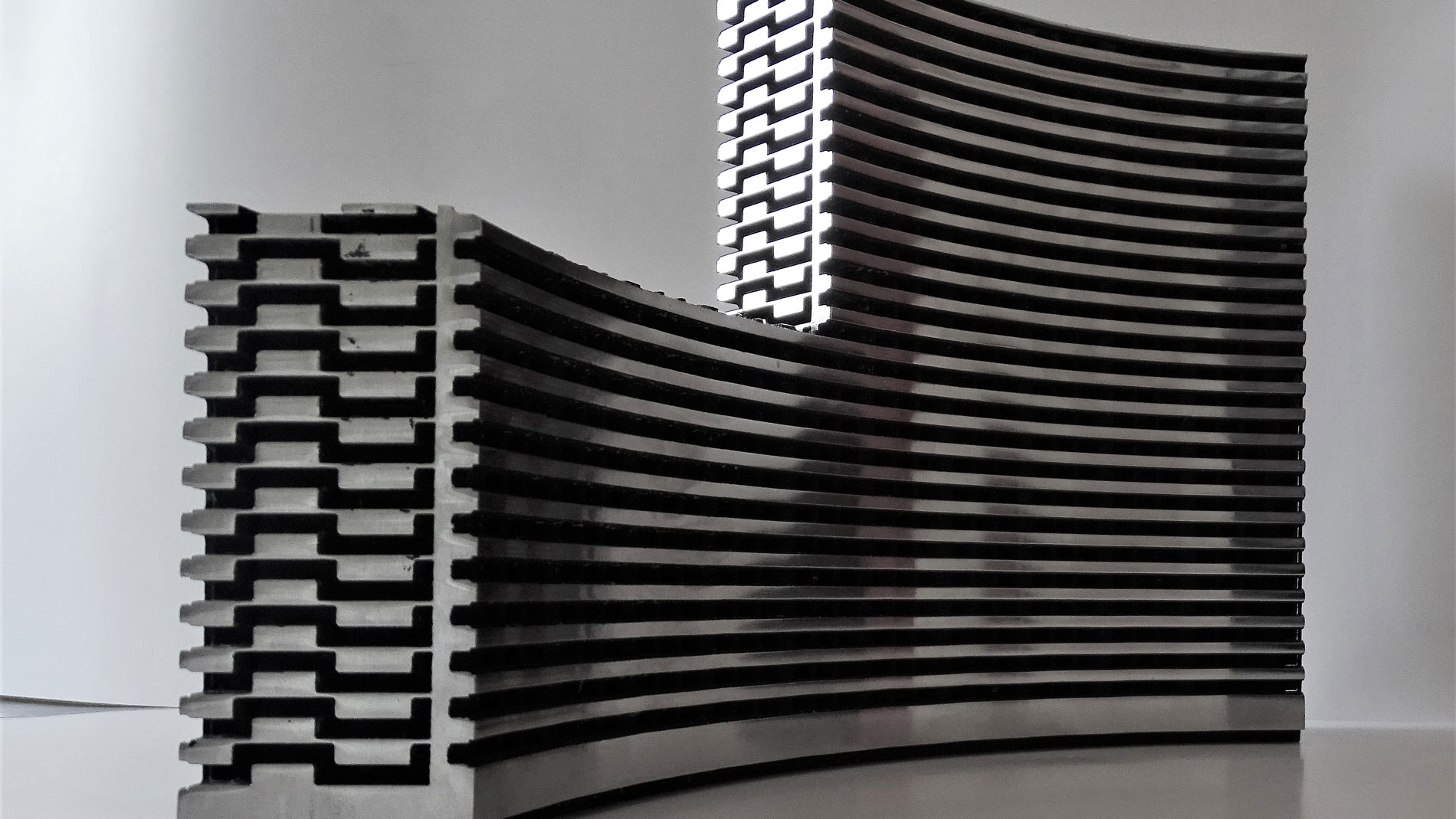