Text: Thomas Masuch
Additive manufacturing has been used in the aerospace industry for more than 30 years, and today all major aircraft and engine manufacturers have integrated the technology into their production processes. The GE9X turbofan engine from GE Aerospace shows how far this process has already progressed: The largest and - with a maximum thrust of 597 kN - most powerful engine in civil aviation contains around 300 additively manufactured components.
Additive manufacturing is also playing an increasingly important role in the construction of satellites and rockets in the aerospace sector: More and more companies, including many start-ups, want to get involved in the zero-gravity business and are using 3D-printed components and engines for their rockets. Or they just print an entire rocket, like Relativity Space.
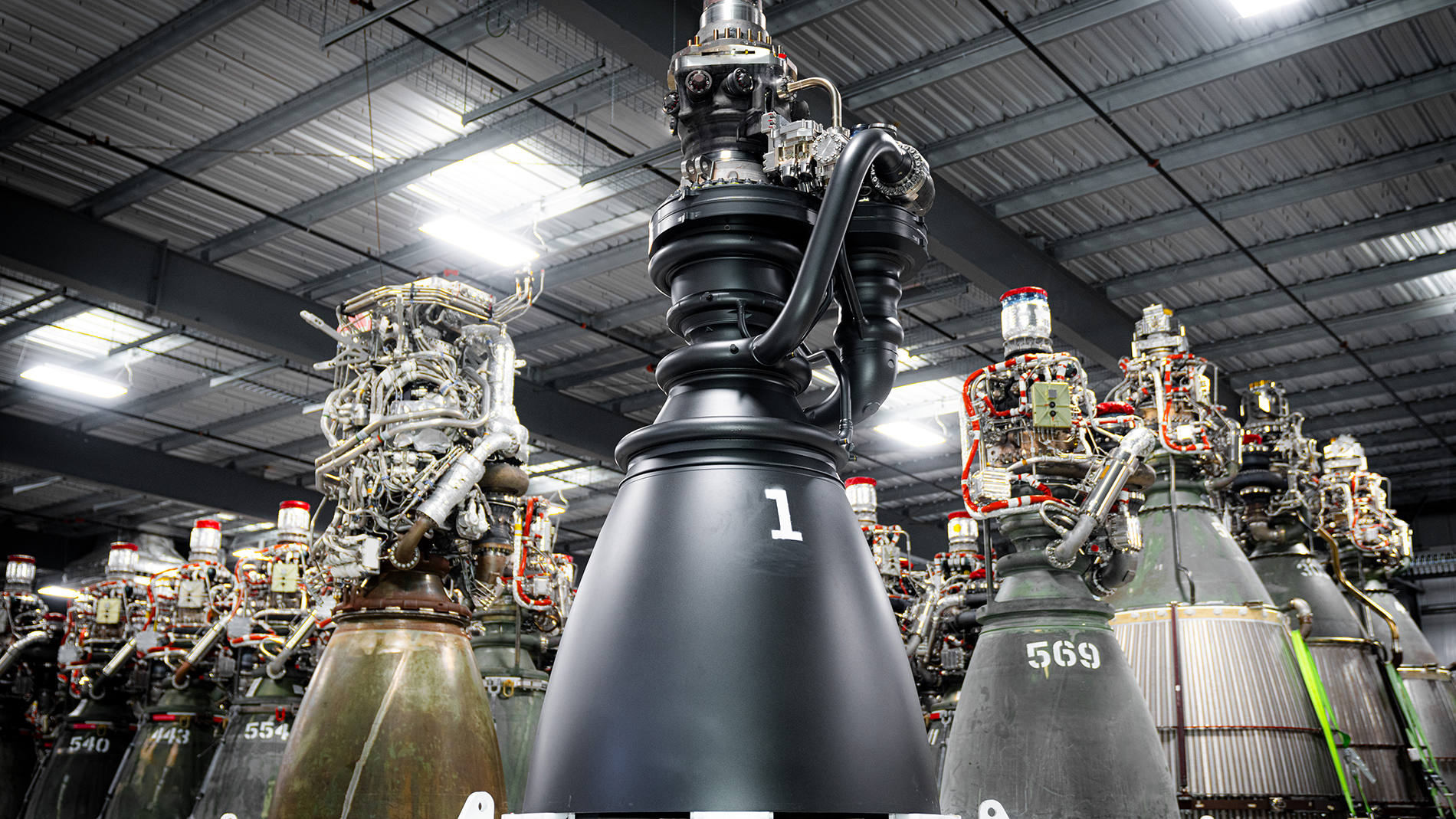
The new Raptor 3 engine from SpaceX. Image: SpaceX
The space market is currently dominated by SpaceX: According to Brycetech, Elon Musk's US company transported 518 satellites into space in the third quarter of 2024 alone - around ten times as many as China's CASC, the world's second most important space company. The European Arianespace only managed to launch 12 satellites. SpaceX also uses additive manufacturing for its Raptor engines and has recently used DfAM to further optimize the design of its engines. Compared to the Raptor 1, the weight of the Raptor 3 has been significantly reduced from 2080 kg to 1525 kg, while the thrust has been increased from 1700 kN to 2750 kN, according to the company.
Important user industry
The importance of aerospace for additive manufacturing (and vice versa) was particularly evident at Formnext 2024. Corresponding applications were on display on numerous stands of machine manufacturers, service providers and other companies, ranging from large rocket engines, which were either completely printed (AMCM) or had numerous additively manufactured components (Trumpf), to smaller thrusters for satellites (e.g. EOS, service provider FKM and many others), antennas, plastic components for aircraft interiors and numerous metal components for aviation.
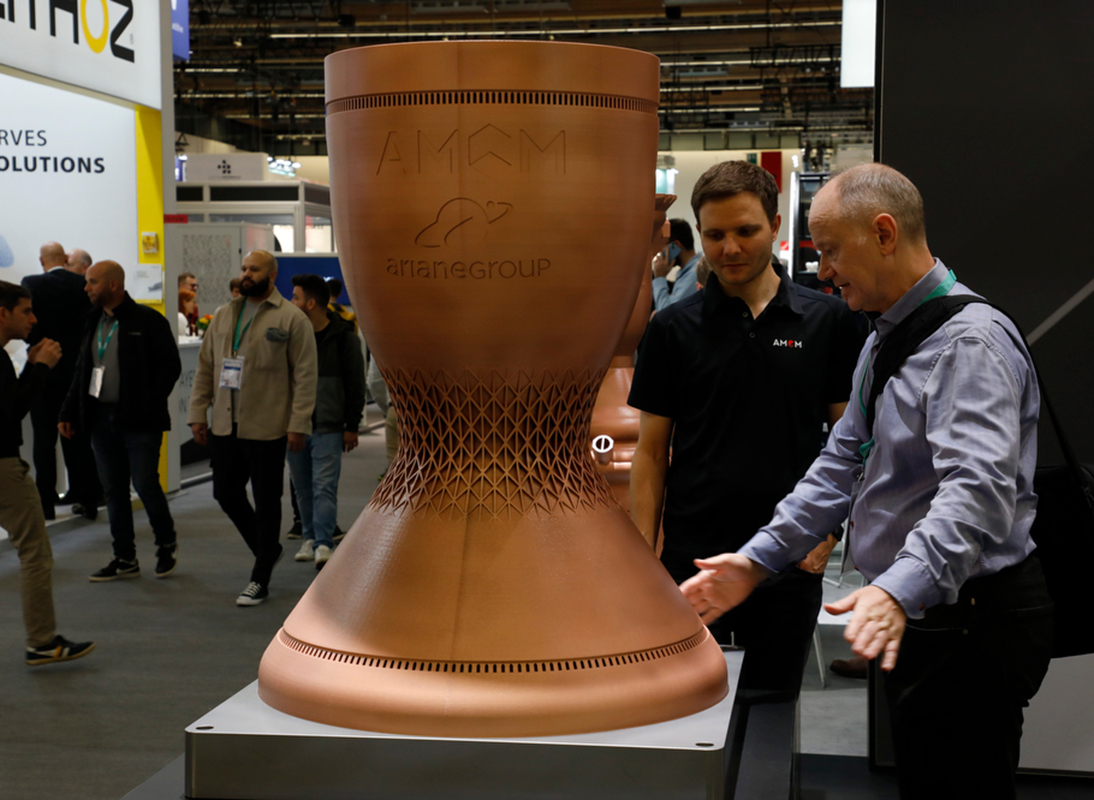
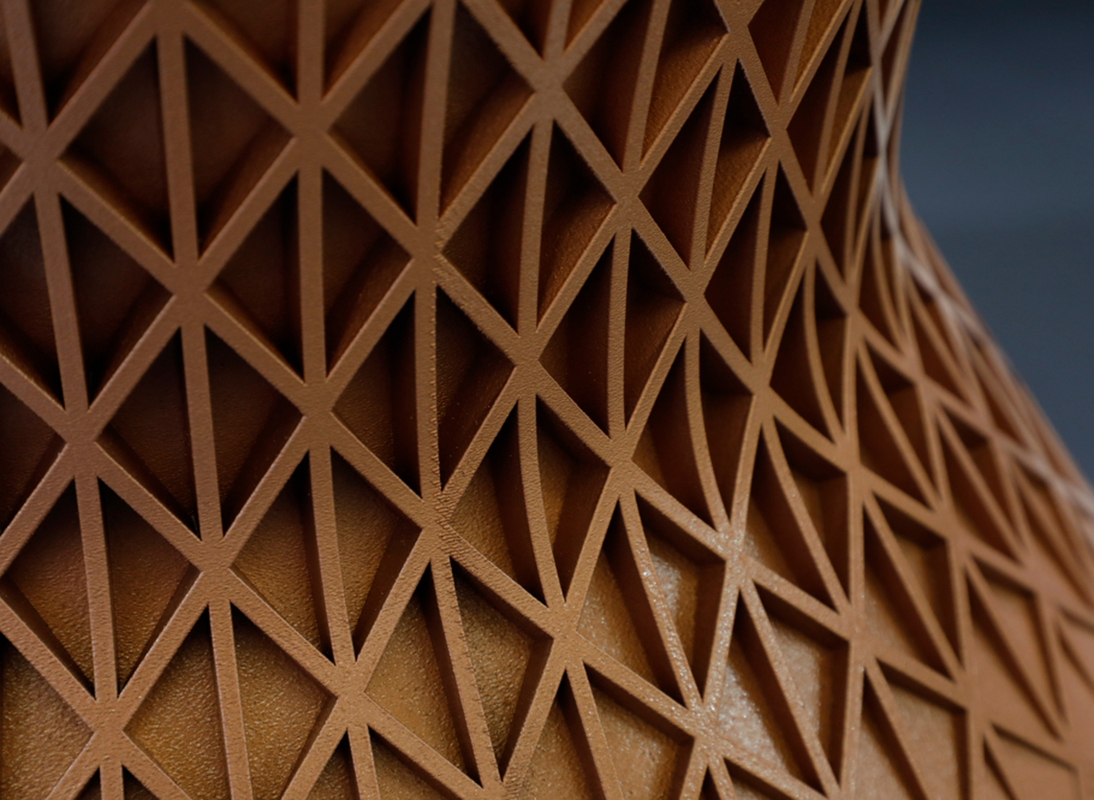
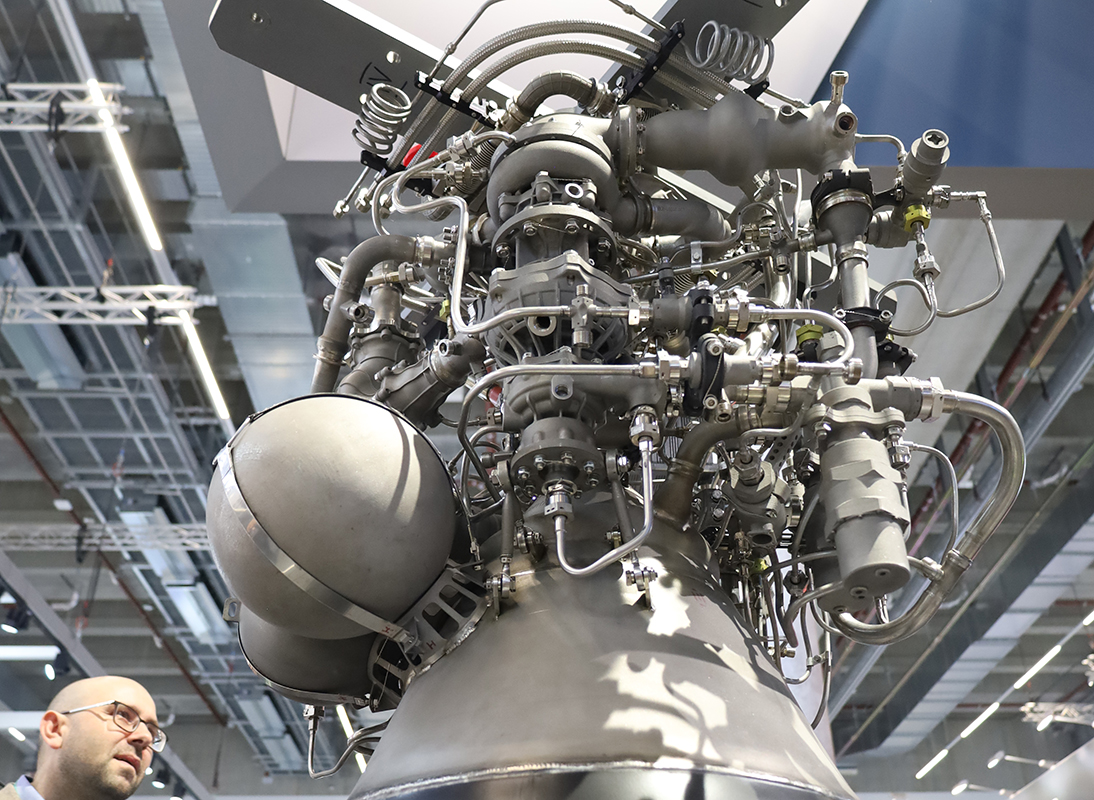
Rocket engines that are either partially or entirely 3D-printed were a leading topic at Formnext 2024 – here from AMCM and Trumpf. Images: Mesago / Marc Jacquemin (2), Thomas Masuch
Space and aviation are now often regarded as separate user industries. And that makes perfect sense, because the requirements and strategies of a start-up that wants to launch rockets with 3D-printed engines into space are very different from those of an aviation company such as Airbus or Boeing.
One of the reasons why additive manufacturing is so successful in both industries is that in most cases only small quantities are required. AM can also demonstrate its full capabilities in complex designs. This is another reason why the aviation and space sectors are among the most important user industries for additive manufacturing. According to the Wohlers Report, AM in the aerospace sector generated sales of USD 1.01 billion in 2023, which corresponds to 13.3% of the AM market. The proportion is even higher if you only look at the machines sold: According to the Ampower Report, machines worth EUR 440 million were sold to companies in the "Space" and "Civil aviation, turbines, helicopters" sectors in 2023, which corresponds to a combined share of 16.3% (Ampower has calculated sales of AM equipment to be worth EUR 2.71 billion in 2023) According to Ampower, turnover in both areas is set to roughly double by 2028.
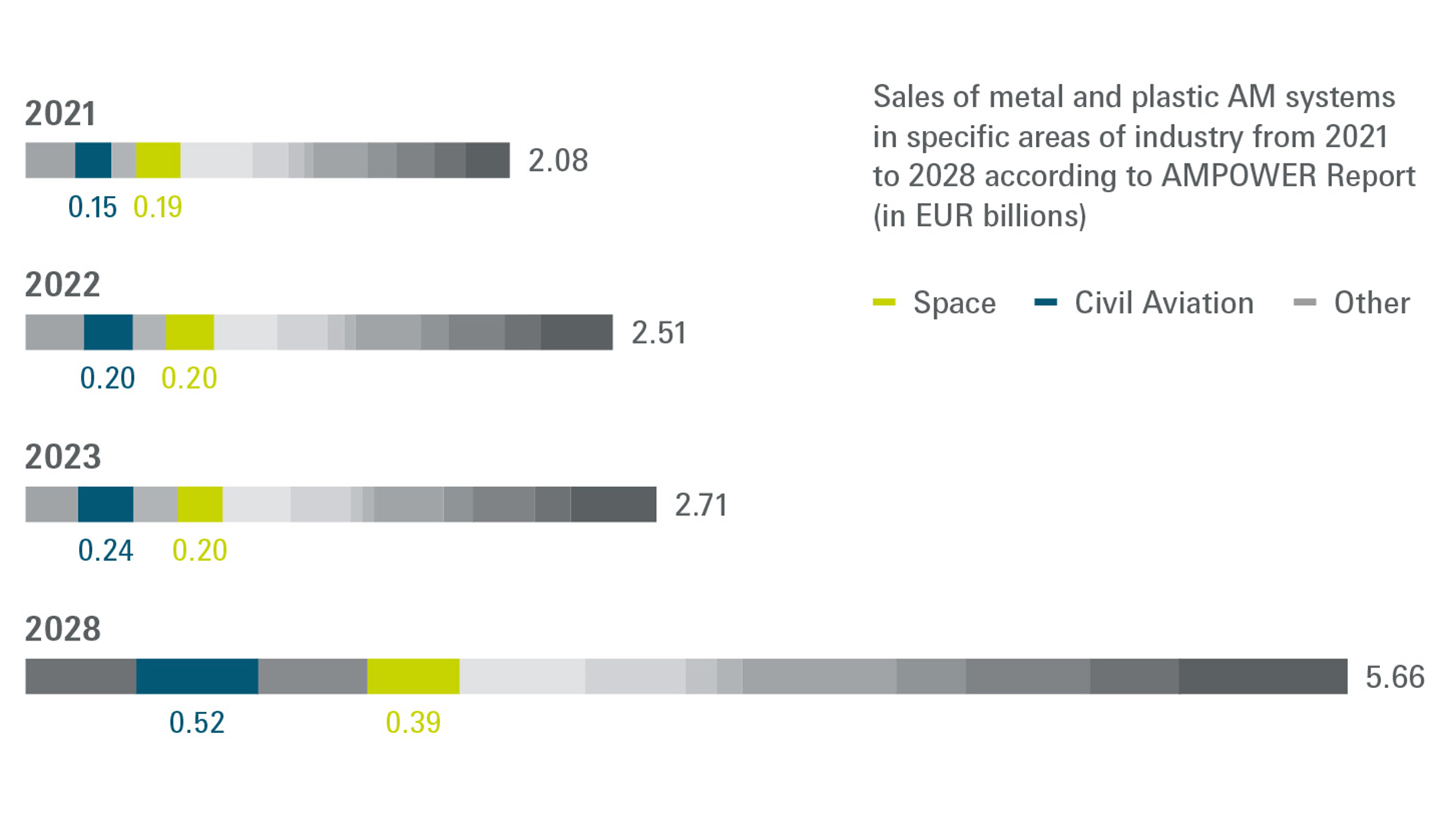
Applications in the space industry
A wealth of exhibits at Formnext 2024 showed that the space sector is constantly discovering new applications in addition to the already lucrative printing of engines and components for satellites. Among other things, Addup exhibited a very light antenna for satellites, while CONCR3DE presented a precise lightweight ceramic structure that can be used in telescopes, for example. In any case, space was also an important topic for other suppliers of ceramic 3D printing, as this material is very well suited to the harsh conditions in space due to its inert properties (see article on ceramics).
Dubai-based company Leap71, which specializes in AI-based engineering technology and develops rocket engines, among other things, shows just how quickly development is progressing. The company recently presented a 1.30 meter high 3D-printed 200 kN rocket engine. The component, which was manufactured on an Eplus system in 354 hours, is said to be the world's largest rocket engine printed in one piece. In December, Leap71 then announced that it had additively manufactured and tested an aerospike engine made of pure copper that generates a thrust of 5 kN and was developed in just a few weeks.
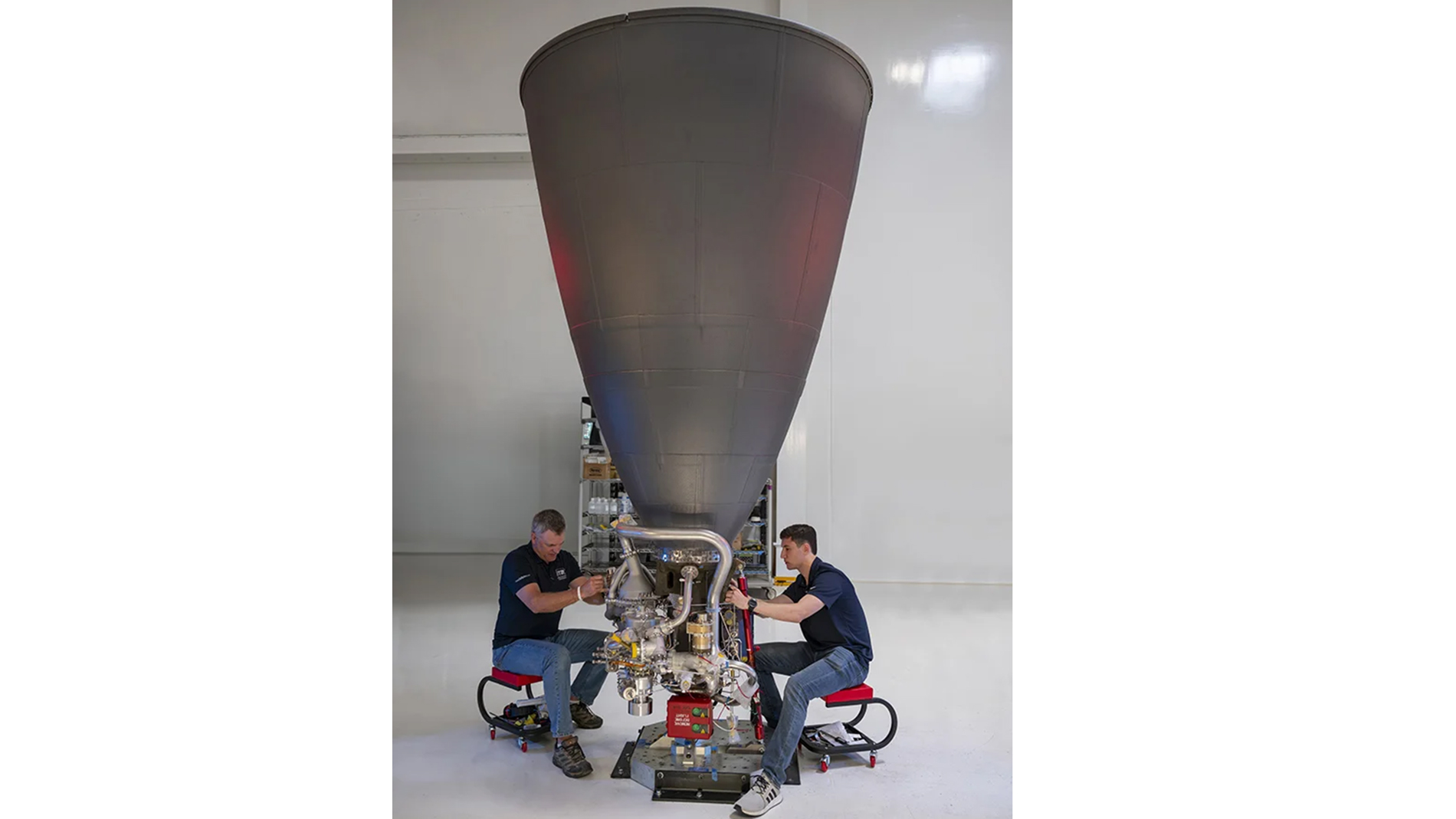
RL10-engine from L3 Harris. Image: L3 Harris
The new RL10E-1 copper engine, which the US company L3Harris delivered to its customer United Launch Alliance (ULA) in November 2024, is significantly larger. The RL10 engine has been in use for more than 60 years and has launched hundreds of satellites into space. Thanks to additive manufacturing, L3Harris was able to reduce its number of components by 98 percent. With a thrust of around 210 kN, the new engine is set to propel a Vulcan rocket into space this year.
Riccardo Marrucchi, Key Account & Business Development Manager Italy at Addup, presents A flight-ready Cassegrain antenna that Thales Alenia Space developed with Addup. 325 mm in diameter and 1 mm thick, it weighs just 385 g. Images: Thomas Masuch
Applications in aviation
There is an enormous range of applications in the field of aircraft construction and aviation – this also became clear at Formnext 2024: Metal components of turbines, structural elements, distributors and much more were exhibited on numerous stands. EOS presented a range of components for various AM users in the aerospace sector, including a miniature jet engine printed in 118 hours from nickel alloy IN718 with support-free overhangs of less than 35 degrees. Plastic applications were no less numerous and ranged from decorative vases for business class cabins to air ducts and caps for armrests.
3D-printed drones and their housings were also clearly in evidence at Formnext 2024, although this is certainly a specialized sector of aviation which has requirements that differ completely from the construction of airplanes. Drones are all about efficient production – intelligent designs, for example, ensure that numerous drone bodies can be stacked on top of each other and printed in one construction job.
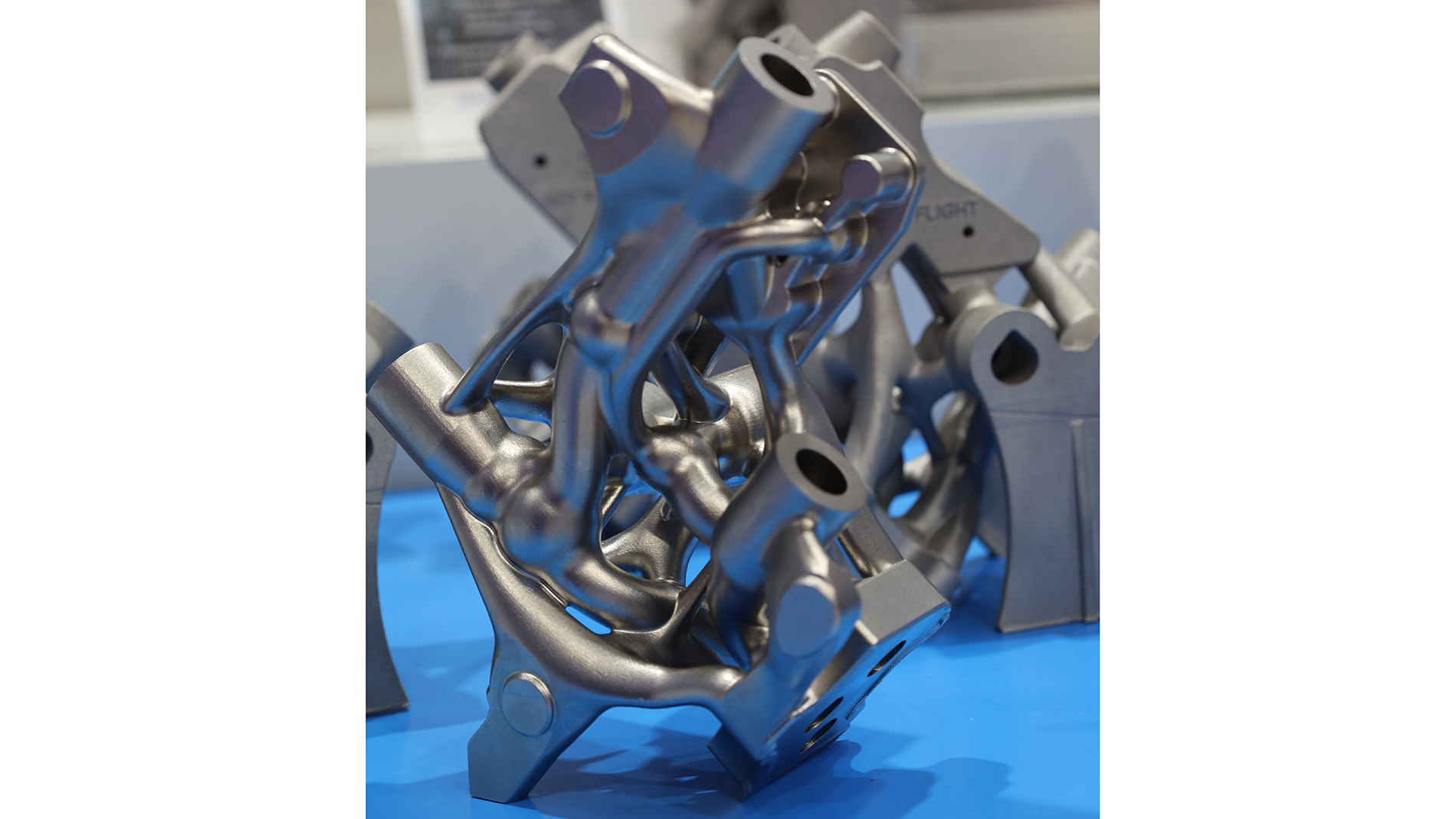
A manifold made of Ti6Al4V that was developed by Airbus and manufactured on an M2 Series 5 machine from Colibrium Additive. Image: Thomas Masuch
At the same time, new technological developments and materials are also opening up new business opportunities. The AM Craft start-up, which presented its interior solutions at the Stratasys stand, specializes in procuring spare parts for aircraft. If, for example, interior components on individual seats are damaged, the seats may have to remain unoccupied. And sometimes airlines have to reorder entire sets even though they only need one component. This is not only expensive but also time-consuming. At Formnext, Stratasys presented a solution that allows airlines to print the components they need themselves or purchase them from certified service providers. Stratasys supplies the machine and the material and helps with the certification of the process.
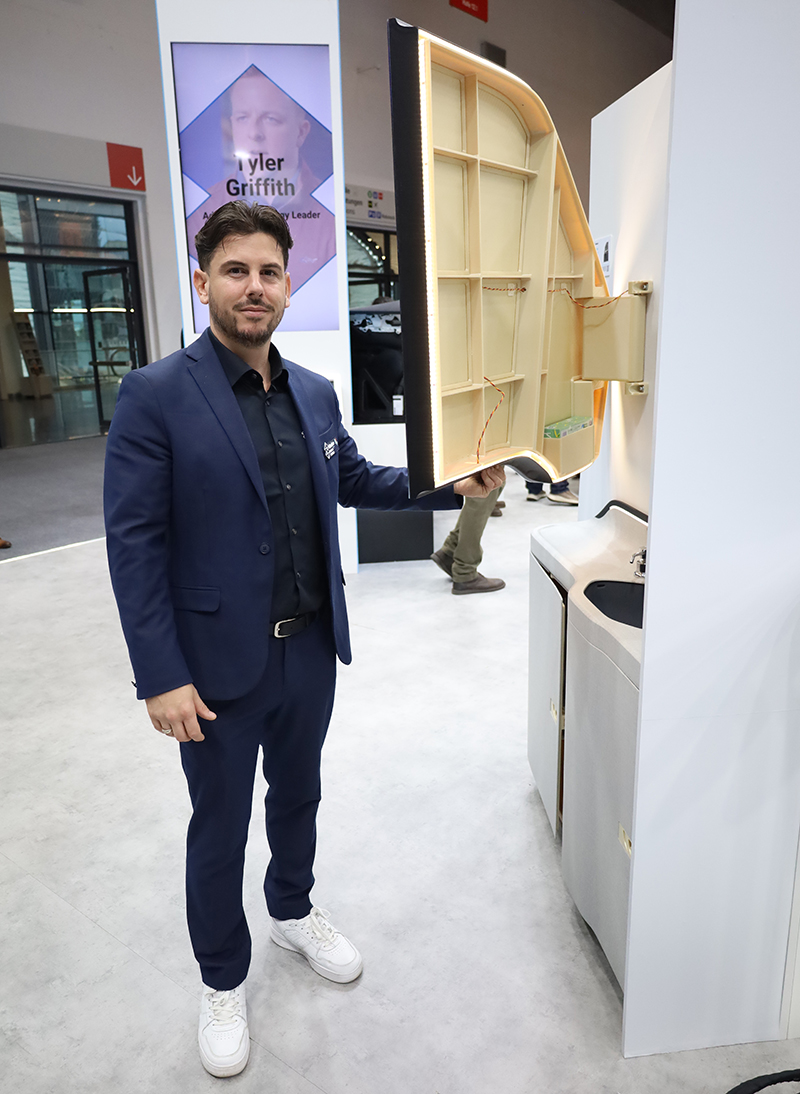
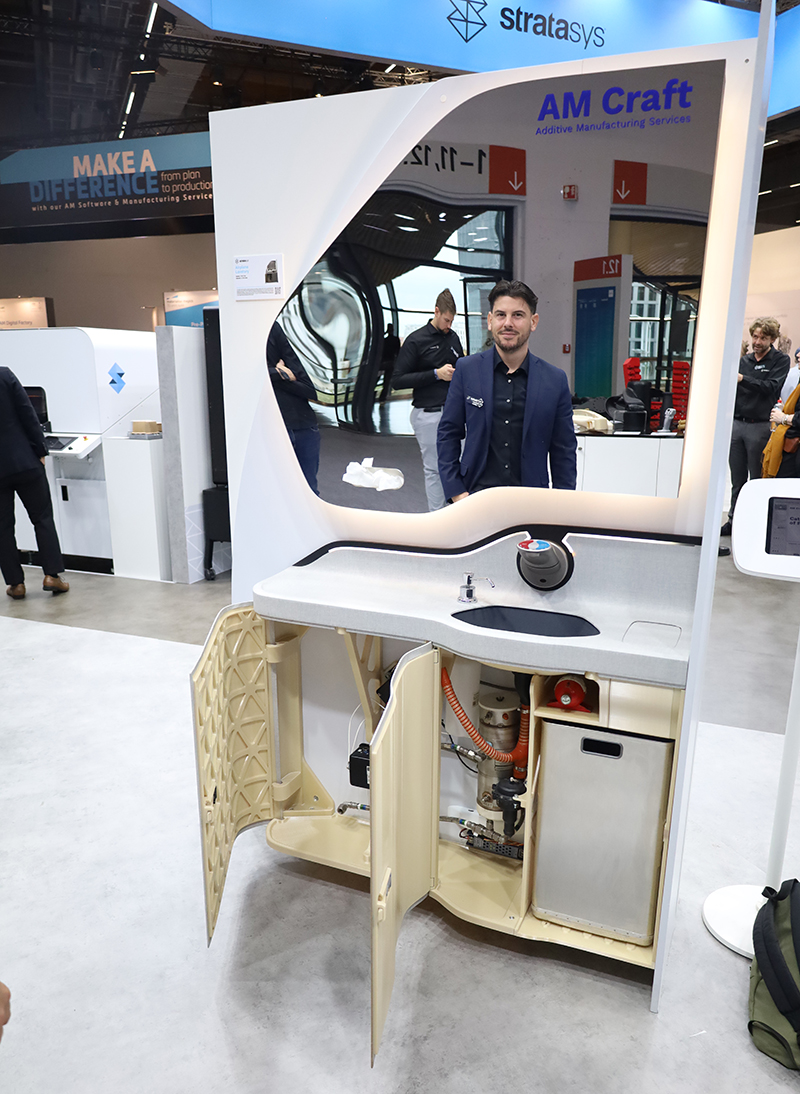
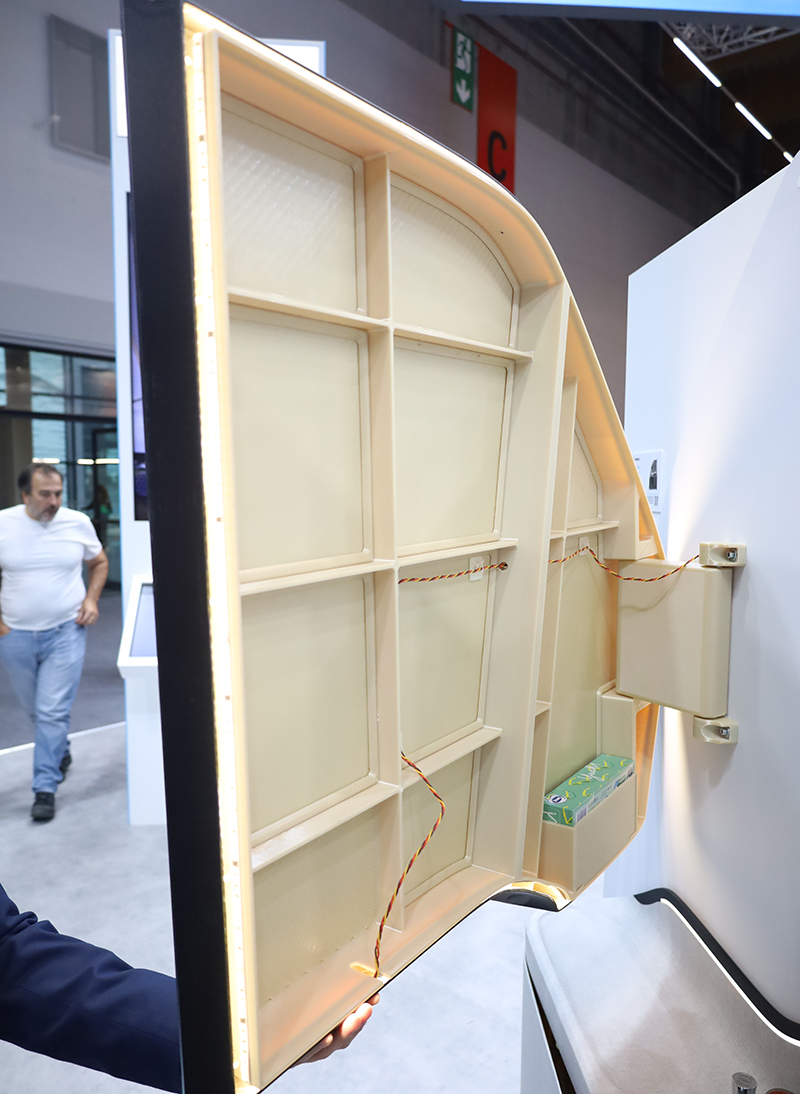
Maxime Borreca, Sales Manager France & KAM Aerospace EMEA, shows a 3D-printed aircraft interior from AM Craft at the Stratasys stand at Formnext 2024. Images: Thomas Masuch
Chinese manufacturers crowd the market
Chinese AM manufacturers are making great efforts to position themselves as system suppliers or development partners for important users and suppliers in the aerospace industry. For example, BLT proudly presented an O-ring seal that was printed on a BLT-S400 and is used in the Airbus A330.
Western industry insiders reveal in confidential discussions that some Chinese manufacturers are so committed to entering the market that components are offered at prices below the cost of materials or that the manufacturers themselves bear the entire costs of development.
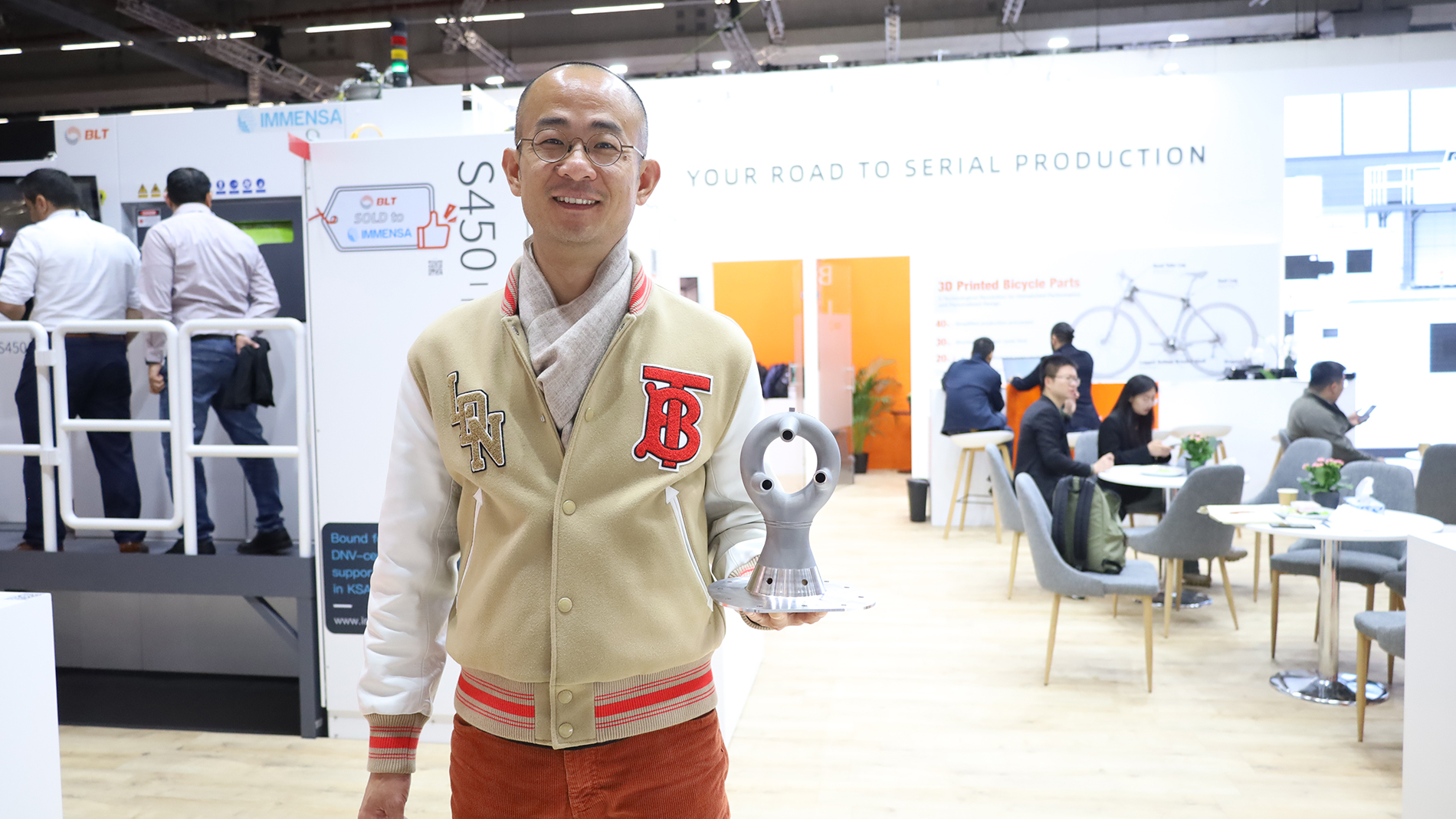
Gary Ding, Managing Director BLT Europe proudly shows the O-ring seal. Image: Thomas Masuch
Challenges and outlook
One of several indications that the aerospace sector offers excellent business opportunities is the fact that Sintavia, one of the major AM contract manufacturers, invested a further USD 25 million in its already extensive and modern production facility in Florida in 2024.
However, the fact that not all of the potential in the industry is being exploited is also due to the bottleneck of post-processing. Although there is sufficient plant capacity at Airbus and its suppliers, post-processing is prescribed and regulated for quality assurance purposes.
"It takes a lot of time and special processes, some of which are only available externally, to process printed parts ready for installation. The processes include heat treatment, non-destructive testing and surface finishing. Usually these are specifically required only for additive components, which makes it less attractive to offer this expertise. This is why there are only a few suppliers for the industry, some of whom have hardly any aviation experience," explains Jan Roman Hönnige, who is responsible for Manufacturing Engineering DED at Airbus.
EASA sets very high requirements for certification, which can make it difficult for smaller AM or testing service providers to comply with the internal requirements and those of the authorities.
The demands that a company like Airbus makes on the further development of additive manufacturing are also based more on practical considerations: "To increase the footprint, we don't need any specialization of the technologies, any special solutions for individual components or any development of special new materials," says Hönnige. "We need a harmonized supply chain that understands our challenges and certification processes, otherwise we are solving problems that are not at the top of our list. This calls for strategic decisions and better communication."