Text: Thomas Masuch
In his job, Norbert Gall has adopted a modesty that is quite unusual for his position: As head of marketing at Lithoz, a specialist in the 3D printing of ceramics, he encounters new, highly innovative development projects and applications practically every week. But he can only use a few of them for his work. “Unfortunately, we are not allowed to show most of them, as we have usually signed NDAs,” Gall explains. Indeed, he and his team are delighted when he is allowed to bring one in perhaps 20 applications into the public eye.
One such application was ceramic filter membranes for lithium production, which the company presented to international experts for the first time at Formnext 2024. The British company Evove, which specializes in filtration technology, produces the membranes on a CeraFab S320 from Lithoz and stacks them into modules one meter in length. Thanks to improved designs, Evove expects the ceramic membranes to deliver higher performance and a longer service life for the filter elements.
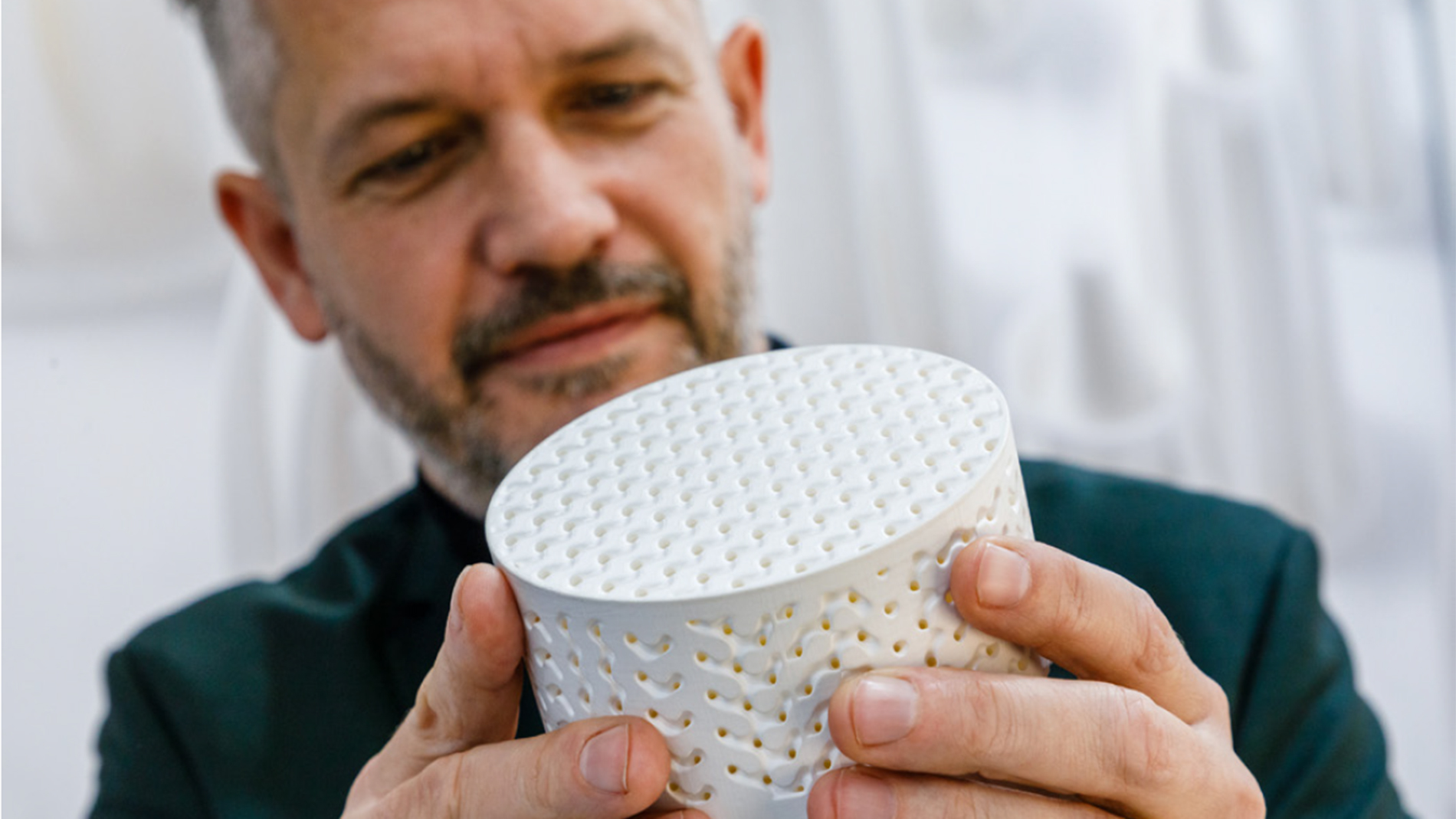
Norbert Gall presents a filter membrane 3D-printed by Lithoz at Formnext. Image: Mesago / Marc Jacquemin
The fact that only a few applications from the field of ceramic 3D printing have seen the light of day reflects the sensitive situation in which the young and still relatively small industry finds itself. The technology offers such great potential that many users are looking into it; they are building up expertise and seeking to gain a technological edge. At the same time, the process is complex and developing new applications is often laborious and time-consuming. “Our industry is a delicate plant that needs to be nurtured over the long term,” Gall says. “The potential is truly endless, especially when you consider that there are certainly many sectors and industries that have yet to discover ceramic 3D printing,” adds Kareen Malsallez, marketing manager at 3DCeram Sinto, another renowned manufacturer of ceramic 3D printing systems.
Evove stacks these 3D-printed ceramic membranes into modules one meter in length. Images: Mesago / Marc Jacquemin (2), Thomas Masuch
The technology
What often stands in the way of simple applications is the rather complex production technology. “Ceramic is a complex material that requires a great deal of expertise. It is not necessarily difficult to shape; the challenge lies in firing,” Malsallez points out. As with most other manufacturers of ceramic 3D printers, 3DCeram Sinto's SLA technology is based on a three-stage process in which a ceramic blank is first created, then debinded and fired at quite high temperatures in the third stage. The SLA process is a top-down stereolithography in which a ceramic slurry, which also contains a light-sensitive polymer, is exposed to a laser and partially solidified. The additives are removed in a second, thermo-chemical process. The rather fragile ceramic green bodies are then placed in an oven and baked at 1,000 to 2,000 °C. In Lithoz’s lithography-based ceramic manufacturing (LCM), on the other hand, the slurry is exposed using light projectors, which means that the technology can be classified as digital light processing (DLP). Basically, the three-stage manufacturing process causes the components to shrink by around 3–30 percent, which must be considered in their designs.
The mass production of ceramic components was another trending topic at Formnext, as D3-AM (left) and Lithoz (aerospike nozzles at right) demonstrated. Images: Mesago / Marc Jacquemin
Even though manufacturers such as Lithoz assure that shrinkage is “very well controlled via important parameters”, the entire process of 3D-printing ceramics is “even more complex than metal 3D printing”, according to Nobert Gall. “The thermal processes of debinding and sintering in particular require a great deal of specialist knowledge.” To obtain the necessary knowledge, Lithoz customers can request a one-week training course in Vienna after purchasing a machine. “This is an absolutely key moment in the customer relationship,” Gall continues.
Customers' AM knowledge has grown
The international technology company Bosch has used its decades of experience in the conventional production of ceramic components to offer additively manufactured components, as well. Since 2016, Bosch Advanced Ceramics has been establishing a division that focuses on the industrial production of ceramic components at the company’s Immenstadt site in southeast Germany. The division operates as a start-up under Bosch's own business builder, Bosch Business Innovations GmbH, and uses systems from 3DCeram Sinto and Lithoz in combination with a specially developed process monitoring system.
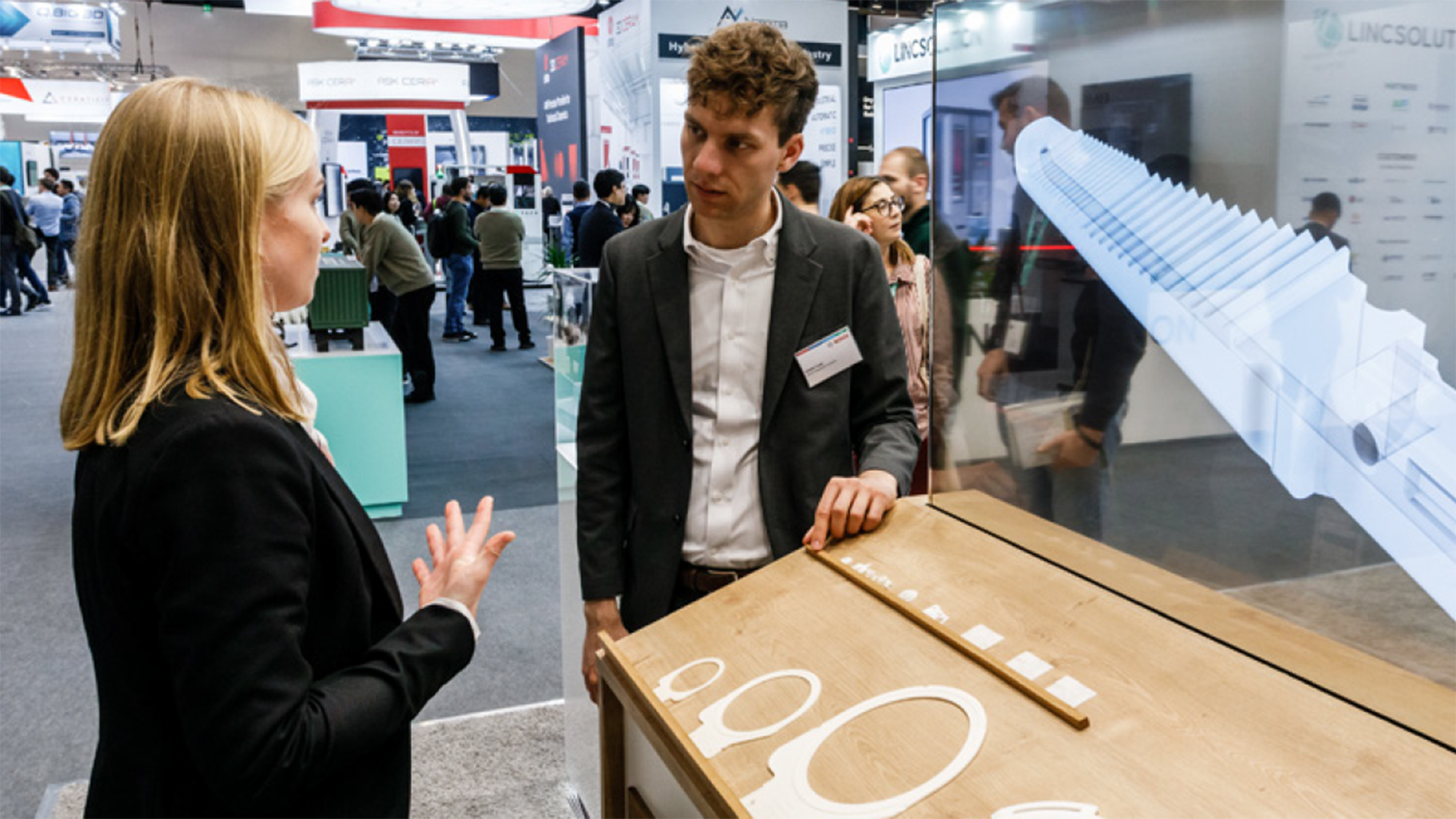
Many interesting discussions took place at the Formnext 2024 booth of Bosch Advanced Ceramics, whose large ring blades see use in handling wafers in the semiconductor industry. Image: Mesago / Marc Jacquemin
“The complex process is difficult to master, which is why our customers like to make use of our service to benefit from the advantages of ceramic 3D printing,” explains Sabine Tulachan, who is responsible for marketing at Bosch Advanced Ceramics. Its customers come from the semiconductor, aerospace, adhesives, and medical technology sectors, among others.
Knowledge of the possibilities of additive manufacturing has generally increased, as Tulachan reports. “There are projects where the customer already knows exactly what they need. But there are also projects where we work together on design optimization in order to fully exploit the advantages of additive manufacturing.”
At Formnext 2024, for example, Bosch Advanced Ceramics presented a sleeve 3.5 mm thick with a wall thickness of just 0.09 mm, which reduces and improves the size of medical devices. According to Bosch Advanced Ceramics, the sleeve was developed in five months. In total, Bosch Advanced Ceramics now produces up to 50,000 such sleeves per year.
The players
Lithoz is one of the veterans of ceramic 3D printing. Founded in 2011 by Dr. Johannes Homa and Dr. Johannes Benedikt, the company has around 150 employees and is still owner-managed. While it does not want to disclose the exact number of systems it has delivered to date, Gall says it is well into the three-digit range. He adds that Lithoz has “reached a critical mass” that is now enabling the company to approach the industry with reliable quality guarantees and offer systems for series production.
3DCeram Sinto has also been in business for many years. Founded in Limoges (France) in 2001, the company was originally active as a service provider – supplying 3D-printed implants to the hospital in Limoges, for example, which, according to Kareen Malsallez, “are still in place today”. Its business model was later changed in 2017, when 3DCeram began developing and selling systems for the entire additive manufacturing process for ceramics. At the same time, Japan’s Sinto Group became its main shareholder, with company founders Christophe Chaput and Richard Gaignon retaining shares in the company.
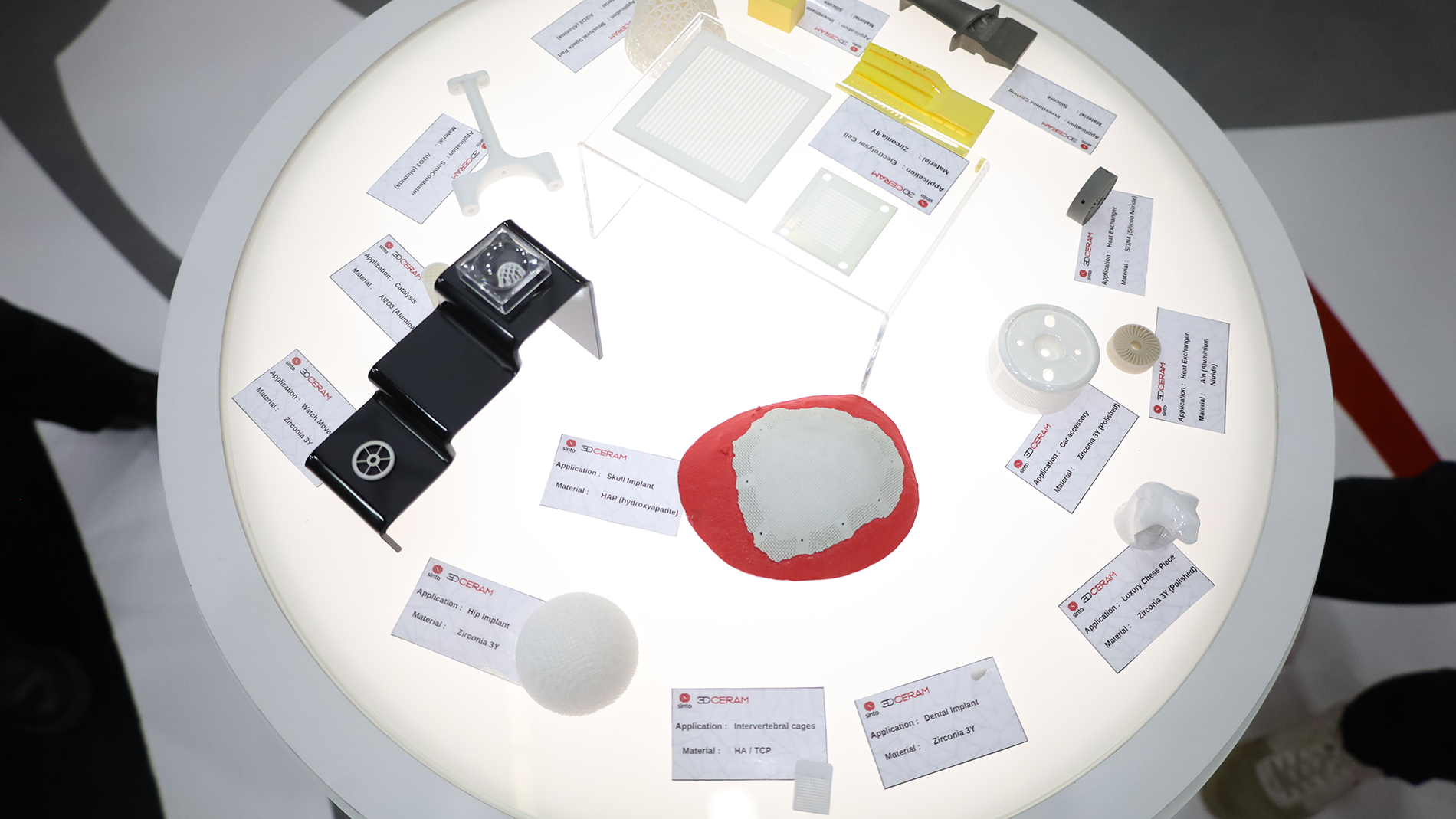
3DCeram Sinto presented applications from various industries at Formnext 2024. Image: Thomas Masuch
As the industry grows, more and more players are emerging. A few years ago, the Durst Group from Brixen (northern Italy) founded the subsidiary D3-AM GmbH, which presented its LABII printing system for micro particle jetting for the first time at Formnext 2023. Other companies, such as Amarea (a spin-off of Fraunhofer IKTS), Concr3de, ExOne, Nano Dimension (and its subsidiary Admatec), Voxeljet, WASP, and XJet, also offer printers that can be used to process ceramics. In addition, material suppliers such as the French company Nanoe SAS enable the FFF printing of ceramic blanks with special ceramic filaments.
Furthermore, the number of service providers is growing steadily. Steinbach AG and the US company Sinaptic, for example, have specialized in ceramics and use LCM technology from Lithoz. Service providers such as CADdent and the Japanese company Yugyokuen have also included ceramic 3D printing in their technology portfolios.
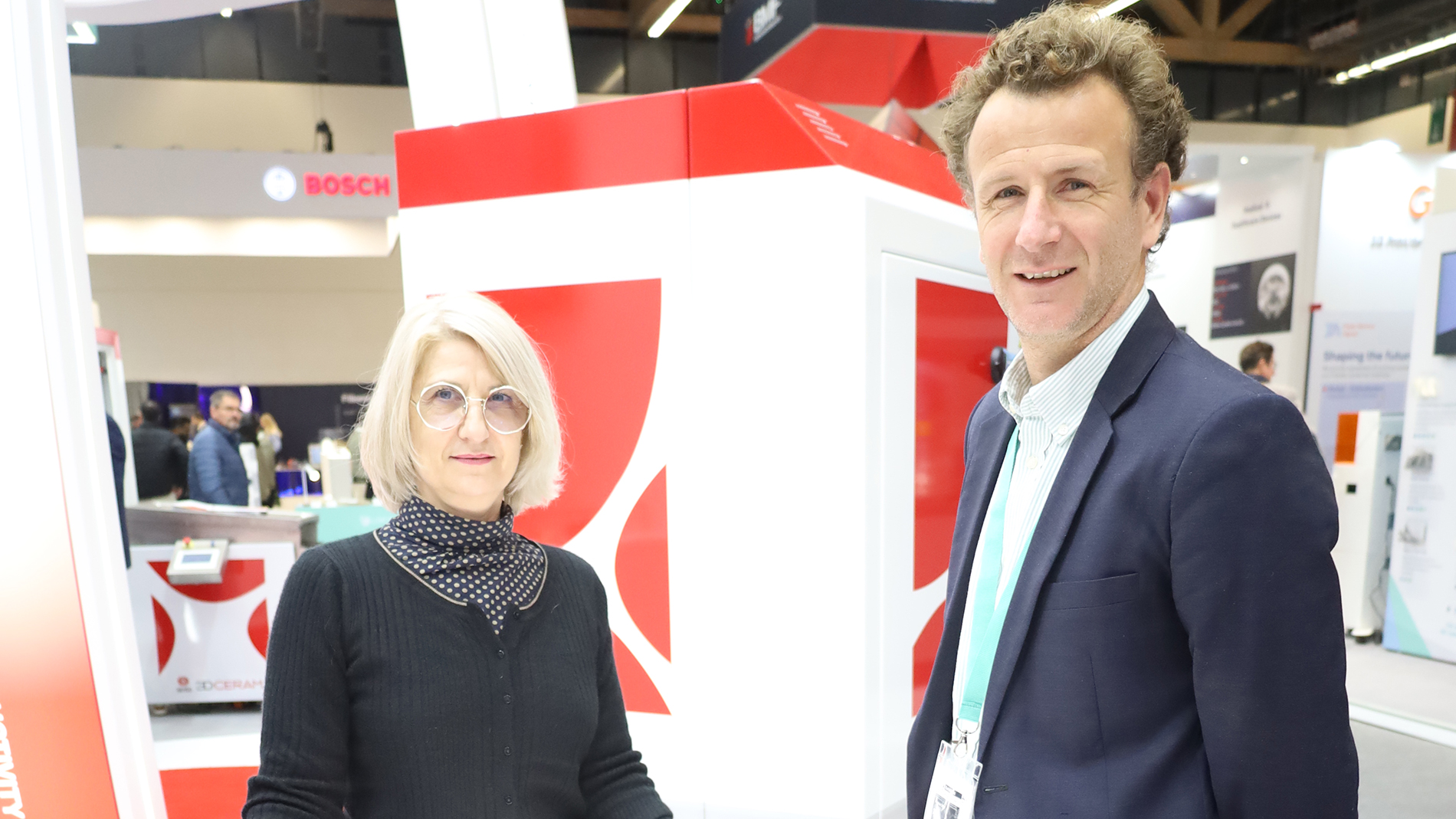
Kareen Malsallez and Arnaud Roux from 3DCeram Sinto presented applications from various industries at Formnext 2024. Image: Thomas Masuch
For large system manufacturers such as Lithoz, qualified service providers play a very important role in spreading the technology. On the one hand, they often have machine parks of often five to seven systems, which makes them good customers that account for the majority of machine sales. At the same time, these service providers pave the way for the technology to become even more prevalent, as it is very rare for production companies to start out with their own ceramic 3D printing systems. “You don't have to buy a printer straight away if you only need a small series,” explains Norbert Gall. To make it easier for users to get started with ceramic 3D printing, Lithoz has set up the Ceramic 3D Factory – a network of contract manufacturers that includes Bosch Advanced Ceramics, Steinbach, CADdent, Sinaptic (USA), and the two Japanese companies Mitsui Kinzoku and Yugyokuen.
Applications
Once the technical hurdles have been overcome, ceramic 3D printing will open up an enormous field of application. Here, the industries that are currently important to Lithoz are those that also play an important role in other areas of additive manufacturing:
- Medical technology: e.g. micro surgical devices with various functions (drills, probes, light channels, tubes for suction or tissue removal)
- Space: e.g. small nozzles for satellites, sensors and receivers (made of dielectric ceramics)
- Aviation: cast cores for turbines in which AM enables ever finer cooling channels, leading to better cooling of the turbines and ultimately lower fuel consumption
- Semiconductor industry
- New energies
- Heat exchangers (found in many branches of industry) – here, Norbert Gall describes aluminum nitride is “the star among heat exchangers” due to its high electrical insulation and optimal thermal conductivity
- Automotive industry: another area in which ceramics are an important topic for many OEMs, although the applications are not published
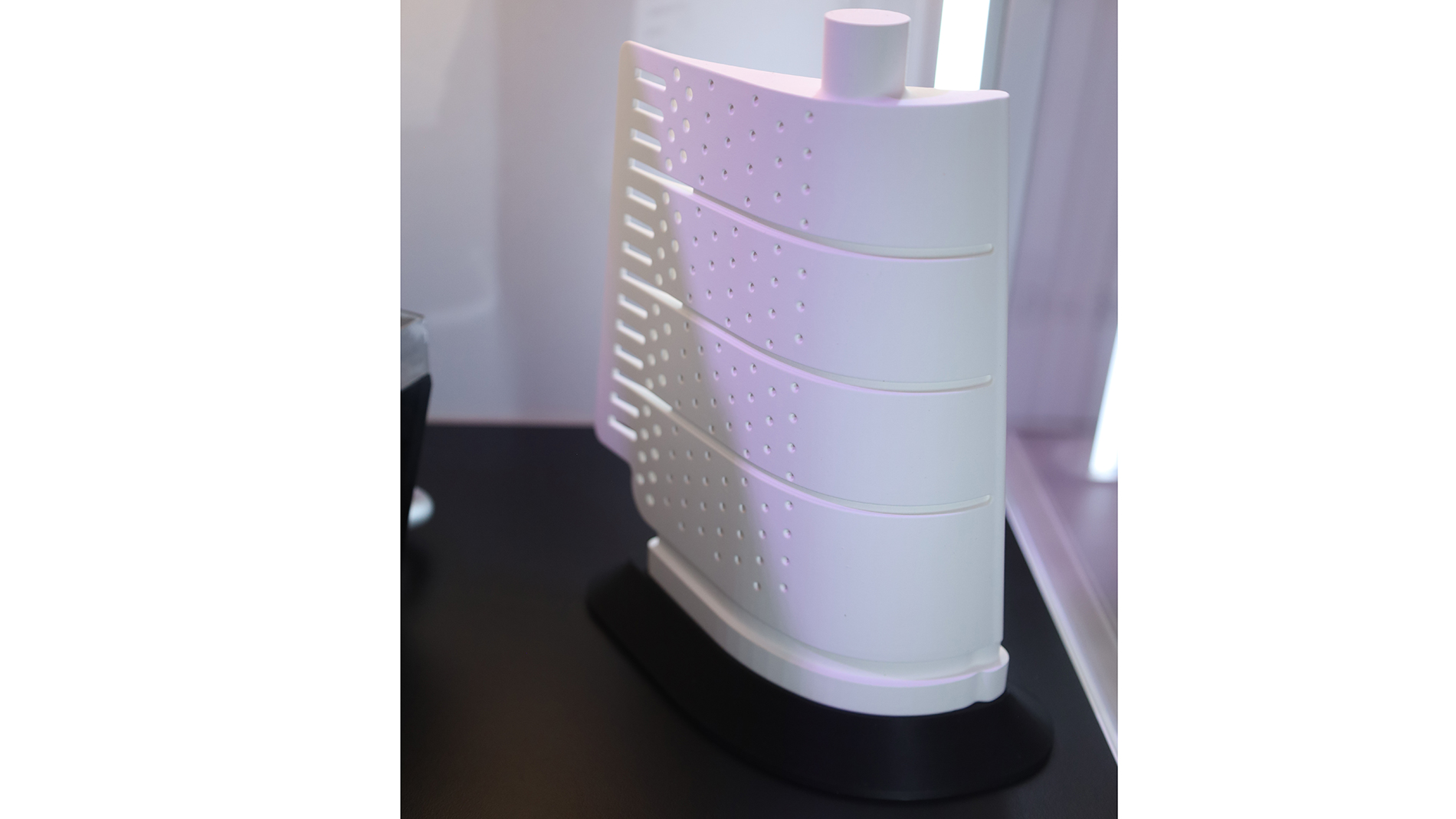
In the aviation industry, cast cores for turbines are 3D printed which allows ever finer cooling channels. Image: Thomas Masuch
The decisive factor here is that ceramic 3D printing creates real added value, as the complex production process does not necessarily make the components cheap.
Meanwhile, 3DCeram Sinto presented a promising project for the hydrogen industry a few weeks ago. The company has developed its latest, most highly automated machine, the C2000 Dualmatic, specifically to meet customer requirements for the production of corrugated plates that are components of the SOEC cells used to produce green hydrogen. The system, which was delivered in December 2024, has six lasers, each of which exposes two automatically alternating build platforms measuring 500 x 400 mm. This results in a high throughput that is designed to cover the high demand for ceramic cells. After all, a single SOEC cell requires 70 corrugated plates with internal channels measuring 163 mm x 130 mm and a thickness of a few millimeters.
"This marks the first time that an entire printing process has been fully automated for the mass production of larger components in the ceramics sector,” says a delighted Kareen Malsallez. At the same time, the C2000 Dualmatic machine is equipped with Ceria, an artificial intelligence developed over the past three years by 3DCeram.
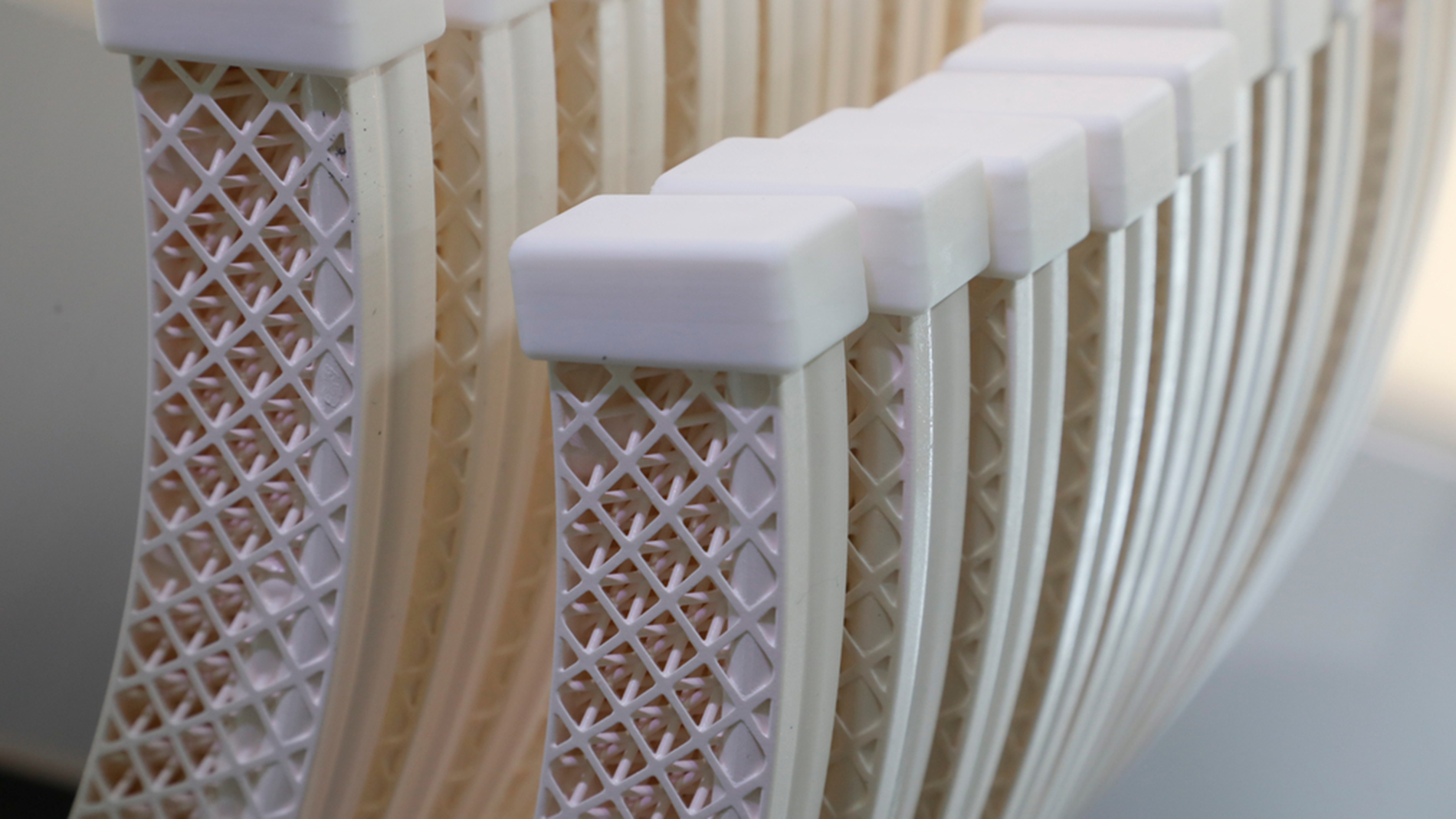
Segments of an atomic layer deposition ring (or gas distribution rings) made of aluminum oxide that Lithoz unveiled for the first time at Formnext. The component's design originally came from Alumina Systems. Image: Mesago / Marc Jacquemin
Hurdles standing in the way
With so many successful applications and rather mature technologies, the question arises as to why the 3D printing of ceramics has not long since outgrown its niche and is still “the little plant that needs careful nurturing”.
“Companies entering the 3D printing of ceramics usually have to overcome a twofold challenge,” explains Nobert Gall. “They’re not only switching from conventional to additive manufacturing, but also from metal to ceramic – a completely new material for many engineers.” Such a drastic change in technology can also be a venture.
In addition, the investment needed is higher than when getting into FFF printing, for example. The costs of the production technology – including sintering, an oven, and corresponding software – are in the six-figure range.
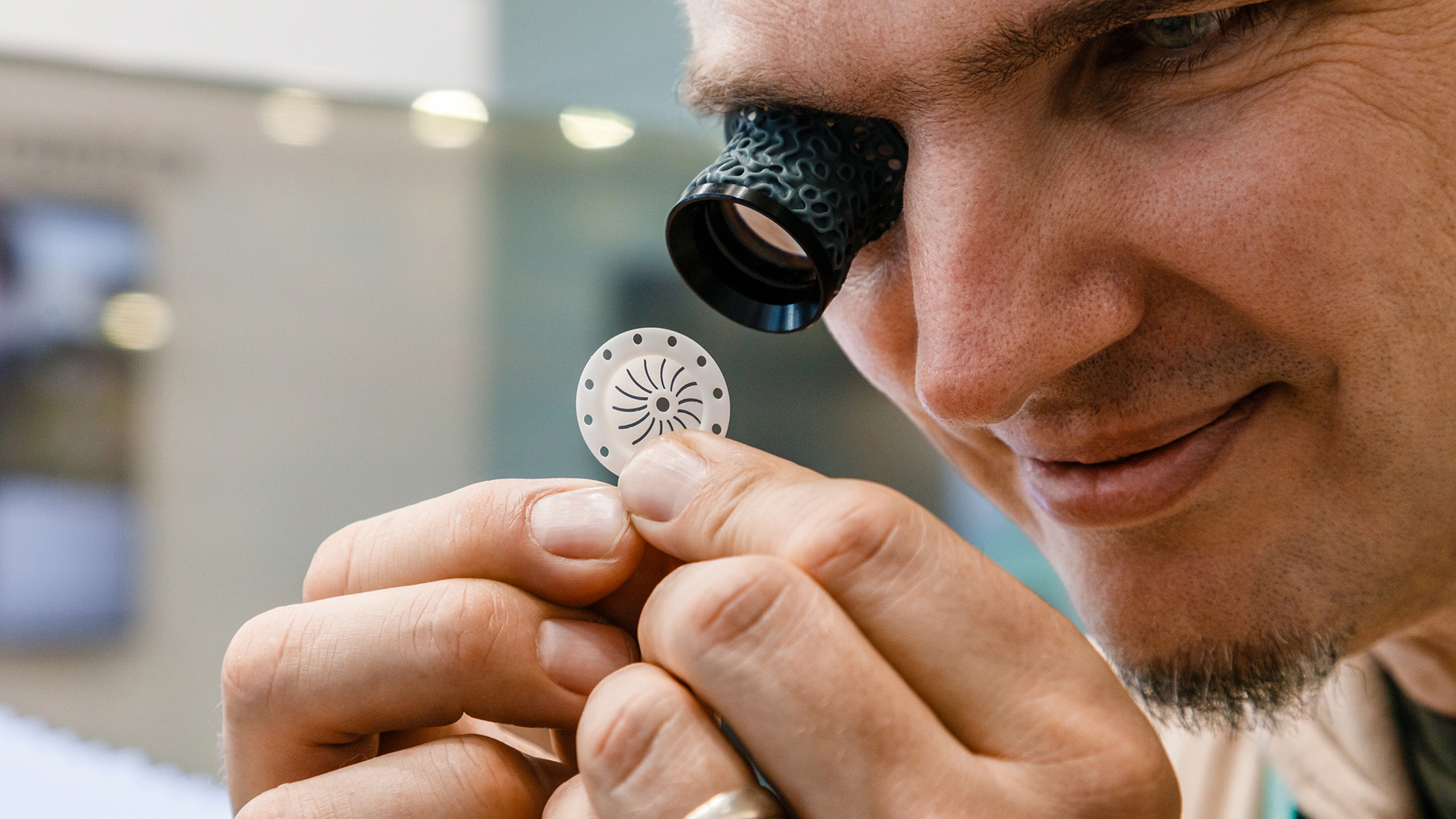
This laser cap from Bosch Advanced Ceramics is designed to protect optical and electronic components from process residue and other contaminants. Image: Mesago / Marc Jacquemin
Outlook and objectives
Overall, the major manufacturers believe their ceramic AM systems are ready for industrial use. “All of our references are real applications, including series production,” explains Norbert Gall from Lithoz. “We have already come a long way here and have covered most of the ground.” At the same time, Gall expects the range of applications to increase significantly over the next few years. “We have our foot in the door of many applications and industries.”
The Austrian company is doing everything it can to put the technology on solid footing. “Our goal is to enable customers to succeed with ceramic 3D printing in the long term,” says Gall, who has also identified some black sheep in the industry. “We have competitors that we really appreciate, but also some that take a less solid approach to projects. If customers are then disappointed because their project was not feasible, they are not only lost to this manufacturer; they usually say goodbye to ceramic printing forever. In that case, nobody benefits at all.”
Overall, Lithoz’s next step will focus even more on series production, and 3DCeram Sinto’s future plans are heading in a similar direction. “We will continue to work on automating the process beyond printing and developing our Ceria AI while doing our best to transfer the technology to industrial players,” says Kareen Malsallez. If the industry continues to develop at such a steady pace, there will certainly be even more real-life applications to report on in the future.