3 July 2023
In collaboration with GKN Powder Metallurgy and HP, John Deere has 3D-printed valves for tractors. It was the company's first additive metal series application.
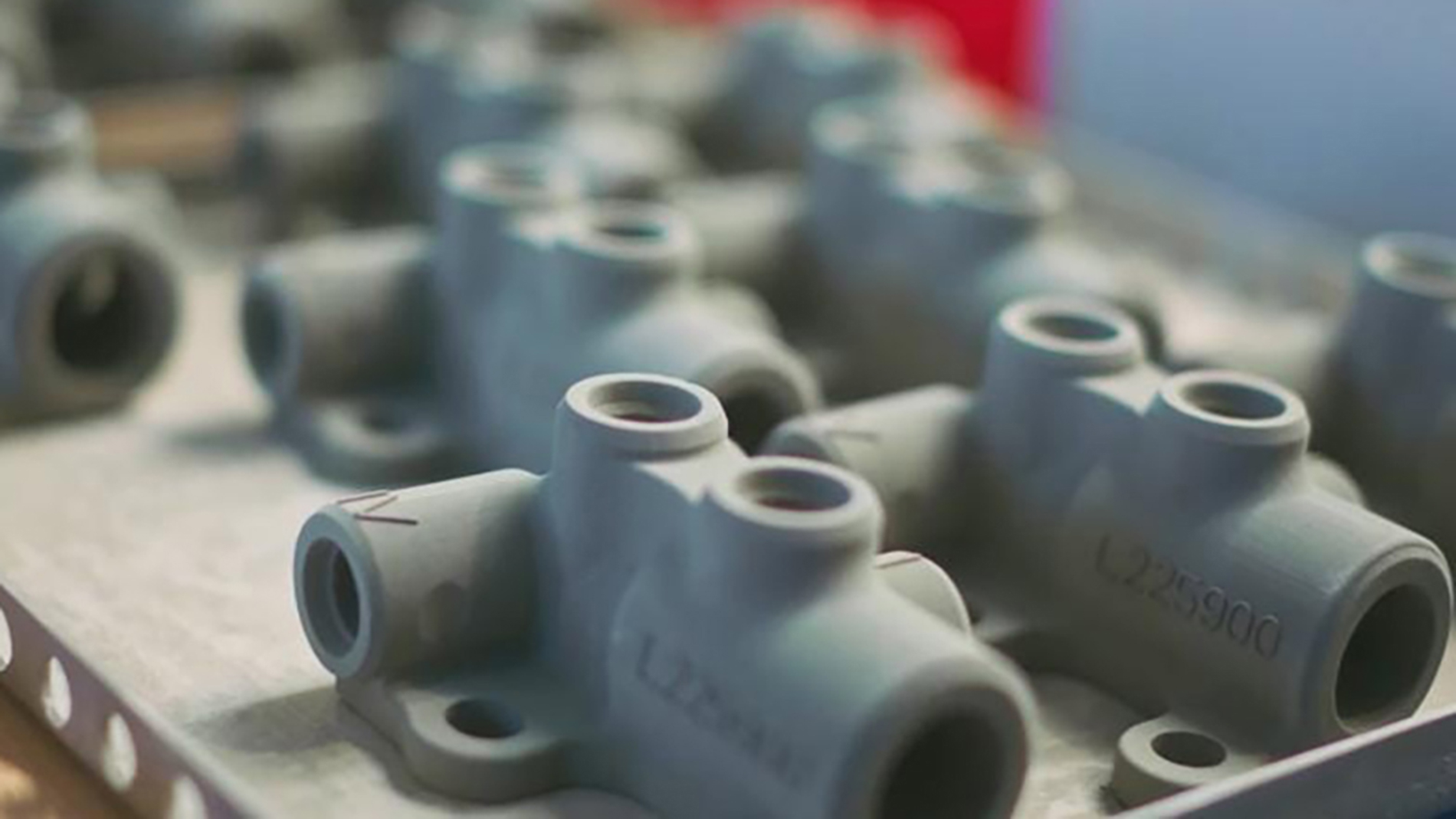
John Deere is the world's leading manufacturer of agricultural and turf equipment. The company is not new to Additive Manufacturing (AM). In fact, John Deere factories across the globe have used AM for years to 3D print thousands of tools, jigs, and fixtures that improve processes and increase ergonomics. In its Mannheim design center for small- and mid-size tractors, however, the company has recently incorporated metals into 3D production. According to Dr. Jochen Muller, Manager of Global Digital Engineering, this marks new territory. “With the new thermal diverting valve for tractors, John Deere goes one step further. It is the company’s first 3D printed metal part going into production.”
As a project partner, GKN Powder Metallurgy GKN Powder Metallurgy has been instrumental in bringing the John Deere valve to fruition, utilizing HP Metal Jet technology. Here, a metal powder is glued together, through a binding agent, layer upon layer until a green part is created. The fragile green part is then sintered in industrial-grade ovens, moving from conventional powder metallurgy to high quality, durable, and tough metallic parts.
GKN is the world's leading manufacturer of powder metal products, delivering 3D printed parts to the automotive and other industries. The product engineers at John Deere and the manufacturing experts at GKN worked closely together to refine and improve the design of the fuel valve for 3D printing. And for HP, too, the valve was a premiere: it is the world's first technical application mass produced with the HP Metal Jet process.
Images: John Deere
The 3D-printed valve is more efficient than a traditionally manufactured version and 50 percent cheaper, significantly smaller and consumes less material. According to Muller, “the thermal diverting valve underwent rigorous testing in order to ensure excellent part quality.” Meanwhile, over 4,000 valves are being shipped from GKN to the John Deere tractor factory for final assembly. In addition, 3D printing delivers a broad range of other benefits: The ability to perform fast iterations and rapid prototyping is essential. Designers can easily test their ideas and verify their concepts at a very early stage within the development process, Muller says.
According to Muller, 3D printing not only has reduced costs per part but has also increased the performance. The thermal diverting valve is the result of a targeted John Deere strategy, “it’s one of many innovative 3D printing solutions to come in the future.”
FURTHER INFORMATION:
Tags
- Automotive
- Additive Manufacturing