by Yejun Fu
After taking home the Newcomer Prize in last year's purmundus challenge, Yejun Fu had the chance to design the trophy for the 2021 competition. The young product designer recently gave Formnext Magazine some exclusive insights into her design and manufacturing process for the award and the trends that have influenced her work.
Project overview
The trophy project started in November 2020 after my adaptive splint project was awarded the Newcomer Prize in the purmundus challenge. At the beginning of the concept development stage, I deconstructed the splint into its constituent elements for inspiration. After comparing several concept models and discussing them with other project members, I decided to use the multi-layer structure to explore the form further. In developing the design, I focused on finding a balance between spontaneous form and pre-planned structures. It was important to realize the form and fine details while ensuring the printability and durability of the model. The whole process was fully supported by the purmundus team and Addmio.
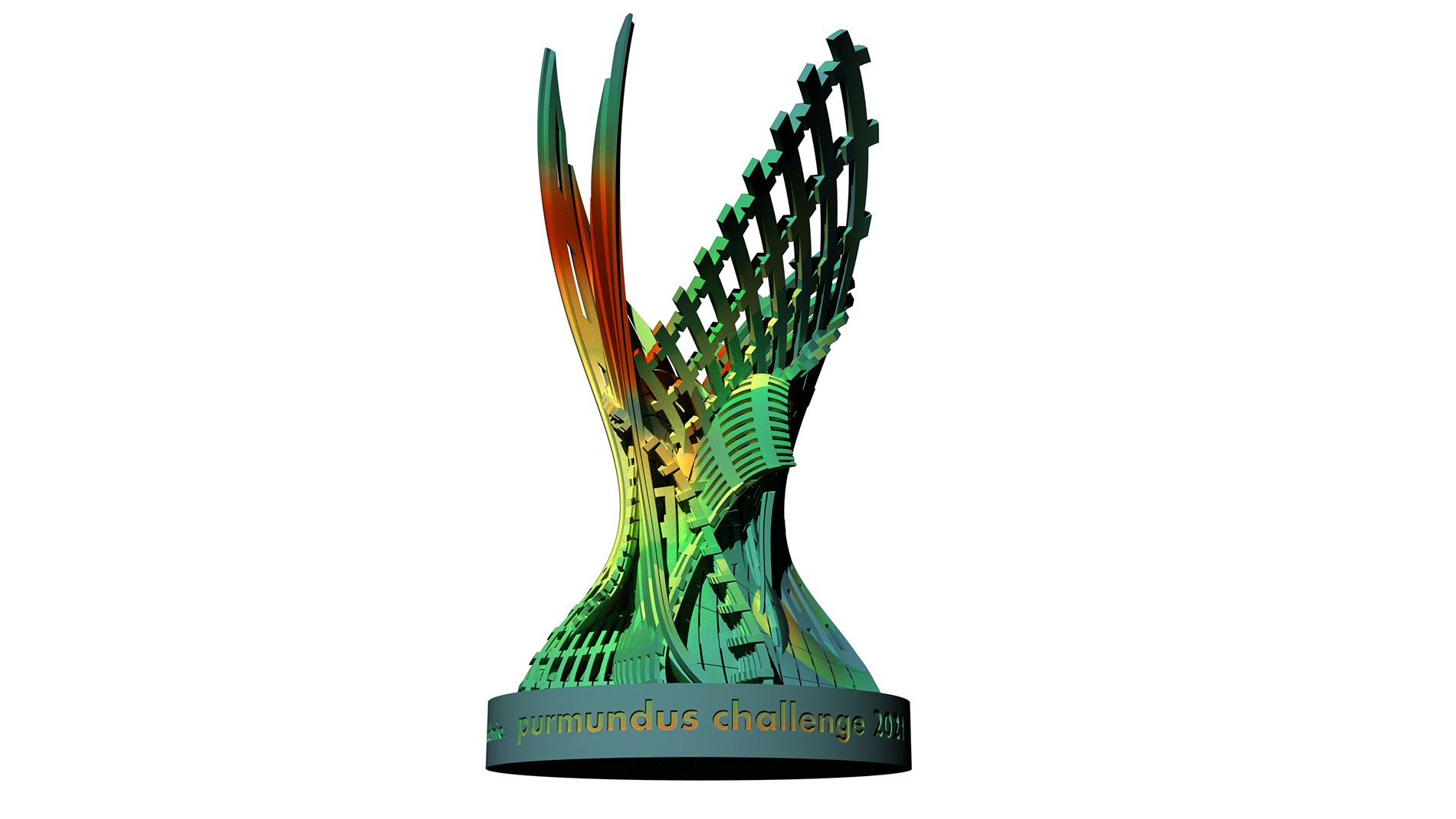
Design
The design of the trophy was inspired by the multi-layer structure of my adaptive splint, which I developed for my master’s project. In that project, I explored the possibility of using 4D printing to build wearable devices based on the example of an adaptive wrist splint for progressive rehabilitation. The splint consisted of three layers with different geometric structures made of three different materials. The responsive material became flexible when stimulated by heat and moisture, while the other materials retained their qualities. The combined effect of the multi-layer structure and the different performance of the materials was designed to enable the splint to adapt to the requirements of a healing body.
Production
HP and Addition came on board when we started planning the geometric prototype printing and color design. One of the challenges we faced was ensuring that after printing and sandblasting, the powder could be fully cleaned from the model. Though none of the layers were solid, it was necessary to add larger openings to the model to get rid of the powder from the central void composed by the densely interweaving layers. We decided to split the trophy into two parts – the body and the base – and add openings to the bottom of the body to let out the powder. We are very happy that we managed to improve the quality of the outcome while staying true to the design.
Adding the fourth dimension
My passion for form exploration using 3D Printing has grown since the first time I used an FDM printer for my undergraduate project. I found this technology so exciting and inspiring because it offered so much more freedom for customization and reduced the limits on product geometry. In my subsequent experiences using different types of 3D printers, I have found more and more advantages in the technology, including its high dimensional accuracy, the ability to respond quickly to modifications, and lower material waste. Using responsive materials, it is also possible to introduce the fourth dimension to 3D Printing technology, namely time.
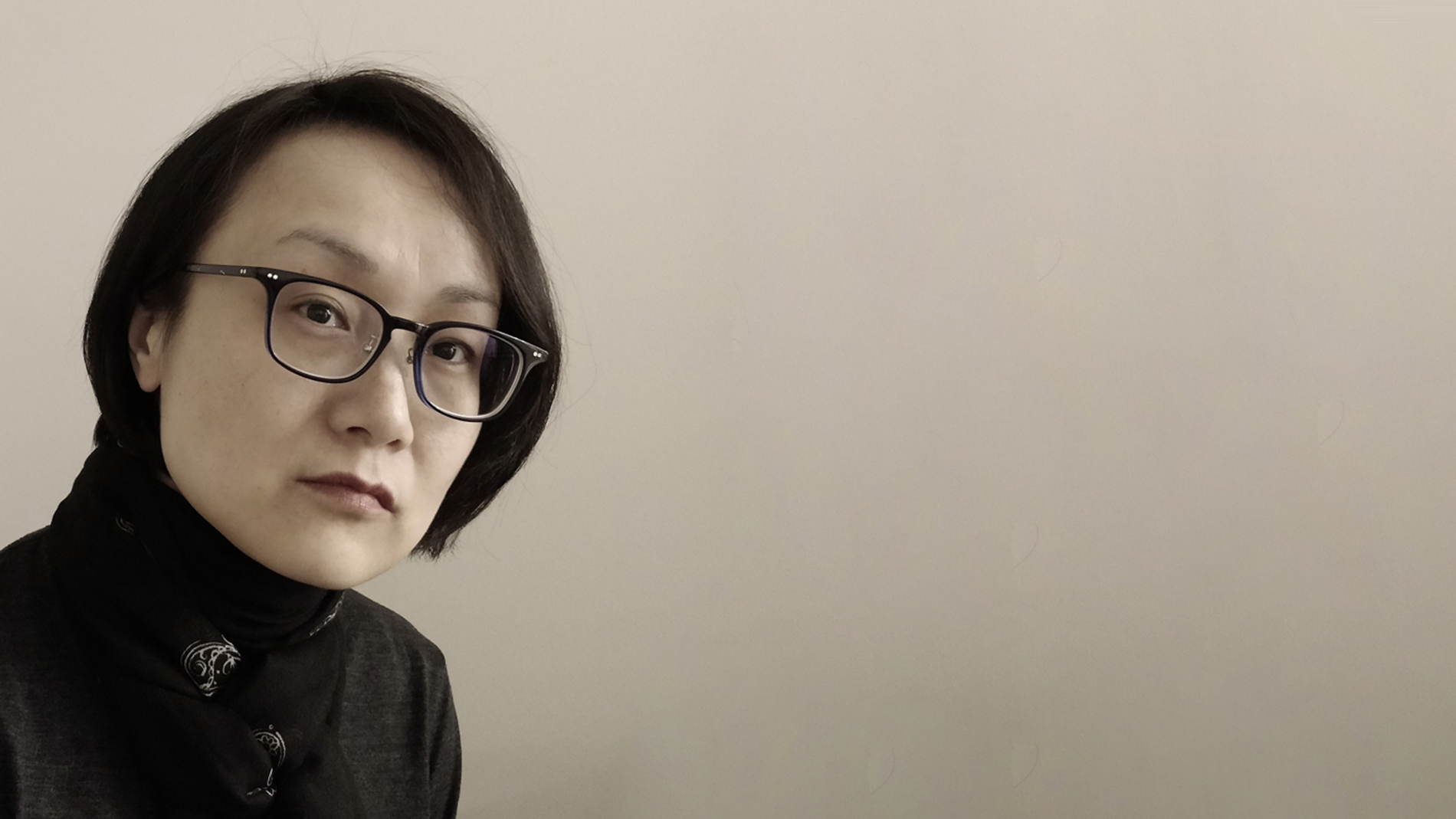
Employing CAD
Another trend that has been influencing my work is the development of parametric design tools and the explosion of online design resources (e.g. open-source software and tutorials on techniques). Parametric design used to be more widely utilised in architecture, but now a number of product designers are also employing this CAD tool. The easy access to these resources has made continual self-education possible and become a source of solid support for designers who want to respond actively to changing needs.
Sustainability
The third major change I have been observing is people’s growing awareness of the importance of improving sustainability. In different stages of an overall manufacturing process, an industrial designer can cooperate with related departments to make reasonable use of degradable/recyclable materials, extend the life cycle of products, and produce less material waste. I feel a responsibility to take these aspects into consideration in my work.
Cross-disciplinary thinking
Last but not least, cross-disciplinary thinking has become especially important in the design of highly functional products. This trend inspires people to think outside of their areas of specialization and encourages effective cooperation among professionals in different fields. When I was doing my adaptive splint project, I worked alongside material scientists from the National Science Challenge and studied the medical materials provided by the clinicians from Wellington Hospital. Their input was essential to the project; in fact, the research on new materials and wound healing processes was the ground on which my design was built. This experience made me more certain of the profound value that lies in always being ready to learn from and be inspired by others.
FURTHER INFORMATION:
purmundus-challenge.com
Tags
- Additive Manufacturing