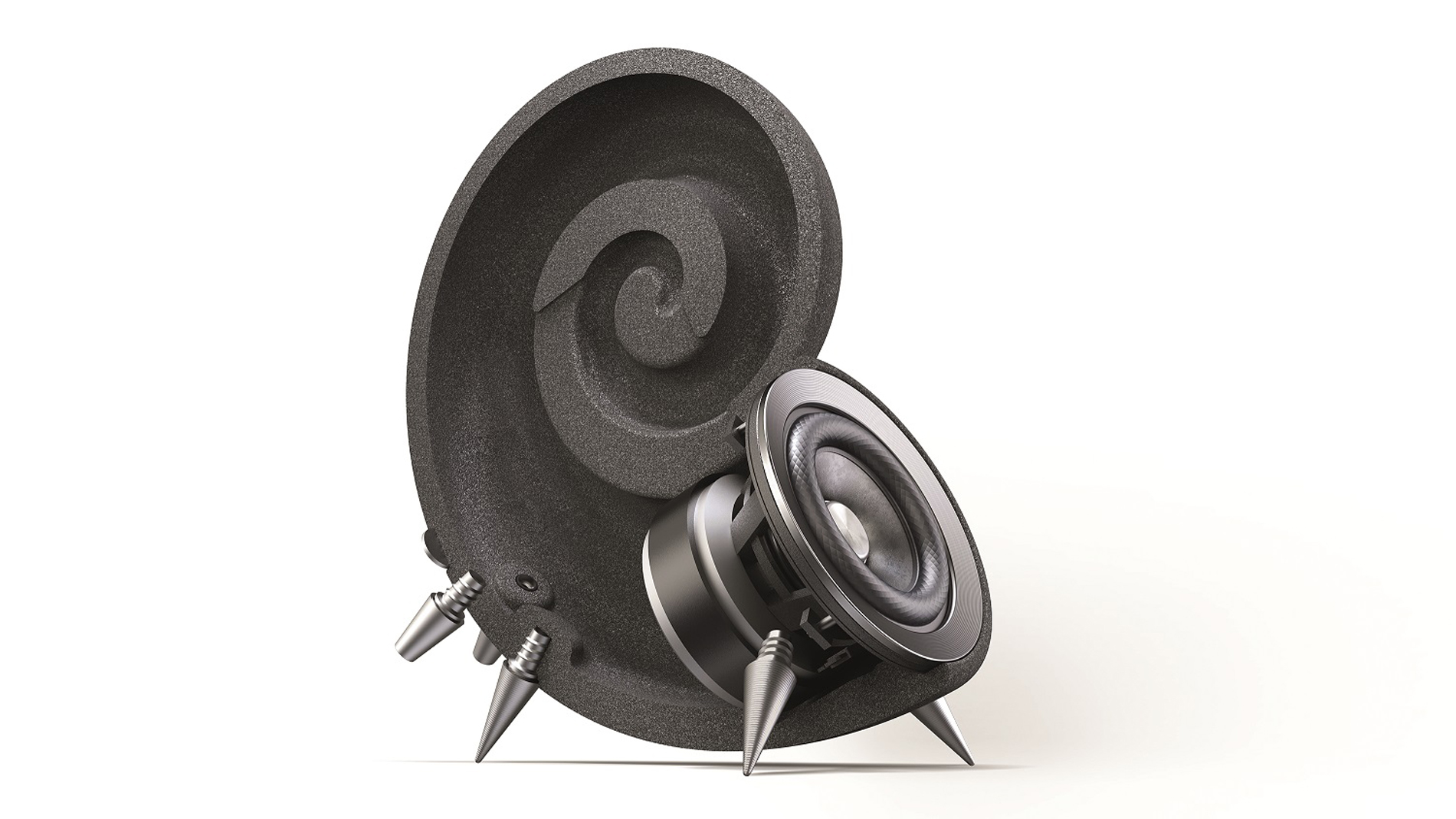
It started, as many creative revolutions do, with a problem. “I’m a designer, a creative,” says Ondrej Chotovinsky, Founder of Deeptime Audio, “so I spend a lot of time working at my desk listening to music.” There are a few items you will find on every creative’s desk: a computer, a large monitor, and speakers. The problem, however, was that music fans faced a choice. Standard PC speakers are compact but generally have poor sound performance. On the other hand, professional sound equipment like studio sound monitors are large and expensive. And neither of these options offer the visual appeal of something designers want to have on their desk.
The quality of a speaker’s sound is not just determined by the electronics built into it, but by the acoustic properties of the casing the electronics are housed in. Traditional speakers are made of sheets of MDF or plywood. With the added strength of a box-shaped construction, the finished case is stiff and airtight to reduce vibration and create a resonant chamber behind the speaker membrane.
But what if you don’t want your speakers to be box-shaped? This was the start of an eight-year quest for the perfect speakers, made possible by an innovation that is revolutionizing the creative industry: 3D Printing. “We started with 3D Printing in plastics,” says Chotovinsky. “They looked fantastic, but the sound wasn’t that great.” It’s a logical place to start – 3D printed plastic can be used to build more interesting shapes, but the material is light and not particularly rigid. This is a problem for sound quality since an unstable speaker cabinet will cause adverse resonances.
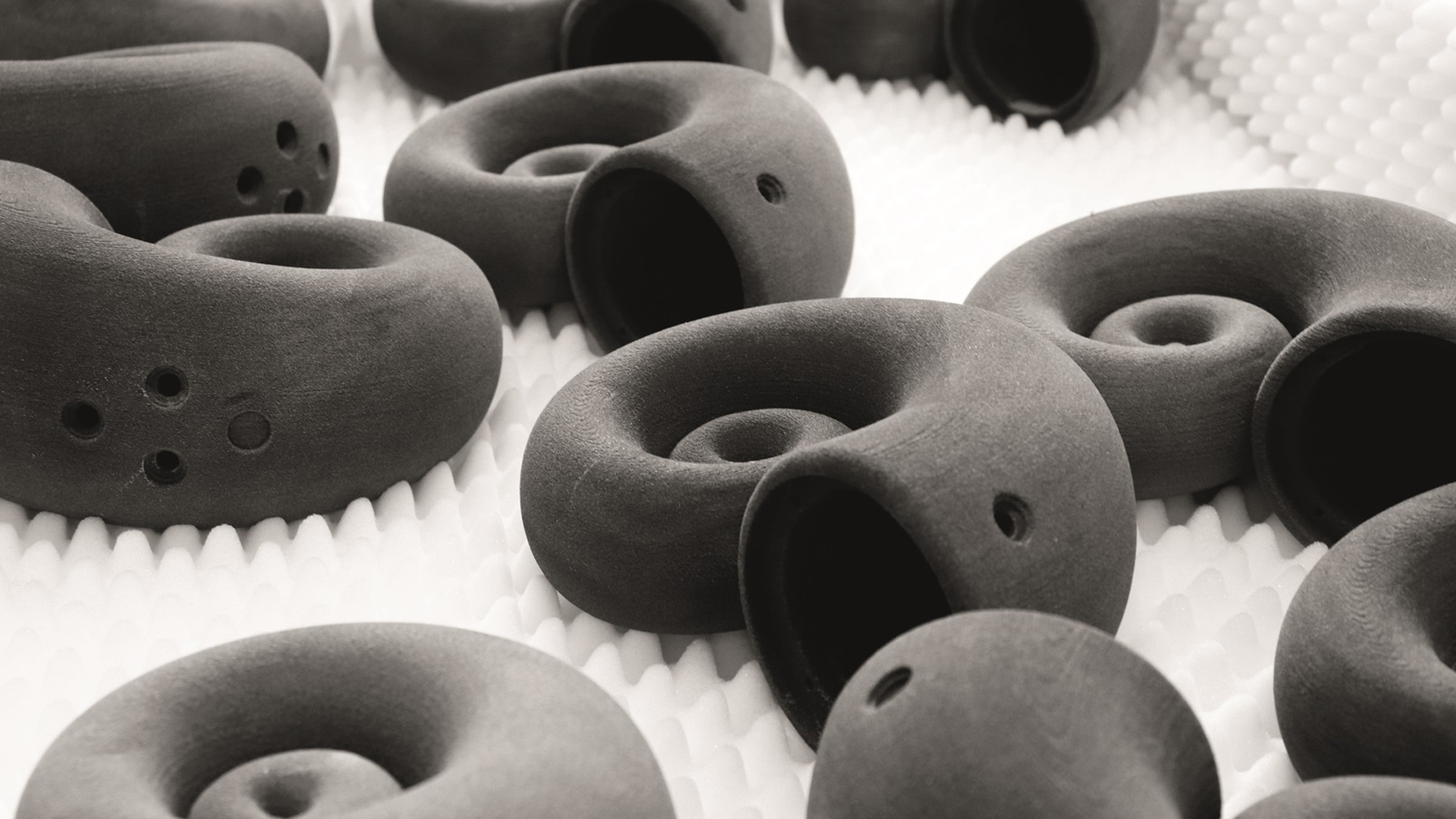
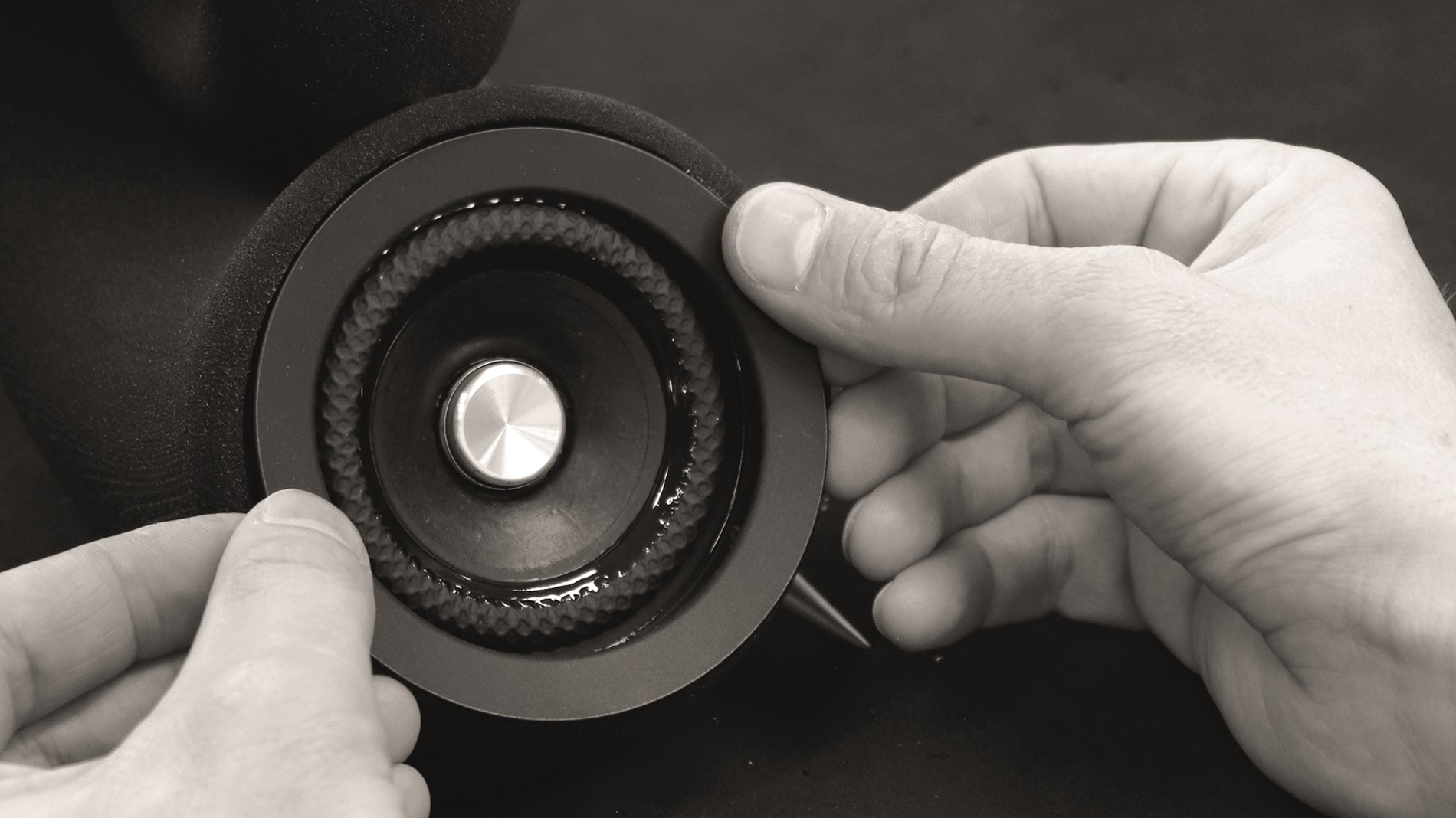
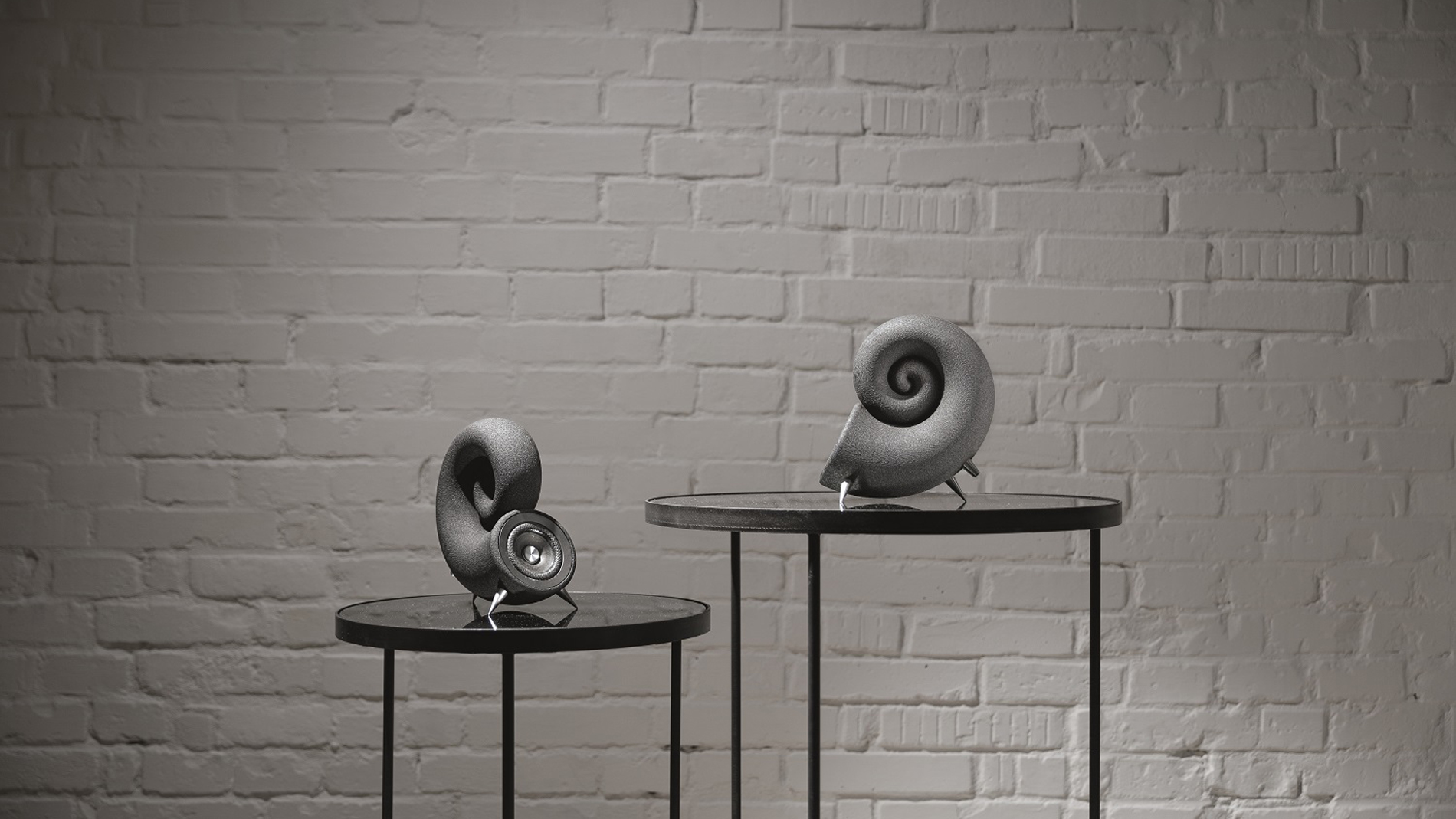
The breakthrough came when Chotovinsky discovered 3D sand printing at ExOne. By using their binder jetting process, the first printed objects were made from a combination of sand and adhesive.
The prints this method produces are heavy and stiff, but porous, which is not ideal for acoustic applications. Speaker cases need to be airtight, to produce a clean sound free from distortion, so further processing would be necessary to the sand forms.
A curing process over two months
After years of experimentation Deeptime had found the perfect solution. Now, the raw housing is printed at the ExOne Adoption Center in Germany and shipped to the Deeptime facility just outside Prague, arriving seven days later. In the course of the manufacturing process the prints are cleaned and repeatedly dipped in a proprietary solution that impregnates the porous sand structure. A slow curing process over two months ensures that the material hardens and the housing is airtight and dense.
The outstanding sound properties of the final products exceeded even the high expectations of the developers – and could be scientifically proven. A two-year study conducted at the Brno University of Technology verified the acoustic properties of the finished material; the sand structure manufactured on ExOne 3D printers is 86 % more rigid than MDF, leading to double the sound damping inside the unit compared to a more traditional speaker.
The spiral design of the finished Deeptime Spirula satellite speaker mirrors the organic shapes found in nature – the curve of a sea-shell or the proportions of an uncurling fern leaf.
FURTHER INFORMATION:
ExOne at Formnext 2021:
Hall 12.0, Booth D69
Tags
- Additive Manufacturing
- Electronic engineering and electronics