Text: Thomas Masuch, 4 December 2024
Sometimes big things start small, and that’s certainly true of filament manufacturer Fiberthree. This Darmstadt-based company has developed a process that recycles carbon-fiber-reinforced plastic and significantly minimizes its carbon footprint. At the same time, the recycled material involves no additional costs and offers almost the same mechanical properties. While recycled material still accounts for less than 10 percent its total sales, Klaus Philipp, co-founder and managing director of Fiberthree, wants to position his company more strongly in this field.
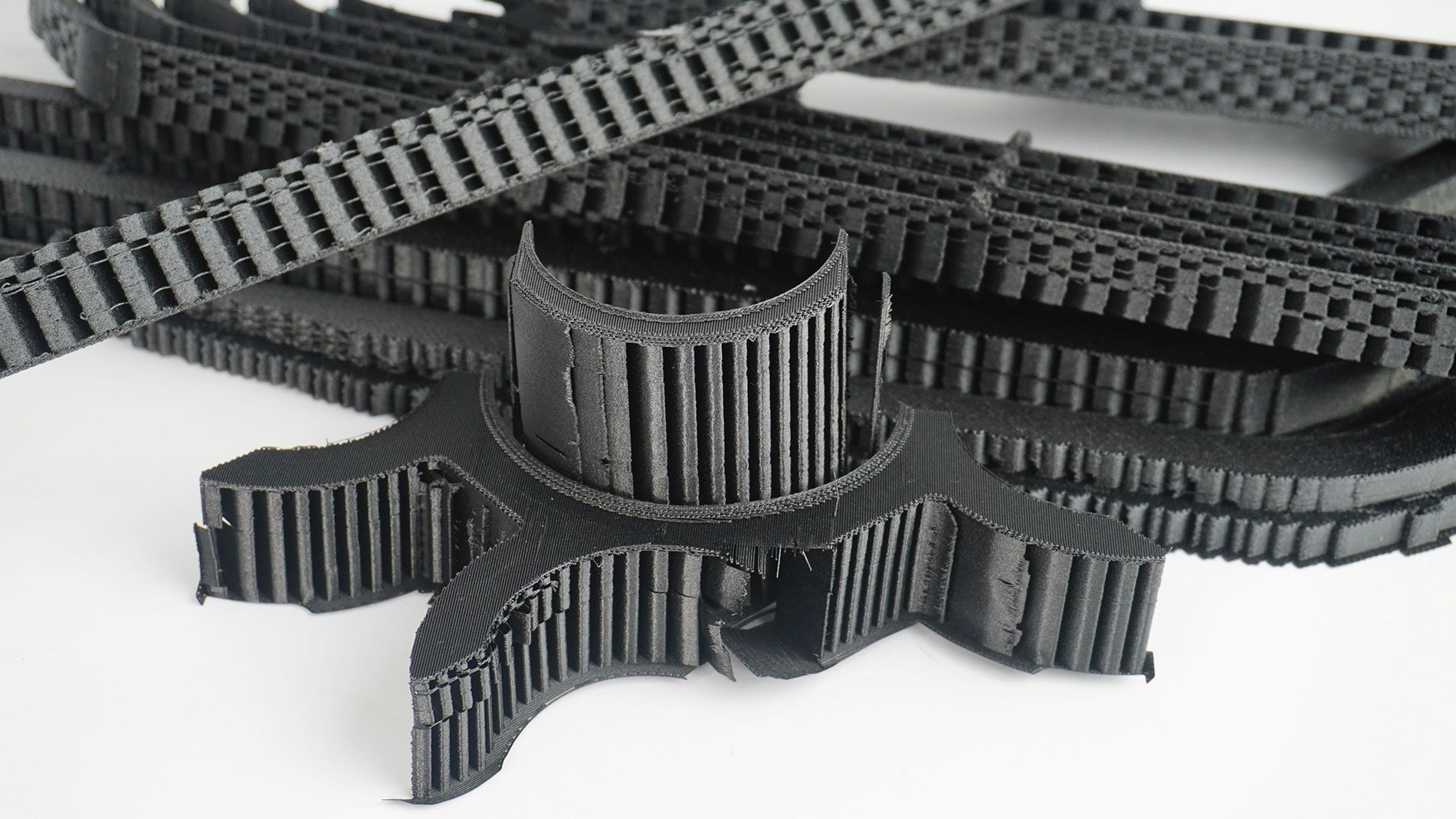
An important driver of this development was the mechanical engineering company Andritz Kaiser, which has been sourcing its filament from Fiberthree for many years. “We generate a lot of waste, particularly when developing new components – be it in the form of support structures, rejects, or misprints,” says Paolo Matassoni, head of development at Andritz Kaiser. “Material is a precious raw material and it's far too good to simply throw away.” Matassoni and his team collect the waste from the 120 kilograms of carbon-fiber-reinforced plastic that is printed at Andritz Kaiser each year and send it back to Darmstadt, along with their empty filament spools. As Andritz Kaiser also has the components for its series machines 3D-printed at Fiberthree, further residual materials from Fiberthree’s PA-CF Pro plastic are collected here, as well.
Recycling process presents challenges
Klaus Philipp is particularly motivated by the desire to ensure that the remnants of PA-CF Pro do not end up as waste. “In this day and age, we can no longer afford to simply throw away a high-performance material. We have to realize that plastics have value.” This recycling approach is also important because “we have young employees who are very committed to the issue of sustainability,” as Philipp explains.
According to Fiberthree, the recycled material achieves around 90 percent of the performance of the original filament. Images: Fiberthree
Fiberthree, which employs four people and sells around three tons of plastic per year, now collects 250 kilograms of PA-CF Pro per year for recycling. In the first step, the material is shredded by a partner in the region. What sounds trivial is a challenge with a material like carbon-fiber-reinforced plastic: “It puts a lot of strain on the machine and can wear it out,” Philipp points out. Next, the shredded material is processed into granulate and then into filament. The intermediate step to granulate takes place “for safety reasons,” Philipp continues. “Otherwise, any contamination could damage the filament extruder.” This makes clean separation even more important.
Technical properties almost like the original
“Technically, the recycled material is almost as good as before; we achieve around 90 percent of the performance of the original filament,” Philipp reports. For Matassoni, the material’s slightly diminished strength is not a problem: “We don't use the recycled material for high-strength applications, but for support structures, for example, or for components such as oil pipes that are not exposed to high tensile or compressive forces.” Further tests are currently underway at Andritz Kaiser to determine the exact technical properties of the material. The results should be available by the end of 2024.
Filament production and tests on the company's own printers are carried out in-house in Darmstadt. Images: Fiberthree
Up to 90 percent less CO2
PA-CF Pro is a polyamide 6 with a carbon fiber content of 15 percent. Philipp has calculated that producing one kilogram of this material generates 10 to 12 kg of CO2 emissions. This is based on the CO2 footprints of polyamide (around 5 kg of CO2 / kg of material) and carbon fiber (30 kg of CO2 / kg of material) and that of compounding and filament production.
Philipp anticipates that Fiberthree’s recycling process will lead to significant reductions in CO2. For large tonnages, the rates achieved can reach 90 percent, and 60–80 percent can still be achieved with smaller quantities. One variable here is the use of electricity – that is, whether you include green electricity or the electricity mix in Germany. On average, Philipp has calculated three kilograms of CO2 emissions for each kilogram of recycled material.
Recycling has not yet saved any money, but there are no additional costs, either. The price of the recycled material is the same as that of new filament. “And that's already a strong argument,” asserts a happy Paolo Matassoni. “You reduce CO2 at practically zero cost.” This means that recycling will also be of interest to companies and corporations that are committed to sustainability and are pursuing set goals in this area. “The great thing about this application is that it’s very honest. Sustainability is not glossed over here; it is tangible,” Matassoni points out.
FURTHER INFORMATION:
Tags
- Materials