Text: Thomas Masuch, 04.12.2024
Manchmal beginnen große Dinge im Kleinen, so wie beim Filamenthersteller FiberThree: Das Unternehmen aus Darmstadt hat einen Prozess entwickelt, der carbonfaserverstärkten Kunststoff recycelt und den CO2-Fußabdruck deutlich minimiert. Gleichzeitig kostet das recycelte Material nicht mehr und bietet nahezu die gleichen mechanischen Eigenschaften. Noch beträgt der Anteil des recycelten Materials weniger als 10 Prozent vom Gesamtabsatz. Klaus Philipp, Mitgründer und Geschäftsführer von FiberThree, will sein Unternehmen damit aber stärker positionieren.
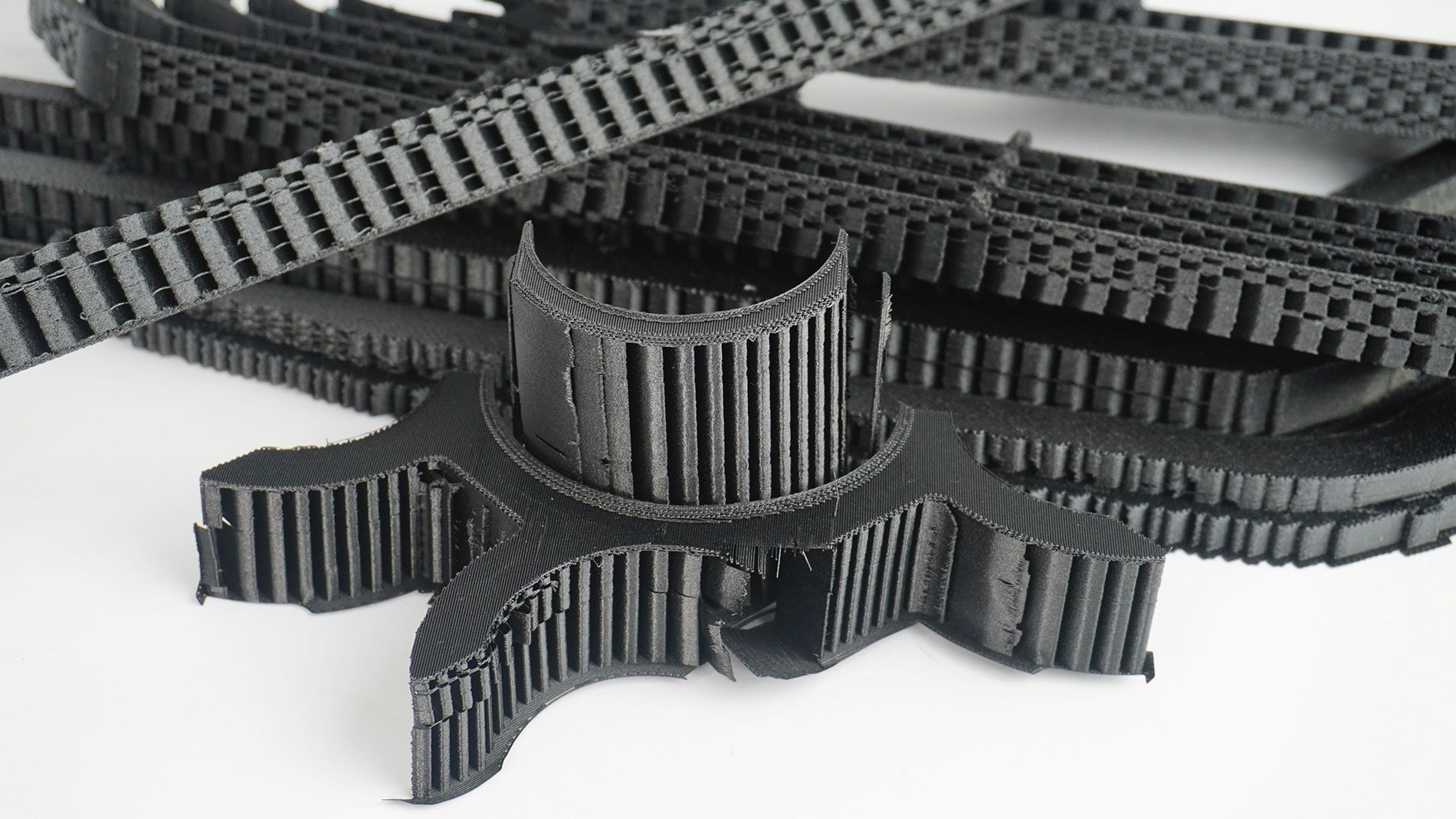
Ein wichtiger Treiber bei der Entwicklung war das Maschinenbau-Unternehmen Andritz Kaiser, das seit vielen Jahren seine Filamente bei FiberThree bezieht. „Insbesondere bei der Entwicklung neuer Bauteile fällt bei uns viel Abfall an – sei es in Form von Stützstrukturen, Ausschuss oder Fehldrucken,“ so Paolo Matassoni, Leiter Entwicklung bei Andritz Kaiser. „Dabei ist das Material ein edler Rohstoff, und es ist viel zu schade, ihn einfach wegzuwerfen.“ Von den 120 Kg carbonfaserverstärktem Kunststoff, die bei Andritz Kaiser im Jahr verdruckt werden, sammelt Matassoni mit seinem Team die Abfälle und schickt sie inklusive der leeren Filamentspulen zurück nach Darmstadt. Da Andritz Kaiser die Bauteile für seine Serienmaschinen ebenfalls bei FiberThree 3D-drucken lässt, kommen hier noch weitere Reststoffe des von FiberThree entwickelten Kunststoffs PA-CF Pro zusammen.
Recyclingprozess mit Herausforderungen
Klaus Philipp ist es eine besondere Motivation, dass die Reste seines PA-CF Pro nicht im Müll landen. „Wir können es uns in der heutigen Zeit nicht mehr erlauben, einen Hochleistungswerkstoff einfach wegzuwerfen. Wir müssen uns bewusst machen, dass Kunststoffe einen Wert haben.“ Darüber hinaus sei dieser Recyclingansatz wichtig, „da wir junge Mitarbeiter haben, die sich sehr stark für das Thema Nachhaltigkeit einsetzen.“
Technisch erreicht das recycelte Material laut Fiberthree rund 90 Prozent der Leistung des Originalfilaments. Bilder: Fiberthree
So kommen bei FiberThree, das 4 Mitarbeiter beschäftigt und rund 3 Tonnen Kunststoff pro Jahr absetzt, inzwischen 250 Kg PA-CF Pro pro Jahr für das Recycling zusammen. In einem ersten Schritt wird das Material bei einem Partner in der Region geschreddert. Was trivial klingt, ist bei einem Material wie carbonfaserverstärkten Kunststoff eine Herausforderung, „da es die Maschine stark beansprucht und verschleißen kann“, erklärt Philipp. Das geschredderte Material wird im nächsten Schritt zu Granulat und dann zu Filament weiterverarbeitet. Der Zwischenschritt zum Granulat erfolgt „aus Sicherheitsgründen“, wie Philipp erklärt, „da ansonsten jede Verunreinigung den Filamentextruder schädigen könnte.“ Umso wichtiger ist eine saubere Trennung.
Technische Eigenschaften fast wie beim Original
„Technisch ist das recycelte Material fast so gut wie das Ausgangsmaterial, wir erreichen rund 90 Prozent der Leistung wie beim Originalfilament“, erklärt Philipp. Für Matassoni sind die etwas geringen Festigkeiten kein Problem: „Wir benutzen das recycelte Material nicht für hochfeste Anwendungen, sondern zum Beispiel für Stützstrukturen oder für Komponenten wie Ölleitungen, die keinen größeren Zug- oder Druckkräften ausgesetzt sind.“ Derzeit laufen bei Andritz Kaiser weitere Tests, um die genauen technischen Eigenschaften des Materials zu ermitteln. Die Ergebnisse sollen bis Ende 2024 vorliegen.
Filamentherstellung und Tests auf den eigenen Druckern erfolgen in House in Darmstadt. Bilder: Fiberthree
Bis zu 90 Prozent weniger CO2
Das Ursprungsmaterial PA-CF Pro ist ein Polyamid 6 mit 15 Prozent Carbonfasern. Philipp hat für die Herstellung eines Kilogramms einen CO2-Ausstoß von 10 – 12 Kg errechnet. Dieser ergibt sich aus den CO2-Bilanzen von Polyamid (rund 5 KG CO2 / KG Material) und Carbonfaser (30 KG CO2) und der Bilanz des Compoundings und der Filamentherstellung.
Für das Recycling rechnet Philipp mit deutlichen CO2-Einsparungen: Bei großen Tonnagen kann die Einsparung bei 90 Prozent liegen, bei kleineren Mengen bei 60 – 80 Prozent. Eine Variable dabei ist der Einsatz des Stroms – ob man dabei Ökostrom hineinrechnet oder den Strommix in Deutschland berücksichtig. Im Mittel hat Philipp einen CO2-Ausstoß von 3 Kg CO2 / KG recyceltem Material errechnet.
Geld sparen lässt sich mit dem Recycling bisher noch nicht, Zusatzkosten entstehen aber auch keine. Der Preis für das recycelte Material entspricht dem der neuen Filamente. „Und das ist ja schon einmal ein starkes Argument“, freut sich Matassoni. „Man bekommt praktisch eine CO2-Einsparung zum Nulltarif.“ Damit sei das Recycling auch für Unternehmen und Konzerne interessant, die sich der Nachhaltigkeit verschrieben haben und hier feste Ziele verfolgen. „Das Schöne an dieser Anwendung ist, dass sie sehr ehrlich ist. Hier wird die Nachhaltigkeit nicht schöngerechnet, sondern sie ist wirklich greifbar.“
MEHR INFOS UNTER:
Tags
- Werkstoffe und Halbzeuge