Text: Thomas Masuch, 26 October 2023
Additive manufacturing is already a powerful driver of sustainability in many areas of industry – from aircraft assembly to energy and building construction. However, experts say that the green potential of industrial 3D printing is still vastly underestimated. To help change that, Formnext will be putting even more of a spotlight on sustainability this year.
One of the most well-known 3D-printed components anywhere is surely the fuel nozzle General Electric produces for use in aircraft construction. Besides being a masterstroke in technical terms, this part also shows how innovative AM technology can impact the economy and the broader effort to achieve sustainability. GE Aviation builds the fuel nozzles into its LEAP turbofan engines, where they have helped save thousands of tons of CO2.
These days, more and more companies, managers, and politicians are recognizing the potential AM presents in connection with sustainability. Along with more economical jet engines and lighter-weight components for airplanes, it opens the door to more efficient power plant generators, customized heat exchangers, various motors and pumps, and many other types of power units. “Additive manufacturing is technology that makes sustainable products possible,” says Matthias Schmidt-Lehr from Ampower, a Hamburg-based consulting firm that specializes in AM. “We’re far from exhausting its potential in that regard, however; in a lot of areas, we’ve only just begun and can expect a lot more applications in the coming years.”
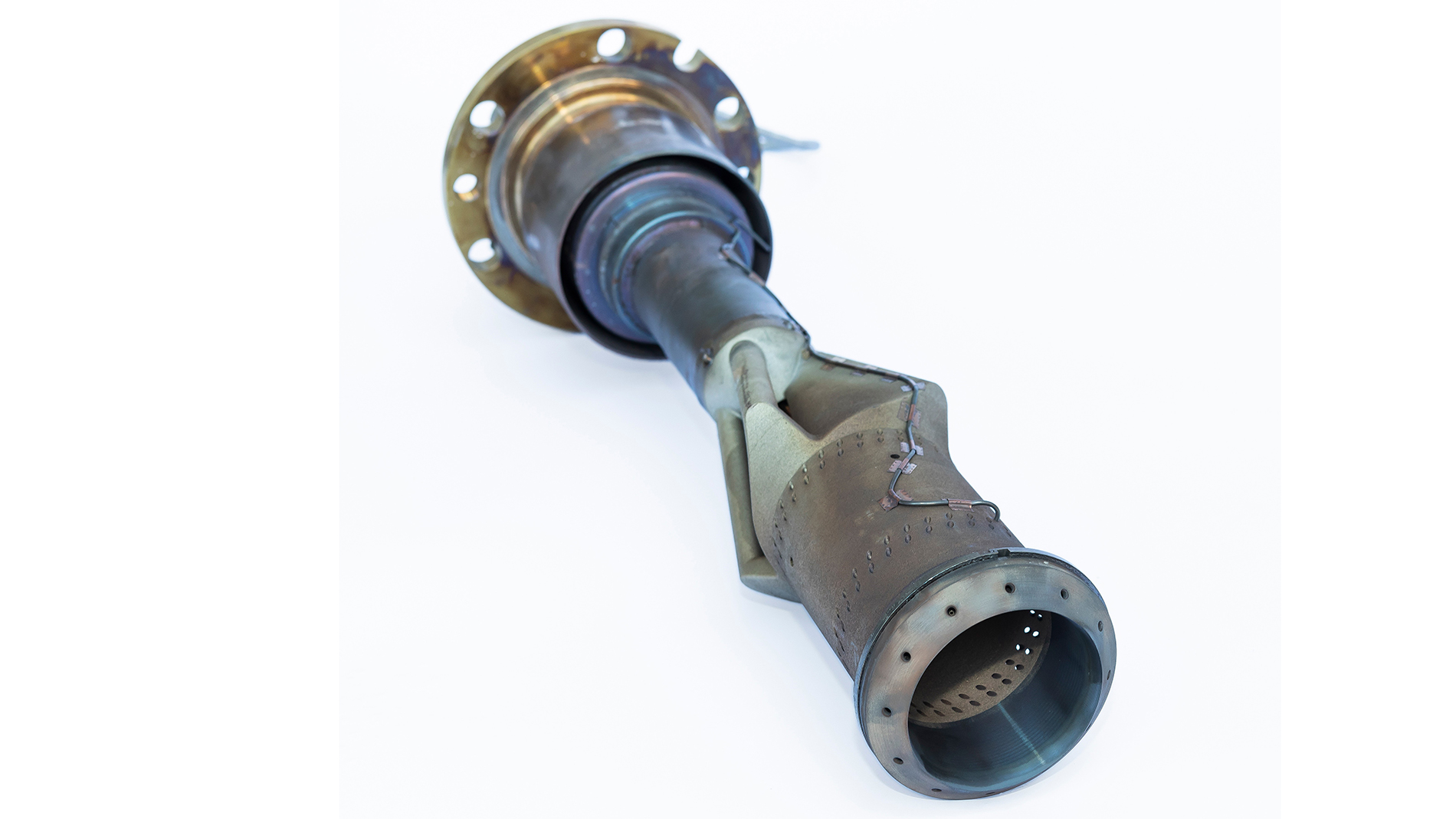
AM at Siemens: CO2 footprints for 3D-printed components
The sustainable developments facilitated by AM can play a key role for both nations and corporations like Volkswagen, Siemens, and General Electric as they work toward their carbon reduction targets. Siemens, for instance, has already been utilizing AM for years and now operates an expansive AM competence center in Erlangen. The facility evaluates and presents various additive methods, including in combination with components and software made by the long-standing German giant. “AM enables us to work more efficiently in many areas of our group, which ultimately reduces our carbon emissions, as well,” reports Dr. Karsten Heuser, vice president of additive manufacturing at Siemens Digital Industries. “In the process, it’s also important to make these achievements measurable. Using our software tools, our experts can calculate the carbon footprint of a given component and figure out whether it should be 3D-printed.”
In Finspang (Sweden), meanwhile, the former subsidiary Siemens Energy has established one of Europe’s largest 3D metal printing locations, where it has been printing burners for Siemens’ gas turbines for many years. Unlike in conventional manufacturing, where they once had to be assembled from 13 different parts, these burners are printed in a single piece. Their optimized design enables them to operate more efficiently, which Siemens says can reduce the carbon emissions of an overall turbine installation by 7,000 tons.
For another example, Dr. Heuser points to a 3D-printed robotic gripping arm. By enhancing the design’s topology, AM has reduced the arm’s weight by 64 percent and its carbon footprint by a full 82 percent. Dr. Heuser believes additive manufacturing has tremendous potential to enable future advancements in sustainability in the area of robotics alone. “Many of the around three billion robots in use around the world can already be outfitted with 3D-printed grippers,” he points out. “That would not only save plenty of CO2, but improve the robots’ performance, as well.” As an added bonus in this use case, an optimized robot requires 54 percent less energy and takes up half the usual space.
One type of bracket – 43 fewer tons of CO2
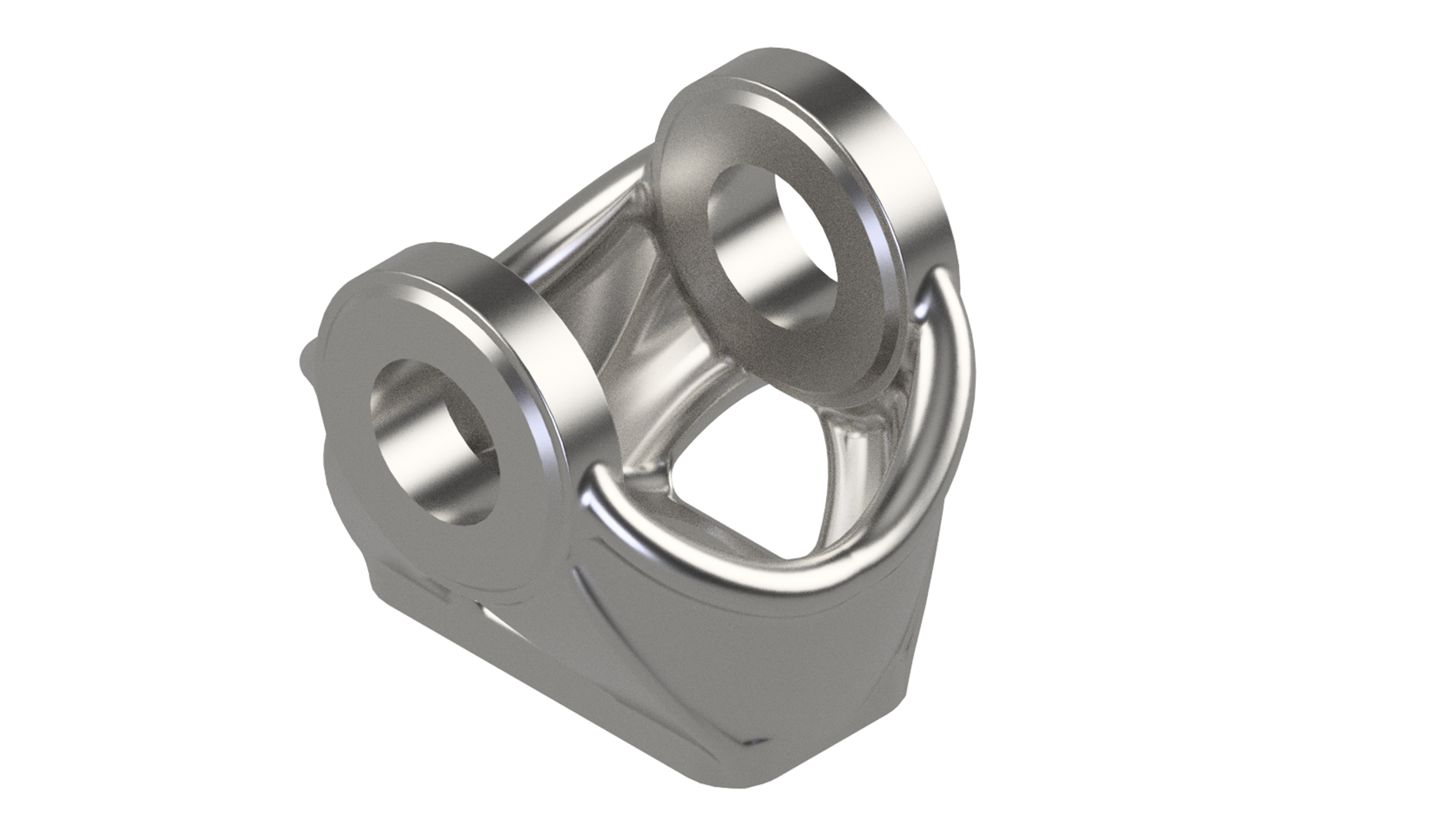
Aircraft construction is generally a key area of application for AM. After all, it’s a field where the technology can leverage one of its greatest strengths: Its ability to optimize topology makes it possible to realize things like bionic designs that recall human bone structures. These designs, which can typically only be 3D-printed (and not machined, for instance), are both extremely sturdy and extremely light. The resulting weight reductions are enabling the engineers at Airbus, Boeing, and other manufacturers to make airplanes lighter, which can ultimately reduce fuel consumption to a considerable degree.
Every kilogram saves around €2,000 (or 2,000 liters of kerosene) per year – and with the price of CO2 certificates set to continue rising, those savings are sure to increase, as well. Over the 30–40 years of an aircraft’s useful life, every kilogram less can also conserve some 100,000 liters of kerosene.
Another good example of AM’s considerable potential when it comes to sustainability involves the brackets that can be found in large numbers in airplanes. In a recent study, Ampower calculated the carbon footprint of the corresponding manufacturing process and found that AM produces less greenhouse gas than the conventional method (eight kilograms of CO2 instead of 10). However, the real potential for savings is only revealed by the brackets’ performance in use: Thanks to their reduced weight, they help reduce carbon emissions by more than 43 tons compared to brackets of conventional design and manufacture.
Key to carbon footprints: a sustainable energy mix
“3D printing requires significantly less energy compared to other production methods, especially when you’re working with titanium,” reports Matthias Schmidt-Lehr, whose company has developed a carbon footprint calculator for AM components that factors in everything from material production and actual manufacture to recycling. The tool shows that individual details play a significant role in the production process – take the origin of the powder used, for instance: “Depending on the regional energy mix in question, powder production in countries like China can entail much higher carbon emissions than when renewable energy sources are used, as some plants in Europe are currently doing,” Schmidt-Lehr continues.
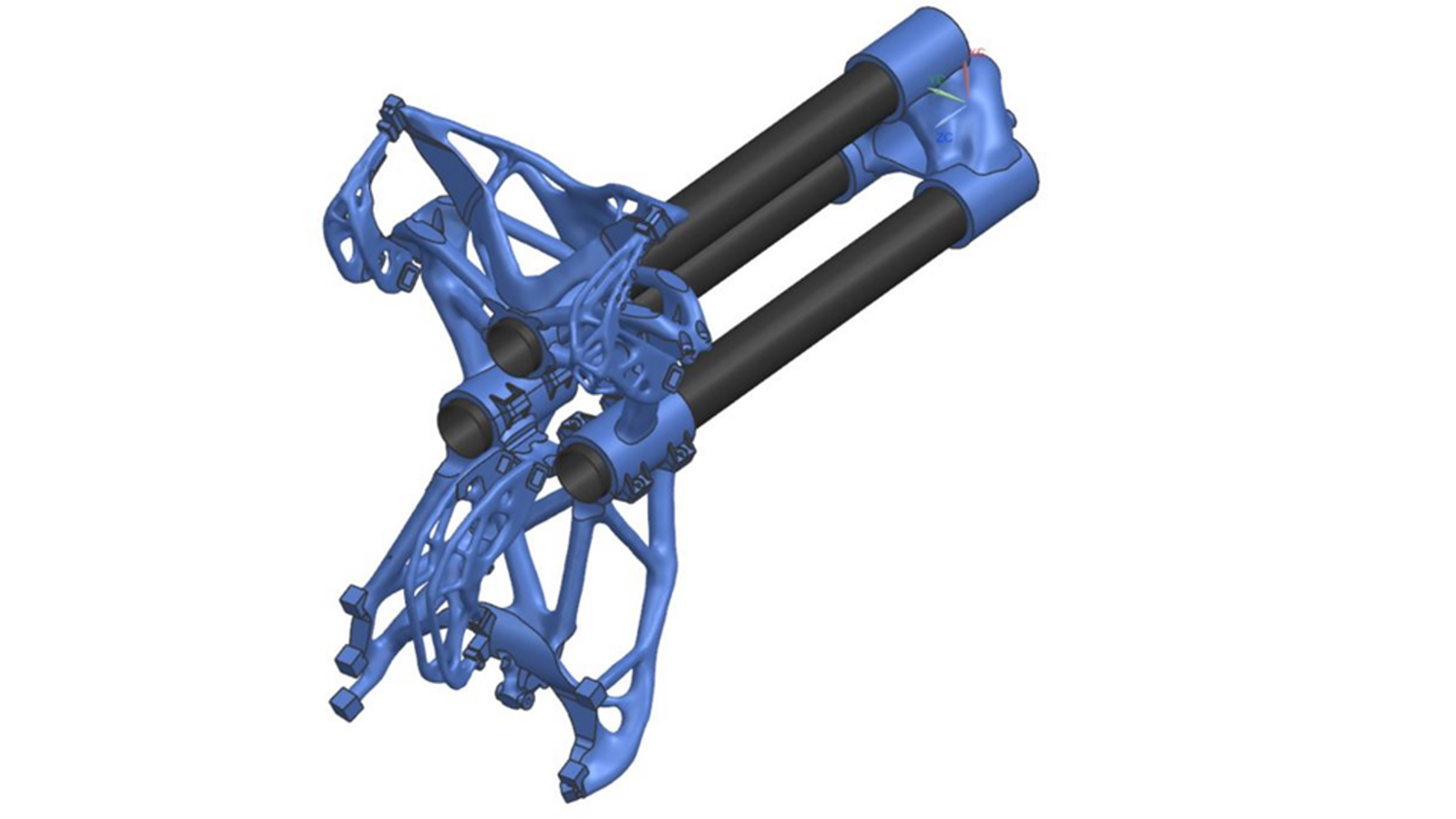
The main potential here lies in the possible applications, however, which are incredibly diverse. In many cases, small components of an intelligent design can enhance entire systems. Searching for them is something like looking for the Holy Grail of engineering. That said, it doesn’t always have to be a game-changer; minor improvements often have a major impact, as well. “Up to 80 percent of a product’s impact on the environment is determined by its design,” Dr. Heuser explains. This is another area where AM can be a huge help, as it takes product development to a whole new level. “It’s a catalyst for rapid iteration, which means products can take on sustainable qualities that wouldn’t be possible otherwise,” Dr. Heuser adds. The possibilities afforded by additive manufacturing are much more wide-ranging than that, however. For example, parts can be repaired instead of having to be replaced. And let’s not forget another of AM’s main strengths: decentralized production. This means instead of being made in China as they so often are today, things like eyeglasses can be manufactured regionally and shipped across much shorter distances. Major automotive manufacturers like Daimler are among the many different companies that want to take advantage of this in supplying spare parts.
“Potential still not sufficiently recognized”
“When it’s applied across a range of areas, AM has the capacity to make manufacturing more sustainable,” Dr. Heuser explains. “As of today, however, the potential of this technology hasn’t been sufficiently recognized; policymakers in Germany haven’t paid much attention to it.” In contrast, additive manufacturing can be found in the national growth strategies of the United States and China. “Incorporating an AM strategy into Germany’s own national plan for growth could be a significant boon to German industry,” Dr. Heuser suggests.
Meanwhile, Formnext will be focusing even more on the topic of sustainability this year. Not only will numerous exhibitors be showing off their solutions for reducing carbon emissions; the event’s surrounding program and conferences will highlight current and upcoming solutions that make industrial 3D printing possible, along with everything from vertical wind turbines and bio-inclusive cities to more sustainable shoe production.
FURTHER INFORMATION:
Siemens at Formnext 2023: Hall 12.1, booth D119
AMPower at Formnext 2023: Hall 12.0, booth B99
Tags
- Sustainability
- Aviation and aerospace
- Energy
- Market reports and studies