Text: Thomas Masuch, 26.10.2023
Die Additive Fertigung treibt bereits in vielen Industriebereichen die Nachhaltigkeit stark voran – vom Flugzeugbau über den Energiesektor bis zur Bauindustrie. Trotzdem wird das nachhaltige Potenzial des industriellen 3D-Drucks noch stark unterschätzt, sagen Experten. Um dies zu ändern, spielt das Thema Nachhaltigkeit in diesem Jahr auch auf der Formnext eine noch stärkere Rolle.
Eines der berühmtesten 3D-gedruckten Bauteile weltweit ist sicherlich die im Flugzeugbau eingesetzte 3D-gedruckte Einspritzdüse von GE. Sie ist nicht nur eine technische Meisterleistung, sondern zeigt auch, welchen Einfluss diese neue Technologie auf Wirtschaft und Nachhaltigkeit haben kann: Mittels der Einspritzdüsen, die GE Aviation in seinen LEAP-Strahltriebwerken verbaut, wurden Tausende Tonnen CO2 eingespart.
Inzwischen erkennen immer mehr Unternehmen, Manager und Politiker, welches Potenzial AM in Bezug auf Nachhaltigkeit bietet. Das reicht von den sparsameren Turbinen oder leichteren Bauteilen für Flugzeuge über effizientere Kraftwerksgeneratoren und maßgeschneiderte Wärmetauscher bis hin zu Motoren, Pumpen und vielen anderen Aggregaten. „Die Additive Fertigung ist eine Technologie, die nachhaltige Produkte möglich macht. Dabei ist das Potenzial bei weitem noch nicht ausgereizt, in vielen Bereichen stehen wir erst am Anfang und können in den nächsten Jahren noch viele weitere Anwendungen erwarten“, so Matthias Schmidt-Lehr von Ampower, einem auf die Additive Fertigung spezialisierten Beratungsunternehmen aus Hamburg.
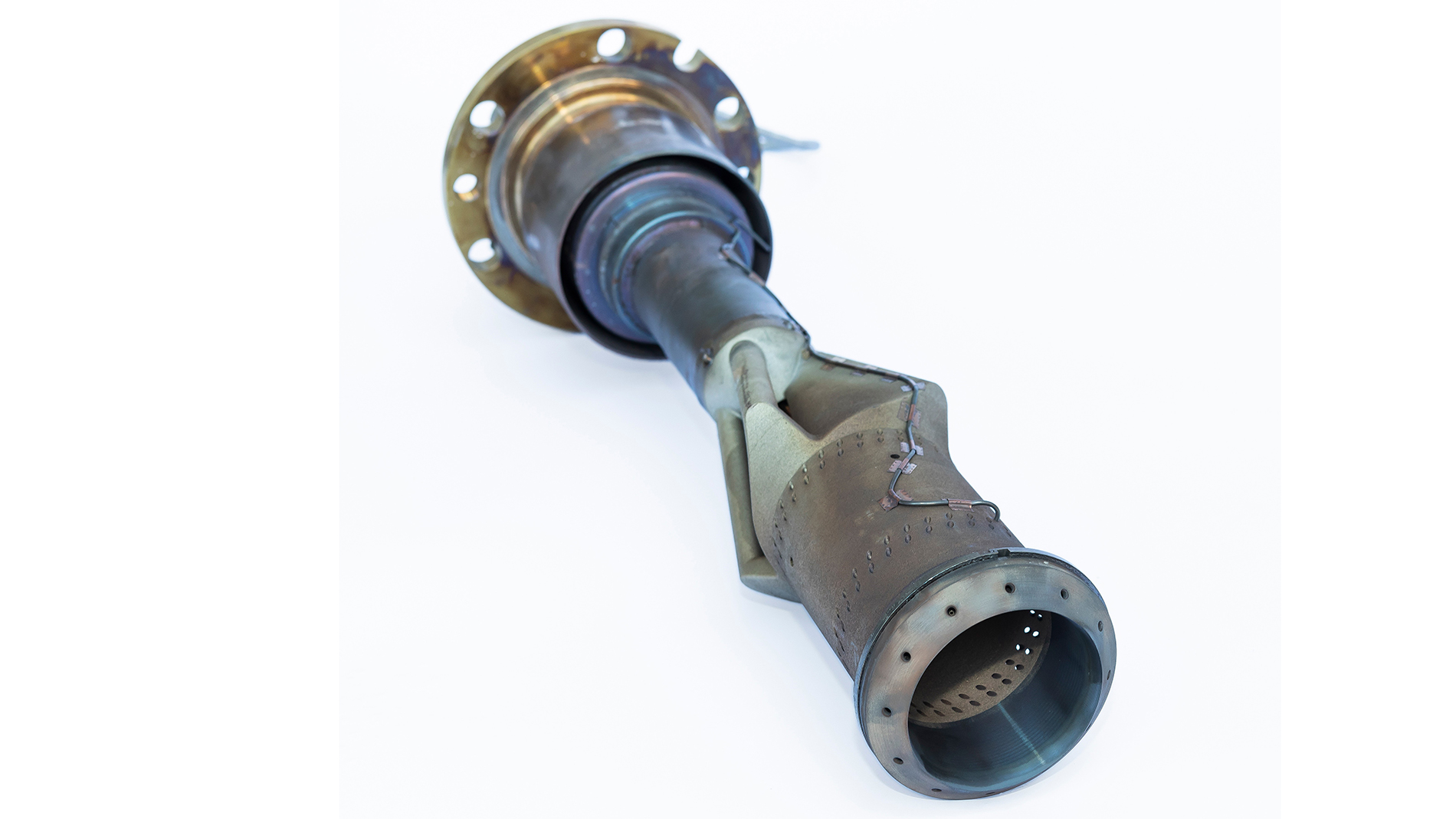
AM bei Siemens: CO2-Fußabdruck für AM-Bauteile
Die nachhaltigen Entwicklungen, die die Additive Fertigung ermöglicht, können ein wichtiger Baustein sein, damit Staaten, aber auch Konzerne wie Volkswagen, Siemens oder General Electric ihre CO2-Einsparziele erreichen. So setzt Siemens bereits seit vielen Jahren auf die Additive Fertigung und betreibt ein umfangreiches AM-Kompetenzzentrum in Erlangen, in dem verschiedene additive Verfahren evaluiert und präsentiert werden – auch verbunden mit Komponenten und Software des deutschen Traditionskonzerns. „Mit der Additiven Fertigung können wir in zahlreichen Konzernbereichen effizienter arbeiten und damit letztendlich auch CO2 einsparen“, so Dr. Karsten Heuser, Vice President Additive Manufacturing bei Siemens Digital Industries. „Wichtig ist es dabei, diesen Erfolg auch messbar zu machen. Mithilfe unserer Softwaretools können unsere Experten den CO2-Fußabdruck eines Bauteils ermitteln. Dadurch entscheidet sich, ob das Bauteil additiv gefertigt wird oder nicht.“
Im schwedischen Finspang hat die ehemalige Konzerntochter Siemens Energy einen der größten Fertigungsstandorte für Metall-3D-Druck in Europa aufgebaut und druckt hier seit vielen Jahren Brenner für Siemens-Gasturbinen. Die 3D-gedruckten Brenner werden in einem Stück hergestellt – vorher, bei einer konventionellen Fertigung, mussten 13 Bauteile zusammengesetzt werden. Durch das optimierte Design arbeiten die Brenner zudem auch effizienter, was letztendlich laut Siemens den CO2-Ausstoß einer ganzen Turbinen-Anlage um 7.000 Tonnen senken kann.
Als weiteres Beispiel nennt Heuser einen 3D-gedruckten Robotergreifer. Durch das Topologie-optimierte Design kann die Additive Fertigung hier 64 Prozent Gewicht einsparen und den CO2-Fußabdruck um 82 Prozent reduzieren. Allein im Bereich der Robotik sieht Heuser für die Zukunft noch enormes nachhaltiges Potenzial durch die Additive Fertigung. „Eine Vielzahl der rund 3 Mrd. installierten Roboter weltweit könnte heute schon mit 3D-gedruckten Greifern ausgestattet werden – damit wird nicht nur viel CO2 eingespart, sondern die Greifer können auch die Leistung der Roboter verbessern.“ Ein weiterer positiver Effekt in diesem Anwendungsfall: Der optimierte Roboter benötigt 54 Prozent weniger Energie und 50 Prozent weniger Platz.
Ein Bracket spart 43 Tonnen CO2
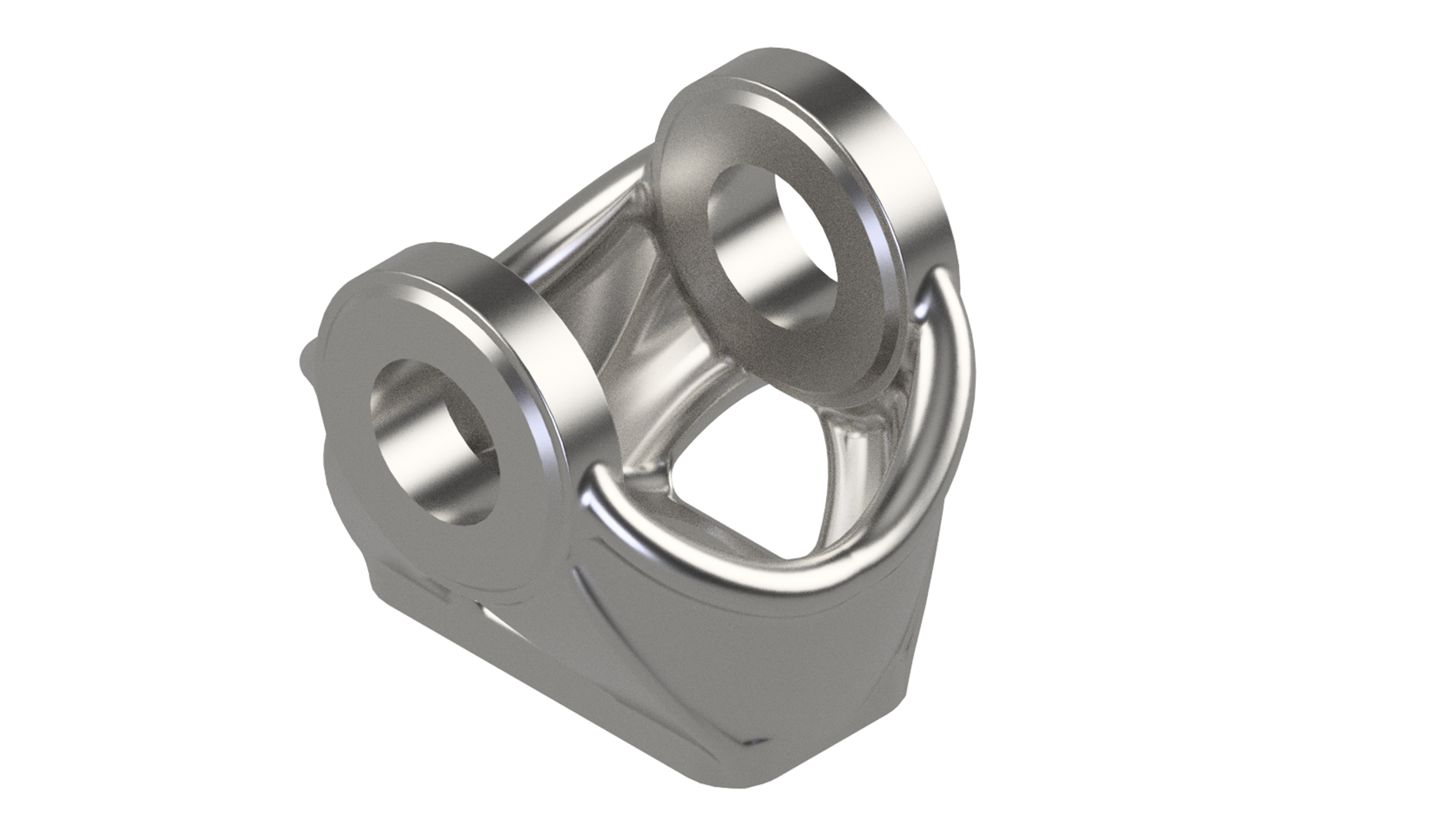
Der Flugzeugbau ist generell ein wichtiges Anwendungsfeld der Additiven Fertigung. Denn gerade hier kann die Technologie eine ihrer größten Stärken ausspielen: Über Topologie-Optimierungen lassen sich zum Beispiel bionische Designs umsetzen, die an die Knochenstruktur von Menschen erinnern. Diese Designs, die sich in der Regel nur im 3D-Druck und zum Beispiel nicht in der Zerspanung umsetzen lassen, sind extrem stabil und sehr leicht. Die Gewichtsersparnis nutzen die Konstrukteure von Airbus, Boeing und anderen Herstellern, um Flugzeuge leichter zu machen – was letztendlich den Treibstoffverbrauch deutlich reduzieren kann.
Jedes reduzierte Kilogramm Gewicht spart jährlich rund 2.000 Euro bzw. 2.000 Liter Kerosin – in den nächsten Jahren dürften die monetären Einsparungen aufgrund weiter steigender Preise für CO2-Zertifikate sicherlich noch höher ausfallen. Und über eine Lebensdauer von 30 bis 40 Jahren pro Flugzeug kann damit jedes Kilogramm Gewicht weniger rund 100.000 Liter Kerosin einsparen.
Ein gutes Beispiel für das hohe nachhaltige Potenzial der Additiven Fertigung sind sogenannte Brackets, die sich zahlreich in den Flugzeugen finden. Ampower hat in einer Studie den CO2-Abdruck bei der Fertigung dieser Bauteile berechnet. Im Produktionsprozess verursacht die Additive Fertigung im Vergleich mit der konventionellen Fertigung weniger Treibhausgase (8 kg CO2 statt 10). Doch das wahre Einsparpotenzial zeigt sich, wenn man die Bauteile in der Anwendung betrachtet: Durch sein geringeres Gewicht reduziert ein 3D-gedrucktes Bauteil gegenüber einem konventionell gefertigten (und designten) den CO2-Verbrauch um mehr als 43 Tonnen.
Für CO2-Bilanz nachhaltiger Energiemix wichtig
„Vor allem bei der Verarbeitung von Titan spart der 3D-Druck signifikant Energie im Vergleich zu anderen Produktionsmethoden“, berichtet Schmidt-Lehr, der mit Ampower einen CO2-Kalkulator entwickelt hat, der von der Materialherstellung über das Recycling bis zur Produktion den CO2-Fußabdruck für additive Bauteile berechnen kann. Dabei zeigt sich auch, dass im Produktionsprozess einzelne Details eine wichtige Rolle spielen – zum Beispiel die Herkunft des Pulvers: „Abhängig von dem regionalen Energiemix kann die Pulverherstellung in Ländern wie China zu deutlich höheren CO2-Emissionen führen, als wenn regenerative Energiequellen genutzt werden, wie es einige Werke im europäischen Raum derzeit tun,“ so der Ingenieur.
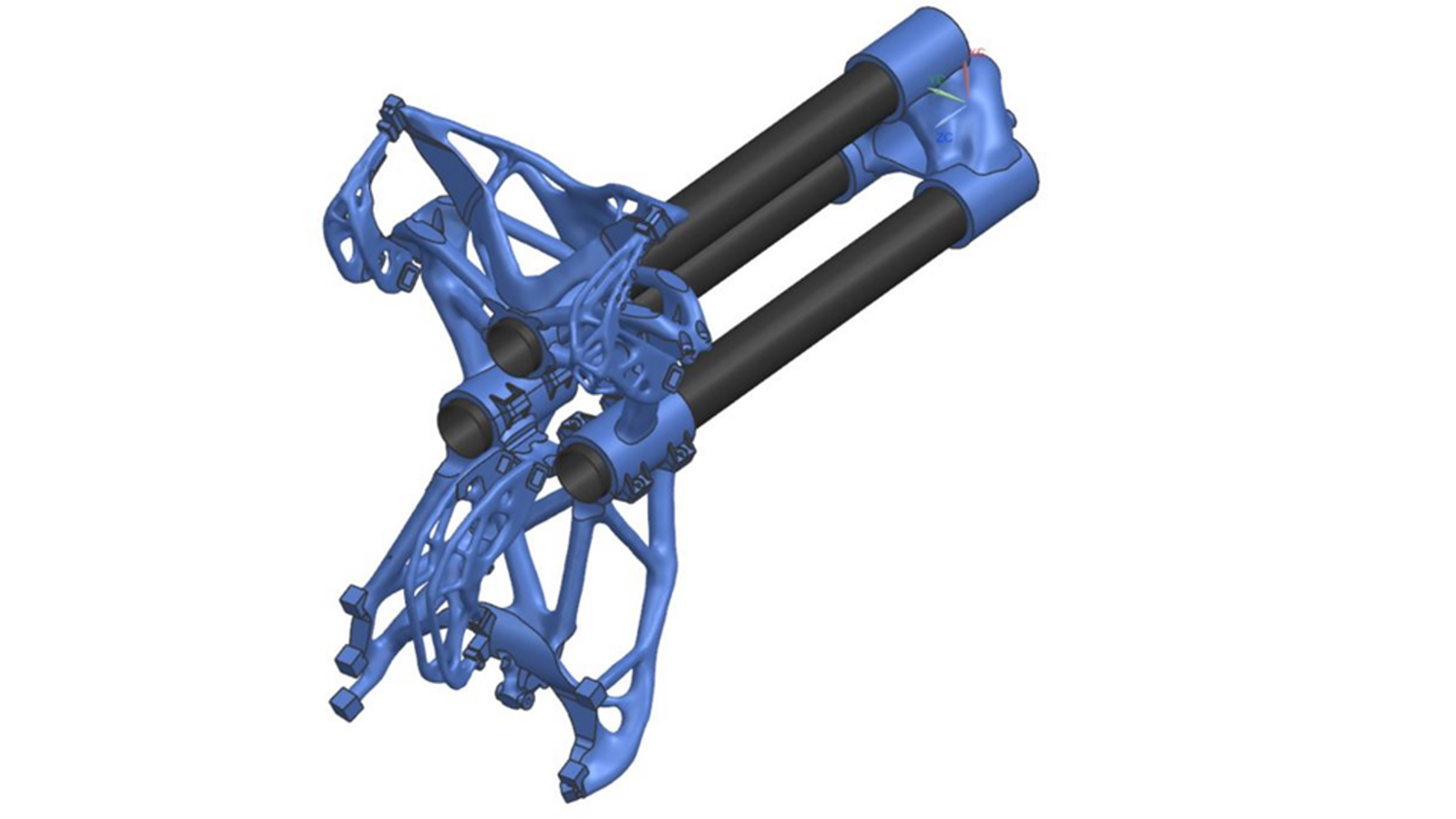
Das große Potenzial liegt aber in den Anwendungen, das Feld dafür ist äußerst vielfältig. Oft lassen sich durch kleine, intelligent designte Bauteile ganze Systeme verbessern. Die Suche danach ist wie die Suche nach dem heiligen Gral der Anwendungsingenieure. Doch es muss nicht immer der große Wurf sein, oft haben auch kleine Verbesserungen deutliche Effekte. „Bis zu 80 Prozent des Einflusses auf die Umwelt werden beim Design der Produkte festgelegt“, erklärt Heuser. Und auch dabei kann die Additive Fertigung enorm helfen, denn sie hebt die Produktentwicklung auf ein neues Niveau. „Schnelle Iterationen sind möglich – die Produkte können damit nachhaltige Qualität erreichen, die anders nicht möglich wäre“, so Heuser. Aber die Möglichkeiten der Additiven Fertigung sind noch weitaus vielfältiger: So können zum Beispiel Bauteile repariert werden, die dann nicht neu produziert werden müssen. Auch die dezentrale Produktion ist eine große Stärke der Additiven Fertigung: So können zum Beispiel Brillen regional und nicht wie üblich in China produziert werden – das spart weite Transportwege. Auch große Automobilhersteller wie Daimler, aber auch viele andere Unternehmen wollen diesen Vorteil für die Ersatzteilversorgung nutzen.
„Potenzial wird nicht ausreichend erkannt“
„AM hat das Potenzial, die Fertigung nachhaltiger zu machen, wenn man die Technologie breit einsetzt“, erklärt Heuser. „Allerdings wird das Potenzial dieser Technologie heute noch nicht ausreichend erkannt. Die Politik in Deutschland hat bisher wenig Aufmerksamkeit auf sie gerichtet.“ Im Gegensatz dazu ist die Additive Fertigung in den USA und China Teil der nationalen Wachstumsstrategien. „Eine AM-Strategie in Deutschland, die Teil der nationalen Wachstumsstrategie wäre, könnte auch der deutschen Branche erheblich zugutekommen.“
Eine verstärkte Aufmerksamkeit erhält das Thema Nachhaltigkeit auch auf der Formnext. Hier zeigen nicht nur zahlreiche Aussteller Lösungen, um CO2 zu einzusparen, auch das Rahmenprogramm und die Konferenzen thematisieren aktuelle und künftige nachhaltige Lösungen, die der industrielle 3D-Druck möglich macht – von vertikalen Windturbinen über bioinkludierte Städte bis hin zur nachhaltigeren Schuhproduktion.
MEHR INFOS UNTER:
Siemens auf der Formnext 2023: Halle 12.1, Stand D119
AMPower auf der Formnext 2023: Halle 12.0, Stand B99
Tags
- Energie
- Marktberichte und Studien
- Nachhaltigkeit
- Luft- und Raumfahrt