Text: Thomas Masuch; Photos: Airbus Defence and Space, OHB System AG — 2021/05/22
It is as if Additive Manufacturing was tailormade for the satellite construction industry, which is all about very small quantities, complex designs, and a quest to reduce weight: all demands that suit Additive Manufacturing to a T. No wonder, then, that satellites containing 3D-printed components have already been orbiting the earth for several years now. In this second part of our "AM in the Space Industry" series, we look behind the scenes to find out how widespread AM is in satellite construction at the moment, what market potential it has, what trends are driving the industry, and what challenges satellite manufacturers and their service providers still face.
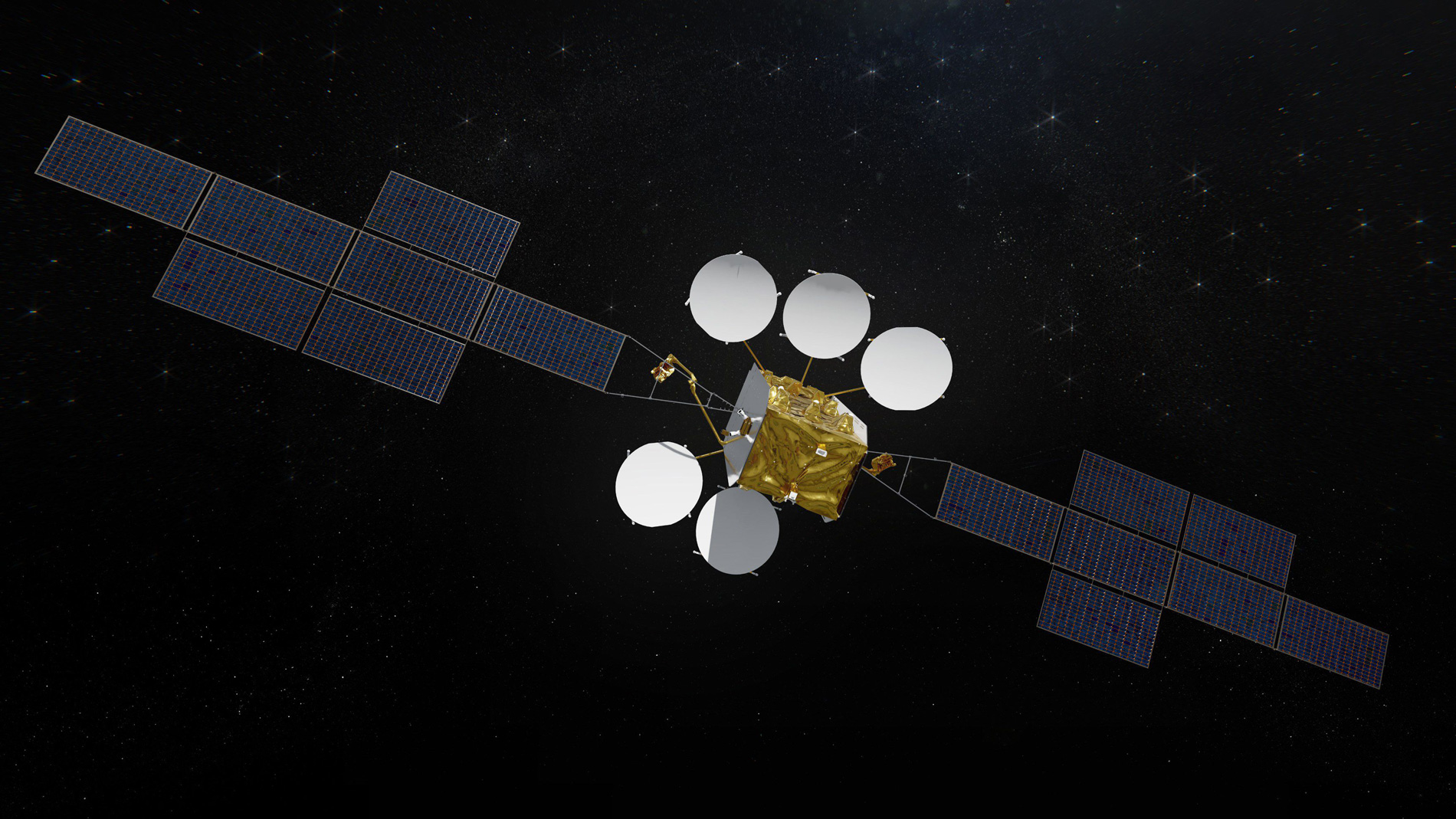
Airbus Defence and Space is currently manufacturing two Hotbird satellites for its customer Eutelsat, which will be fitted with a total of 500 3D-printed components. These parts are made from an aluminum- silicon-magnesium alloy (AlSi10Mg) and produced by certified partners using the selective laser melting (SLM) process. "There are more than 100 different waveguide designs, together with other network designs. The waveguides conduct the RF signals around the spacecraft. The components come in sizes ranging from about 100 mm [4"] to about 300 mm [12"]," explained Andrew Neal, an expert in additive layer manufacturing at Airbus in Portsmouth, UK, when he spoke to Formnext Magazine.
Aerospace company OHB System AG has also been engaged in Additive Manufacturing for more than six years now. "At first, it was a development project. Now we are at the stage of not only replacing existing components, but optimizing them in a really targeted way," said Marco Mulser, a technology manager for Additive Manufacturing at OHB. Next year, after several years of development, the first metallic AM part installed by OHB System will launch into space.
"Our job is very different to working in the automotive industry or even in aviation."
AM has also been high on the agenda for another industry heavyweight, Thales Alenia Space, for years now. The French company built a 3D-printed aluminum antenna into the TurkmenAlem communications satellite way back in 2015, before installing additively manufactured parts in 45 other communications satellites in 2017. Today, all Thales Alenia Space communications satellites use 3D-printed antenna brackets and reflector sleeves.
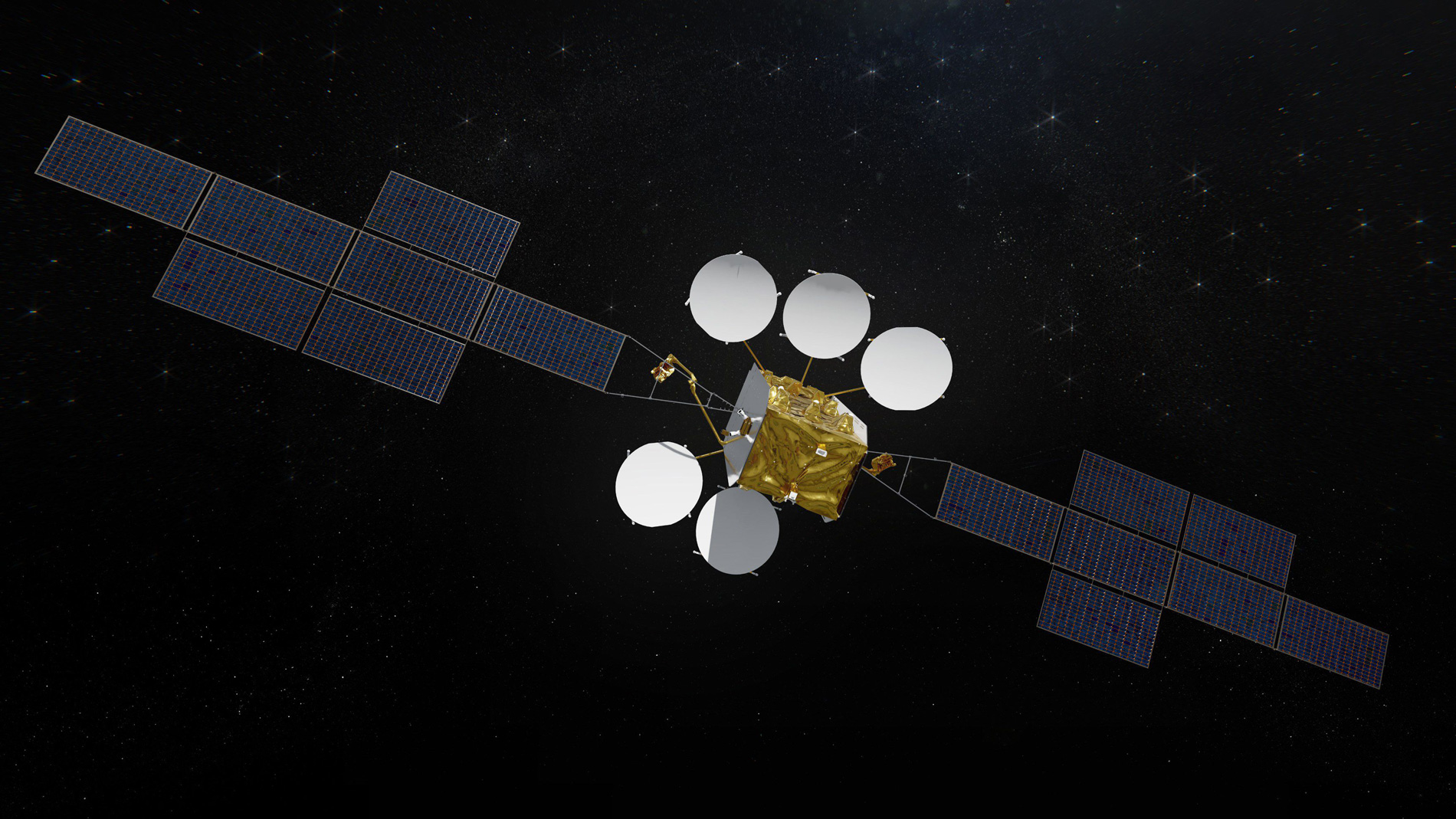
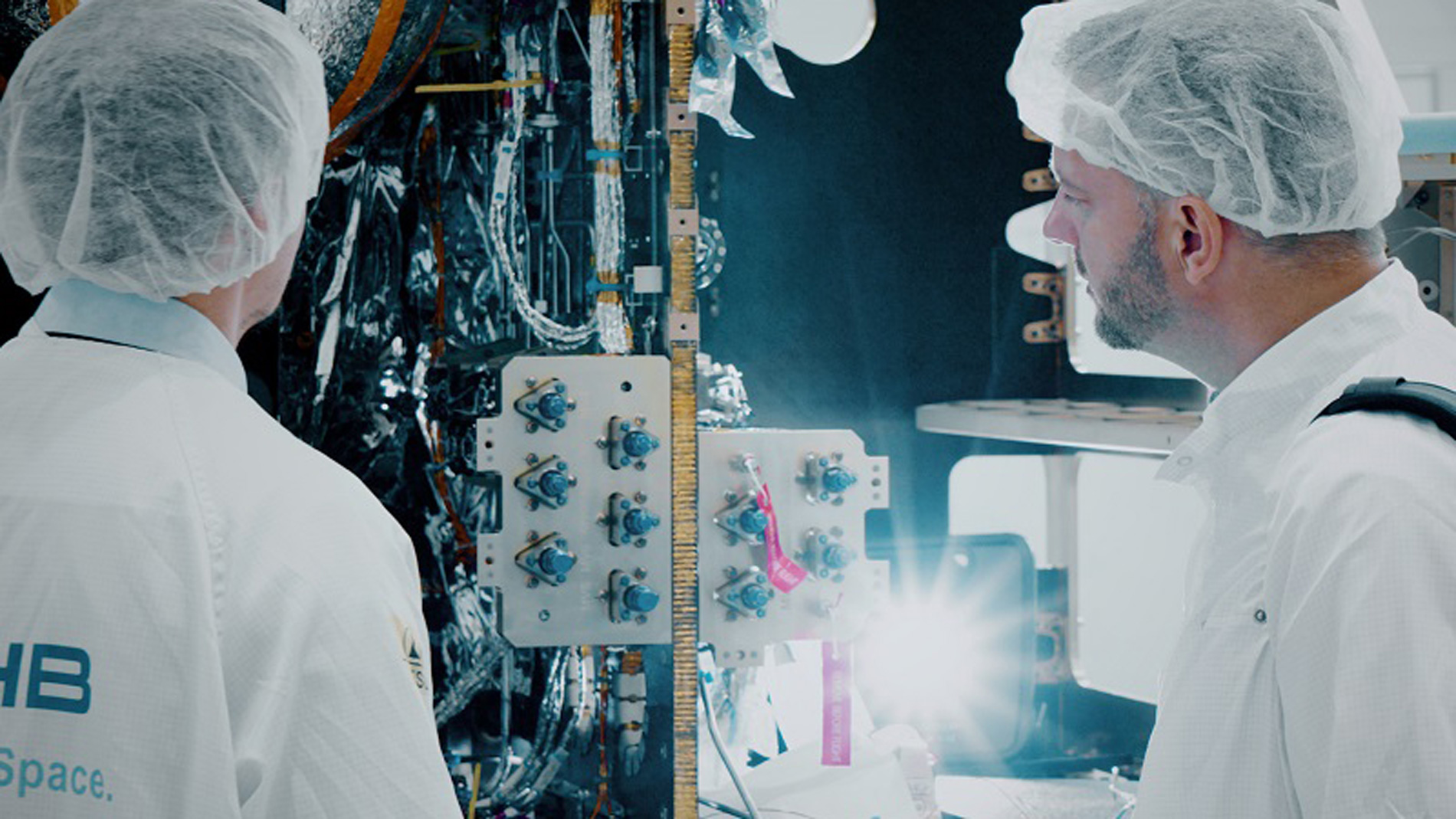
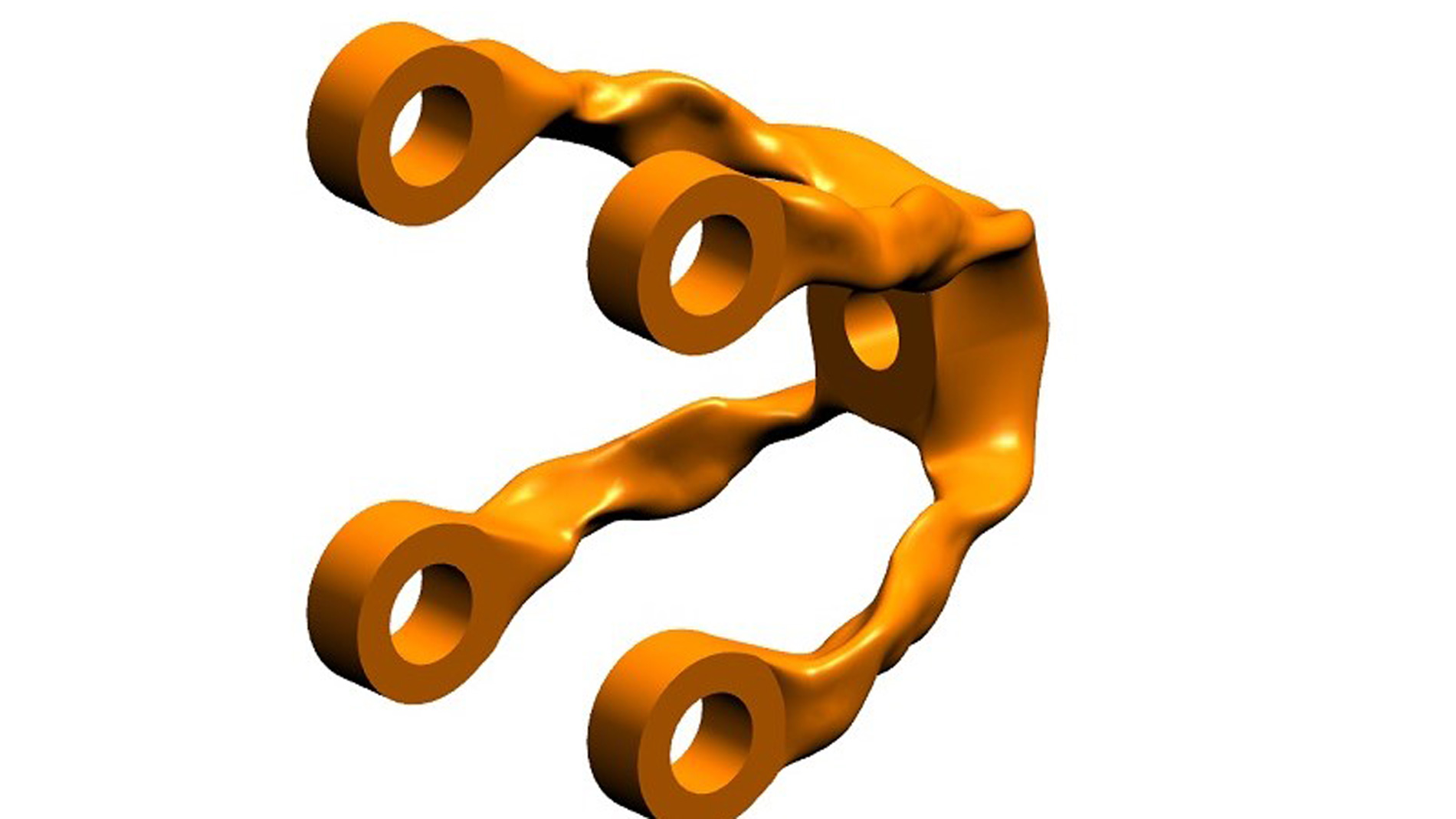
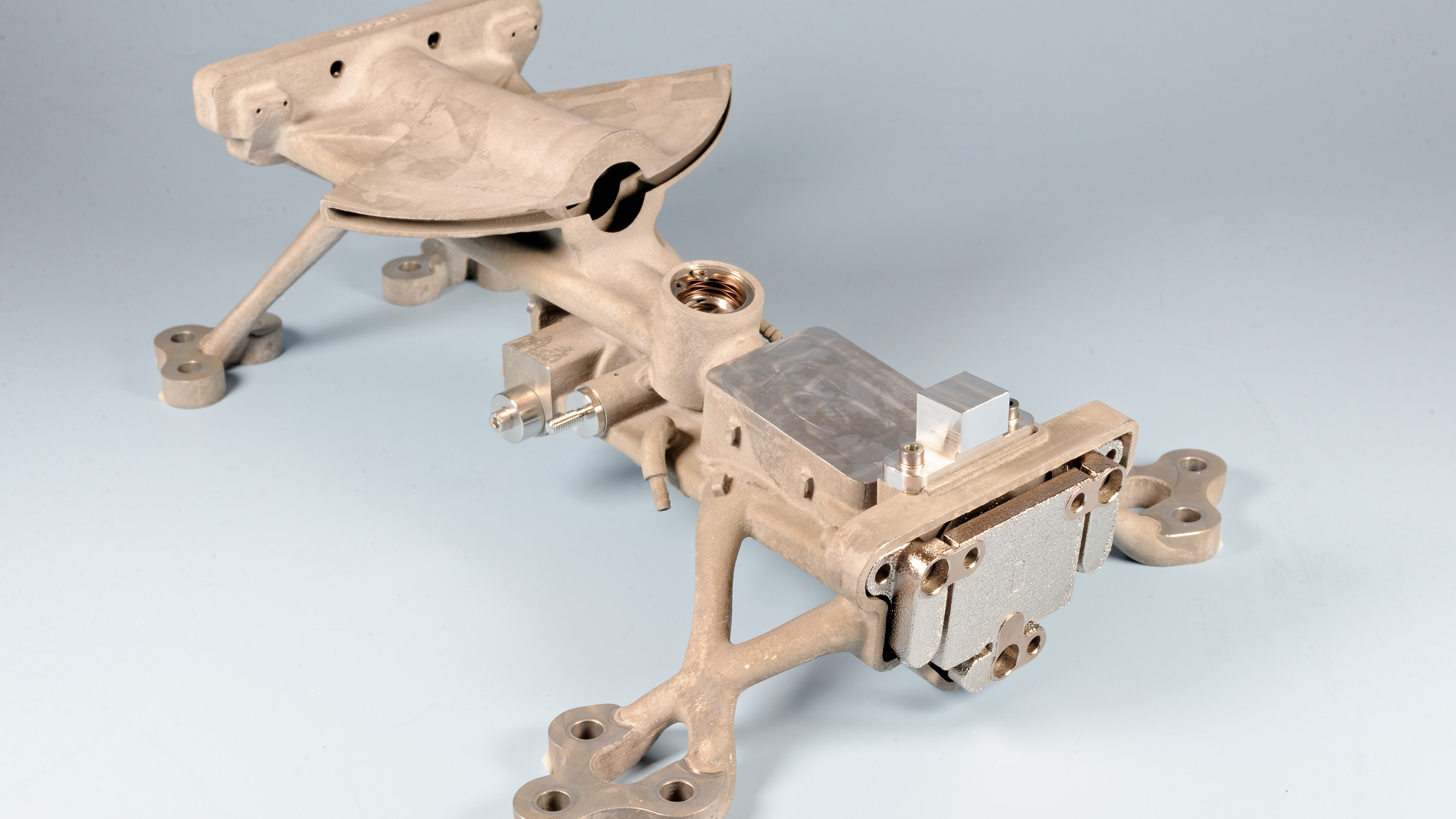
PURCHASED FROM SERVICE PROVIDERS
Both OHB System AG and Airbus Defence and Space purchase their 3D-printed components from suppliers, but only once they have "gone through a complete supplier and qualification process," according to Neal. OHB System decided four years ago to purchase 3D-printed parts solely from suppliers – the same approach the company takes to most of the other parts and components it uses to make its satellites. "We want to be able to rely on service providers having stable processes," said Mulser. And the engineer considers established companies in particular to be at an advantage here, "because it’s not so easy to just catch up on years of experience." OHB System turns to external partners for quality assurance too, "although we choose specifically which technology and which type of quality inspection is used."+
RELIABILITY IS A PRIORITY
Generally speaking, the satellite production industry has extremely high demands when it comes to reliability, which means redundant solutions are sometimes required. "Our job is very different to working in the automotive industry or even in aviation. After all, we cannot repair a faulty part or recall a product," said Mulser. "This means that the manufacturing process must be stable and consistently deliver reproducible results." This excludes the possibility of developing the process over time, a "learning by doing" approach, so to speak. Engineers at OHB System therefore work with fixed process parameters that have been verified in advance and use these as a basis for deciding where Additive Manufacturing could be a suitable production method, then designing components accordingly. "By now we have a very clear picture of which applications this works for," according to Mulser.
A PRETTY ROBUST SECTOR SO FAR
With its extraordinarily complex technology and long development times, satellite production has actually been a pretty robust sector in the past. Although the market did fluctuate depending on what was happening with certain major projects, it showed quite steady single- digit growth overall. In the years 2014 to 2018, satellite production revenues stood at $16.2 billion (source: Satellite Industry Association, SIA), with more than half that amount attributable to the USA. According to the SIA, 62.4 percent of global satellite production in 2019 took place in the USA. (See chart.)
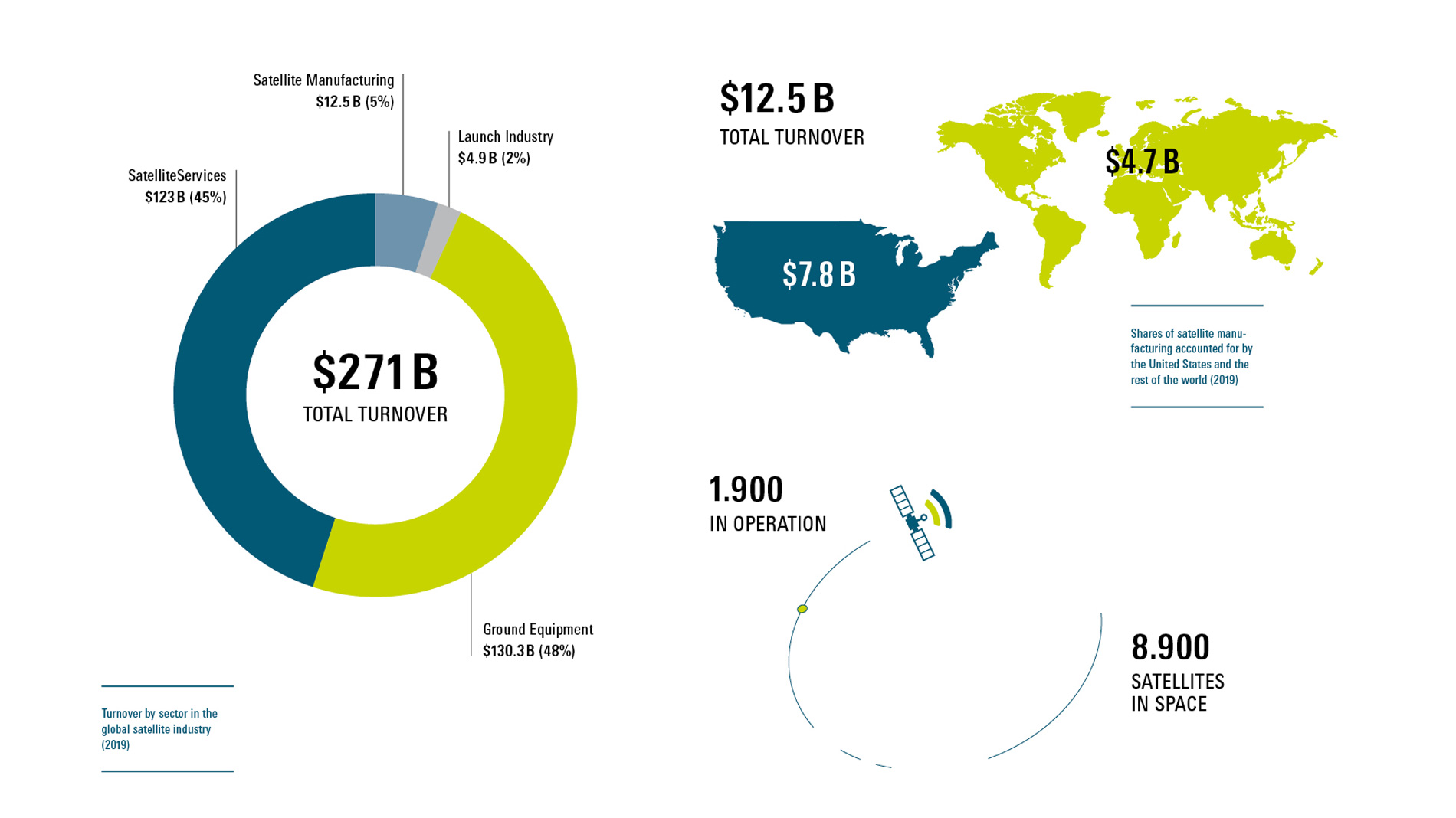
Infographic: feedbackmedia.de, Source: Satellite Industry Association, SIA
Overall, satellite production makes only a small contribution to the entire satellite sector of the aerospace industry. According to Brycetech, this satellite sector generated revenues of $217 billion in 2019, but that figure also includes ground equipment, TV, mobile services, and launch services.
Some 8,900 satellites have been launched into space since 1957, with 5,000 still orbiting the Earth and 1,900 of those still operational. Having ushered in a new era of rocket engineering, Elon Musk and SpaceX are now set to do the same for the satellite industry: The Starlink project, which aims to bring highspeed broadband internet even to rural areas (for a fee), has launched 1,318 satellites into the Earth’s orbit at an altitude of around 270 km [168 miles] since May 2019 (data correct as of March 24, 2021). This led to SpaceX becoming the world’s largest satellite operator very quickly indeed.
One Falcon 9 delivers 60 Starlink satellites into orbit. But despite its large number of satellites, Starlink has not significantly increased the volume of the exclusive satellite construction market. That’s because, with estimated manufacturing costs of $250,000 to $500,000 per unit, the 260 kg [570 lb] Starlink satellites are positioned toward the lower end of the market’s price range. Other satellites, such as those used in Earth observation, are competing in a whole other weight class due to their size alone. One of the largest satellites ever launched was the TerreStar-1 back in 2009, which weighs 6,910 kg [15,230 lb] and has solar panels with a span of 32 m [105 ft]. According to estimates from satellite phone provider Globalcom, a typical weather satellite costs around $290 million.
TREND TOWARD SMALLER SATELLITES
In addition to Starlink, the trend toward ever smaller satellites is giving the industry a boost too. Fired up by new applications in agriculture, energy, civil defense, or oil and gas, for example, the market for small satellites weighing under 500 kg [1,000 lb] is expected to grow strongly in the coming years. Allied Market Research analysts predict that this sector will grow from $3.6 billion in 2018 to $15.7 billion by 2026, an annual increase of about 20 percent. Contributing to this growth will be the Lightspeed project by Canadian satellite operator Telesat, which intends to launch a fleet of 298 satellites, each weighing 700 – 750 kg [1,543 – 1,653 lb], into orbit around the Earth over the next few years – Thales Alenia Space was awarded the contract for this work in February 2021.
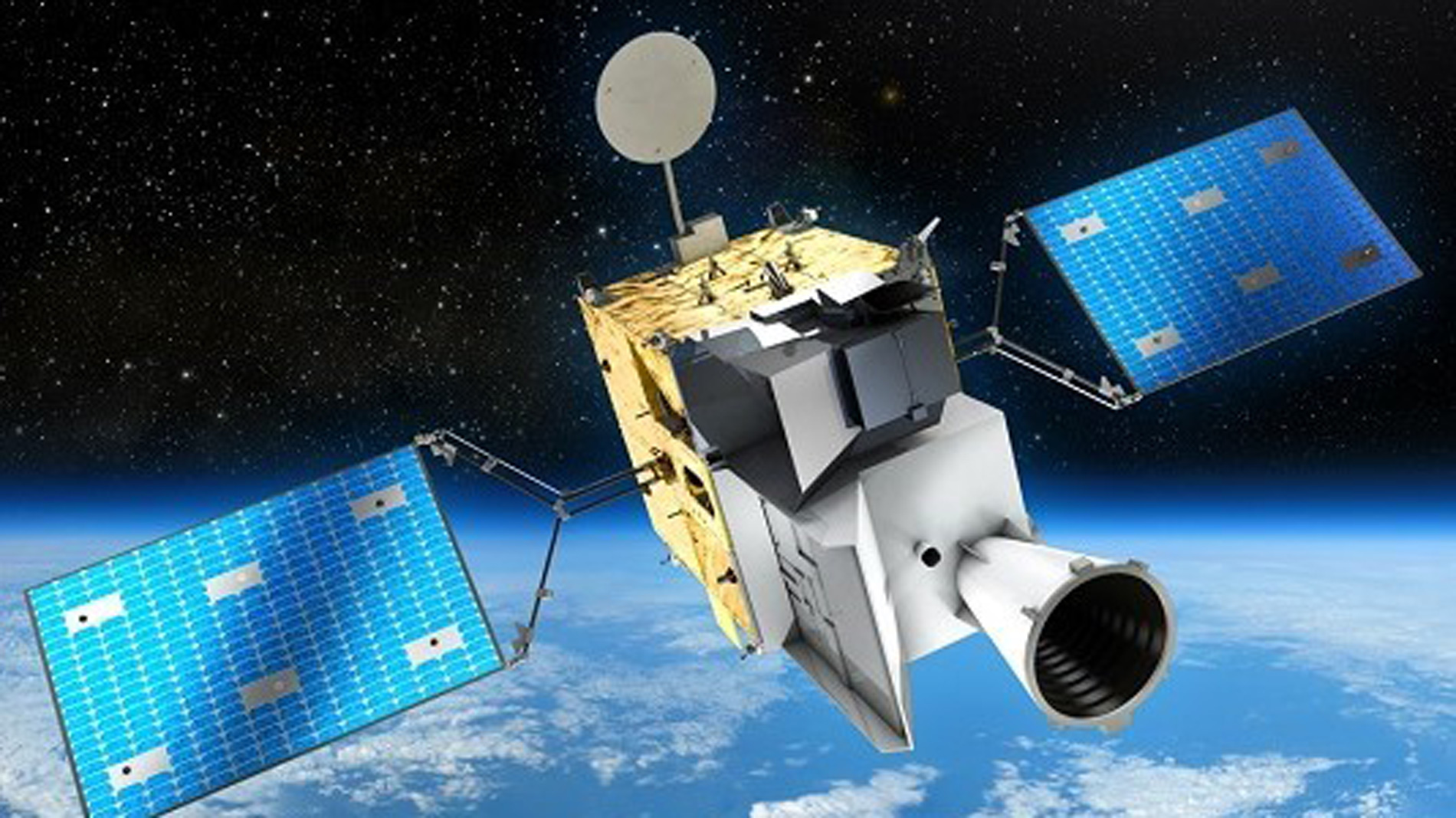
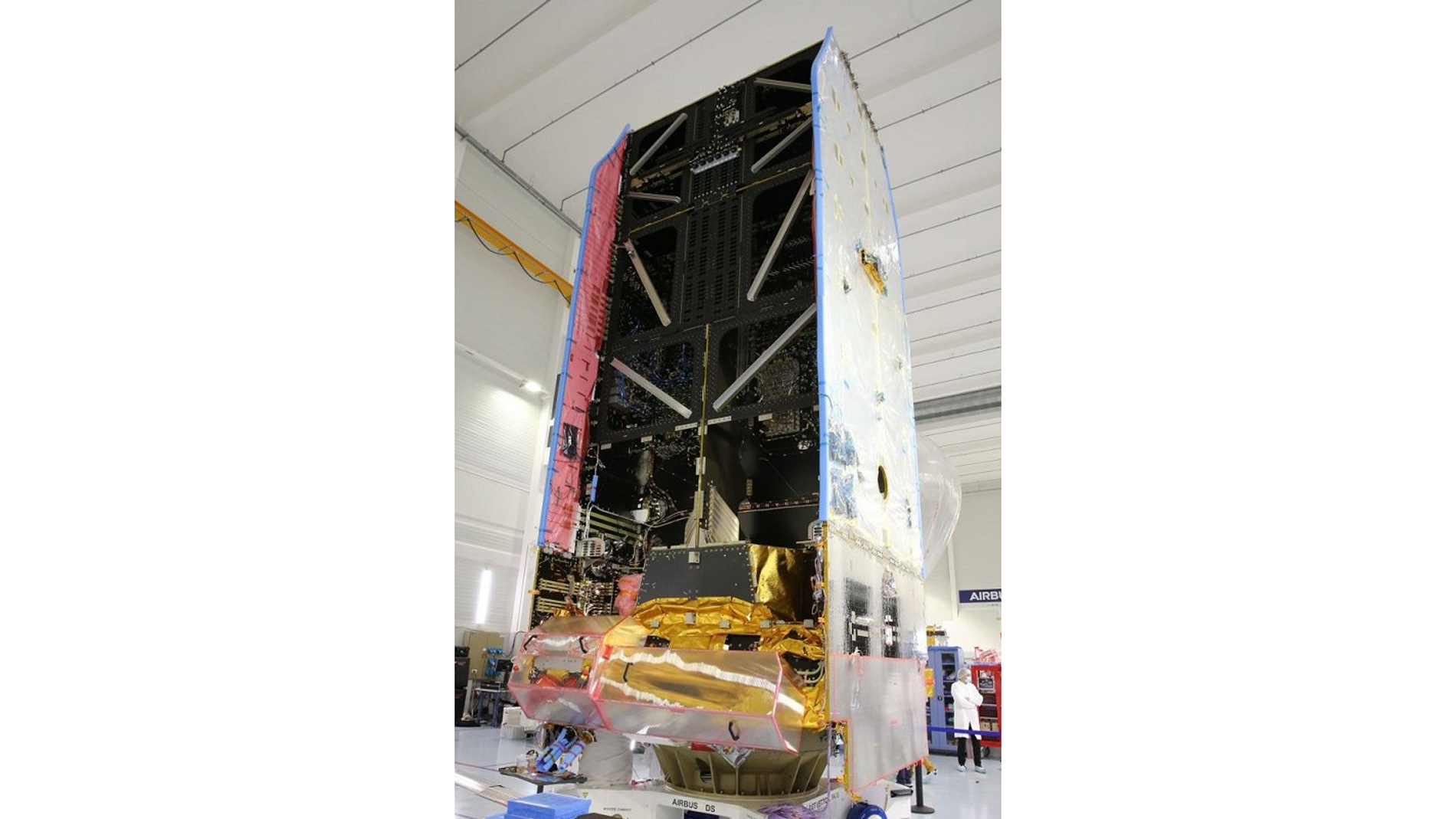
IT'S ALL ABOUT TIME
Generally speaking, it is the contracting entities, i.e., satellite operators such as ESA, Eutelsat, or Telesat, which determine a satellite's performance requirements. Manufacturers such as OHB System or Airbus Defence and Space develop the design, equip the satellites with the necessary instruments and software, and, if necessary, take care of other services such as the journey into space or mission control.
Contrary to popular belief, the main benefit of Additive Manufacturing in satellite construction does not always take the form of reduced weight – at least at present. "We won't say no to that benefit. But satellite weight has already been optimized, and the number of components that can be further optimized by Additive Manufacturing is limited," explained Mulser. Saving a few ounces on a large satellite does not really have much impact on its overall weight. No, where Additive Manufacturing actually offers a great advantage is in the design process. Improvements can be made to individual components much more easily and quickly than to milled parts, for example, which significantly reduces development time and costs. Mulser also appreciated the opportunity "to practice integral construction, that is, to integrate different functions into one component and thus save on joining and assembly steps."
Airbus expert Neal also highlighted this bonus of faster production: "We have speeded things up considerably compared to existing conventional waveguides. On average, we have halved the time it takes to produce waveguides with AM." Where a little over two years were spent working on the initial AM components, now the processes have been industrialized at Airbus Defence and Space it takes just a matter of months.
THE CHALLENGE OF EXTREMELY CLEAN SURFACES
In order to reap the benefit of these faster times, incredibly stringent demands must be met, especially in postprocessing. As an example of this, Neal referred to the smooth surface that waveguides need to have in order to achieve the required RF power. "Satellites are assembled in a cleanroom, the surfaces must be clinically clean," added Mulser. This means even the tiniest powder residues need to be removed, which requires scrupulous cleaning, especially of internal surfaces. But the additively manufactured components also need to have technical characteristics that meet the very particular requirements of space travel. These include the huge loads encountered during lift-off and the enormous temperature fluctuations that occur when satellites or parts thereof are illuminated by the sun or situated in the shade. OHB System, for instance, has developed connecting elements called cleats, which connect two sandwich panels and compensate for thermal deformations, to deal with this issue. "Their structural design means these cleats can only be manufactured additively," explained Mulser.
OUTLOOK: FIVE BECOME ONE
For Marco Mulser, stable manufacturing processes are the key to unlocking all the future potential for the satellite construction sector that is offered by Additive Manufacturing. "This includes, for example, establishing lattice structures in the components and forging ahead with functional integration." Airbus expert Andrew Neal also considered Additive Manufacturing to be vitally important for satellite production in the coming years. On the one hand, "the technology can now also be used as the basis for adjusting the payload." And, as well as providing new ways to speed things up, Additive Manufacturing enables production and assembly costs to be lowered even further. "Because, on average, one AM component will replace a part that was previously made up of five separate components."
Airbus Space and Defence
Airbus Defence and Space is a division of the Airbus Group, which generates revenues of around 10 billion euros and has approximately 34,000 employees. Its business areas cover military aviation and space systems, as well as sensors and communications technology. It is headquartered in Taufkirchen near Munich.
airbus.com
OHB System AG
OHB System AG is one of Europe’s three leading aerospace companies. The systems provider belongs to the listed hightech group OHB SE, where around 2,900 specialists and executives work on key European space programs. With two locations in Bremen and Munich and around 40 years of experience, OHB System AG specializes in high-tech solutions for space travel. These include low-orbiting and geostationary satellites for Earth observation, navigation, telecommunications, science, and space exploration, as well as systems for manned space flight, aerial reconnaissance, and process control systems.
ohb-system.de
Tags
- Aviation and aerospace