Text: Thomas Masuch; Fotos: Airbus Defence and Space, OHB System AG — 22.05.2021
Eigentlich ist die additive Fertigung wie gemacht für den Satellitenbau: Es geht um sehr geringe Stückzahlen, komplexe Designs und das Streben nach Gewichtseinsparung – alles Anforderungen, die dem Einsatz additiver Fertigung wie auf den Leib geschneidert sind. Kein Wunder also, dass bereits seit mehreren Jahren Satelliten mit 3D-gedruckten Bauteilen um die Erde kreisen. Wir haben im zweiten Teil unserer Serie »AM in der Space-Industrie« hinter die Kulissen geschaut, um zu erfahren, wie weit AM bereits im Satellitenbau verbreitet ist, welches Marktpotenzial damit verknüpft ist, welche Trends die Branche bewegen und vor welchen Herausforderungen die Satellitenbauer und ihre Dienstleister noch stehen.
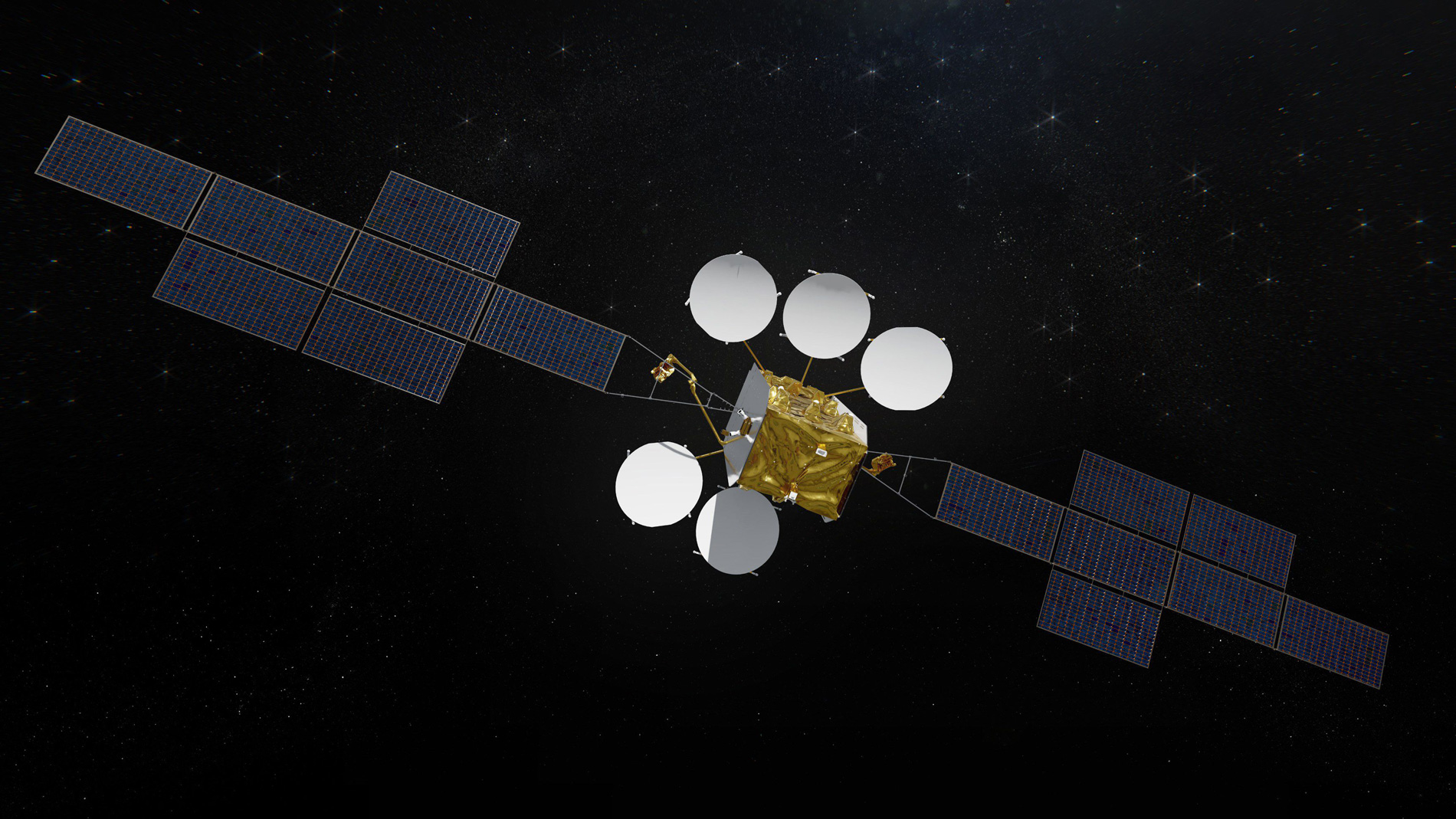
Bei zwei Hotbird-Satelliten, die Airbus Defence and Space derzeit für seinen Kunden Eutelsat fertigt, werden insgesamt 500 additiv gefertigte Einzelteile verbaut. Diese bestehen aus einer Aluminium-Silizium- Magnesium-Legierung (AlSi10Mg) und werden von zertifizierten Partnern im selektiven Laserschmelz- Verfahren (SLM) produziert. "Dabei gibt es mehr als 100 verschiedene Hohlleiterdesigns zusammen mit anderen Netzwerkdesigns. Die Hohlleiter leiten die Hochfrequenz-Signale um das Raumfahrzeug herum. Die Größe der Komponenten reicht von etwa 100 mm bis etwa 300 mm", erklärt Andrew Neal, Airbus-Experte für Additive Layer Manufacturing in Portsmouth, Großbritannien im Gespräch mit dem Formnext Magazin.
Auch beim Raumfahrtunternehmen OHB System AG beschäftigt man sich schon seit mehr als sechs Jahren mit der additiven Fertigung. "Zuerst war es ein Entwicklungsprojekt. Derzeit sind wir auf dem Stand, dass wir nicht nur bestehende Bauteile ersetzen, sondern ganz gezielt optimieren", so Marco Mulser, OHB-Technologiemanager für Additive Manufacturing. Im nächsten Jahr wird nach mehrjähriger Entwicklungszeit das erste von OHB System verbaute metallische AM-Teil ins All starten.
"Wir haben ein ganz anderes Arbeiten als in der Automobilindustrie oder auch als in der Luftfahrt."
Auch für ein weiteres Schwergewicht der Branche, Thales Alenia Space, steht AM schon seit Jahren weit oben auf der Agenda. Bereits 2015 hat das französische Unternehmen den Kommunikationssatelliten TurkmenAlem mit einer 3D-gedruckten Antenne aus Aluminium ausgestattet. 2017 wurden in 45 Kommunikationssatelliten additiv gefertigte Teile verbaut. Inzwischen werden in sämtlichen Kommunikationssatelliten von Thales Alenia Space 3D-gedruckte Antennenhalterungen und Reflektorhülsen eingesetzt.
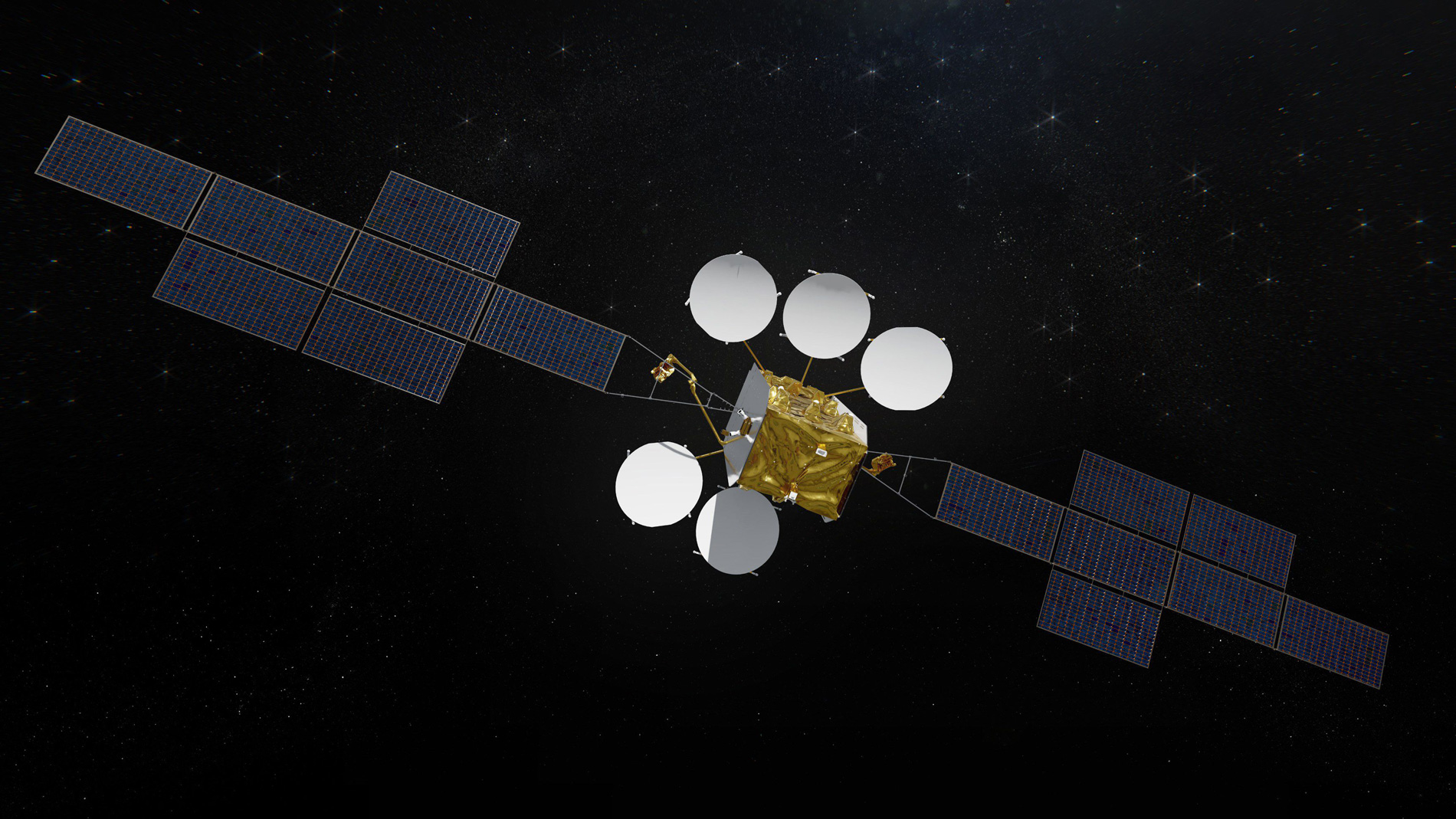
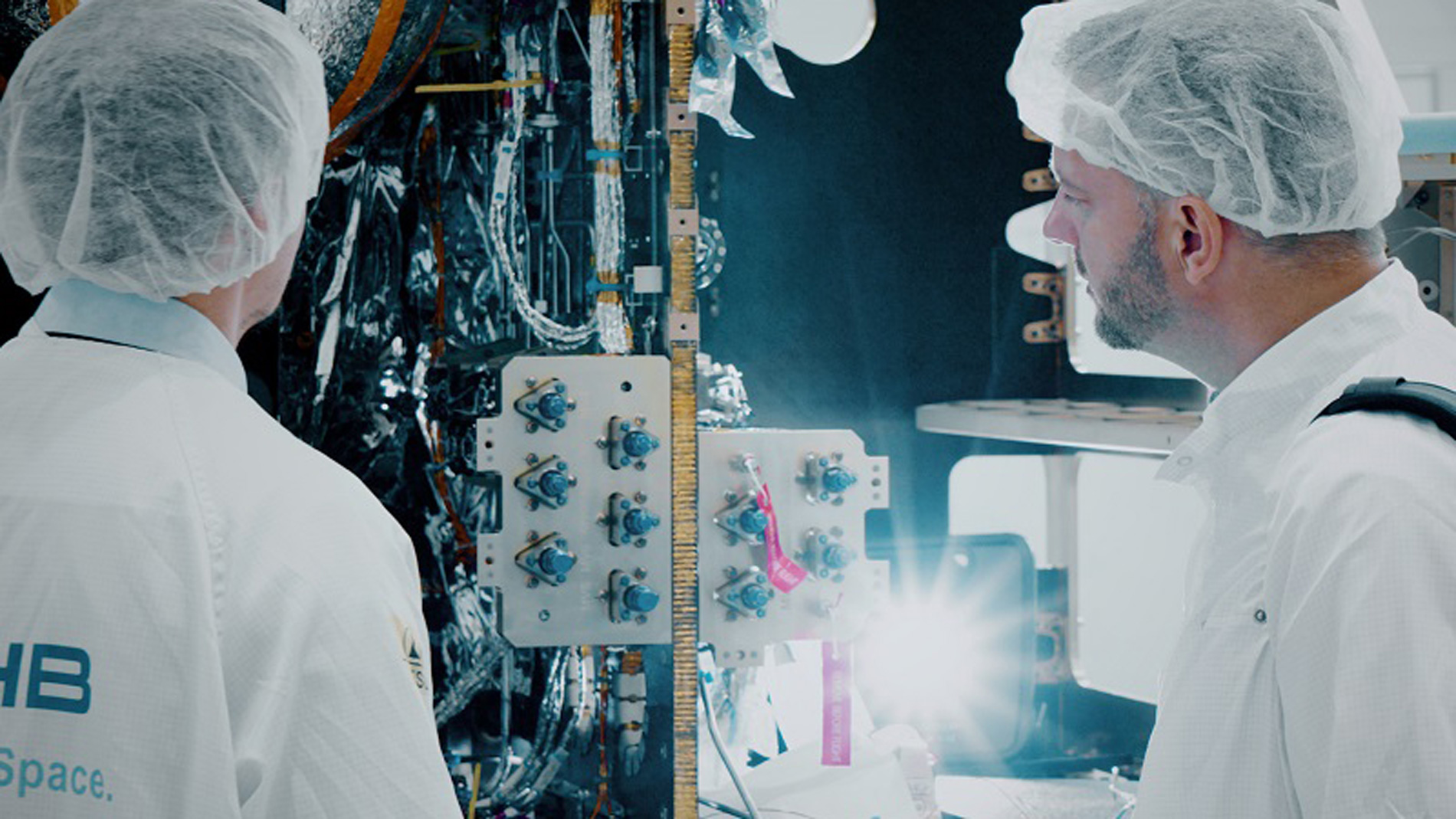
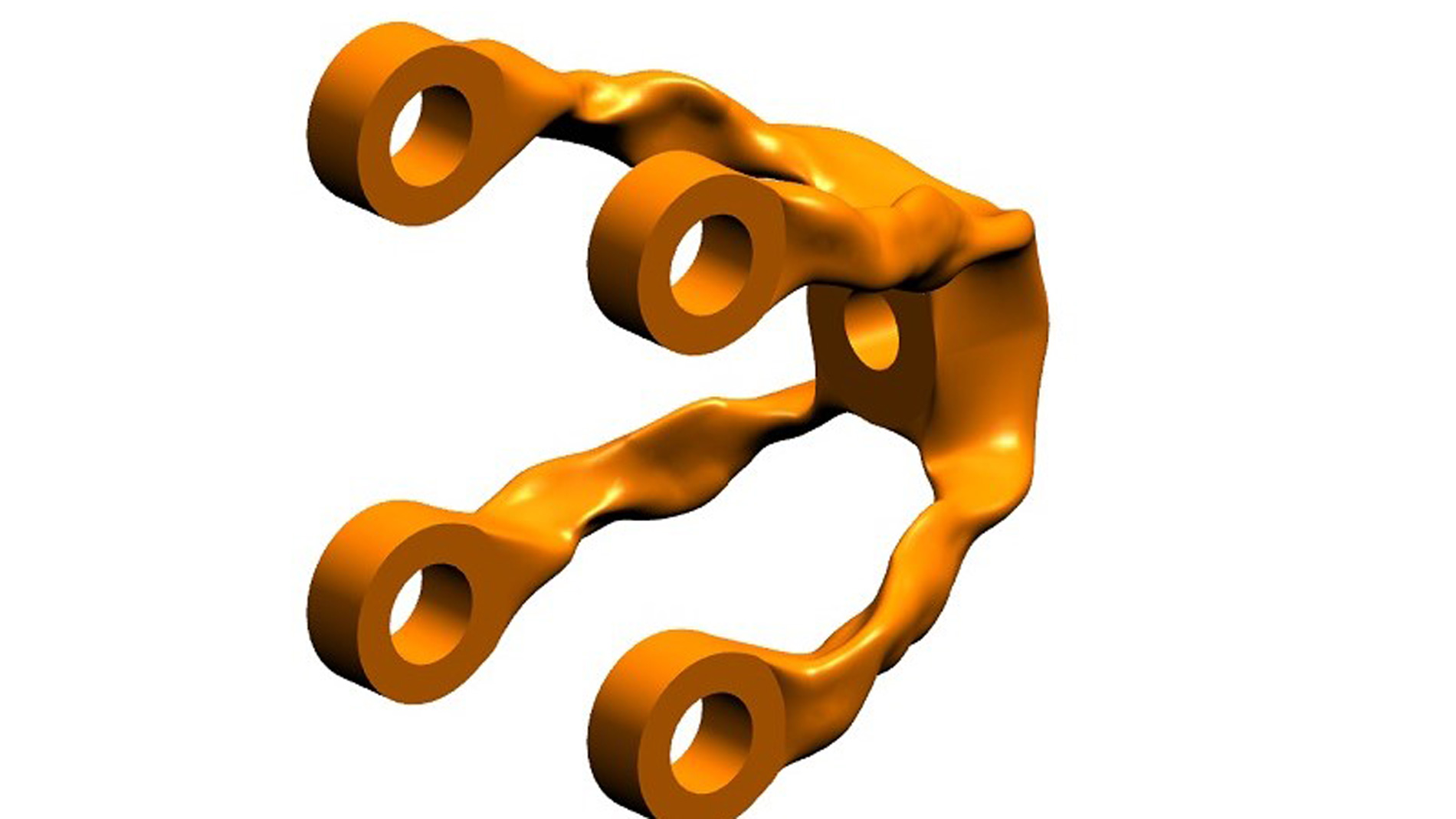
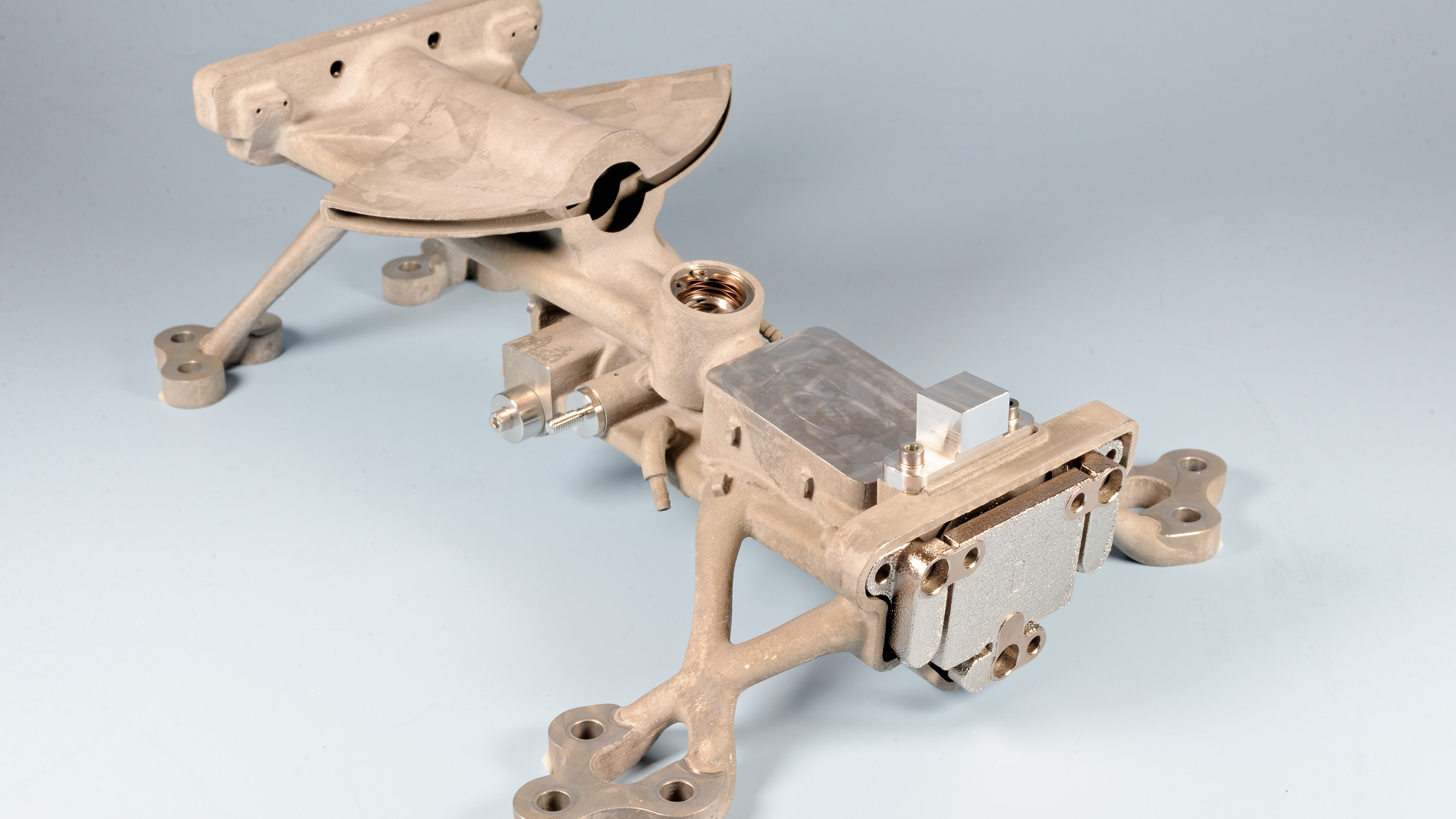
BESCHAFFUNG ÜBER DIENSTLEISTER
Die 3D-gedruckten Bauteile beziehen die OHB System AG und Airbus Defence and Space über Zulieferer. Diese haben "einen vollständigen Lieferanten- und Qualifikationsprozess durchlaufen", berichtet Neal. Und auch bei der OHB System wurde bereits vor vier Jahren beschlossen, 3D-gedruckte Teile ausschließlich über Lieferanten zu beziehen – so wie der Großteil aller Bauteile und Komponenten der Satelliten. "Wir wollen uns auf stabile Prozesse der Dienstleister verlassen", so Mulser. Dabei sieht der Ingenieur vor allem etablierte Unternehmen im Vorteil, "denn jahrelange Erfahrung kann man nicht so einfach aufholen". Auch bei der Qualitätssicherung greift OHB System auf externe Partner zu, "wobei wir gezielt auswählen, welche Technologie und welche Form der Qualitätsprüfung zum Einsatz kommt".
HOHES SICHERHEITSBEDÜRFNIS
Generell seien die Anforderungen an Zuverlässigkeit in der Satellitenfertigung extrem hoch, was teilweise redundante Lösungen erfordere. "Wir haben ein ganz anderes Arbeiten als in der Automobilindustrie oder auch als in der Luftfahrt. Denn wir können ein fehlerhaftes Teil nicht reparieren oder einen Rückruf starten", sagt Mulser. "Das bedeutet, dass der Fertigungsprozess sicher stehen und konstant wiederholbare Ergebnisse liefern muss." Die Weiterentwicklung im Prozess, sozusagen ein Learning by Doing, schließe das aus. Bei OHB System arbeiten die Ingenieure deshalb mit festen, zuvor verifizierten Prozessparametern und leiten daraus die Möglichkeiten ab, additive Fertigung als Produktionsmethode zu berücksichtigen und Bauteile entsprechend zu gestalten. "Mittlerweile haben wir ein sehr klares Bild, für welche Anwendungen das funktioniert ", so Mulser.
BISHER RECHT SOLIDE BRANCHE
Mit ihrer hochkomplexen Technologie und den langen Entwicklungszeiten war die Satellitenfertigung in der Vergangenheit eigentlich eine recht solide Branche. Auch wenn der Markt in Abhängigkeit von einigen Großprojekten schwankte, wuchs er im Schnitt recht zuverlässig im einstelligen Bereich. In den Jahren 2014 – 2018 lag der Umsatz der Satellitenproduktion bei 16,2 Mrd. US-Dollar (Quelle: Satellite Industry Association, SIA), wobei mehr als die Hälfte auf die USA entfiel. Im Jahr 2019 fanden laut SIA sogar 62,4 Prozent der weltweiten Satellitenfertigung in den USA statt.
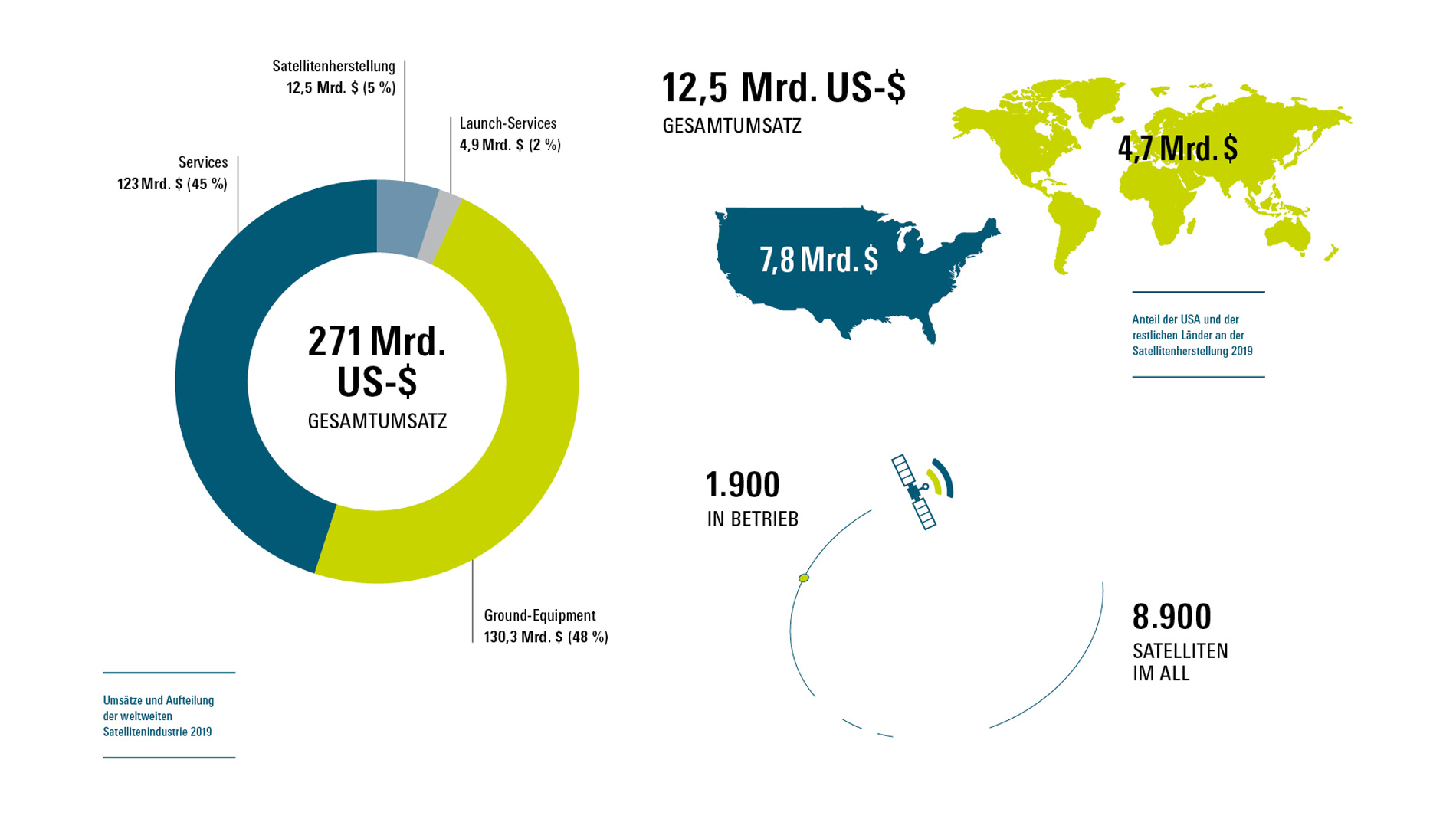
Infografik: feedbackmedia.de, Quelle: Satellite Industry Association, SIA
Insgesamt steuert die Satellitenfertigung damit nur einen kleinen Teil zum gesamten Satellitensektor der Raumfahrtindustrie bei. Diese erwirtschaftete 2019 laut Brycetech einen Umsatz von 217 Mrd. US-Dollar, umfasst aber auch die Bereiche Ground Equipment, TV, Mobile Services und Launch Services.
Seit 1957 wurden rund 8.900 Satelliten ins All geschossen, 5.000 kreisen noch in einer Umlaufbahn um die Erde, 1.900 sind noch in Betrieb. Ähnlich wie im Raketenbau hat Elon Musk mit SpaceX auch in der Satellitenbranche ein neues Zeitalter eingeläutet: Mit dem Starlink- Projekt, das gegen entsprechende Bezahlung eine schnelle Internetverbindung auch in ländliche Gebiete bringen soll, wurden seit Mai 2019 bereits 1.318 Satelliten in rund 270 km Höhe im Erdorbit platziert (Stand 24.03.2021). Damit ist SpaceX in Kürze zum größten Satellitenbetreiber geworden. Eine Falcon 9 liefert 60 Starlink-Satelliten im Orbit ab.
Trotz der Menge an Satelliten hat Starlink das Volumen des exklusiven Satellitenbau- Marktes nicht entscheidend vergrößert. Denn mit geschätzten Herstellungskosten von 250.000 bis 500.000 US-Dollar pro Stück sind die 260 kg schweren Starlink-Satelliten eher in der unteren Preisregion des Marktes angesiedelt. Andere Satelliten, etwa zur Erdbeobachtung, treten allein schon aufgrund ihrer Größe in einer anderen Gewichtsklasse an. Einer der größten bisher gestarteten Satelliten ist Terre Star-1 aus dem Jahr 2009, der 6.910 kg wiegt und dessen Solarpanels eine Spannweite von 32 m haben. Die Kosten für einen typischen Wettersatelliten liegen nach Schätzungen von Globalcom, einem Anbieter von Satellitentelefonen, bei rund 290 Mio. US-Dollar.
TREND ZU KLEINEREN SATELLITEN
Neben Starlink gibt auch der Trend zu immer kleineren Satelliten der Branche zusätzlichen Schub. Angefeuert von neuen Anwendungen zum Beispiel in der Landwirtschaft, im Energiesektor, im Zivilschutz oder im Öl-und- Gas-Sektor soll der Markt für Kleinsatelliten mit einem Gewicht unter 500 kg in den kommenden Jahren kräftig wachsen. Die Analysten von Allied Market Research prognostizieren für diesen Sektor ein Wachstum auf 15,7 Mrd. US-Dollar im Jahr 2026, was einem jährlichen Zuwachs um etwa 20 Prozent seit 2018 entspricht, als der Umsatz noch bei 3,6 Mrd. US-Dollar lag. Dazu passt auch das Projekt Lightspeed des kanadischen Satellitenbetreibers Telesat, der in den nächsten Jahren eine Flotte von 298 Satelliten mit einem Gewicht von jeweils 700 – 750 kg in die Erdumlaufbahn bringen will – den Auftrag dafür erhielt im Februar 2021 Thales Alenia Space.
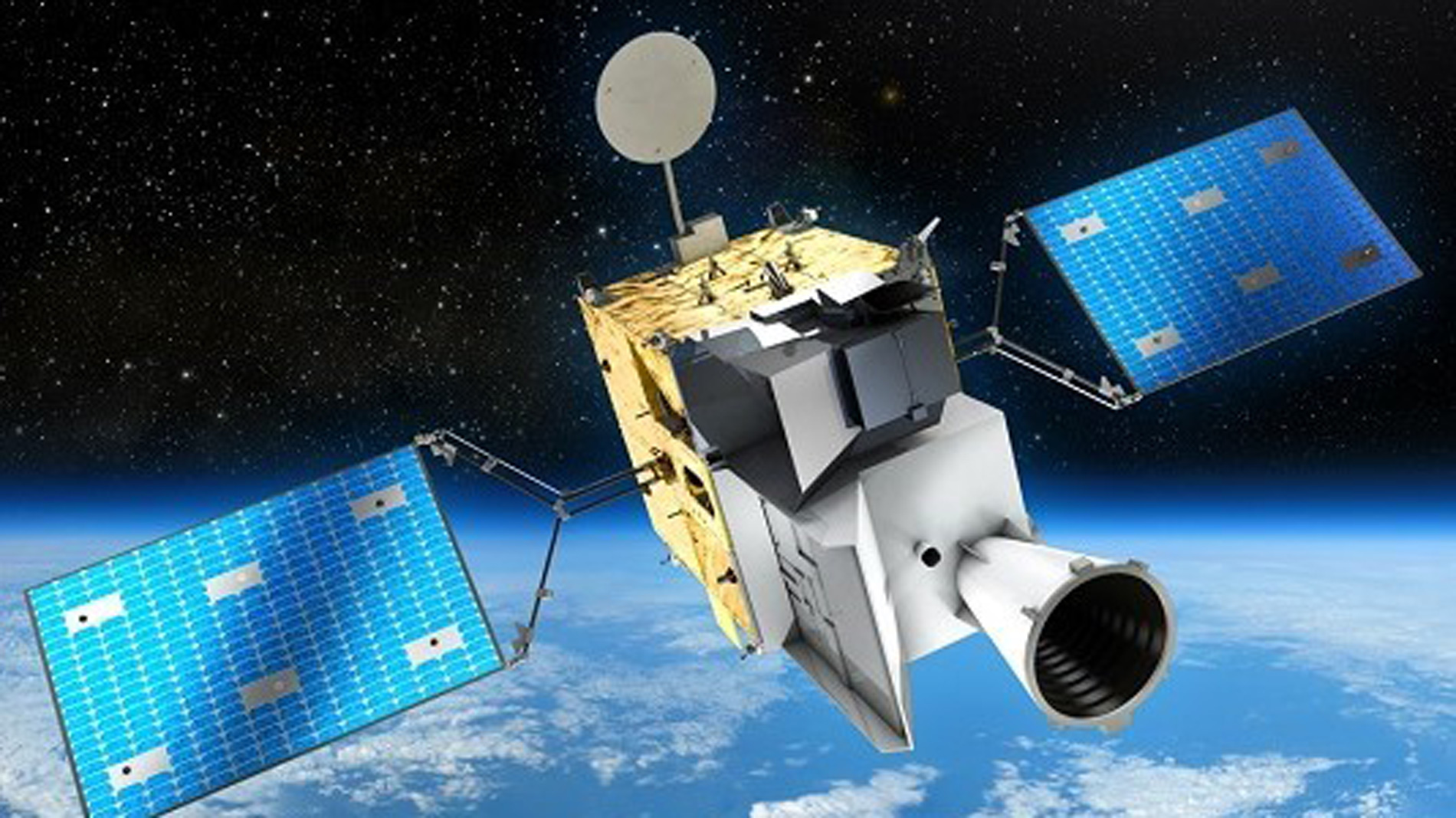
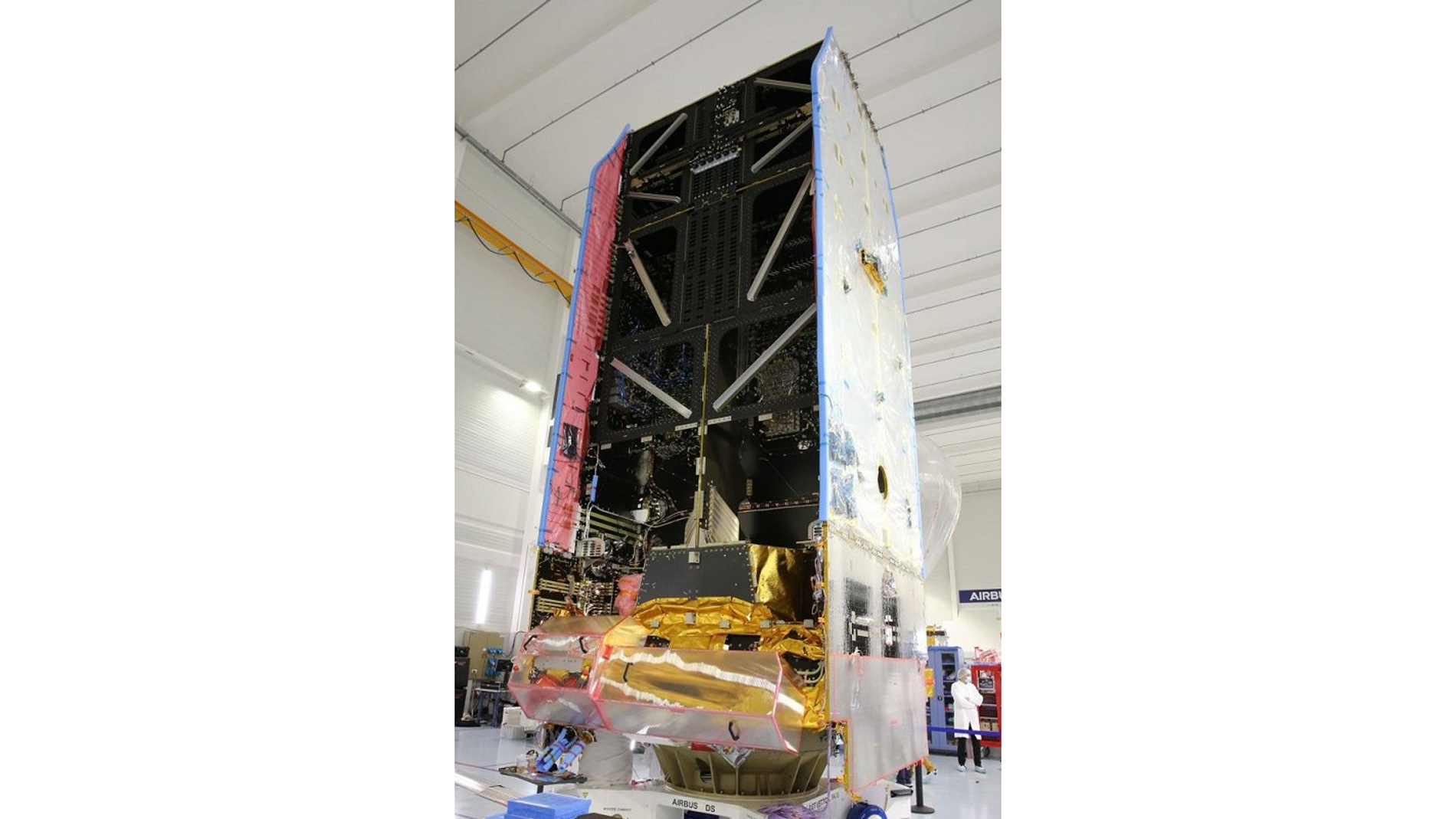
ES GEHT VOR ALLEM UM ZEIT
Generell bestimmen die Auftraggeber, also die Satellitenbetreiber wie die ESA, Eutelsat oder Telesat, die Anforderungen an die Leistung eines Satelliten. Die Hersteller wie OHB System oder Airbus Defence and Space entwickeln das Design, bestücken die Satelliten mit den nötigen Instrumenten und Software und kümmern sich bei Bedarf auch um weitere Serviceleistungen wie die Reise ins Weltall oder die Missionskontrolle.
Entgegen der üblicherweise vorherrschenden Meinung liegt der Hauptnutzen der additiven Fertigung im Satellitenbau nicht immer in der Gewichtseinsparung – zumindest derzeit. "Diesen Vorteil nehmen wir gern mit. Aber das Gewicht der Satelliten ist ohnehin schon optimiert, und die Zahl der durch additive Fertigung optimierbaren Bauteile ist begrenzt", erklärt Mulser. Bei einem großen Satelliten ein paar Hundert Gramm einzusparen sei nicht wirklich entscheidend für das Gesamtgewicht. Stattdessen biete die additive Fertigung einen großen Vorteil im Designprozess. Verbesserungen an einzelnen Bauteilen lassen sich deutlich einfacher und schneller umsetzen als zum Beispiel bei Frästeilen, was die Entwicklungszeit und damit auch die Entwicklungskosten deutlich reduziere. Mulser schätzt zudem die Möglichkeit, "integral zu bauen, sprich verschiedene Funktionen in einem Bauteil zu integrieren und so Füge- und Montageschritte einzusparen".
Auch Airbus-Experte Neal streicht diesen Vorteil der schnelleren Produktion heraus: "Wir haben im Vergleich zu den bestehenden konventionellen Hohlleitern erhebliche Zeitverkürzungen. Im Durchschnitt haben wir die Produktionszeit von Wellenleitern mit AM halbiert." Nachdem die Arbeiten an den ersten AM-Komponenten etwas mehr als zwei Jahre dauerten, ist es bei Airbus Space und Defence jetzt, wo die Prozesse industrialisiert sind, nur noch eine Frage von Monaten.
REINSTE OBERFLÄCHEN ALS HERAUSFORDERUNGEN
Um diesen Zeitvorteil realisieren zu können, müssen besonders in der Nachbearbeitung höchste Ansprüche erfüllt werden. Andrew Neal nennt hier zum Beispiel die glatte Oberfläche, die Hohlleiter haben müssen, um die geforderte HF-Leistung zu erreichen. "Satelliten werden im Reinraum montiert, die Oberflächen müssen klinisch sauber sein", ergänzt Marco Mulser. Das erfordere die Entfernung auch geringster Pulverreste, was besonders für innenliegende Flächen besonders hohe Anforderung an die Reinigung stelle.
Aber auch die technischen Eigenschaften der additiv gefertigten Bauteile müssen den besonderen Ansprüchen der Raumfahrt genügen. Dazu zählen etwa die hohen Belastungen beim Start sowie große Temperaturschwankungen, die entstehen, wenn Satelliten oder Teile davon von der Sonne beschienen werden oder im Schatten liegen. Hierfür hat OHB System zum Beispiel Verbindungselemente, sogenannte Cleats, entwickelt, die zwei Sandwichpaneele verbinden und thermische Deformationen ausgleichen. "Diese Cleats sind aufgrund ihres strukturellen Designs nur additiv herstellbar", erklärt Mulser.
AUSBLICK: EINS STATT FÜNF
Stabile Fertigungsprozesse sind für Marco Mulser die Basis dafür, um in Zukunft weitere Stärken der additiven Fertigung für den Satellitenbau auszuspielen. "Dazu zählt zum Beispiel, Lattice-Strukturen in den Bauteilen zu etablieren und die Funktionsintegration weiter voranzutreiben. "Auch Airbus-Experte Andrew Neal misst der additiven Fertigung eine entscheidende Bedeutung für die Satellitenfertigung der nächsten Jahre zu. Zum einen "ist die Technologie nun auch als Basis für die Nutzlastanpassung verfügbar". Zum anderen ließen sich neben weiteren Möglichkeiten der Zeitverbesserung die Kosten für Herstellung und Montage weiter reduzieren. "Denn im Durchschnitt ersetzt ein AM-Bauteil ein Teil, das vorher aus fünf einzelnen Komponenten bestand."
AIRBUS SPACE AND DEFENCE
Airbus Defence and Space ist ein Geschäftsbereich der Airbus Group und erzielt mit etwa 34.000 Beschäftigten einen Umsatz von rund 10 Mrd. Euro. Neben der militärischen Luftfahrt zählen Raumfahrtsysteme sowie Sensoren und Kommunikationstechnologie zu den Geschäftsbereichen. Hauptsitz ist Taufkirchen bei München.
airbus.com
OHB SYSTEM AG
Die OHB System AG ist eines der drei führenden Raumfahrtunternehmen Europas. Der Systemanbieter gehört zum börsennotierten Hochtechnologiekonzern OHB SE, in dem rund 2.900 Fach- und Führungskräfte an den zentralen europäischen Raumfahrtprogrammen arbeiten. Mit zwei Standorten in Bremen und München und rund 40 Jahren Erfahrung ist OHB System spezialisiert auf Hightech- Lösungen für die Raumfahrt. Dazu zählen erdnahe und geostationäre Satelliten für Erdbeobachtung, Navigation, Telekommunikation, Wissenschaft und Exploration des Weltraums ebenso wie Systeme für die astronautische Raumfahrt, Luftaufklärung und Prozessleittechnik.
Tags
- Luft- und Raumfahrt