by Thomas Masuch - 15 September 2021
In the start-up Mimete, the industrial group Fomas has built up a highly qualified powder manufacturer within a short period of time.
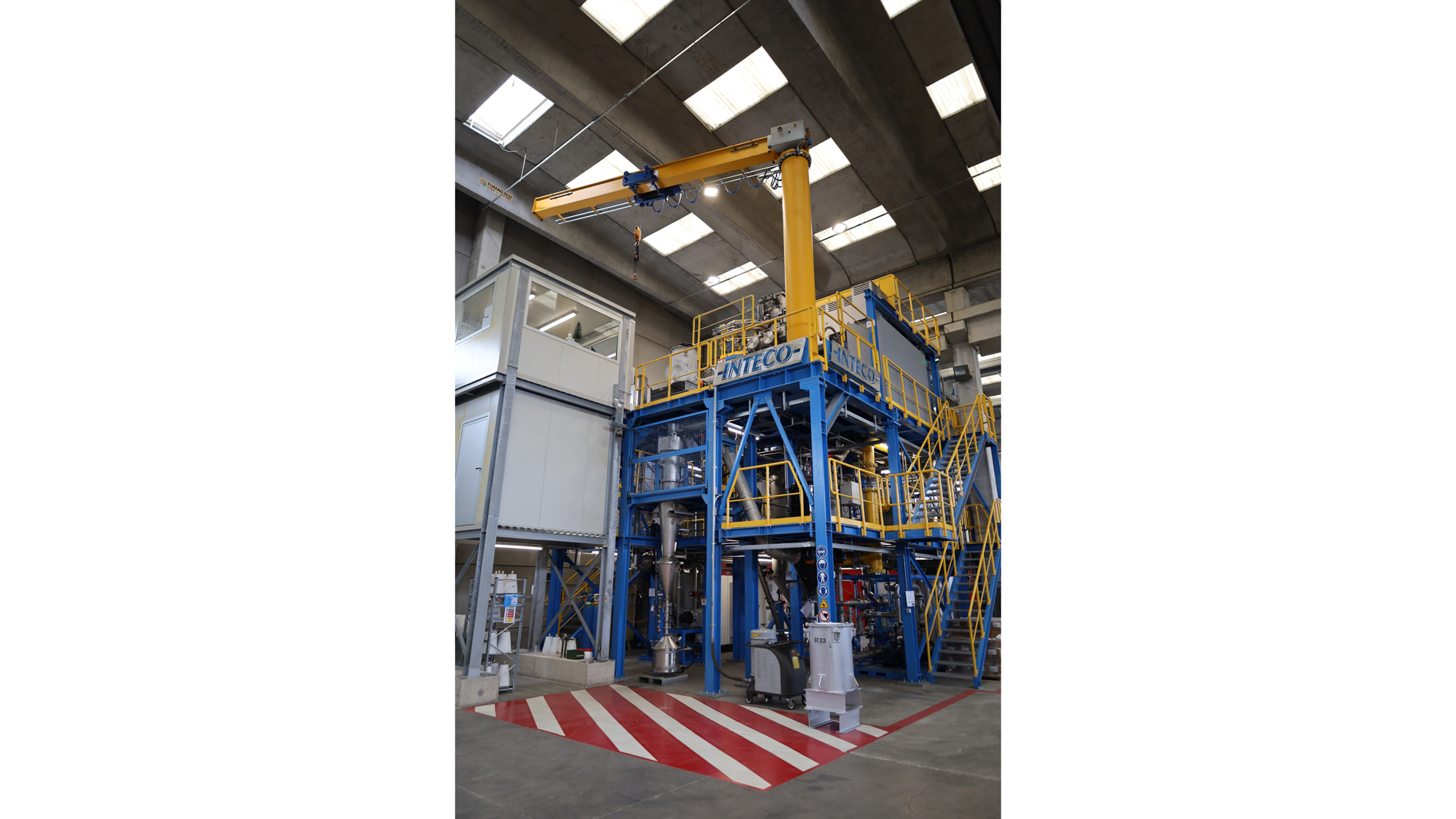
The neatly packed ingredients that will be used to prepare a metallic menu a little later are already lined up on the factory floor: small nickel ingots, a few bars of cobalt, and a few dozen kilograms of iron chips. Andrea Tarabiono, manufacturing manager at Mimete S.r.l., points up to a shiny metallic cylinder that’s raised almost all the way up to the hall’s ceiling by a huge steel frame. "There in the melting furnace, this is heated to between 1,600 and 1,800 degrees. The electrical induction currents enable the metals to mix very well," he explains. A little lower down, the liquid melt mixes with argon and falls as a metallic mist. At the bottom, the alloyed droplets – which have since cooled to form fine powder grains – are collected, separated from the gas, and taken to the adjacent warehouse for further processing (e.g. sieving, quality control, and packaging).
The production of metal powder at Mimete in Biassono, Italy, is by no means limited to atomization in the VIGA (Vacuum Induction Gas Atomizer) machine that operates 12 meters above the ground. From the delivery of raw materials to packaging, samples are regularly brought in for examination in a laboratory located in a separate room of the production hall. "This is the only way we can ensure that the powder meets our strict quality specifications and can be used in customers' applications afterwards," says Francesca Bonfanti, technical development manager at Mimete.
The lab at Mimete plays a crucial role – in the center image, Francesca Bonfanti examines a sample. Pictures: Thomas Masuch
From heavy industry to AM powder
Mimete, a start-up founded four years ago that has been operating near the world-famous Formula 1 circuit in Monza since 2019, focuses on the production of metal powders for Additive Manufacturing. It was set up by the Fomas Group, which has been forging heavy-industry components from steel and other alloys for decades at its headquarters in Osnago barely 20 kilometers away. For Fomas and the 1,450 people it employs around the world, the fast-growing Additive Manufacturing of metal parts "appeared to be both a threat and an opportunity" according to Magda Perez Gila, the group’s corporate communications manager.
Besides pouring significant resources into Mimete’s modern powder atomization system in Biassono, Fomas has thus invested in an elaborate production process that includes the aforementioned laboratory, which is equipped with the latest instruments. Mimete employs a young and high-powered team of 15 employees, some of whom previously worked at Fomas, and it also has some of its parent company’s departments (such as marketing, accounting, and sales) at its disposal thanks to their close proximity.
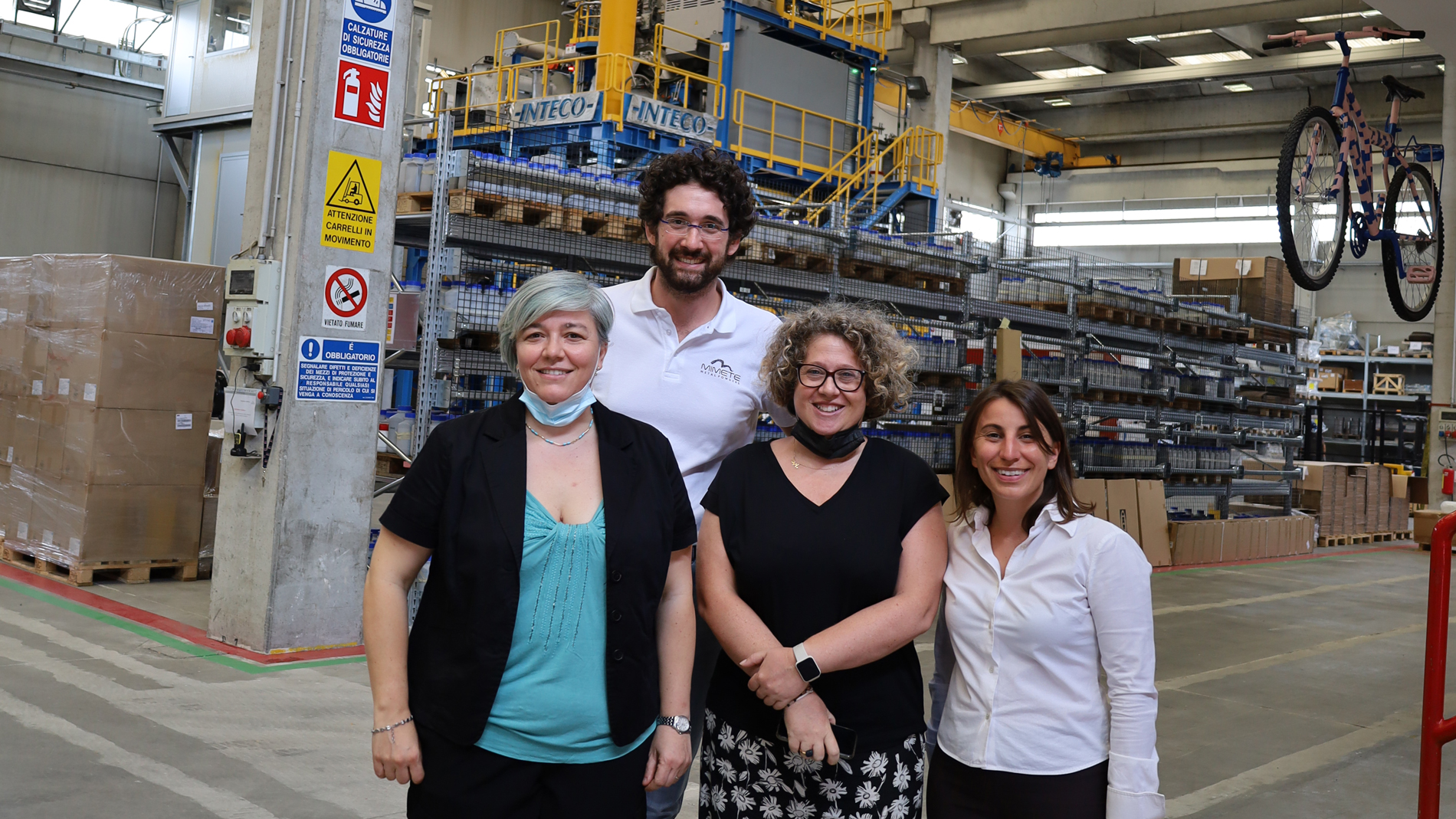
At Mimete, the prevailing atmosphere is a mix of youthful team spirit and professional cooperation. Even though the company’s team is still quite small, its processes are reminiscent of a well-established industrial group, and they consistently demonstrate the close relationship Mimete has with its parent company. Occupational safety, for example, is a top priority: As a visitor, you’re only allowed into production areas wearing a helmet, a high-visibility vest, and safety shoes – and only after watching a detailed video on safety guidelines. In addition, access to the laboratory, the packaging department, or the VIGA machine is only permitted to those who also work there. "We also like to go out together in the evening," explains Andrea Tarabiono, "but here in the production hall, we do our best to maintain the highest level of professionalism."
A certain level of quality takes a certain amount of effort
Powder production in the VIGA, which generates up to 300 kilograms per batch and consumes up to 2,000 cubic meters of argon per hour, is by no means the end of the process. In containers filled with argon gas, the powder enters the post-processing department, where it is sieved, then rotated in a container for homogenization purposes, and later packaged. "In the quality assurance system we’ve implemented, we take samples after each production step and analyze them," says Andrea.
An important component of Mimete’s complex production process is its laboratory, where powders are examined using XRF, ICP-OES, an automatic image analyzer, a Hall flowmeter, a laser diffraction analyzer, and various other techniques and devices. "Among other things, this allows us to identify the chemical elements in the samples, the granularity of the powder, and powder flowability, which is crucial for additive production," says Francesca Bonfanti. These extensive checks result in a workflow that takes 10 days to proceed from atomization to packaging.
A large storage area for raw Materials (left):
From atomization to eventual shipping, the powder is hermetically sealed
off from the outside air. Pictures: Thomas Masuch
In addition to their own samples, the lab staff examine the raw materials that are delivered. "We get them from certified partners, but also check them again ourselves to make sure no defects find their way in,” Francesca continues.
Mimete’s high quality standards in production also require many other details, including the three hours it can take to fill the company’s sieving machine with argon gas. "It’s far more involved than simply opening a valve," explains Andrea Tarabiono. The gas can also be heated to 500 degrees for atomization to further improve the quality of the powder. Even the quality of the bottles into which the powder is later filled and shipped has to meet special requirements: They’re also filled with argon, after all, which forms a hermetic seal between the powder and the outside air from atomization to shipping.
Creative naming
In going to all these lengths, Mimete wants to secure a place for itself as a supplier of high-quality powders among the numerous material providers in AM. The standard powders it offers are divided into the product groups Mars, Venus, and Neptune. The name of the company itself also stems from one of its founders’ creative ideas: It references the Italian writer and chemist Primo Levi, who published a collection of short stories (Storie naturali) back in the 1960s that described a machine – the Mimete – that was capable of cloning any object or living being.
Quality control and raw material: Mimete also tests the stability of components made from its powder. The raw materials used for atomization include loose chips or rods of metal. Pictures: Thomas Masuch
The young company’s stable of customers already includes several OEMs (e.g. from the oil and gas and aerospace sectors), manufacturers of 3D printers, and research institutions. "We also produce for conventional material manufacturers that now want to sell their proven metals in powder form," reports Giulia Conti, who works in sales support at Mimete. Many customers have been in the market for a long time and know exactly what they want in terms of element composition and flow rate, for example. "For them, we produce powder that meets their precise specifications – certified, of course," Conti adds.
In addition to standard materials, the start-up has already achieved some initial success with the new alloys it’s developing. "For a manufacturer of 3D-printed tool inserts, we adjusted some parameters of a certain alloy in order to enhance the durability of tools," Francesca Bonfanti reports.
Plans for further development
Mimete currently manufactures around eight tons of powder at its factory in Biassono every month, and it plans to significantly increase that amount in the future. At its production facility, neatly demarcated open spaces already indicate the further investments will soon follow. Andrea Tarabiono has a fairly precise plan in mind in this regard, and also sees the company as having reached another milestone in its development: "After two years, we have a very clear sense of the further equipment we need and the suppliers that will be a good fit for us."
Over the summer, Mimete also made a somewhat smaller investment: A large olive tree was planted on the edge of the company premises that has since been enabling the company’s production and lab employees to enjoy their lunch breaks in the shade. If Mimete continues to grow at the same pace, it won’t be long before someone makes the connection between the tree and the subject of cloning!
FURTHER INFORMATION:
Tags
- Materials