von Thomas Masuch - 15.09.2021
Mit dem Start-up Mimete hat der Industriekonzern Fomas in kurzer Zeit einen hoch qualifizierten Pulverhersteller aufgebaut.
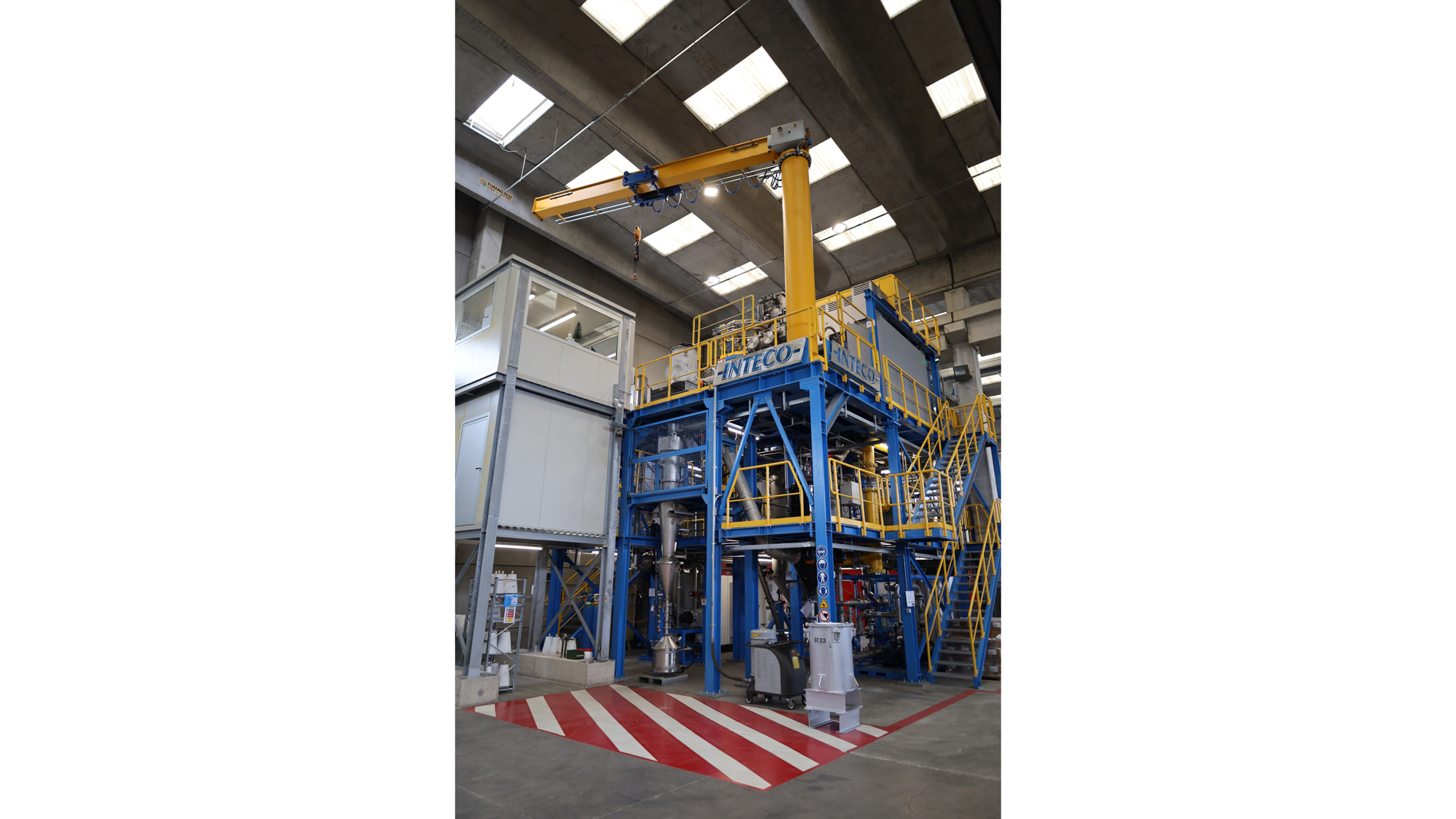
Auf dem Hallenboden stehen bereits säuberlich verpackt die Zutaten, aus denen wenig später das metallische Menü zubereitet werden soll: kleine Nickelblöcke, einige Stangen Kobalt, dazu ein paar Dutzend Kilogramm Eisenspäne. Andrea Tarabiono, Manufacturing Manager bei Mimete S.r.l., streckt den Arm in die Höhe und zeigt auf einen metallisch glänzenden Zylinder, der von einem riesigen Stahlgestell in luftiger Höhe getragen wird, wo er fast das Hallendach berührt. „Dort im Schmelzofen wird das auf 1.600 bis 1.800 Grad erhitzt, durch die elektrischen Induktionsströme vermischen sich die Metalle sehr gut“, erklärt er. Etwas tiefer vermischt sich die flüssige Schmelze mit Argon und fällt als metallischer Nebel in die Tiefe. Unten werden die Nebeltropfen, die inzwischen zu feinen Pulverkörnern erkaltet sind, aufgefangen, vom Gas getrennt und in das angrenzende Lager zur weiteren Verarbeitung (z. B. Siebung, Qualitätskontrolle und Verpackung) gebracht.
Dabei ist die Herstellung des Metallpulvers bei Mimete in Biassono bei weitem nicht auf die sogenannte Verdüsung in der 12 Meter hohen Viga-Anlage (Vacuum Induction Gas Atomizer) begrenzt: Von der Lieferung der Rohmaterialien bis zur Verpackung werden immer wieder Proben ins Labor, das sich in einem separaten Raum der Produktionshalle befindet, gebracht und untersucht. „Nur so können wir sicherstellen, dass das Pulver auch den strengen Qualitätsvorgaben entspricht und hinterher bei den Anwendungen der Kunden erfolgreich eingesetzt werden kann“, so Francesca Bonfanti, Technical Development Manager bei Mimete.
Das Labor spielt bei Mimete eine Schlüsselrolle: Francesca Bonfanti (M.) überprüft eine Probe. Bilder: Thomas Masuch
Aus der Schwerindustrie zum AM-Pulver
Das Start-up Mimete, das vor vier Jahren gegründet wurde, seit 2019 aktiv ist und seinen Sitz nahe der weltberühmten Formel-1-Strecke in Monza hat, konzentriert sich auf die Herstellung von Metallpulvern für die additive Fertigung. Aufgebaut wurde Mimete vom Industrieunternehmen Fomas Group, das seit Jahrzehnten geschmiedeten Stahl und andere Legierungen herstellt und seinen Hauptsitz im knapp 20 Kilometer entfernten Osnago hat. Für die Unternehmensgruppe aus der Schwerindustrie mit 1.450 Mitarbeitern weltweit erschien die schnell wachsende additive Fertigung von Metallteilen „als Bedrohung und Chance zugleich“, so Magda Perez Gila, Communication Manager Corporate von Fomas.
So hat Fomas in Biassono nicht nur kräftig in eine moderne Pulververdüsung investiert, sondern auch in einen aufwendigen Produktionsprozess einschließlich eines mit modernsten Gerätschaften ausgestatteten Labors. Mimete beschäftigt ein junges, schlagkräftiges Team von 15 Mitarbeitern, die teilweise zuvor bei Fomas beschäftigt waren, und kann durch die räumliche Nähe auch einige Abteilungen des Mutterkonzerns nutzen (z. B. Marketing, Buchhaltung und Verkauf).
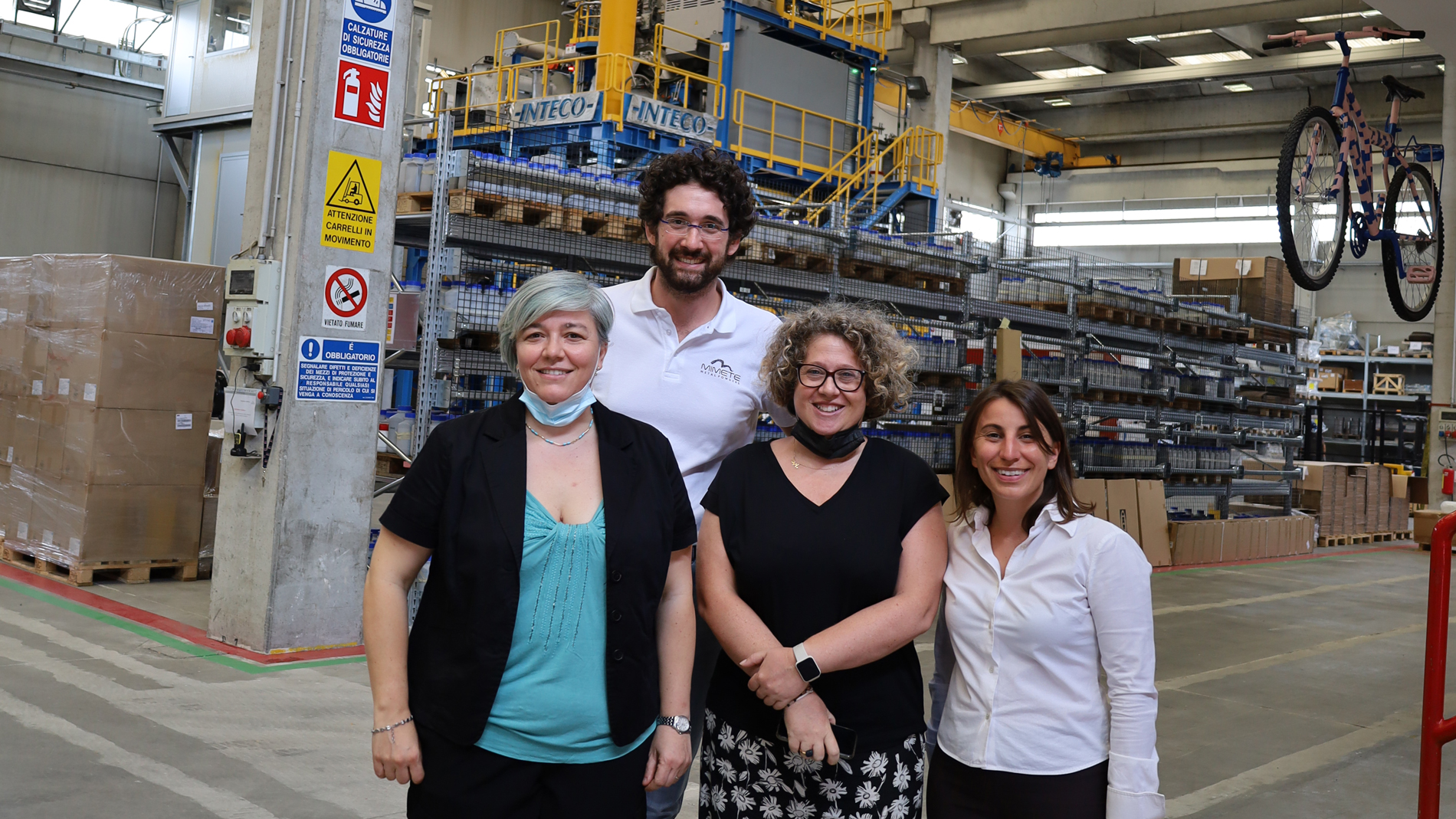
Bei Mimete herrscht eine Mischung aus jugendlichem Teamgeist und professioneller Kooperation. Auch wenn das Team noch recht klein ist, erinnern die Abläufe an einen eingespielten Industriekonzern und zeigen immer wieder die enge Beziehung zur Konzernmutter: Arbeitsschutz wird großgeschrieben; als Besucher darf man nur mit Helm, Warnweste und Sicherheitsschuhen in die Produktion – und erst nachdem man sich einen ausführlichen Film mit Sicherheitshinweisen angesehen hat. Zudem ist der Zugang zum Labor, zum Postprocessing oder zur Viga-Anlage nur denjenigen erlaubt, die auch dort arbeiten. „Wir gehen abends gern auch mal mit allen Kollegen zusammen aus“, erklärt Andrea Tarabiono, „aber hier in der Produktionshalle verfolgen wir höchste Professionalität.“
Hoher Aufwand für hohe Qualität
Mit der Produktion des Pulvers in der turmhohen Viga-Anlage, die bis zu 300 Kilogramm Pulver pro Charge schafft und dabei bis zu 2.000 Kubikmeter Argon pro Stunde verbraucht, ist der Prozess aber längst nicht beendet: In mit Argon gefüllten Behältern gelangt das Pulver in die Postprocessing-Abteilung, wo es gesiebt, danach zwecks Homogenisierung einem Behälter rotiert und später verpackt wird. „Wir haben ein komplexes Qualitätssicherungssystem installiert; zwischen jedem Produktionsschritt nehmen wir Proben und analysieren sie“, erläutert Andrea Tarabiono.
Wichtiger Baustein im aufwendigen Produktionsprozess ist das Labor, in dem die Pulver mit zahlreichen technischen Geräten wie XRF, ICP-OES, automatischem Bildanalysator, Hall-Durchflussmesser oder einem Laserbeugungsanalysator untersucht werden. „Damit können wir unter anderem die chemischen Elemente in den Proben ermitteln, ebenso wie die Größe der Pulverkörner und die Fließfähigkeit des Pulvers, was für die additive Produktion von entscheidender Bedeutung ist“, so Francesca Bonfanti. Die aufwendigen Kontrollen sorgen auch dafür, dass der Prozess von der Verdüsung bis zur Verpackung fast zehn Tage dauern kann.
Umfangreiches Rohmateriallager (links). Die Pulver sind von der Verdüsung bis zum Versand hermetisch von der Außenluft abgetrennt. Bilder: Thomas Masuch
Neben den eigenen Proben untersuchen die Labormitarbeiter auch die Rohmaterialien, die angeliefert werden. „Wir bekommen diese von zertifizierten Partnern, überprüfen sie aber noch einmal selbst, um wirklich keine Fehler zuzulassen.“
Der hohe Qualitätsanspruch in der Produktion erfordert zudem viele weitere Details: So dauert es zum Beispiel bis zu drei Stunden, bis allein der Behälter für die Siebung mit Argon gefüllt ist. „Man macht da ja nicht nur einfach den Hahn auf, selbst das ist ein komplexer Prozess“, erklärt Andrea Tarabiono. Das Argon kann zudem für die Verdüsung auf 500 Grad erhitzt werden, was die Qualität des Pulvers weiter verbessern soll. Und selbst die Qualität der Flaschen, in denen das Pulver später abgefüllt und ausgeliefert wird, muss den besonderen Anforderungen entsprechen – schließlich sind auch diese mit Argon gefüllt, sodass das Pulver von der Verdüsung bis zum Versand hermetisch von der Außenluft abgetrennt ist.
Kreative Namensgebung
Mit dem hohen Aufwand will sich Mimete als Lieferant von qualitativ hochwertigen Pulvern einen festen Platz im Spektrum der zahlreichen Materialanbieter für AM sichern. Die Standardpulver sind dabei in die Produktgruppen Mars, Venus und Neptun unterteilt. Kreativität haben die Gründer auch beim Unternehmensnamen bewiesen, der auf den italienischen Schriftsteller und Chemiker Primo Levi zurückgeht, der in seinen Kurzgeschichten „Storie Naturali“ bereits in den 1960er-Jahren eine Maschine mit dem Namen Mimete beschreibt, die sämtliche Dinge (Sachen und Lebewesen) duplizieren bzw. klonen kann.
Qualitätskontrolle und Rohmaterial: Auch aus dem Mimete-Pulver gefertigte Bauteile werden auf ihre Festigkeit untersucht. Rohstoffe für die Verdüsung: Verwendet werden u. a. loses Metall oder Stangenmaterial. Bilder: Thomas Masuch
Als Abnehmer kann das junge Unternehmen bereits mehrere OEMs (z. B. aus den Sektoren Oil & Gas und Luftfahrt), Hersteller von 3D-Druckern und Forschungseinrichtungen nennen. „Zudem produzieren wir auch für konventionelle Materialhersteller, die ihre bewährten Metalle nun als Pulver verkaufen wollen“, berichtet Giulia Conti, Sales Support bei Mimete. Viele der Kunden sind bereits lange auf dem Markt und wissen genau, was sie wollen – zum Beispiel in Bezug auf die Zusammensetzung der Elemente und die Flussrate. „Für diese produzieren wir dann exakt das gewünschte Pulver, natürlich zertifiziert“, so Conti.
Neben den Standardmaterialien entwickelt das Start-up auch neue Legierungen und konnte damit bereits erste Erfolge erzielen: „Für einen Hersteller von 3D-gedruckten Werkzeugeinsätzen haben wir einige Parameter einer bestimmten Legierung so angepasst, dass sich die Haltbarkeit des Werkzeugs verlängerte“, berichtet Francesca Bonfanti.
Genaue Pläne für die weitere Entwicklung
Rund 8 Tonnen Pulver werden jeden Monat in der Werkhalle in Biassono produziert und in Zukunft sollen es noch deutlich mehr werden. In der Produktion deuten bereits sauber abgegrenzte Freiflächen darauf hin, dass hier bald weitere Investitionen folgen werden. Andrea Tarabiono hat dafür bereits einen recht genauen Plan im Kopf und sieht das Unternehmen auch an einem weiteren Entwicklungspunkt angekommen: „Nach zwei Jahren wissen wir nun recht genau, welches weitere Equipment wir benötigen; zudem können wir nun sehr gut einschätzen, welche Zulieferer gut zu uns passen.“
Ein kleineres Investment hatte das Unternehmen bereits im Sommer getätigt: Am Rand des Firmengeländes wurde ein großer Olivenbaum gepflanzt, in dessen Schatten die Kollegen aus Produktion und Labor ihre Mittagspause verbringen können. Wächst Mimete im gleichen Tempo weiter, muss der Olivenbaum sicherlich auch bald geklont werden.
MEHR INFOS UNTER:
Tags
- Werkstoffe und Halbzeuge
- Additive Fertigung