von Thomas Masuch - 15.09.2021
Wenn Reisende aus den USA, Asien und anderen Teilen der Welt nach San Daniele del Friuli kommen, sind sie meist auf der Suche nach rosa-bräunlichem Fleisch. Denn die Kleinstadt im äußersten Nordosten Italiens ist weltbekannt für ihren Schinken, der hier in einer klimatischen Komposition aus trockenen Alpenwinden und feuchten Brisen von der Adria reifen kann. Mit einer ganz anderen Art von Fleisch und Knochen beschäftigen sich dagegen die Besucher von LimaCorporate, denn das Unternehmen ist weltweit einer der führenden Anbieter von Implantaten und den dazugehörigen Instrumenten. Bei deren Produktion spielt die Additive Fertigung seit Jahren eine immer größere Rolle und hat längst die Schwelle zur Serienfertigung überschritten.
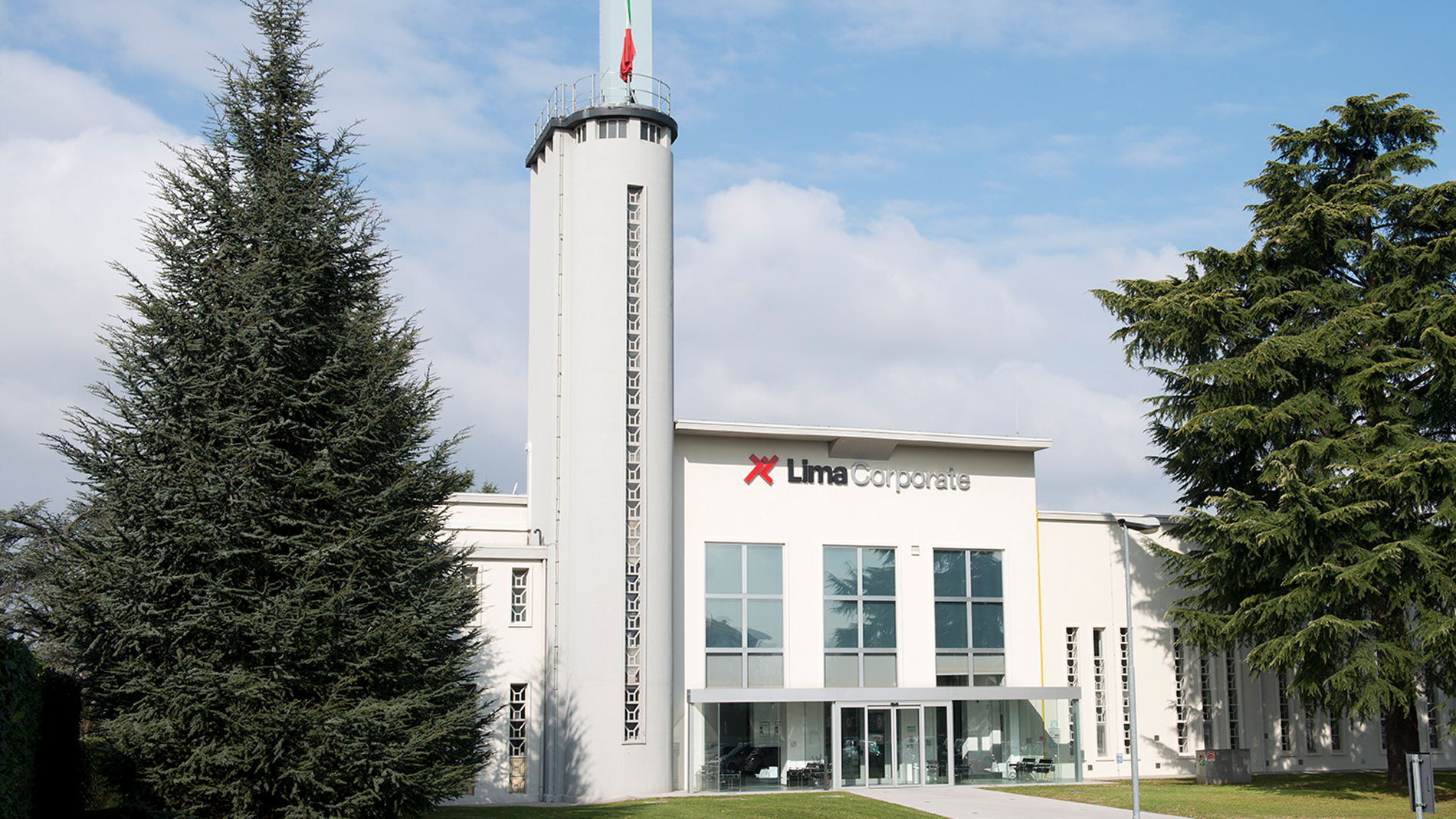
Wenn Michele Pressacco, Vice President Research and Development bei LimaCorporate, aus einem Bürofenster blickt, sieht er im Norden und Westen die Gipfel der Karnischen und Julischen Alpen, die die Grenze zu Österreich und Slowenien bilden. In dieser malerischen und relativ abgeschiedenen Lage hat das Medizintechnikunternehmen eine beeindruckende Erfolgsgeschichte geschrieben: In den vergangenen 20 Jahren ist die Mitarbeiterzahl von 70 auf über 1.000 gewachsen, und mit 25 Niederlassungen weltweit und einem Jahresumsatz von rund 200 Mio. Euro ist das Unternehmen inzwischen ein wichtiger Global Player.
Einen Teil dieser Erfolgsgeschichte hat das Unternehmen auch mit der Additiven Fertigung verfasst, die es schon seit mehr als 15 Jahren nutzt. „Der Metall-3D-Druck wurde zwar in den USA, Deutschland und Schweden entwickelt, aber Italien war eines der ersten Länder, in denen er industriell genutzt wurde – bei uns seit 2005“, erklärt Pressacco, der seit fast 20 Jahren bei LimaCorporate beschäftigt ist.
Über 100.000-mal 3D-gedruckt
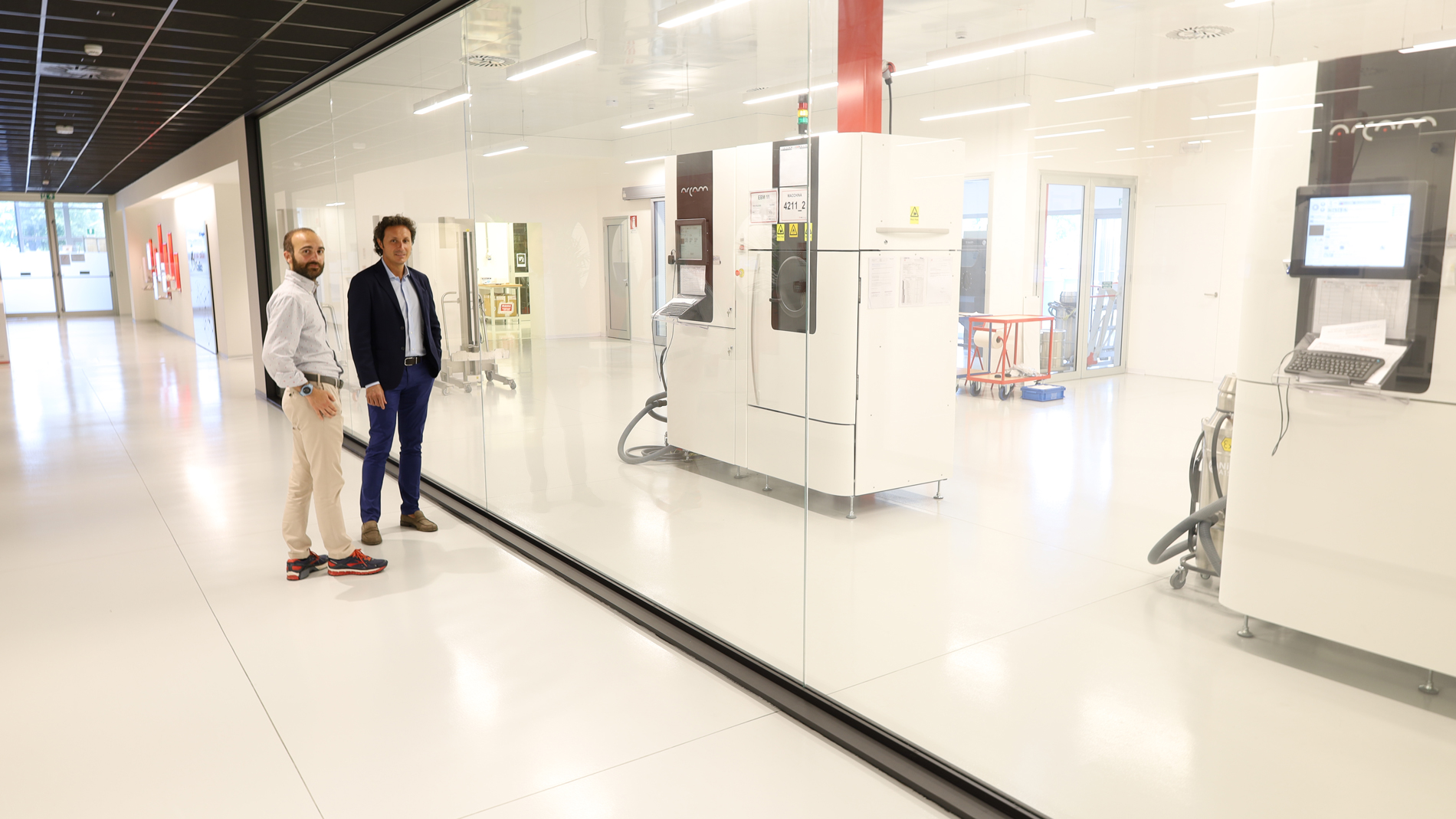
In San Daniele del Friuli entstanden im Pulverbettverfahren zunächst Standardimplantate, wobei bereits 2007 eines der bis heute weltweit erfolgreichsten additiv gefertigten Bauteile auf den Markt kam: eine Hüftgelenkpfanne aus einer Titanlegierung, die inzwischen mehr als 100.000-mal 3D-gedruckt wurde. „Die Komponente hat sich klinisch hervorragend bewährt und zeigt im Vergleich zu anderen auf dem Markt erhältlichen, konventionellen Produkten überragende klinische Leistungen, sodass wir sie auch nach 13 Jahren noch nicht austauschen mussten“, freut sich Pressacco. Aufgrund der umfangreichen Regularien im Medizinbereich müssten bei einer Änderung des Produkts zudem die aufwendigen Zulassungsvoraussetzungen nochmals nachgewiesen werden.
Die allein im 3D-Druck erzeugte Oberfläche der Hüftgelenkpfanne ist sehr porös und fördert damit das Einwachsen des Knochens. Diese additiv gefertigte Oberflächenbeschaffenheit, die das Unternehmen als Trabecular Titanium (TT) patentiert hat, ist seit vielen Jahren bei LimaCorporate Standard in der AM-Fertigung von Implantaten.
Seit 2007 auf dem Markt und inzwischen mehr als 100.000-mal 3D-gedruckt: die Trabecular-Titanium-Hüftgelenkpfanne (links). Daneben weitere 3D-gedruckte Produkte von Limacorporate. Bild: Limacorporate (1), Thomas Masuch (2)
Daneben produziert LimaCorporate auch spezielle Instrumente, die Chirurgen benötigen, um die Implantate im menschlichen Körper einzusetzen. Die Ausstattung der Krankenhäuser mit diesen Instrumenten ist sehr umfangreich, so werden zum Beispiel für Kniegelenkprothesen über 300 Instrumente in sechs Boxen geliefert. Die Instrumente bestehen überwiegend aus Edelstahl. Die Segmente, die letztendlich die künstlichen Gelenke berühren und bewegen, sind dagegen aus einer Titan- oder Cobalt-Chrom-Legierung, aus Keramik oder aus UHMWPE (ultrahochmolekulargewichtiges Polyethylen).
Zugleich legen Pressacco und sein Team bei der anspruchsvollen Gestaltung neben der Funktionalität auch ein Augenmerk auf das Produktdesign dieser oftmals sehr komplexen Instrumente. „Denn die Prothesen laufen weg, die Instrumente bleiben beim Chirurgen.“
Deshalb spiele beim Kauf von Implantaten und Instrumenten, bei dem die Chirurgen einen wichtigen Einfluss haben, nicht nur die Qualität und der Preis eine wichtige Rolle, sondern auch das Design: „Denn ein Chirurg arbeitet mit diesen Instrumenten jeden Tag, da sollten sie nicht nur funktional sein, sondern auch elegant und gut in der Hand liegen“, erklärt Pressacco. Und in diesem Bereich könne sich das Unternehmen aus San Daniele deutlich von der Konkurrenz unterscheiden: „Unsere Kunden sagen immer wieder, dass sie in unseren Instrumenten ein besonderes, italienisches Design entdecken.“
Emanuele Butazzoni, Laboratory Manager, überprüft einen der zahlreichen Versuche, in denen Haltbarkeit und Stabilität der Implantate getestet werden. Bilder: Thomas Masuch
Individuelle AM-Lösungen
Mittlerweile hat LimaCorporate das Portfolio an 3D-gedruckten Produkten deutlich ausgeweitet. Neben Standardimplantaten fertigt das Unternehmen auch individuell gestaltete Implantate, die vor allem bei Patienten mit sehr gravierenden Knochenschädigungen (z. B. bei Krebserkrankungen) zum Einsatz kommen – oftmals dann, wenn andere Lösungen nicht mehr ausreichen.
Bereits 2013 hat LimaCorporate diesen Geschäftsbereich unter der Marke ProMade zusammengefasst. Krankenhäuser erstellen die Scans, Designer in San Daniele erstellen daraus in Abstimmung mit den Chirurgen ein Design für ein Implantat und nach mehreren Iterationen gelangen wir zu einer finalen Lösung, die wir dann produzieren. Auch um den Designprozess noch effizienter zu gestalten, hat LimaCorporate 2018 TechMah Medical übernommen. Die digitalen Lösungen der US-Tochter ermöglichen eine weitestgehend automatisierte CT-Scan-Rekonstruktion mittels künstlicher Intelligenz.
Rauere Oberflächen als Vorteil
Das Design der Implantate und der zugehörigen Instrumente entsteht in der Firmenzentrale in San Daniele, wo LimaCorporate eine umfangreiche Produktentwicklung aufgebaut hat. Herzstück sind mehrere Räume, in denen sich zahlreiche AM-Anlagen reihen, die das Unternehmen stolz hinter bodentiefen Glasscheiben präsentiert. Hier entstehen Prototypen und Versuchsreihen aus Metall, aber auch Operationsschablonen oder andere patientenspezifische Instrumente, Produktionsmittel oder Bauteile aus Kunststoff, die im Labor verwendet werden. Im metallischen Pulverbett verfügt das Unternehmen auch über einige Laserstrahl-Anlagen, setzt aber hauptsächlich Elektronenstrahl-Anlagen ein. „Die Fertigung mit Elektronstrahl-Technologie hat sich für unsere Anforderungen sehr gut bewährt – sie ist etwas schneller, und dass dabei im Vergleich zu anderen Technologien rauere Oberflächen entstehen, kann bei spezifischen Implantaten sogar ein Vorteil sein“, erklärt Additive Manufacturing Manager Riccardo Toninato.
Neben den Implantaten Produziert das Unternehmen auch aufwendige Instrumente, die für die jeweiligen Operationen benötigt werden– hier eine sogenannte Führung zur unikompartimentellen Resektion des Schienbeins. Bilder: Thomas Masuch
Diesen Vorteil nutzt LimaCorporate auch am Fertigungsstandort in Sizilien, der über rund 15 Arcam-Maschinen verfügt. Auf diesen werden derzeit zwölf verschiedene Standardimplantate gefertigt, wobei die Stückzahl der 3D-gedruckten Standardimplantate seit den Anfängen der Additiven Fertigung bei LimaCorporate bereits die Zahl von 200.000 überschritten hat. Die Zahl der additiv gefertigten Produkte soll dabei weiter steigen, denn zehn Implantate und die dazugehörigen Instrumente durchlaufen gerade die Produktentwicklung in San Daniele. Mit dieser neuesten Generation von AM-gedruckten Implantaten will sich das Unternehmen einen wichtigen Wettbewerbsvorteil sichern. „Hierbei haben wir die Designs erstmals Topologie-optimiert, was die Leistung der Implantate in Bezug auf die Kraftverteilung vom Implantat zum Knochen, die Mikrobewegung und schließlich das Ermüdungsverhalten weiter verbessert“, so Pressacco.
Monatelange Testreihen
Entscheidend für Implantate ist, dass sie zuverlässig sind und aufgrund der hohen Reibung, die durch die poröse TT-Struktur entsteht, eine außergewöhnliche Verankerung bieten. Vor allem in den ersten Wochen nach der Operation ist die künstlich geschaffene Verbindung von entscheidender Bedeutung, wie Toninato erklärt: „Danach wird der Knochen zum Einwachsen in die Prothese veranlasst und verbindet sich auf diese organische Weise mit ihr. Studien zeigen, dass bereits nach 16 Wochen ein erhebliches Maß an neuem Knochenwachstum zu verzeichnen ist, das die sekundäre Fixierung des Implantats ermöglicht.“
Die Stabilität und Haltbarkeit der Implantate testet LimaCorporate in seinen Labors mit teilweise sehr langwierigen Testreihen, die auch mehrere Monate dauern können und bis zu 10 Mio. Bewegungen simulieren. In regelmäßigen Abständen wird dabei die Materialbeschaffenheit im Hinblick auf Gewichtsverluste und das Auftreten von Schäden oder Rissen untersucht.
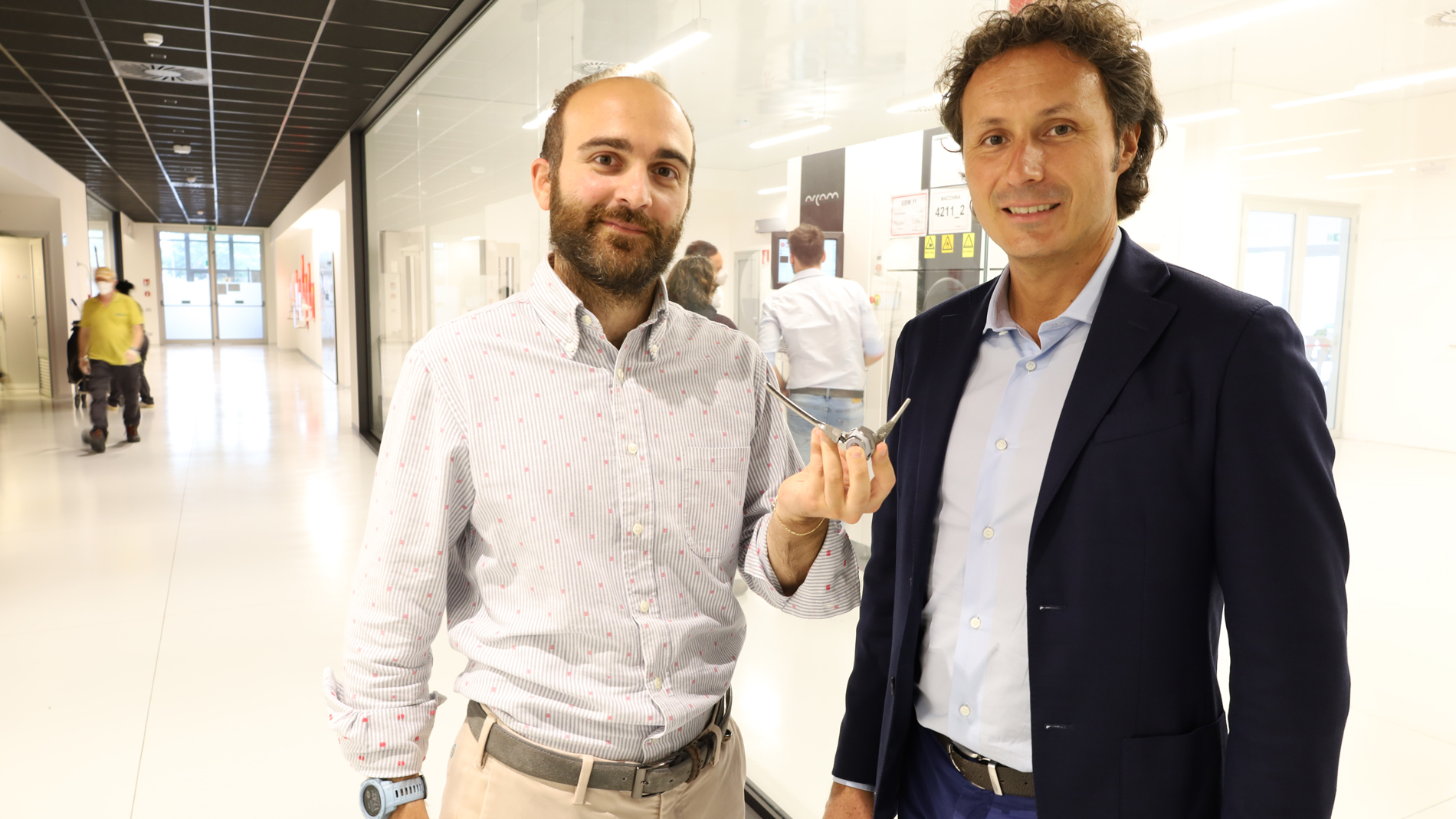
Solche Testreihen helfen auch, die Zuverlässigkeit additiv gefertigter Implantate für Schulter, Hüfte und Knie zu demonstrieren. „Denn trotz aller wissenschaftlicher Studien glauben immer noch viele Chirurgen, dass es zum Beispiel besser sei, konventionelle Knieimplantate mit Zement einzusetzen“, berichtet Pressacco. Dabei habe LimaCorporate „mehrfach nachweisen können, dass additive Prothesen stabiler sind, länger halten und einfach besser funktionieren“. Additive Aufklärungsarbeit leisten Pressacco und das Vertriebsteam deshalb zum Beispiel auf Kongressen, „aber am leichtesten sind Chirurgen überzeugt, wenn sie zu uns ins Unternehmen kommen und die den gesamten Prozess einschließlich Design, Produktion und Qualitätskontrolle sehen“.
Schnellere Produktentwicklung
Dass die Additive Fertigung die traditionelle Produktion bei Implantaten noch längst nicht überholt hat, zeigt sich in der konventionellen Produktionshalle in San Daniele. Hier reihen sich in einer ausgeklügelten und farblich getrennten Ordnung Fräsmaschinen und weitere Anlagen zur Metallbearbeitung. Die Stückzahlen liegen dabei deutlich über denen der 3D-Produktion auf Sizilien.
Aber auch der konventionelle Sektor profitiert vom 3D-Metalldruck, zum Beispiel in der Entwicklungsphase einiger Instrumente. Denn die Herstellung von Prototypen würde sonst mehrere Monate dauern. „Durch die additive Fertigung können wir das auf wenige Wochen reduzieren – besonders in der Frühphase der Entwicklung und für Trainings-OPs “, erklärt Toninato. „Zudem sind Verbesserungen leichter umzusetzen.“
AM-VERFAHREN:
Additive Manufacturing für Metalle - powder bed fusion
Einen strukturierten Überblick in die komplexe und vielschichtige Welt der additiven Fertigungsverfahren, Prozessschritte und Anwendungsfelder liefert Ihnen unser AM Field Guide.
MEHR INFOS UNTER:
Tags
- Additive Fertigung
- Medizintechnik