Text: Thomas Masuch, 3 September 2024
Conflux prints heat exchangers for the space industry, motorsports, and many other sectors
With his company, Conflux, Michael Fuller has specialized in one specific thing: 3D-printing heat exchangers. The 48-year-old sees so much potential for this that he’s not even thinking about other products. “The market for heat exchangers is worth billions, and the potential for using Additive Manufacturing to make them continues to grow. This is due to the fact that AM is becoming more and more efficient and therefore cheaper, which means it’s continuing to improve its position in competition with other production methods. The market is so big, I don't have that many years left to really exploit it,” says the father of four.
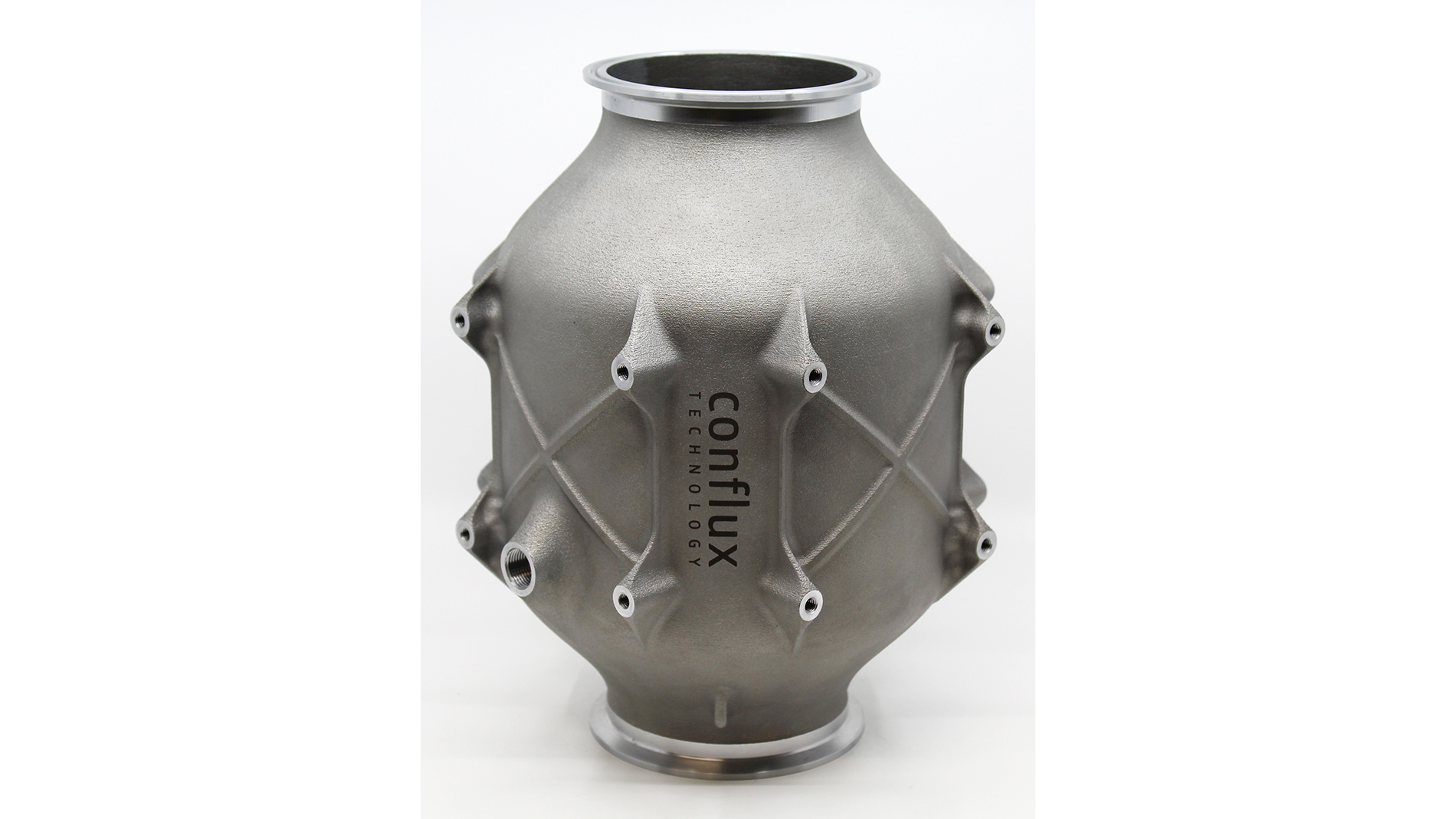
Before founding Conflux, Fuller had worked as an engineer in fields like motorsports, where he gained years of experience in Additive Manufacturing. The reason why he then started his own company in his home country isn’t hard to figure out. "Just look at Google Maps: We're 15 minutes from Bells Beach, and Australia has a really well-educated workforce." The distance to the most important customers in Europe and the USA means that Fuller spends a lot of time on planes and in hotels, but he says it’s "absolutely worth it".
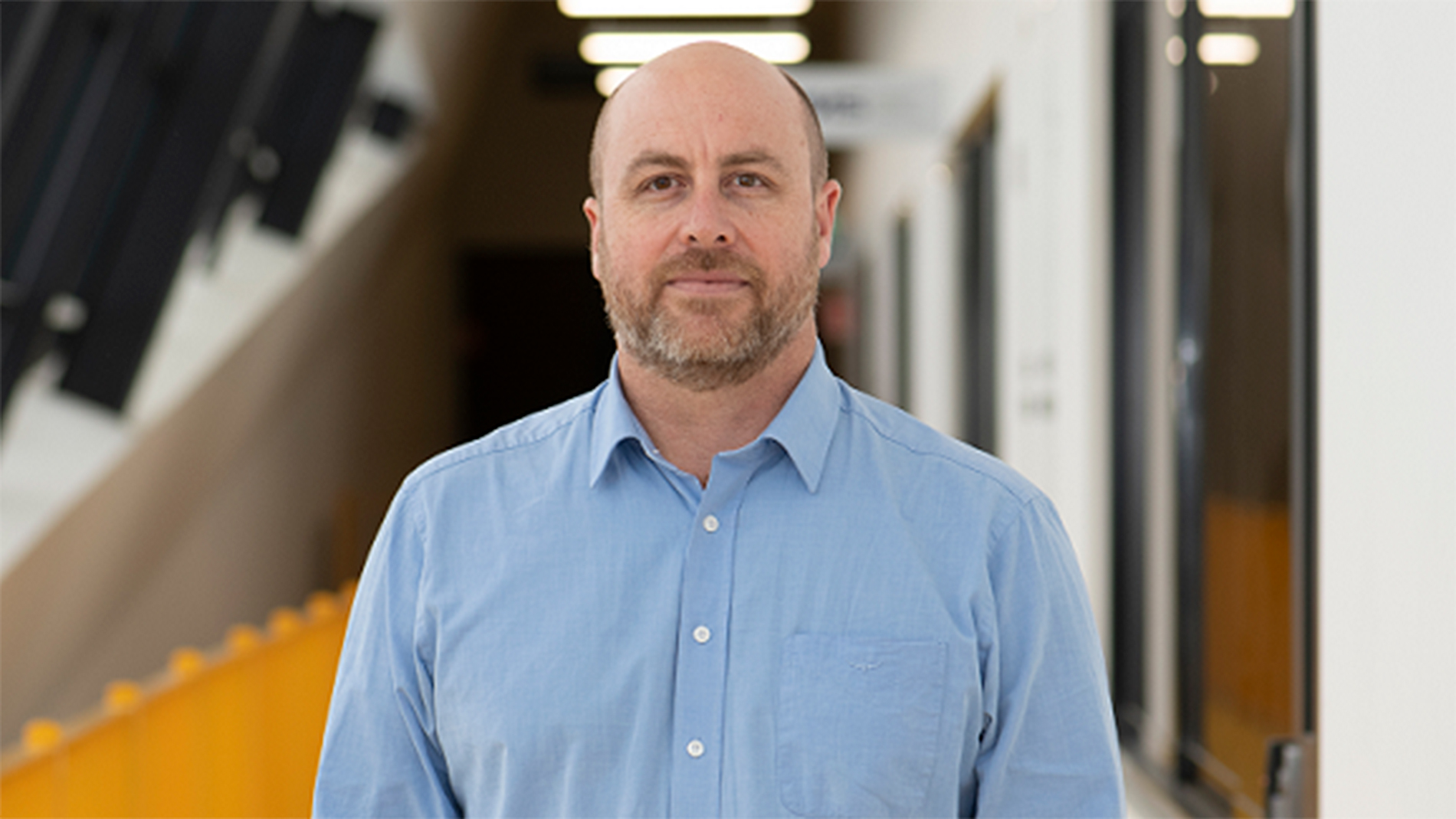
Starting out, Fuller and his team were quite straightforward and pragmatic. "We went to Formnext as visitors, brought heat exchangers with us, and asked companies if they needed one," Fuller recalls. This has since changed dramatically: The company, whose investors include AM Ventures, now has 22 employees and has had its own stand at Formnext for the past two years. Incidentally, the Frankfurt event is the only AM trade fair Conflux attends. Otherwise, the Australian company is only present at events that focus on heat exchanger solutions. "Formnext is extremely worthwhile for us; we had over 200 leads last year," Fuller reports.
Scope of services
Conflux's services range from design to 3D printing (on two EOS PBF systems) and quality control, which includes checking that the dimensions are correct and that no powder residue remains. "The latter in particular isn’t so easy due to the very delicate structures and narrow cooling channels," explains Fuller. Along with his engineers, he wants to further improve the company's expertise in the future, focusing primarily on practical applications. "We’re looking for the most efficient shapes. They’re not always sexy, which disappoints some AM experts, but Additive Manufacturing also has to follow the laws of physics."
Not every heat exchanger that Conflux manufactures is unique, "but we still work with very small quantities," Fuller points out. The number of heat exchangers an order ultimately comprises usually depends primarily on the dimensions of the components, which vary from the size of a fingertip to 400 mm in diameter. Conflux usually supplies small series of between one and 10 components, or as many as 500 units.
Exotic designs
The great potential of heat exchangers lies in the fact that practically every machine has at least one – from computers to 3D printers themselves. But for which systems does it make sense to 3D-print heat exchangers? "Wherever exotic designs are required," explains Fuller. This is the case in aircraft construction, for example. "Weight savings are important here; every kilogram saved has a specific value and can therefore be easily calculated." The same applies to the rocket industry, where the values associated with weight reductions are even higher. Here, 3D-printed heat exchangers are used in both rocket construction and payloads (satellites).
Meanwhile, motorsports represent another important customer group for Conflux. "The main focus here is on the rapid development of aerodynamics. If the design teams can quickly tell what components look like under the surface, they can also better optimize the designs," Fuller says. Other applications include hydrogen drives, semiconductor production, and data centers.
The development of 3D-printed heat exchangers depends on the application and industry in question. "Customers usually come to us when they have developed a heat exchanger provisionally themselves and are now looking for a good replacement," explains Fuller. Things become more complex when very cold liquids are involved, for example, as is the case in rocket construction. "Here, we have to work hand-in-glove with our customers." Conflux then creates a design study, sometimes with several iterations; only then does it proceed with printing the corresponding heat exchanger.
FURTHER INFORMATION:
Tags
- Services
- Aviation and aerospace