Text: Thomas Masuch, 6 September 2023
Danish company Danfoss’s journey to adopting Additive Design and Manufacturing
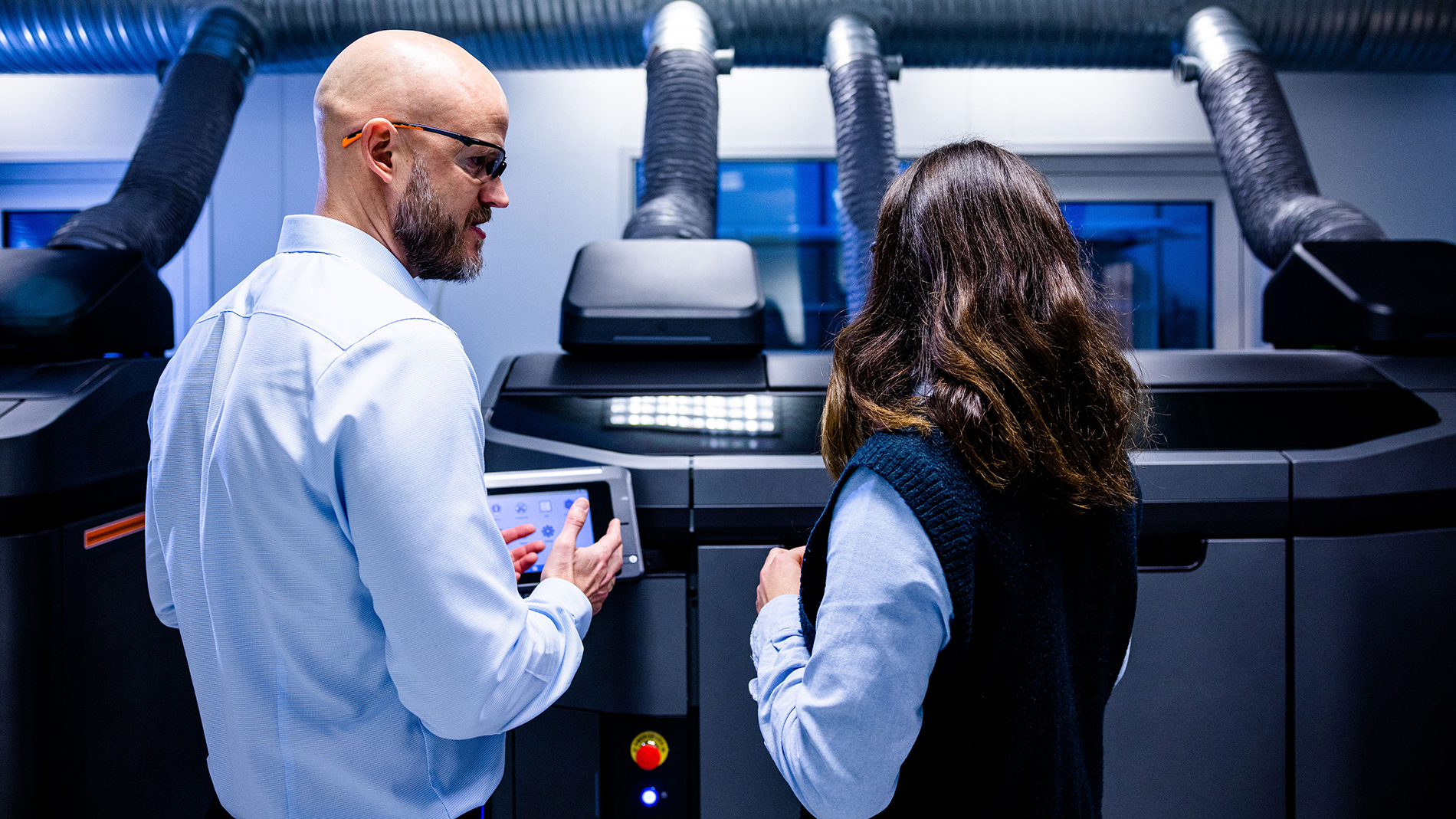
Training was one of the first activities prioritized at Danfoss on the way to group-wide Additive Manufacturing, and it is still the basis for its AM activities today. "Several hundred employees have learned in detail about different AM technologies in this way, developing a general awareness of the use of Additive Manufacturing," explains Wladimir Schamai, Head of Digital Engineering Enablers at Danfoss.
"The process continues with ongoing coaching and application identification workshops," Schamai further explains. This has now resulted in practice communities with several hundred members for simulation and 3D printing. Best practice examples are discussed at the annual internal conference. Here, it also becomes clear how extensive additive know-how already is at Danfoss: "In the beginning, we almost exclusively invited external experts. But now we have the expertise in-house and can conduct workshops and tutorials in part with our own employees," says a pleased Schamai, who heads the Digital Initiative at Danfoss and whose mission is, among other things, to further spread Additive Manufacturing throughout the Group, which has more than 40,000 employees.
Danfoss is one of Denmark's largest companies with sales of €10.3 billion as of 2022. Additive Manufacturing is expected to help the company produce more efficiently, develop and improve its products faster and also help achieve the company's sustainability goals.
Removing barriers
Danfoss has developed a master plan for the long-term roll-out of Additive Manufacturing. "In a large company, it's not just about investing in 3D printing hardware, but also about getting the relevant stakeholders on board," explains Schamai, who has been with the Danish company for more than six years. "Alongside that, it's about removing the barriers created with regard to easy access to 3D-printed parts."
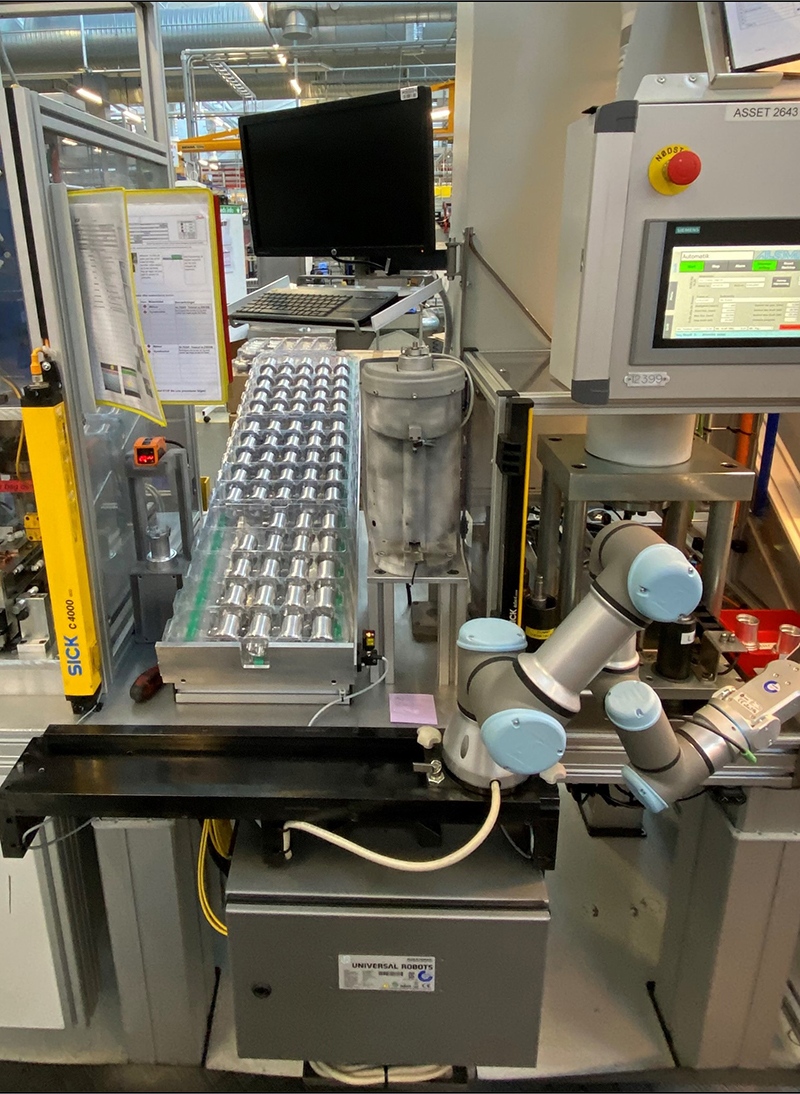
A lot of 3D Printing in a small space: For this production station, an entire ball bearing feeding machine, the frame of an inspection station and a depositing platform were printed in PA12 along with a gripper made of titanium. Image: Danfoss
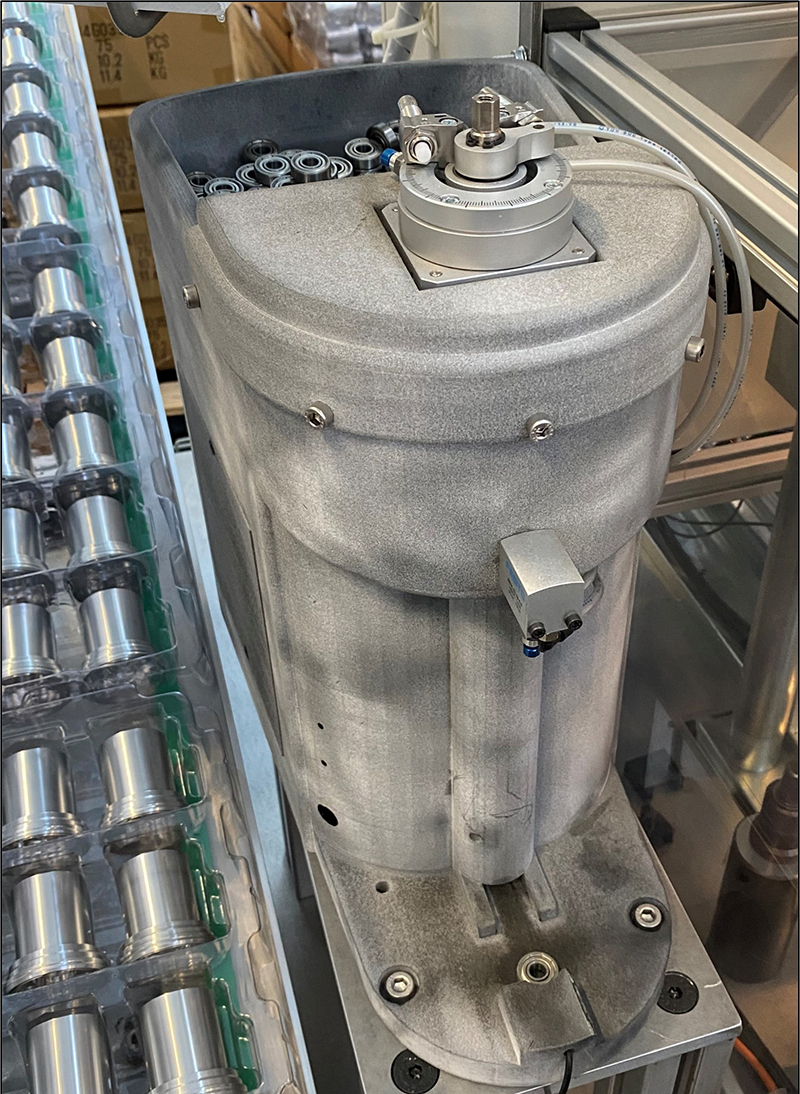
Also, the 40 cm frame of an inspection station was printed in PA12. Image: Danfoss
To enable easy access, Danfoss has gradually set up AM hubs at seven locations in the company. Here, various printers are located on which the required components are produced. With a three-digit number of 3D printers, the company has a variety of common technologies - FDM, SLA, MJF, DLP, SLS or plastic with fiber reinforcement. Danfoss has in-house facilities for printing plastic parts while metal components are additively manufactured by external service providers.
Prototypes, tools and fixtures
Additive Manufacturing was initially used for prototyping, which was very successful at first. "Since we were also developing simulation within the company at the same time, the number of printed prototypes is expected to decrease in the future," explains Schamai. Instead, the use of Additive Manufacturing increased in production and operating equipment, for example, for tools and fixtures.
Using a company-wide platform, employees can upload components quite easily and decide on the material and printing method. A central team advises on print material, process, design and print location (internal or external) in the EU, North America and Asia Pacific regions and processes orders – either on internal printers or using external suppliers. "This lean and 'hybrid' approach suits Danfoss because it is material and process agnostic. For example, there is access to more than 1000 3D printing materials," explains Niklas Franke, Head of Production Simulation and ADM at Danfoss Climate Solutions.
The next stage will be Additive Manufacturing of final components, where Danfoss has already taken initial steps. "We started with less critical components that are relatively easy to implement," Franke says.
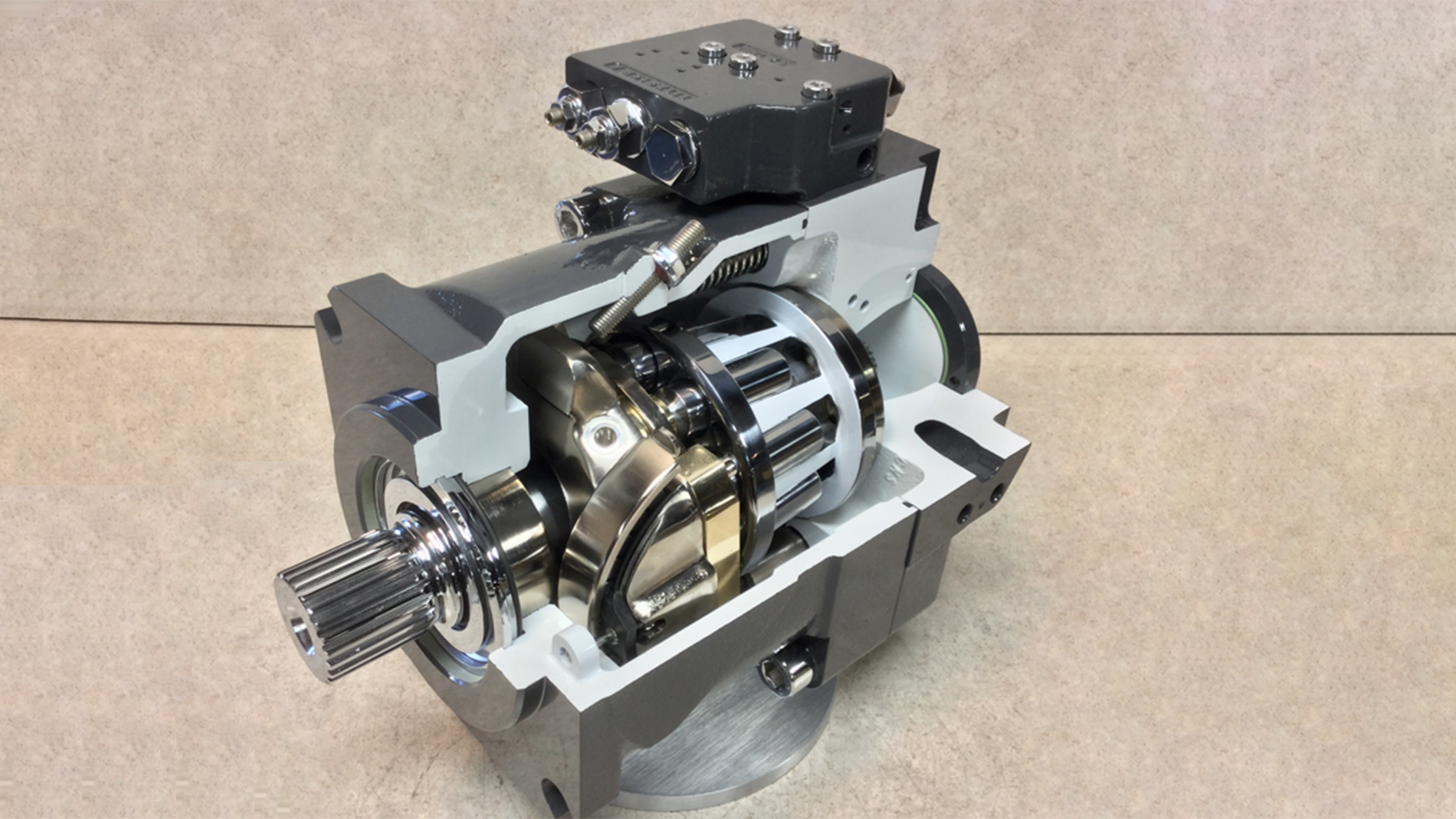
In addition to these "low hanging fruits," however, numerous other applications have since been identified where Additive Manufacturing makes economic sense – for example, less critical components in low volumes (up to several thousands) such as limiters in thermostats. "We have a lot more in the pipeline there."
"Finding highly optimized components"
The design of these end components has not yet been changed. Schamai and Franke expect significantly more additive applications when components are designed for Additive Manufacturing in product development and optimized bionically, for example. "The long-term goal is to find and print highly optimized components that significantly improve the performance of the system they are part of," says Schamai. "That makes it even more important to take as many design engineers with us as possible to spread additive design thinking."
Even though there is still a way to go before the highly optimized final component is available, Danfoss is already seeing considerable success from the AM initiative: over 220,000 prototypes and production tools have been 3D printed since 2017. Franke and Schamai have calculated savings of several million euros for the company as a result. "Moreover, in addition to the systematic use of simulation, Additive Manufacturing has helped to implement projects twice as fast," says Schamai, who is pleased to emphasize the continuous use of the new technologies: "The theoretical training is a good basis, the daily learning by doing is what helps us evolve".
Crucial to Danfoss' additive journey is also the top management's commitment to the technology. The quantifiable successes also help Schamai and Franke to further solidify this commitment. In addition to the usual KPIs such as cost and time savings, Franke can report other softer benefits that are harder to quantify: "For example, when Sales visit customers, the cutaways 3D-printed models help the dialog because we can explain and show the product function more effectively." In addition, deceptively real product models have been 3D-printed from plastic and can easily be taken to trade shows. And this is another way to reduce the cost of transportation and improve the carbon footprint in small steps.
FURTHER INFORMATION:
About Danfoss
Danfoss engineers solutions that increase machine productivity, reduce emissions, lower energy consumption, and enable electrification. Danfoss solutions are used in such areas as refrigeration, air conditioning, heating, power conversion, motor control, industrial machinery, automotive, marine, and off- and on-highway equipment. Danfoss also provides solutions for renewable energy, such as solar and wind power, as well as district-energy infrastructure for cities. The innovative engineering dates back to 1933. Danfoss is family-owned, employing more than 42,000 people, serving customers in more than 100 countries through a global footprint of 95 factories.
Tags
- Education and training
- Electronic engineering and electronics
- Mechanical and plant engineering