Text: Thomas Masuch, 06.09.2023
Wie das dänische Unternehmen Danfoss die Additive Fertigung konzernweit integriert
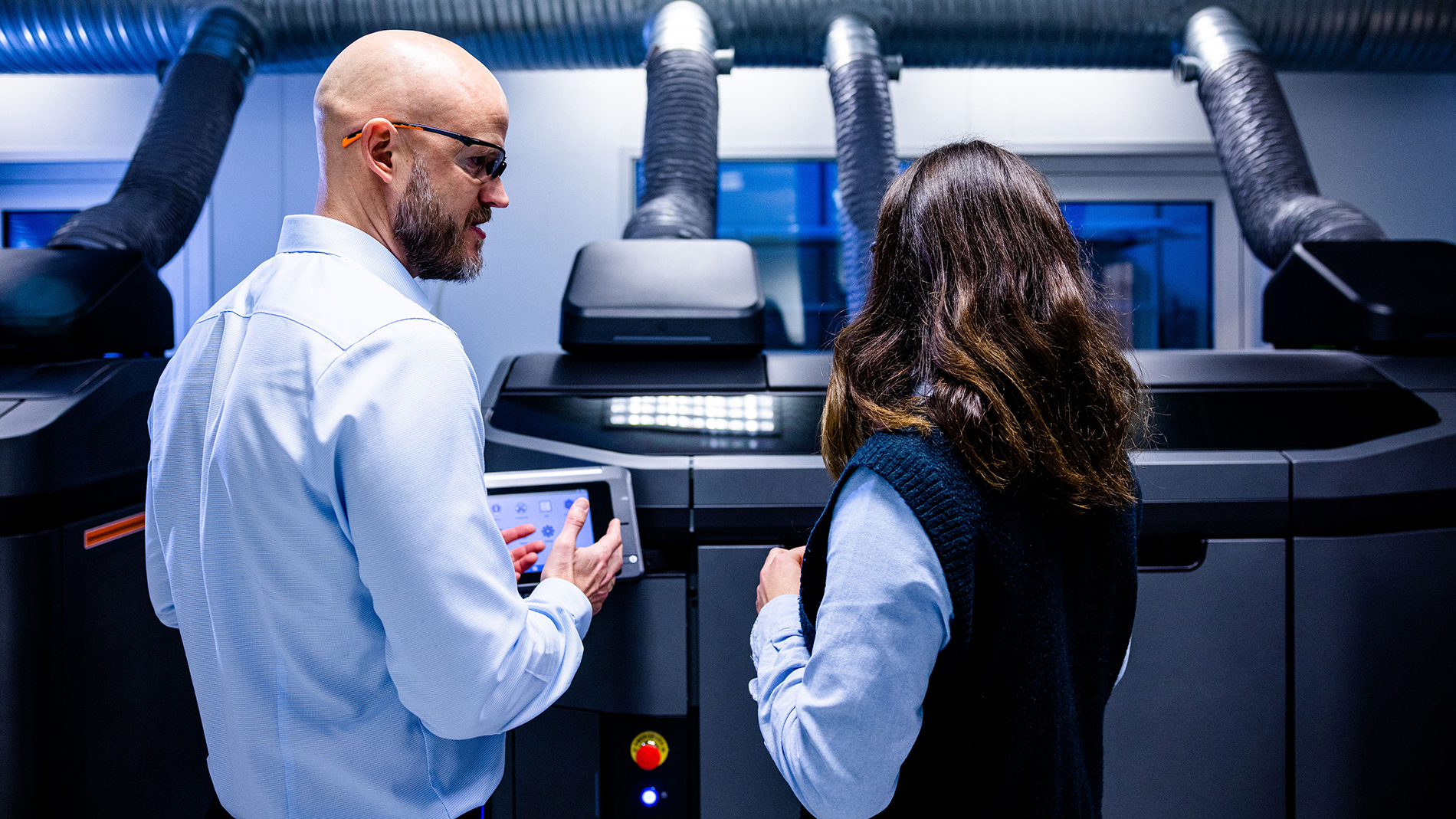
Auf dem Weg zur konzernweiten Additiven Fertigung stellte Danfoss von Anfang an Schulungen ins Zentrum seiner Aktivitäten, und diese Strategie verfolgt das dänische Unternehmen bis heute. „Mehrere Hundert Beschäftigte haben so detailliert verschiedene AM-Technologien kennengelernt und so ein allgemeines Bewusstsein für die Nutzung der Additiven Fertigung entwickelt“, erklärt Wladimir Schamai, Head of Digital Engineering Enablers bei Danfoss.
„Der Prozess wird fortgesetzt durch kontinuierliches Coaching und Workshops zur Anwendungsidentifizierung“, erklärt Schamai weiter. Inzwischen sind daraus Praxisgemeinschaften mit mehreren Hundert Mitgliedern für Simulation und 3D-Druck entstanden. Auf der jährlichen internen Konferenz werden Best-Practice-Beispiele diskutiert. Hier zeigt sich auch, wie groß das additive Know-how bei Danfoss bereits ist: „Anfangs haben wir dazu fast ausschließlich externe Experten eingeladen. Inzwischen haben wir die Expertise im Hause und können teilweise mit eigenen Mitarbeitern Workshops und Tutorials durchführen“, freut sich Schamai, der bei Danfoss die Digitale Initiative leitet und dessen Mission es unter anderem ist, die Additive Fertigung im mehr als 40.000 Beschäftigte zählenden Konzern weiter zu verbreiten.
Danfoss ist mit einem Umsatz von 10,3 Mrd. Euro (Stand 2022) eines der größten dänischen Unternehmen. Die Additive Fertigung soll dem Unternehmen nicht nur dabei helfen, effizienter zu produzieren und seine Produkte schneller zu entwickeln und zu verbessern, sondern auch dazu beitragen, die Nachhaltigkeitsziele des Unternehmens zu erreichen.
Barrieren beseitigen
Für das langfristige Roll-out der Additiven Fertigung hat Danfoss einen Masterplan entwickelt. „In einem großen Unternehmen geht es nicht nur um die Investition in 3D-Druck-Hardware, sondern auch darum, die relevanten Interessengruppen mit ins Boot zu holen“, erklärt Schamai, der seit mehr als sechs Jahren bei dem dänischen Konzern beschäftigt ist. „Daneben geht es darum, durch den einfachen Zugang zu 3D-gedruckten Teilen Barrieren zu beseitigen.“
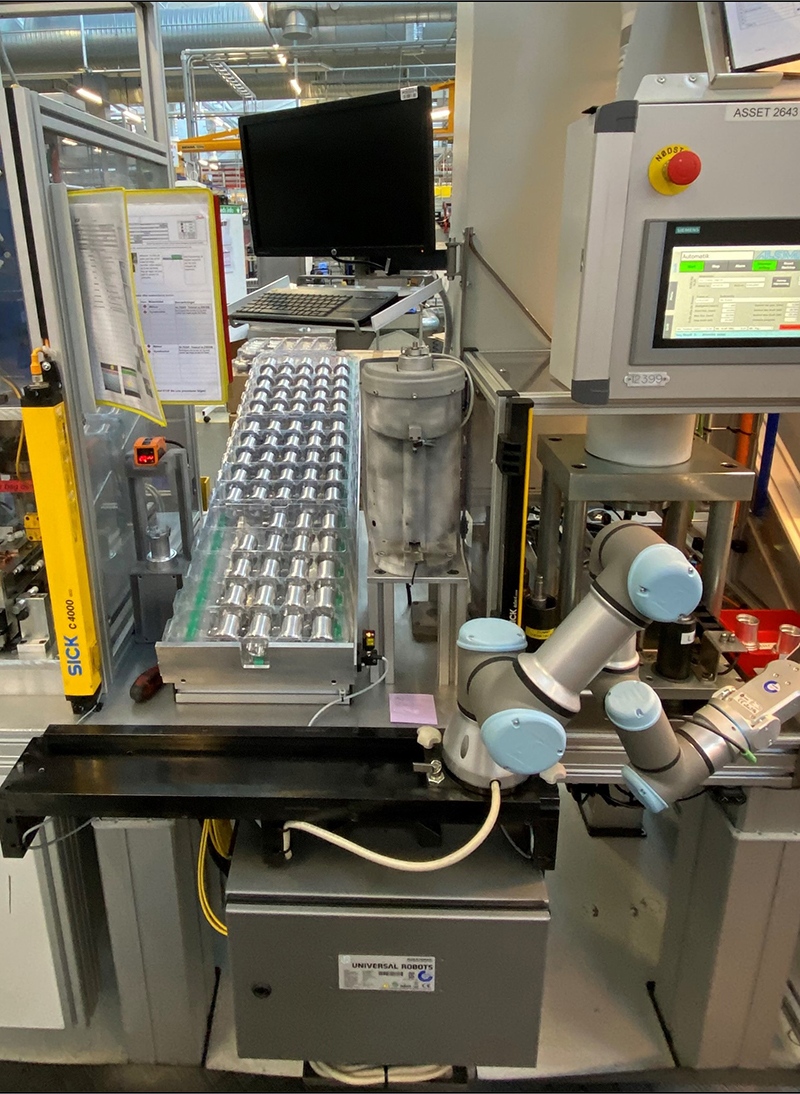
Viel 3D-Druck auf wenig Raum: Für diese Produktionsstation wurde eine gesamte Kugellagereinspeisemaschine, der Rahmen einer Inspektionsstation und eine Abstellplattform aus PA12 gedruckt sowie ein Greifer aus Titan. Bild: Danfoss
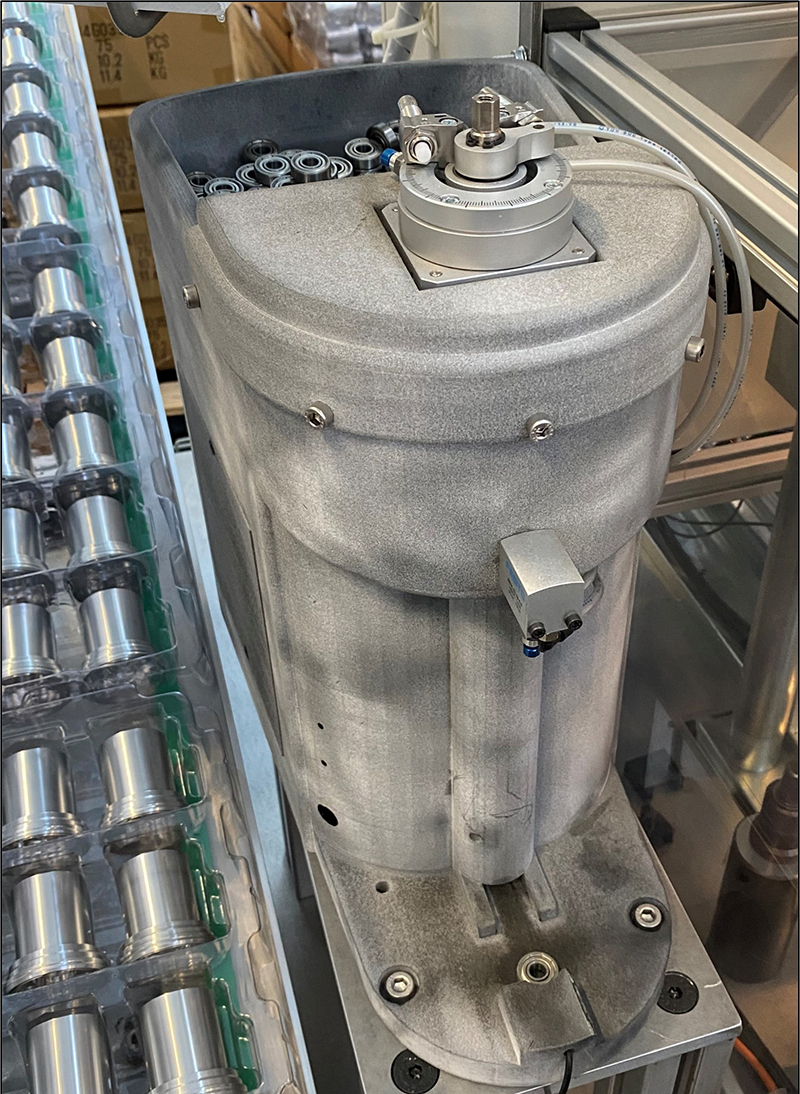
Auch der der 40 cm große Rahmen der Inspektionsstation wurde aus PA12 gedruckt. Bild: Danfoss
Um den leichten Zugang zu ermöglichen, hat Danfoss nach und nach an sieben Standorten im Unternehmen AM-Hubs aufgebaut. Hier stehen verschiedene Drucker, auf denen die benötigten Bauteile hergestellt werden. Mit einer dreistelligen Anzahl an 3D-Druckern verfügt das Unternehmen über eine Vielzahl gängiger Technologien – FDM, SLA, MJF, DLP, SLS oder Kunststoff mit Faserverstärkung. Danfoss nutzt intern Kunststoff-Drucker – Metall-Bauteile werden über externe Dienstleister additiv gefertigt.
Prototypen und Betriebsmittel
Angewendet wurde die Additive Fertigung anfangs für Prototypenfertigung, was zuerst auch sehr erfolgreich lief. „Da wir gleichzeitig intern auch die Simulation weiterentwickelt haben, rechnen wir damit, dass die Zahl 3D-gedruckter Prototypen in Zukunft zurückgehen wird“, erklärt Schamai. Stattdessen stieg der Einsatz der Additiven Fertigung im Bereich Produktions- und Betriebsmittel, zum Beispiel für Werkzeuge und Halterungen.
Über eine unternehmensweite Plattform können Mitarbeiter recht einfach Bauteile hochladen und sich für Material und Druckmethode entscheiden. Ein zentrales Team berät über Druckmaterial, Verfahren, Design und Druckstandort (intern oder extern) in den Regionen EU, Nordamerika und Asien/Pazifik und wickelt Aufträge ab – entweder auf internen Druckern oder über externe Zulieferer. „Dieser schlanke und hybride Ansatz kommt Danfoss entgegen, da er material- und prozessunabhängig ist. So besteht zum Beispiel Zugang zu mehr als 1.000 3D-Druckmaterialien“, erklärt Niklas Franke, Head of Production Simulation and ADM bei Danfoss Climate Solutions.
Die nächste Stufe ist die Additive Fertigung von Endkomponenten, bei der Danfoss schon die ersten Schritte gemacht hat. „Gestartet sind wir mit weniger kritischen Bauteilen, die sich relativ leicht umsetzen lassen“, so Franke.
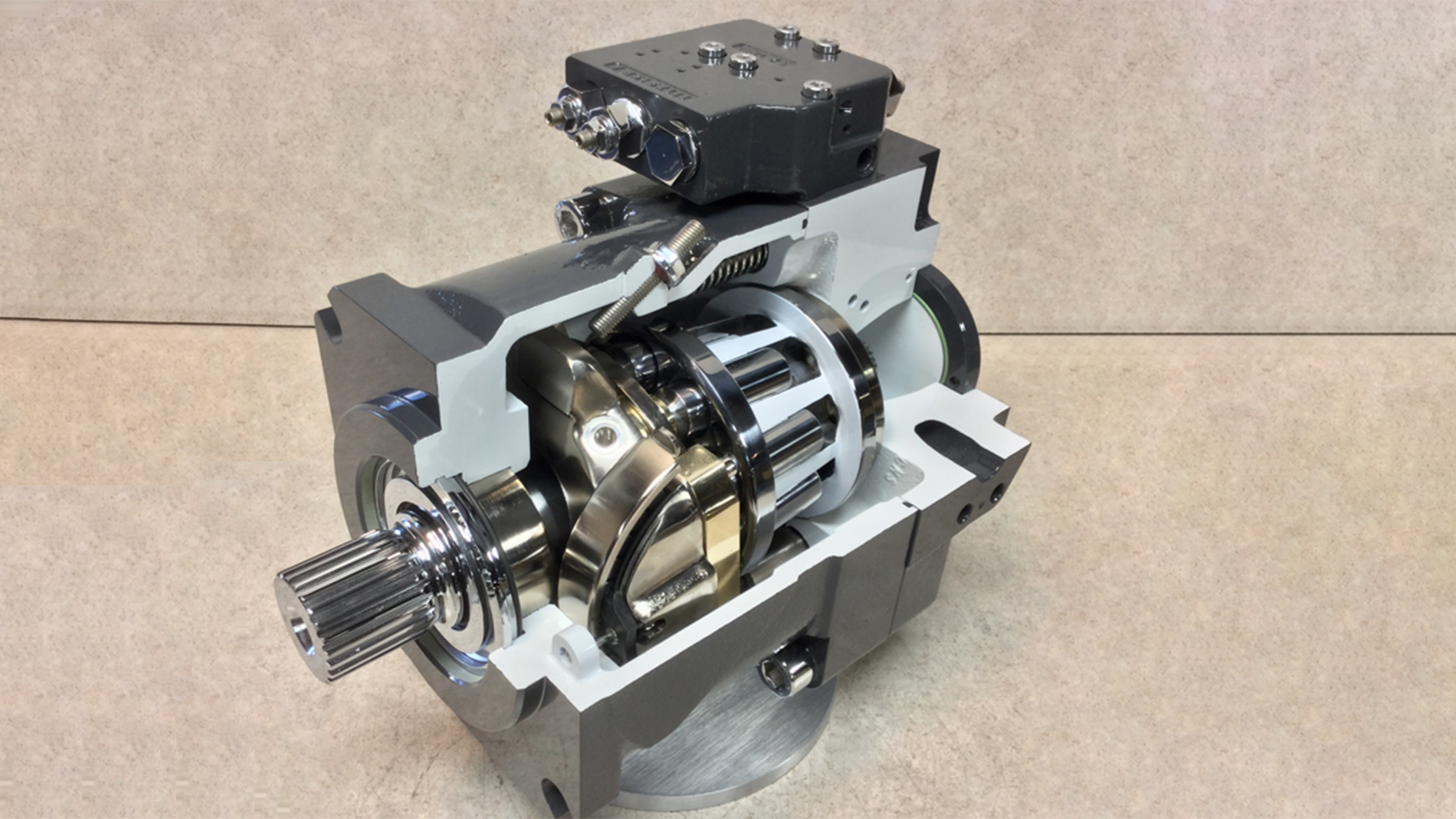
Neben diesen „low hanging fruits“ wurden inzwischen aber auch zahlreiche weitere Anwendungen identifiziert, bei denen die Additive Fertigung wirtschaftlich sinnvoll ist – zum Beispiel weniger kritische Bauteile in geringen Stückzahlen (bis zu mehrere Tausend) wie Limiter in Thermostaten. „Wir haben da noch einiges in der Pipeline.“
„Hochoptimierte Bauteile finden“
Bei den bisher gefertigten Endkomponenten wurde das Design noch nicht verändert. Mit deutlich mehr additiven Anwendungen rechnen Schamai und Franke, wenn in der Produktentwicklung Bauteile für die Additive Fertigung designt und zum Beispiel bionisch optimiert werden. „Das langfristige Ziel ist es, hochoptimierte Bauteile zu finden und zu drucken, mit denen sich die Performance der Systeme verbessert, in denen sie eingesetzt werden“, so Schamai. „Umso wichtiger ist es deshalb, möglichst viele Konstrukteure mitzunehmen und additives Denken zu verbreiten.“
Auch wenn es noch ein Stück Weg bis zur hochoptimierten Endkomponente ist, zeigen sich bei Danfoss bereits beachtliche Erfolge der AM-Initiative: Über 220.000 Prototypen und Produktionswerkzeuge wurden seit 2017 3D-gedruckt. Franke und Schamai haben daraus Einsparungen von mehreren Millionen Euro für das Unternehmen errechnet. „Zudem hat die Additive Fertigung neben der systematischen Nutzung von Simulation dazu beigetragen, dass Projekte doppelt so schnell umgesetzt werden konnten“, freut sich Schamai, der die kontinuierliche Nutzung der neuen Technologien betont: „Die theoretische Schulung ist eine gute Basis. Das tägliche Lernen hilft uns, uns weiterzuentwickeln.“
Entscheidend für den additiven Weg von Danfoss ist auch das Bekenntnis des Top-Managements zu der Technologie. Die quantifizierbaren Erfolge helfen Schamai und Franke auch dabei, dieses Bekenntnis weiter zu verfestigen. Neben den üblichen KPIs wie Kosten- und Zeitersparnis kann Franke noch von anderen, weicheren und schwerer quantifizierbaren Vorteilen berichten: „Wenn der Vertrieb beispielsweise Kunden besucht, helfen die 3D-gedruckten Schnittmodelle bei den Gesprächen, weil wir die Produktfunktion besser erklären und zeigen können.“ Außerdem wurden täuschend echte Produktmodelle aus Kunststoff 3D-gedruckt, die problemlos zu Messeauftritten mitgenommen werden können. Und auch so lässt sich der Aufwand für Transporte verringern und die CO2-Bilanz in kleinen Schritten verbessern.
MEHR INFOS:
Über Danfoss
Danfoss entwickelt Lösungen, die die Produktivität von Maschinen erhöhen, Emissionen reduzieren, den Energieverbrauch senken und die Elektrifizierung ermöglichen. Die Lösungen von Danfoss werden in Bereichen wie Kühlung, Klimatisierung, Heizung, Energieumwandlung, Motorsteuerung, Industriemaschinen, Automobile, Schiffe sowie Off- und On-Highway-Ausrüstung eingesetzt. Danfoss bietet auch Lösungen für erneuerbare Energien wie Solar- und Windenergie sowie Energieinfrastruktur für Städte. Die innovative Technik geht auf das Jahr 1933 zurück. Danfoss ist ein Familienunternehmen, das mehr als 42.000 Mitarbeiter beschäftigt und mit 95 Fabriken weltweit Kunden in mehr als 100 Ländern beliefert.
Tags
- Maschinen- und Anlagenbau
- Aus- und Weiterbildung
- Elektrotechnik und Elektronik