17 August 2022
Optimizing protective clothing for at-risk occupational groups such as the police or security companies – that is the goal of the StereoTex research project at the Bielefeld University of Applied Sciences. The project is developing a process that will make it possible to produce stab-resistant protective clothing from a combination of textiles and synthetic resins.
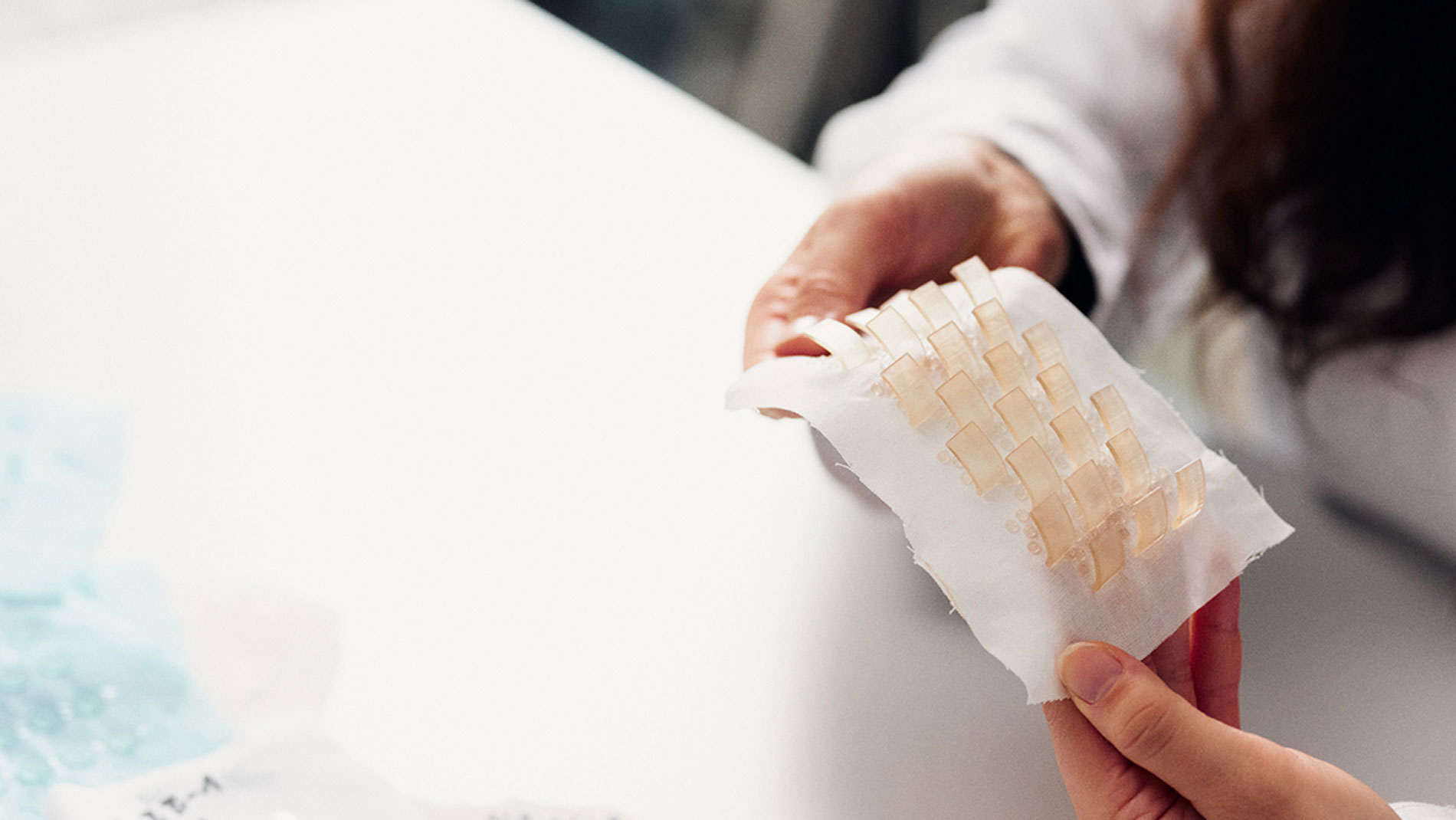
The project, which is being carried out by the university’s Department of Engineering and Mathematics, is using the stereolithographic 3D-printing process (SLA) as the basis for its research. In this process, 3D objects are printed directly onto textiles that are set onto the print bed using a fixture the project developed itself.
The goal is to develop customizable resin-textile composites with stab- and cut-resistant properties. "In very concrete terms, this means we want to use the composites to produce protective clothing for potentially vulnerable occupational groups such as the police, security companies, or bus and cab drivers," reveals StereoTex project manager Timo Grothe. He says it’s important that the composites be breathable and remain stable for at least 10 years. "Especially for protective equipment that has to be worn very close to the body for several hours a day, it's necessary to make it lightweight and comfortable, but still capable of providing solid, durable protection."
Focusing on porous resin
The linchpin of the development lies in the nature of the resin used to print the various textiles. "Since the synthetic resins available on the market aren’t optimized for our novel process, we’re working with ALWA GmbH – a company that makes resin-casting systems – to develop an innovative, porous resin that can be printed on textiles without any problems and is also permeable to air and water,” Grothe reports. Since this resin currently exists only for casting purposes, the next step will involve making it printable.
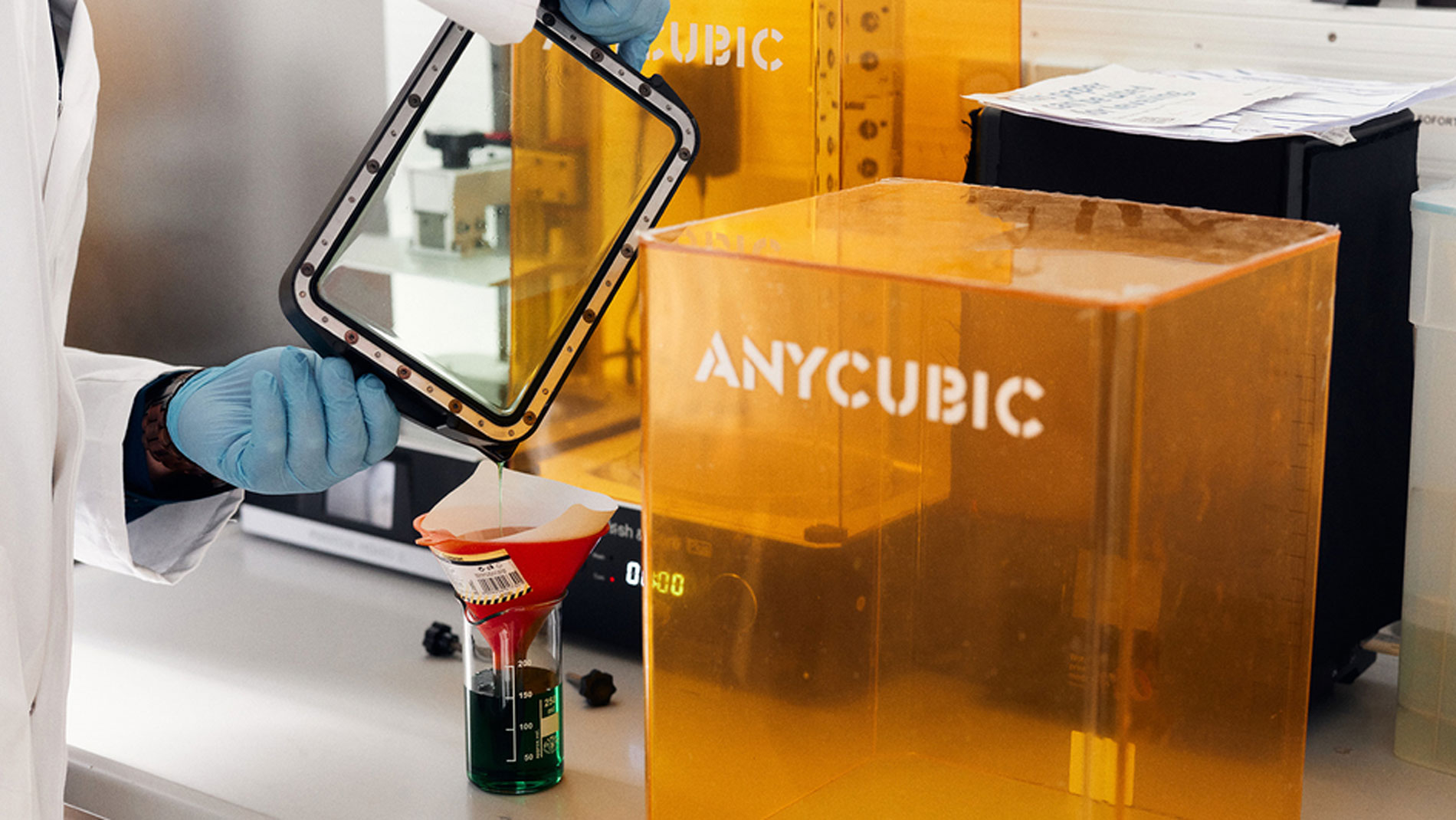
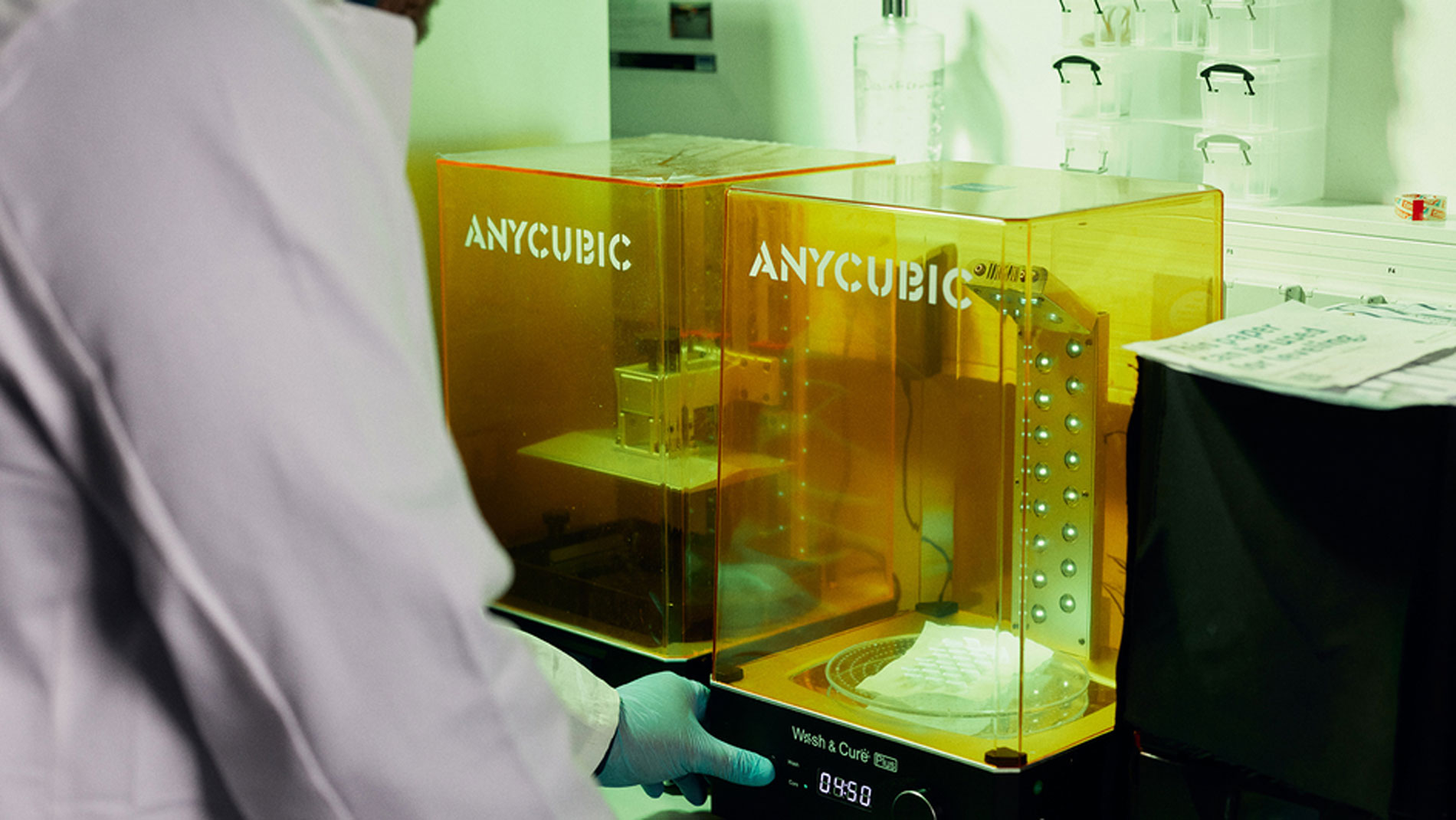
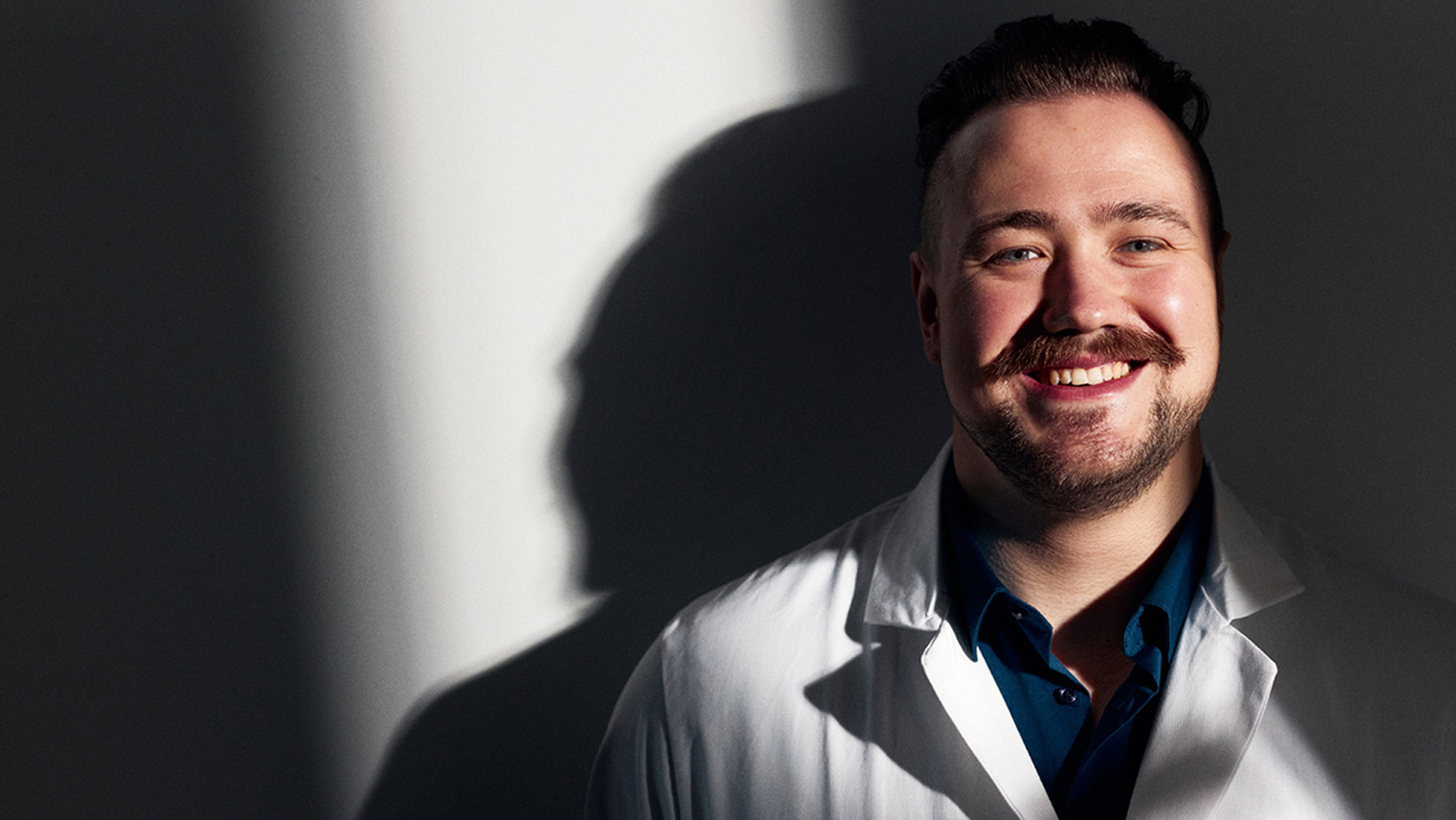
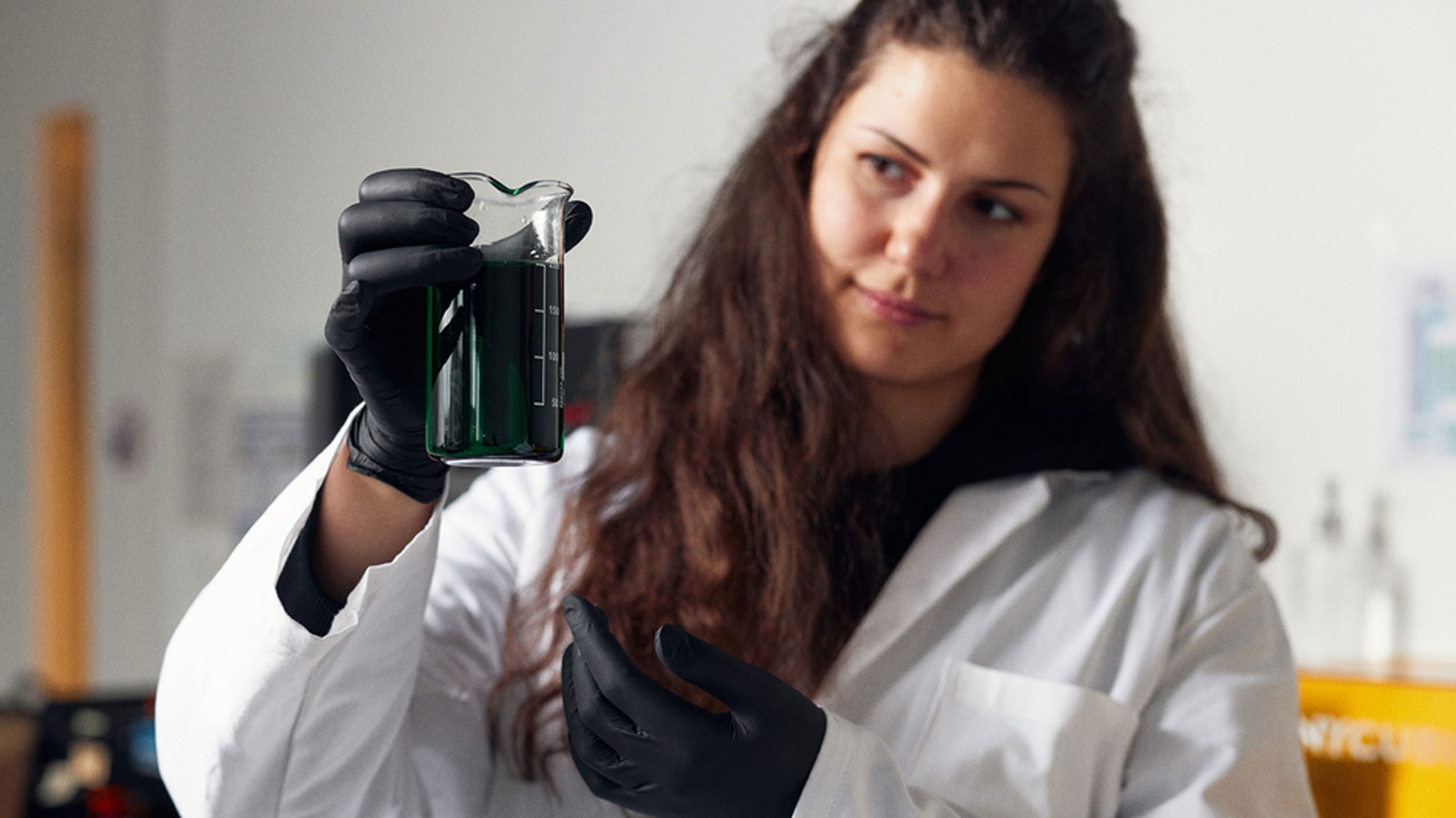
Promising initial results
Although the project is still in its early stages, it’s already had some initial success, as research associate Elise Diestelhorst points out. "To find out which textiles are best suited to our application scenario, we’ve printed a variety of them with commercially available UV resin. We’re now investigating which textile properties are best for both resin adhesion and long-term performance as a textile-resin composite. In the process, we've also tested different shapes and sizes of 3D objects on the textiles – smaller and larger cylinders, as well as elongated square structures that overlap like roof tiles and are modeled after historical armor and plating from the animal kingdom." The first research results are expected to be published soon, but Grothe is willing to offer a sneak peek: "It works!"
Now, to develop a hybrid printer…
In the next step, the Bielefeld experts want to develop a hybrid 3D printer that uses liquid resin and UV light for curing like in the SLA process, but applies the resin to textiles in a manner comparable to fused deposition modeling (FDM) technology. "For StereoTex project, our goal is to apply liquid resin to the underlying textile from above with millimeter precision like FDM printers do, and at the same time cure it directly using a UV source," says Diestelhorst. This would eliminate the need to place the textiles in a pool of liquid resin, along with the time-consuming step of removing the excess uncured resin from the fabric. In addition, it would be possible to save on materials and protect the environment.
FURTHER INFORMATION:
AM TECHNOLOGY:
Additive Manufacturing for polymere - photopolymerization
A structured overview of the complex and multi-layered world of additive manufacturing, the process chain and areas of application is provided by our AM Field Guide.
Tags
- Additive Manufacturing
- Research and development