3 September 2024
The 3D printing workshop at the Refactory in Flins (near Paris) prints prototype parts, manufacturing support tools, and mass-produced vehicle parts to meet the needs of the Renault Group and external companies. The French carmaker has poured its more than 20 years of experience in additive manufacturing into the location. The center now has 18 polymer 3D printers spread out over 500 square meters, along with a dedicated post-processing area that includes an AM Solutions surface-finishing machine and a coloring machine.
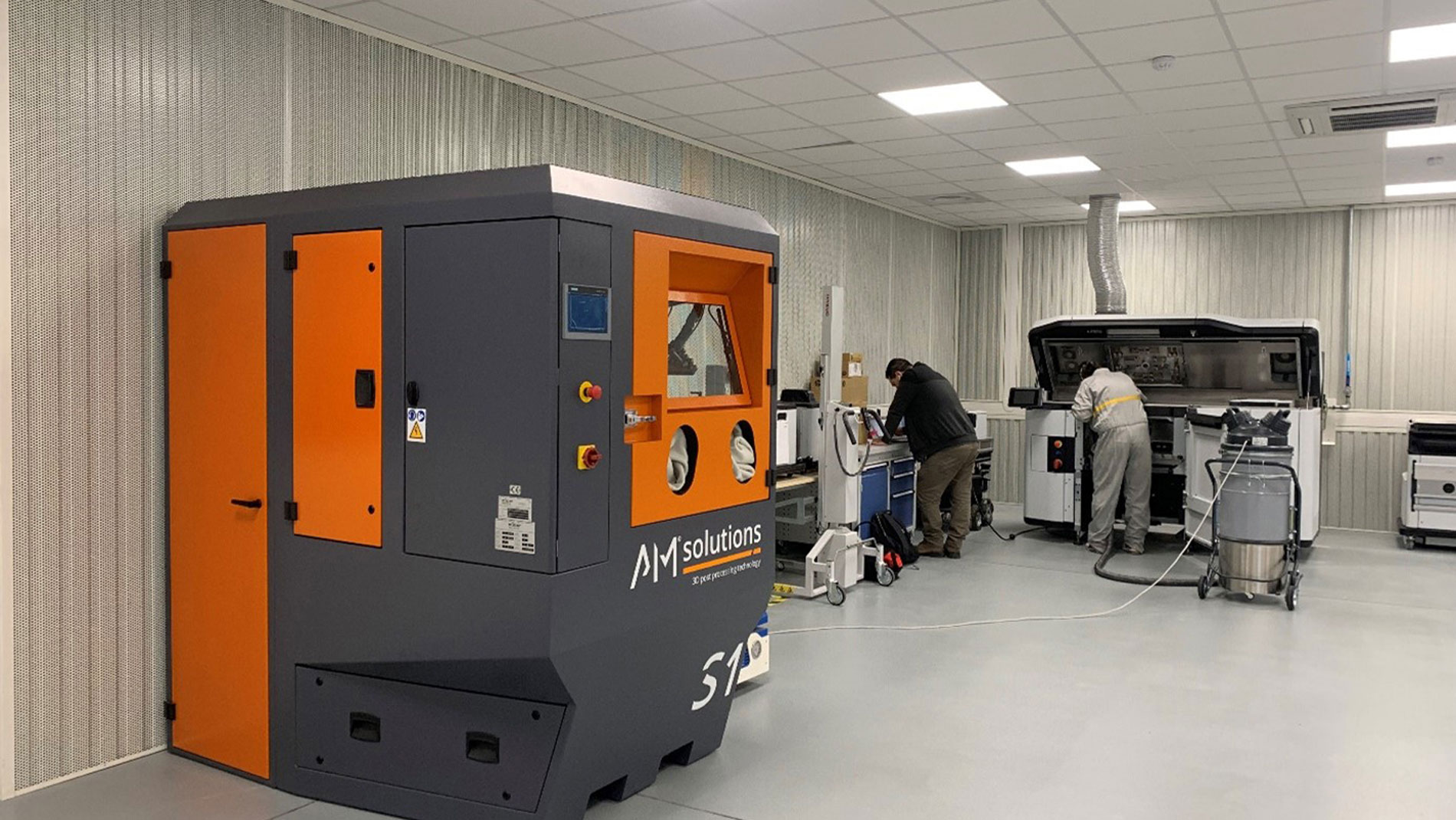
When Renault embarked on its AM journey some 20 years ago, it began with wire deposition processes to design tooling. The group has since continued to develop AM at various production sites. In 2020, the Refactory project was initiated in Flins with a focus on four main areas, which Renault has dubbed Re-trofit, RE-energy, Re-cycle, and Re-start. "Industrial 3D printing needs to be reliable, repeatable, and efficient in terms of cost, quality, and lead time," says Mélanie Chevé, additive manufacturing process manager at Renault Flins.
In the past, many post-processing operations still had to be carried out manually on Renault parts. Apart from being time-consuming and labor-intensive, this produced inconsistent results. To optimize these operations, Renault Flins procured an S1 post-processing machine from AM Solutions, which is designed to reduce blasting and cleaning times and improve the durability and appearance of dyed parts. The challenge therefore lay in automatically cleaning MJF PA 12 printed parts and then finishing them with color.
The S1 is capable of performing cleaning and surface finishing with just one processing medium in one self-contained unit. It can also automatically remove residual powder after printing. The constant rotation of work pieces during the cleaning process ensures consistent and repeatable blasting results.
"The ability to use the S1 for different blasting programs with different recipes and different media was what gave rise to our post-processing project," says Nicolas Blondel, head of the 3D printing team in Flins.
FURTHER INFORMATION:
Tags
- Automotive
- Surface treatment