11 July 2022
For the first time, the French transportation technology group Alstom has qualified a 3D-printed stainless steel doorstop for series production for its train compartments. Alstom worked together with the Replique platform.
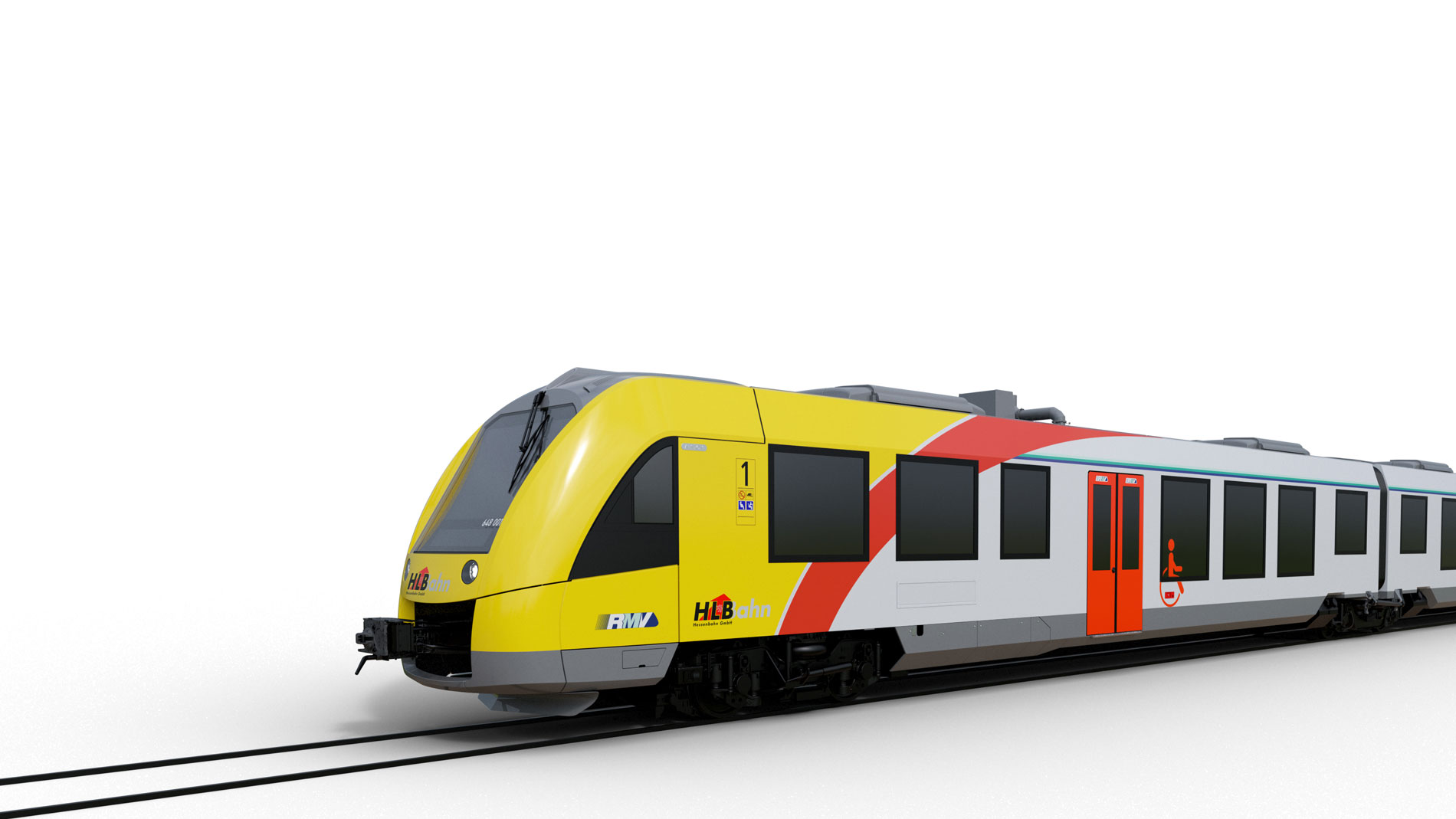
In train manufacturing, small batch sizes lead to high manufacturing costs due to the production of molds and other tools. 3D printing can solve this challenge by eliminating fixed costs. As a result, parts can be produced economically even in small quantities. Alstom has already taken advantage of the technology within the production of spare parts.
To meet a specific customer request, Alstom needed several doorstoppers for a partition door that will divide the passenger compartment of a diesel multiple unit into a first and second class. The small number of such components is usually an obstacle to initial production and typically, it comes to project delays as a result of long delivery times.
Replique assisted Alstom with material and technology selection and was able to qualify and deliver the doorstopper for serial production within just 1.5 months. During this process, the doorstopper went through the protocols of initial sample testing and assembly and received the final approval for series production.
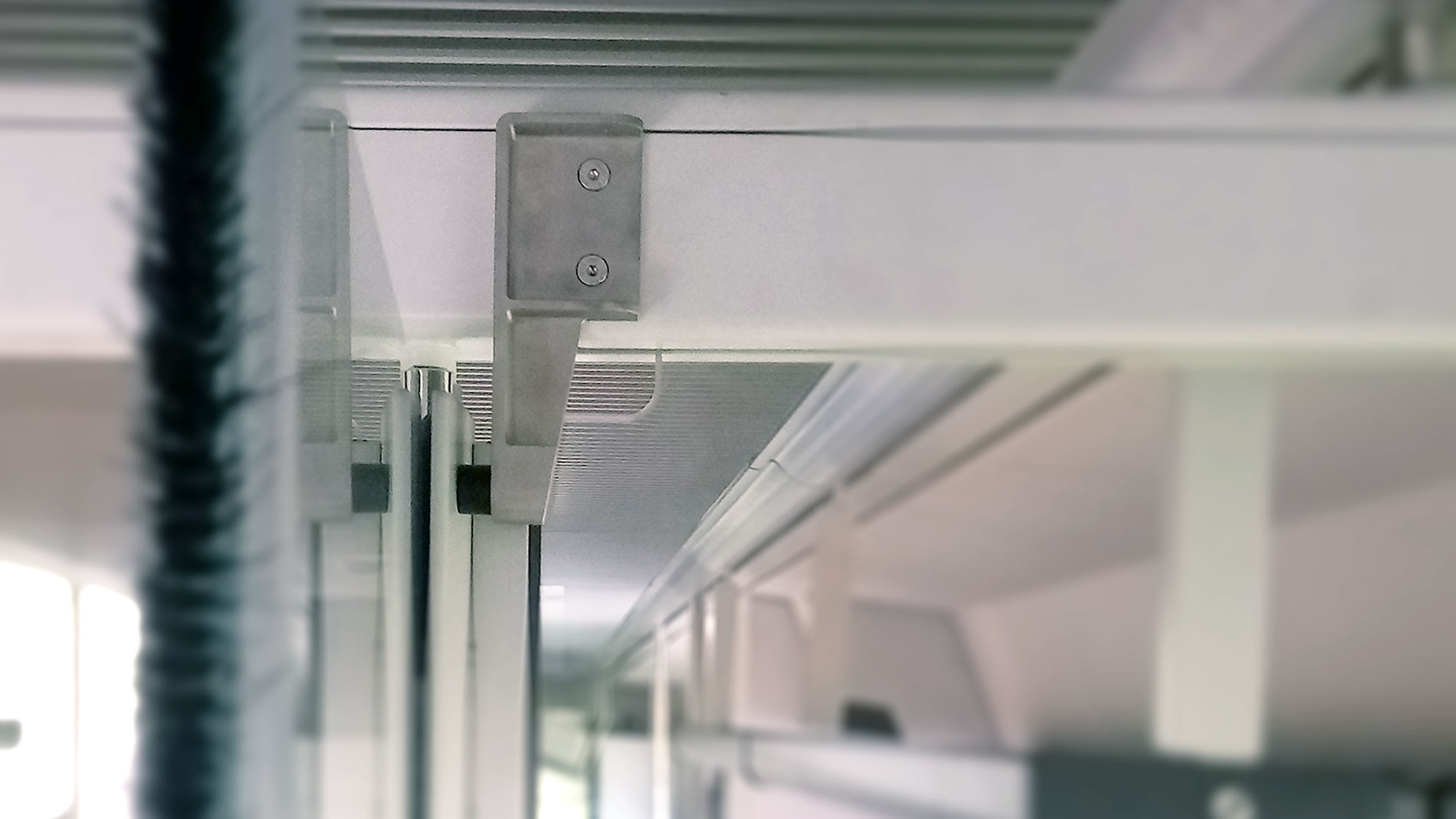
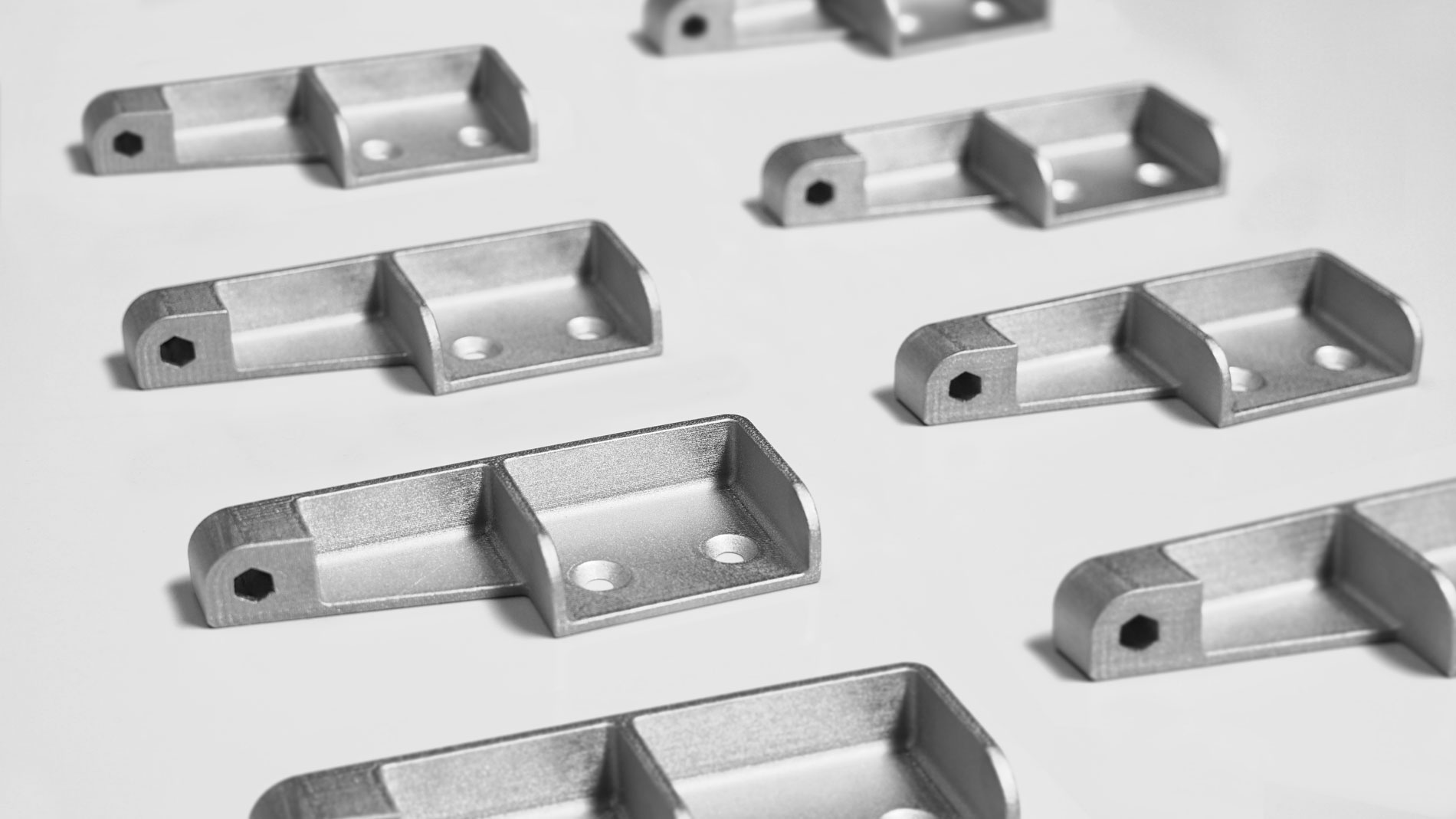
Careful qualification including the selection of the right material had been crucial. The doorstopper must not only fulfill its function over the entire service life of the train, but also meet high aesthetic standards, as it is a visible part inside the train compartment. Stainless steel meets these requirements. Thanks to FDM 3D printing with Ultrafuse 316L from Forward AM, brand of BASF 3D Printing Solutions, followed by debinding and sintering, costs could be reduced compared to other additive manufacturing processes, such as powder bed with 316L, as Alstom said.
“We were able to produce the doorstopper in a cost-neutral manner compared to conventional methods. Within the near future, we plan to further exploit the technology’s potential by creating topology-optimized designs of new parts, or even make them lighter by using reduced infill,” explained Ben Boese, 3D Printing Hub Manager at Alstom Transport Deutschland GmbH.
AM TECHNOLOGY:
Additive Manufacturing for AM metals - material extrusion
A structured overview of the complex and multi-layered world of Additive Manufacturing, the process chain and areas of application is provided by our AM Field Guide.
Tags
- Additive Manufacturing
- Rail and transport