7 Septemper 2022
Before 3D-printed turbine blades, gas turbine engine components, injection-molded plastic inserts, or artificial knee joints are usable, they often first make a trip to St. Priest near Lyon, France. Here, Binc Industries ensures that the surfaces become as smooth as required by their customers.
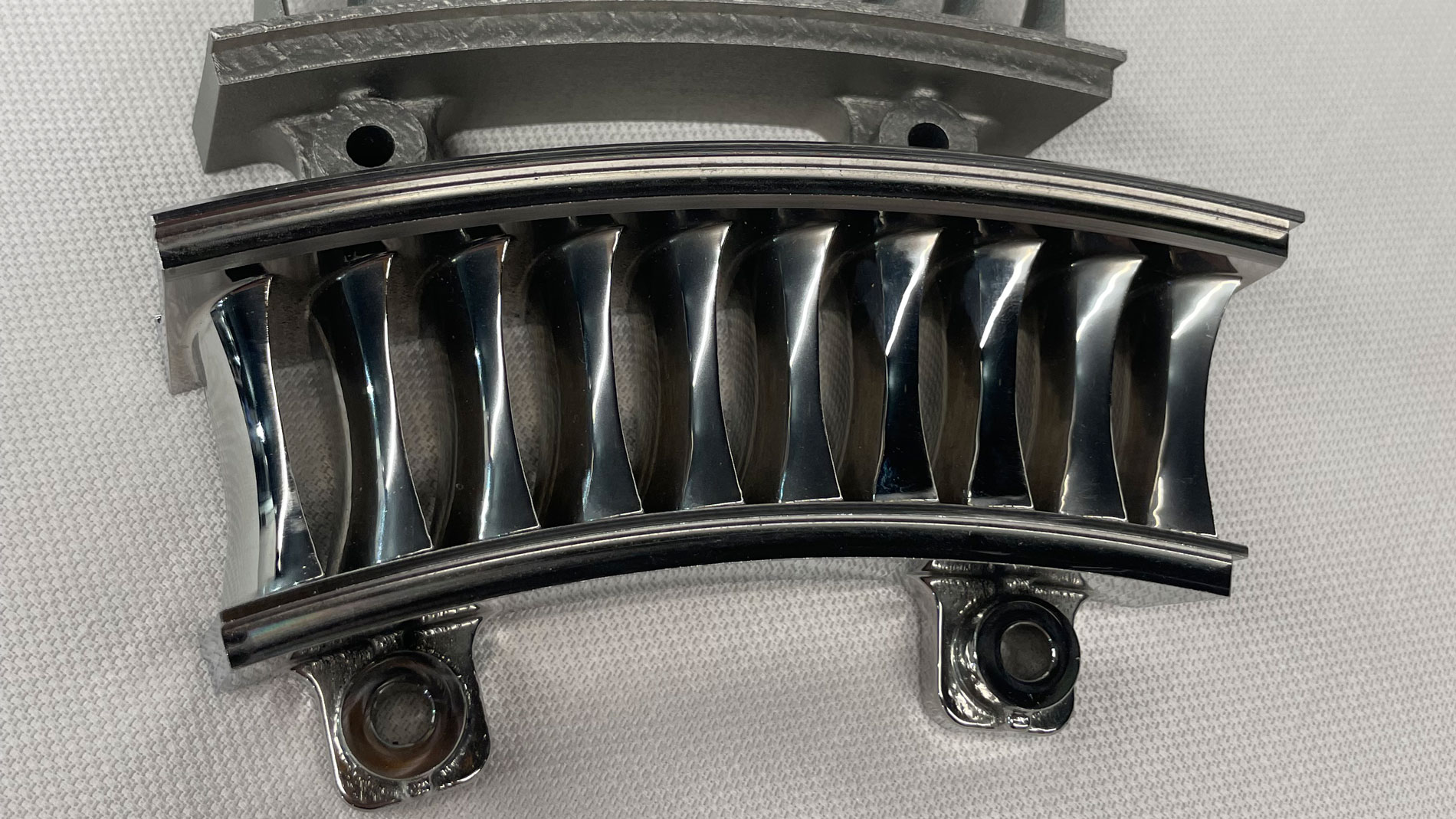
The Binc Industries group specializes in post-processing and surface finishing. Its French subsidiary, Binc Industries France SAS, employs around 20 people at its site in St. Priest. At the core of the company is its proprietary Micro-Machining Process (MMP), which uses "microtools" that float in a liquid and are aggregated by a catalyst. The workpiece is firmly anchored in the machine, and the tank is filled with the solution and the microtools. High-energy movements along three axes then cause the aggregates to scrape past the surface and remove only the "targeted range of roughness frequencies." "Typically, 3D-printed parts have a surface roughness of 15–30 microns. With this process, surface finishes of 0.8 microns or less can be achieved, which is very close to a mirror," explains Christophe Jacobs, Commercial Director Europe at Binc Industries. In addition, the emulsion reaches virtually every angle of the component, including some internal channels.
Surface engineering to improve performance
This sophisticated process, which Binc Industries offers only as a service (the company does not sell machines), is more than just surface machining according to Jacobs. "It’s surface engineering we use to improve the performance of components,” he explains. "When our customers send us a component for technical validation, we first analyze the full roughness profile and study the frequency ranges present. We then use this as a basis for determining the appropriate MMP to be applied – that is, the composition of the microtools, the movement program, and the positioning of the part.” In total, Binc Industries has around 650 recipes.
The MMP technology is already 20 years old and was originally developed in Switzerland as an alternative to manual polishing to produce high-quality surfaces on watches and jewelry. At the time, the innovation gave rise to the Swiss company Binc Industries SA, which today has around 125 employees and branches and subsidiaries in France, Germany, the USA, India, China, and Japan. The company’s current location in St. Priest was chosen because it is both quite close to Switzerland and lies within the second-largest economic area in France, as Jacobs explains.
It was around 17 years ago that MMP was then also discovered by the additive community through the European project RC2. "Manufacturers of AM equipment approached us at that time because they wanted to finish the surfaces of 3D-printed products to show what was possible with additive manufacturing, and that there was a service chain for it," says Jacobs.
Not just for prototyping anymore
For Binc Industries, which was also one of the first exhibitors at Formnext, the additive manufacturing industry has now developed into an important business segment. Around 15 percent of its sales are now generated with 3D-printed components, as Jacobs reveals. "And this sector is growing by far the fastest – at a rate of 100% from 2021 to 2022, in fact. AM is really booming." The reason for this, he says, is that additive manufacturing is increasingly extending beyond prototyping and being used in more and more industrial applications.
The objects that undergo surface engineering in St. Priest range from knee and hip joints made of a wide variety of materials (stainless steel, ceramics, zirconium, etc.) to components for the aerospace sector, gas turbines, stamping and cold forging tools, high-performance transmissions, and the pharmaceutical industry.
FURTHER INFORMATION:
Tags
- Additive Manufacturing
- Surface treatment