Interview: Martin Grolms, Fraunhofer ILT — 8 Oktober 2024
Additive Manufacturing is more agile than almost any other industry, with new technologies and materials rapidly emerging to enable novel applications. In this interview, Dr. Stefan Leuders from Voestalpine and Dr. Tim Lantzsch from Fraunhofer ILT discuss the evolving landscape of AM, especially in the metal sector, the challenges faced, and which companies are likely to benefit from these advancements.

What are the current trends in additive manufacturing? Which developments do you find most promising?
Lantzsch: A key trend I observe is the increased adaptation of materials and applications specifically tailored to the requirements of AM. Many materials currently in use were not originally developed for additive processes. While the technology is costly, its value becomes clearer when we target cost reductions and focus on niche applications.
“Too expensive” is a common critique of AM. What economic challenges are you addressing in this area?
Lantzsch: The main economic challenges lie in the high costs associated with equipment and materials, which significantly influence component prices. There remains substantial room for optimization in this regard. Process reliability is another critical aspect that needs improvement and is not yet widely achieved across the board.
Leuders: I agree that the hourly machine rate remains a key economic factor. However, we’re seeing significant shifts in equipment costs, especially due to increasing competition from non-European suppliers. This, in turn, raises the proportion of costs attributed to materials, creating additional pressure to reduce these expenses.
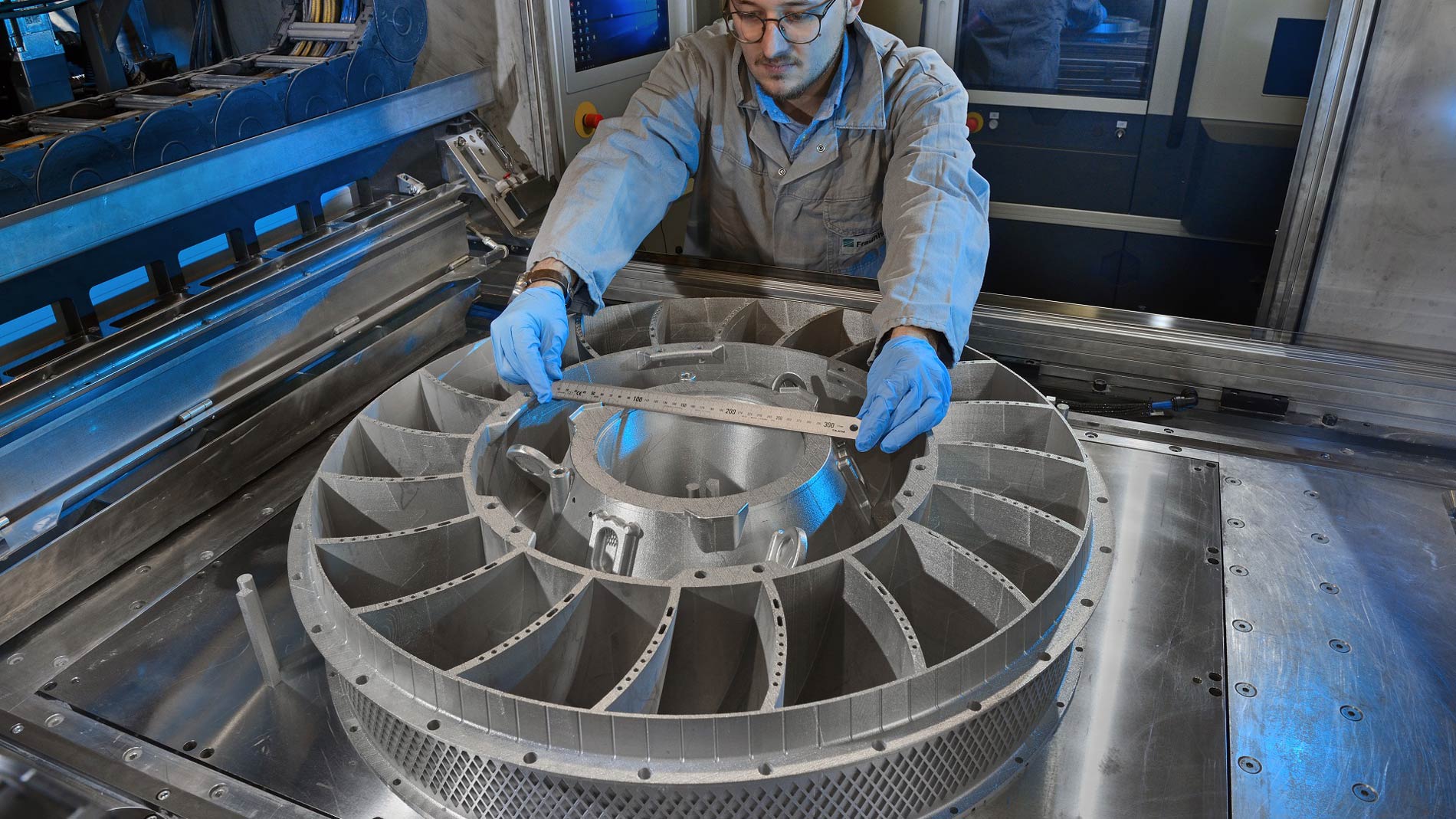
What can AM offer in terms of sustainability?
Lantzsch: AM allows for the precise use of materials, processing only what is needed, which can substantially reduce resource consumption—especially when considering the entire product life cycle. However, it’s important to recognize that material production and processing are energy-intensive.
Leuders: There are also benefits in the later stages of product use. For example, additively manufactured tools with conformal cooling can reduce scrap rates and shorten cycle times in aluminum die casting and plastic injection molding. Another significant aspect is the repair and reconditioning of tools and components, which can greatly extend product service life.
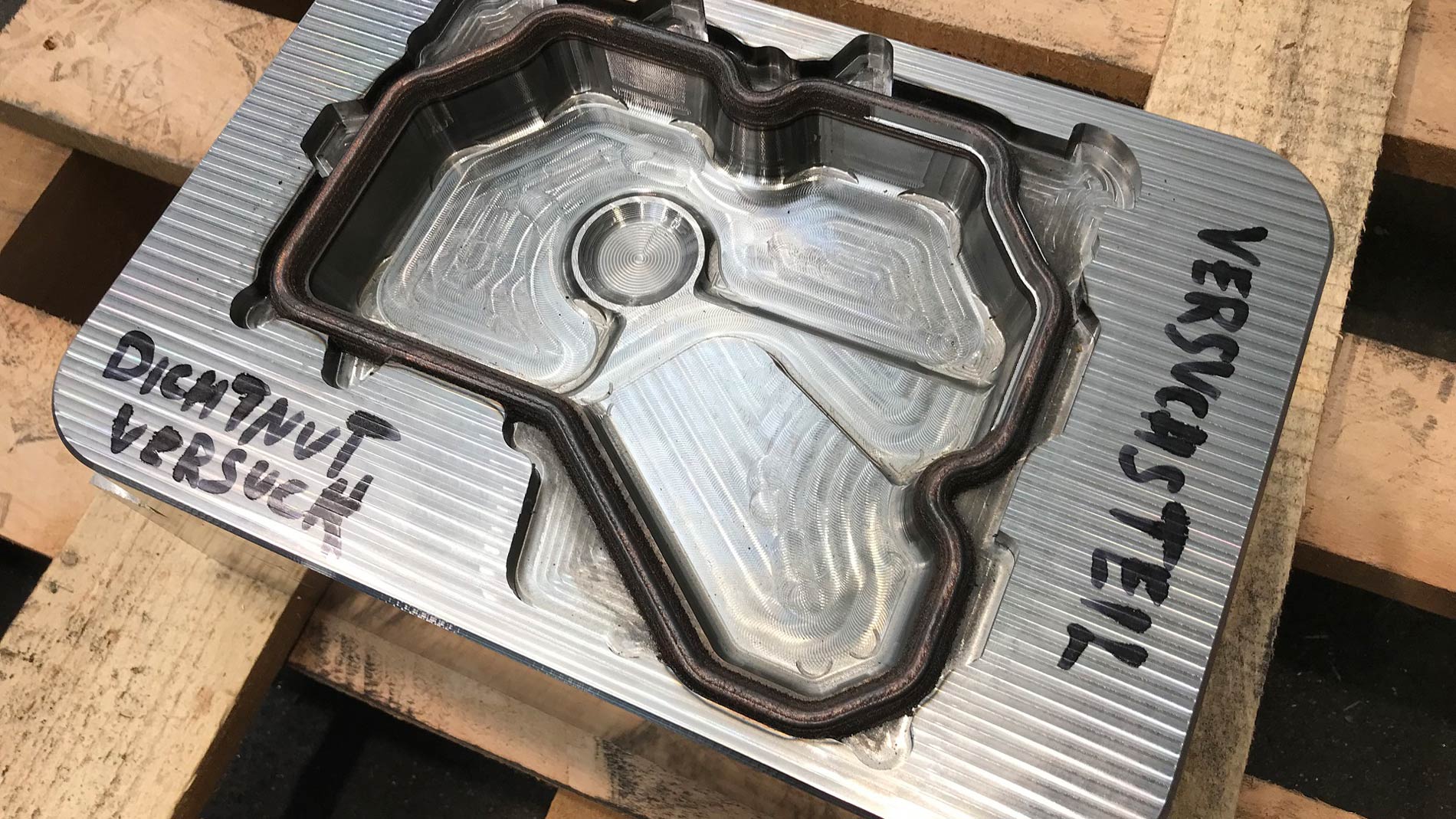
What are the long-term prospects for additive manufacturing? Where do you see it in five to ten years?
Lantzsch: In the next five to ten years, I envision additive manufacturing becoming an integral part of industrial production. It will move beyond its niche, finding applications across various industries, particularly where there is demand for customized, complex components.
Leuders: I share this optimistic outlook. Over the next decade, I expect AM to be integrated into more production chains and play a central role in the circular economy. The cost-effective recycling of components and tools will become increasingly important, especially from a sustainability perspective.
How is the industry changing, and who will be the winners in additive manufacturing?
Leuders: The long-term winners will be companies willing to make strategic investments in new technologies while managing the associated uncertainties. In contrast, industries heavily reliant on cost-driven mass production may struggle to adapt.
Lantzsch: I agree. Industries that require customized, highly complex components and can capitalize on AM’s flexibility and design freedom will be the clear winners. Aerospace and medical technology, in particular, stand to gain significantly from AM’s potential. High-end automotive engineering and motorsport will also benefit, especially with lighter and more efficient components enabled by AM.
Dr. Tim Lantzsch (left) and Dr. Stefan Leuders in discussion. Image: Fraunhofer ILT
What advice would you give companies to ensure they are among the winners?
Lantzsch: Companies should be ready to invest in research and development. It's essential to view the technology as part of an integrated system, not as a stand-alone solution, and to embed it within existing production processes. I also recommend targeted investments in employee training and skills development.
Leuders: Taking a strategic, long-term approach to Additive Manufacturing is key—companies shouldn’t just focus on short-term gains. Constructively dealing with potential setbacks is part of the journey. Fortunately, technological entry barriers can be significantly lowered. Plant manufacturers, service providers, and research institutions have built substantial expertise, and collaboration is invaluable. Learning from others’ experiences can prevent repeated mistakes.
MORE INFORMATION:
voestalpine.com/highperformancemetals/deutschland/de/service/additive-fertigung/
Tags
- Materials
- Additive Manufacturing
- Tool and die making